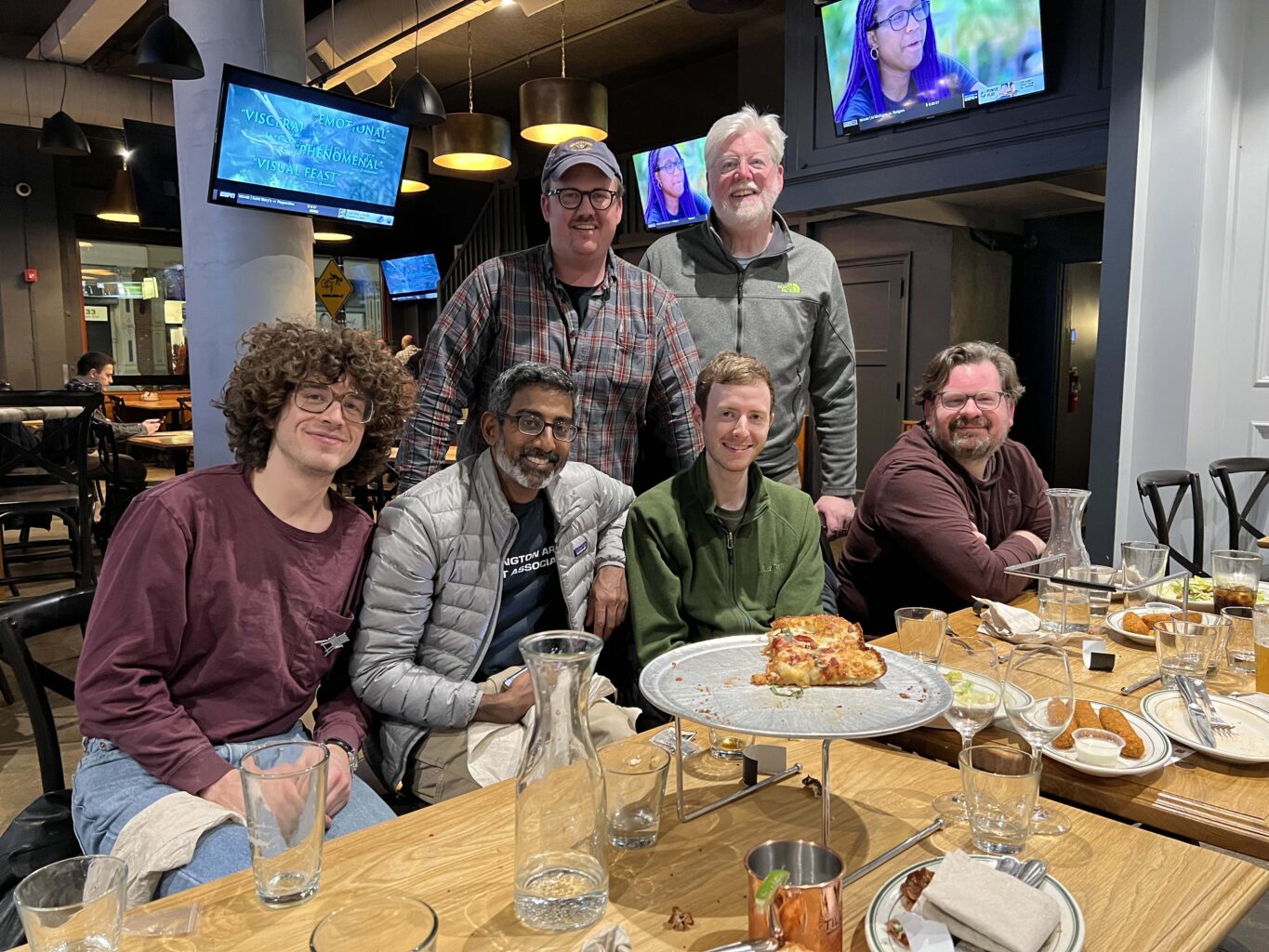
Sometimes students ask what they can do to prepare for a class in handwork at our storefront. In the past, I’ve told students to sharpen their tools and try to read up on the project or the topic we’re covering in the class.
But I don’t think that’s enough. I’ve been teaching woodworking for almost 20 years, and I’ve watched students who succeed versus those who struggle. Here are some suggestions to consider if you have a class coming up with us or any other hand-tool instructor.
