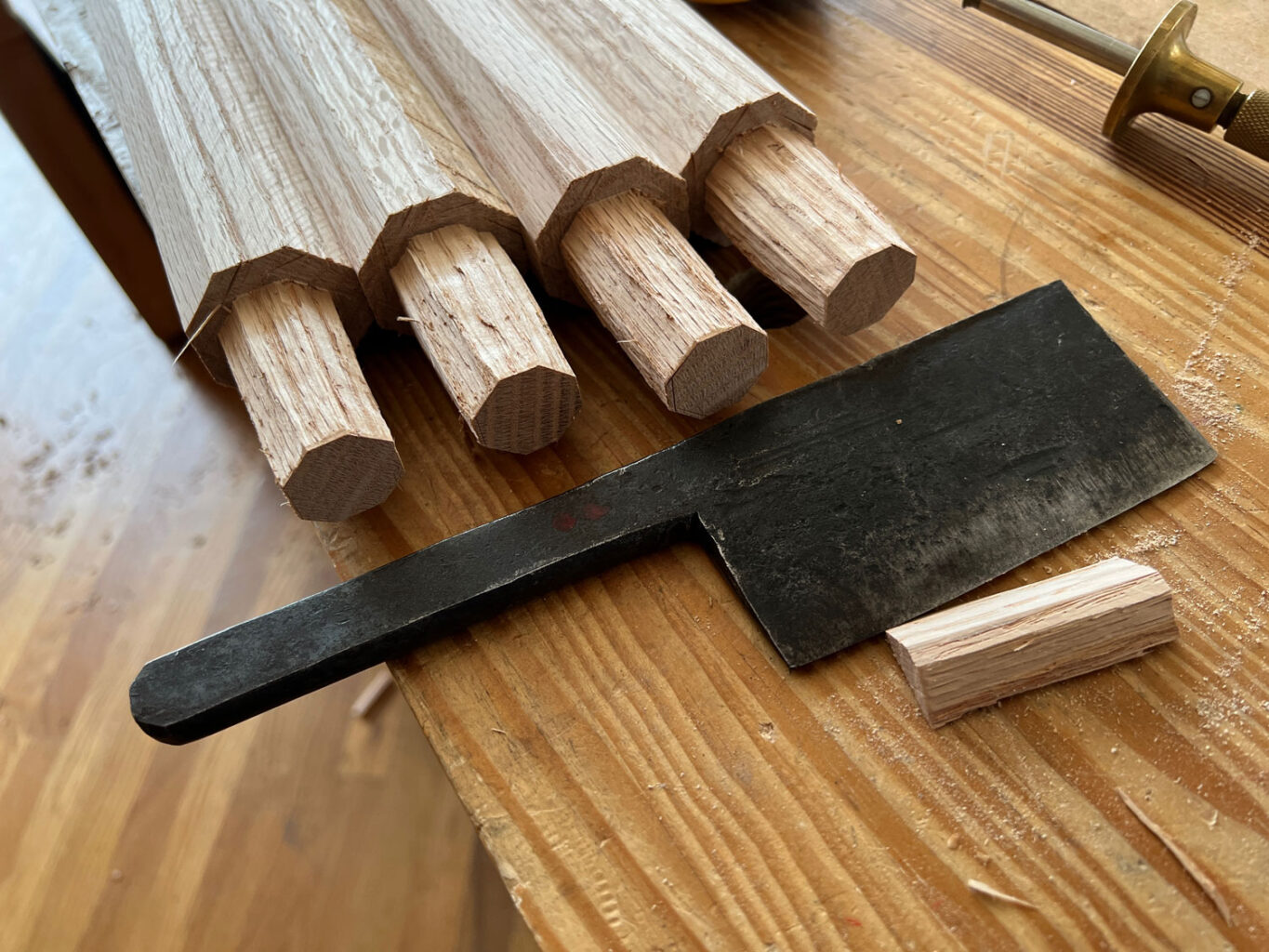
For most of my career, I have helped other woodworkers “get published.” That task could be as simple as spell checking their excellent work. Or as involved as being a ghost writer – taking an oral history of their work and transforming it into an article or entire book.
After 25 years of doing this, I find most skilled woodworkers fall into two categories: Those who want to make things easy for other woodworkers. And those who want to make things hard.
