Editor’s note: With the first Stick Chair Journal shipping out very soon, we wanted to highlight the woodcut on the cover. >>Stay tuned for a shipping date!<<
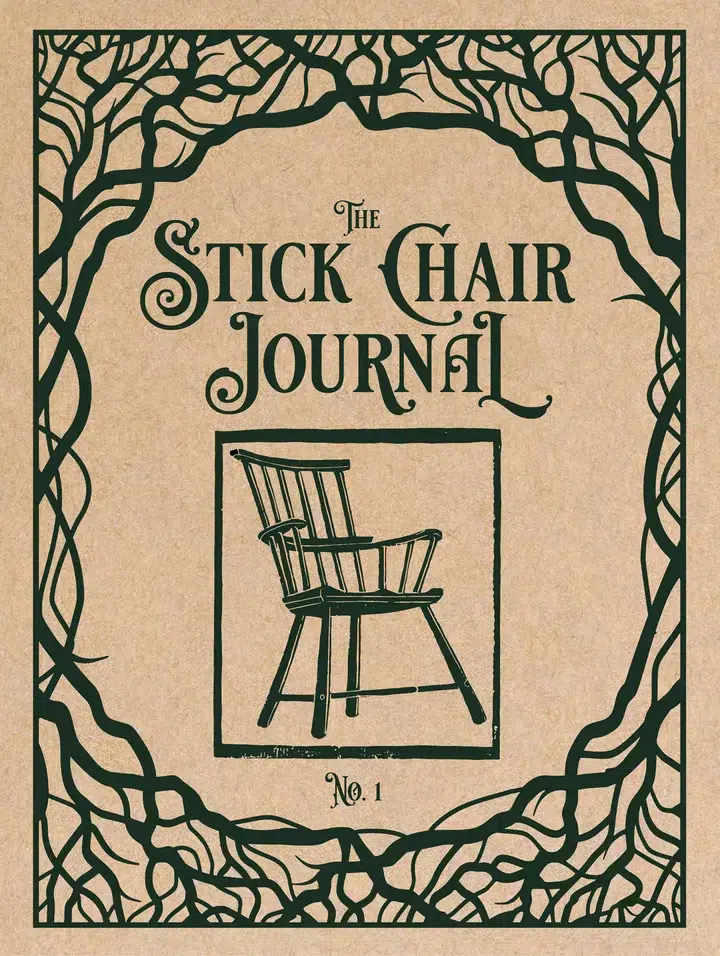
Making a Woodcut
When making a woodcut you need to make sure to remember two things:
- The printed image will be a mirror of the image you see on the block you are carving.
- You have to remove the areas in the woodblock that will not be printed.
In short, this means that the black lines you see on the finished image are the places you didn’t cut any wood away on the block. To make a woodcut, you have to think in the negative and in mirror.
Stick Chair Journal No. 1
I started this woodcut using a photograph of the beautiful chair featured in the Stick Chair Journal No. 1, made by Christopher Schwarz.
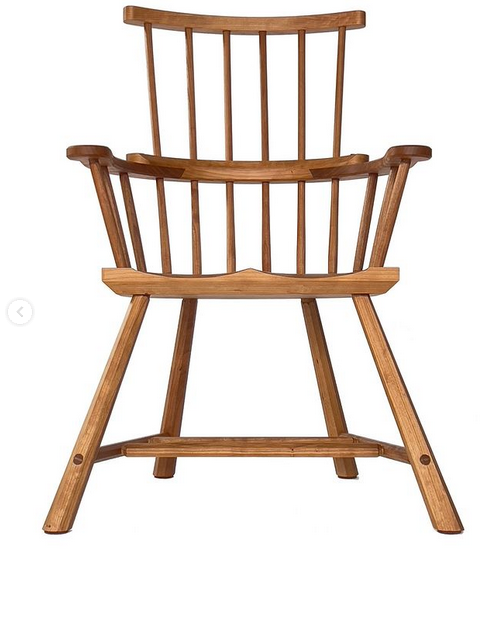

I made some sketches to see how the print would look. For sketching, I recently started using black paper and white pens. In essence, this is exactly the process used in making a woodcut.
