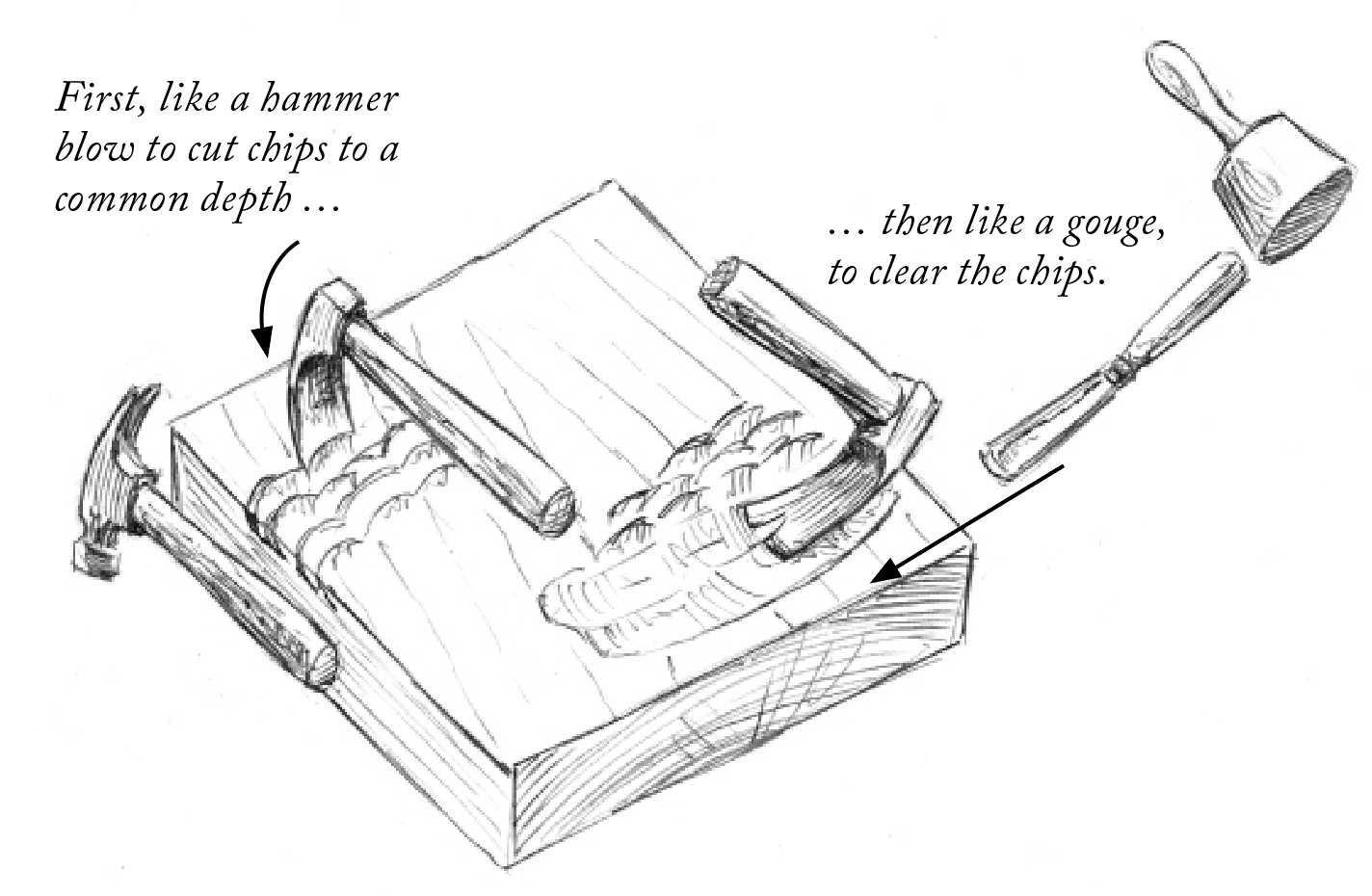
The following is excerpted from “Chairmaker’s Notebook,” by Peter Galbert, from the section on tools for seat carving.
Whether you are an aspiring professional chairmaker, an experienced green woodworker or a home woodworker curious about the craft, “Chairmaker’s Notebook” is an in-depth guide to building your first Windsor chair or an even-better 30th one. Using more than 500 hand-drawn illustrations, Peter Galbert walks you through the entire process, from selecting wood at the log yard, to the chairs’ robust joinery, to applying a hand-burnished finish.
