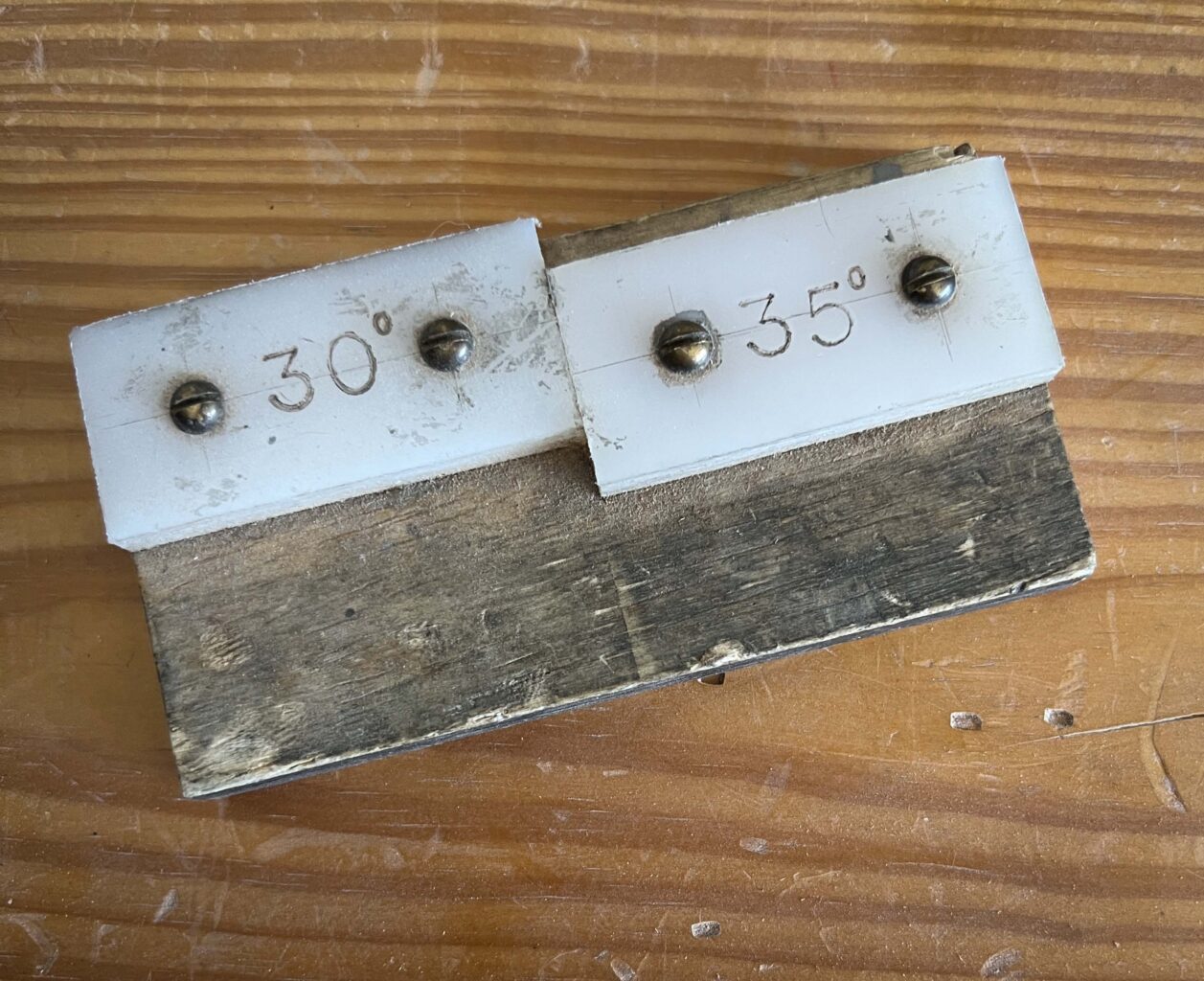
Our angle-setting guide.
Every time we get questions about our setting jigs, I joke that I’m going to start making them to sell. Had I done it years ago, I could probably now afford that paint job my house needs…or at least afford some fancy cat treats!
The questions have ticked up recently, due to the publication Christopher Schwarz’s book “Sharpen This.” But I still can’t bring myself to make these jigs, ’cause it’s so easy to make your own. But also because different honing guides require different placement of the blocks (it has to do with how far the blade projects)… and I don’t have time to make these for every guide out there. So here’s how to make the one we use, for our Lie-Nielsen honing guides:
Screw two pieces of ultra-high molecular weight polyethylene (UHMW) to a block of plywood. Done. No magnets. No magic.
