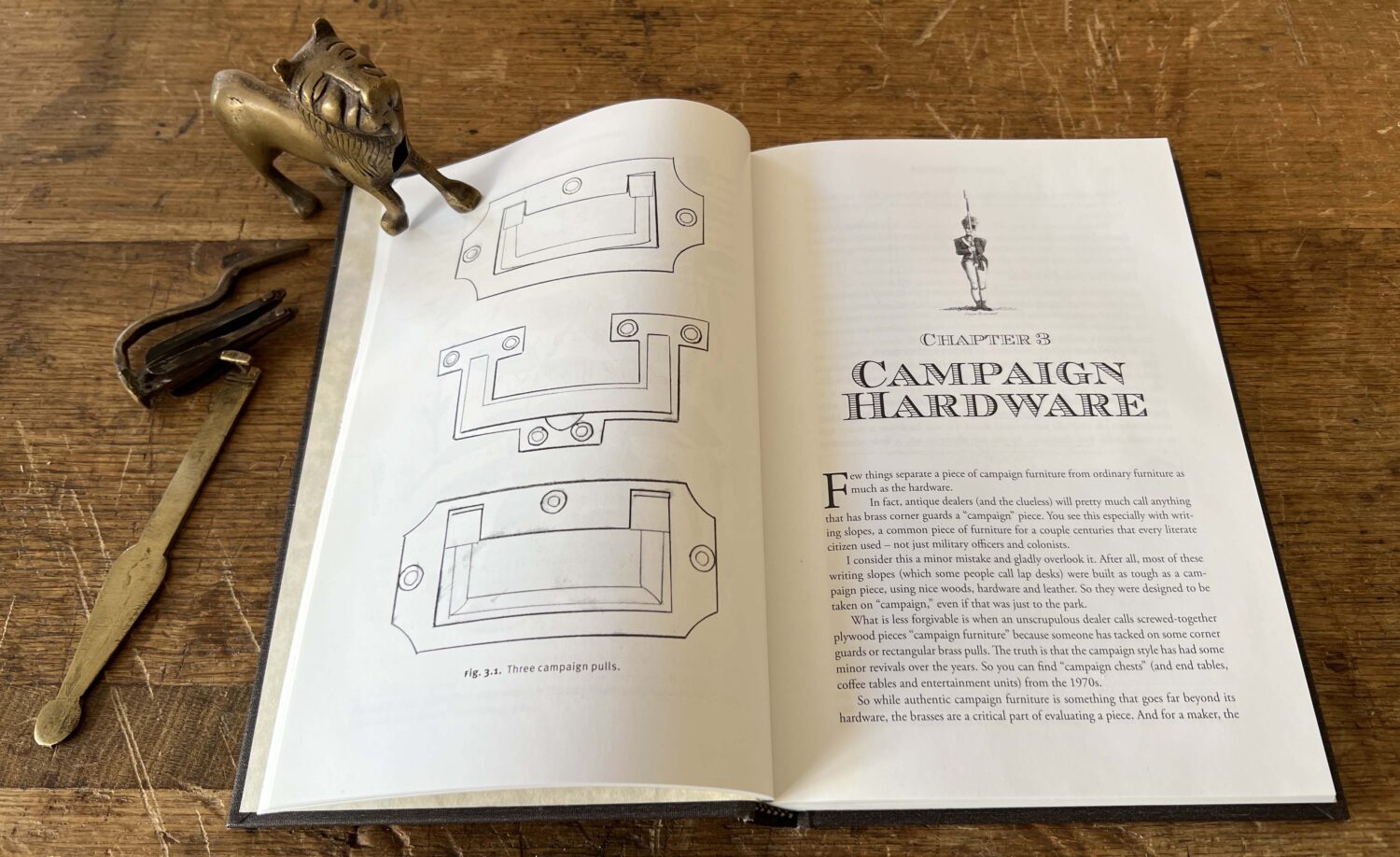
The following is excerpted from Chapter 3 of Christopher Schwarz’s “Campaign Furniture.”
For almost 200 years, simple and sturdy pieces of campaign furniture were used by people all over the globe, yet this remarkable furniture style is now almost unknown to most woodworkers and furniture designers.
“Campaign Furniture” seeks to restore this style to its proper place by introducing woodworkers to the simple lines, robust joinery and ingenious hardware that characterize campaign pieces. With more than 400 photos and drawings to explain the foundations of the style, the book provides plans for nine pieces of classic campaign furniture, from the classic stackable chests of drawers to folding Roorkee chairs and collapsible bookcases.
Few things separate a piece of campaign furniture from ordinary furniture as much as the hardware.
In fact, antique dealers (and the clueless) will pretty much call anything that has brass corner guards a “campaign” piece. You see this especially with writing slopes, a common piece of furniture for a couple centuries that every literate citizen used – not just military officers and colonists.
I consider this a minor mistake and gladly overlook it. After all, most of these writing slopes (which some people call lap desks) were built as tough as a campaign piece, using nice woods, hardware and leather. So they were designed to be taken on “campaign,” even if that was just to the park.
What is less forgivable is when an unscrupulous dealer calls screwed-together plywood pieces “campaign furniture” because someone has tacked on some corner guards or rectangular brass pulls. The truth is that the campaign style has had some minor revivals over the years. So you can find “campaign chests” (and end tables, coffee tables and entertainment units) from the 1970s.
So while authentic campaign furniture is something that goes far beyond its hardware, the brasses are a critical part of evaluating a piece. And for a maker, the brasses are one of the major expenses when building a piece. When you shop for hardware, it’s tempting to buy pulls that look OK from 10′, but feel like tin foil in the hand.
This short chapter is designed to introduce you to the different kinds of hardware and the ways they are made – cast, extruded, bent, welded and die-cast. And to teach you a bit about the strategies for installing inset pulls, corner guards and the other inset plates common on campaign pieces.
How Hardware is Made
Like your tools, the brasses for your furniture can be made in many different ways. The process affects how the hardware looks, feels in the hand and costs.
A lot of campaign brasses I’ve studied have been cast. There are several ways to cast metal; the three most common methods for making hardware are sand casting, die-casting and investment casting (and their variants).
While all these casting processes are different in their details, they are the same in their basic idea: There is a mold made in the shape of the hardware and it is filled with molten metal. When the metal cools, the casting is finished and assembled.
All three types of casting have advantages and disadvantages for you, the furniture maker, and I’ll be covering them in some detail here. Most woodworkers are woefully uneducated about the way hardware is made and as a result make bad decisions. As you are about to see, a little education about metal casting can go a long way toward improving the quality of your projects. Let’s start with sand casting.
