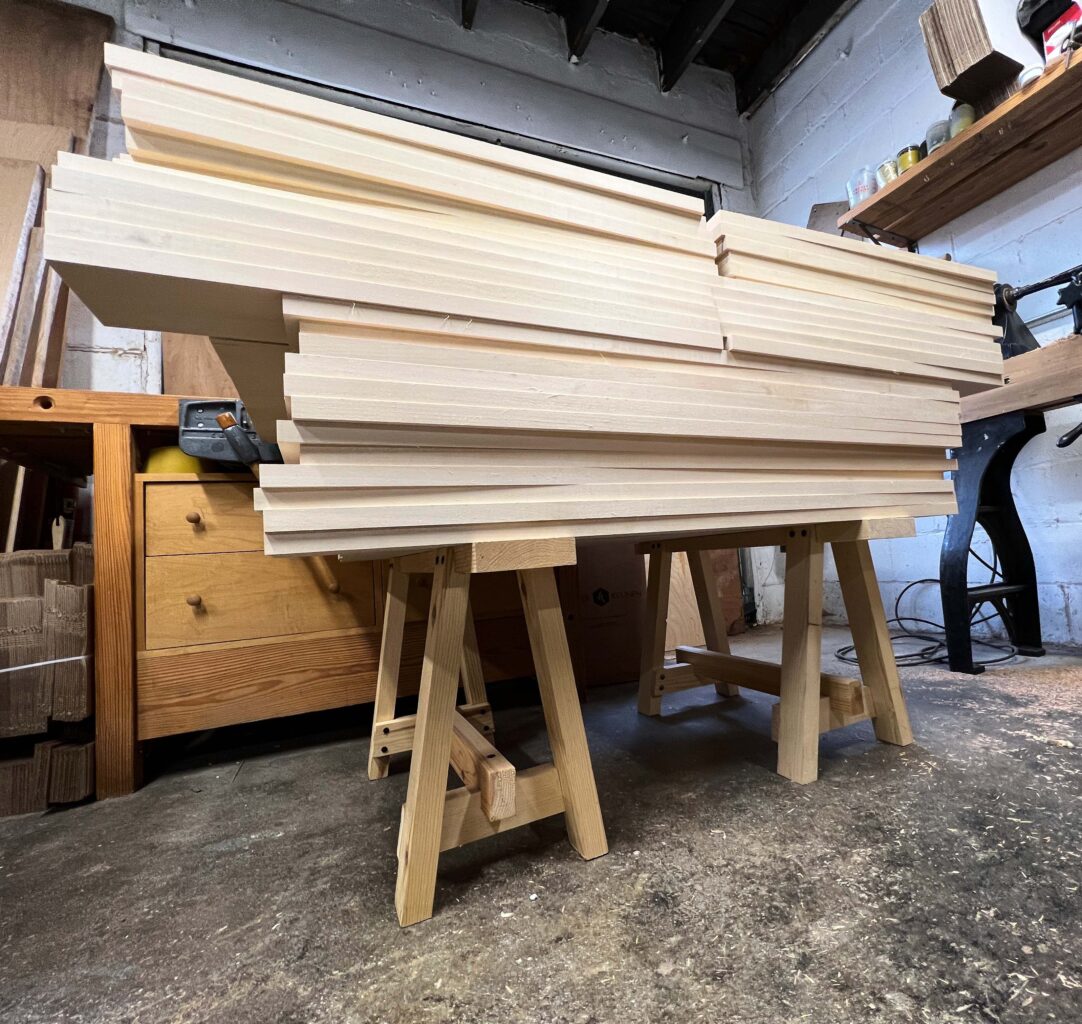
One of the most difficult things of late has been sourcing my beloved sugar pine for tool chest classes. It’s “imported” from the West Coast – and with lumber companies struggling to fill demand and the still-high cost of shipping, it has been impossible to get. I’ve heard time and again from my local supplier that “we expect some next week,” but no joy. So I had to find another solution.