OK, OK…here are a few more particulars:
The 1/2″-thick plywood block is 4-1/4″ long x 2-1/8″ wide. (Other sizes would work.) We like plywood because it is unlikely to warp as much as solid wood.
The 1/4″-thick UHWM plastic is left over from another project – but it’s the perfect thing for this. It doesn’t get munged up as easily as a block of wood when you register a blade against it, so it lasts a lot longer. The two little blocks of UHWM are 1″ wide x 1-1/8″ long.
The plastic is screwed in place with brass screws, because they won’t rust.
The 35° block is 7/8″ from the front edge; the 30° block is 1-5/32″ from the front edge.
Those are the only two angles at which we hone/polish 99 percent of our edge tools (and really, we mostly use only the 35°). But if you want a lot of angle choices on your jig, Lie-Nielsen Toolworks has a free download for a fancy one. But we don’t do fancy when it comes to tool sharpening – ’cause making them dull is a lot more fun.
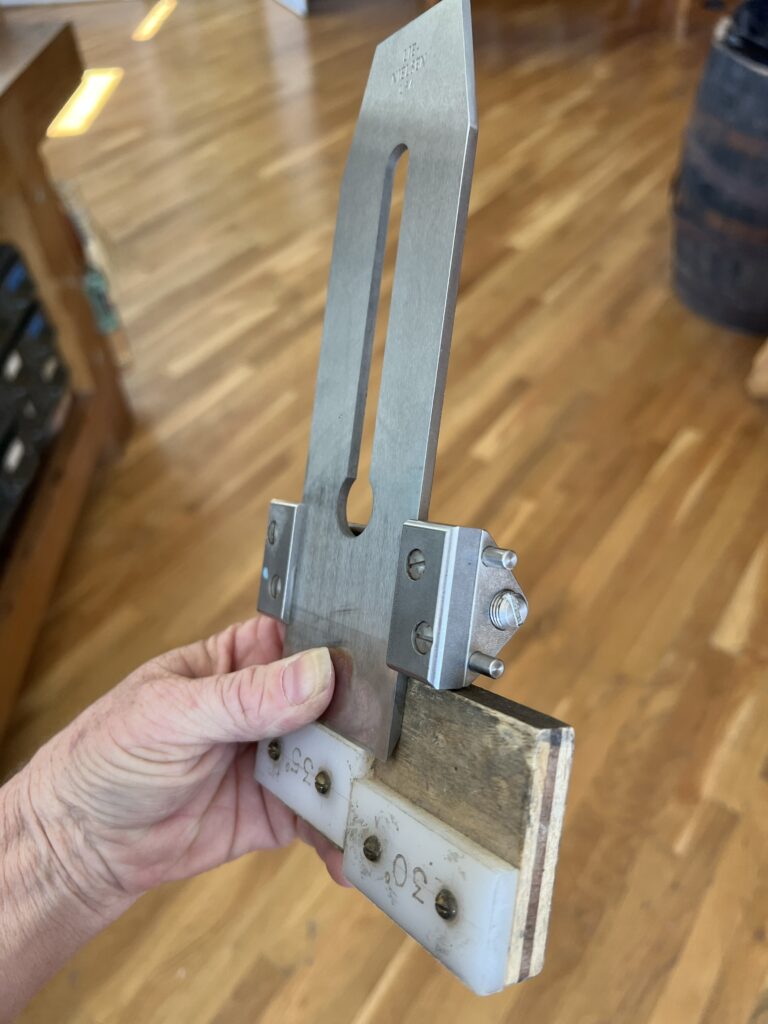
But what if you don’t have a Lie-Nielsen honing guide, or you want different angles? Well, you’ll just have to figure out the proper projection to get the setting block in the right place. Here are two ways to do that.
Put a blade in your guide, then put a Tilt Box on the blade and register the bevel against a flat surface. Adjust the guide until the readout matches your goal angle. Tighten the guide, then measure the distance from the body of the guide to the end of the blade. That’s the distance from the guide’s body the setting block should be secured to the setting jig’s base.
