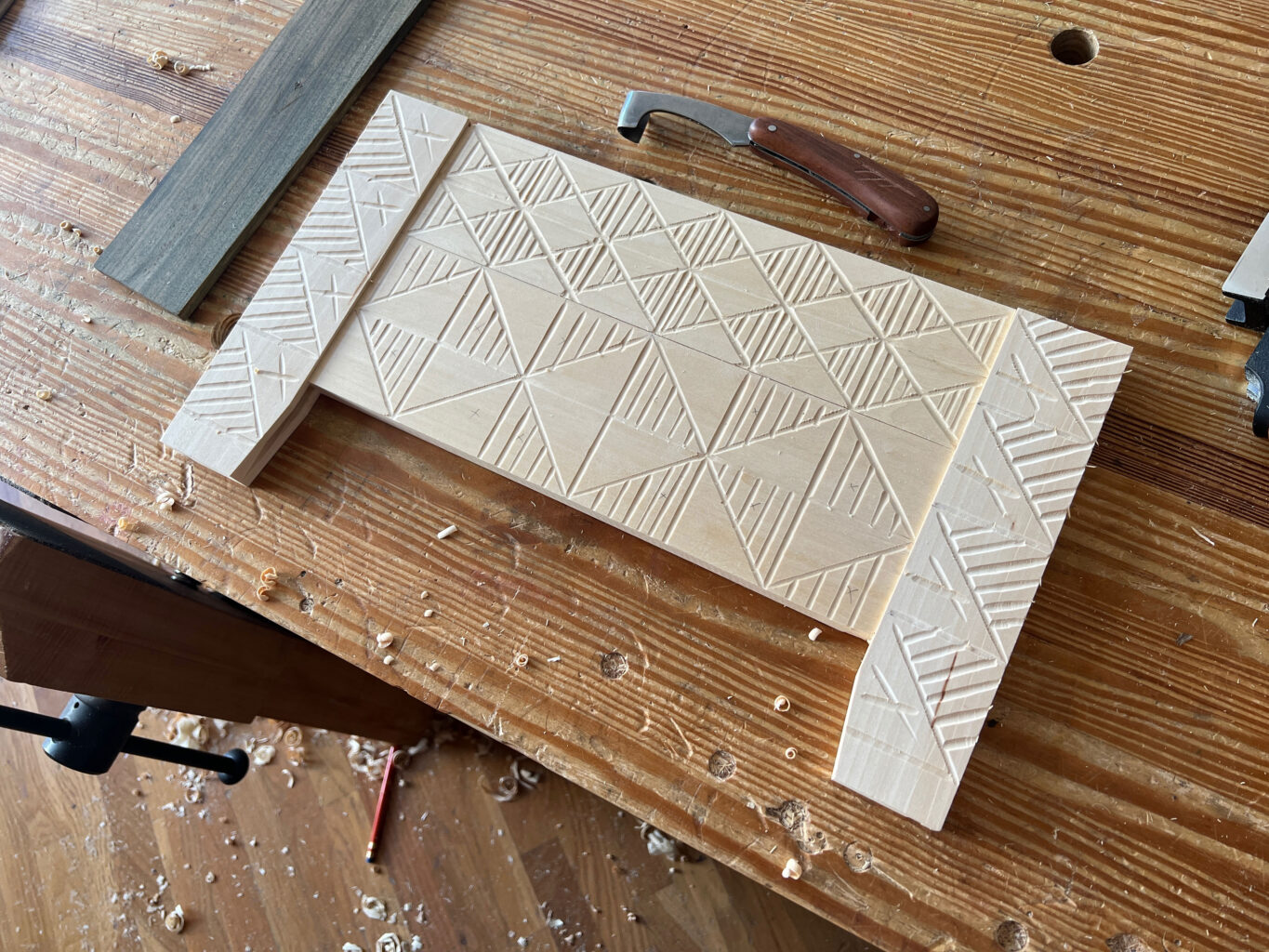
If you have a question about woodworking or our products, this is the place to get it answered – today.
Here’s how. Post your question in the comments section below. If possible, I’ll answer it. Simple.
But (and as Pee Wee Herman says, Everybody’s got a big butt)….
I reserve the right to ignore questions that are troll bait. Also, if you post a comment and it does not immediately appear, it has been flagged for moderation. First-time commenters are always kicked to moderation. Also, posting a lot of links, using hateful language or a lengthy message causes the software to flag it for moderation.
Your comment will appear after I approve it.
In other words, there is no need to keep posting a comment over and over.
Comments are now closed. See you next Saturday!
— Christopher Schwarz
Made a dining table trestle style based on your article from a long time ago at PW. Frame in SYP, through mortise in the legs made by gluing up two dado halves, tenon wedged and drawbored. After a few years the joint at the bottom is loose resulting in the table rocking back and forth.
I imagine I can knock out the drawbored peg and disassemble it for repair (love hide glue) but I fear that this was just compression of the wood and will happen again if I don’t use something firmer. People seem to put their weight on the table when sitting down and that’s a lot of leverage to ask any two tenons to support. Thoughts?
SYP is plenty strong for this task. If the wood has compressed, add oak wedges when you reassemble to stiffen things up.
Hi Chris, what made you decide to choose a tool chest with tills over one with drawers? Aren’t drawers a more efficient use of space?
Drawers obscure what is inside them. With three tills arrayed front to back in my chest, I can see every tool at a glance, and every tool below is accessible by sliding one till.
It is a fantastic way to work. I didn’t come up with it. Most tool chests have tills instead of drawers in my experience.
Assaf, to add to what Chris said, for decades I worked as an executive chef and kept my tools in a box with drawers. Tools get jumbled and jostled and fishing for something in the back means tools get pushed forward in pile while you try to make clearance for a tool in the rear.
Plus, you need to be especially careful pawing through a drawer full of sharp objects.
I’m going to build a wooden chest with tills to try out.
Hi Chris, I have just milled some boards from an ash (European) tree that I felled about 18 months ago. They still have a very high moisture content so I suspect they will undergo some warping and checking as they dry. I appreciate that some shrinkage in the seat is good but is it better to let them partially season before using them as seats? Also, I have some great slabs of crotch wood from the same tree, would they make good seats or do you think they would warp too much? Cheers!
Slightly damp seats (with dry legs and sticks) works well and has been used for centuries. But not too wet. Maybe let them get to about 20 percent MC before using them.
Crotch looks great for seats and usually doesn’t split (a good thing). But saddling it? Whew. No thanks.