I looked for Eastern white pine (another good tool chest choice that’s usually easier to get around here than sugar pine), but all I could find was #2 (at best), and usually too thick (I like a full 7/8″ for the “Anarchist’s Tool Chest” builds). Another decent option is poplar – but it’s harder to cut and chop, so it takes longer for students to work their way through the 52 dovetails that go into this chest (if you go the poplar route, 3/4″ is thick enough – no need for the additional weight). I’ll use poplar for the ATC class if that’s all I can get – but I don’t like to (though it is typically an economical choice). I want my students to have nothing but success, and that’s easier to achieve with a softer wood that has a better “mash factor” – by which I mean you can get away with squeezing a few joints together that really shouldn’t go together because they’re slightly tight, or the cuts aren’t quite straight. Everyone needs a little forgiveness now and then, and poplar has less of it to give.
So, on the recommendation of Jameel Abraham of Benchcrafted, I got in touch with the Amana Furniture and Clock Shop. (Amana Colonies is in Amana, Iowa – it’s where Benchcrafted holds Handworks which, by the by, is now scheduled for September 2023.) Amana cuts and kiln dries linden from the property for use in the shop’s own projects, and Jameel thought there might be some to spare some for tool chest kits. He put me in touch with Chris Ward, sales and manufacturing manager, who worked with his team to make a sample kit for me to try out earlier this year.
I was sold, and I ordered 13 more kits – seven for the class that concluded yesterday, and six for my February ATC class (to save money on shipping). I can’t make the kits for less than Amana charges (and right now I can’t even get material) – and they have better facilities and industrial-sized equipment for making the multiple large panels for many chests all at once. Plus they have more than one person to do it! And to be