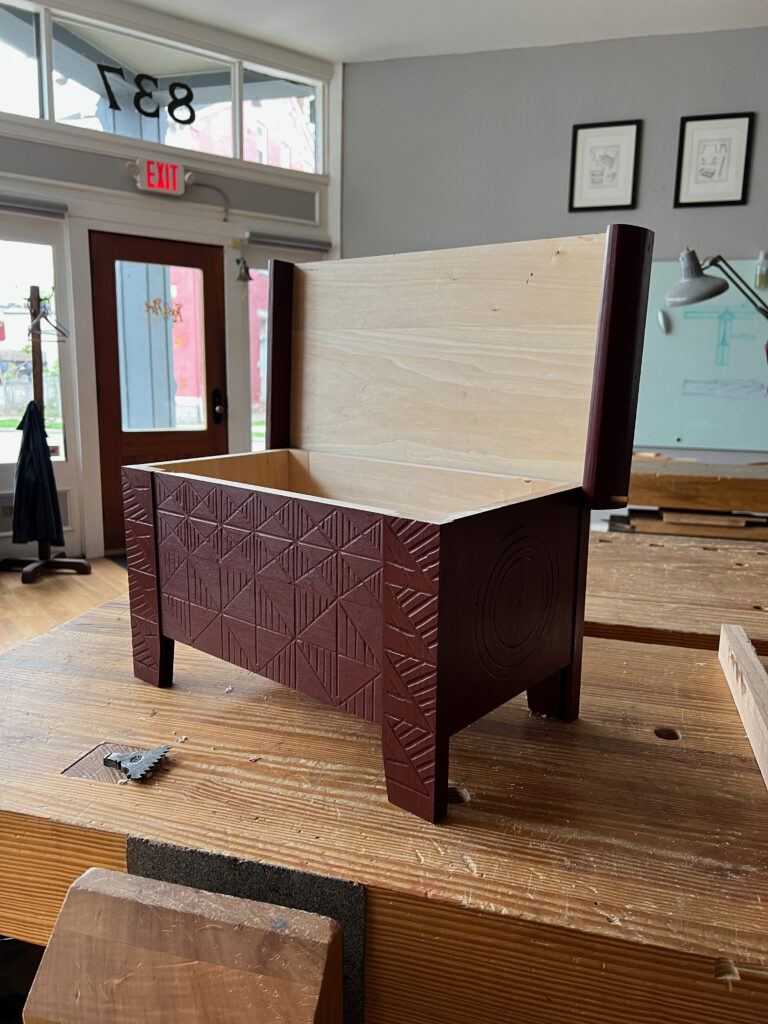
UPDATE: Comments are now closed. Thanks everyone! – Fitz
Hey everybody, I am in Pittsburgh today for my daughter’s graduation ceremony. So today’s Open Wire is hosted by Megan Fitzpatrick.
She is standing by today to answer your woodworking questions. Write your question in the comments section below, and she will do her best to answer.
Before you ask a question, a couple requests and comments.
- Megan asks if you could be gentle and not ask about her Dutch tool chest book (when is it coming? This year, she promises).
- If you could limit the number of questions you ask to one or two, her fingers will appreciate it.
- If your question is your first comment here, it will automatically be flagged for moderation. Your question will appear after we approve it.
So here we go…. Note that comments for this entry will close about 5 p.m. Eastern.
— Christopher Schwarz
Good morning Ms. Megan! My client had about 20 old railroad spikes laying around and gave me 6. I remember reading in TAW that those spikes make good planing stops. I’m not a blacksmith. Can I use them as is or do I need to find smith to flatten the top and cut teeth into them? Thank you!
With a domed head, you’re likely to run a plane into them, and without teeth, they’ll perform no better than a square piece of wood as a stop. So you could use them as is, but I’d find a way to flatten to top and tooth them. I think spikes are relatively mild steel – you might be able to DIY
Hi Megan,
Thanks for your contributions today! You are correct. Railroad spikes are extremely mild steel. Low carbon allows them to flex without snapping. They’re extremely malleable, and can be twisted into severe shapes, without breaking. Definitely an amateur metalworker’s dream.
Good morning Megan,
Several years ago you wrote about your dovetail cutting method with clever tricks and techniques. For the life of me I cannot find them anywhere. Would you be willing to share them again? Thanks
Those were all on Instagram. But I’ll be including those and more in the book about which we shall not speak.
That was for a month or so on Insta. But those will all be in the book I’m working on (about which we are not speaking), too.