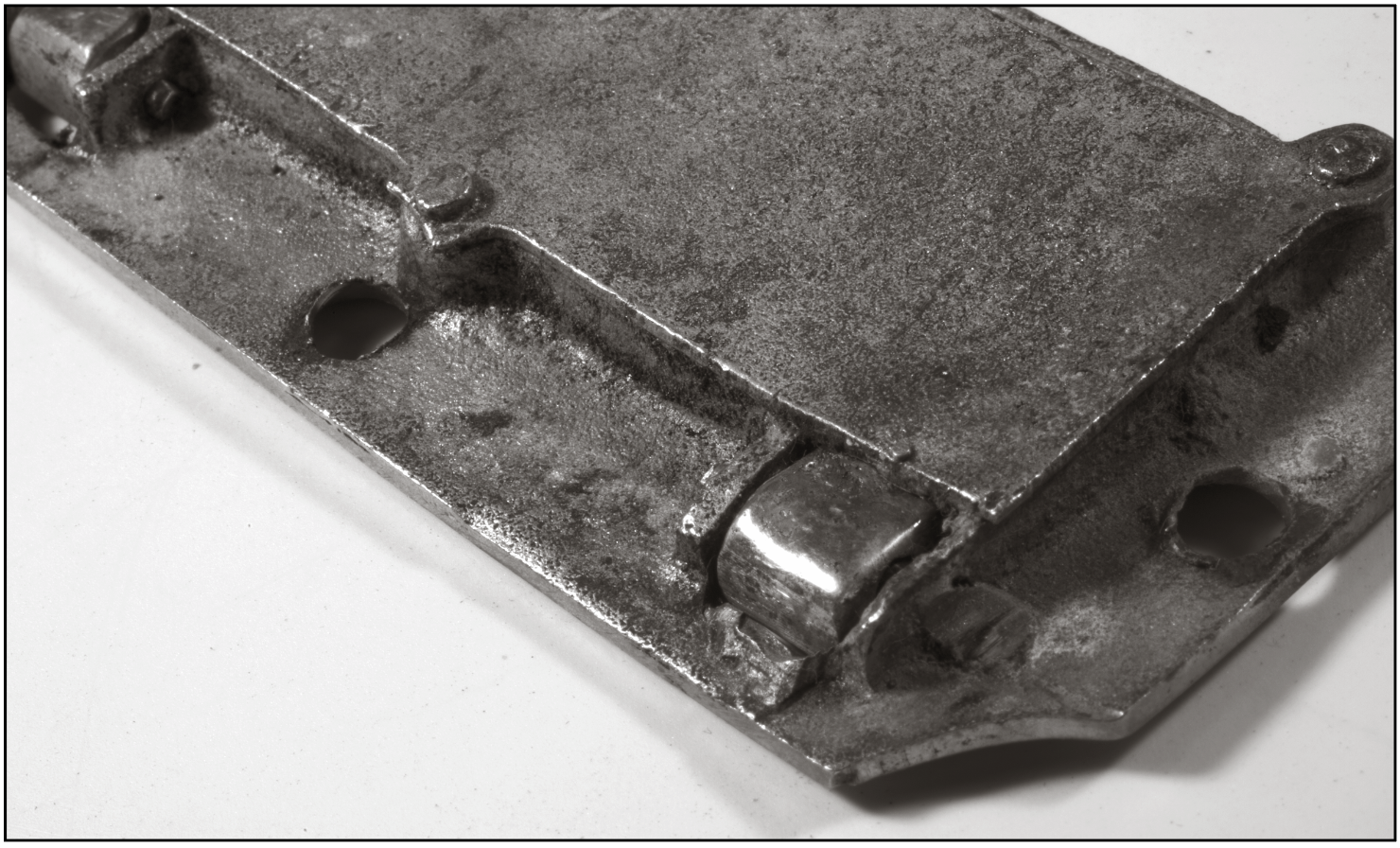
Sand Casting
Many handplane bodies (and woodworking machines) are made using sand casting. It allows a maker to produce castings in an economical way. The downside to sand casting furniture hardware is that the surface finish is never nice enough to use as-is. The manufacturer usually needs to finish the visible surfaces and touch points. This can be labor- or time-intensive.
But what is more important for a furniture maker is that the finishing process can make the parts non-interchangeable, especially if the pieces are finished by hand. The upside is that hand-finished hardware with small variations can be beautiful.
Hardware made this way is called “sand cast” because a sand that is moistened with oil or chemicals is used in the casting process The casting begins with a “pattern,” which was traditionally wood, but is now typically aluminum for pieces of hardware. Then either the pattern or a matchplate or some other representation of the finished object is used to make depressions in two boxes of sand – one is called the cope and the other is called the drag. These two bits of sand are put together and the cavity is filled with molten metal via tubes called “sprues” in casting parlance. Gates are put into the matchplate or simply cut into the sand itself to allow the metal to flow completely through the part and out the other side. This helps the metal completely fill the cavity and helps prevent shrinkage (which is a cause of surface pitting).