frank, they can produce better large panels than can I, because they have a panel clamp system and a wide-belt sander to level the seams if need be. I have K-bodies and handplanes (which work just fine – but not quickly when there are 28 panels to glue up and flatten). I did the final squaring and sizing in our shop…because I’m anal retentive. But perhaps for my next order, I’ll have their team do that, too; my back is not getting any younger.
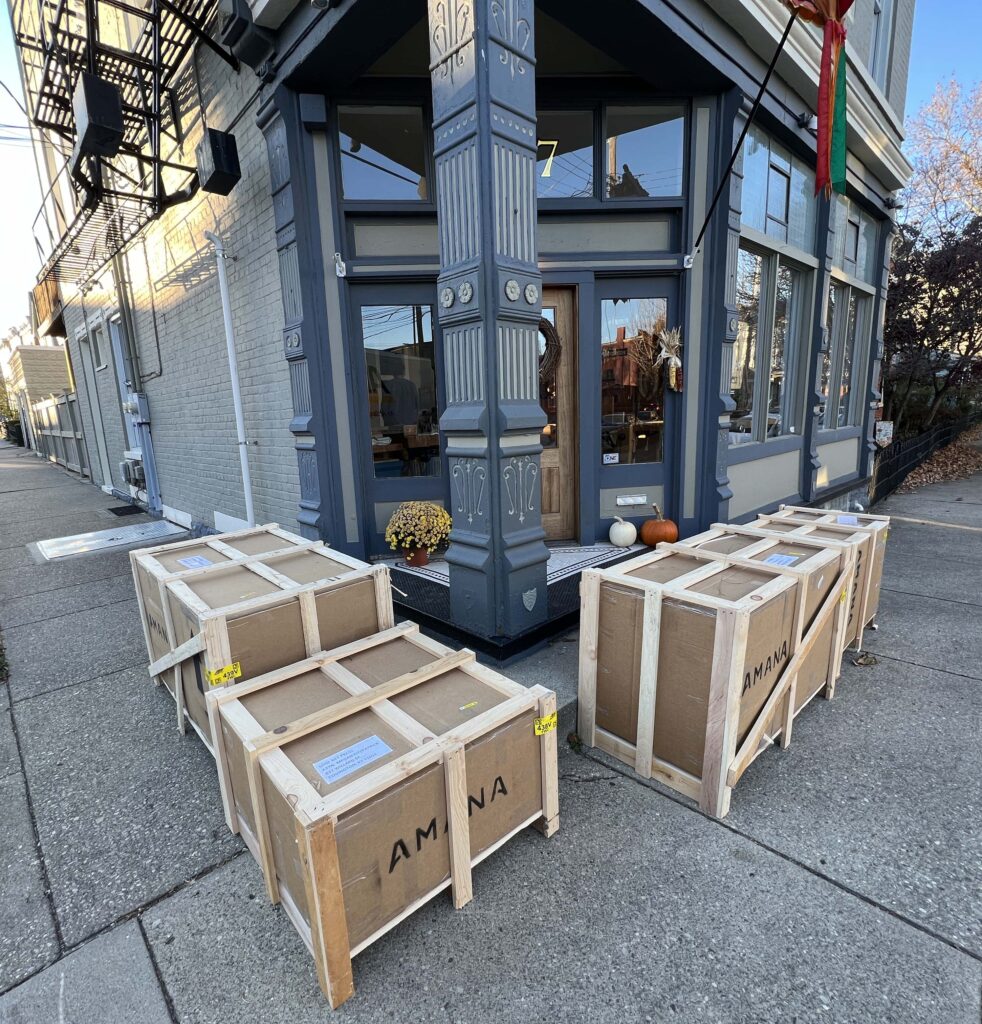
But I wasn’t completely convinced on the linden (which is also known as basswood and American lime) until we started cutting the joints. With experience now in a class setting, I actually think it is in some ways better than pine – there are no sap pockets or streaks, so saws don’t get gummy and therefore cut more smoothly for longer (no need to stop and clean them), and it’s a little less fragile on the corners. That makes sense, given that it’s slightly harder on the Janka scale (sugar pine is 380; linden is 410) – but not so much more dense that it weighs significantly more. (I meant to weigh one of the finished linden chest for comparison…but I forgot. But I did help lift four of the six into various vehicles, and I’ve lifted dozens of pine ATCs into cars and trucks over the years, and I noticed little weight difference. I’d guess maybe 5-10 additional pounds.) It also takes paint nicely – much like pine and poplar. I tested General Finishes “milk paint” on an offcut, and was pleased to find that two coats will likely be sufficient (at least in dark blue).
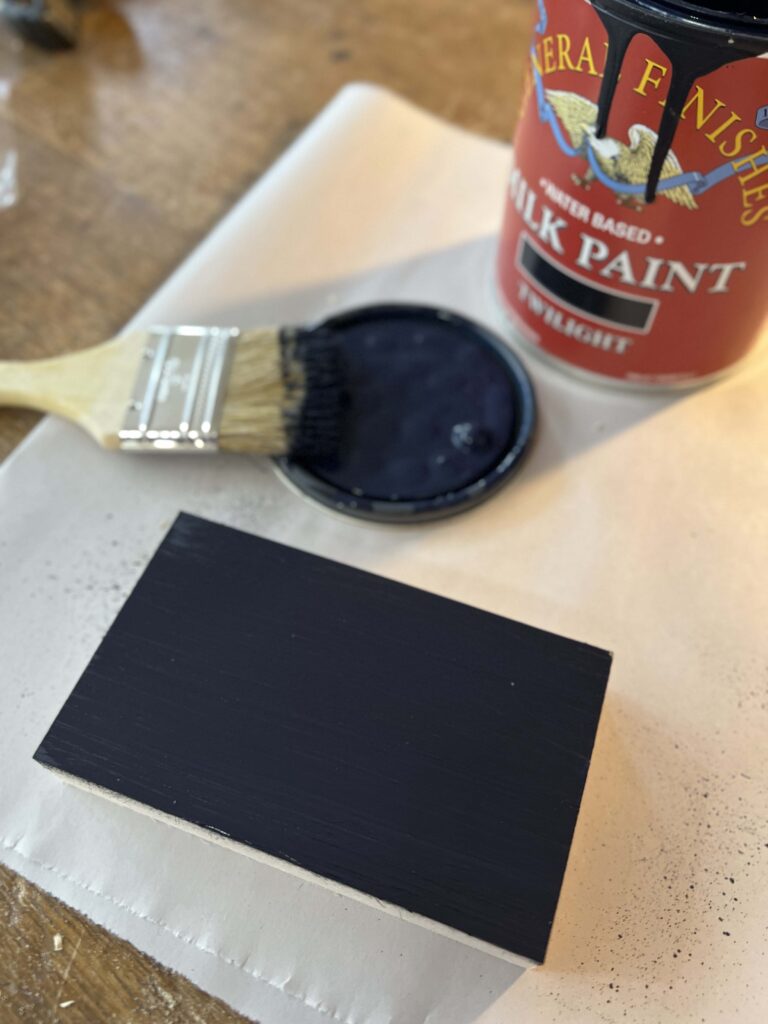
My only complaint is that linden has little odor; I missed the scent of the pine. When seven people are working hard, well, a bit of natural pine air freshener is a bonus (I’ll hang a pine air freshener under every bench for the next class!). And the students did work very hard – everyone left with a chest just about ready for final cleanup (finish planing/sanding) – and they all looked great.