Get in Shape a Bit
This recommendation is for hand-tool classes only. When I have taught machine-based classes, it’s not as much of a factor. During a week-long handwork class, a fair number of people are exhausted by Wednesday evening. And the last two days are difficult – sometimes uncomfortable.
Though we emphasize conserving your energy and show ways to sit down while you work (Roman-style), students are on their feet a lot. If you are a mouse-worker in an office, standing for eight hours in a day can wear you out.
So, wear the most comfortable, lightweight shoes you own (fashion is a low priority here). Plus clothes that move easily (gusseted pants and shirts work with you; not against you). And to prepare for the standing, we recommend getting in decent cardio-vascular shape. That is as easy as taking a 30-40 minute walk each day. This will work wonders for your ability to stand at the bench for the long hours.
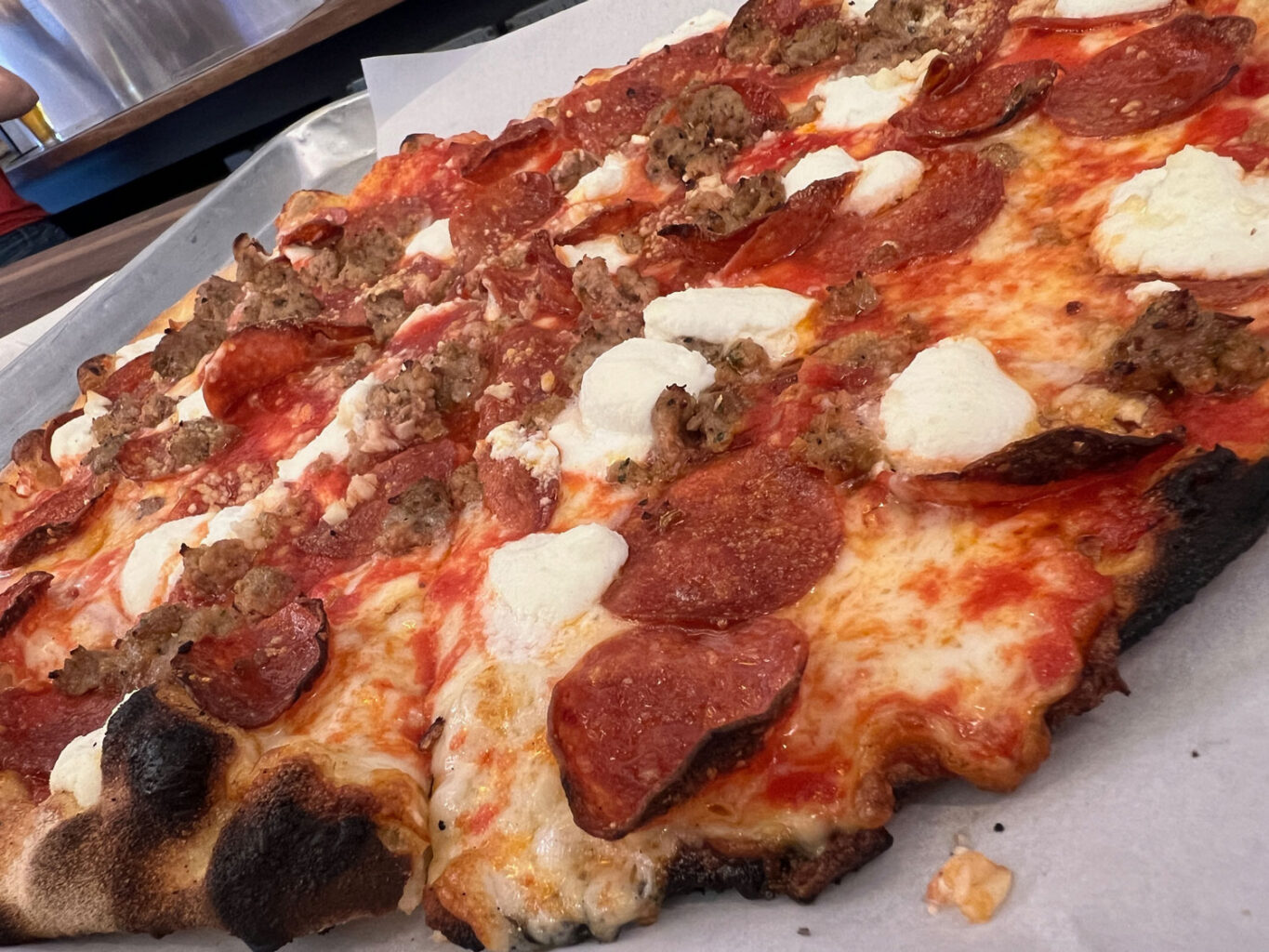
Diet
Forget your weight-loss diet during the class. You need energy. We have a lot of students who skip breakfast and/or lunch and are absolutely spent by 3 p.m. You need protein and carbs to do the work. It doesn’t have to be junk food. But you need to eat.