Many thanks Chris, and I really appreciate you taking the time to do this. 👍😎
Seal the end grain with glue or paint to prevent checking I learned this the hard way!
“Gee, it’s really nice out.”
Pee Wee Herman: “Well, then leave it out.”
Morning. Is there a reason you didn’t add the 1:4 dovetail guide to the third rail of the 1:6/1:8 guide?
You need one leg at 90 degrees for marking out dovetails.
Then the guide would be mostly useless. You need that 90° leg to mark out the joint.
Is it easier to create dovetails in softer wood like pine, or a harder wood like cherry? I’ve only had the courage to experiment with the softer, cheaper varieties. Thanks.
White pine will make you feel like a dovetailing God. Soft and homogeneous. Something with alternating hard and soft layers, like Douglas fir or Southern Yellow Pine are a pain to dovetail. I’d rather dovetail cherry than one of those “softwoods.”
Practice in pine or poplar. Then move into the more expensive woods, such as cherry and walnut. Basswood is also a joy to dovetail. Avoid ring-porous species (oak or ash) or softwoods with big denisty differences between the earlywood and latewood.
Hi Chris, do you have a favourite chair in the collection at St.Fagans? If so, what makes it stand out to you?
Yup. It’s one on the cover of “Welsh Stick Chairs.”
https://lostartpress.com/collections/books/products/welsh-stick-chairs-by-john-brown
It is impressive in person. Clearly made by a non-professional. But beautiful in every way. And so simple.
Chris, Do you have any thoughts on finishes and woods to use for chairs that will mostly be outside? Exterior paint seems like a good choice, but if I wanted to show off the wood, and I also want to avoid film finishes that have to be completely removed to refresh, are there any good options?
Deck stain.
if it will be in a covered location and stay out of hail, you might consider one of the interlux schooner line of varnishes. it’s a tongue oil and phonelic resin based boat varnish. spendy, but really good. I’ve only used it on pine, but it holds up REALLY well to all the elements except hail which will crack the varnish and let water in. i have a piece going on at least 10 years on my covered porch and still looks good. (Omaha Nebraska lots of sun and cold).
I painted my stick chair with milk paint and then finished with a mix of varnish and linseed oil. The appearance is a little too matte for my taste. How would Soft Wax 2.0 affect the luster?
It will add a little luster. But I would instead just add a coat of wax. Renaissance Wax or whatever you can get.
I have had good success burnishing the milk paint with 0000 steel wool, then tung, and then paste wax. It’s a lot work but the results speak for themselves. Watch Curtis Buchanan’s YouTube Windsor chair videos. He has a lot of good tips.
Tung oil
thanks for the suggestion. That’s super helpful.
Hi Chris, what are your thoughts on General Finishes milk paint vs the powdered stuff? I am starting on the boarded bookcase from ADB, in white oak, and was thinking of finishing with Tuscan red and black bison wax on the sides (inspired by the finish on one of your recent chairs), and two coats of shellac for the inside.
The General Finishes “Milk” Paint is actually an acrylic. And a very good one. Lays out beautifully and kinda simulates the milk paint look. Good stuff.
Thanks. I’ll give it a try.
Good morning, I have 100 red oak 1″ thick 9′ planks to air dry in widths up to 20 “. How thick of sticker wood is recommended for plank separation. Logs were fallen on March 16 and arrive from the mill this week coming. Thank you.
We use 1x for stickers. Usually white pine.
As a beginning woodworker, I have one saw, a dovetail saw. What would you recommend for a second saw? Carcase? Handsaw (rip or x-cut)? Thank you.
I would buy a tenon saw so I could cut tenons efficiently. And use a first-class saw cut (from Essential Woodworker, basically a trench cut with your chisel) to saw the tenon shoulders. This will prevent splintering from the rip teeth.
I have many feet of rabbets in my near future (sound lucky!) but don’t have a rabbet plane (not so lucky). What I do have is a Veritas small plow plane, a Lie Nielsen No. 60 ½ rabbet block plane, a large router plane, and a medium shoulder plane. I have no skill in making rabbets. I am assuming that the plow is my best bet, but I wondered if you could talk me through the best technique so that I don’t ruin the wood while gaining the skill. Do I plow a ¼” groove, then remove the 1/8” remaining groove wall material with the block plane? I’ll be using white oak. Would your answer change at all if it were quarter sawn?
My advice would be to clamp a fence to your work and run the shoulder plane against it. You will need to set the iron so it is slightly (only a hair) outside the body of the tool on the fence side. Otherwise you will make a stepped, sloped rabbet.
If you do make a sloped rabbet, you can turn the shoulder plane on its side and clean up the wall.
Your plane with a plow will work, it’s just more tool setups. Maybe try both.
Quartersawn vs flat sawn wouldn’t change my answer.
As an aside to Chris’ comment; you can run up to a 3/4” cutter in your small plow. Check LV for one. The Veritas small plow is a very capable rabbet maker.
Just my 2¢
Favorite cookbook?
Do you have a certain way you organize your tool rolls?
Plans for any new books with measured drawings other than then the peasant one?
The Lee Bros. Southern Cookbook (even though they are Yankees)
My tool rolls are stacked (on end) in the saw till.
LAP has lots of books in the works with plans. Megan and I are working on a book on Western Shaker Furniture.
“Yankees”?
🤤 lots of interest in a book on building shaker furniture. I assume “western” means Kentucky.
Yup. There were several colonies here and we have photographed about 100 pieces that are worth examination in a book.
Hi Chris. I’m making my first Gibson-like chair, and I have to steam bend the comb. I don’t want to make a steam box for possibly the only chair I’ll ever make. Could you point me towards an alternative way of steam bending: pouring boiling water over the blank, covering it with wet towels in the oven or something else? The blank is 21”x4”x1” quarter sawn white oak, kiln dried. I’m soaking it now. Thanks for any help.
Best,
Michael Beck
The originals were sawn from solid, FYI. I laminate mine from three pieces of 8/4.
What you are attempting is a 10 on the difficulty scale for a first-time steam bend. Try putting it in a roasting pan, filled with water and covered with foil, in the oven at low heat. Maybe an hour or more. Good luck!
For what it’s worth, all of my bends are in water, not steam. Hot and moist makes wood bend. On a really tough bend I wait until the wood sinks. Sawn wood, not split. It always works.
Take a look at large bamboo steamers sold at Asian markets and restaurant supply houses.