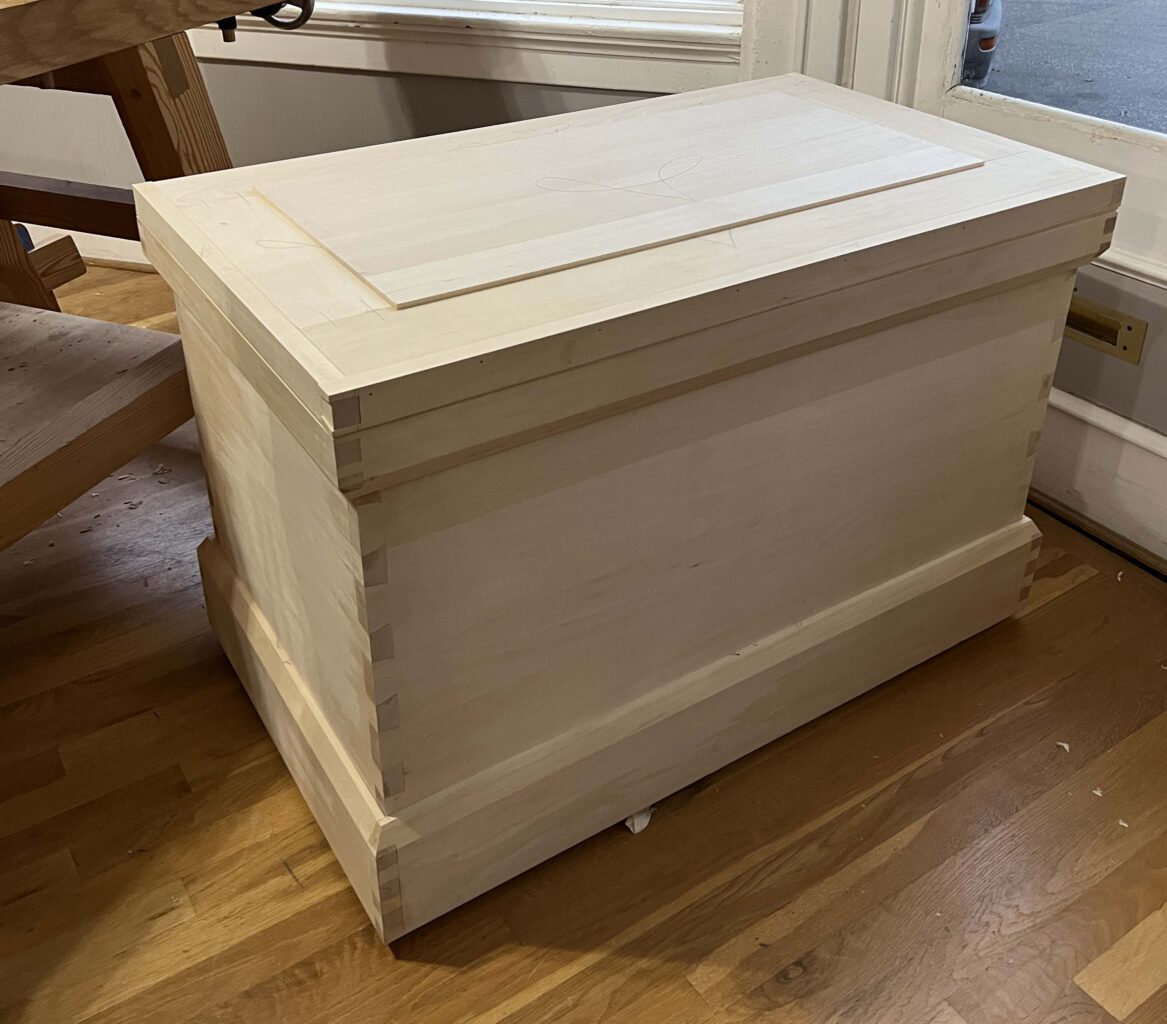
Will Amana sell one of these dimensioned kits to commoners like me? I’m ready to take a crack at making an ATC, having read the book like 12 times, but here in NYC, all the wood I find is absolute garbage.
