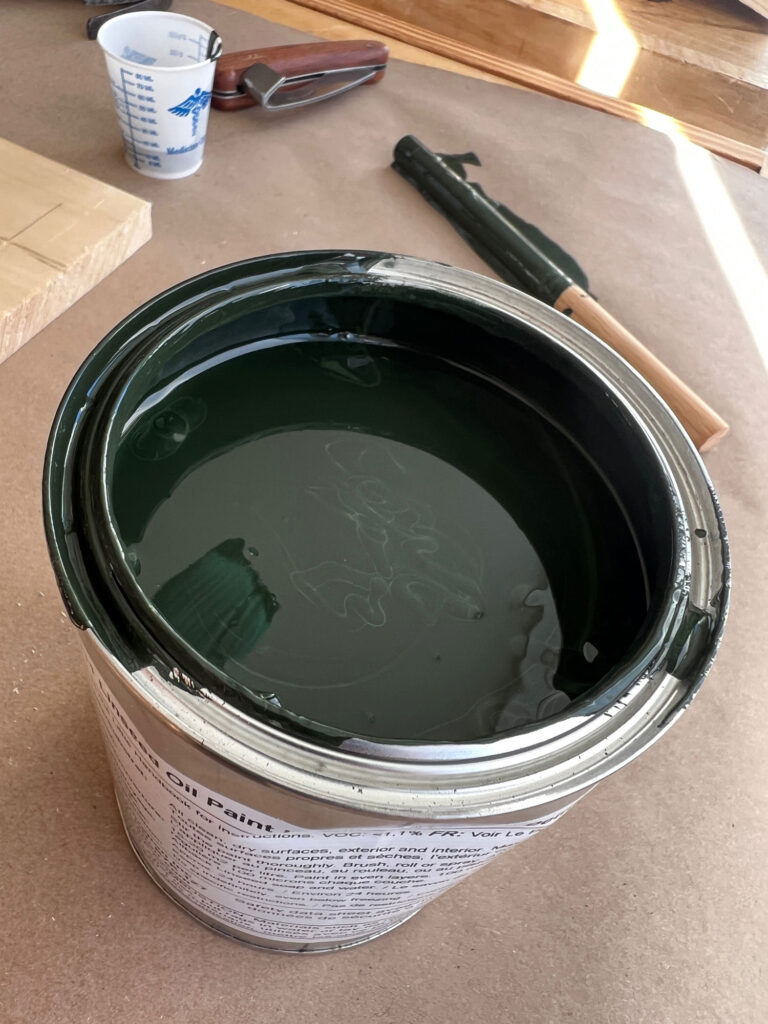
For the last 20 years I’ve used mostly milk paints and acrylics on my furniture. I have reservations about both kinds of paint.
On milk paint, I find it inconsistent and a lot of work. When it works, it’s great. But it takes significant effort and time (for me) to get good results. And just because you know how to use red milk paint doesn’t mean you can use the same methods for black or blue.
That said, the paint has a lot going for it. It’s non-toxic. It is hard-wearing and looks better after a lot of wear. And it doesn’t create a plastic film over the wood like other paints do.
From the perspective of someone who sells furniture, however, I need to charge more for pieces that use milk paint because of all the extra time and steps involved.
Acrylics, on the other hand, are consistent and fast. I can spray a chair in the morning (about 45 minutes of work total) and have it sittable by the end of the day. The major downside is that it is a plastic finish. I’m not a fan of plastic – full stop. Nothing about plastic makes me happy. Acrylic wears fairly well, but it hasn’t been around for all that long (only since the 1930s). So the jury is still out on it (as it is on plastic glues such as polyvinyl acetate – aka yellow glue).
About seven years ago, we started working with the Canadian distributors for Allbäck, a Swedish finishing company that makes excellent linseed-oil-based finishes. The distributor also became our Canadian distributor for Lost Art Press for a time (we parted on amicable terms).
As we got to know one another, the Canadians sent us a bunch of their products for us to try. I became a huge fan of the Allbäck linseed oil wax. So much so that I sought to make our own variation on it for our shop (which we call Soft Wax 2.0).
They also sent us some of the Allbäck linseed oil paint. I’d made my own linseed oil paint before, and it’s a bit of a pain to get the pigment mixed into the oil. And then the paint takes a long while to dry. So I was a bit skeptical.
But I decided to give the Allbäck paint a try because everything else the company made was really good.
I painted it on our chopping block outside. The next day, the paint was still wet. Three days later, it was still wet. It took a full week for it to dry to the touch. At the time I remember saying: “I can’t wait a week for a single coat of paint to dry. I’ll starve.”
However, I was amazed by how good the paint looked, even after it was subject to our Midwestern climate with its extreme heat, humidity, snow and ice.
