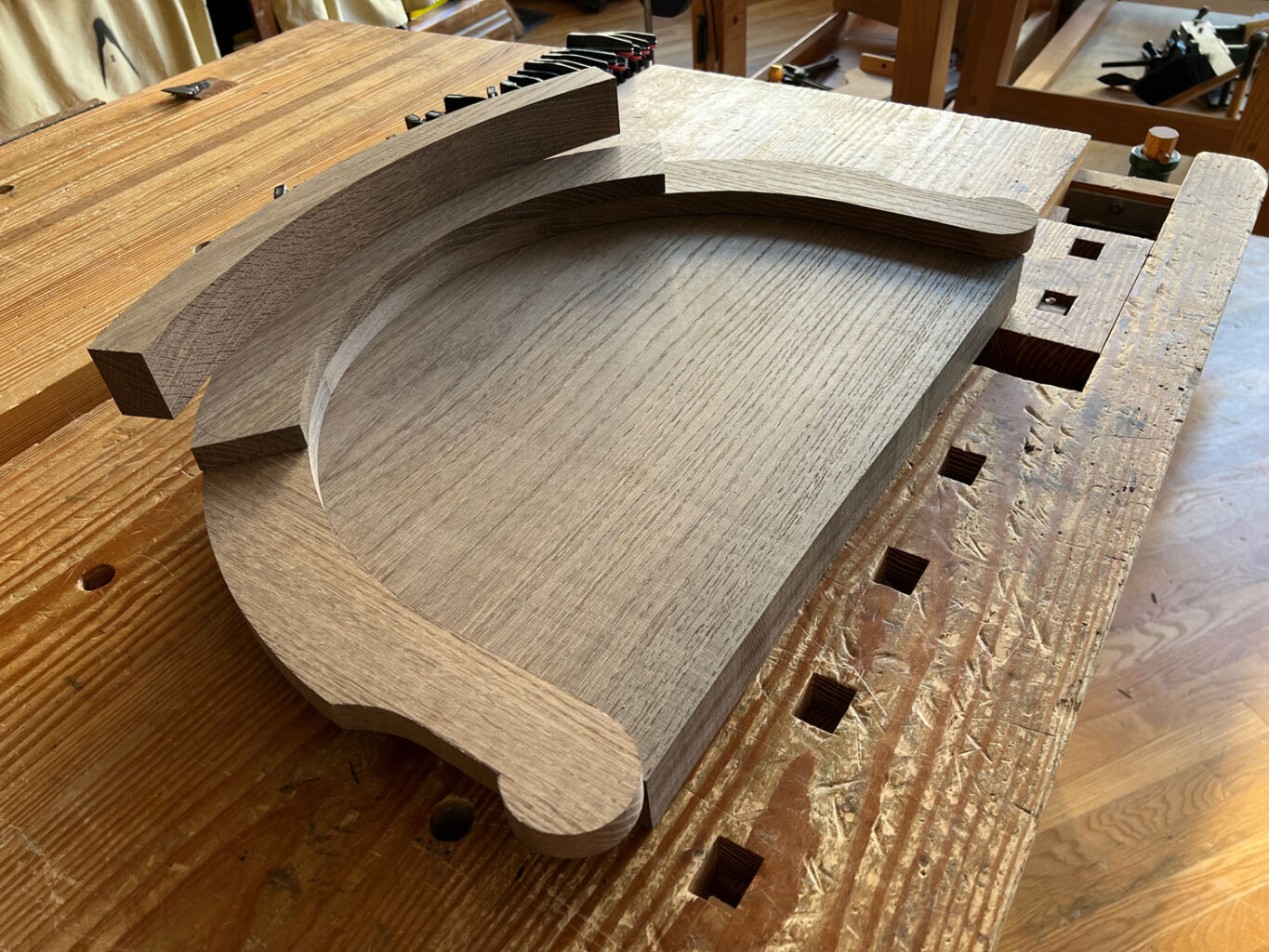
For the last year I’ve been building chairs using slabs of bog oak that are 2,000 years old (according to a carbon dating test) and was harvested in Poland.
