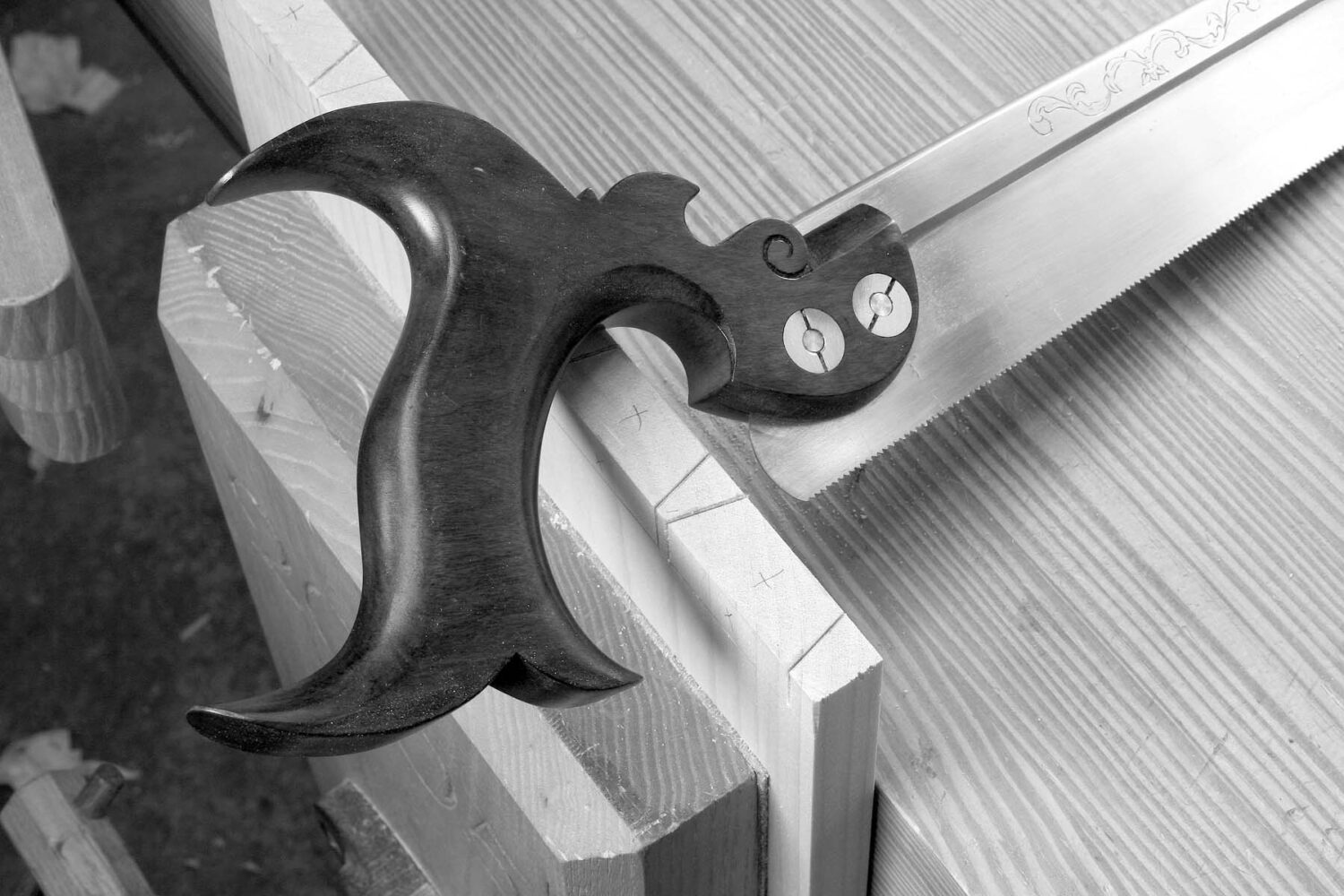
The following is excerpted from “The Joiner & Cabinet Maker,” by Anonymous, Christopher Schwarz and Joel Moskowitz, from the chapter on making the dovetailed schoolbox.
In this chapter, as with the other projects in the book, Chris builds “alongside” young Thomas, the main character in the charming 1839 fictional account of an apprentice in a rural shop that builds everything from built-ins to more elaborate veneered casework. The book was written to guide young people who might be considering a life in the joinery or cabinetmaking trades, and every page is filled with surprises. You can read more about it here.
To understand how little that is certain with dovetails, let’s take an abbreviated journey through the literature. I promise to be quick like a bunny. Charles H. Hayward, the mid-20th-century pope of hand-cut joinery, suggests three slopes: Use 12° for coarse work. Use 10° or 7° for decorative dovetails. There is no advice on hardwoods vs. softwoods. F.E. Hoard and A.W. Marlow, the authors of the 1952 tome “The Cabinetmaker’s Treasury,” say you should use 15°. Period.