I set the stuff aside until I started work on “The American Peasant.” After much thought it became clear that linseed oil paint was the right paint for all these projects. It looked right. It was simple. It was low-VOC. Natural. I decided to give the paint a second go.
This time I read up on the paint a lot before using it. I experimented with adding a thin coat of oil on the wood the day before painting – this seemed to really help. And after applying the paint, I kept it in a room with low humidity. Plus I exposed it to lots of sunlight (a tip from Jögge Sundqvist).
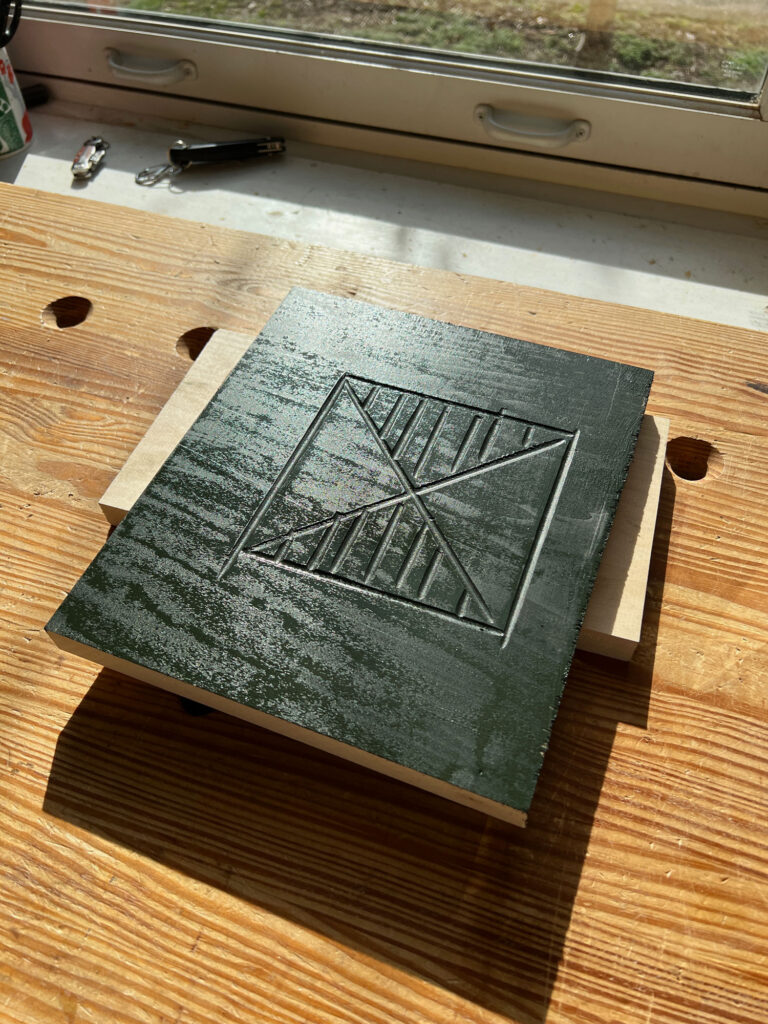
The coat of oil before painting made the paint go on very smoothly (like I was applying a second coat of paint). Controlling the drying conditions reduced the paint’s drying time to less than 24 hours.
And the linseed oil paint looked great with just one coat. You could still see the wood’s grain, the paint was fairly matte and there was no plastic feel.
