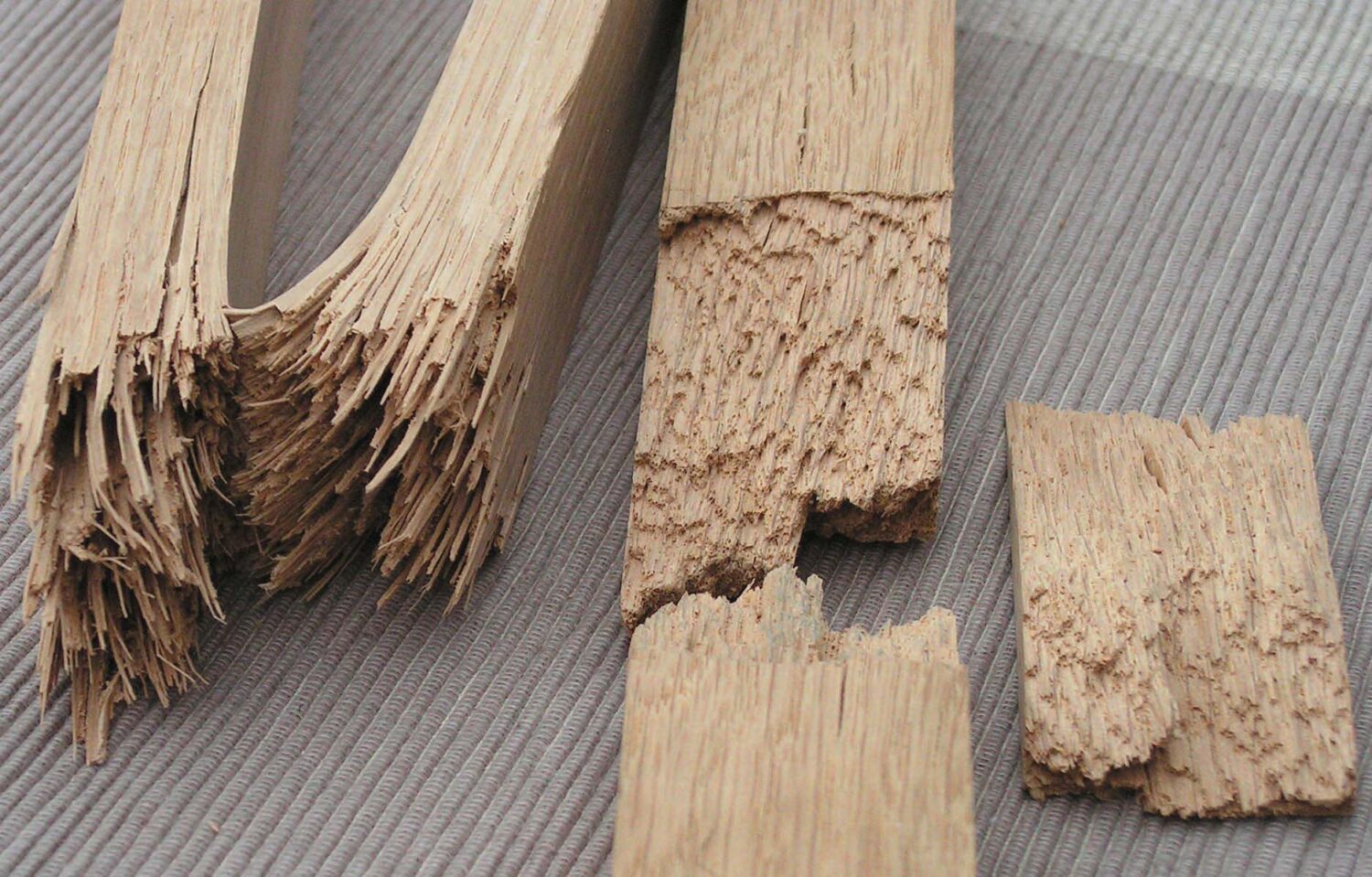
The following is excerpted from “Cut & Dried: A Woodworker’s Guide to Timber Technology,” by Richard Jones.
Jones has spent his entire life as a professional woodworker and has dedicated himself to researching the technical details of wood in great depth, this material being the woodworker’s most important resource. The result is “Cut & Dried: A Woodworker’s Guide to Timber Technology.” In this book, Jones explores every aspect of the tree and its wood, from how it grows to how it is then cut, dried and delivered to your workshop.
Jones also explores many of the things that can go right or wrong in the delicate process of felling trees, converting them into boards, and drying those boards ready to make fine furniture and other wooden structures. He helps you identify problems you might be having with your lumber and – when possible – the ways to fix the problem or avoid it in the future.