Hi,
Can you comment on what it takes to run a woodworking school?
No idea – we’re not a school!
That was for a month or so on Insta. But those will all be in the book I’m working on, too.
Sharpening?
Which round bevel / angle gauge do you use to measure a blade angle? I have several and all the gaps are too big for thin blades. The sharpened angle goes all the way into the round hole.
Thanks Dennis
I don’t – I use a 35° secondary bevel on just about everything. But the Gramercy one has some shallow angles on it.
Hello. I’m working with some wood that is strange to me – it’s quite hard and has a very “grainy” grain, to the degree that when I take a fine shavings it has perforations like an oversize tea bag. Planing leaves a sort of pitted surface and hard edges seem to flake off. Any tips, tricks suggestions or deep insight into how to work with it? Thanks very much.
Erm… Is your blade sharp? Sharp always helps. And get the chipbreaker as close as possible to the cutting edge (if your plane has a chipbreaker) And try skewing the plane in the cut.
Does Chris still like the slanted leg vice on the Nicholson bench in his first workbench book? I think you are a wonderful skilled writer. Thanks Steve
Hello. I’m not doing well with sharpening. I use Arkansas stones and an oil mix. I am working on flatting the backs with progressive grits. I use an aftermarket elsipe style bevel guide and bevel stop stick for repeatable results. A range of decent to good chisels.
Question: how many passes and what pressure should I use? Firm or white knuckle? Read all the posts and Chris’s book.
To sharpen is The Gateway skill.
thanks, michael
Flatten the backs on a coarse stone…or #300 grit sandpaper adhered to a flat surface (marble tile, e.g.). After it’s flat, you can use higher grits or your stones to polish it. I don’t know how many passes – as many as it takes to get them flat, using firm but not white-knuckle pressure. On the bevel, same re pressure. If the grind is good (ie straight across and you’ve removed any toothing), just a few passes on each stone to establish a secondary bevel then polish it should be sufficient. Like everything, it takes a bit of practice, so stick with it!
If you are trying to get them sharp for the first time Arkansas stones are very difficult. While expensive diamond stones make sharpening much easier especially for initial sharpening.
Thank you Steve!
That slanted vise still works fine – students use it without trouble in every class. The downside to it is that you have to bend over to move the pin in the parallel guide from time to time in order for it to securely hold various thicknesses of stock. It is now harder for most of us to bend to do that than it was 15 years ago. But it remains a good, inexpensive approach to making a good leg vise.
When I’m gluing up mitered boxes, I seem to always get squeeze-out on the inside corners, which is very hard to remove. I’ve obviously tried using less glue, but I don’t want to starve the joint, and even a little squeeze out is not ideal. Do you have any tips or suggestions to help prevent this?
Put a strip of blue tape just behind the edge of the joint, so the extra glue goes onto it instead of the wood – be careful not to get the tape in the joint, of course.
Megan I have seen any updates about your home? Did you finish the bathroom, fix all the plumbing and I believe you had a banister to do as well?
I will write a new blog post with an update soon at https://rudemechanicalspress.com/ – tomorrow if I remember. The downstairs bathroom is finished (well, mostly – it’s certainly usable!), and I have a banister! I still need to decide what to build, then build it, at the side of the bottom landing, but the front stairs are mostly safe 😉
I always enjoyed those updates, both on this house and the one prior. Thanks.
Good Morning from Maine, Megan,
I recently donated to the warehouse fund and there will be a book headed my way signed by Chris. I would humbly request that in addition to his signature that yours and Bean’s be added as well if possible. Will Bean require extra treats for this service. If so please let me know his preferred brand and I will forward them soon. Thank you and Chris for all you do for us out here on the jagged edge of the realm. I have learned much from your writings and will continue as long and I can push a hand plane and chisel.
Richard
Aw thanks (and on behalf of Bean). No promises, as I don’t yet know the plan on those…but I’ll try to remember.
Thank you.
Thank you for taking on this responsibility! I find that chisel arrises sometimes slice my fingers when paring. Ouch! Do you sand them down to avoid that? Any downside to doing so? Other solution, like electrical tape on fingers? Or perhaps you don’t have that problem? Thank you.
I sand down not only my own, but any new ones students bring to classes. I’ve been sliced open many times when I’ve forgotten to ask if the chisels are new. I use whatever sanding disk is handy, and take a few passes down the sharp edges. A cheap chisel is the worst…because not only are the edges sharp, but there are little bits of metal still attached to the sharp edges – great fun simultaneously cutting oneself and embedding shards in the cuts.