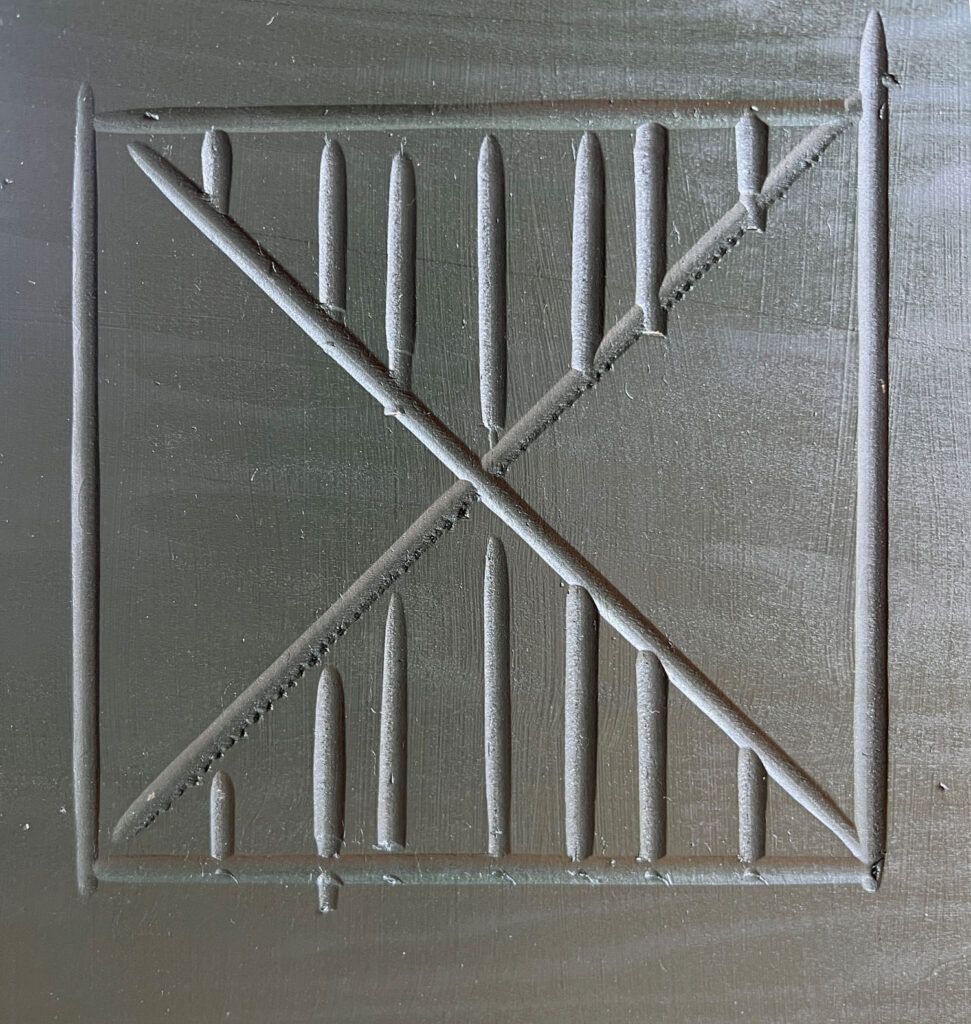
I’m sold.
For the book, I’ve bought three colors of paint. (I could have bought all of them. The Allbäck colors look absolutely gorgeous to me.) Here they are: Old Blue, Holkham Green, and Old Red.
It’s a little more expensive. Allbäck is about $2 an ounce. (Quality acrylics are about $1.70 an ounce.)
But the quality of the Allbäck is outstanding. In fact, now that General Finishes is reducing its acrylic offerings, I’ve decided to try linseed oil paint on my chairs to see how much time it adds to my process. I suspect it won’t add much labor. But I will need to be patient and allow the paint to dry.
— Christopher Schwarz
Alback sells a siccative (drier) that will help the paint dry more quickly. I am pretty sure that it is magnesium sulfate (maybe manganese sulfate?). A totally natural drier. You buy it is a small vial of crystals and “salt” some in. This was >~10 years ago, maybe now they have changed their approach. A very dense pigment, one coat gives great coverage. Meant for outside coverage in those Nordic winters.
Litharge is also totally natural, very traditional with a history of use dating back centuries, and a very effective siccative. Otherwise known as lead oxide, its use is distinctly frowned upon now.
Allback’s siccative is far more benign but the the call to naturalness gets my hackles up.
It is a manganese oxide . It does help a lot indeed. I did use that paint on steel, ramps etc
Exceptional. Period. Love it .
Was the “thin coat of oil” BLO, or something else?
Raw linseed oil
Right- takes longer, but natural. Got it.
Raw because it’s more fluid . Or their BLO but applied at 35Celcius approx. Same results. It’s a question of viscosity mainly.
Very timely Chris. I just came to my desk to finish a blog post about a chair I just painted w milk paint – and I wrote: “Takes more patience than I have. Next time I might do oil paint & be done with it.” – ’nuff said.
I do love the look of milk paint but it does take literally days to get it the way I want it. Having an alternative would be great
Hello from Canada. The Allback linseed oil paints are excellent products and I have specified them extensively for wood window conservation work in southern Alberta. They wear well in our climate, and more importantly, take additional seasonal coats easily (with very little difference between the coats even after time has passed). I’ve found these paints have very good for colour fastness to sunshine (UV) and weathering. Excellent, traditional product that is highly suitable to furniture as well.
How does it do with layering colors, like black over red?
In the book “On Writing Well”, William Zinsser provides an excerpt from Life magazine that he uses as an example. Part of it goes: “Linseed oil, for example, has a kind of memory. Once exposed to light, even if only briefly, it will change consistency and speed the second time it is exposed. It will ‘remember’ its first encounter with the light.” Maybe there’s something useful (or at least interesting) there.
So happy you’re talking up linseed oil paint. In Europe there seems to be a significant shift away from petroleum based paint, and it should be happening here too.