Furniture maker Andy Brownell is responsible for starting me down this path. He offered me some scraps of bog oak from one of his commission pieces. After experimenting with it and building a chair using the scraps, I was sold.
Together we bought a large chunk of a bog oak tree. It was the most I have ever spent on a single load of wood. However, don’t be freaked by that statement. Because I work almost entirely with common domestic woods that aren’t highly figured, my lumber bill has always been minimal.
This entry is about my experiences with the wood – good and bad. I’ve worked before with some older bog oak from Denmark, so I have a little perspective. But I am not an expert. Trees, like people, are individuals and are weird.
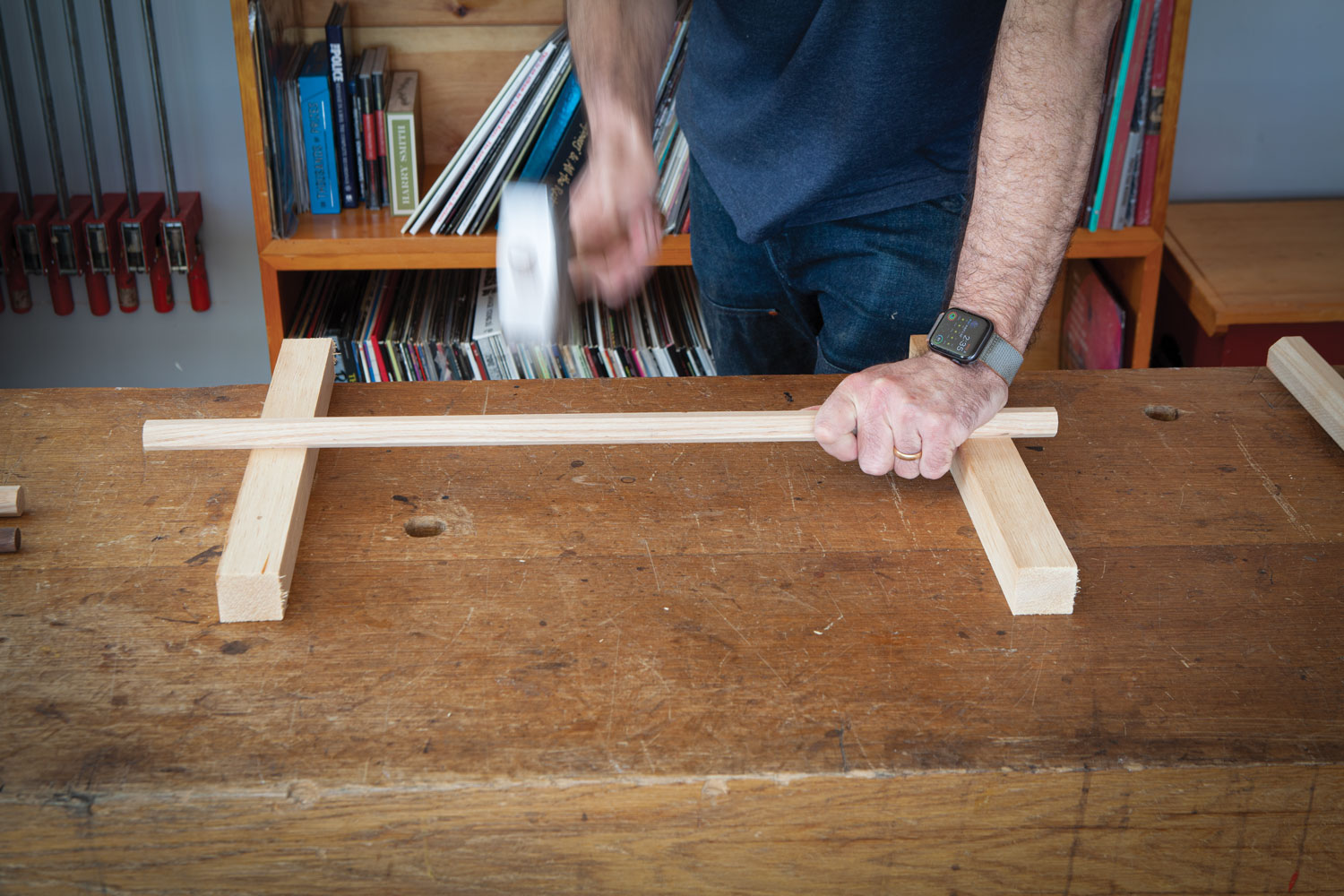
Strength
My biggest concern with the bog oak was that it wasn’t strong enough to use for a chair. This is oak that has been in a peat bog for 2,000 years and is on its way to becoming petrified. After wallowing in an anaerobic environment filled with turtle poop, is it too weak?