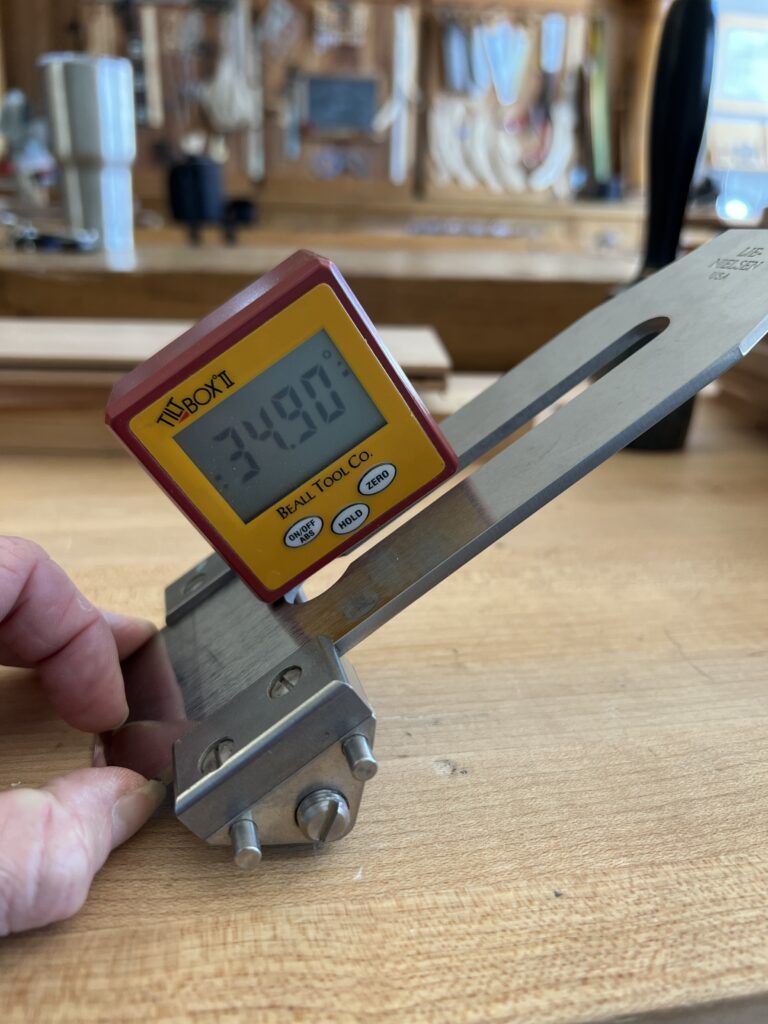
The Tilt Box II in use.
Or put a blade in your guide and register the existing bevel against a flat surface. Put a protractor upright on that same flat surface. Align the business end of the blade with the center of a protractor (make sure the 0° on said protractor is on the edge – they aren’t all). Adjust the guide until the angle matches the one you want.
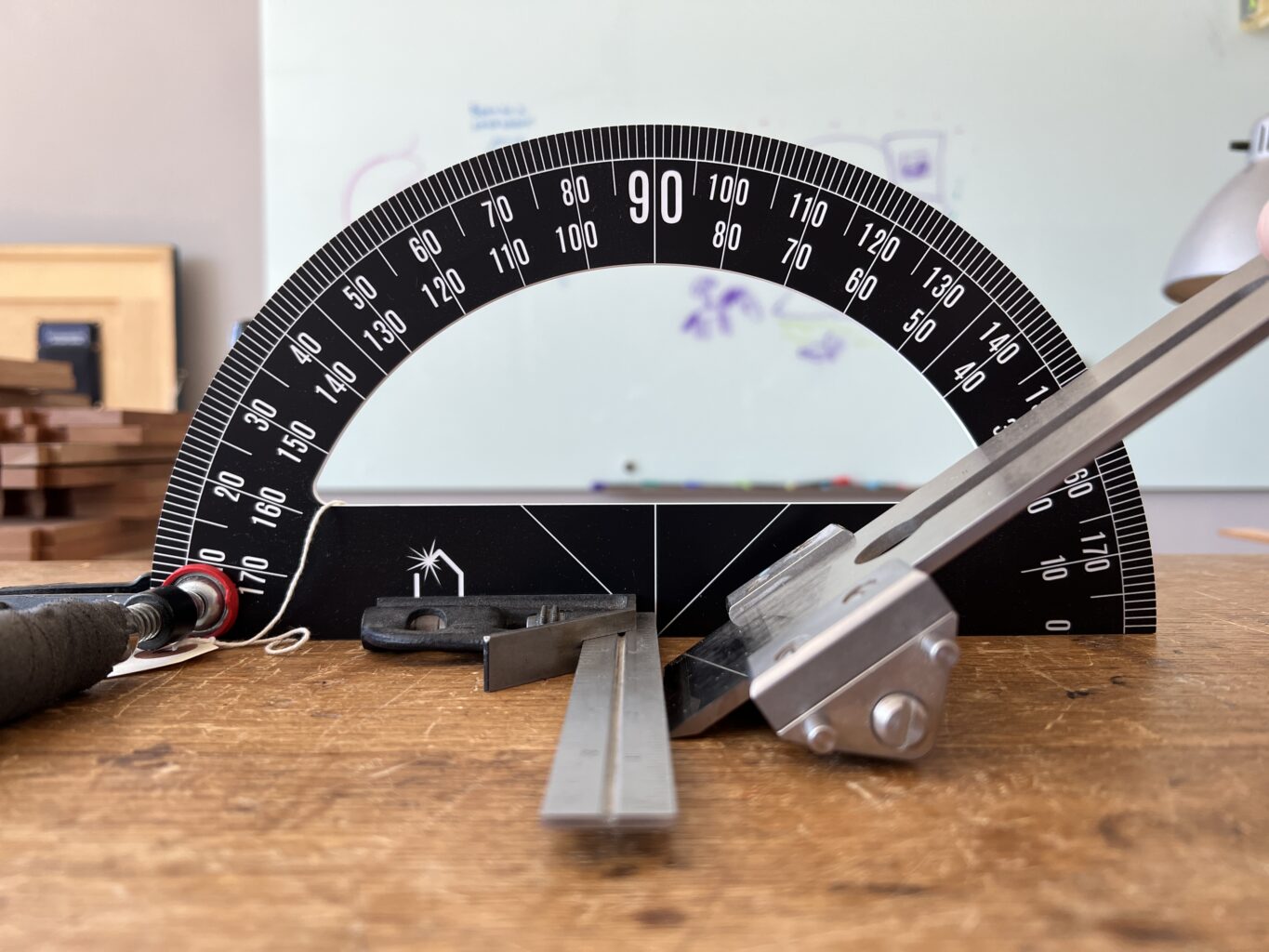
— Fitz
Two minor, additional tips, from personal experience:
If you also have the mortise chisel jaws to go with the Lie-Nielsen honing guide (or have some other guide into which your mortise chisels fit) you may want to make the stop blocks a bit taller than those shown in the photos here, to make sure the edge doesn’t pass above them.
And if for some reason you want to make a second, identical angle-setting jig (as a spare, or for a travelling tool kit, or whatever) don’t bother going through the projection finding process again, and don’t measure the distance on the existing jig either; just set and lock in the projection with the first jig, and then use the guide and blade as a reverse stop against which to fix the new stop block in place.
You forgot one step: “Ensure the slots in your screw heads are parallel to the block’s edge.” 😅
Well that’s just assumed – of course one should clock the screws!
Clock around the block!
If making isn’t your thing (ummm), there are a few etsy sellers who 3d print these for different guides.
My vintage 05 Record plane (made in England) has 25 degrees stamped on the cap iron as a “whet gauge” not 30 or 35?
A lot of people grind at 25° and then hone at 25°. Nothing wrong with that except for the fact that the edge is not as durable.
I like making my own jigs but sometimes its nice to buy them from someone you respect and appreciate the knowledge they are sharing. So if you made one for sale I would buy it.