I can also recommend Ottossen’s linseed oil paint, oil wax and linseed oil, available in the US through solventfreepaints.com and earthandflax.com. When I emailed the Swedish manufacturer with a question, I got a reply from Gunnar Ottossen himself, which impressed me. But I’ve used Allback as well, and have no complaints (although their primary red, “Signal Red,” is kind of grainy and is being discontinued—frustrating if you mix colors). Another manufacturer is Bourne, in England. Mortise and Tenon Magazine has an article by him all about the virtues of linseed oil paint.
I started using linseed oil paints on my hardwood picture frames last year, and what you say about coverage and the way the wood comes through is also my experience. Linseed penetrates extremely well, and this has a visual effect, which is that it looks more integral, less superficial, than other paint. It can also be ragged on like oil as well as thinned with straight linseed oil for simply tinting.
As for drying, I put it right on the wood with no primer coat of oil, and after one day (when it was dry enough that dust wouldn’t stick to it), I put it out in the sun. So it seems to be two days to dry, and of course it keeps curing for a couple of weeks.
With respect, Tim, it’s Broun, not Bourne, in case anyone wants to look it up online. It is very good exterior paint.
Right–actually Brouns & Co. (https://linseedpaint.com/ ). And I forgot to mention Viking, also available through solventfreepaint.com.
I bought some paint from Brouns late last summer to paint the exterior of my house. I was in the process of removing the vinyl siding and repairing and painting the wood siding underneath. It went on well using a primer coat (paint diluted with raw linseed oil) first and I really like the finish coat. I was 3/4 done before I fell and tore my rotator cuff.
The completely varying behavior of milk paint based on colour within a same brand is very surprising.
Do you have to thin the Allback oil paint at all?
No thinning necessary. The paint stretches very nicely. A little goes a long way.
How much paint is needed for a chair? Does the 6.8 oz jar cover one chair? Thanks
If there is one thing Austin has plenty of its sun. And low humidity, though that can change from 10% to 80% in a matter of hours. Still, overall low humidity. I’d be curious to see how quickly it would dry in the bed of my truck. The cab of the truck on a 100 degree day (38 C) is a great place to warm up hide glue.
So back when we used oil paints for outside applications my dad would use linseed oil on the bare patches of wood before painting. This method was used on our shoreline cottage which faced extreme weather high humidity along with sustained winds. By golly I thought after reading your blog, my dad was on to something!
So I looked up the paint online and in fine print they say they can’t ship to Connecticut along with a few other states around me.
So the logical conclusion is this paint must be very dangerous for the environment , people, animals and its just not safe to use…..
Either that or my state leaders are full of cow excrement.
Luckily I have a friend who lives 20 minutes away in Massachusetts where I can have any illegal shipments sent and pick them up at my leisure.
At least I can buy all the pot I could wish for because that’s perfectly legal now in my state.
I can even carry a gun around now that it’s unconstitutional to ban people from carrying guns just because they are stoned or on drugs. ( google Utah decision)
I just wish my state legislators would stop smoking so much of the stuff.
It could also be that the company uses a shipper, like UPS, that places restrictions on shipping flammable items. Raw linseed oil is definitely flammable and that could lead to special shipping requirements.
Sometimes vendors use different shippers depending on the distance – that could be why they are able to ship the products to some states but not others.
As a Californian I feel your pain, however it appears Lee Valley may just be extra cautious. Look up Sage Restorations, they also seem to carry the full line and I can see no shipping restrictions.
There are some CA stores that do sell things to woodworkers that technically they shouldn’t. It always puts a smile on my face. Like you have found Tom, there are some retailers who won’t ship to CA and others who will for the same product.
Have you tried spraying it yet?
No. The manufacturer says you can spray it. But we don’t have the facility to deal with oil-based off-spray.So we were going to brush it (and try other application methods such as a sponge or rag followed by tipping off with a brush).
Very timely post. I have a love-hate relationship with MP and might be done with it for good after failing to get a good finish on a chair. Will give the Allback a try.
Great to see you’re trying out the Allback paints, I have been messing around with them on and off for a few years now. Always thought they would be great for a traditional finish on stick chairs. Lots of tests, and one client piece in the wild (a sideboard). Been weary of using on a chair, as I have concerns of pigment transfer to clothing. Now I am going to need to dive back in and do some more tests. I also have some of the Linus wall paint lying around that still needs some proper testing.
Looking forward to seeing what you do with the paints!
Sadly can not be shipped to CA
I’m in CA, and have had no trouble buying from solventfreepaints.com or Sage Restoration.
Seems like has different look and fell than M.P., so aesthetics are the the reason many would use linseed paint over M.P. As always there are trade offs and different considerations for every instance. What I found humorous is your lack of faith in yellow glue after seventy years, but seem to give this product a break after such a short personal experience. Not being snarky but I did chuckle.