Upper Body
We emphasize using your core as much as possible in handwork. But your arms need to be in decent shape to assist with planing and sawing tasks. The best exercise for this is – shocking – planing and sawing. (More on this in a moment.) But if you can’t practice in the shop, try some beginning strength training. You can find many simple tutorials on the internet for this.
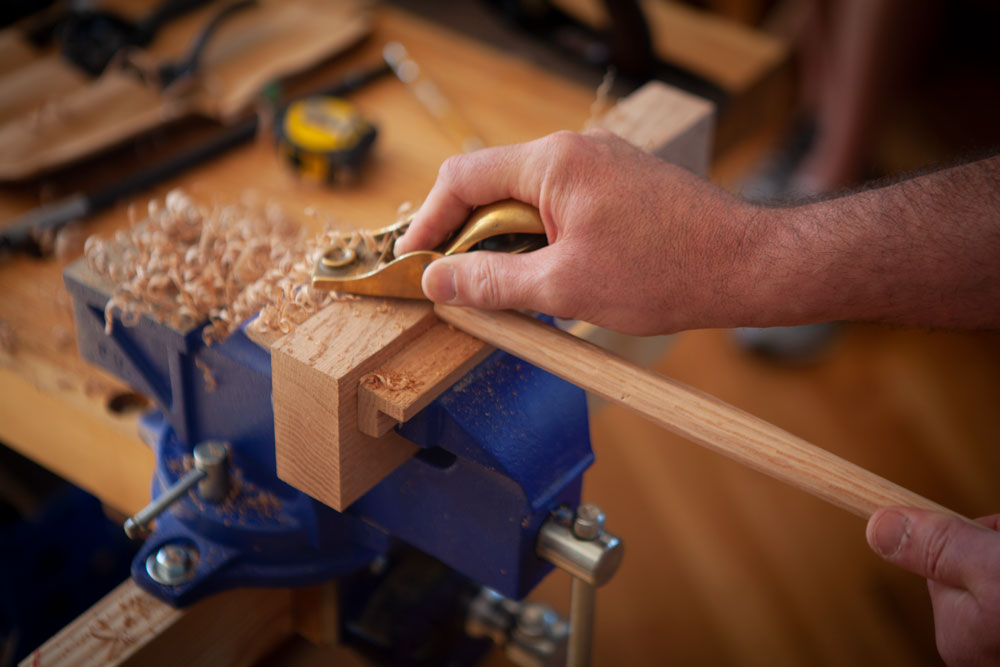
Practical Practice
Depending on the class you are taking, I recommend some different exercises to try in the week leading up to the class. If you are taking a class on chairmaking or staked furniture, there is a lot of planing. I mean, a LOT of planing.
There is a point at which you learn how to “ride the bevel” of a coarse tool, which greatly reduces the effort required to plane a stick or taper a leg. This is not something you can teach through words. It’s something you have to figure out yourself.
When smooth planing or jointing work, there is a lot of downward pressure required to end up with straight edges and flat boards. With chairmaking the goal is to use minimal downward pressure because you might take 60 or 70 strokes to shape a spindle. So you have to feel where the cutting edge of the tool is, put it to work and try to get the sole out of the equation as much as possible.
Scratching your head? Here’s how to start the process of finding that magic moment.
Take a 3/4” x 3/4” x ~15” stick of straight-grained hardwood. Place a small stop in your face vise. Press the end of the stick against the stop with your off hand. Plane the stick with a block plane set for a rank cut.
Try to make the stick into a dowel. After it’s round, use taper cuts to make it into a magic wand with a pointy tip as quickly as you can. Plane fast. Skew the tool. Try to find a place where the cutting edge is the only thing contacting the work. (It’s not possible, but it’s the goal.)