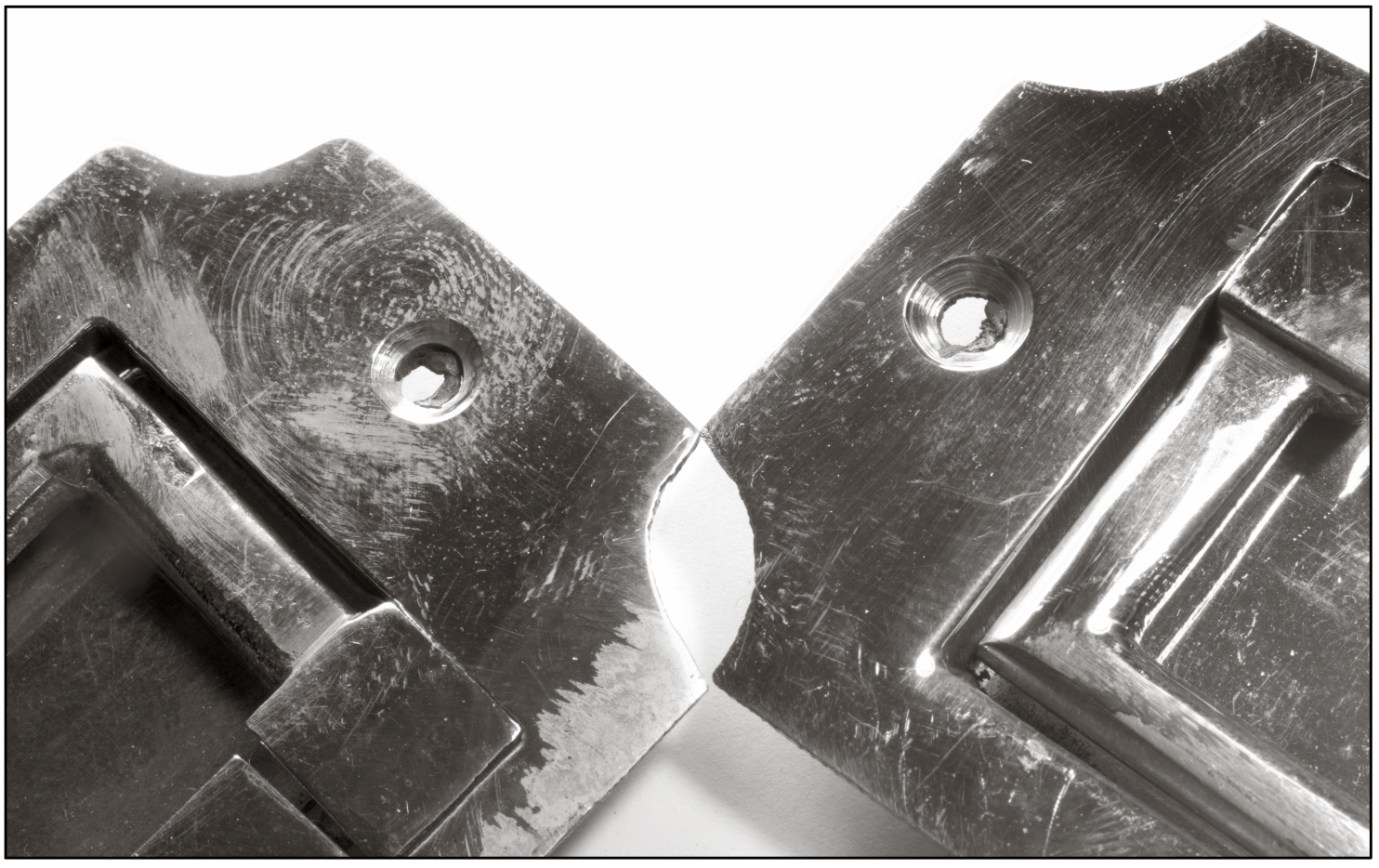
After the metal hardens, the sand is removed (and reused) and the resulting metal shape is finished – by grinding, filing, polishing, machining or some combination of these processes. After grinding and/or filing, all cast parts are put into vibratory tumblers filled with a variety of different medias to get the surface finish smooth. The tumbling is the key process that turns a very rough casting into a smooth finished part. Machining typically takes place after tumbling.
Sand casting produces hardware that typically has a substantial feel. Its components are fairly thick. The unfinished faces of the hardware will typically be a bit coarse – like sand. (Proper tumbling eliminates this rough surface.)
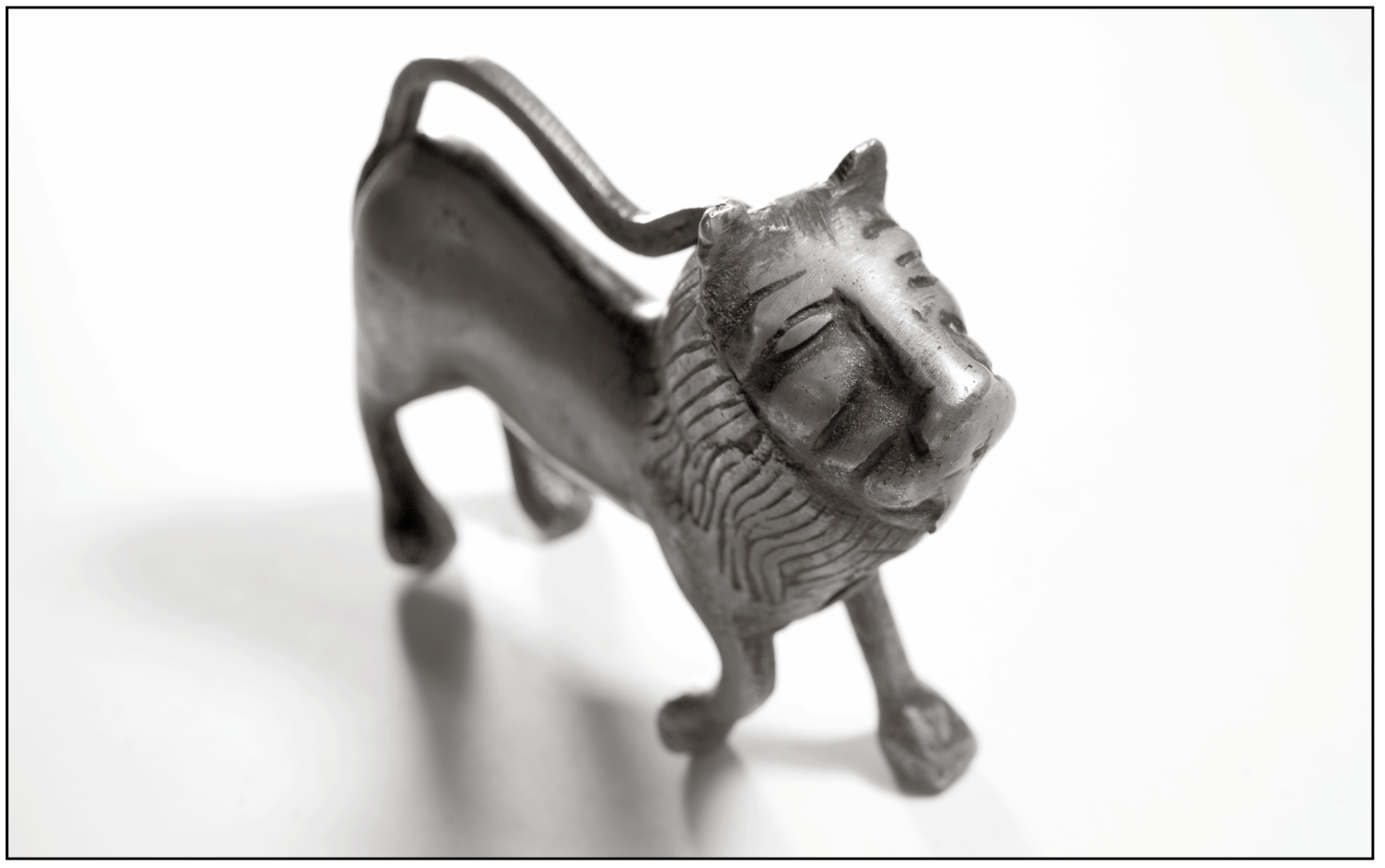
These qualities are the nice things about sand-cast objects, but there are some downsides with sand-cast hardware. The level of detail isn’t as good as with other casting methods. So a sand-cast lion’s face will look a bit “blurrier” than one cast by other methods.
Also, the sand-casting process can result in some variance in dimensions. This is not a big deal at all if you install your hardware piece by piece. But if you want to have one router template for all your inset sand-cast pulls, you might want to closely examine the pulls first and see how close in size they are to one another.