And if you’ve never thought about building a chair, this book might convince you to try. Building a chair will open your eyes to ways of working wood that you might miss if you stay in the rectilinear world of boxes.
The adze is like a gouge, but rather than striking the end of the tool with a mallet, the force is supplied by swinging it like a hammer. I use an adze to hog out much of the waste material in the seat. When correctly shaped and weighted, the adze can cut with surprising control and leave a clean surface. The trouble is that most adzes were designed for some task other than carving seats, so a little extra awareness of the tool and its geometry will help when tuning them for this use.
The adze is often soft steel that could be abraded with a hard file, but I don’t recommend it. A finely honed adze will stay sharp longer and leave a much better surface. There are two configurations for adzes: one with the bevel on the outside (out-cannel) and one on the inside (in-cannel).
The adze process is called “hewing” and requires two steps. First, you make a series of consistent-depth cuts as shown at right in a pattern of rows resembling fish scales. When striking each row, the direction of the swing is toward the previous row. This leaves the chip unsupported and allows a weak layer to form at the depth of the cut. Then you clear the broken chips to the depth of the initial blows. When the geometry of the tool and the swing is correct, the adze follows a radius that will take and clear loose chips.
This is a controllable method, and practice brings speed and certainty to the process.
By removing material in successive stages with this technique, the remaining shape and surface can be refined. Clean-up cuts that travel across the grain while skewing the adze “downhill” can leave a polished surface.
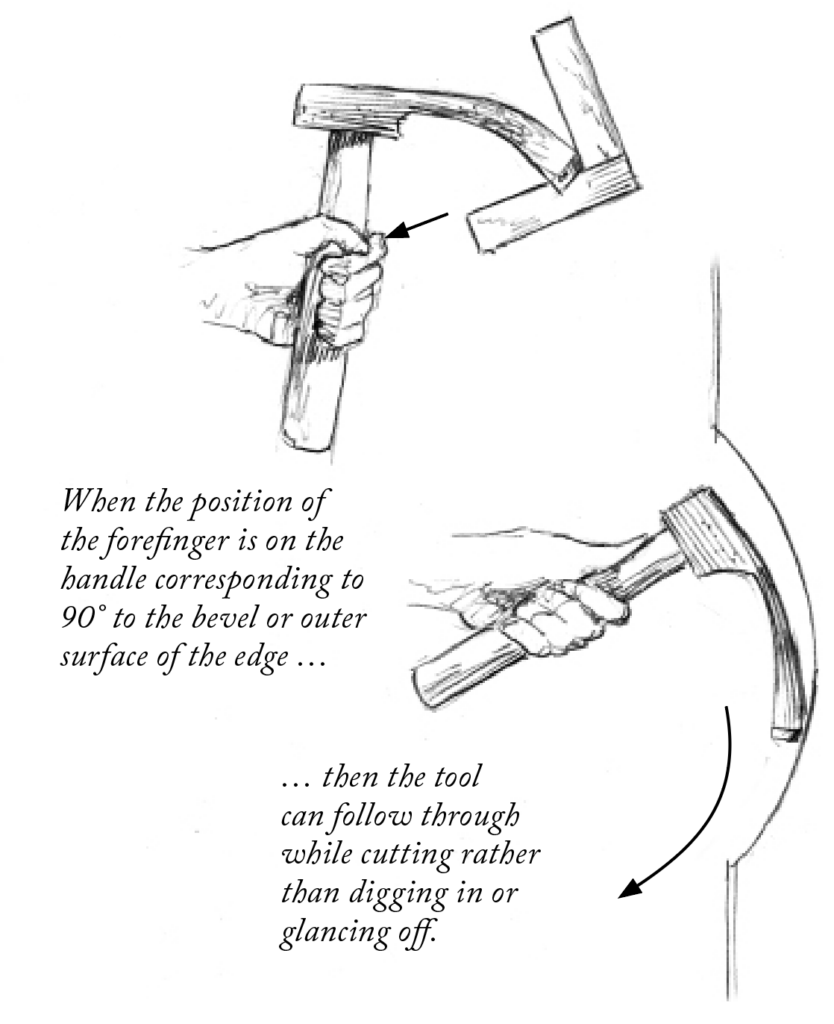
Body position is critical to using this tool effectively. I’ve seen long-handled adzes used while standing on the seat. I prefer a smaller hand adze in conjunction with the workpiece on a podium platform or clamped to the seat of my shavehorse.