They are relatively inexpensive
You can take heavy sheet plastic and fold it around the wood and use spring clamps or clothes pins to hold it closed. A wallpaper steamer makes a great steam box. Makes a good quick and dirty steam box and works great in boat building for parts too large for a steam box. I would steam for at least an hour.
Chris: I live in the SF bay area.. I have acquired more woodworking tool than I need (or can store) hand and power. I have tried to give them to a few local tool libraries but they are not interested in woodworking hand tools (too sharp, too hard to maintain, not what their clients need) nor power tools that may maim their clients w/o sufficient training. All this makes sense. Do you have any idea who could use these sorts of tools. Is there a directory for North America. Not really looking to sell any of them just donating.
Check out the Living Tools Project.
https://www.thechairmakerstoolbox.com/the-living-tools
We support this organization and participate!
Perfect – Thanks
Hey at the risk of overstepping what is alowed in the blog, im from israel, a well known tool desert. In the last decade the beginings of a small movement has begun in woodworking in this country. I know of a school for underprivileged? students that has started looking for donations to open up a hand tool shop class. I know donations would be really appreciated. If this is acceptable to you and LAP id appreciate it is you reached out to my email if you are interested.
I run a group shop called Gardenville Station in the Bayview in SF. We rent studio space and shop memberships. We’re hoping to start classes this year. I could probably find a good home for some of your gear!
I guess a link might be helpful?
gardenvillesf.com
RC – I do not want to detract from the very worthwhile suggestions that have already been offered. If you’re interested, you may wish to contact Bay Area Woodworkers (https://www.bayareawoodworkers.org/) or Diablo Woodworkers (https://www.diablowoodworkers.com/). Either organization might be able to assist in finding a new home for your donated tools and equipment.
Hello Chris, i would like to know what do you think of the Clifton 500 spokeshave ? , could it be a good travisher alternative ? Thank you.
I have never seen or used one, I’m afraid. The radius is very tight for a travisher, however.
If you are looking for travisher alternatives, how about the travisher from Windsor Workshops (about the same price).
https://thewindsorworkshop.co.uk/travisher/
Any tips for using a No. 212 Small Scraping Plane?
I
I’m going to sound like an ass, but there is a reason that tool is so rare….
I don’t like scraper planes for my work. And I think there are few operations that really need them (marquetry and lutherie are two of them). A good card scraper handles 99.9 percent of my needs. If you really really need to scrape a large surface, the No. 80 is a better choice and SO much easier to set.
No worries, I appreciate the answer. I got one in a lot of tools and I am trying to figure it out.
I use a Lie-Nielsen 212 to clean up errant glue spots ie, glue that I wiped off but didn’t get it all and other such marks. The scraper is easy to set up. Set it on the bench, loosen the screw, press the blade lightly into the bench, and re-tighten the screw. It is really handy, plus it is so cute.
I’ve recently built a new top for my workbench. It’s 3″ thick and built from used construction grade 2x4s (pine, doug fir, etc). It’s all reclaimed wood that was destined for a landfill or bonfire. For me it turned out absolutely great and has exceeded my expectations but for one issue. I drilled (with a brace and bit) 3/4″ dog holes for 11/16″ holdfasts but the holdfasts do anything but hold (either fast or slow). They are 8″ long and were purchased from my local Woodcraft. My question is “is this issue a function of the lumber used to build the top or the quality of the holdfasts”?
Thanks,
BobE
It can be many things. Holdfasts work best when the fit is tight. I shoot for a hole that will barely allow the shaft in. A smooth shaft is bad. Holes that aren’t perfectly 90° are bad.
Try for a tighter hole. Rough up the shaft of the holdfast. Make sure the hole is dead 90°.
Tanx
Counter bore a little larger hole up from the bottom, in your existing holes. Maybe only an inch or so.
I had the same problem with those holdfasts and Tools for Working Wood gave me that same solution. Worked like magic.
Take some wet dry 150 sandpaper in a circular twisting motion around the shank. Those small grooves work wonders, and it removes any packing oils.
For 3/4 in. holdfasts, I don’t think you can beat the Gramercy holdfasts from Tools for Working Wood for price or hold. Scuffing up the shank works well as does tight hole.
You mention that the furniture is based off of farmers in the high carpathians. I keep wondering if you’re talking about dracula’s furniture…
Was dracula a farmer? Vlad the Impaler (of pumpkins)?
This furniture is of the oppressed.
So, more like the furniture of the people in the crowd waving torches and pitchforks at Dracula’s castle gates, then?!
Likely. All like extras in a movie.
Any progress on your small hammer?
We are waiting on the handles. They were supposed to be done last week, but….
Hey i wanted to ask about that, Lie Nielsen has a very similar set of hammers in brass and A2 steel.
Is there a difference in your warrington hammer vs theirs?
Last time I checked, Lie-Nielsen stopped making them. Ours are a different weight. Different handle (shape and species). Different detailing.
Cant wait until they come are on the market (internationally)
I will be building an exterior door (near Chicago, southern exposure), and will likely use siding stain to finish it. What would be a good option for wood species that will last well for outside and sun exposure?
White oak is great. Cypress (if you want to save money). Sapele or Utile or another African mahogany-like species (if you want to spend money).
Thank you very much.
Why do you use a tapered mortise and tenon joint for your legs vice a straight wedged tenon with a shoulder?
I use both. Vernacular chairs almost always use a cylindrical joint. And that is (to be honest) my preference. But the tapered joint is so much easier to teach, and to adjust, with students. You get about five chances to ream the hole to the correct angle.
With cylindrical mortises, there is no forgiveness.
What is the latest on Megan’ Dutch Tool Chest book?
It is scheduled for this year. Let’s hope Megan makes her deadline!
I have 3 young kids and space for all 4 of us to be working in the shop on separate projects simultaneously. I’m trying to fill out my kids’ tool chest and wondering if I should get a full (age appropriate) kit for each, or haveonly 1 (or perhaps 2) full kit(s) for them to share.
Wow. I have never had such a bounty of interest from my children.
Kids like to have their own stuff. My inclination would be to get them each a rule, square, block plane and a few other personal tools. Then have them share the stuff that isn’t used as much.
But maybe other readers here have better experience in this matter than I do.
Spokeshavea and a good vise.
I totally second that! It is such a fun tool (and useful).
There’s inexpensive small japanese saws that fit small hands, use these under supervision first (my 5 year old is close to being allowed using it alone again). Oh, and a small-ish hammer. Hammer nails into wood, tie wool around them for some abstract art.