Do a stick like this each night for a week before class, and you will ace my class.
Also, learn how a cordless drill works – especially the clutch and speed settings and how they interact with the torque of the drill.
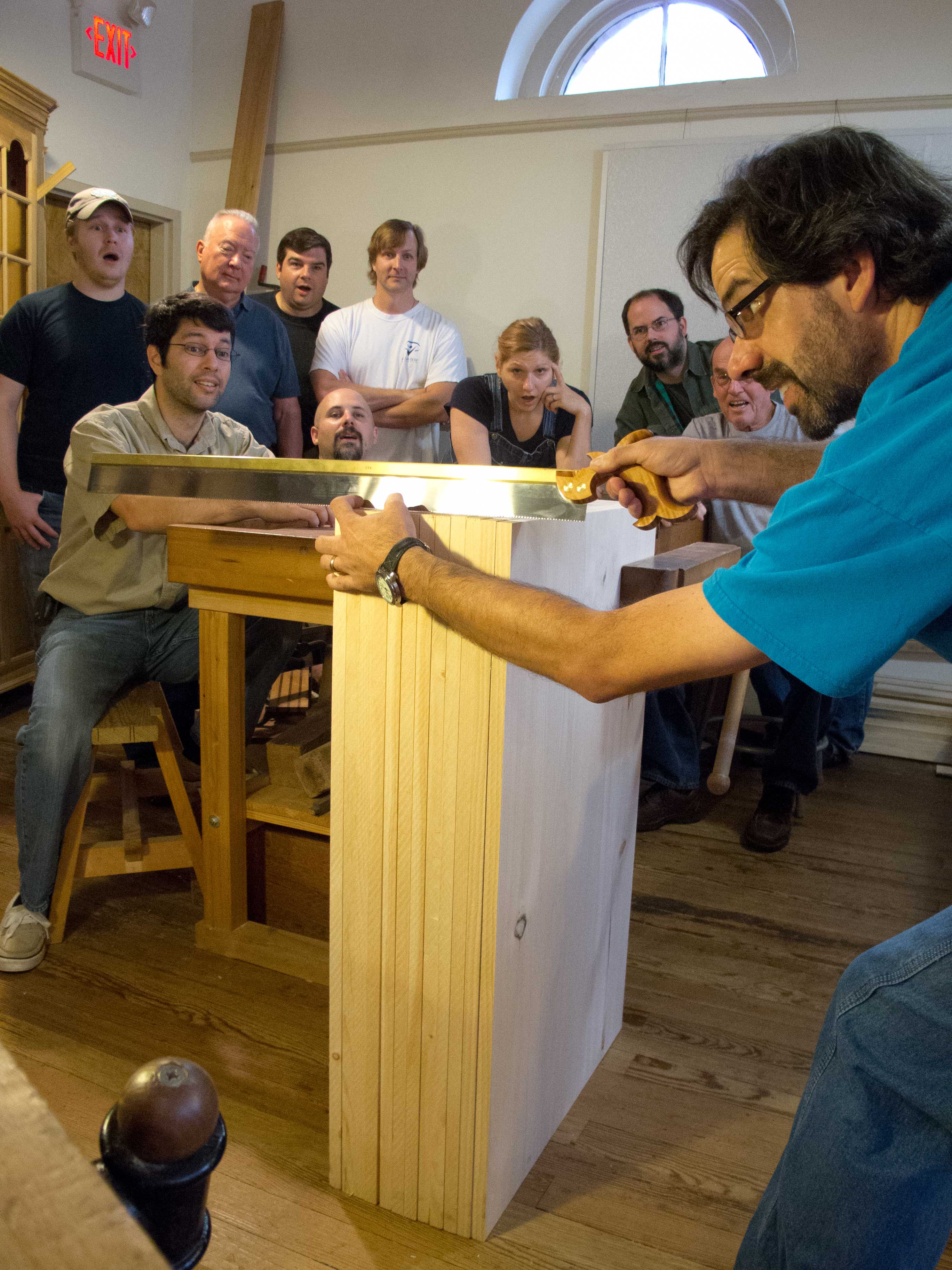
Saw to Success
Megan’s classes on casework joinery involve a lot of sawing and chopping. Most people seem to struggle with the sawing. Frank Klausz had a straightforward solution to prepare a student to cut dovetails for the first time: 100 lines.