The good news is that the tree we bought was fast-grown oak. Some of the annular rings are 3/8” apart. Fast-grown oak is typically stronger than slow-grown oak. Also, the grain was incredibly straight, except at the butt of the tree. I have never worked with wood that is this rod-straight.
I made some sample chair-sized parts – legs, stretchers, sticks and arms. Then I propped the test pieces up on 4×4 blocks and smacked them with our lump hammer. Hard. They all survived just fine. No cracking, though they dented a little more easily than modern European oak.
Because the parts passed the test, I made some chairs using the bog oak.
Working Properties
The bog oak feels a bit like plowing dirt at times, instead of slicing wood. The wood requires more effort to saw, chisel and shape than modern European oak (which I have a lot of experience with). I also feel like it is more difficult to get a finished surface, but it’s not because of tear-out. It’s because the stuff is dense and resists you.
It smells quite a bit when you cut it with electric machines. And the smell it makes is: bottomland. Mud, dirt and cod poo. But it’s not awful. The worst-smelling wood I ever used was mahogany that had been sunk in the Amazon for 200 years. When you cut it, it smelled like rotten, burning fish that had been injected right into your nose.
The smell goes away quickly. And the finished pieces have zero smell (just like normal wood).
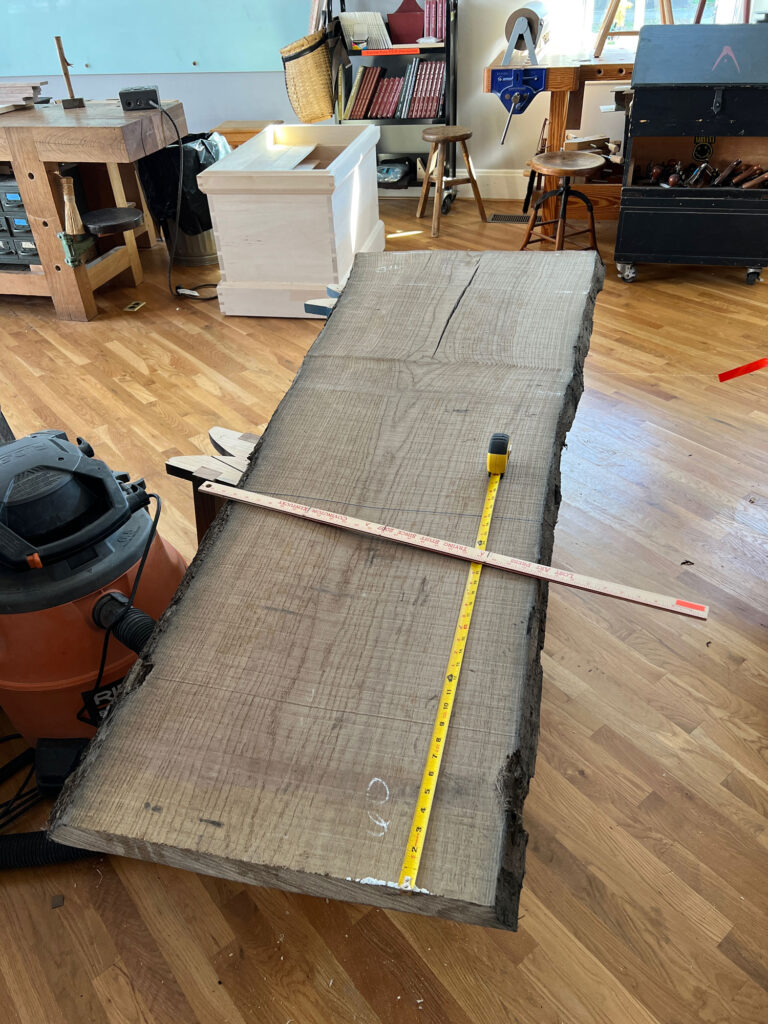
Color
Bog oak gets darker as it percolates in the bog. I’ve worked with 4,000-year-old stuff that is almost black. This 2,000-year-old stuff has lots of variation. The wood by the bark is nearly black. The majority of the heartwood is a chocolate brown. And some parts are tan or khaki. And you see that variation all in one board from one tree.