A small brace (kukri?) is also great.
Have a great time in the shop!
If you could only chose one, would it be a bevel up low angle smoothing plane, or a bevel down no.4 smoother with a high angle (50,55) frog for tricky grain or tear out?
Neither. I use a No. 3. Stock frog. Chipbreaker set close for squirrely grain. It’s small, like the old wooden smoothers. which makes it fast to clean up panels. I find the No. 4 to be too big to be efficient. And the No. 2 is too small for my hands.
I am in the process of building an anarchist tool bench, currently building the top. Can you get away with having a piece with pith in the middle of the glue up? It will be a 5inch thick top made from 8/4 SYP and the pith would be about 1 inch from the bottom on a single board if that makes a difference.
The pith will likely split. The question is: how much. I have seen one example (out of thousands) where the benchtop split in two as a result. Probably won’t be a problem for you, however, because of the lamination and it’s 2x material.
But still, SYP is cheap. Get a better board.
Dave Fisher makes beautiful carved bowls and explains things clearly. I especially like his drawings for illustrating key processes. He really needs to write a book. I would buy the first one. It would be a shame if anyone but LAP published it. The quality of other publishers does not compare. A book about an American making bowls from found American wood needs to be published in America on quality paper, dammit! Chances of this happening before the decade is out?
We have talked to Dave about a book. He is not ready to write one. But we have agreed in principle to work together on it when he is ready.
I would love that book if it ever happens.
Me too.
Me three
Have you ever considered traveling to I don’t know, let’s say Boise Idaho to do a class at a Maker Shop? If you haven’t, you maybe should…
I traveled to teach for 15 years. For several years I was on the road 18 weeks each year. It is exhausting to travel, then work like hell and sleep like crap in an unfamiliar place. No matter how nice the destination is….
I make far more money teaching here. Plus I sleep in my own bed. Eat with my family.
I recently finished a stick chair made of red oak with Allback paint and I had a few places where the paint came off while I was applying wax (Liberon Black Bison in dark oak). I hand sanded the entire chair with 180 grit, wiped everything down with naphtha, applied a thin coat of Allback linseed oil the day before paint, I applied the paint with a brush as thin as I could and let it dry for five days before waxing. It was dry to the touch by day two. The places where the paint came off seemed random and no bigger then an inch square. Any idea what happened.
Wow. I do not. I would contact Sage Restorations, which distributes Allback in North America. Good guys.
Could the sandpaper have had some sort of coating applied to prevent the sandpaper clogging, that could gave gotten absorbed into the wood ?
This is a rookie technique question. I’m building a simple cherry dining table using hand tools. But I don’t know where “good enough” is for flatness of the five six-foot planks for the top. One is still bowed a little (about 1/4 inch), and two have some twist remaining (about 1/8 inch). But I don’t want to lose thickness if I don’t have to. These planks started out as 4/4 and are now about 3/4 as I continue to true them. I plan to use fir cauls during glue up. Is it likely that I’ll wind up with a wonky top if I don’t take these down to veneer-like thickness? (Frustrated exaggeration, of course)
Thank you for your advice!
It’s really hard to say without seeing the wood and the amount of bow.
A wonky top can be flattened to some degree with cross-grain battens below the top. So that’s an option if things got heck.
When I encounter this problem, I cut the boards into shorter lengths (reducing the wonk) and get some more wood. I don’t want to stare at my mistakes at every meal.
Is there a good reference on the correct way to construct a plinth? Specifically for the Monticello bookcase….I just can’t seem to visualize how the plinth interacts with the case
Plinths are typically a dovetailed frame with glue blocks in the corners. The carcase sits on the plinth and mitered moulding hides the gap.
Get the book “Illustrated Cabinetmaking” by Bill Hylton (it’s available cheap when used). It shows how every furniture form goes together. Very helpful.
Thoughts on using cherry wood for stick chairs? Thinking it’s strong enough, but just wanna confirm 🙂
I use cherry all the time. Straight, straight grain is very important.
I’ve been having issues when assembling the undercarriage in my last 2 chairs! I have tapered tenons, and an ‘h’ stretcher setup. After shaping the parts I dry fit legs and stretcher assembly. Everything looks good and tight. All parts are marked as to keep the same orientation. I disassemble, cut the kerfs, glue, and start assembling. After getting the stretchers on the legs, I get the legs in but when I am knocking them home, the opposite leg will pop out of its mortise. After pounding the crap out of the legs to no avail, I turned the seat upside down and clamped it to my bench to try to hold the tenon in place while I wedged it, which ultimately did not work very well. So now my leg is wedged in the tenon and not completely tight in the mortise. Any input/advice would be appreciated. Thanks
If it’s hide glue you used, you can reverse things.
When this happens, it usually means that a stretcher is slightly too long or the mortises for the stretcher are not in the same plane. When you add glue, it first acts as a lubricant and things slide. Then as it gels it will start to hold stuff in place.
If legs pop out during assembly, I just keep hitting them until the glue grabs. It can take 10 minutes of hiotting at times, depening on the glue and the temperature in the shop.
The DTC from the March class has decided it wants a chrome green linseed finish so I have some questions:
1. Not clear in various instructions: do or do not you need a primer of just oil? pros and cons? sounds like for the spell blocks you had 1 coat of paint followed by 1 coat of oil. I think I may not be clear when they are talking exterior house vs furniture.
How do you clean and store the brushes? There are some references to “linseed oil soap” which seems to be oil and water which doesn’t make sense. Like wise “storing (brushes) in oil”, either they have to be suspended somehow or the bristles get bent?
My biggest concern is cleanup, soap and water is so easy, especially if you are doing a small project as an experiment. My past experience is with a spit coat of linseed to pop grain, or over milk paint, both of which have involved disposable applicators which doesn’t seem like a fair test for a real paint job.
I did search on linseed oil on the blog, the vast majority of hits was Katy’s wax which I have made successfully, thank you for the recipe!
There are a number of both written sintructions and useful videos on painting with linseed oil paint available on the Ottosson website; for the latter either with subtitles in English or sometimes even with English speaker voice. While mainly concerned with larger uses than furniture (think: houses), they also cover indoors use on panelling, millwork and the like, both previously painted and bare wood, which of course is very similar to furniture.
As for a base coat or not, I have tried both just boiled linseed oil, a mix of 2/3 boiled linseed oil and 1/3 linseed oil paint, or straight paint with no base coat, and they all work. If you want to find out if it makes any difference noticeable to you, with the paint you intend to use, do a couple of test pieces first, and see what gives!