Both approaches are valid.
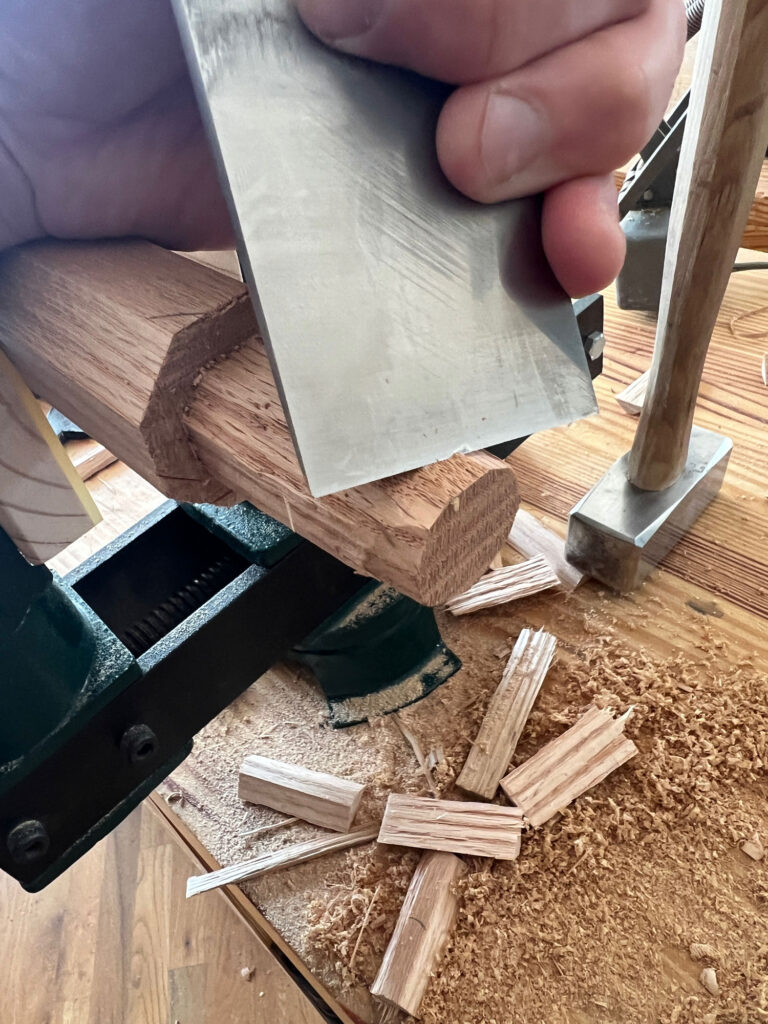
Making Things Hard
It’s difficult to argue with this approach. Woodworking is inherently difficult, and pushing others to do things “the hard way” creates hard-bitten, independent, skill-junkie woodworkers.
Sometimes the “hard road” is about withholding information from students. If you decline to explain critical steps of the process, the student then has to fill in the blanks. The information is then earned, rather than given. And it is therefore cherished when finally obtained.
Sometimes the “hard road” is about setting limitations on tools or materials. If you want to build a certain piece, then you lay down the only accepted way to go about it. One example: Want to build a 17th-century-style carved oak chest? Then you must learn to rive green oak. Dry it a bit. Then carve it. Lumberyard kiln-dried oak will never look right.
And sometimes the “hard road” is about cracking the whip. The lessons are complete and detailed. But if you don’t follow them to the letter, there is a price to pay. You will be yelled at, belittled or mocked until you learn to do things correctly.
It’s difficult to argue with the results of these approaches, and I am in no way criticizing these approaches. Some of my best teachers approached their lessons these ways. And I have been subject to all three. One boss delighted in “firing me” at least once a week when I did something too slow or poorly.