Many thanks, Megan! I will get the sandpaper out, and put away the electrical tape.
I have always hunted inspiration for my furniture in odd text much like Lost Art Press. One source that has been invaluable to me is the Foxfire book series. Are you familiar with these books. I also have adapted techniques from these text into my own woodworking.
Yep – https://blog.lostartpress.com/2022/10/23/covington-mechanical-library-week-3-foxfire/
Would staked furniture construction be appropriate for outdoor patio furniture or does that type of joinery not hold up out in the elements? Thanks so much for your time!
It’s not the joinery that causes exterior projects to fall apart; it’s water. Paint is your best friend. Marine varnish it your second-bset friend. But my guess water will have an easier time getting into a mortise that is through-tenoned into the top of something – you’d have to keep that finish in tip-top shape. (Because as the joint moves under pressure, it’ll crack the finish around the tenon, and water could creep in.)
Hi Megan, will LAP completely move to the Anthe building or will there remain a dual presence between wharehouse and storefront?
We will eventually move the editorial offices to LAP East (I think it’s east of here…) – but that will be a ways out. But as far as I know, the plan is to keep the shop and classes here (and of course, Chris and Lucy live upstairs – they’ll be here!)
Megan thank you for answering questions today! Quick one: for dovetails for ATC, which one to choose: the Knew Ti (5 or 8”?) or the Blue Spruce (ignoring price).
They both work – as can a $20 coping saw from the hardware store. But if price is no barrier, the Blue Spruce, because it can swivel independently of the tension and cut in any direction, without having to stop to reset the blade angle. It’s awfully slick.
I have so many new questions, but I’ll pace myself.
With the new building, there’s a possibility of classes moving there. I envision a herd of new workbenches filling the third floor. And plans for them? We all know it’s going to happen. It’s like giving a rich person an empty 20 car garage.
I’m picturing an exact copy of a Roubo bench, straight out of Plate 11.
The benches/classes are staying at Willard for the foreseeable future. It will be a long time before we get around to turning our attention from the shipping/storage plans (floor 1, phase 1), then the editorial office plans (floor 2, phase 2), to the third floor. Like…so long that we may be too old and crotchety to teach.
I have a plan for the third floor, but I dare not say it out loud. (this is Chris, taking a minute before the graduation ceremony)
So secret that I don’t know about what you’re talking about!
No one does. Not even Lucy. I don’t want to manifest anything by accident.
You don’t need to acknowledge it now, but I’m assuming the plans include a loft for the Night Watchman, where I can grow old.
Chris so you came up to the “Burgh for Sunday graduation?
If you went down 376 you would go by my house, be sure to wave
Ralph
You’ve all had a really big week! Congratulations to everyone.
Congratulations on the PhD daughter! Not an easy road, and there are still discouraging stories about the hassling of women trying to join the science club. Brava!
I expect a picture of gowned and hooded daughter to appear on the Instagram feed in the neawfuture!
Maybe some volunteer labor would help this along.
I hope we’ll have an opportunity for a volunteer work party in the future – but for now, it’s getting the HVAC installed ASAP, a roll-up door in place, a loading ramp poured and the like.
Thanks for taking the reins today, Megan! A few months ago, Chris shared a Spotify playlist of shop songs he cycles through–what’s on your list, or are you hostage to his musical whims?
I like much the same music, most of the time (Uncle Tupelo, Isbell, Wilco, Son Volt, Bob Mould, Jayhawks, John Moreland…) But I also like some 90s new wave that Chris does not. (Romeo Void, The English Beat, The Church, Peter Murphy, Joy Division…). And the Kinks. I love the Kinks.
There is a museum nearby that has a nice collection of work benches that were used at a factory for the manufacture of musical instruments. Would you care if I shared my photos with you and if so, how
Sure – we’d love to see them! fitz@lostartpress.com
If all else fails, I’ll slip you a CD at hand works
Hi Megan! I live in Sweden, can I contribute to the Anthe restoration or are there shipping restrictions as usual?
Sincerely
Jerker
For now, you’d have to use a mail forwarder, I’m afraid. (But we’ll let everyone know if that changes)
Is butternut strong enough to make a stick chair?
I’m afraid stick chair questions are beyond my solid ken, but my guess – and it is only a guess – is that you’d want to make the legs a bit thicker than with oak to be strong enough. It’s easy to carve though – so saddling a seat would be a joy. I think Follansbee used butternut on a brettstuhl seat (with oak battens) …so it must work.