As for cleaning brushes with linseed oil soap, yup! It works an absolute treat! It is not oil and water, but saponified linseed oil, i.e. soap boiled up from linseed oil. I have only tried the Ottosson brand, and am extremely happy with it. I was told once by a brush maker (the people at the Gnesta Brush Works in Sweden) to make sure the linseed oil soap was not too strongly basic, i.e. not with a pH above +/- 10, as that would not be good for a natural bristle brush in the long run, but otherwise it is the cat’s Jim-jams for cleaning one’s linseed oil paint brushes.
It is also possible to store a brush in raw linseed oil between coats, without cleaning; I think you’ll find this possibility amply mentioned in the material linked to above.
I forgot to add that some of the instructions I linked to suggests adding (real) turpentine and/or a siccative to the paint. I have never done that, as I’m painting indoors and don’t want either the odours or the potential health issues; neither is necessary – they just improve absorption into the wood a little, and shorten drying times.
<<1. Not clear in various instructions: do or do not you need a primer of just oil? pros and cons? sounds like for the spell blocks you had 1 coat of paint followed by 1 coat of oil. I think I may not be clear when they are talking exterior house vs furniture.>>
A primer coat of oil seems to make the paint lay out nicer. We are still experimenting. Either is fine. If I have the time, I’ll put on a thin coat of oil the day before I paint.
The linseed oil soap is miraculous. Cleans up the brushes quickly and your hands. Then we store the brushes in their cardboard sleeves. For overnight storage (more painting the next day) I suspend them in oil in a cup. I make a thingy from a coat hanger to hold the brush up off the bottom of the cup.
<>
I highly recommend the linseed oil a soap. A little goes a long way.
Hi Chris, and thanks for doing this. I’m in the early stages of planning my new shop, a 12×16 shed (upgrading from a rather cramped 7×10 shed). I’m currently wrestling with how to floor it. The plans call for T&G OSB subflooring, but I’m thinking of using 5/4 pressure treated decking instead and either ship lapping it or making it T&G myself to keep things affordable but still have a decent floor. (Insulation will be going underneath whatever I use.) I’m in central Maryland so I do eventually plan to finish & insulate the whole interior, and add A/C (go go gadget dual-split). Am I heading down the right track with the decking idea, or is there some other flooring solution I should consider? FWIW I’m squarely in the hybrid camp vis-a-vis hand and power tools, mostly using benchtop power tools for stock prep. Thanks in advance to you & any readers who chime in.
I am not a fan of pressure-treated wood for anything. But especially not for interiors.
OSB is great, but looks like crap to my eye. My preference would be to either:
Put down the OSB as a subfloor and make T&G flooring from SYP 2x12s. Looks nice. Durable as heck.
Put down OSB and buy the “fell off a truck somewhere” solid wood T&G oak.
Thanks!
HomeRepot carries a 1 1/8 t&g plywood. Or 23/32 . My floors are plywood and I roll power tools over them all the time. They dent dropping tools or boards but it’s a shop. I coated mine with a water base urethane.
You should be able to get tongue and groove plywood sub flooring which is really tough stuff. It would probably look somewhat better than OSB but not as good as Chris’s suggestions—but cheaper.
I think you previously mentioned finishing some pieces with boiled linseed oil. However, when doing a search to find a suitable brand, I found some articles where they claim that linseed oil yellows over time and that the best produt to use for finishing is real tung oil To make things more confusing there also seems be polymerized linseed oil. What is your opinion please? Thank you.
“Boiled linseed oil” is not boiled. It has heavy metal driers in it. Yes, it yellows over time, which is lovely and looks like old furniture.
Tung oil is fine. Be wary because some tung oil is not tung oil. It is something else entirely with varnish.
“Polymerized linseed oil” is likely (but check the SDS) oil that has been heated so it will dry faster. It also yellows wood over time.
Any are a fine furniture finish. I use linseed because I like it and it fits my Western furniture tradition.
A woodworking ethics question. I am making a stair rail in my timberframe shop. It will have lots of frame and panels. Stylistically with the timber frame, I want pegged mortise and tenon joints. As a woodworker who wants this job done, I want dominos. In your opinion, would pegs in the domino’ed frame just for looks be unethical? No one would know but you and me.
I have no problem pegging Dominos. That’s how the Greeks built boats – pegged loose tenons.
Good Afternoon Chris!
I learned woodworking from my Dad, and architect and skilled carpenter. We only had wire nails. I found the straight side of these nails worked quite well. To take apart nailed boards we would hammer along the length of the nail. It would take many blows to separate the boards because the nails would grip along the length of the nail. Or, after a few blows we could hit the boards back together. This allowed the nail head to protrude enough to allow us to pull the nail out using a claw hammer. The lever action of the claw hammer was needed; it was not possible to pull the nail out by hand. In use, such as in a fence, some (not too many) nails would loosen due to the forces of nature over the years. We would hammer these nails back down, re-paint the fence and then it would be good to go for several more years. The only time this would not work was if the wood had rotted. This, however, is not a problem with the nail. To solve this problem, we could clench these nails. It was not pretty, but it worked. Also, we would drive the nails in at different angles. Then, forces that would loosen one nail would be resisted by another nail driven at a different angle.
When I read about nails in The Anarchist Design Book, I was puzzled by your preferring nails that are wedge shaped. A wedge-shaped nail would produce a wedge-shaped hole. To my mind, once the grip of the nail is broken, the wedge-shaped hole would not hold the nail and it would just fall out. This wedge-shape appears to me to be a liability and not an asset. I am getting ready to build the Boarded Low Bench, Chapter 21 in The Anarchist Design Book. The blacksmith-made Roman nails I ordered arrived yesterday from France. I must admit, these are the most gorgeous nails I have ever seen. So, here is my question. What am I missing? Where is my analysis going wrong? What can I expect to find when I build this bench?
I don’t mean to be glib, but try them. The wedging action is impressive. I have have had backboards get destroyed before the nail came out. Just practice first on some scrap with different pilot holes – depth and diameter.
The lath on the ceilings of my 1887 house hold up thousands of pounds of horsehair plaster. And the lath is attached with ludicrously small looking 3 penny nails. Cut nails are awesomely strong.
My workshop area is in a basement with two 90 degree turns in the stairwell. Is it possible to make a Anarchist Workbench where the top is removable/semi-removable, or do I need to plan on sawing off the bench top at the tenons when we eventually move?