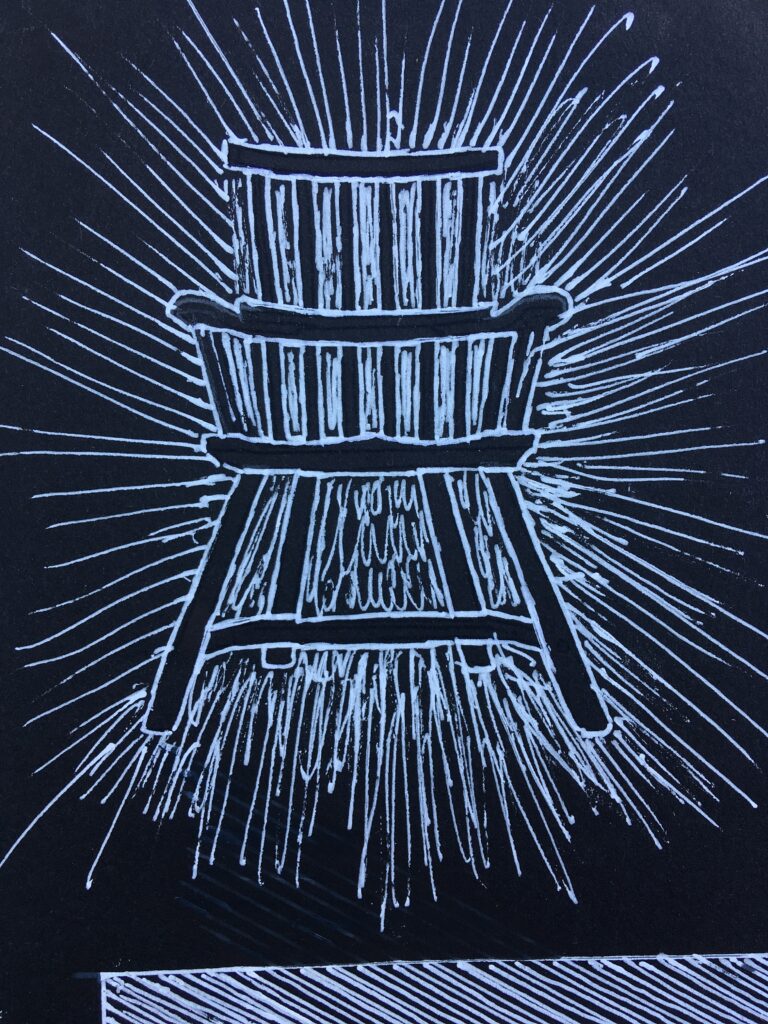
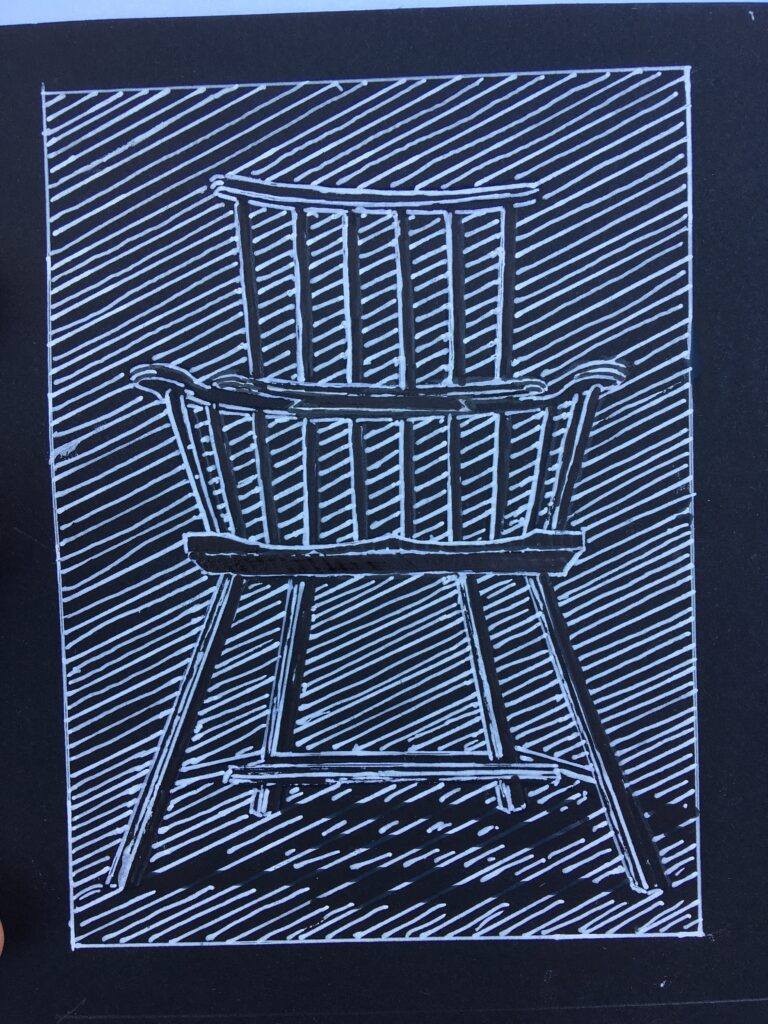
I initially wanted to create a ‘grey’ background behind the chair, similar to my wood engraving of a Welsh Highback Chair but the diagonal lines