A few months ago I built a low staked bench, and whenever I use it for hand sawing it produces a loud terrible rumbling noise as if the board and the bench are hitting some kind of resonant frequency. This happens regardless of size or species of board, type of saw or cut, and how the board is held in place (held by hand, knelt on, clamped, held in vise, etc). It is otherwise stable and solid, not moving or making a sound while planing, chopping, or any other operations. What might be causing this sound? Did I accidentally create an acoustic chamber or is it simply not thick or heavy enough? Thanks!
Huh. I don’t know. But my guess is that either the bench or the work is flexing as you pull the saw back (given that isn’t not happening when applying only downward pressure in other operations, it’s likely the bench). Or maybe you have a musical saw: https://www.youtube.com/watch?v=7E_U1xyK7Gw
I forgot my second question: I’m working on a set of cherry knife handle scales for a friend, but when cleaning up the inside curves and end grain with a file and/or sandpaper a cloudy surface has been left behind obscuring the grain. Because the fit of the scales to the tang is crucial I’ve been hesitant to do anything that might remove too much material. How might I fix this? Thank you!
Scraper, or sand to higher grits. But if you think you’ve already sanded to a high-enough grit, I’d put some alcohol on that end grain to see how it looks. You might be closer to finished than you think, and sawdust is obscuring that.
Hi Megan! What’s one woodworking skill you want to improve on?
I’d like to get better at diagnosing WW problems from afar (that would be useful today, for example!). But for myself, I’d like to be better/faster at trim carpentry.
Good morning Chris. Thank you for doing this. I’ve expanded from hand tools and now have the DeWalt 735 and PowerMatic PM1500 bandsaw. At some point I may get a 12” jointer. I need proper dust collection. I was planning to get the Oneida CV1300 (3 HP). I like the form factor of the Harvey 700 or 800. Have you heard others who own the Harvey’s if they think it is a decent system? Much of what I see on YouTube is where Harvey has provided them to YouTubers so hard to find unbiased opinions. Thanks.
Hi Joe – Chris is out of town today, so I’m answering questions as best I can. FWIW, a neighbor has a Harvey – I think the 700 – and his basement shop stay impressively clean. (He also has an air scrubber though, so I don’t know for sure it’s the dust collection that keeps it completely tidy.) But I’ve not used one myself, so… Perhaps some readers with experience can weigh in?
Thanks Megan. I really like the form factor for my garage. Just want to make sure it works well. Fingers crossed your are at PTSWW in 2024 – been holding off on making a full sized ATC in hopes I still can make it with you – stupid 2020 Covid.
I hope to be there in June 2024 (talking to them now!)
Awesome! I will sign up for sure! I will pack my tools in the mini-ATC for the class.
Any chance of getting the Charles Hayward books offered as PDFs? I prefer the PDF versions because I don’t want big books cluttering things up in my already too-cluttered house.
I’m afraid not. We don’t own right to offer them digitally.
The Internet Archive has Hayward’s volume, “The Complete Book of Woodwork,” including text and illustrations, available as a PDF file, as well as other digital formats, at the link given below. Since it is the “Complete Book”, what more could anybody want?
https://ia804706.us.archive.org/1/items/in.ernet.dli.2015.425567/2015.425567.The-Complete_text.pdf
I don’t know? Perhaps permission from the family, which holds the rights?
Since Hayward’s “The Complete Book of Woodwork” was first published in 1955 when the length of copyright was 28 years, and that is the particular edition made available as a PDF, it is highly likely that the copyright for it expired in 1983. Do you know for a fact that his family still holds the rights to it, since that is what you have asserted? The Internet Archive is a reputable organization, and I doubt they would make it available if it were still under copyright protection, and in that case, the rights of his family to any control of it would have expired when the copyright did. I understand that publishers would like to preserve copyrights into perpetuity, but even that ever-more-restrictive law still has legal limits.
Yeah, that’s not how any of that works.
This might be of interest re the Internet Archive: https://www.npr.org/2023/03/26/1166101459/internet-archive-lawsuit-books-library-publishers
Also, as it states in the front of every one of our Hayward books: “Text and images are copyright © 2017 by The Woodworker, MyTime Media”
Copy
In the UK copyright expires 70 years after the death of the author. He died in 1998. I don’t know what else to say.
Good morning. Is there a listing anywhere of woodworking stories/articles in the Foxfire series? Thanks.
I’m not aware of one.
