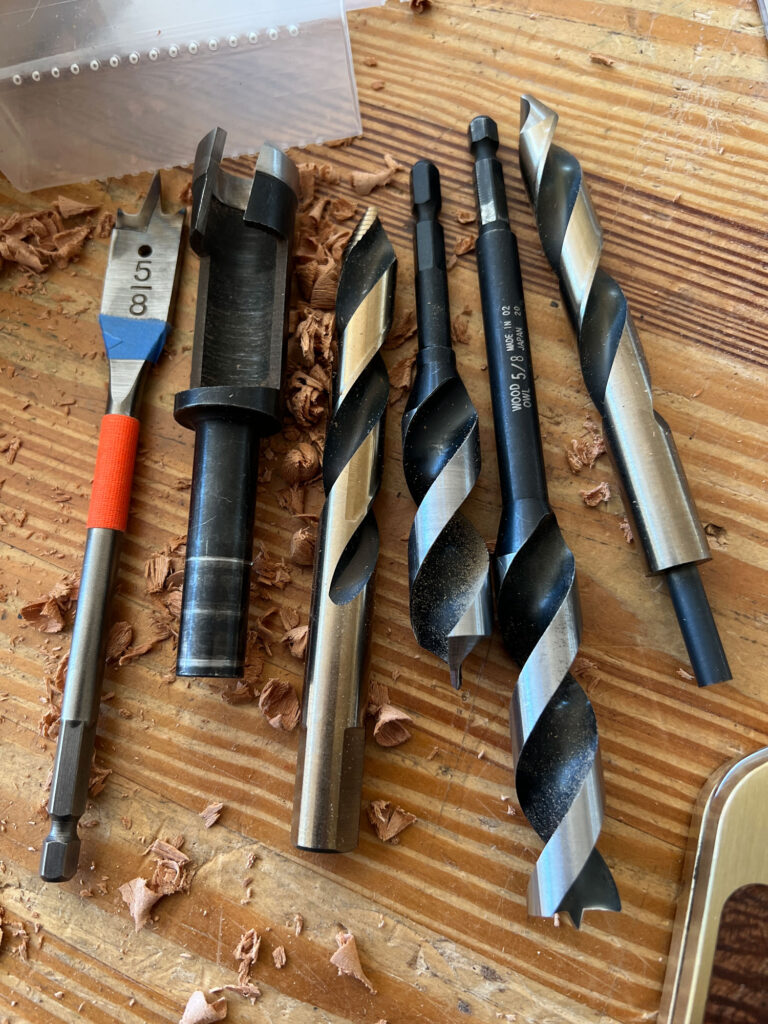
When you drill a hole with a 5/8” bit, then use a 5/8” tenon cutter to make the tenon, you should be golden…right?
Nope – unless you get lucky.
If you dare enter the fascinating world of boring you will quickly realize this truth: It is up to you to get your drill bits and tenon cutters to work together. You cannot trust the measurements stamped on the tool.
A quick example: a 5/8” WoodOwl spade bit and a 5/8” plug/tenon cutter from Lee Valley are not compatible. The tenon will drop into the mortise like throwing a hot dog down a hallway. It’s not a good joint.
There is no way I can cover all the bits and tenon cutters out there. But here is the methodology I use to get my mortises and tenons nice and tight.