So you have to think about color the entire time, even though the wood comes from the same damn tree. A stick from the bark part of the tree can look radically different from a stick 3″ away.
Downsides and Defects
Wood that has been under ground/water for a long time can have some faults. I find far more structural faults with bog oak than standard European oak. Some of these splits and cracks look like the result of the wood being dried. Other cracks look much older (something killed this tree and sent it into the bog).
When ripping up the stuff, you absolutely have to pay close attention to the end grain and look for splits. Most of the splits I have found are near the pith of the tree, but I have also found some out by the bark.
I reject anything with a split for structural parts (basically all my chair parts). These pieces are fine for boxes or stuff that doesn’t support a human body, but shakes and chair parts don’t go together.
The other odd quality of the wood is that it’s not good for making wedges. I made many bog oak wedges to secure the legs and sticks of the chair. It was poor wedge material. When struck on its end grain, the bog oak was mushy and split easily. (Even though it was strong when struck 90° to the end grain – weird.)
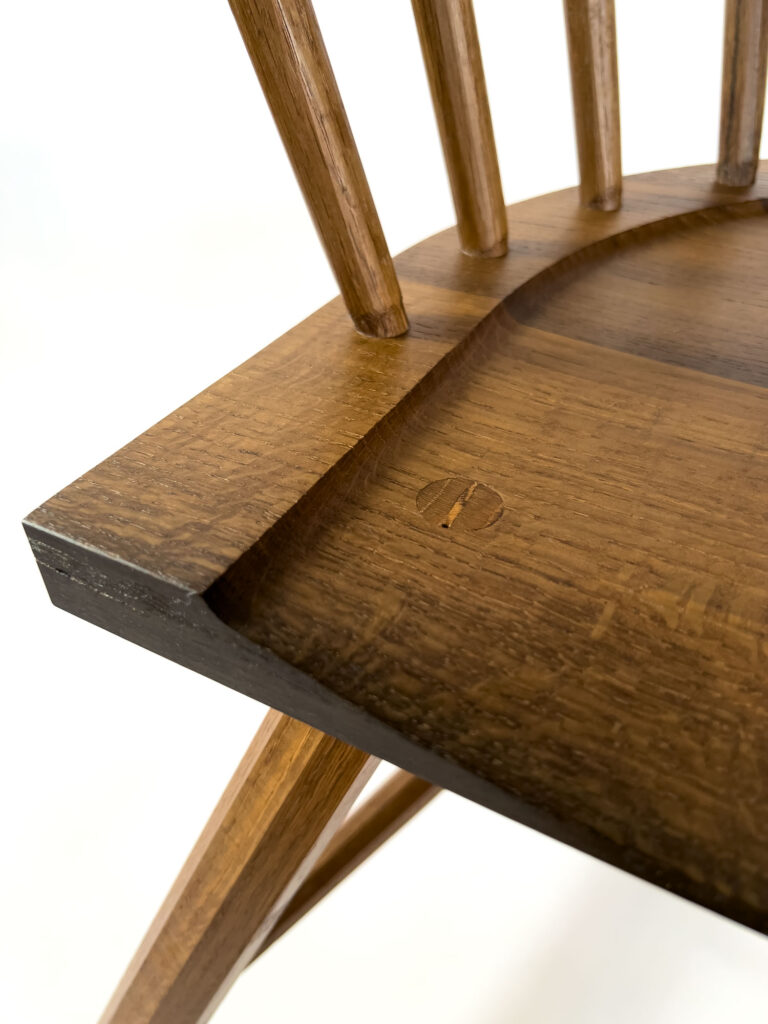
The Upside
The stuff is beautiful, even with simple finishes. I use linseed oil and beeswax, and the range of color is extraordinary, from coal black to an olive green. Plus, after five or six chairs, I have found ways to use this color shift to my advantage in the design.