I took it a bit differently than you. Yellow glue was invented 70 years ago, and we don’t know what it will be like in 100 years, or 150, etc. Linseed oil paint was invented at least 900 years ago (according to the quick google search I just did), and we know exactly how it behaves over time. So, his experiences with this particular brand might be novel, but the basic material is not exactly a new thing.
As I think you know, Chris, I love linseed oil paints (although I’m more of an Ottosson man myself), so I’m very excited about you giving them a proper go, and will be very interested to hear what you make of them in the slightly longer run! I find high quality linseed oil paints (and Allbäck very much are on that list!) a joy to use, and the finish they produce so much nicer than acrylics, both to my eyes and to my hands.
Yes, they are a bit more complicated to use than some of the modern types of paint, and can be less forgiving of mishandling, but if we think it fine to have to learn and develop our skills for working the wood, why should it be any different when it comes to finishing it?
As you know, I painted the stick chair I built in the class with you last year with linseed oil paint, applying three coats. The base coat was a mix of 2/3 boiled(*) linseed oil and 1/3 paint; the second and third were undiluted paint, straight out of the can. And yes, it was slower than milk paint or acrylics would have been, in that I had to wait about 60 hours between coats; however, the actual painting was not slower than brush painting most any paint would have been. I’m not the fastest chap in any point of the compass with a brush, so I think it took me about an hour per coat to apply the paint.
After the third and final coat, I then left the chair alone for a further week before sitting in it, at which point it was more than dry enough, although not yet fully cured.
All that drying, however, while slow, doesn’t need any help — the paint does it all on it’s own, so one is free to spend that time on other stuff. Unless, of course, one decides to take up the exciting new hobby of watching paint dry … 😉
In other words, the slower process will mostly starve the craftsperson only if the longer time it takes to get the finished piece out of the door leads to cash flow problems, or if the number of pieces produced are large enough that additional storage facilities are needed to keep the pieces until they’re ready to go out the door. It will be a bit more expensive, both in materials(**) and time spent painting, than sprayed-on acrylics, but to my understanding that should be the main financial difference.
Cheers,
Mattias
() The Ottosson boiled linseed oil that I use is actually *boiled, as in heated for a week to pre-polymerise it, not doctored with heavy metal driers.
(**) Being the Fancy Lad™ that I am, I did of course have to opt for the most expensive linseed oil paint out there: the Ottosson Cobalt Blue that, because it uses a very costly pigment, comes with a price tag hefty enough to cure hiccups. Most other linseed oil paints are not that hurtful to one’s wallet, I’m happy to say.
Mattias,
I work in a shop with poor ventilation and dirt (well, gravel) floors. How much if an issue would to expect dust to do be during the drying process? 60 hours seems like a lot of time for dust to settle on a still-wet piece if it were to collect dust while wet.
Or would I have to build a plastic tarp “clean room” or order to dry a piece?
Hi Jace,
In my experience, the paint remained sufficiently sticky for dust to get stuck for somewhere between 12 and 24 hours. After that it was more a question of waiting for it to have dried sufficiently for sanding between coats not to be an issue, but the surface was already dry enough that dust accretion was not an issue for me. Also, it is not a high-gloss, thick film finish where the least speck of dust would show up like Mount McKinley.
My shop is certainly not dust free, but the part where I usually paint stuff is away (by some 12 feet or so) from the main sources of dust; it is actually set up as as a kind of plastic tarp-clad clean room, but in reverse as it is where I airbrush paint my model boats, for which my main concern is to keep the paint dust from that process away from everything else (it can be an absolute bear to get rid off).
For painting the chair I worked inside that cell, but did not close the curtains, as one of the key elements with any linseed (or other polymerizing) oil based paint or other finish is that it does not cure by evaporation, but by oxidation, which means that it will dry rather faster and better if it has a steady supply of oxygen. Or, in other words, if the area where it is drying is well ventilated! So when you say that your shop has poor ventilation, that sounds to me like almost more of an issue than the dust.
Maybe a good way to find out how it would work for you and how much you like or dislike it would be to get a small (4 or 6 oz., depending on brand) sample pot, and do a couple of test pieces?!
Cheers,
Mattias
I live in Sweden with my wife and we are restoring a traditional Swedish log built home that was built in 1896. We have tried to be kind to the house in our restoration and have looked to use linseed oil paint through out. Having used modern paints in previous projects I would always now look to use linseed oil paints now, both in their “gloss” and matt finish. It is just a beautiful paint to use in its application, smell and in its finish. I have used the “gloss” on the floors and higher wear areas and although taking a little longer to dry the resulting low sheen is very durable. It is a finish that also ages beautifully, dulling down slightly. The light also plays on the surface of the finish to reveal great depth and natural texture. The first coat I sometimes thin slightly with a balsam turpentine to aid penetration.