Having been gifted with the complete 14 book set (foxfire 1-12 plus 40th and 45th anniversary) for my birthday recently, that’s a very good question. I found a list for 1-6 at https://websiteofahistoricalpolymath.wordpress.com/bibliographies/contents-of-the-foxfire-books/ but no complete lists for the others. If you search for each volume separately you should at least get a set of general topics. These are all articles from a student run magazine but some things are very detailed (complete drawings and explanation of a home brew sawmill complete with a couple ’30’s patents from the builder; how to build a log cabin in voluminous detail at 3 different quality/skill levels..). I know one is mostly pottery and iirc another is mostly blacksmithing. Warning: they are kind of like the Hayword series but not organised topically, you can lose a lot of time popping down various rabbit holes once you pick one up.
(My sis was appreciating help raising a metal kit 24x40x18’8″ houseframe, that’s not the norm for birthday presents!)
Thanks, Esther.
Hey Megan,
When building finer casework, how do you handle the nail holes left by the yardstick extrusion technique to align dovetails? Do you leave them? Do you attach the yardstick differently?
I don’t use that method if it’s going to possibly show on a project where it might matter. But if I had to, I’d attach the stick w/strong double-sided tape, and be gentle. But I’d be far more likely to cut a rabbet at the baseline if I needed the positive stop (say, for large casework – for small projects, I just align things by eye).
What do you guys use a Lump Hammer for most often?
I use it for assembling large casework (tool chests, mostly), putting a scrap between the hammer and the work. I have also used mine to bash chocolate into tiny bits (inside a plastic bag) and to knock plaster off of lath.
You don’t have a chocolate-specific hammer? I thought that was a given.
I used to…but Lumpy is heavier.
Hello! Thank you so much for starting this quick question Saturday! So much great info. Here’s mine:
Is it safe to break down wood for multiple projects into blanks at the outset to help get organized, even if those projects might be an extended process?
My kid and I are going to be doing projects off and on all summer with different types of lumber (sawbenches and a stool for him, and a chair for me.) so things will definitely be fun, but not quick!
My thought was ‘Yes,’ based on the stick chair video where Chris explains using blanks to replace broken pieces, but wanted to check before I do something dumb. Moisture in the rough stock is about 8-9% at 20mm, while wood in my house is about 8-11% at 20mm as far as I can tell, but there are different finishes on the interiors I measured, so not 100% sure. They seem close and I have no AC in the garage or house.
Thanks Megan!
You can break it down – just leave it long enough to safely go through the planer (if it’s going through the planer), and don’t take it to final thickness until you’re ready to use it. If possible, let it acclimate in it the environment it will end up in – but if neither the house or shop have AC, I guess that won’t matter (though in the winter, I assume at least one of those is heated!).
I read the backstory to the Anthe building. Woodworking machinery and printing. Wow. Does anyone dig deeper or faster than Kara Uhl on a research project? Love her stuff.
When using linseed oil paint, Chris said that it flows better with an initial coat of linseed oil. Would that be cut with something, so it would dry quicker? Assuming oil with no heavy metal driers in it
Nope – just a thin coat of pure linseed oil
Good morning Megan,
Thank for you doing this in Chris’s stead. I have a question regarding the physical materials used for LAP’s books. There are a handful of books I like to keep in the shop (which is an unheated garage, very much prone to temperature fluctuation) for quick reference while I’m working; the Anarchist books, the Stick Chair Book, a few others.
I notice that the hard covers over time begin to cup outward, not unlike a piece of wood that isn’t fully dried. Usually when I take the books inside the warpage dissipates after a couple days, though sometimes it doesn’t entirely disappear.
I don’t care about this from a functional standpoint, but I just want to know if my allowing the books to be a little more exposed to changing temperature/humidity is going to reduce their lifespan in the long run; I love my ever growing LAP library, and I’d hate for the books to degrade due to my mishandling of them. Have you encountered this before, or do you know if this is detrimental in the long term?
Well, the boards are a wood-based product (heavy cardboard), so yep – they’ll warp. It’s why HVAC and a dehumidifier is of paramount importance for the new space. That’s why the books are wrapper in plastic, too – to maintain the humidity level in transit and storage. I don’t think the warping hurts the covers from a functional standpoint, though I guess with enough cupping/flattening, the endpapers could start to lift. I suppose keeping them in a plastic baggie could help (do it before they warp…). Or build a book chest with a Goldenrod in it for book storage 🙂
Thank you for the insight, I appreciate you taking the time!
Good Morning, Megan. I had a question regarding the tongue & groove car siding that you utilize on tool chest bottoms. I think this is a great idea and I found some clear boards at my local Menards. My question related to the v-groove that is milled in the middle of the boards. Do you typically put this v-groove toward the inside of the chest or to the outside (facing the floor)? I appreciate you taking the time out of your day to do this!