All in all, the stuff is worth working with. The prices I fetch for bog oak chairs make it worth the effort. However, I wouldn’t want to work with it exclusively. It is recalcitrant. And I am always happy to start saddling a chair in modern red oak or white oak after working the boggy stuff for a couple weeks.
Where to get it? There are vendors who specialize in the stuff. I don’t have experience buying from them, so do your research. Andy and I bought our bog oak from M. Bohlke, a long-time local supplier of amazing woods.
— Christopher Schwarz
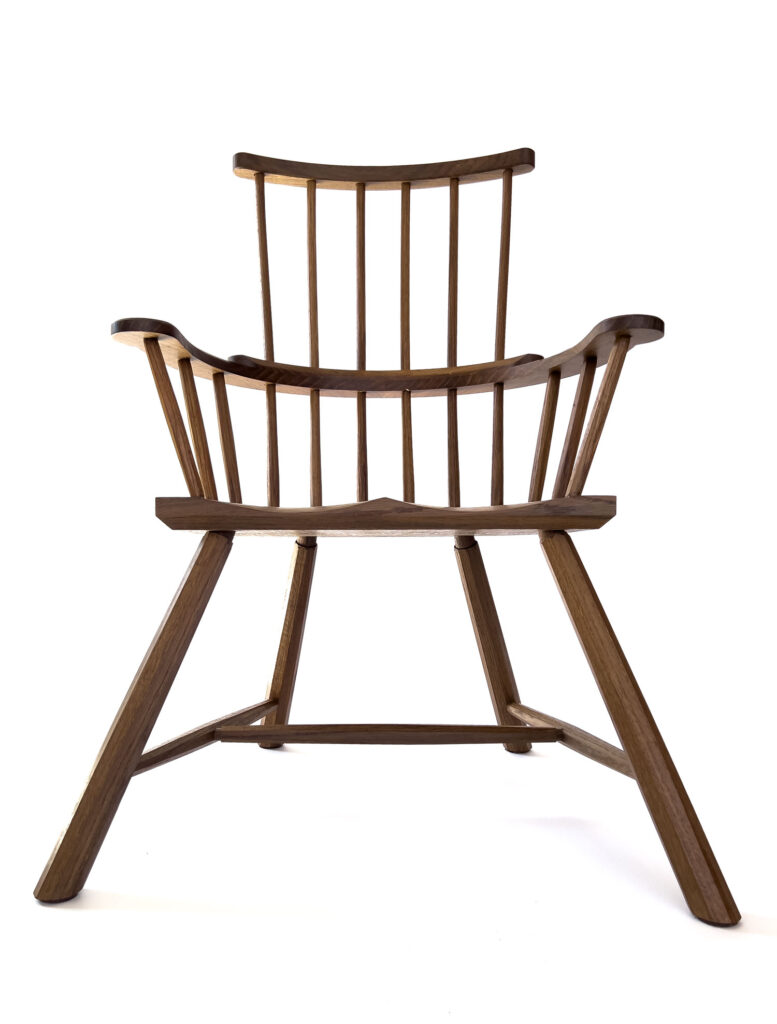
What did you spend on the bog oak and where could one order some?