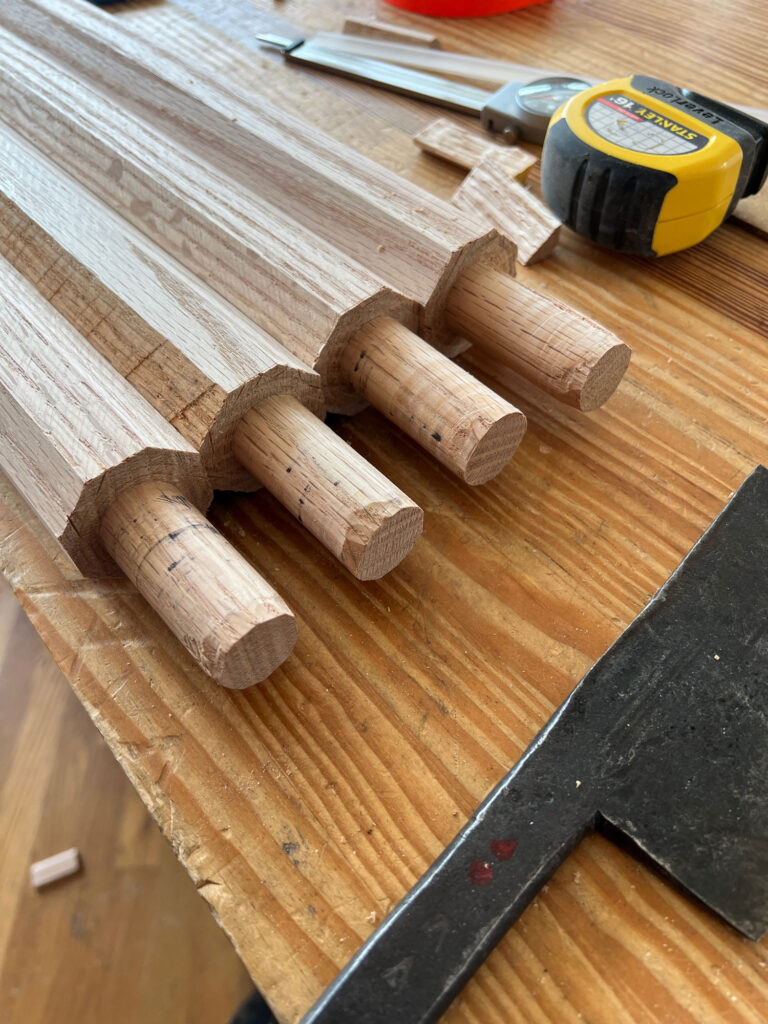
Making Things Easy
I cannot for the life of me make things difficult for students. It’s not in my programing. I am far too terrified that the craft will shrivel away because I didn’t explain to the next Norm Abram the right way to saw a tenon shoulder.
So I spend hours at the bench agonizing over how to explain a technique to readers. How can I make this easier? How can I do this with fewer tools? How can I reduce the need for years of practice from this operation (without adding some complex machine)?
This month I have been obsessed with figuring out the best way to cut 1″-diameter x 2-1/4″-long tenons on the ends of chair legs.
The expensive way: Buy a lathe.
The hard way: Shave them to fit.
The easy way? That’s what I have been working on. I have developed two approaches. The first involves sawing the tenon’s shoulder, then riving away most of the material with a hacking knife or chisel. Then finishing the tenon with an inexpensive tenon/plug cutter chucked in a brace or a drill. The result is perfect tenons that look “traditional.”
But my brain wanders. Why can’t the tenons be “loose” – like a Domino? All this approach requires is a 1″ drill bit and some 1″-diameter oak dowel. Drill a mortise in the end of a leg. Drill a mortise in the seat. Glue the loose tenon (made from a dowel) into the leg. Then glue the completed leg into the seat. Easy.
Too easy?
— Christopher Schwarz
Drilling straight down the length of a chair leg is harder than it seems. It can result in that leg angle not what you planned for. Otherwise that joint should work perfectly well and hold up quite well.
I use loose tenons for joining an arm to a front leg in my ladderbacks. After experimenting with hand drilling and building a jig for the drill press the mortise is drilled on the lathe – easy but expensive.
When can we read about this new tenon-cutting technique in detail? The Stick Chair Journal? How did they do it before the invention of the tenon-cutter/plug-cutter? Concave spokeshave? Another use for the scorp/inshave/croom iron?
I’ll be covering this in the next Journal….
Would not be surprised if many just rasped or filed it round after roughing in with a draw knive. You can get surprisingly accurate results this way for not a huge amount of effort.