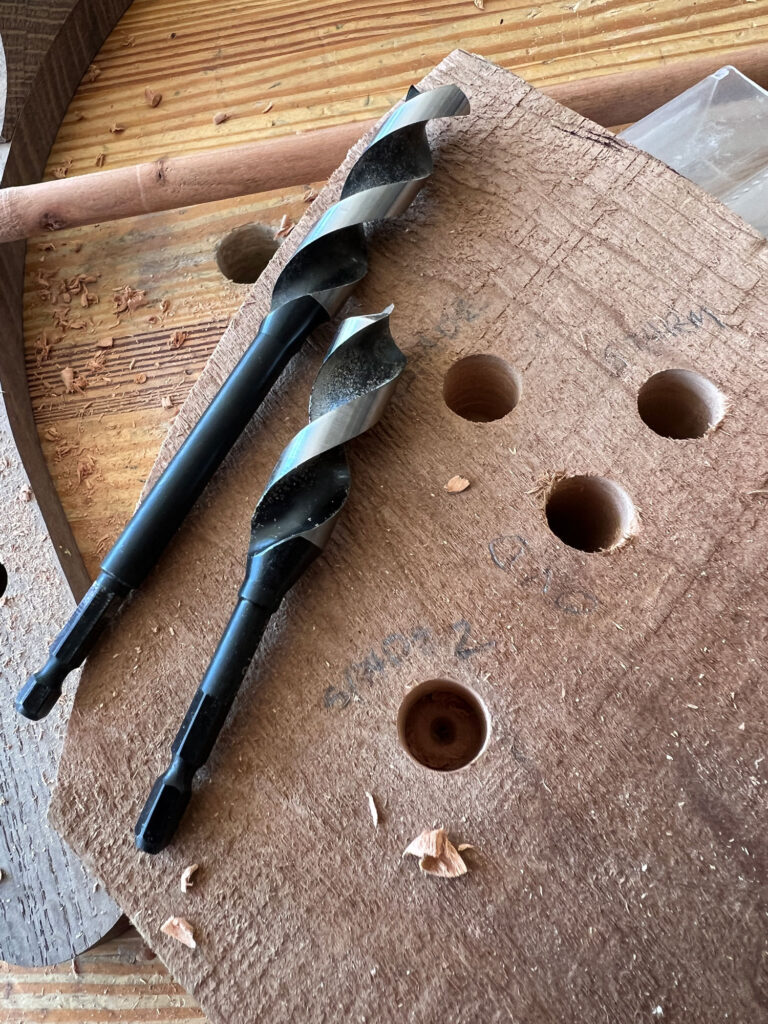
Suggestion No. 1: Ignore the Official Measurements & Make Samples
A WoodOwl 5/8” spade bit and a WoodOwl 5/8” OverDrive bit make different-size holes. Because of its cutting geometry, the 5/8” spade bit cuts a hole that is .010” oversized. And that difference is enough to ruin a joint.
So when I get a new bit, I drill holes in oak, cherry and whatever species I have sitting around. Then I measure the holes and test them against the tenons I am making.
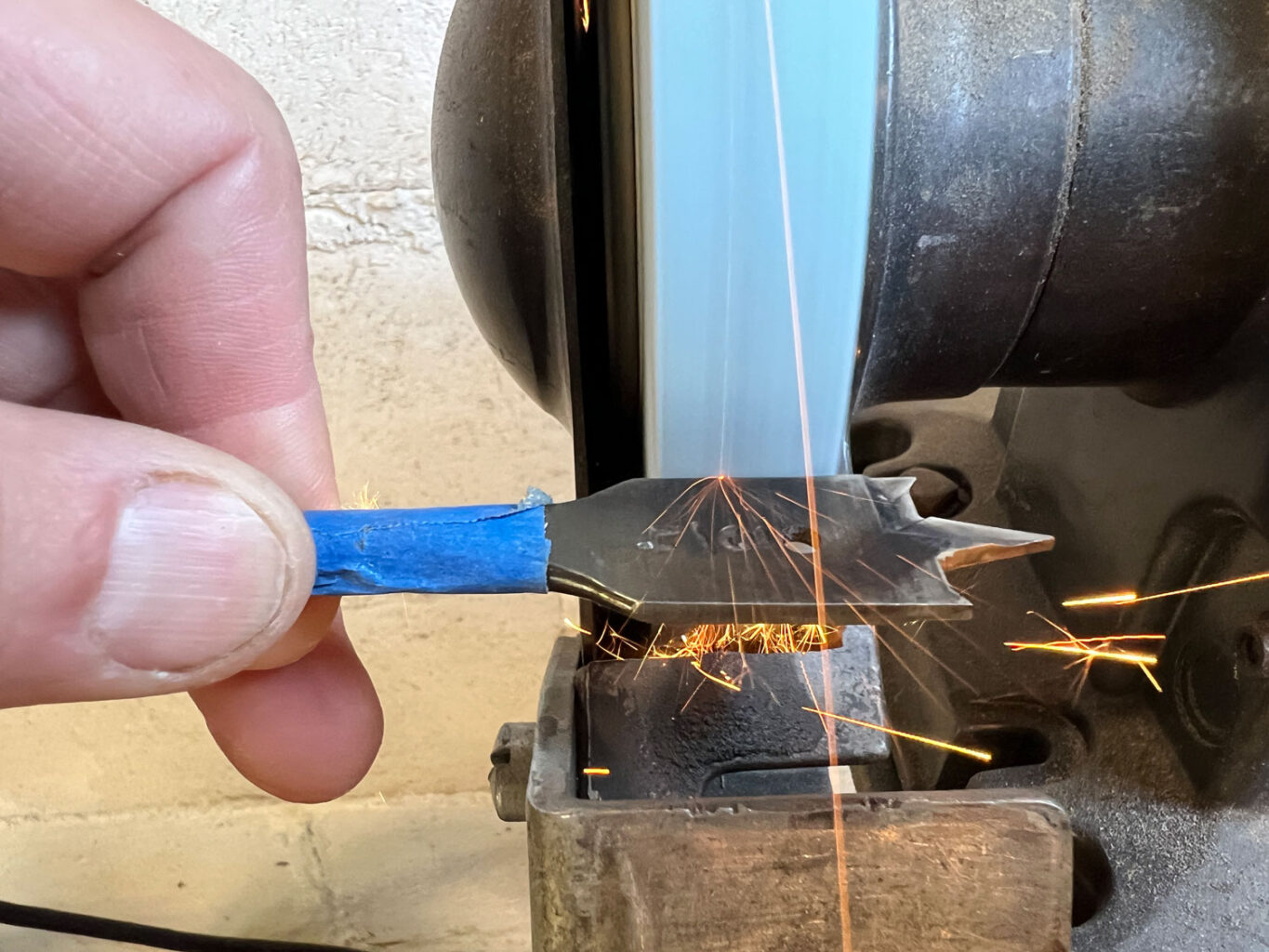
Suggestion No. 2: Ensure One Tool of the Pair is Adjustable
I can pair my Veritas 5/8” Power Tenon cutter with almost any 5/8” or 16mm bit because it’s adjustable. So usually I lean on that tool to make fine adjustments to the bits I have in my shop. I can pair it with my WoodOwl 5/8” spade by retracting the cutter of the tenon cutter. Or I can match it with my 5/8” OverDrive bit by advancing the tool’s cutter.
Here’s another example. Let’s say you have a 5/8” tenon/plug cutter because you cannot afford (or find for purchase) the adjustable Veritas 5/8” Power Tenon Cutter. In this case you cannot adjust the tenon/plug cutter, so you have to have an adjustable drill bit.
And that’s when you should definitely turn to spade bits. You can easily grind spade bits to match your tenon cutter. It takes seconds to do it, and you can sneak up on the right fit.