Sure. Run lag screws through the tenons instead of pegs. No glue.
Should I be making the tenons any larger to accommodate the screw holes or just build it as per the book and sub the lag screws for pegs on a 1-to-1 basis?
I think the tenons are big enough. But no harm in making them bigger.
Acknowledged, thank you!
While building the six stick comb back, from the stick chair journal,
I decided to drill the mortises for the sticks all the way thru the seat,
and wedge them from below.
What changes do you recommend to the order of operations during the glue up,
that is described in the journal?
Specifically, I’m wondering how best to manage the short sticks and arm assembly during the glue up.
Since the mortises in the seat are now open, filling them with glue and inserting the arm and stick assembly may not to be the best choice.
Thanks,
Mark
I don’t change anything about assembly when I drill through the seat except taping over the mortises so the glue doesn’t explode everywhere. The sticks should be tight in the mortises, so it’s just like assembling a chair with blind joints.
Thanks Chris! You’ve mentioned that your American Peasant work is going to have a lot of tongue and groove boards in the furniture, so you’re using a T+G plane a lot (maybe the Stanley 48?) Can we hope to hear about user-made alternatives, for peasants who are more interested in making something to fit their needs than spend the time looking for a survivor or the money on a new equivalent? I’m inspired by eg Paul Sellers and Rex Krueger with shop-built router, plow, and rabbet planes.
There are lots of Stanley 48s out there. And wooden match planes. Making your own is pretty simple stuff. But the 48 is so versatile and easy to use (and common) that I’m not inspired to build my own (at this point).
I have a Lee valley standard taper reamer and regardless of whether I use it in a brace, drill, or drill press I almost always end up with an oval hole.
What am I doing wrong?
And follow up question, Andy thoughts on what can be done to fix an oval hole other than tossing the seat in the fire and making a new one?
You can try to plug it and cut a new mortise. You can try a bigger wedge. If the joint is sound, you can fill with putty (we use Durhams Water Putty) and paint the chair.
Is it truly oval or does look oval? A compound-angle tapered mortise presents as an ellipse on a bisecting plane.
Truly oval holes are cause by a lack of control – of the reamer or the work. Usually students are working too fast when this happens. Stead and slow wins the… hole?
Truly oval when the tenon goes in.
Thanks, ill try going slower!
I split a (tapered) tenon while wedging a leg in my first stick chair. The split goes down about 2 inches below the seat. Seems to me that the taper prevents the split from becoming a problem. Is this wishful thinking? I’ve been using the chair just fine for the past month. Ignore, reinforce (how?), or replace?
I’d watch it. If the split lengthens, replace the leg because disaster is ahead.
Can you describe a hand tool method to create a shouldered tapered tenon with the Veritas tapered tenon cutter on the top of an octagonal leg. FYI moderate skill level and no lathe available.
I do this all the time. Taper the leg so it is a 1″ octagon at the top.
Put a 5/8″ diameter circle on the tip of the leg, centered. I use a 5/8″ Forstner pounded into the end.
Mark a line around the leg 6″ from the top. Use a jack plane to taper-plane the top of the leg down to the 5/8″ target. Three strokes per facet. Don’t cross the 6″ pencil line.
Then round over the facets with a block plane.
Put the tenon into the tenon cutter and shave it. If it stops cutting too soon, press the tenon hard into the cutter. That will burnish the high spots that need to be removed.
I was hoping to avoid the 6” taper in favor of a shoulder. Seems unlikely to me absent a lathe hence the question.
I have bench chisels with a 30 degree bevel. Can I use those for dovetails or do those have to be chisels with bevels on the order of 20/25 degrees? Thank you.
30° is a great angle for chopping. Don’t change ’em.
Hi Chris,
I too had Titebond Liquid Hide glue fail about 3 or 4 years ago. Had a well glued with two boards edge glued together fracture along the glue line. Took me about two years before I tried that glue again.
Curious about Old Brown Glue. What I like about Titebond Liquid Hide glue is the longer open time relative to Titebond 3. QUESTION: How does Old Brown Glues open time compare to Titebond Liquid Hide glue? I’ve got a huge carcass full of dovetails (bigger than ATC) I need to glue up. Debating to switch to Old Brown glue or keep with Titebond LHG. Really depends on the open times as for this project I really need it?
Thanks.
Joe
I get about 30 minutes of open time with Old Brown Glue. It’s the best furniture glue I know of.
Thanks Chris.
When sharpening chisel and plane irons,with and without jigs they end up skewed. Any suggestions? How much pressure is used when honning on diamond plates or stones? Thanks for your time.
You need fairly firm pressure. But nothing extreme. If the abrasive is cutting and the tool is under control, you are good.
I love my honing guide and feel no shame in using it. Paul Sellers and Rob Cosman can give you instructions on sharpening without the jigs.
Hi Chris!
Like you, I’m a big history buff and after reading years of your posts, I’ve now found myself looking for work benches and maker’s marks in old cathedrals, castles and monasteries.
I ran across this article recently and thought you might find it interesting. Researchers have found French Oak in the Holy Land. Thanks to modern technology, they’ve believe the Oak trees were felled between 40 and 60 CE, almost 2,000 years ago. They also speculate on how it was transported and include a map.
The world was more connected than I realized, very interesting.
Cheers!
Paul
And…. Now including the link! Whoops!
https://www.biblicalarchaeology.org/daily/ancient-cultures/ancient-rome/in-jesus-time-the-ancient-art-of-the-deal/
I look forward to reading that after I type my fingers off today.
More of a comment than a question… On a lark I asked ChatGPT how to build a Roubo wb. It gave me a slew of historical and technical info and finished up with:
“Roubo’s workbench design was not widely known outside of France until it was translated into English by Christopher Schwarz in the early 2000s. Schwarz, a woodworking author and editor, wrote about the Roubo workbench in his popular book “Workbenches: From Design & Theory to Construction & Use,” and he has since become one of the most well-known advocates of the Roubo workbench design. Today, the Roubo workbench is a popular choice among woodworkers who value its sturdy construction and versatility.”
Next time you’re playing around with that AI, ask it to write a story about a curious monkey named George, in a museum, who’s good at making trouble. What it spits out will be just like the pap you read to your kids when they were young, except maybe the Mayor won’t show up to give him a medal at the end. That’ll give you a good sense of how those things are working these days, for better or for worse. (Now, the future, on the other hand, might be a whole different trouble-making monkey.)