Thanks,
Jacob
I go both ways – in my English chest (ATC) the center V-groove is facing up. But I usually put that groove facing down in the ones I sell. I have no idea why.
I appreciate the response – thank you!
In the class last month they were outside, keeps the inside tight to things like rainstorms.
Thanks you!
True – heart side out is always safer, to combat cupping – especially on a chest that might get moved in and out of climate-controlled spaces a lot
Good day Megan. I am building cherry end tables and experimenting with different natural finishes. I made and tried soft wax on some scrap, and I liked how the figure is brought out, but it is a tad too matte for my taste. I bought a pollisoir from Don Williams and I’m experimenting with that. Do you use a hard wax like beeswax with the pollisoir or can you use softer waxes? Can you use a pollisoir to get more\r sheen with Soft Wax?
Thanks taking on these questions, and PS, I love my ATC. Thanks again for teaching such a great class.
I think you could add glow by using the pollisoir on soft wax, then buffing. But it will be more of a glow – not a highly reflective shine. I dunno – try it!
(And thank you)
Pardon my ignorance. PTSWW?
Port Townsend School of Woodworking, in Port Townsend, WA
It’s a little slice of paradise in the Pacific Northwest. I like it so much there (as does my wife) that we may move up there. We both felt that way BEFORE the woodworking school opened. Both my wife and I lived in the Seattle WA area before we were married and knew each other and both used to visit there often. Coming from the SF Bay Area, everywhere else in the country seems affordable.
If you could only buy one, would you buy the Veritas skew rabbit plane or the LN skew block plane? Which would you find more versatile for boxes and furniture?
Veritas skew rabbet. I don’t like block plane that has the blade sticking out to the side of the sole. I always cut myself if using it for anything other than rabbeting. So I use my rabbet plane for rabbets, and my block plane for block-plane tasks.
Hi, My question is about design, sketches, drawing… from the idea to a useful sketch for the workshop.
My thought starts with the fact that nowadays, most of woodworkers are using sketchup or similar softwares. The thing is this is fairly novel in the woodworking history although people hardly conceive to do differently.
First, I do not like those softwares. Second, I always wonder how task was performed “before”. It seems to me that classic authors do not speak much about the preparation ahead of woodwork production. What are the steps to design? from rough drawings to elaborated views with assemblies (thinking of art du trait in very complex curved pieces for instance). How to be efficient and not starting with too much details that required time to redo in case of a mistake. Any drawing techniques to know? And then, the feedback from the workshop (after planing wood pieces, dimensions may slightly differ), how to handle it.
I might overthink this, but all the preparation ahead of making is not often treated in modern and classic book (afaik) and I would like to know more on this topic. Is there any reference you may suggest to read?
Sorry for being long and thank you for your time.
Any book on mechanical drawing and drafting. Plus George Walker and Jim Tolpin’s books for inspiration. Furniture is the child of architecture and uses the same design principles and tools – there is a lot of work on this subject.
Megan, I have a question on one of Chris’ projects, so if you don’t know the answer no problem. Have you seen/used the campaign desk he built for the Campaign Furniture book? I’m curious how sturdy it is. I’m planning on building one for my daughter (she is at that stage where a desk would be nice sometimes, but being able to get it out of the way to play would be good at other times). I figured this might be a good option, but I’ve never actually seen comments anywhere from someone who has built it. I’d probably make the top one solid piece, but I don’t really see that having an effect on stability.
The field desk or the secretary? Either way, I have answers. The field desk was at my house for a while, and is plenty sturdy. The secretary is Chris’ desk upstairs, and I believe Lucy used it daily when we were all working from home. Both have held up well since he made them, and have seen use.
I was specifically thinking of the field desk, but thanks for the info on both. Good to know it is sturdy. 🙂
Hi Megan:
I took a Dutch Tool Chest class with you at LAP in 2019 – you’ll be happy to hear that I got it home and finished it and have been using it since. I really love it. My learnings: 1) I should have thinned the general finishes milk paint a bit – do you dilute yours with water and if so how much dilution do you recommend? 2) Installing hardware is trickier than I initially thought and I had to try twice to align the hinges properly, and 3) still figuring out the best place to put the dovetail saws in this chest – any opinions?
Finally, Sir John Falstaff is one of my favorite comic characters in Shakespeare – who’s yours?