A beautiful natural paint finish that I will always look to use.
Now a slight deviation but timber building related
We live a short walk from a gentleman, Anders Voxberg, who over the last 12 years has, all but single handedly, built a Stavkyrka, a Stave Church, mostly using hand tools, in traditional Scandinavian style. I had the privilege of working with Anders for a month on the project when the wooden roof staves were fitted and helped with tarring the building with pine tar, another beautiful natural product. The church and other old timber buildings moved and re-erected by Anders can be seen on his website ocklagard.se
Nice post, Chris. Thanks. I love Allback linseed oil paints and after several years using them I’m still finding that they open up new possibilities for pieces, including cabinets, that want to be painted rather than finished with shellac etc. I find a great advantage of linseed paints is way the visibility of the wood grain can be controlled very easily and locally by wiping with a rag. After an initial coat of oil to mask absorbent grain, paint then wipe for one or two coats. No smuges and looks beautiful.
Chris, thanks for this paint review. Would love to try it. I want to know what type of oil you used for the pre-coat. Linseed oil? Boiled? Or?
I’ve love to know what you think of the pine-pitch coatings (not even sure if it is paint?) that Sage Restoration carries. I’ve tried it on an outdoor planter and it was the same sort of deal. Lots of mixing, took a while to dry, but lets the wood come through. Also smells like BBQ while drying which was… interesting but not unpleasent. Not tried the Linseed paint but good to know it is a solid option for projects down the road.
I believe the entire Allback line is avaliable through Lee Valley…I’ve purchased the tinted linseed oil wax there. I’m also a big fan of the regular linseed oil wax as a finish
Great choice! With oil paints, thin layers are key. So better two thin layers than one thick one.
What Mattias says in another comment about Ottosson’s boiled linseed oil also applies to Allbäck’s one – no added dryers, but shorter drying times due to heating.
Unable to buy in California.
You might enjoy trying one or two coats of hide glue applied hot, or not cold anyhow, and then the paint.
Basically you are now in the very well-explored territory of painting on wooden supports. All the more reason to continue as you are!
There are a lot of artists who will insist on their own maps being the territory, a lot of thou shalts and whatnot, with warnings of here be dragons, edge of the earth over thisaway, et cetera, but there are loads of humble, generous explorers of their craft, too.
Historically, for painters anyhow, the reason for drying in sunlight is to temporarily unyellow the oil. It will return with time, if say you kept the painting in a closet, but it goes away again with sun exposure. Linseed oil dries by polymerization (and oxidation, I think, thus the spontaneously combusting rags?) so sunlight may not help drying other than a thin surface layer, but who knows, this is furniture with different use scenarios than paintings on walls, so maybe skin formation moving ahead of the slower inner drying might be of benefit, if it is happening at all, and you are working in thin layers on an absorbent surface, so you gain latitude that painters who use impasto may not have. Oil paint dries when it dries, so patience is the thing, but it is well-rewarded. Short of adding toxic driers, as you rightly point out.
Absorbant supports supposedly have the risk of pulling the oil into the support, leaving the pigment to become friable due to lack of binder, but again, you are working thinly, so there is more penetration of pigment molecules into the “mechanical” structure of the wood fibers. And it will allow you to move on before the paint is thoroughly, technically, dry deepdownin.
Getty Conservation Institute has all kinds of fascinating, science-based resources. And I have found that Kremer Pigment has always been very generous with information, and hears a lot of feedback from a wider array of craftspeople than just painters, who can be rather possessed by pseudoscience.
Kremer is also a great source of fabulous materials of all kinds. There are non-toxic earth pigments out there, including blacks, that are magic incantations in and of themselves, simply glorious nature at its most beautiful.
Some “old master” painter tricks in the literature may be of use, like using a touch of pigment with manganese content for drying help, stuff like that. Max Doerner’s famous book is quite fun to read and I think would be useful and inspiring to you in ways contemporary books are not.
Also (sorry this is running long, it is just so exciting how you always strike out and explore, free of orthodoxy, and discover though play and experimentation), putting aside milk paint mixes, there are other types of distemper than casein that are easy to manage making from raw materials, with more flexibility than the dried mixes (heck, making your own casein paint from milk might be just what you are looking for and not finding in the pre-made stuff), which tragically locks you into the mixmaker’s pigment choices when there is a shining infinite cosmos of pigments to explore.
Gummy bear hide glue as a pigment vehicle, varnished/sealed with your beeswax paste could be quite amazing. There is an entire jazz universe is out there for everyone to find their voice and vocal shading for this particular spell and something else perfect for the other spell, and on and on.