Believe it or not, sand casting (the oldest form of casting, by far) can be done at home or even on the beach. Peter Follansbee once showed me ring pulls that he and other researchers at Plimoth Plantation made on the beach. And Thomas Lie-Nielsen fondly recalls how his father – a boatbuilder – would cast the keels of his boats on the beach.
Investment (Lost Wax) Casting
Investment casting is a more complex process than sand casting, but it is suited for small objects and short runs, and results in some fine details that might not require additional finishing.
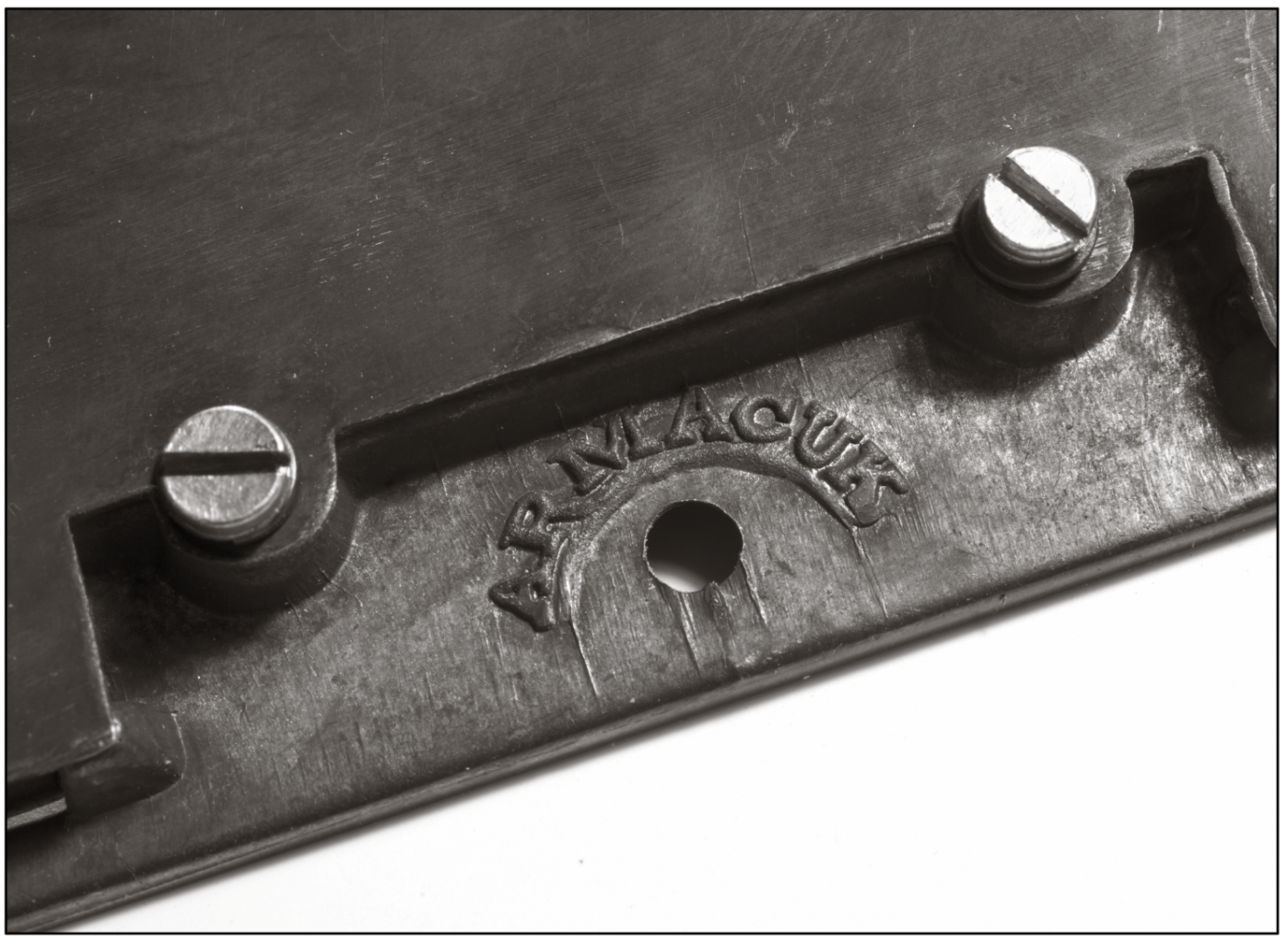
The process is complex (and can be more expensive than sand casting), but it starts with a pattern that goes through several stages of production involving creating a wax mold of the object that is then covered in a ceramic material.
Investment-cast pieces of hardware have few downsides, other than the fact that they are typically more expensive than a similar sand-cast object. They allow much finer detail than a sand-cast piece, can have a much thinner cross-section and have the presence of a sand-cast piece.
Orion Henderson, the owner of Horton Brasses, says that investment casting can be pretty economical for very small parts. He says the downside to investment casting is that the metal suffers from greater “shrink” – when the metal cools it gets smaller, leaving pitting; the part gets so small that sometimes the part is not usable. The molds need to be oversized to account for this. Because of this shrinkage, Henderson says, investment casting is fine for small parts but not as suitable for big pieces – a bed wrench for tightening bed bolts, for example.
Die-cast Hardware
Die-cast objects get a bad rap. And that’s because die-casting has been used with lightweight raw materials to produce lightweight (sometimes featherweight) pieces of furniture hardware. They are inexpensive and look good from across the room. But once you grab the hardware, it can feel insubstantial.