“Cut & Dried” is a massive text that covers the big picture (is forestry good?) and the tiniest details (what is that fungus attacking my stock?). And Jones offers precise descriptions throughout that demanding woodworkers need to know in order to do demanding work.
For the first year or two of working wood in the 1970s, I didn’t come across the term brash wood because the craftsmen I worked with called the condition “carroty” or “carrot wood” and I assumed, being young and naïve, this was the normal name. The woodworkers around me, on finding some particularly weak stick would say things like, “It’s rubbish; the stuff just carrots off in your hands.” It was an apt description because a brash break in wood is visually slightly similar to a carrot broken into two half-lengths.
Brash wood has a variety of related names including brashy, brashness and brashiness. Other names for this condition are brittle heart, carrot heart, spongy heart, brash heart and soft heart. Natural brashness or brittleness develops in the living tree caused by the way a tree grows and the stresses it experiences in life. In every case brash wood is weak wood and it unexpectedly snaps across the grain under a load normal wood of the same species would carry with ease.
Brashness often develops in association with cross shakes discussed in section 13.3.3. In another instance, it develops in exceptionally slow-grown ring-porous species where the tree lays down a high proportion of soft spongy and weak spring growth, and a low proportion of denser stronger summer-growth wood. Ring-porous species with unusually narrow year-on-year growth rings are one possible feature to look for to identify brashness; the result of this growth pattern is the wood is also likely to be exceptionally light for its species, and this may indicate potential brashness. Fast-grown conifers tend to lay down a much greater proportion than normal of weaker, lighter spring wood than they lay down in denser and stronger summer wood, and this, too, is brashy. Juvenile wood is frequently brashy, especially if it has grown fast with widely spaced growth rings. Unusually dense reaction wood in coniferous trees, known as compression wood, is often brash, and this type of wood should not be used in furniture, but carvers and turners may find uses for it (Hoadley1, 2000, p 99-100). Shield (2005, p 133) discusses brittle heart or brashness being the result of growing stresses within plantation-grown Eucalypts. He notes that growth increments develop tensile stresses in their length with each successive new growth increment developing slightly more tensile stress than the previous year’s growth. To compensate for this the tree develops longitudinal compression stresses toward the tree’s core. Finally, an artificial cause of brashness is induced when wooden artefacts are subjected over time to high heat “such as wood ladders used in boiler rooms.” (Rossnagel, Higgins and MacDonald, 1988, pp, 43-44.)
The lesson for woodworkers is brash or brittle wood is not appropriate for load-bearing structures, e.g., floor joists, floorboards, table or chair legs and rails etc. The safest thing is to not use it at all except perhaps for purely decorative items such as small carvings or other non-critical parts. Secondly, materials other than wood might be better choices for shelving, steps, ladders and so on in high-heat environments including forges, boiler rooms, certain areas within commercial kitchens, glass-blowing workshops etc.
interesting, does he go on to show how to easily identify a board that is brashy, or are we left with knowing only after it breaks?
I don’t know of any way to identify brash would except for the fact that it is slow growth and weighs much less.
The clues in the text above are a guide for identifying potential brashness. Also, as mentioned, if the piece seems lightweight compared to similar sticks of the same species might be a warning sign. Lastly, if you’re suspicious of brashness, try breaking the piece. I have seen brash wood break through the simple act of carelessly dropping a piece on the floor or through other forms of rougher handling than normal.
Based on the above excerpt and LAP’s description of the book I wish it had been available when I was majoring in forestry in the 1970’s. During my third year I took “Wood Technology And Utilization.” The course text book was difficult to comprehend. Jones’ presentation would have been a welcome supplement. I also would have welcomed him as a guest lecturer in as much as his bio indicates that he is a natural teacher. Is that because he doesn’t have “,PhD” after his name? If anyone is questioning the monetary value of this book ($71) consider this, I paid $50 for the aforementioned text book in January, 1977. I opened it today for the first time since May of that year and the price sticker is still on it!
As to Jones’ question, “Is forestry necessary?” let me state unequivocally, “Yes it is.”
In the business of repairing a lot of newer Asian import furniture, brash wood (and extreme grain run-out) was way too common. But I think the worst was the 1.5″ punky knot in the middle of the top beam on a sofa. It only took someone leaning on it to get it to snap. I used to have a (silent) comment, “Well, there’s a piece of wood that just should have gone into the scrap pile.”
I took the “Make a Chair from a Tree” class with Drew Langsner decade ago and learned that you follow the grain by riving for maximum strength.