Thank you for sharing your process; I think it is of great service.
Hi Eric, are you saying hide glue applied before milk paint can help getting more consistent results with it? Also, I really like the Getti resources, as well as the following forum, which you might already know:
https://www.artcons.udel.edu/mitra/forums
Hello Charles,
I was proposing hide glue as a “sizing” before the oil paint, as an alternative to what Christopher tried: using a coat of oil before the oil paint. Not saying a glue sizing is more right, just another option that will help the first coat of paint be more like a second coat of paint, as Christopher put it. Glue sizing would do similar things for a subsequent coat of milk paint as well, for similar reasons, I think. The final visual effect will be different, and another arrow in the quiver for making finishing choices!
My sense is that anything that reduces the absorbency of the wood will help the paint go on easier and will yield more uniform absorption/a more uniform surface gloss, if that is what one wants. The less absorbent the wood before painting, though, I think would reduce the mechanical aspect of adhesion and thus reduce wear resistance to the extent the paint become a film on top of the wood more than “liquid” absorbed into the wood fiber. Kind of a continuum with shifting/non-linear advantages/disadvantages
One advantage to glue over oil as a way of “occupying” the wood before applying paint is that the glue dries much faster than oil, so oil paint over top of it is more likely to look closer to how it will once dry. Oil first will take its time absorbing and drying and you won’t know the final effect as well by looking in that moment. You would need old samples, or experience seeing your finishes over time to be able to know how they will look once they are done changing. But not knowing and watching change over longer spans can be exciting, too, for some of us : )
I’m a fellow explorer, not an expert! Sharing back to help the group project of opening doors for each other that might be helpful for someone else.
Speaking of which: MITRA looks really great, thank you! Even better than the Getty resources for what we’re doing, it seems. David Gottsegan’s books are fun and great because he always gives alternate recipes/formulas for each type of thing, and it is great to see his forums have been revived in spirit.
Best,
Eric
I must admit I am still at the stage of painting small wood items with artist’ oil paint after the object has a dry thin layer of citrus solvent/linseed oil 1:1 ratio mix applied, and panicking the next day if it the paint is still sticky.. Do you know if/which of Gottsegan’s books cover painting on wooden panels? I read many times that the Joconde was painted over a poplar panel, but when I research about paint on wood panels it often returns poeple applying a canvas to a panel before painting. I wonder if Da Vinci painted it straight on the wood or not.
Ouch, another mistake from me. Mark David Gottsegen is his name. I forgot the Mark part, and put an A in his last name . . . Apologies.
Different woods will have differing absorbencies, and one type of wood will vary based on how it is cut/what the grain orientation is–not sure of terminology . . . so that could leave your medium less absorbed and it will seem less dry, or may seem to dry faster–but I’d think it is just the speed/depth of absorption you are experiencing.
Could be the solvent; some dry gummy. For finish, just me here, thinking like a painter/having painter’s habits, I would still use higher quality artist’s solvents. Which could be overkill, I don’t know. And of course, there’s stuff marketed as “artist’s quality” as an excuse to jack the price and unload non-artist stuff. Gottsegen should have advice on what terminology to look for to get better stuff.
Artist’s paints are usually not pigment and oil and nothing else, they usually have different formulations, and may be designed for longer working time/slower drying, or formulated to be cheaper by using a lot of fillers, some of which, like wax, may extend the drying time a lot. Drying time can vary greatly by pigment, too . . .
Gottsegen definitely discusses wood as a support, but as I recall his whole approach is more about various considerations for contemporary painters than it is about historically accurate practice, unless it was still the best practice. Doerner would be of more help here. But definitely Da Vinci would not have painted directly on the wood. Typical practice was very dilute hide glue sizing applied hot, probably more than one layer, especially if it was poplar, and then multiple layers of a ground made with sizing and things like marble dust, certain chalks, worked to great smoothness after dried. Leonard was a great experimenter, though, and had his share of disasters. (Where people apply a textile on top of the wood panel, it is thought to make the painting layers less subject to inevitable changes in the wood/telegraphing grain and cracks and such. In my mind it is more of a modern practice, but I have seen icons and other things here and there with that approach.)
Someone on MITRA should be able to point you to good texts about what is known about how the Mona Lisa was made! It is amazing how much more is learned as art conservation science advances.
*I see all this discussion as excitement and volubility inspired by Christopher, and related to his reinventing poetry and incantations by interacting with old forms in new, personal ways, and I hope this has not been “thread hijack”–my intention has been the reverse.