proved to be too distracting for the cover.
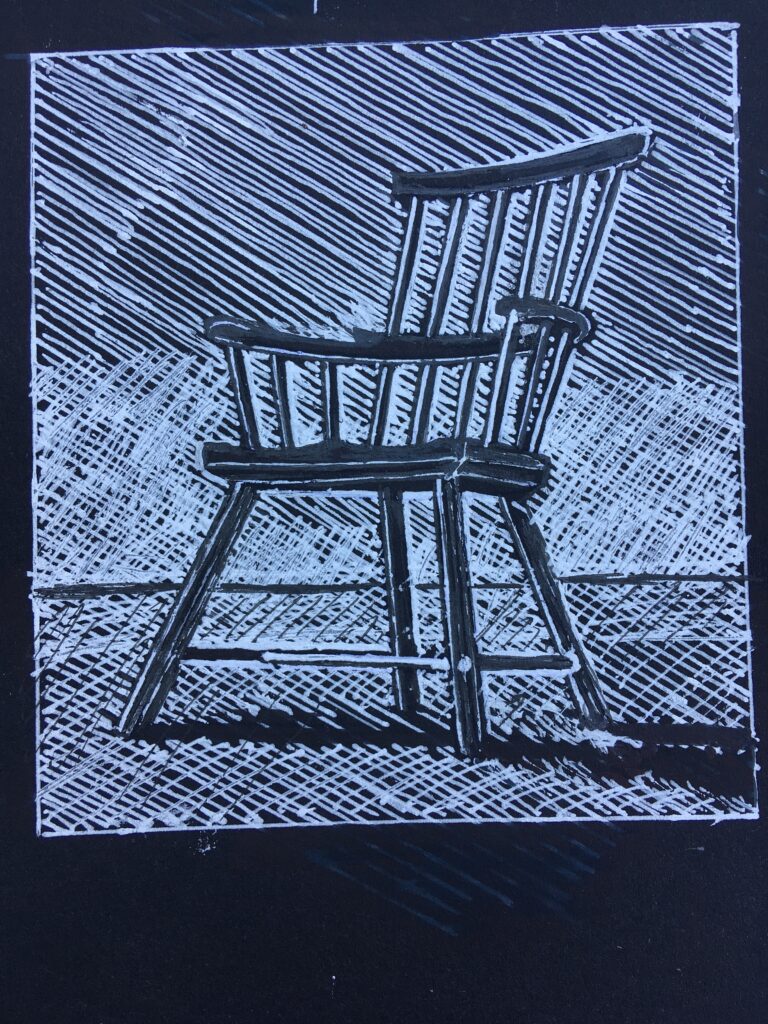
So we decided on a blank background instead, to really make the chair stand out. This woodcut also became the design of the Stick Chair Merit Badge.