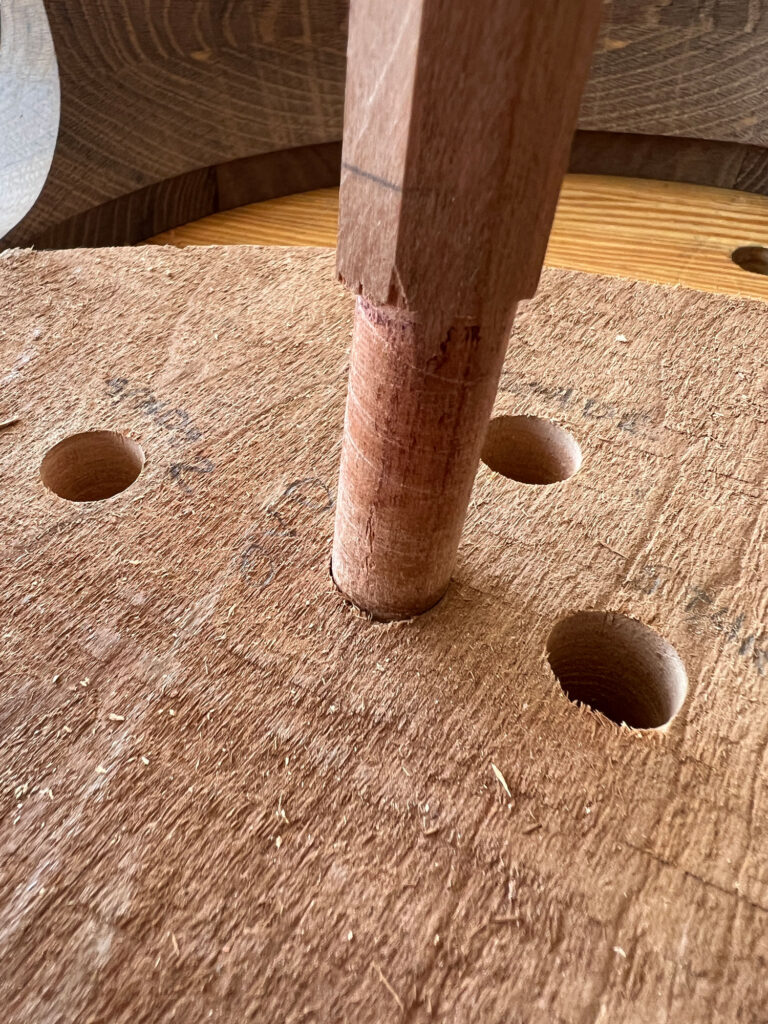
Suggestion No. 3: Go for a Snug Fit – at First
I am obsessive about the fit of my joints. Perhaps overly so. If you are like me, here’s how to go overboard. I adjust my tooling so that the tenon is a bit oversized and will not enter the mortise with hand pressure (usually .005” oversized or a little more). Then I use soft-jaw pliers to compress the tenons so they slip in to the mortise easily with almost no pressure.
This process makes assembly easier – the tenons slide right in. And the joinery is sound. The wet glue expands the tenons and locks the joint.
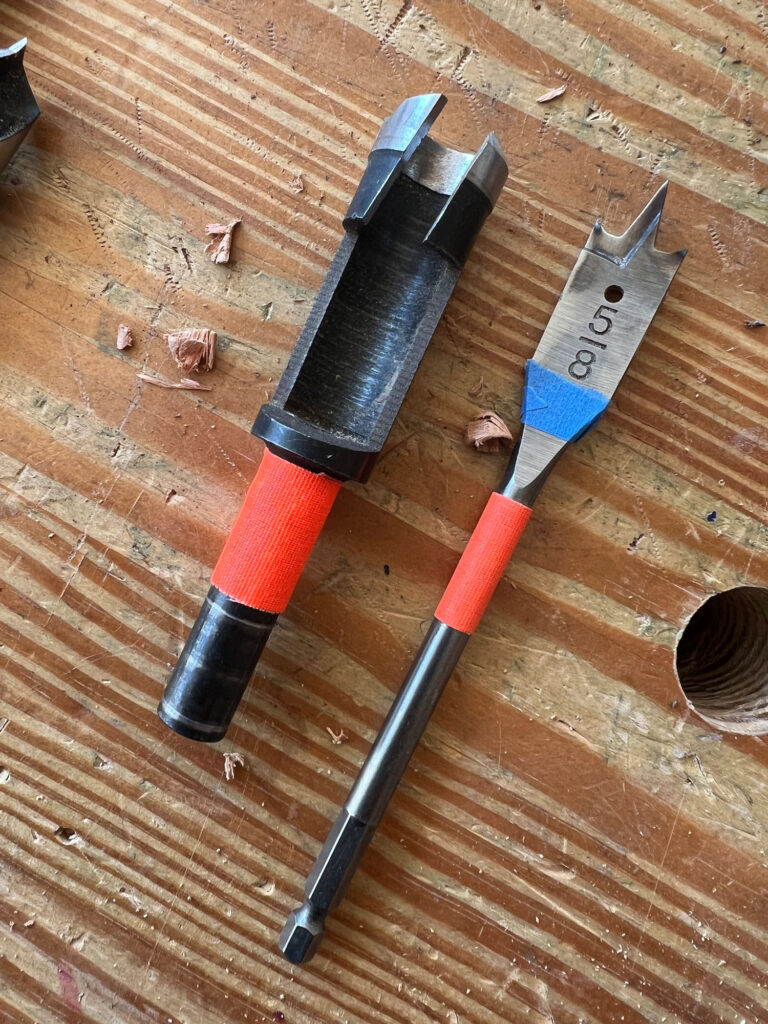
Suggestion No. 4: Use Tape
Once I have matched a tenon cutter and a drill bit, I wrap them each with a piece of brightly colored tape. This prevents me from making a terrible mistake.
— Christopher Schwarz
Thank you, my default drilling and tenon making did not match your video example. Now I have a plan to make my next chair better! Jake
Like throwing a hot dog down a hallway
“If you dare enter the fascinating world of boring”. I love this line
Thank you tremendously for such info . I should have thought again about that a couple of days ago. Anyhow, thank you !
Long live LAP et M&T.
Lacking a tenon cutter (they’re vexingly perpetually out-of-stock over here it seems), I just lay out the diameter of the tenon by gentle scoring the endgrain with the same auger bit I drilled the mortise. Lay out the length and cut just proud of final diameter and remove all the waste with a chisel and finally carve it to a tight fit, or shave it down with a plane if possible, using an offcut with the same mortise as a go-gauge. It’s a bit risky, and quite probably not as fast as a tenon cutter, but it works.