We spent about $6,000.
You can buy bog oak from a wide variety of sources, such as Rare Woods (https://www.rarewoodsusa.com/species/oak-bog/). But you can find smaller bits of it on eBay and etsy easily. Expect to pay $30 to $35 a board foot. We paid less because we bought half of a tree and we are a commercial account.
I’m curious what your yield is per board foot. I know how to calculate board footage in a project (and add 20%), but seems like stick chairs might get get higher waste, especially with some of the defects you’re working around in the big oak. Throwing out a number I’d guess 25bf/chair?
Am I correct in guessing that the wood was air-dried after being cut?
I don’t know. From the way it behaves when I cut I would say yes. It works more like air-dried than kiln-dried. I’ll check its moisture content, which might be a clue.
I’m going to guess it was kiln- or vacuum-dried. All the stuff is between 5 and 7 percent MC. That’s really low for air-dried oak.
Perhaps I’m wrong. Happens all the time.
I thought pretty much all imported wood had to be at least heat treated, if not kiln dried. And I’d think if you’re gonna put high value hardwood in a kiln they’d probably leave it in long enough to dry it. But I’ve been wrong before. Thinking of it I doubt they’d want to heat treat dense exotics, but maybe they do if they have to?
For the FORP did they have to heat treat the French oak?
What kind of moisture meter are you using? Timber that has spent a long time soaking can give extremely wrong readings when MC is read, particularly with pin type (resistave?) meters. In checking remilled marine piles we’ve had to abandon all meters and rely on the oven dry method only.
Ligno. No pins.
Speaking of poo- I worked in a planer mill that specialized in decking from So. American hardwoods. One species was called Brazilian cherry and the whole mill smelled of dog poo when it was being planed.
Hello. I am Polish and I live in Poland. Nice to read that you sourced material in my country. I know a bit about black oak. Things are a bit forgotten at the moment. I think I have some boards somewhere in the workshop. I was so inspired by your post that I think I’m going to do something with this material as well.
Maybe the “Ultimate piece of Bog Oak”. https://www.thefenlandblackoakproject.co.uk/ I went to see it a couple of weeks ago and to stand next to it was just wonderful. I can’t really fins the words to describe the beauty of it.
Chris, do you know what species of oak it is? I think the term ‘bog’ oak just means it lay in a bog for a long time. I also see this referred to as ‘black’ oak, but I think this refers to its color, not the species.
I’m told it is European oak (Quercus robur). And it certainly looks like it.
I am curious if it is possible for “bog oak” to be man-made… In other words, is there some sort of industrial process to crank out the stuff, rather than digging it out of the ground? Maybe that would not be economically realistic. But if we can make diamonds and other gemstones, for instance, seems like we could make bog oak that might be more consistent in both quality and color… and for a much lower price point than $35/BF. Or is it just that there’s a mystique associated with the working of wood that is thousands of years old? There’s no doubt that the natural material sure is beautiful…
Why is it that fast-grown oak is stronger than slow-grown oak? I’ve always heard that old-growth, slow-growing woods tend to be stronger. Although maybe that just applies to softwoods.
Slow-grown oak has a lot more earlywood, which has big vessels, which are mostly air. Fast grown oak has smaller vessels, so less air.
https://www.woodmagazine.com/wood-supplies/wood-figure/what-is-latewood
Nice post. I learned something today. Also, that wood is even older than you.
I’ve worked maho too but the smell wasn’t quite as pungent as the cypress I acquired by way of 100 hundred year-old church pews. As with your bog oak, the scent does go away. Thank heavens.