Regards,
Bill
I struggled with my milk paint as well when I used it on a mini-ATC I made. So much so, that I have kept my eyes open to see if I can have a more pleasant experience the next time I use it. As such, I once saw a blog post Chris wrote where he used 2 parts of water to one part of powder. That really caught my eye as the instructions talk about a 1:1 ratio. The other person who has written about viscosity for milk paint is Elia Bizzari in his 29Oct2017 blog (I copied in the notes feature of my iPhone). He uses plastic Pepsi bottle with a 5/32″ hole drilled into the cap. Ideally the stream (not the last drop) flow for 10-13 seconds. I don’t know the viscosity of what Chris suggests but would be easy enough to measure.
Hi Bill!
I do not thin it for brush application (I just draw it out with the bristles). For spraying, we dilute with water about 10 percent (and it will work fine with a brush then, too – but might take an extra coat). 2. Yep – especially with that angle and hand-made hinges (I’m assuming you used the LV strap hinges) – I have to move them on the underside of the lid sometimes to get things to align perfectly at the back edge. I typically install one screw on each and carefully test before fully committing. It’s easier with butt hinges, but they don’t look as cool!
I use a floor till at the back of the top cubby for my saws.
Caliban.
Suggestion: Sharpen This book. In a future update, add a paragraph or 3 on Secondary Bevels – arguments for and against them on tool edges. Its missing from the book. Thank you
Hi Megan (and apparently Chris) – I’ve been having with my 5/8″ wood owl auger bit, which has decided that it is a splitting tool rather than a hole-making tool. It feels like the lead screw is pulling the bit ahead faster than it can cut…but the bit is relatively new (in fact, I bought it for a LAP stick chair class just a few months ago). I’ve switched over to a regular wood-owl bit, but I don’t like it as much because it’s harder to eyeball resultant angles with it. I’m thinking of filing down the threads on the lead screw…is that nuts?
I’m afraid this one will have to wait for Chris. I don’t know.
The lead screws on the Wood Owl auger bits are more wedge shaped than vintage auger bits.
That is why they sometimes cause splitting. A solution is to pre-drill all the way through with a much smaller bit that is close to the diameter of the lead screw so that it still bites just a little. I have not tried filing the screw.
In the history of the new building, there is a section on companies that tented space, data coming from old help wanted ads. One of those ads was looking for seamstresses for sewing “… skirts, middles…”. What is a middle? Petticoat concept? Underwear? Early crop tops?
Thank you for what is always an interesting read.
No idea. You might not guess it from my sartorial brilliance, but my fashion history knowledge is lacking 😉
Hi Megan, I’m looking for some workbench advice. I have this Sjoberg workbench, which used to be an apartment workbench, but now it’s a patio workbench (sad times). It has taken significant weather damage: there are visible gaps between the boards in some parts of the top, the top is no longer flat, the benchdog holes trapped the benchdogs, etc. Could you provide some advice on how to restore it or protect it? (I understand this is a big question, so any resources you recommend are great too). Currently I have it covered in the best tarp I found, and resting on some rubber pads.
Erm…I’m afraid this is beyond my remit. I know of no workbench-specific restoration books. As far as protecting it, if it has to stay on the patio, a well-attached tarp would be my solution (which it sounds like you’re already doing). It sounds like the top is delaminating…so help that delam along, then flatten all the pieces and reglue them, and re-drill the dog holes I guess? But honestly, I’d not bother until you can not have it on the patio; it’ll just happen again.
Hi Megan. Any chance of LAP hosting some tool shows with the additional space?
People would love to see Lie-Nielsen, Lee Valley, and all the local makers tools too.
There is always a chance.
Hi Megan , I have been using General Finishes Milk paint for the past several years but I am finding the colour selection limited and for some items I would like a slightly higher sheen . I find powdered milk paint a lot of work ( my results are not that great ) and I am not quite ready for LInseed oil paint . So , are there other paints you have used that can be applied without a primer that would work well on furniture ? Thanks and please give my best to Bean .
I’m afraid you’ve named all that I’ve used, with the exception of latex, which can look a bit plastic to some people. That said, my tool chest at LAP is Benjamin Moore latex, and I like it just fine. (And the available colors are legion.)
GF (which recently severely limited its ready-made color selection) says you can tint it with hardware store paint tints – but I don’t know any stores that would do that if you’re not buying it there, and none of the hardware stores near me sell GF paint. So catch-22 there, I guess.
But as far as a glossier sheen, after the “milk paint” has fully cured, you could spray a topcoat with higher sheen.