A woodcut is a play between white and black lines (or, in the case of this cover, green ink and Kraft paper). Though I like seeing a silhouette of a chair, for my woodcuts I like to add some lines to it to mimic light.
I added white lines to the parts of the chair that would be illuminated from a light source coming from the right. Every stick therefore has a white line running from top to bottom.
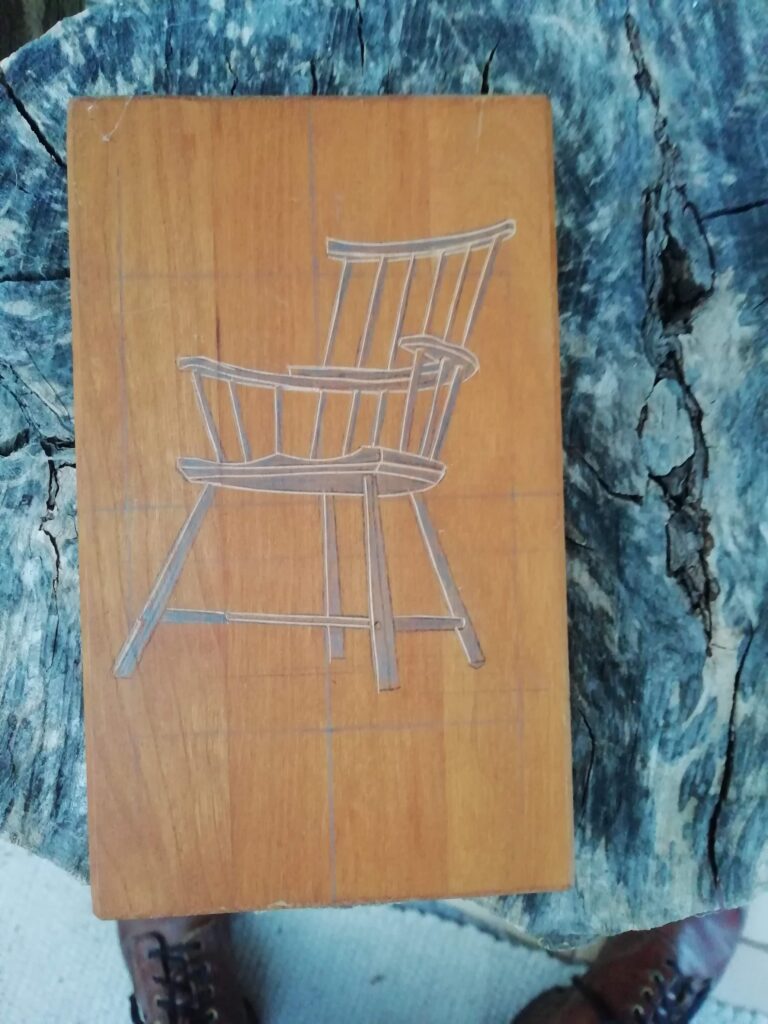
With the design complete, I traced the outlines of the image onto the wood using carbon paper and a fine pencil. I used a piece of cherry wood that was more or less the correct dimensions for the cover.
As you can see, I didn’t mirror the design before carving it. So much for Rule #1.
Next was removing all the “white” in the image – all the parts that won’t receive ink. This is the most enjoyable part of making a woodcut. After all the planning has been completed, carving the design into the wood is a very pleasurable experience.