I got tired of pulling out the ruler when it was time to put a new edge on steel. so, I cut a fine line into my bench at the right distance from the edge of the bench and filled it with red nail polish. I put the iron in the jig set it on the edge of the bench adjust the iron and sharpen. that was over 10 years ago, and it is still there, and I still use it. I don’t need to look for it when I need it.
You might consider fastening a stop to your sharpening area. I used to use a scribed line on my bench to set my tool’s projection. I found that a fraction of a line difference made a significant difference in how long it took to hone a new edge.
When I switched to using a stop, the honing went faster.
Just my observations….
Well, I didn’t think about how just a little difference in the setup would move the edge. I only use the jig to set an edge angel, I free hand it after that. still need to fix the angel now and then. I will set a stop for the students for sure.
Any large grocery store carries the UHWM in the disguise of thick plastic cutting boards. Substitute it for the plywood section too.
I was just about to ask if repurposing an old cutting board, or buying a small one, would be a good source for the plastic!
An additional note: for honing guides like the Eclipse and its knockoffs that use two different clamping positions for chisels and plane irons, you need different sets of stops.
Thanks for the suggestions of tilt-box or protractor for setting angles. Much nicer than trigonometry 🙂
So, how do you get the nice 30 and 35 degree markings on the UHWM?
Number stamps
OR … learn to sharpen freehand. No guides or jigs needed.
Seriously, thanks for the tutorial I still use a guide for certain plane irons.
I’m with you, but….. it sure was nice to have my stop and eclipse guide (neither have been used in over a year) when my 6 year old asked to sharpen his block plane today. he did great working through the grits and came out wicked sharp. I’ll teach him free hand in a couple years. he doesn’t have the muscle control and discipline to keep the blade locked in position freehand. for now the guide is perfect.
The plastic blocks should each be 2-1/8″ in length.
What tools do you sharpen at 35 versus 30?
I sharpen all my bench tools at 35. The 30 is for guests….