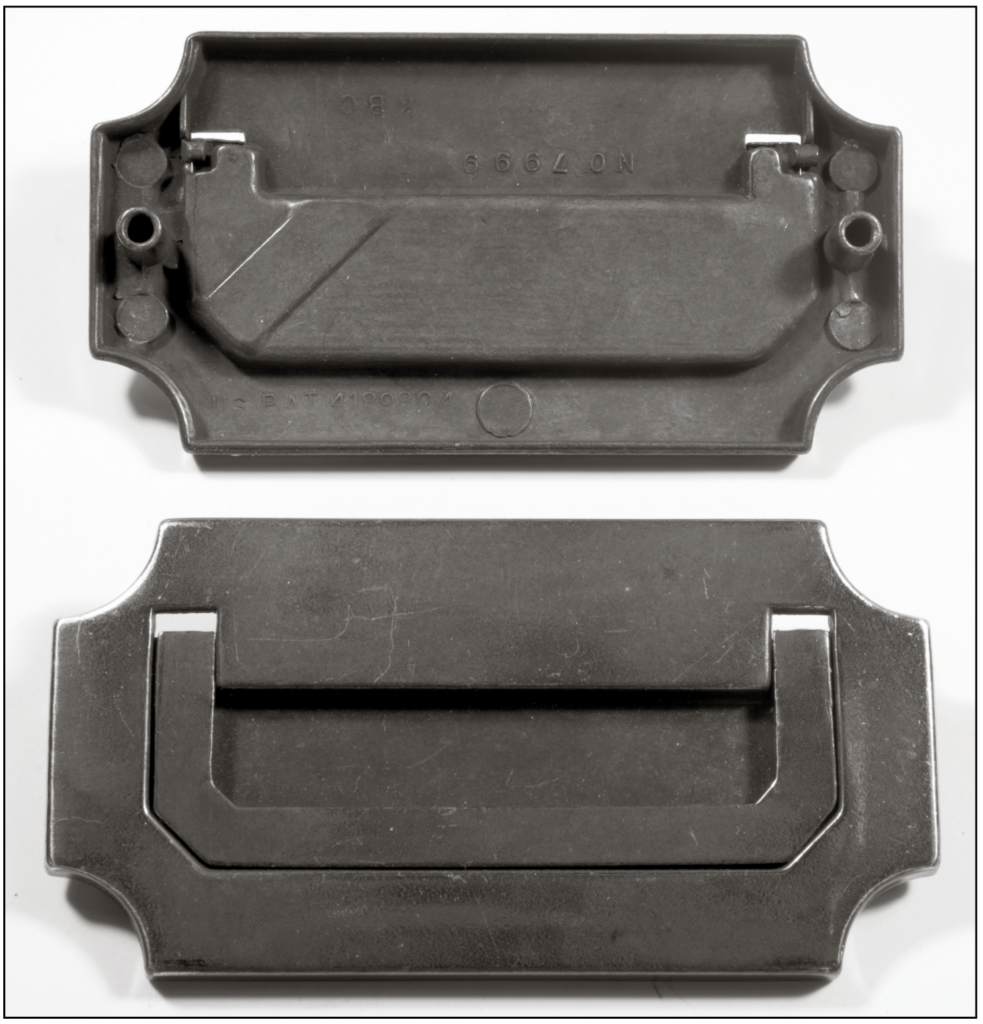
Like all casting processes, die-casting has a mold – in this case a two-part metal mold called a die that is machined with hollow areas. Molten metal is injected under pressure to fill the hollow areas in the die. Then the two pieces of the die are mechanically separated and the finished part is ejected.
Die-casting produces parts that require little or no finishing. The parts are remarkably consistent. You can make many of them in a minute, and the individual units are inexpensive as a result. So why do some people dislike the process?
Like all technology, die-casting isn’t the problem. It’s how it is employed.
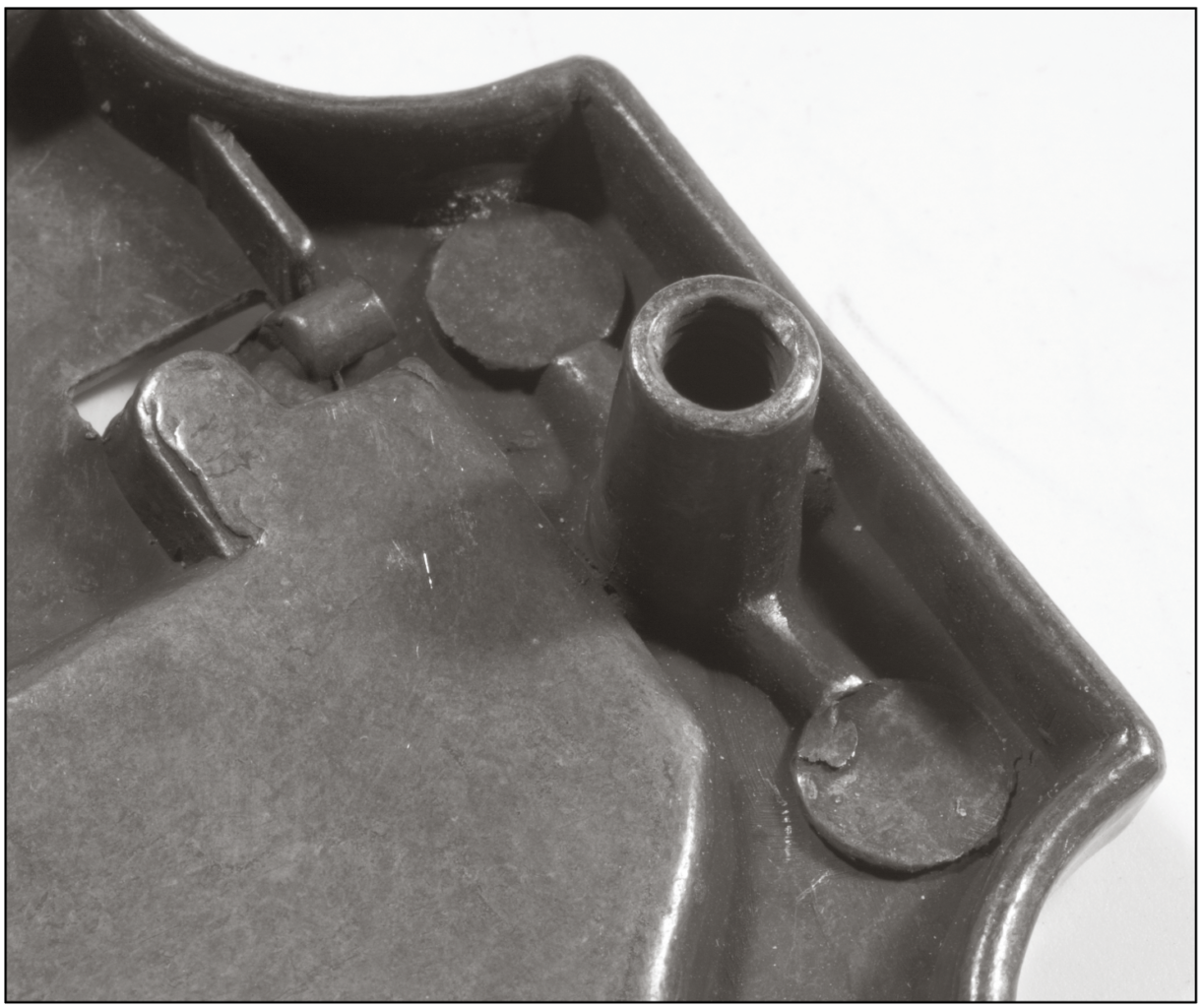
You can use copper (or even lead) in die-casting to make a nice and heavy piece of hardware. (In fact, die-casting was invented in the early 19th century to make movable lead type for printing presses.) But in many instances, the manufacturer will use lightweight metals, such as aluminum, tin, zinc or Zamak, an alloy of lightweight metals.