Hilarious. I didn’t translate Roubo. But OK.
I notice that, aside from imported woods like bog oak, you use mostly walnut and cherry for your chairs, but I haven’t seen much maple. Is this a preference due to strength and workability or aesthetics? (I’m trying to decide on what wood to use based on what I can get locally in Washington state, where big-leaf maple is abundant.)
I love maple. It is one of my favorite woods. I have made many chairs with it. Here the problem is finding a supply of straight stock. The stuff at our yard just isn’t straight enough for my tastes.
It is getting harder to find straight stock, of any species. Big Leaf, here I come! Thank you for taking time to day to answer all our questions.
Do you think a soap or soft wax finish would be a good fit for an interior oak stair handrail? I remember you mentioned having a soap finish on your desktop and loving it. It seems a desktop would get more abuse than a handrail but maybe not as much direct hand contact.
Soap is not durable. I probably would choose soft wax. It will get better with people’s touch – moreso than soap.
Hello Chris,
What other pocket knives do you carry often. Is the Sebenza your favorite knife and your daily carry? I cannot tell from the picture if it is a small or a large. Looking for any additional insight into your pocket knife/knives. Thanks!
It’s the small one. The Sebenza is my favorite. Light. Well-made. Worth the price.
I like Kershaws for beaters and loaners. I have a Benchmade that I also love but is bulky.
I have a knife on every horizontal surface in our shop…. but I’m not terribly knowledgeable about them.
Re: making wooden screws. You used to recommend soaking the dowels overnight in BLO before cutting the threads. By “soak,” did you mean completely submerged? As in find a suitable container and fill with oil and dowels? Or just apply a heavy coat and leave it be? Maybe wrapped in plastic wrap?
I also recall someone (Jennie Alexander?) recommending a wipe down of mutton tallow rather than a soak in oil. Have you tried the tallow? Do you have a preference for one over the other?
Some people soak theirs overnight in the oil. I just apply a good coat before I cut – as a lubricant.
The tallow is fine. (As is Crisco.) But I have tons of linseed oil here and not many sheep.
Have you tried the Anarchist’s Bandsaw Adjustment Method by Alex Snodgrass? Fast, no measurements, and makes even crappy bandsaws like my California welded 14 incher saw wood like a 16th century Frenchman ;-). https://www.youtube.com/watch?v=bxVyKsbuwZQ
Some good tips there. Michel Fortune’s video at FWW has the additional step of aligning the table to the blade. This made a noticeable improvement.
I love my band saws.
I do not remember the why for your fascination of the Eastern European Spell carving. Care to illuminate us?
Is this furniture heading for your Daughter’s apartment?
It’s one of the many corners of the furniture world that I am fascinated by. I see my job as finding things like this, and bringing them to light for others to enjoy and build. And to spur more research. Plus, I like to remind people that our furniture history didn’t begin with the Shakers (love ’em though I do).
There are so many cultures that have furniture forms that are ignored by the West and modern people. Plus, I have some Eastern European blood, so I feel an affinity for these pieces.
The furniture built for the book will be photographed and sold. I gotta eat, and working on this book has cut into my income.
Hi Chris,
Any thoughts on how to prevent blowout when drilling through a turned leg (in my case a through mortise for a stretcher)? If it was square I could just clamp wood to the back but what for a round piece?
Much appreciated!
Traditional approach: Use a bit with a long lead tip. When the lead tip emerges from the other side, stop drilling. Finish the hole from the other side.
New approach. There are a lot of new drill bits that can drill through holes without splintering on the exit would. the Star-M bits from WoodOwl are one brand.
Not sure if we’re still under 100 questions but I can try again next month. Any updates on the Dutch tool chest book?
It is still scheduled for the fall. Megan works on it at night. I haven’t seen the thing yet.
Hey Chris,
Planning on building a stick chair in the next few months. Given it is my first time I’m entirely expecting to have to service it down the road but wondering about disassembling wedged components. What’s the best way to remove a wedge and dissemble a joint (put together with hide glue) while avoiding marring the surface enough it becomes a painted chair?
Thanks,
Ryan
Heat and moisture loosen the glue. I drill a small hole or two in the wedge and jam my scratch awl in there and try to pluck it/lever it out. Usually works.
When learning dovetails is it ok to rely on aids such as (for example) the K-M magnetic dovetail guide or does that create bad habits? Thank you.
Those guides are great. Use them to get a feel for the process. Then decide if you want more flexibility (in slope) or not. Some people use them their entire careers. (They have been around a long time.)
Can you recommend any woodworking classes/schools on the west coast? I know of the Krenov school, but their options seem limited these days. Thanks!
If you are in SoCal, there are a few I know about: lawoodshop.com, communitywoodshopla.com, and alliedwoodshop.com. These all offer intro/intermediate level classes. Somewhere in WA is the Port Townsend school of Woodworking. I recommend grabbing a copy of woodworkers west at your local Rockler or Woodcraft, these and others advertise there.
The Port Townsend School of Woodworking is located in the Fort Worden area of Port Townsend on the NE corner of the Olympic Peninsula. If you attend the PTSW for any classes (which I also highly recommend), plan to stay 2-3 days more just to take in the local scenery!
There is also Palomar College in San Diego, which has a variety of courses that you can take individually.
The California Community Colleges have many programs….. Some of the State Colleges as well.
Generally cheap, well equipped and provide an excellent education. I went to teh Cerritos College program myself. It is really superb.
The other commenters are doing a better job than I could!
You’ve mentioned a preference for the 1/2″ Woodslicer blade on the bandsaw. Are you using that exclusively for stick chairs or are you using something smaller for things like the details on the arm bow?
We use it for everything. It’s the only size we use. (We don’t do scrollwork with the band saw; we use a coping saw or fretsaw for that.)
Chris and Megan, no obscenities, complaints or wise crack questions here (well maybe that was smarty pants-ish). Just praise and appreciation for your teachings, perspectives, great books and tools. As a beginner on this woodworking journey, you have been inspiring and a valuable resource, especially the Anarchist series. Thank you. Dave
Thank you!
I’ve followed your chair making for a bit of time now but I have never had the opportunity to sit in a high back stick chair. You mention the Gibson and Lowback are your two most comfortable chairs. What is the advantage or use of a higher back stick chair?
The Gibson is a high-backed chair. It just doesn’t look that way.
