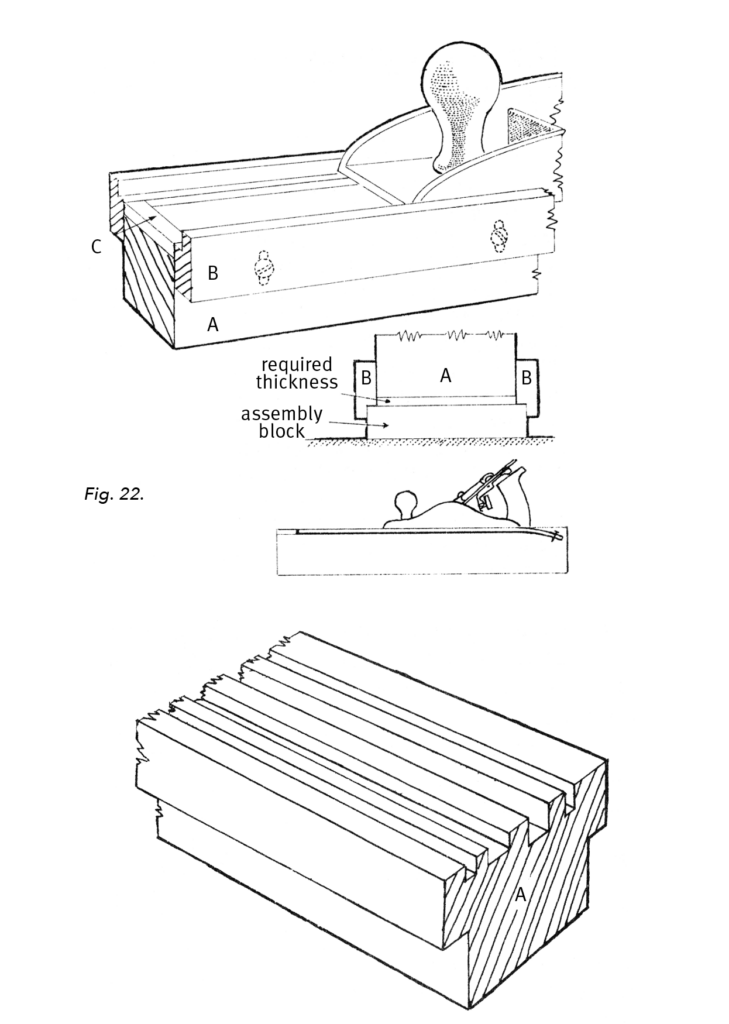
Below are two handplaning techniques from Robert Wearing’s “The Solution at Hand.” Wearing was one of the foremost experts on woodworking appliances; he wrote extensively about them for Woodworker magazine and published a number of books on the topic. In 2019, we approached Wearing about collecting the best of the appliances for handwork into one new book, and he agreed.
The result is “The Solution at Hand: Jigs & Fixtures to Make Benchwork Easier,” a hardbound book of our favorite jigs from Wearing’s career. The book covers a wide swath of material, from building workbench appliances for planing, to making handscrews (and many other ingenious clamps), some simple tools that you cannot buy anywhere else, to marking devices that make complex tasks easier.
– Fitz
Thin strips of identical thickness, such as may be required for laminating, can be accurately produced by handplaning by means of a simple jig. This consists of a base-block, A, and two rebated side members, B. The space between the two rebates must just allow free movement of the chosen jack plane. A projects below B, to be held in the vice.
The sides are glued and pinned in place using an assembly block with a true face in the plane position and a piece of ply, card or suitable spacing material of the required thickness. The illustration makes this clear. When complete, an end stop, C, is fitted.
Modifications: For the making of stringings for inlaying or musical instrument making, grooves are ploughed or cut on the circular saw in the baseblock A. In this case there is no need for rebated sides. Very thin pieces will tend to buckle when planed against a stop. This is overcome by cutting away some of the baseblock and pinning on the workpiece below the level of the blade. In this case, of course, the components and the jig must be made extra long.
An adjustable model can be made by slotting and screwing on the sides. The adjustment is made using the same method as when gluing on the sides to the simple model. Solid wood keys for reinforcing mitre joints can be produced in this manner.