The only way to find out is experiment. But I can’t imagine it would be “easy,” or strong, or pretty. Drilling a 1″ mortise, straight, into endgrain, can’t be any easier than cutting the tenon onto a leg blank.
And it would have very thin walls, unless you leave the leg blank quite heavy. Which would be unattractive.
And if it was a good method, wouldn’t it have been done?
That last point has caused many people to fail to file for patent, or publish, when they really should have. Simple and “hasn’t anyone tried that before” do not guarantee it isn’t a novel insight that really has been overlooked.
John, the thin walls was my first thought. I remember Robert Lang did an article for PW where he was dropping anvils on all sorts of joints. He concluded he “would never make a mortise that is more than a third of a piece’s thickness.” Search for “Robert Lang anvil test”. It’s an interesting read.
I had a similar thought, and then realized it was simply a matter of order of operations. Drill the hole in the end of the block, first. Glue in the dowel, then shape the leg.
You could make layout tools that referenced the dowel. Or a shooting ‘Box’ for shaping the block, that holds the dowel at one end, and has walls on either side that would keep a plane from planing too far into the octagon shape.
I remember Yeung Chan explaining once about his ‘lathe’ that was a box with a pattern on top. He’d mount a screw in the end of a leg blank, set it up in the box, turn the leg with a drill, and then pattern-rout the leg shape while the leg turned. It was a great example for me of a simple idea that worked, even though it wasn’t being done ‘the right way,’ with a normal lathe.
As easy as that sounds, your drilling of the seat has to be 100% accurate for the rake and splay to be spot on with each other, ( only made one chair and only a few pages into your book) where as, with a tapered reamer you can correct your inaccuracies as you’ve shown in your videos….am I wrong??
Hi Martin,
Not everyone wants to buy all the gear to make chairs. And there is still quite a shortage of the specialty tools. So I’m looking for ways around that barrier.
Almost every vernacular stick chair was built with cylindrical (not tapered) joints. And so some variation in rake and splay is part of their charm.
But yes, the tapered joints help you nail the rake and splay.
It would interesting to know if someone has not tried to patent this idea before now. Imagine a plunge attachment for electric drill to control centering of hole and depth. The shoulder could be trimmed to a desired angle before the “loose” tenon is glued into it. What more could be desired other than a catchy registered trademark name? And just think…it doesn’t even need to go side to side!
Is it April already?That winter passed quickly
Thanks for making things easy. On the Woodwright’s Shop a decade back, you demonstrated how to cross-cut thicker pieces using a knife wall. It was a real “ah-haaa” moment for me. Fast forward to this month and I’m proud to say I got an article published in the current issue of Fine Woodworking Magazine.
That’s how Justin Nelson with Fernway Woodworks does his tenons for his production chairs. I haven’t heard him say one has ever failed. Look up the Oxbend chair. Not the way I’d prefer to go about it but hard to argue with when it’s working.
That is he uses a loose tenon for the leg to seat joint. Not sure it’d it’s 1”. I think it’s actually bigger. Maybe 1-1/4”.
I have used 5/8″ loose round tenons (dowels) to repair broken stretchers on a couple stools. I found that so long as the stretchers were securely clamped to my bench drilling a relatively centered hole was not hard. For a little extra security you could pin or drawbore the tenon to the leg with a skewer.
Chris, if you haven’t, i suggest you read some of the works of Shinichi Suzuki. He is most known as the creater of the Suzuki Method and philosophy of teaching music. he turned music education on its head. but he also ran a violin making factory. he wrote 2 books that are easy reads: “nurtured by love” and “ability development from age zero,” and numerous articles that can be found here: https://internationalsuzuki.org/tej-archive
if I’ve learned anything diving into woodworking the past 8 years, it’s that the principles of good teaching are the same no matter the subject.
A less expensive twist on the lathe choice is a spring pole lathe and I thought I remember Chris teasing a LAP book on this topic in the pipeline. Is this a false memory?
It is not a false memory – Jarrod Dahl is working on one, but we don’t have a pub date yet.
To be fair, specialty tools for cutting tenons on the end of chair legs are available from the venerable Canadian tool manufacturer (and maybe others?), but the price isn’t really ultra cheap ($100+), even if the quality of the tool you get for your money isn’t really bad compared to typical quality woodworking tools.