To be honest, these lightweight metals are fine for some pieces of hardware. A drawer knob, for example, can be just fine when it is die-cast. But when you get into pieces of hardware that have movable parts that you grab, such as a drawer pull, the whole thing can feel chintzy.
You can identify die-cast pieces of hardware easily, even if its catalog description doesn’t mention the process. The finished casting is pushed out of the die by ejector pins – movable rods inside the die. These pins leave telltale round marks on the hardware. Look for them on the back of the hardware, and you’ll start to see them everywhere.
Bent Plate
When it comes to the corner guards that are prevalent in campaign furniture, many modern manufacturers will use thin brass plate that is bent and sometimes welded at the corners.
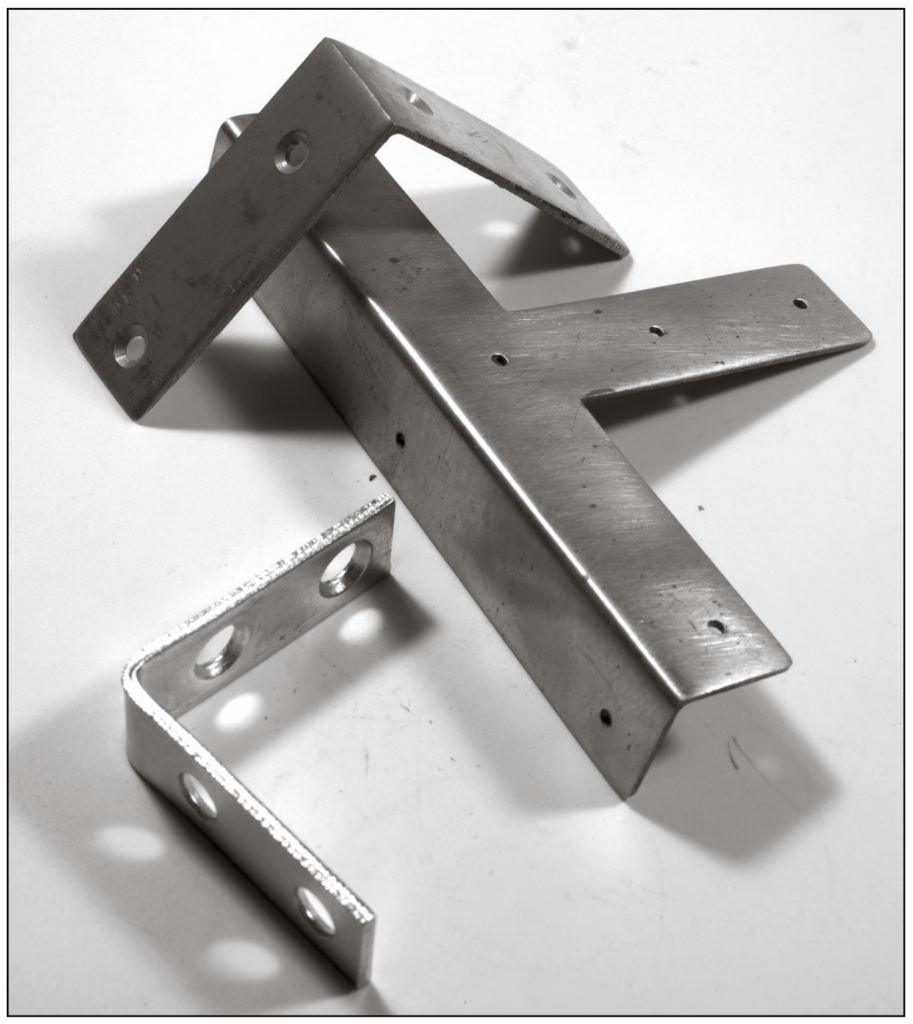
This might sound like a cheap shortcut. It indeed is a shortcut compared to cast-brass corner guards, but it can be a good shortcut.
The plate is more consistent in thickness than any piece of sand-cast hardware. So installing it is easier because you can use one depth setting on your router plane or electric router.
The downside to using brass plate is that the corners of the hardware – both the inside corners and outside corners – are rounded because of the bending process. The cast corner guards can have sharp inside and outside corners. It’s a subtle difference, but it is noticeable once you are sensitive to it.
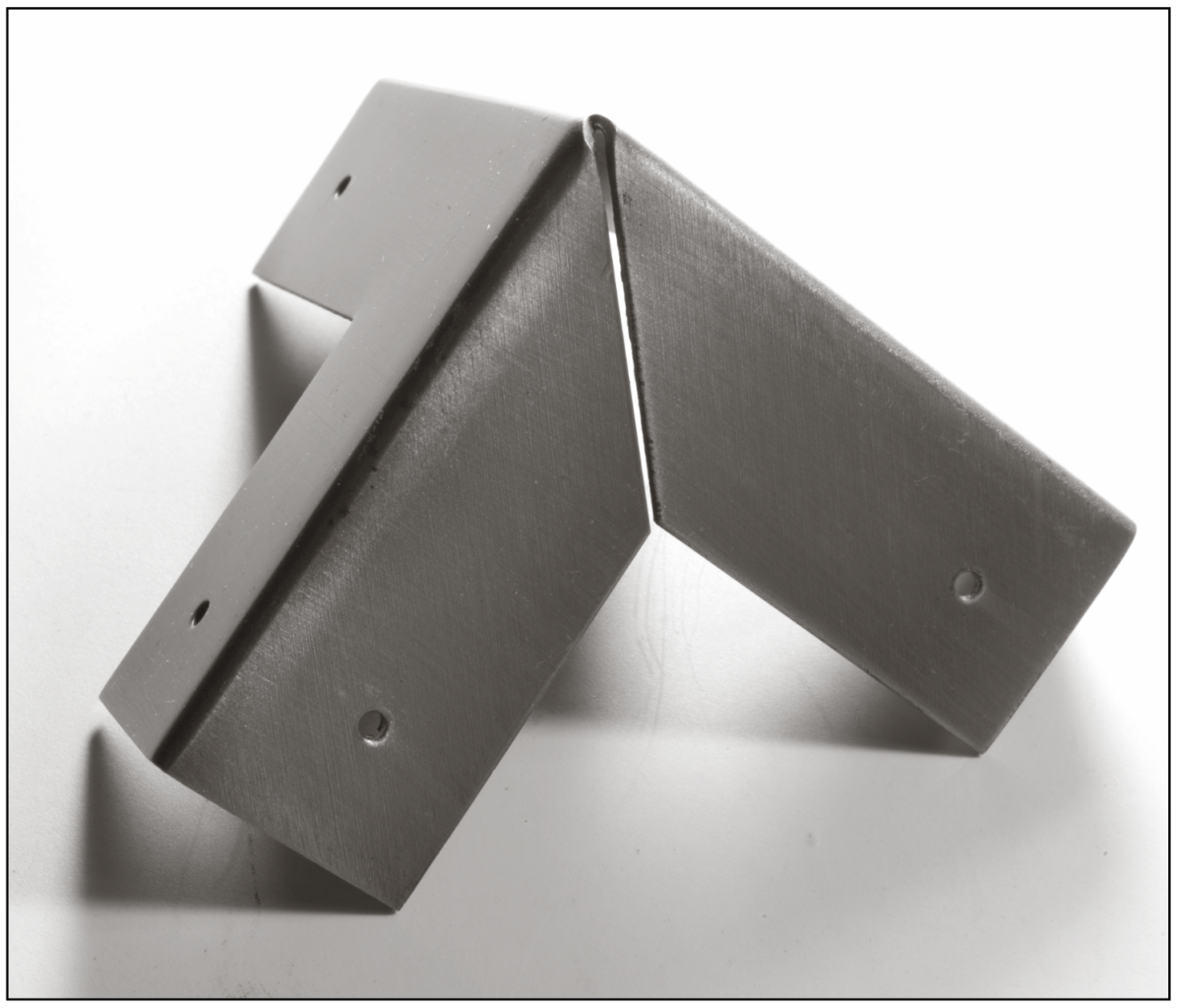
If you do use hardware made from bent plate (and I do), look for welds at the corners when the hardware covers three surfaces, such as when you have a brass guard designed for the top corners of a chest. A quality guard will be bent then welded. Some of the less expensive guards are simply bent with no weld. This looks just weird and wrong to my eye.