I’ll ask them.
Much appreciated!
Add me to the much appreciated as well. This is on my list this year and would love to get a “kit.”
Any news on whether they will take kit orders?
I have the same question, Megan. I’m sure others do. I could see where if Amana wants to take orders so they can do a production run, it might be worth their time.
Looks like you found a good alternative to pine for now. But I would miss the pine smell also, hard to beat the smell of pine while working it!
I had just assumed that big pile of boards at the open house was poplar. My father told me later that you said it was linden/basswood, to my surprise. As I’ve only previously encountered it as a great carving wood (I only ever see it sold in bricks and blocks), I imagine it’s a real joy for cutting dovetails in.
Kudos on the new source of good wood.
This is great information, and a little surprising. The only basswood I’ve used was in carving, and I’d have guessed it was lighter and softer.
But it’s a fantastic alternative for you, and should be great for future classes if you let them do completed kits. You don’t need to pay yourself a pittance for milling lumber.
After seeing those kits crated up so nicely, I couldn’t help but wonder… Any chance they might be made available for purchase+shipment for those making their ATC at home vs the in person class?
This actually answered a question that had started bouncing around in my mind a few days ago. Basswood (aka linden) for carving, but not for things like the ATC? Was I missing something, some fundamental reason why “nobody did that”? Turns out, the answer was no. Just probably that what everyone is/was doing is/was what everyone else is/was doing. Baa. Baa. Baas-wood for the win!
Sounds like a phenomenal class. Are the 52 dovetails all done by hand?
They are – by the end of the week, everyone is a lot better at dovetailing!
FYI “basswood trees are considered a species, while linden is considered a genus. All basswood trees are linden trees, but not all linden trees are basswood trees. To call a basswood tree a linden tree is technically correct, but you cannot call all linden trees basswood trees, as there are a lot of different linden tree species.” Although European linden is now grown in North America what you purchased is probably Basswood. Air dried (and not too dry) is better for craving. The kiln dried basswood you got for the tool chests will be great. And gives me some ideas of what to do with some that was given to me that was incorrectly dried and is now too hard to carve. Basswood although a light wood is very strong! I like the colour when sealed with shellac+alcohol or with blo+mineral oil, but prefer shellac because it is easier to clean up after and doesn’t have the order that blo has. I seal with shellac befor painting with acrylics. But milk paint works better, as you know, over raw wood and then sealed with shellac.
The problem with common names is that common usage doesn’t always follow the dictates or desires one might have when it comes to taxonomy.
For instance, I’ve heard it said that “basswood” is the term commonly used in North America to refer to the various Tilia species, generally native, found there; other species of the genus are native in other temperate regions throughout the northern hemisphere, including, of course, Europe, from whence European Linden. I was told sometime way back before the internet started doing its thing that the name, basswood, came about as a result of the use of fibers from the bast (inner bark) for making textiles, threads, etc.—“bast wood” became “basswood”.
It’s not unusual for species other than Tilia americana (the archetypal American basswood) also to be called basswood. Tilia carolinensis is one example; some append the species name to the common moniker to give us Carolina basswood. I don’t see this as especially problematic, given that most if not all American species of Tilia produce wood of similar nature, commonly used in carving, musical instruments, and structures needing lightweight, reasonably strong, stable wood frames.