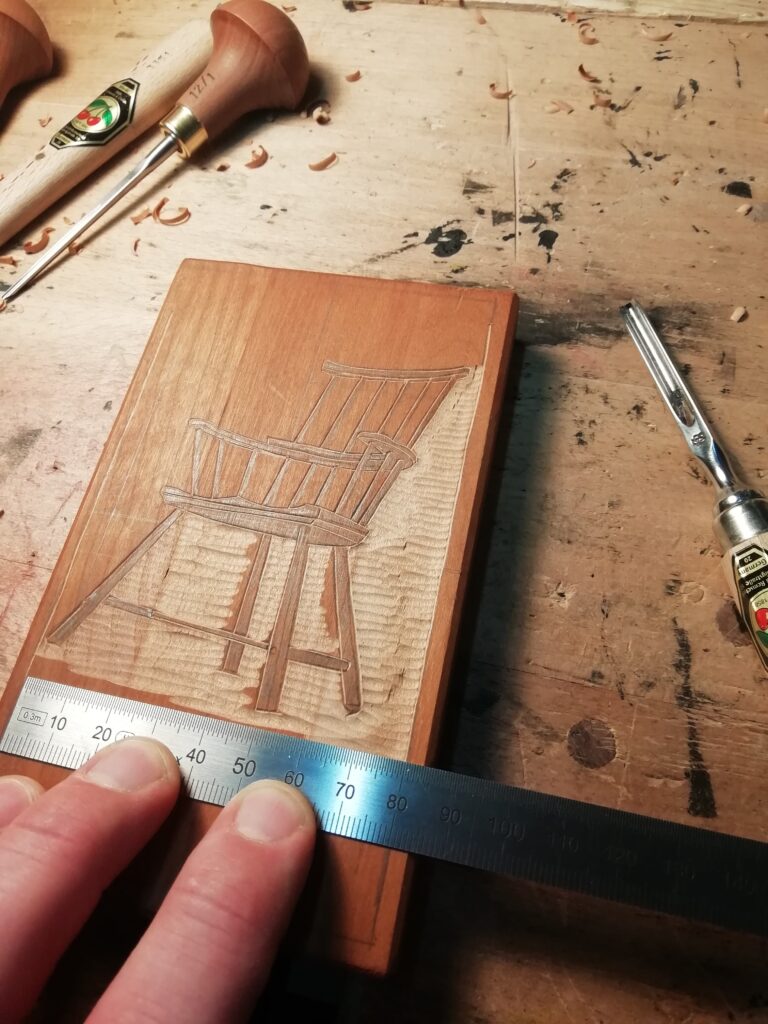
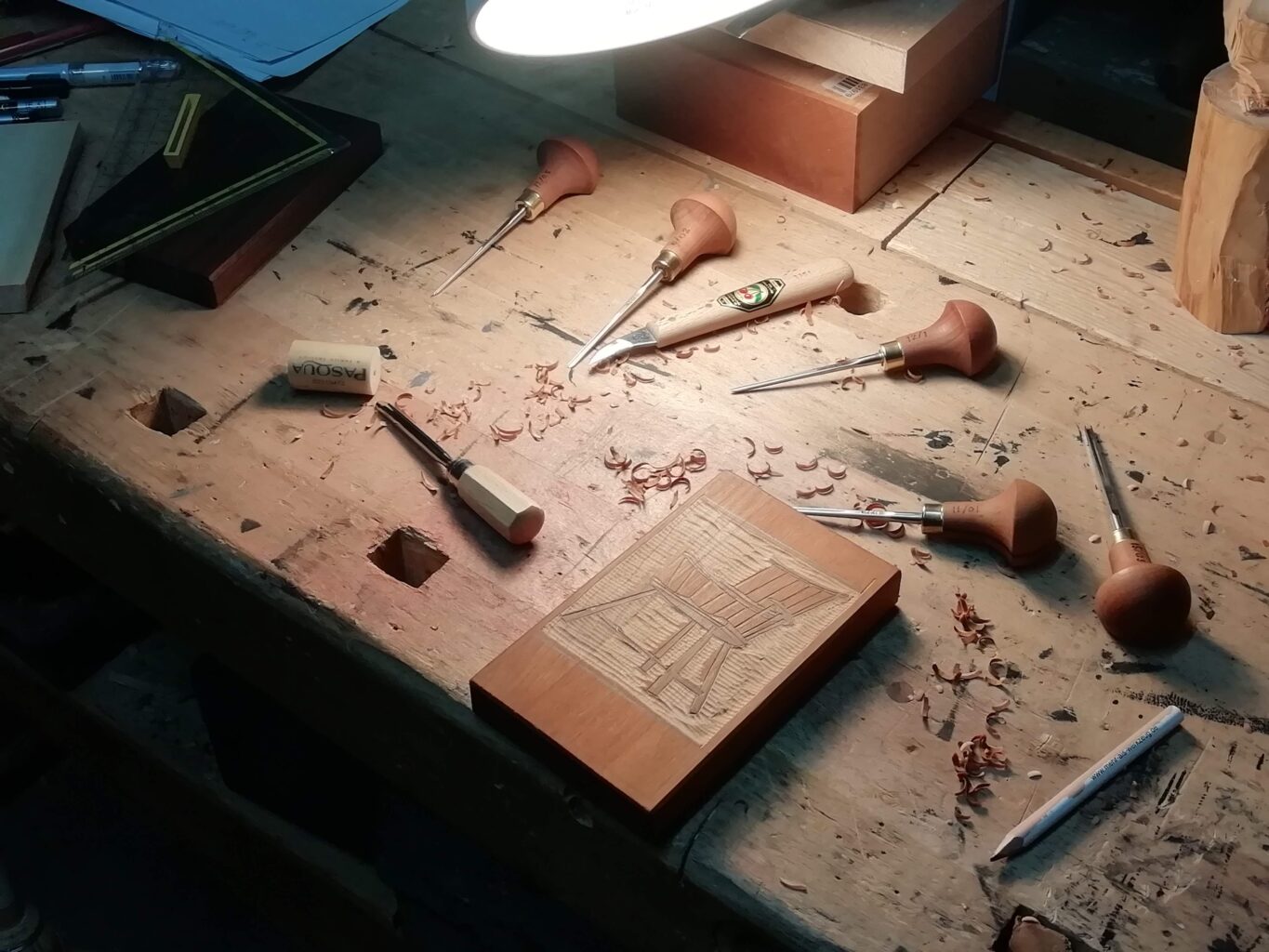
A first quick printing reveals any areas that were not completely cut away.