Extruded Hardware
Some of the hardware you’ll see in catalogs will indicate it is “extruded.” Extruding hardware parts is analogous to making macaroni or using the Fuzzy Pumper Barbershop with Play-Doh. Metal (cold or hot) is pushed through a die to make a finished shape that is then cut up to finished lengths.
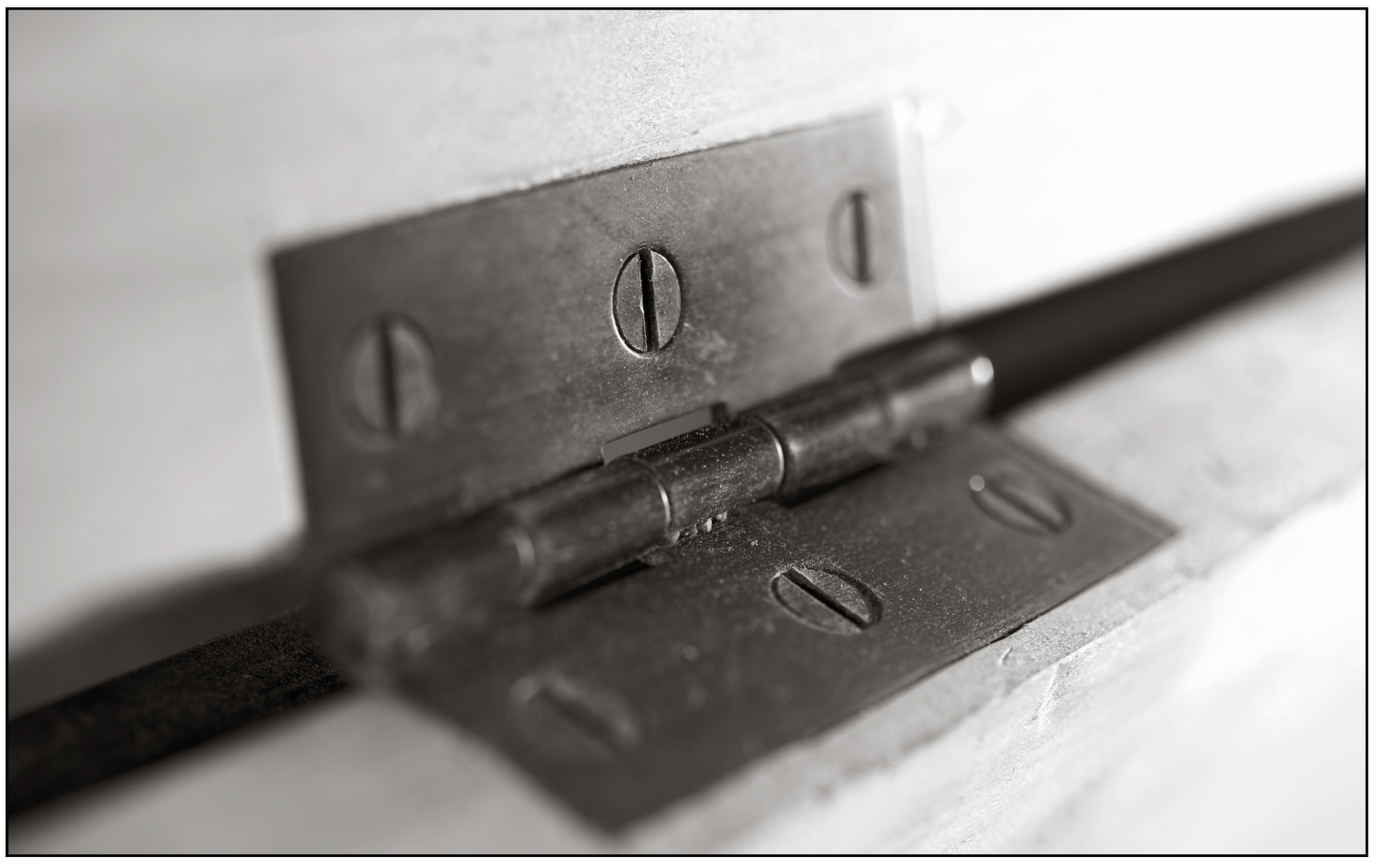
Many quality hinges are made with extrusion. The leaf and barrel are extruded. Then they are cut to length and machined to accept screws. The only downside to extruded hardware is its price.
Choosing Hardware
So why is all this talk about hardware manufacturing important? I think that hardware can make or break a piece of campaign furniture. A zinc die-cast drawer pull on a teak chest is like a nugget ring on a millionaire’s hand.
When I am shopping for hardware for a piece of campaign furniture, I like to purchase a sample pull, hinge or corner guard to inspect the quality before dropping hundreds of dollars on a suite for a chest or trunk.
The samples also help me ensure that the color and finish on the hardware will work. And the color of the brass is another can of worms we need to open.
If you buy your hardware from several sources for one piece of furniture, the chance of them matching in color is tiny. And the last thing I want to do after spending $700 on pulls is to open a chemistry set to strip the hardware pieces and color them.
If you like dabbling in solvents and other noxious fumes, you can easily find information on how to strip the lacquer from your hardware and color it with ammonia fumes. Me, I have enough volatile organic compounds in my life. I’d rather leave that to other people.