Given that the red oak one buys at the big box stores may be that of several different red oak species, and the same can be said for many commonly used woods, it wouldn’t surprise me to learn that some significant portion of the basswood marketed and sold in the US isn’t Tilia americana, but some closely related, and very similar, species instead.
No corroboration and am just spouting hearsay. I’ve heard linden became the name as a result of the inner bark you mentioned being used also in the twisting of lines (primitive cordage). Line: Linden. Again, strictly hearsay on the naming of it and no idea which came first. However, I can attest that the inner bark of linden trees does make fantastically strong (for the diameter) twisted cordage.
I mean “blo+mineral spirits” in the above post.
Paraphrasing Shannon Rodgers: Carvers are the reason why we don’t see linden boards at our local lumberyards.
I’m not sure how difficult it would be to get in ATC-sized panels, but paulownia could be another option.
This is awesome. I recently used basswood for a box bottom and it worked beautifully.
Regarding poplar ” is typically an economical choice”: While visiting my local Woodcraft yesterday I noticed poplar was twice the price of red oak at about $7 a board foot.
Red oak is cheap – but it weighs a lot and is a LOT harder for beginners in which to cut dovetails. I meant economical in light of decent choices for wood for a tool chest class (and for a tool chest in general).
Great to know! I’ve read through the wood database entries in most of the native woods where I live (about an hour from Amana, actually) so when my parents had to take down the basswood in their front yard I snagged a 6′ section in the hopes of making a DTC from it (after the book comes out…). Glad to know it will work as well as the specs said it should.
I live on the west coast, and I have noticed that the “good” sugar pine at my local hardwood store has jumped up in price quite a bit. Its actually cheaper for me to get red alder. The knotty stuff is still pretty cheap. Home centers also tend to have more what they label “whitewood” or SPF(which lately is doug fir) Whereas a few years back it was mostly pine. I have noticed that most of the pine from a location a few hours north is mainly milled into shiplap and T&G paneling. I guess they can get far more money for it that way.
And here, it’s likely double! (My supplier told me what the bf $ would be…the kit price would be astronomical.)
One of my first significant projects from rough cut lumber that involved a lot of hand tool work was the Einfield cabinet. The building process followed your article from the old but still excellent Woodworking magazine. I made the cabinet out of basswood and painted it.
Linden = Basswood. From my limited carving experience, it is hare for me to believe that it would be able to take the bumps and bangs of a tool chest.?????
Well it’s harder than sugar pine or Eastern white – which it was Iv’e been making them from for a decade, so…
I’m not sure any commonly used wood is softer than eastern white pine. And it’s been used in tool chests and all kinds of furniture for centuries.
Well for example there is balsa and cedar. 🙂
Ooh, now I want an aromatic cedar ATC!
Hey! That’s my chest!
We use tons of basswood for harpsichord cases, panels and keyboards. It works wonderfully, is quite dimensionally stable once dried and is really tough stuff so it doesn’t split as easy as pine. I’m glad to see others discovering its wonderful qualities!
Fitz, I have been using basswood for plane storage boxes I have been assembling for my ATC. Since the goal was just to keep things separate and not provide strength I first thought of balsa but it was a no go, too fragile. I then tried basswood and was impressed, easy to work with and did what I wanted it to do. The only issue I ran into is if it is too thin (say 1/8 inch) it had a tendency to cup, especially if I couldn’t finish the assembly the same day but at 1/4″thick that trait seemed to disappear and the increase in weight was minimal. It’s nice to see that it’s working for you as well.
I bought Christopher`s DVD “Build a sturdy tool chest in two (hundred:)) days”. No dovetails, just screws and glue. Made some changes to original plans. I used birch plywood, one of the most common wood species here in Finland. Very happy with the end result!
In school we made model rocket fins from basswood instead of the traditional balsa.
I have used basswood (Linden) on some of my chair seats and have had great success with it. The problem has always been sourcing 8/4 materials.
Looking forward to the answer on the ATC kit for those of us not able to get into the class. I live in Utah which is pretty much a desert for good wood.
I’m taking the ATC class in February and this is making me even more excited about it!