Draw 50 lines that slope to the right (like one side of a dovetail) across the end of the board. Scribe in a 3/4” baseline. Then saw right next to those 50 lines, one after the other. Try to do each one a little better and faster. When done, saw off all those kerfs. Now draw 50 lines the slope to the left, put in a baseline and saw those.
This accomplishes a few things, some of them not obvious.
First, beginners usually own a new saw with freshly filed teeth. These teeth are grabby and difficult to start. About 100 kerfs helps break in the saw.
Many beginners have difficulty starting the kerf. Doing 100 lines one after the other rapidly (it takes less than an hour) teaches you to take the weight of the saw off the teeth when starting. I like to tell students that they should almost hover the teeth over the wood as they begin to push forward.
And the 100 kerfs help you fall into a comfortable sawing stance. Figuring out where your feet should be, how your sawing arm should swing free and that the work should be level to your elbow. Oh and stop trying to choke the saw to death (not a euphemism).
I’m sure I could come up with more exercises, but I’d worry that I’d scare you off. But these simple things will definitely make your week (or weekend) here a lot more rewarding.
— Christopher Schwarz
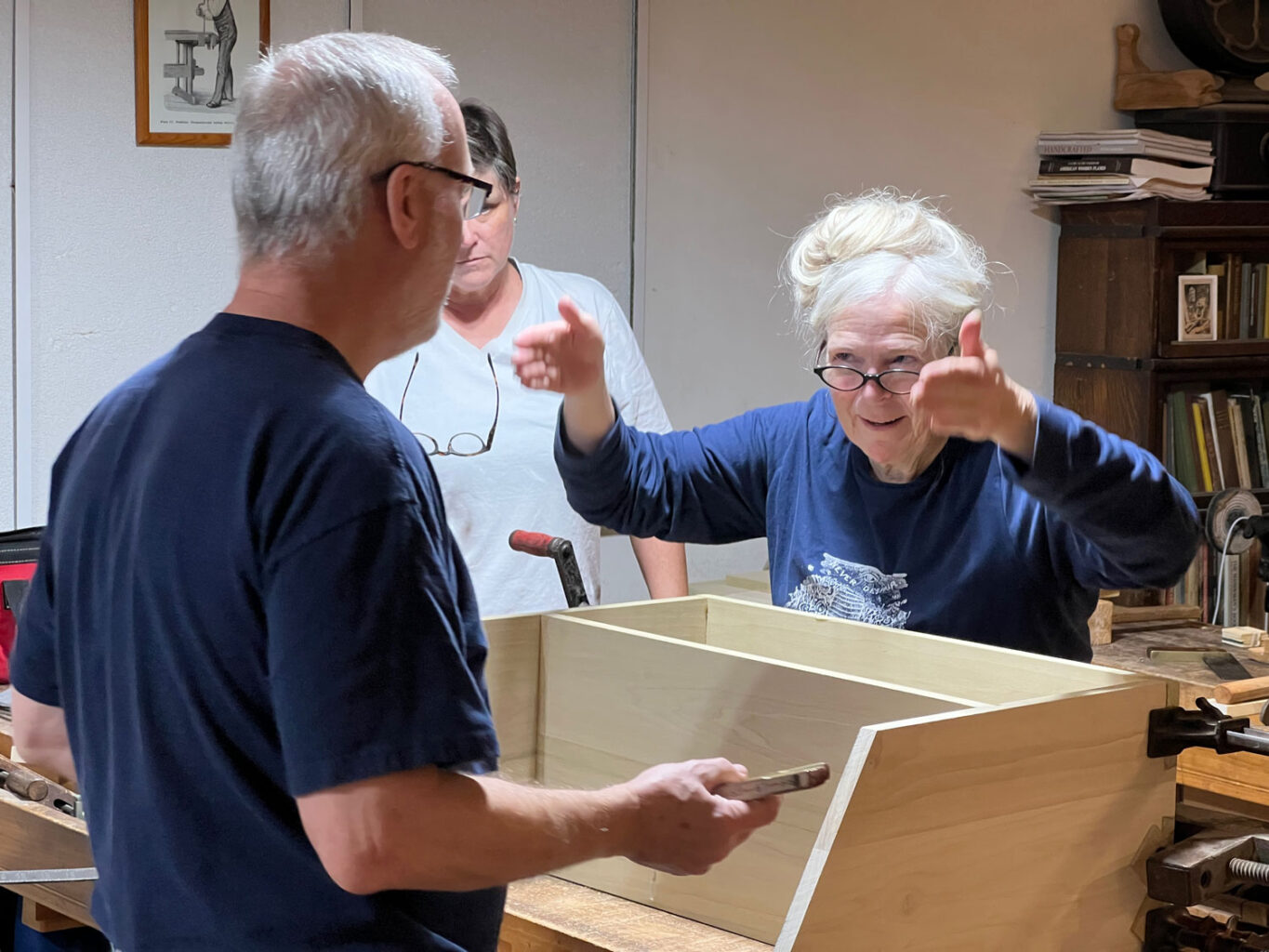
What saw is this? How long?