Thanks a lot for all the details! I’ll consider asking about the Joconde on MITRA as well 🙂
Let’s hope that bringing the comments section for this entry to a boil will make Chris consider bringing back the fabled Anarchist Finishing Manual from the grave, with a long chapter on linseed oil paint! See you in another thread 😀
https://blog.lostartpress.com/2020/11/30/rip-the-anarchists-finishing-manual/
Hide glue under milk paint will likely create a crackle finish. Whether you mean to or not.
At glue strength, yes, thank you, Fitz. Crackle might be the best case scenario!
I should have been more clear and thorough, sorry. (Are you telling me my unexamined painter’s thoughts/assumptions are not audible via internet?!)
I should have mentioned it should be diluted to sizing strength rather than glue strength. Formulas are out there. Again, good catch, thank you.
After lunch I’ll read through my posts and see if there is anything else like this.
Apologies, everyone!
And there is the rabbit hole. Beware!
I tried the Allback Linseed Oil paint once . It took forever to mix and my test boards just never really cured . I am happy to wait until the LAP gurus have a proven application process a Peasant can follow before dipping my brush in again .
Once I get my bloody super international stamps, I’ll be sending you a picture of a stick chair I painted with Allback linseed oil paints, Old Red over Black, then after about a week drying, evened out with an application of oil/wax bend. Looks tops! There’s definitely a learning curve with linseed paints, and a ‘forget what you think you know,’ but once figured out, they’re a dream to use. They’re gorgeous under (and perfectly compatible with) Le Tonkinois linseed/tung varnish as well.
Natural pigments and linseed oil make a pretty paint for sure, but it may be time for another dose of mushrooms if not getting a smooth even coat of paint on coarsely carved peasant inspired furniture is causing any distress at all. Sloppiness for the sake of sloppiness is not the path to beauty, but worrying about getting a perfect finish for this batch of furniture seems to me to be kinda losing sight of the deeper aspects of the mission statement.
There is a great book out recently called The Belligerent Finisher which I’d highly recommend getting a copy of. Treat it more as a description of an attitude than a recipe book.
Hi lulu,
I am trying my best to live up to this style of furniture. The carvings/engravings I have seen are not coarse at all. They are incredibly fluid. And the painted finishes are fantastic. My work is aspirational.
Has anyone made furniture sized batches of linseed paint by hand?
Steve Voigt has very interesting info about refining linseed oil on his blog. He is using traditional techniques to prepare “clean” linseed oil with good drying qualities for his plane finishes. You can readily grind your chosen pigment into oil…and why not linseed oil paint ( a glaze) over milk paint??? Rabbit holes multiply.
Linseed oil over milk paint (the dry kind) works well and can be quite beautiful. You can mix in artist’s oil paints, oil based stains, or dry pigments to make glazes of whatever color you want. Paint or stain alone work well too. I’ve done all of those with no problems at all. You can layer shellac in the mix too for various effects and can even mix dry pigment into that.
I don’t know if Stephen Shepherd is “canon” in the LAP universe, but his book “Shellac, Linseed Oil, & Paint” is full of useful information on making oil paint and using it. He also calls into question the clam that milk paint is a traditional finish, and I’m inclined to believe he’s right. The stuff in cans is latex with ground chalk (whiting) added which you can do yourself. Oil based paints may or may not stick to that, but I’d guess they do well enough.
A fine art painter named Tad Spurgeon did a lot of experimentation with traditional methods of refining and processing linseed oil including letting it sit in the sun or bubbling air through it with a fish tank air pump. Food grade linseed oil from a grocery store washed with water a few times seems to work well. His website was recently shut down, but he’s apparently one of the first to start experimenting with that and probably wrote the material that more recent bloggers are basing their experiments on. His name makes his work pretty easy to find and it’s well written and thorough.
Ralph Mayer’s “Artist’s Handbook” is the classic on the subject and easy to find.
How are the users of linseed oil paint cleaning their brushes?
I use linseed oil soap. And you can also leave it in non boiled linseed oil .
I recently built a wall-hung cupboard for the electrical fuse box in my hallway, frame and panel doors, a basic box carcase, I was thinking of using milk paint but only had some federal blue from years ago, too bright, the local store here in the UK stock Rustoleum Chalk finish paint, drab green, only small 125ml tins which was just what I needed, the paint is great with just 1 coat, the 2nd coat was terrible, I read up a bit about chalky paint, it is so dry/thick that if you go back over the area you just covered within 2 mins the stuff just does not work, I found that having a small cup of water to hand and dipping the brush in the water every load of the brush it works out fine.
Rustoleum not only make the Chalk finish, they make Satin and Matt, for kitchen cupboards, garden furniture, virtually everything, I’m looking forward to when they bring out paint for the different days of the week, ie Monday, Tuesday etc, Diversifying again. I wonder what the difference between the Matt and Chalk finish is ? apart from the spelling.