For the money though, a cheap woodworking lathe is way more versatile, especially for other tasks involved in other potential chairmaking tasks, as well as other woodworking tasks in general.
Even a cheap woodworking lathe from that national import tool dealer that smells of liw quality rubber should be perfectly fine for something like chair tenons.
As for loose tenons, the technique goes all the way back to Ancient Egypt and one of their ship building techniques, although the tenons were cut into side grain.
According to an article in that major woodworking magazine from Connecticut ( I think), tests found that standard pointy twist drills made for drilling metal were best for drilling into wood end grain, with the more open flute “parabolic flute” drills for metal being slightly prefered.
I love this article. It has implications far beyond just woodworking but in transferring any life skill or practice to others. Thanks for this analogy.
I used to want to do everything the hard way as some sort of flex. “Look at me skills and be amazed!” Very little got done and no one was amazed. Now, I just focus on the most efficient way, things get done and stopped worrying about impressing people.
What about the risk of the dowel swelling with the glue and splitting the leg?
It might be useful to glue the dowel before shaping the leg. That would give the opportunity to grip/constrain the extremity of the leg with clamps more easily while the glue cures.
No shaping work wasted in case of splitting.
Ah yes, getting yelled at. When I started working as a carpenter framing houses the lead carpenter (Bill) would yell at us rookie carpenters most of the day. His style reminded me somewhat of my Marine Corps drill instructors. We all got threw it and as the years went by Bill became a great friend. Unfortunately Bill passed back in 1988. We also did things the hard way. I must say I look for the most efficient way to build things. I have been building chairs for the last couple of years and I use a horizontal mortise machine and use floating tenons. It’s quick. I bought the machine from a local furniture maker where I live. I still occasionally yell at myself for screwing something up. I personally don’t recommend yelling at folks to get things accomplished on a job site. It sometimes makes people screwup even more!
Chris, your observations about teaching are fantastic and much appreciated – Thank You! Years ago, I took a turning course with Bob Rosan at his studio in Pennsylvania and became white knuckled after he easily explained a turning procedure that I was trying. Bob came over as he saw me struggle, put his hand on my shoulder, and asked why are you struggling so much, then exclaimed “It takes three years to get Lousy at turning. Wow, this was the greatest turning observation I had ever heard, and I was able to relax a bit, stop beating myself up because I realized that Bob had 25+ years experience of daily turning under his belt and even though his explanation and demonstration were spot on and looked easy, there was 10,000 hours of practice behind his hands wielding his turning chisels. I was not aiming to be a “Turner” however his observation enabled me to generate better turnings for my furniture projects that I was building from your PW Magazine articles.
I did not see who wrote this article and I was wondering just who it was, Chris or Meghan. I thought it was Meghan when I got to the part about making it easy and Chris up until then. SORRY
I like to think of woodworking as choosing my own adventure. Some things I want to challenge myself. Other things I just want to get it done with. Varries between projects and the individual steps of a project. Right now, I am in the early stages of a new build. I am debating what I want to do for the back. I could go with plywood (nice cherry skinned plywood I have at home). I could go with a frame in panel and the pannel could be either that cherry plywood or real cherry. Don’t know what I will do. How important is this one step to me? How important is it for a part that really won’t be seen? How important is it a piece for me and not for someone else. How important is it for something that will reside in the workshop. Don’t know yet. All options are viable. I just have to sort out what I want to do.
Chris,
You say you read the comments so hopefully this idea crosses your eyes. i once saw a jig on youtube that cut dowels with a table saw made of nothing more than some ply. It was basically the same setup as a splining jig–two intersecting ply boards that meet at 90 degrees. So heres my thought, turn the jig sideways (perpendicular to the saw blade) and with a fence stop on the opposite end being cut you can then raise the blade to whatever depth and spin the leg. Move the fence stop in and repeat. So on and so forth. If you have a table saw but don’t own a lathe, this seems like an easy and quick way to see good results. Plus the beauty is the tenons will always be centered if your jig and leg are 90 & cylindrical
Addendum
I didnt notice the legs were polygonal. Just add a depth plate matching the width of each side down into the bottom of the jig where the 90 degree junction is.