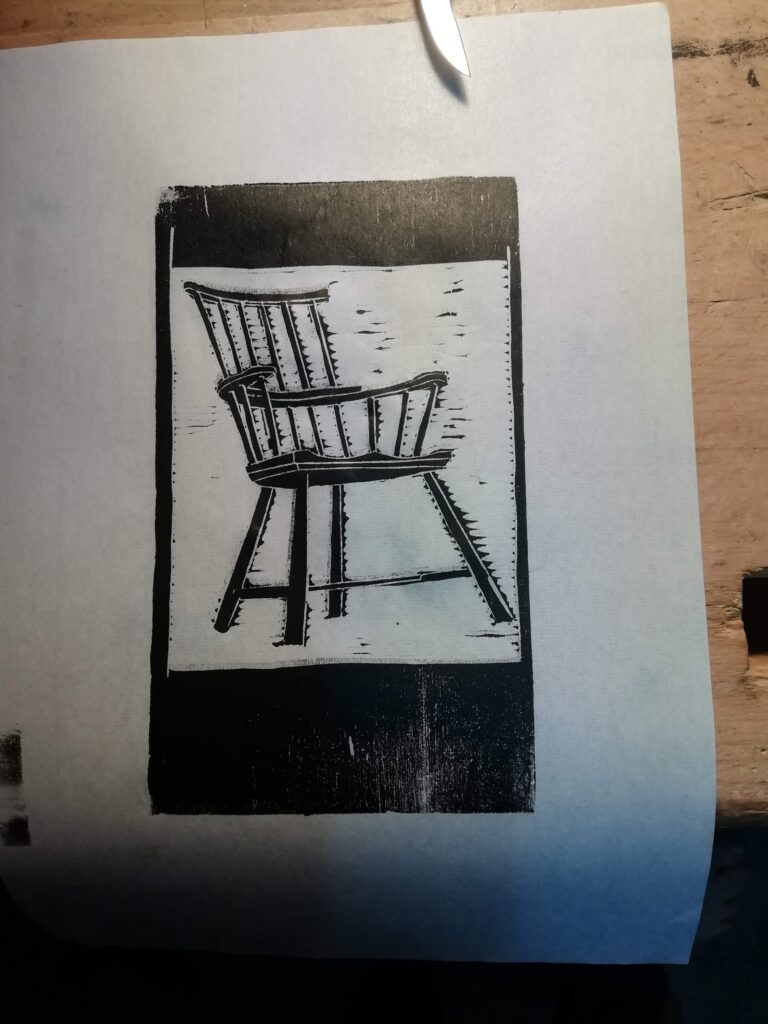
When there is a large white area present, ink sometimes ends up on the high spots that need to be cut away deeper.