“Audel’s Carpenter’s Guide,” an early 20th-century technical manual, says that 7.5° is for an exposed joint and 10° is right for “heavier work.” No advice on hardwoods vs. softwoods. “Modern Practical Joinery,” the 1902 book by George Ellis, recommends 10° for all joints, as does Paul Hasluck in his 1903 “The Handyman’s Book.” So at least among our dearly departed dovetailers, the advice is to use shallow angles for joints that show and steeper angles if your work is coarse, heavy or hidden. Or just to use one angle and be done with it.
At least in my library, the advice on softwoods and hardwoods seems to become more common with modern writing. Percy Blandford, who has been writing about woodworking for a long time, writes in “The Woodworker’s Bible” that any angle between 7.5° and 10° is acceptable. The ideal, he says, is 8.5° for softwoods and 7.5° when joining hardwoods.
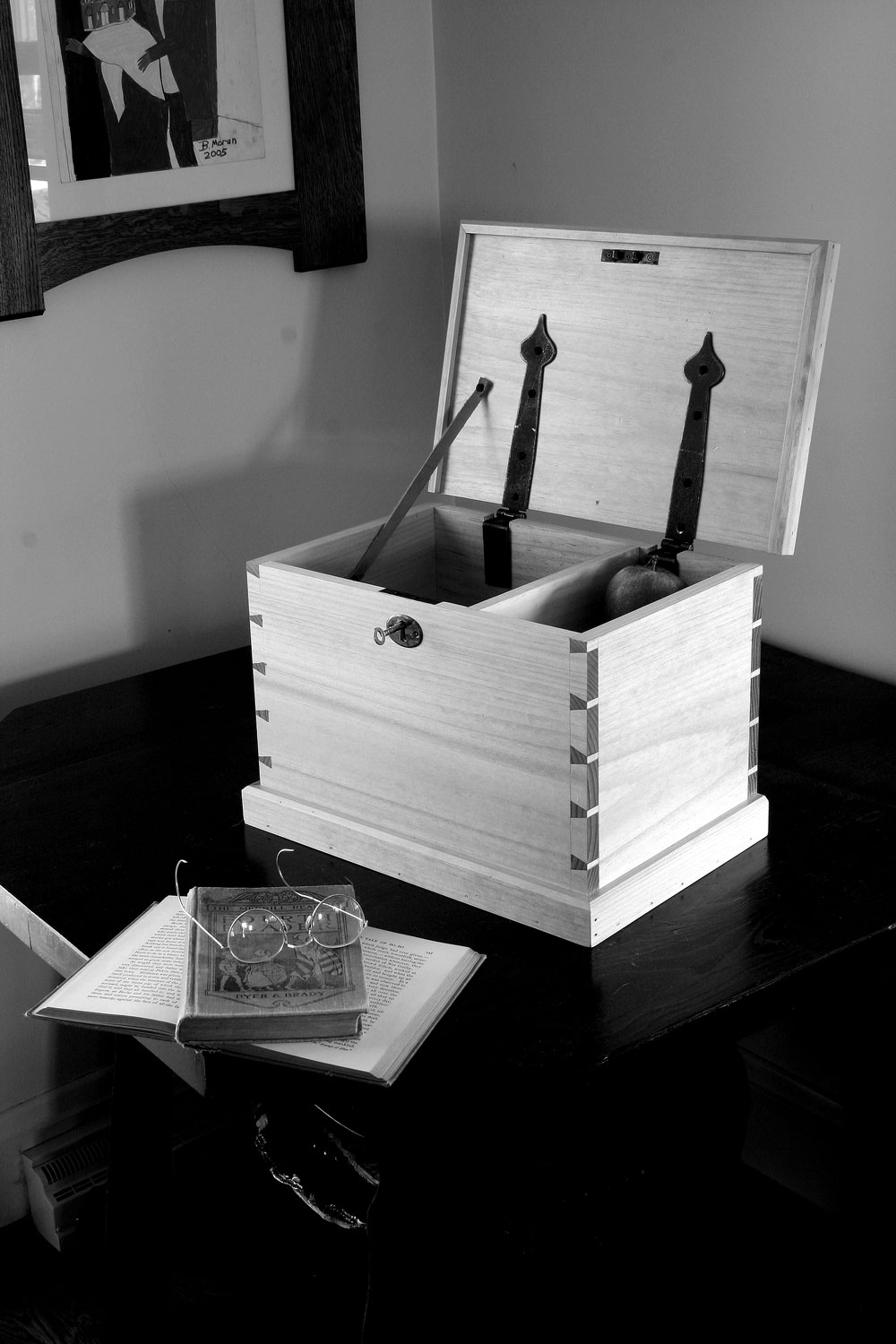
One Wednesday morning as I toiled with these old books, I went into the shop and laid out and cut a bunch of these dovetails. I ignored the really shallow slopes because I wanted to adopt something more angular. The 10° dovetails looked OK. The 12° dovetails looked better. The 14° tails looked better still. And the 15° looked good as well. Whatever angle you use for your joint, you can rest easy knowing that someone out there (living or dead) thinks you are doing the right thing.
One thing is certain: As dovetails have become somewhat of a cultish joint (a 20th-century phenomenon), their angles have gotten bolder. As Thomas’s slope looked too shallow for my eye, I chose 14°.