Funny I did a repair yesterday of a broken stretcher doing just that. Not sure how “easy” and strong it would be on a leg however.
I just finished a chair where I used the second method. 3/4″ oak dowel set into 3/4″ holes that I drilled into my leg stock before turning the legs. Super clean install into the chair seat and plenty strong with the large shoulder I gave it. Is it the easiest method – I don’t know. But it did give great results. Check out the chair at this year’s Texas Furniture show which just opened in Kerrville, TX.
Very interesting questions, and great example. I always enjoy your columns.
I am good at making things more difficult. I had a similar experience putting legs on a simple stool I was making. I used dowels stuck into the ends of the legs, and holes in the underside of the stool. The dowels were loose, the legs spun around. I knew if I glued them up I would never get them oriented right, and they wouldn’t be secure. So I cut some square dowels a little larger, and chopped out mortices where the holes were. Though it is still a wonky stool the legs are secure.
I’m working nights to finish my first chair before the badges disappear. And I’ve been battling the steam bending (two attempts and counting) and tenons for most of that time.
The Veritas power tenon cutter works for me, but very inconsistently. A straight tenon is easy after watching your video; but the blade often stops cutting a moment after it starts. I wish Veritas had more documentation on ideal blade adjustments. It’s all very humbling. I’ll probably be forced to shave or rasp the tenons by hand, until I learn what I’m doing wrong.
Having experimented, I found a lathe to be the cheapest and most versatile. When making a round tenon you don’t need a premium lathe. I bought a secondhand Record DML 24 for £100, similar available for similar prices.
I tried the method you’ve shown here. I didn’t like the cheap plug cutters, buy a few the cost adds up, it’s time consuming as well.
I used to be intimidated by the thought of a lathe, but turning a round tenon is painfully basic and fast.
This post explains more about you than I think I’ve ever read over the many, many years of your blogs, books, and magazine articles. It also explains a part of me that I’ve never totally understood, and why I’ve disagreed perhaps neither rightly or wrongly with your approach. Thanks for that.
Thanks ric. That was the point of the post more than a discussion of tenons.
I do the same, always try to make a process simpler. I have however discovered that on occasion the hard way is the easy way. It only seems hard because of my ability or knowledge. Researching the historical way(s) of doing it often helps. Sometimes its a wash, oh well.
Agree!
Christopher ,
Wood working is enjoyable whether it’s a difficult or easy way. One might use machines and others hand tools. Both provide enjoyment.
Woodworking as a n artist is difficult Because it seems people don’t pay well for the art in any discipline.
I want you to know that your teachings are appreciated even if I can’t afford your chairs. But I do enjoy reading your descriptions.
I read you over the last 30 years as your skill moved around. Keep up the good work as there are many that appreciate your dedication.
Wayne Wright
I have no lathe (by choice – it would consume all my time making useless objects). But I do have lying about an old Trend Router Lathe (Sears Router Crafter in the US). I find it ideal for turning leg tenons quickly and accurately.
I use the sloyd knife + test hole method, which is definitely the easy way for me. The hardest part is resisting the urge to pound the almost-there tenon through the test hole and splitting the scrap it is drilled in.
It is interesting to me to realize what techniques are easy and which are hard for different people. I certainly would have more trouble drilling the hole into the leg straight enough than I do shaving down the tenon. But it would get tedious pretty fast if I had to do it more often (I got the tools for the plug-cutter method for the 5/8 tenons for that reason).
To add to Chris’s points, people may also find it helpful to try alternative methods if those methods tie into skills they want to build.
Got a lathe and want to get time on it to work your way up to making balusters? Start by turning tenons for your planed or shaved stick chair legs.
Been making all your chair legs from carefully sawn stock and then using your jack plane to turn them into octagons? Want to build up some skills with your drawknife and spokeshave? Start by shaving your tenons.
I’m speaking from personal experience. Everyone learns differently, so your mileage may vary! But this was a helpful way for me to slowly build skills with tools I was new to. And full disclosure, I was lucky re: the lathe. I found a local teacher that was happy to teach turning, and sold me an old Rockwell lathe on the cheap that was/is rough on the eyes but does its functional job quite well. Sometimes it is better to be lucky than good…
Tell me about your hacking knife! I want one!