The shape of the adze and its relationship to the handle is key to its function. An adze works best when the most comfortable and balanced point on the handle corresponds to the outer surface of the edge of the tool as shown above. This relationship is called the “hang.”
If your adze doesn’t do this, then you can regrind the edge to get the geometry to work better. If your adze is ground in-cannel and the hang doesn’t work well, you can either grind a bevel on the outer surface or make a new handle with a bend in it that will correct the issue.
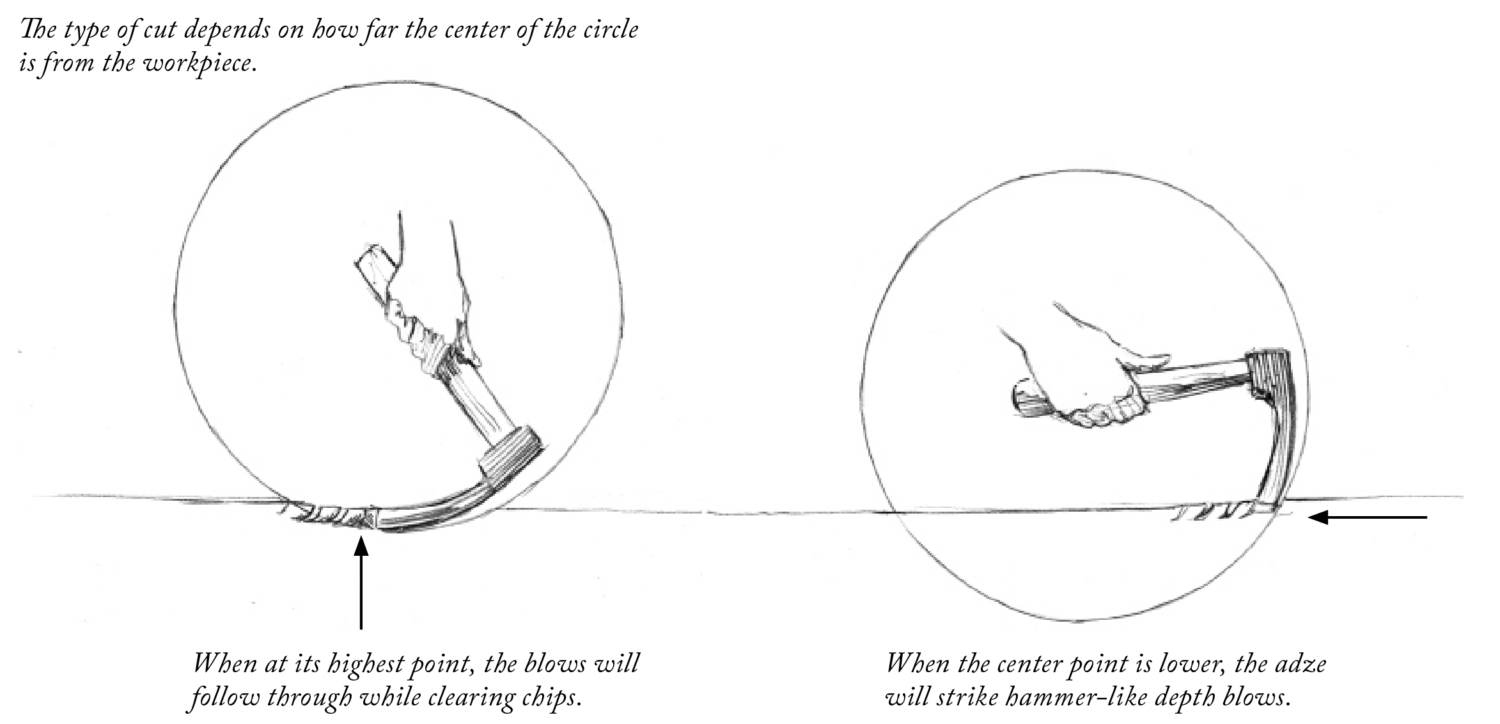
When evaluating the geometry of an adze, I assess how easy it is to control where it cuts. An adze with the proper hang and good balance will hit where you want and where you expect. If this isn’t the case, you will have to exert excess energy to control the tool and it will become tiring to use.