There seems to be a trend in life, brought about by online discussion, to become dogmatic and ever more to express entrenched views. This appears to be infecting discussing simple woodworking ideas and techniques. One MUST adopt this means of sharpening a gouge or one MUST always use this glue up technique. Maybe I feel this as a wood turner for we have competing and very expensive gouge sharpening gadgets and each has their dogmatic following of enthusiasts. Me, I just use a standard bench grinder with a cheap and simple jig.
I think the tendency towards dogmatism predates online discussion. I have a wheelmaking book that consists of articles in the trade journals from back when wheels were made of wood. Lots of dogmatism and disagreement there, too.
People can use whatever they like. There are the 14 degree people, and everyone else (who are wrong).
For what it’s worth, I have in my head that Christian Becksvoort uses a 10 degree angle.
And then there are nuts like me that use 45 degrees:
https://www.popularwoodworking.com/editors-blog/arrowhead-joint-box/
As an engineer I can tell you there is only a couple of concerns. First, you need enough angle on the pins so the head does not compress and squeeze through the neck of the tails. And for strength, the joint is in double shear. Therefor, the thickness of the boards, the grain of the wood and grain boundary strength are the important factors.
There has to be a scientific study of optimum dovetail angle, and dovetail angle for various species of lumber somewhere, with or without various adhesives.
I know there are a couple timber framing dovetail jigs that had to determine engineering specs for the strength of their joints in certain timber framing lumbers.
It would strike me as odd if the US department of agriculture forrest service had never researched dovetail joints and other woodworking joints.
iirc Matthias Wandel compared the strength of dove tails and box joints and concluded that modern glues make the joint/angle mute.
Yeah, the angle really doesn’t matter. Even small angles hold great. The Morse taper on machine tools is usually less than 3 degrees.
I chose 14 because it looks prettiest to my eye. I dislike anything down around 7, because it starts to look like a box joints. I find box joints very unappealing.
i found it depends on stock thickness. in 1/4″ i loath a 1:8 ratio cause it looks like a box joint. but in 1″ thick contrasting stock 1:8 looks awesome.
I am quite impressed with this article. I expected some dogma that you must use angle x for softwoods and angle y for hardwoods, where as strict adherence to a specific angle is absurd. Modern aliphatic resin or polyvinyl acetate glue (e.g. yellow or white glue) will make up for any strength issues. With say hide glue you might pay attention to what Robert Bowden has said.
I have one, homebuilt, dovetail guide. I don’t know the angle but it seems to be quite shallow. I keep meaning to make another one. Perhaps today will be the day.
I have that book and distinctly recall reading that part. Basically it meant I could use whatever I wanted. Fitz, in one of her bloggings 5ish years ago talked about a Lee Valley/Veritas inexpensive guide. It is either 1 in 6 or 1 in 7 (just can’t recall) and I’ve been happily using that ever since. I did recently purchase the LAP jig, which is definitely nicer, just need to see if I can change my habits when I reach for one. Ideally, some day, I will make my own out of a nice offcut of wood. Little by little, I am trying to build a complete tool chest of tools that I have made myself. Isn’t too hard to make most tools. Probably the biggest challenge will be to make the chisels but I am sure I can find a local blacksmithing class to learn how to do it.
Where I went, the first session of the blacksmithing class was making a cold chisel out of a truck spring. Change the measurements a bit and you have a wood chisel; I have three that I made, including the one that was just a regrinding of the original cold chisel that I made.
It may simply be that small angles require less chopping.
I use a 1 to 8 at ends (so I can double the number of dovetails at the ends with an 1/8 pin) and 1 to 6 for the rest. Less angle for thick wood and more for thin looks better to me.
the best angle is what Frank Klausz recommends: (something like this) “put the saw on the board and make a cut. then another. there’s a pin. now we put another pin here, and a half pin. then the other half pin. now flip it over and take your pencil, then cut here and chop out the waste. put it together. if it doesn’t go the first time, get a bigger hammer. done.” (every one looks at their watch and sees less than 4 minutes have passed).
I draw them in Adobe Illustrator and tweak until I like the look, then spray glue printouts to the boards. It’s lame – but works. I have NO idea of the angle.
You can bisect a 30˚ angle from a drafting triangle and get 15˚. No need of trigonometry, protractor or bevel gauge. As long as you have the straight edge and dividers out, you can construct an equilateral triangle and bisect one of the 60˚ angles twice, thereby avoiding the use of the drafting triangle. So I will probably start my journey into dovetails with 15˚ angles.
Cut two strokes with the dovetail saw. Let the blade droop to one side. Continue the cut. The set of the saw determines the angle (together with how deep your initial cut was)…
Oh, yeah, that’s tails first.
How about different angles for pins first, or tails first? Has anyone done a study on this?
I agree with Jesse Griggs- it all depends on the thickness of the stock you’re using. I cut some very small dovetails in 1/8th thick ebony for a tray and 1:3 did the trick. Any other angle looked vertical. And yes, I had to use a magnifying glass and rub chalk in the cut lines to see where I was supposed to cut. Thats why I never buy dovetail angle templates. and use a sliding bevel instead.