I’m almost done reading the Anarchist trilogy and am also in the middle of By Hand & Eye. So far I’ve loved the LAP books and I have three more on the shelf I need to read (The Essential Woodworker, Chairmaker’s Notebook, and With The Grain). What are some of your favorite books you would recommend once I’m finished with the ones I have?
ATC is my favorite. Among those you don’t have, I’d probably go with “The Joiner and Cabinet Maker” and “The Handcrafted Life of Dick Proenneke” (But I love them all of course!)
I loved watching Alone in the Wilderness on PBS! And I’m really excited you guys have a book on it. And having your books in hardcover gives me such a greater reading experience than paperback. The extra time and resources you guys spend to do this are well worth it.
What is a “ golden rod”?
A brand of low-profile dehumidifier. Usually sold for gun safes, but I’ve installed them in tool boxes.
Hello Megan. Thank you for this and I hope you are enjoying this today as much as we are.
Two questions regarding cut nails.
You have always expressed a preference (reverence?) for the expensive and sometimes hard to get French Rivierre nails. How/why are these superior to the slightly less expensive but easier to procure Tremont nails? Also, do you know of a resource or guide regarding appropriate pilot holes for these nails?
Hi Paul! They hold better, thanks to four corners biting into the wood (and though more expensive, blacksmith-made nails typically hold better still because the shafts are more rough). But I like the Tremonts a lot, too, and they’re what I cheerfully use when I can’t get the Rivierres (and where I don’t want such a prominent head). Their hold is also strong – far strong enough for any of the projects I make. As far as pilot holes…start by matching the pilot to the size of the nail at its tip and test it in offcuts in the same orientation and stock as the actual work. Go up from there. More on nails: https://www.finewoodworking.com/2020/09/30/on-nails
Is there any way to harden the crucible dividers? They bend pretty easy when the legs are thin.
I’m afraid that’s a question for Chris; I don’t know much about metalwork (if he doesn’t answer here, ask again next Sat., when he’ll be back at his keyboard)
Mail it to me at 837 Willard St. Covington KY 41011. I’ll modify and sharpen the tips so they are stronger. The first 100 or so were too long in the tip
Megan, I’m going to be in northern Ohio — Sandusky, Toledo — this coming week. I should be able to make it down as far as Colonial Homestead in Millersburg, Tuesday, I hope. Any suggestions, or recommendations?
Be sure to take cash or your checkbook to the Colonial Homestead, as he does not accept cards. There is a bank machine in downtown Millersburg, if needed.
Take lots of $$$ 🙂 Chris loves the Der Dutchman in Walnut Creek (I merely like it). If you have time, go to Yoder’s hardware and check out the wood selection – they always have a lot of weird locally harvested stuff, which is a lot of fun to see! Tree of Heaven, for example, last time I was there. I’ve never seen it milled before.
Thanks!
What is the best lubricant to use on all wood threads on workbench vises ? I have to vises on a very old workbench that have never been lubed, and I don’t want to contaminate with the wrong product
Regards Tim
I use canning wax on my wood-screw bench at home. I’ve also heard mutton tallow works well.
Do you have any experience with ECE wooden planes? I really like them. I use the scrub, Jack and smoothing plane all with the wedge.
I’ve used them a few times. I like my Stanley metal jack (with its heavily cambered iron, so I can use it like a scrub), and Lie-Nielsen bronze No. 3. Nothing wrong with the ECEs if that’s what you like – just not my daily users.
Hi Megan – I’m building a workshop, but very slowly. To keep me sane I’m daydreaming about it being finished and decorating it. I’d be interested on your thoughts please on an antichrists tool chest vs hanging wall cabinet in a small shop (approx 16.4042′ x 9.84252′ or 5m x 3m).
I’m probably going to make a DTC either way, just in case there’s some tool overspill.
Hugs, Jay in the UK.
Antichrist’s tool chest made me giggle. I prefer a large floor chest for the shop – I take out what I need, then put it back when I’m done. I guess the same would work in a wall chest…but I’m partial to what I’ve always used! But 5m x 3 m is pretty small, so I’d make it low enough that it can roll under the end of your bench if it has an overhang.
Hi Chris, do you ever make several chairs at once (ie batch production) or do you always make them one at a time?
Not Chris. But he typically works on no more than 2 at a time. He’ll usually batch out parts for 2 at the same time (plus extra sticks and legs for future chairs), maybe cut and glue up arms and seats for both, and rough in all the legs. Then, he usually turns his attention to just 1 through to finish before the second one.