I think of the adze head as moving around the circumference of a circle with my hand at the center point. If my hand is close to the work, the adze digs in for deep cuts and strikes like a hammer. If my hand is high off the work, I get a glancing blow for clearing chips. In each case, the center point shifts slightly in the direction that the tool is swinging as well.
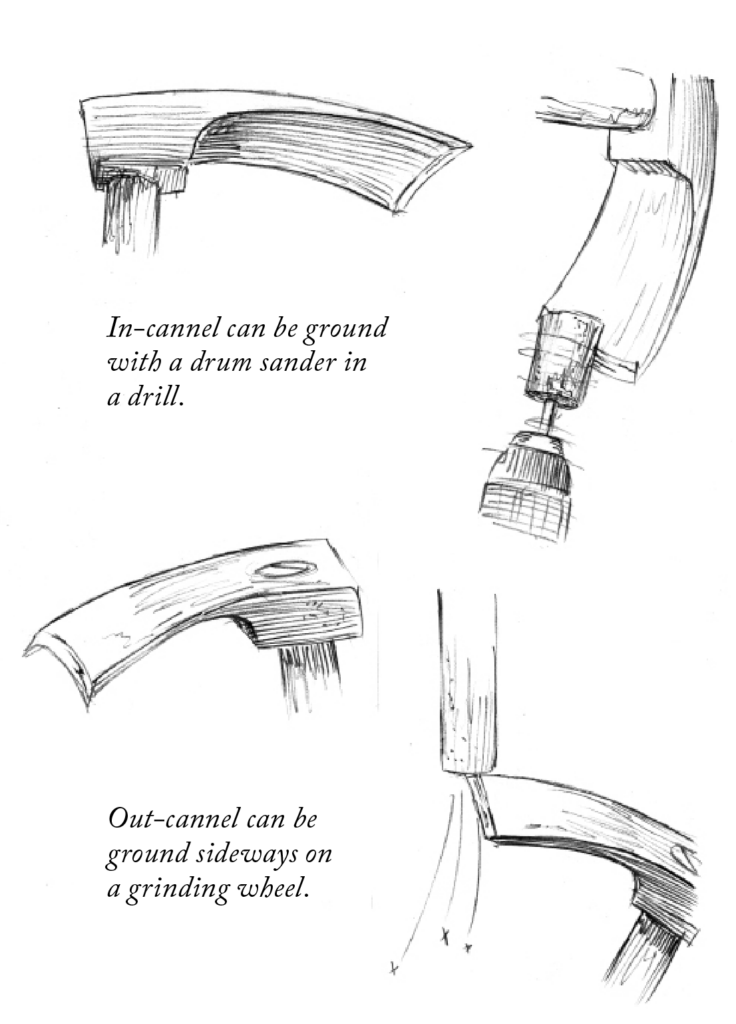
Like any tool, the adze is going to perform best when it not only has proper geometry at the edge, but a high level of sharpness. Don’t let the brutal impression the tool gives keep you from experiencing it at its sharpest. Grinding and honing the adze is certainly different than chisels or plane blades that have lots of flat surface to reference, but a little focus and creativity can yield controlled and repeatable results.
If the handle or head shape gets in the way of buffing the inside curve, I use a drum sander in a drill or a dowel with sandpaper wrapped around it. A dowel charged with honing compound will polish it up. When choosing the angle for the bevel, consider the point on the handle where you are most comfortable gripping as well as the thickness of the edge for durability.
For consistent grinding, a means for holding the adze head in a jig can be helpful. Remember, the adze is just a gouge, so thinking of sharpening your turning or carving gouges can help when conceiving of the best way to go about it. The holding jigs shown at left might take some effort to make sure that the position and movement of the blade contacts the edge properly when the tool is rolled, but the results will most likely prove it worthwhile.

The in-cannel adze is trickier to sharpen, and the location of the grip is dictated by the shape of the adze head, not the bevel angle. Polish the outer surface of the head and dub the edge a bit. Grind the bevel with a drum sander or grinding burrs in a drill or Dremel. I like to use diamond pastes of sequential grit to get my final polish. There are no rules about the grind – whatever works, be it in-cannel or out-cannel or a combination of the two. All are worth exploring.
Recommendations for brand/source?
Ed Labinski above the Wood Wrights School of Roy Underhill in Pitsburgh, NC frequently has excellent tools such as this. He buys them from tool shows and auctions in England.
I’m not finding on Google. Perhaps Highland Woodworking has something to help.