That’s a custom saw Lie-Nielsen made for Roy Underhill, if I recall correctly
My, that is one LONG dovetail saw! I doubt Frank Klausz meant that saw as the means to 100 cuts through a stack of boards! (10 cuts w/ 10 boards.)
And shop clothing- never, ever wear fleece in the workshop. Fleece and wood dust/chips/shavings are one step removed from Velcro parts A and B. Cotton tee shirts, twill shirts and pants, same with denim, all brush off or vacuum off easily with a shop vac. Soft and fuzzy stuff- no.
What ? That would mean no cats🙀🙀🙀
This is great. Making your first ever cuts for a project on the actual wood you’re using for it seems foolhardy. I love this idea of repetition to learn a technique. Wish there was an obvious one for mortise and tenon joints. I mean apart from just cutting a crap load of mortise and tenon joints on throwaway wood. I’m not sure what else one could do but it’s clearly important to learn a technique before applying it in earnest on your expensive stock.
Did I get “eye to hand coordination” and “muscle memory” in this message?
I don’t know what I like best about this post, the practical advice or the pic of that pizza. Actually I do know. It’s the pizza pic. Man that looks delicious.
That is from Bircus down the street. Good stuff.
https://bircus.com/
very good stuff. When you think you got it, do it 50 more times.
I am very embarrassed reading this this to realize that I should have been shaving with a block plane. I’ve been using a smoothing plane like a chump
Here here! These observations you’ve set concerning the storefront classes are worth a read for every woodworker emerging from winter. I hope this blog post at least also helps scratch that itch in all of us; that is an inventory of all the other minutiae we do each and every day regarding what we eat, exercise, preparation for the day, and our proficiency (or lack of these considerations). Even the person who works a 50 hour job and with excitement carves out 2 hours one evening or a full Saturday to labor in their shop; this blog post is for you. Imagine that Saturday rolls around and not beginning it with a low sugar/high protein breakfast; instead you pop a few donuts down the old ‘pie-hole’ and by 11 am your crashing and the blah feeling steps in to occupy that excitement you had at 8 am. I’m just saying that diet, clothing, exercise, and sawyer calisthenics are considerations worthy of consideration for all of us.
-B
The real question is how much of a discount did you give to the students to look at you in awe during that picture?! Pizza sure sounds good tonight………..
How do I find out what “a block plane set for a rank cut” means?
How do I find out what “a block plane set for a rank cut” means?
“Rank” means “heavy.” Take a thick shaving.
Thank you.
Now you tell me! (Just finished the Dutch tool chest with Megan. I will say that I expected the feet to get sore ando was not shamed for sitting down for 5 minutes periodically. Being the oldest by more than a decade does have some advantages.
Sounds like you’ve had quite a bit of negative recent student experiences.
Not at all, anonymous!
We are just trying to make people’s experience here even better.
I was thinking of attending a woodworking class ( sorry not yours) but after hearing about how rigorous they are I have figured it would be a bad idea for me. The money I would save not going; cost of the class, food, transportation and lodging I could buy all the wood I wanted even if 50% was scrap. Now I walk three miles a day and I’m very active but I’m not able to do 8 hours standing and working in a shop. Especially if I’m using only hand tools! I guess once you get into your late 60s early 70s you’d better stick to pickle ball!
Hi Tom, I am not trying to be discouraging. We have many students in their 70s who kick the butts of the 20-year-olds. It’s all about being ready.
As Tony Robbins said, “…necessity might be the mother of invention but it is repetition that’s the mother of skill.”