I was just about to say, this post is perfect timing for me. I have made my tenons the way you stated above up until now, but I just got a plug-cutter (as I am thinking of trying a chair with more sticks soon).
Love the color coded tape idea.
Totally useful information! Love it. Thanks again.
Chris, I love your blog entries because not only is your advice and information always fantastic, but your analogies are always funny. “That’s like throwing a hot dog down a hallway”, is my new favorite and I plan on stealing it and using it in every situation. Even ones where it doesn’t make sense.
Excellent tips.
Hmmm. In considering making my first stick chair, I’m thinking about my grandfather’s adjustable hollow auger. A workable handtool alternative?
Give it a go. You might need a spoke pointer, too.
Just happen to have a pointer too. Grandpa used ‘em to make spokes for wagon wheel repairs.
There’s always Chair-Loc?
http://www.westernwooddoctor.com/chairloc.htm
Thumbs up to grinding spade bits. I am constantly adjusting them, diameter, center point, scoring spurs, cutting edge, I make them suit me. Think of a spade bit as a starter kit, assembly and fine tuning required. They are cheap enough you can afford to experiment.
Given your healthy obsession with chairs and drilling holes, I’m willing to bet you could design the perfect bit for chair making. I am sure you could find some company willing to sell it 🙂
I wish I had the time to teach myself about modern bit manufacturing!
Thanks for this great tip! I just tried this out with my dowel plate and an array of bits and now I know which ones to use for a tight fit, which are snug, and which one’s are the hot dogs.