Any chair can be comfortable. My comb-backs are comfortable. But my lowback and Gibson chairs are just a little more comfortable. It’s not the form – it’s the woodworker who made it. I am constantly tweaking my designs to improve comfort, strength and looks. It is a never-ending process (for me, at least).
Thanks for this. Quick drawboring question: is a 3/8” diameter pin/peg appropriate for a tenon that is 1.25” long, 3/8” thick, and 1.5” wide? And does the pin need to be a different species? I’m considering cherry for all parts of this project, and one pin in each tenon.
I like to use a tough species for the peg. Oak that has been rived out is my favorite. I would use a 1/4″ or 3/8″ peg in that joint. With a 1/16″ offset.
Thank you for making this Q&A available – it’s very generous of you. A few questions:
I built the boarded bookshelf from the ADB. Do you have any recomendations for finishing the surfaces of the shelves? Or do you leave them bare?
Do you have a recommendation on books relating to Scandinavian vernacuar furniture? Everything I have found seems to be somehow related to Danish Modern – nice, but not what I’m looking for.
Thinking purely about longevity and durability, is there any practical difference between the boarded furniture you present in the ADB (for example) and furniture held together by more complex joinery (Shaker furniture, for example)? At what point, if ever, does one form begin to outlast the other?
Thank you for your time.
<>
I prefer bare shelves. It’s better for the books (in my opinion).
<>
There are many. But not in English. I started my journey with “Danske Bondemobler” by Axel Steensberg. I bet some of Scandinavian readers would have a better list.
<>
Good nailed furniture and joined furniture can last for centuries. So I don’t go by durability. Instead, what is appropriate for the piece? A six-board chest should be nailed. A joint stool should be joined. Somethings need dovetails (drawers especially). But don’t worry too much about it. Do your best with what you have. As you get deeper into the craft, your tastes in joinery and fasteners will be come complex.
I received a Stanley 12-960 low angle block plane for free. It is in like new shape but is a cheap as they come. I have lapped the sole and sides and tuned up the rough spots including the iron it works fairly well but fails to fully participate in the program. Would it be worth it to invest in a new iron, a Hock or something similar? Can I make a silk purse or should I just buy a new pair of wool socks and be done with it?
Well you did not over-pay….
I really dislike these tools. They are built to a low standard. And the contact between the iron and body is poor. Keep it for carpentry. Save your pennies for a good vintage block or one from Lie-Nielsen or Veritas.
When putting the bead profile on the tongue and groove backboards of the boarded bookcase from ADB, what size beading plane do you prefer? Thanks!
I like 3/16″ for furniture. It doesn’t insist upon itself.
Howdy!
1) With expanded distribution will LAP/Crucible products become more available to Canadians?
2) Many other modern woodworking public figures have embraced Youtube. You seem to mostly avoid it. Having read your books I can infer why but was curious what your say would be.
Thanks so much. Your work has meant a lot to me.
Lee Valley carries almost all of our products. We cannot ship overseas without losing money. We’ve tried different systems on two occasions. And neither worked. When we get to a certain size, we might be able to open a distribution house in Canada. For stuff Lee Valley carries, my recommendation would be to try a mail forwarding service. They are reasonable and reliable.
We have eschewed video up until recently because we LOVE books. We know that will have to change. So soon I’ll be making epoxy resin tables with bullets encased in them on YouTube. And hawking magic rags. The following is mostly untrue, but we will be on YouTube more.
Do you mean Viemo (sp) or YouTube? Seems like you prefer Viemo and I’m guessing there is a reason for that. Curious if there is.
We use Vimeo to serve video because it is commercial-free. And Vimeo is the backbone of how we sell videos through our store.
We also use YouTube fore some things. And will be using it more in the coming months.
Hi Chris,
Speaking of books, Don Williams any closer to getting his finishing book done? Any other books on finishing in the works? I really like historical finishes and am trying to learn all I can.
Sincerely,
Joe
I do not have any new information on Don’s book. Last I heard he was working on more Roubo volumes.
Thanks. I know he has a lot of pokers in the fire as it were. I’ve purchased his videos on finishing, read the articles, even downloaded the shellac Ph.D. dissertations. Just need to take his in person class.
Hi Chris.
I recently purchased the crucible scraper, here at Lee Valley in British Columbia.
Worked great right out of the envelope. I burnished one edge and I’m getting those fine thin curled shavings from it. It’s quickly be coming the go to scraper.
I’m also interested in the coffee mugs and beer steins but Lee Valley doesn’t carry them.
Any one in Canada carry them.
Best regards.
No. But you can use a mail-forwarding service (lots of Canadians do) for a small fee.
Or come visit. Kentuckians are friendly!
That certainly sounds inviting! But probably a year or two away.
In the meantime ( interesting combination, mean and time), I’ll check out the mail forwarding service option.
Best regards.
How is this coffer related to shepherding?
Shepherds used it to store shepherd stuff in it.
Chris,
Thanks for doing this weekly blog.
A friend that lives in Western KY had to have a large oak taken down. He has had it miles and kiln dried and now has it stacked in a barn with spacers between the boards and layers. I have suggested that he may want to consider sealing the ends to help prevent warp, checking or splits. What would you suggest he use? He has offered some to me to build a low back stick chair from the Stick Chair book. I won’t be able to get to the project until August or later in the fall. Any advice would be welcome.
Thanks
Tom
Anchorseal is the good stuff. If he doesn’t want to pay for that, latex paint does a good job. Sealing the ends and good air circulation are the key!
Hello,
I am planning an exterior door using White Oak. The plan is to use mortise and tenon construction. I was planning to use a plunge router for the mortises. Considering the stiles will be 5″ wide the suggestion is to make the mortises 2/3 of the width of the stile. This would put the mortise over 3″ deep. Any suggestion as to a method to accomplish this. I wanted to use uncut spiral bit but it appears I can only find these bits with a maximum depth of cut of 2 1/2″.
You can finish the bottom of the mortise with a Forstner bit in a drill press. The mortise doesn’t have to be pretty….
I’m at Keeneland with my wife, away from the kids for the first time ever. Anything cool to see in Lexington while I’m here?
If your into horse racing, and your staying overnight, breakfast at the backside cafe, it is open to the public and well worth the time.
I haven’t lived in Lexington since 1995…. So I’m a tourist when I go there. Lots of good restaurants downtown. The West 6th Brewing is a cool place (with lots of other little restaurants around it). The Kentucky Horse Park is cool. But sheesh — so many horses. The Henry Clay estate is a beautiful building with lots of impressive high-style furniture.