Handplaning Very Small Components
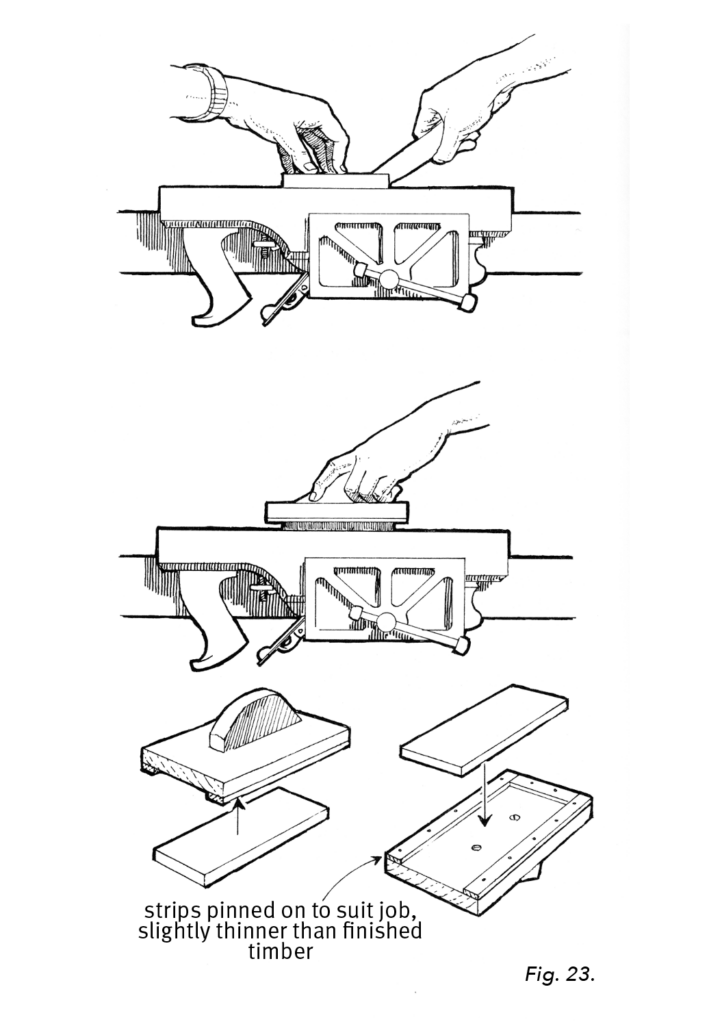
Very small components can best be planed by holding a plane upside down in the vice and pushing the workpiece over the blade. As this method gives every chance of shaving off the fingertips, a push stick is an advantage. Even better is this simple planing device. It consists of a hardwood base with a firmly secured handle. Guide pieces, thinner than the finished job, can be pinned or glued on so that they can be changed when the aid is used for another job.
Yes, highschool me discovered the fingertip removing abilities of an upside down hand plane. I think I was too embarrassed to tell anyone what I’d done at the time.
DON’T try clamping an iron plane upside down in a vise like this shows. You can do it with a wooden or transitional plane but you will surely crack the sides of an iron plane.
Have you cracked a plane body this way? I haven’t, and I clamp my (gray iron) plane in a vise all the time.
yup same here. i clamp my 60s era stanley all the time. no issues. lining the jaws with crubber helps give more grabbing power while also granting some spring in the hold so you don’t need to cinch it so hard.
Illustration looks like wood body. If using metal plane best to get low in vise and minimal force. This can be hard on old Stanleys.
I’m always careful to clamp the vice down low, so you are putting force directly into the sole instead of the sides. It works fine for me.
This is EXACTLY the solution I needed to know for a current project trouble-spot! Carry on!
Thanks for posting this. Your publication rate has exceeded my ability to purchase everything (though my wife might disagree). Seeing this better helps me understand what is in this book. Looks useful enough to own. Valentine’s Day is comming up. Hmmmm. Sweetie ….
Related to this. At one point, I was making some bench dogs to for my Lie-Nielsen work bench (no joke, I sold my 5L 5 speed 1990 Mustang to buy it; kinda miss the car but not enough to regret the decision). As such, I needed some 1/16″ or 1/8″ strips. I basically took my router plane, a chisel, and some pine to create a housing dado that was proper depth. Put the plane centered over the groove, and cyano acrylate glue some strips slightly wider the plane. Worked like a charm to thickness the wood. It literally took all of 10 or 15 minutes to make the jig. I like this more permanent jig better.
I’ve used a similar style of jig to make octagonal spindles and it works well on shorter stock, not so much on longer but that may have been a flaw in the way I made it (several pieces rather than one or two). Wound up using software to figure out the depth of the side walls relative to the bottom of the V that supported the stock (FWIW 0.9″ for 3/4″ stock).
1.41 is the ratio to work at. Look up spar gauge.
That looks useful, but at the time I was planning on doing around 60 spindles. Doing all that by sight and making it consistent seemed problematic so a jig seemed the best way to not muck things up too much since the jig bottoms out at the right size. Will keep one of those in mind for when I eventually tackle a one-off like a paddle though.
I clamp the handle of upside down low angle jack plane in the vise with the “humps” of the plane body resting on bench top. Not white knuckling the pieces being planed so hopefully not stressing the handle. Been doing this for years without a problem…knock on wood!