That’s why I take one of two strategies when buying hardware: Either I buy all the pieces from one maker to ensure they have a consistent color, or I ask (nicely) if the hardware seller can color the pieces. The better hardware merchants are happy to do this for you. In fact, some will even bring in hardware from other sources and color your entire suite so everything looks the same. It might cost a little more to go this route, but the results are worth it.
One last note about buying hardware and I’ll shut up: I think slotted screws are really the only kind of screw that looks good on a campaign piece. Phillips screws are a 1930s invention that were intended for assembling cars – not fine furniture.
Once you get your hardware in hand, you can build the piece and install the pulls, knobs and corner guards. There are several strategies for creating the recesses for the hardware, ranging from a chisel and a mallet all the way up to templates for the electric router and pattern-cutting bits.
I found this post very interesting and informative,
I specialized in 19th century building restoration. There was a period where door hinges were made with buttons and recesses on the barrels. Were these made by casting one side, then using that casting as a part of the mold for the second side? This has puzzled me for many years.
I would have to see a photo. Usually in casting when you see round buttons those are evidence of where the casting was attached to a sprue (the channel of metal that flowed through all the pieces). These are usually ground off. But not always.
I just wish there was more on late early 19th or late 18th century campaign furniture. Most books on the subject do a great job of covering the later 18th which focuses largely on what was used by the British in Africa and India. Would love to see some that focus more on say the early American uses around the American revolutionary war or the war of 1812.
Of course when I finally start making a campaign chest hardware becomes even more scarce 🙁
Excellent piece, and a great addition to one of my favorite Lost Art books
Thanks Megan for sharing. I have been curious about this book and that excerpt was helpful.
Believe it or not, I haven’t bought all of the LAP books, yet. Your rate of publishing is exceeding my mad money. Plus, I may need to save up if you end up teaching an ATC class at Port Townsend. It’s the only reason I refrain from building one on my own.
Great excerpt. Succinct, use explanations of the different casting processes. One question: are there ever occasions where a Phillips-head screw would be appropriate for fine furniture hardware? This is a serious question. None come to mind, but I’m always open to being educated.
I have no problem with modern screw heads on the interior of a period piece (as long as you aren’t trying to make a period replica).
I’ve seen original midcentury pieces with Phillips screws. So those would be totally fine with me for a repro.
I’m not trying to be a snob. Promise. Just trying to get my pieces to look as good as I can.
Previous comment was mine. Anonymity was due to fat fingers used too quickly
Period proper screws would likely have tapered slots cut with a similar taper to the taper on a Knife File, or at least that is my experience when looking at screw heads from the early to mid 1800s or earlier.
I’m not sure when machined parallel slots became common, but I would presume US Civil War or later.
The tapered screw slots are sort of nice, because you can wedge the screw onto the tip of a tapered flat head screwdriver for less slippage when driving.
My brother and I had bedroom furniture, as kids, in the “campaign” style, a la JCPenneys. Totally same looking pulls as above, die cast in “antique brass” look, and later, a handle or two fell off from the abuse of two boys. Straps around corners and all … held in place with a sort of cut-head nail/tack. My mother, an art teacher, was aware of “styles” (and good at colors and all kinds of other stuff), but maybe not actual “campaigns”. She knew the reason for its being, but maybe not the engineering behind its construction.
Later, I became a musician and experienced what Campaign should have meant – if you can’t lift the speaker cabinet by its handles, they’re no good. If you can’t shove the road case into the corner of the van, for fear of bending up a corner, the corners are no good. In fact, modern “Campaigns”, aka “warfare” use the same or better road cases than musicians on tour. Dropped from a helicopter.
But nobody wants that in their house. It is not “furniture”.
My wife and I fell for the look of Campaign at Arhaus furniture, a mini chain in our part of the country. About 50% of the casework is correct. In one place, however, they applied a “foot” in place of what should have been a continuous member, top to bottom. Those feet have not snapped off only because I caught the error. Only god knows what wood species. The hardware is not bad – heavy, bent strapping, attached with similarly colored zinc #8 flat head screws. Not a durable piece by any measure. Reminiscent of Campaign, but not Campaign.
I sometimes tend to think that re-creating something whose purpose has been supplanted is a bit precious. Nobody’s campaign furniture will ever again be hauled, on camel’s back, across a desert. There is no purpose to this furniture, except as a recreation or reminder of days past.
But by this narrow viewpoint, any table could be supplanted by the $39.99 folding table from Costco. Either will provide a reasonably flat surface approximately so high from the ground, etc.
I kinda like the “toughness” and “practicality” of Campaign furniture. It’s “manly” stuff, and I like the look of woods and metals. But yeah … maybe the only campaign would have been if my wife and I had bought such furniture before moving from college apartment to college apartment across country and back. Or hell, road cases might have been the appropriate pieces for us. In either case, we could send it along with our kids as they move around before settling down.
(what we actually bought was Pine Factory furniture, which could not be killed by any means)
(PS: I buy or build much better furniture now – I can’t afford to keep buying the cheap stuff)
I know folks, myself included, that do still use campaign furniture as it was intended. Granted we are not in the majority by even a fantasy, but one the festival and fair circuit, and in some field schools that setup for long periods, you still the old furniture and new pieces still fulfilling the old duties. I actually used a couple pieces I built from the this book on last round of the Festival circuit.
Another modern use of campaign furniture, and it’s later off-spring patent-furniture, is for small homes and guest spaces. One somewhat lesser known feature of campaign furniture was that it could often serve dual tasks. A common example is the camp bed, during the day it could collapse back in to a “chest of drawers” or love seat so that the bed was not taking valuable tent space while providing a second function; and at knight convert to large size comfortable bed. These beds were far more comfortable than modern cots or even air mattress.
Many campaign pieces actually had “road cases” to protect them that would also double as extra storage and such on-site. Just because the furniture is sturdy, did not mean they did not want ot keep it looking nice when being hauled around. So while it may not be going to war these days, the style can and does still do it’s orginal purpose quite well.
I’ve been known to rant about screws. Cross head screws (Phillips, for example) have no place on pieces I build. For one thing, cheap cast brass screws are about as hard as dogpoo and break easily. Some are steel poorly plated and also unworthy. When I started seeing iron screws holding brass furniture on period muzzleloaders and proper modern made pieces, I began binning the screws included with hardware and using slotted steel screws. Cad plating gets removed in muriatic acid from the home store, outdoors, because of fumes. Then thoroughly dried in a warm oven, handled with disposable gloves to avoid hand fat contamination, and blackened with cold gun blue solution such as Birchwood Casey. Once suitably blackened, a good coat of oil such as Ballistol will stop rust. I like the iron-brass interface. And don’t get me started on hex-head nuts and bolts. A little effort will locate square head black iron nuts, lags, and such. Hardware should look right.