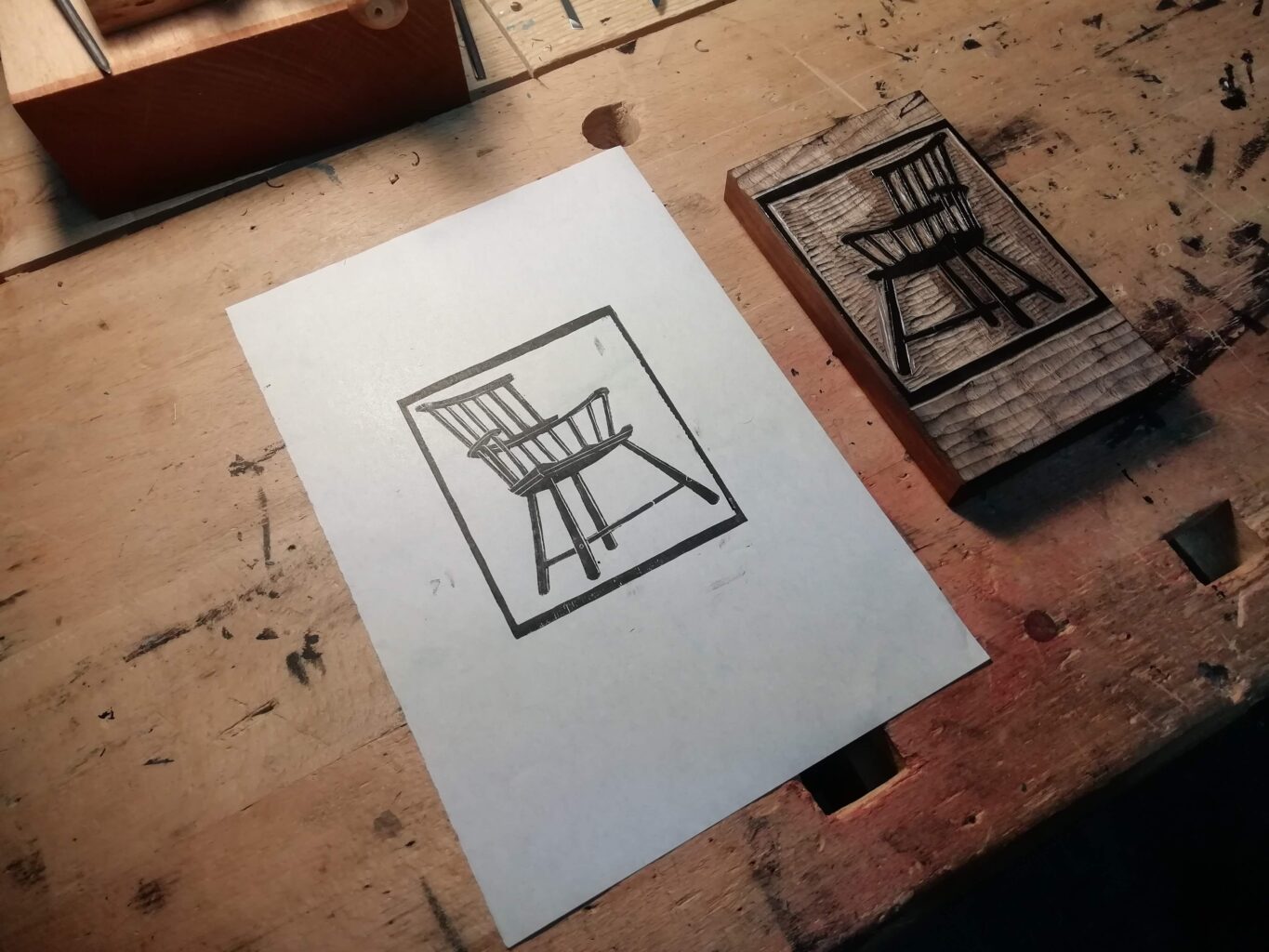
I removed the high spots so they wouldn’t receive ink and cleaned up the rest of the chair. With the woodcut printed to my liking, I scanned it in so it could be used for the cover of The Stick Chair Journal.
The Journal will ship this week and I am very happy and proud that my woodcut adorns the cover.
— Rudy Everts, aka Underhatchet
Absolutely gorgeous work, Rudy, and a great explanation of the process, too!
I’ve never tried my hand at a wood cut, but many, many moons ago did a series of linoleum cut prints (a fairly similar process) in art class at school.
Thinking about that makes me wonder if any of them are still in my old art class portfolio, up in the attic. I shall have to have a look!
In the meantime, though, I’m eagerly awaiting the release of the SCJ #1!
Cheers,
Mattias
Thank you Mattias! Good luck finding your linoleum blocks, those are fun too (and like you say very similar)
Please do a follow up (unless it’s in the book) about what ink and applicator you use. Paper?
Would printing an image and transferring onto the wood with lacquer thinner help those of us that are lacking in drawing skills?
Yes, it would! The Japanese woodcuts are first drawn by the artist on paper, then glued on the printing block. Then, the carver cuts the block (rather blocks, there are several for coloured prints).
Yes, the Japanese printmaking technique is quite laborious! But beautiful as well.
There are various ways to transfer the design to the block, I like to draw it on there with pencil but gluing on a piece of paper would work well too
Very nice.
Do you make the final cleanup cuts across the grain as well, or do you clean up along the spindles by carving with the grain?
I don’t want to be the one sharpening that 12/1 gouge
Along the spindles I followed the grain. I had to sharpen my 12/1 gouge once and I used magnifiers, which helped.
Love the woodcut prints. I can’t remember if it was 6th, 7th ot 8th grade that school let the class do a linoleum cut, I loved it then and the idea now, will have to be put in the line on things to learn. Can’t belive they gave us sharp objects.
When I made linoleum prints as a kid, all the carving tools were blunt. This did not make the process any fun at all. Great that they gave you something sharp to work with.
I loved screen printing back in highschool, and this has got me excited to give it another shot. Thanks for the inspiration!
Very happy to hear that!
Stupid question but when you are confused, is the paperback book available yet? Can you pay by check?
It’s now available. And to pay by check, please send an email to help@lostartpress.com
Great post Rudy. Thanks for explaining the process, it is much more involved than I had imagined. The final print looks amazing!
Thank you, Pascal! Yes, there are quite a few steps involved in making a woodcut. And one wrong cut in the block….
Have you considered a limited-run printing from the block?
Signed and numbered there might be an audience for 50 or 100.
If there would be enough interest, I would definitely consider it.
I love woodblock prints. I just ordered my copy of the journal & am looking forward to the cover. Your explanation makes it better.
Have you ever made a multi-color woodblock like the japanese ones?
Thank you. I have yet to make a multi-color woodblock print but I will definitely do so at some point, it is a beautiful technique.
I’m just curious, what size/sweep of gouge did you use for the general background carving? Thanks!
Hi Andy, for the background I used a small #6 gouge, 6mm wide.