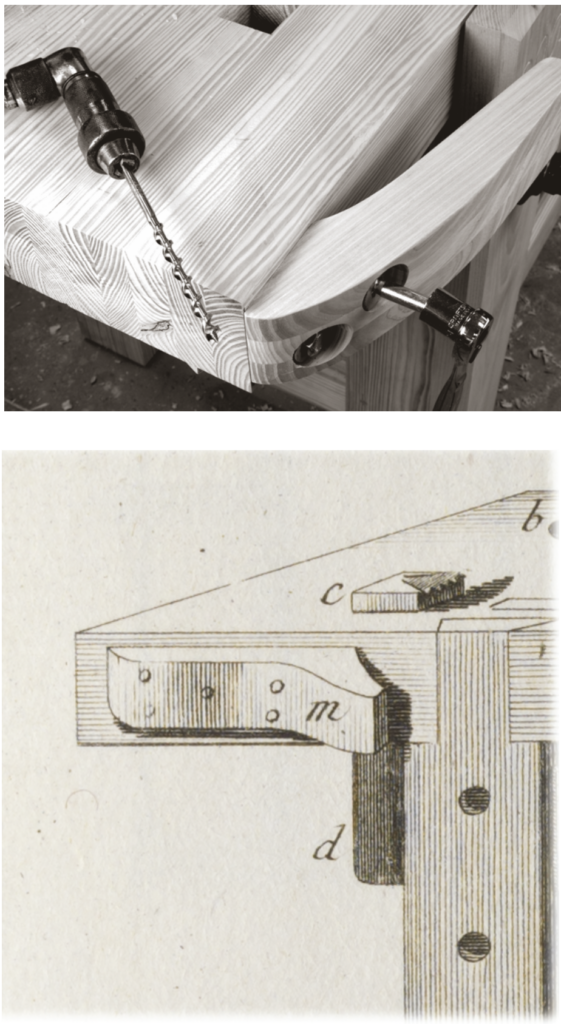
The following two early workholding methods are excerpted from “Ingenious Mechanicks,” by Christopher Schwarz.
Workbenches with screw-driven vises are a fairly modern invention. For more than 2,000 years, woodworkers built complex and beautiful pieces of furniture using simpler benches that relied on pegs, wedges and the human body to grip the work. While it’s easy to dismiss these ancient benches as obsolete, they are – at most – misunderstood.
Schwarz has been building these ancient workbenches and putting them to work in his shop to build all manner of furniture. Absent any surviving ancient instruction manuals for these benches, Schwarz relied on hundreds of historical paintings of these benches for clues as to how they worked. Then he replicated the devices and techniques shown in the paintings to see how (or if) they worked. This book is about this journey into the past and takes the reader from Pompeii, which features the oldest image of a Western bench, to a Roman fort in Germany to inspect the oldest surviving workbench and finally to his shop in Kentucky, where he recreated three historical workbenches and dozens of early jigs.
The crochet (French for “hook”) could be described as a planing stop attached to the edge of the workbench, but that doesn’t quite capture its full utility. A good crochet is also good for securing work for dovetailing and tenoning.
There are a couple kinds of crochets out there. Some of them are like wedges. You press the work into the opening and its V-shape helps hold the work (though you will still need a holdfast to complete the job). Old French ones, as shown in “l’Art du menuisier,” work more like a planing stop as opposed to a wedge. Their opening is square instead of V-shaped. Both forms of crochet work, but I prefer the V-shaped ones on my benches.
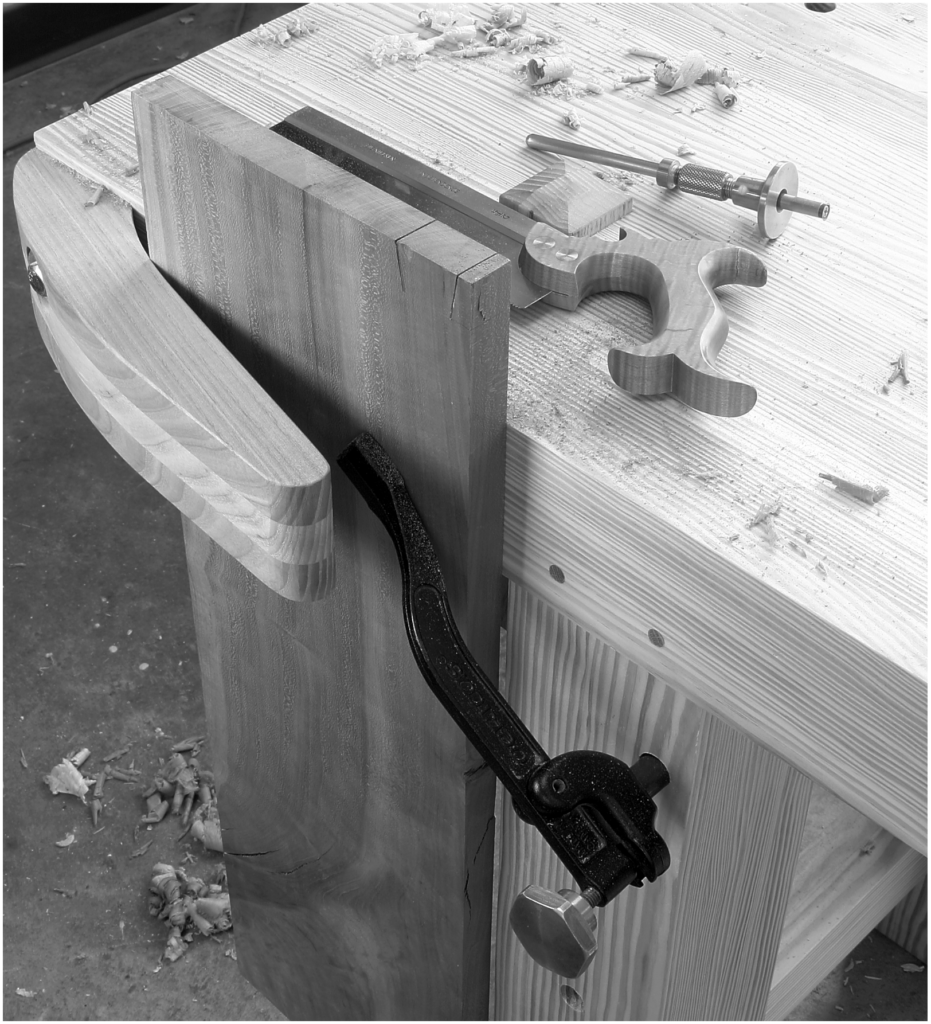
I make my crochets out of a tough and springy wood, such as oak or ash. I recommend you make the hook big enough so that it can handle 8/4 stock. So, the opening should be slightly larger than 2″. Many early crochets are shown attached with nails. I prefer 6″-long carriage bolts with washers.
Using the crochet for working on the edges of boards is straightforward. Typically, you secure the work to the front of the bench with one or two holdfasts (depending on the length of the work). Then you push the end of the board into the crochet to prevent the work from shifting as you plane it.
If I have a lot of boards of similar widths to work (say for a large tabletop) I take a different approach. I use holdfasts to secure a 2×4 to the front legs of the bench that will act as a platform for my boards. Then I press the end into the crochet. Gravity and the force of the plane immobilize the work.
Crochets can also be used to affix the work so you can cut dovetails or tenons. Put the edge of the work into the crochet and affix it to the front edge of the benchtop with a holdfast (or a bar clamp across the benchtop, if you are sadly holdfast-less).
Notches & Wedges
In many old paintings and drawings you’ll see benches that have no vises but instead have a large rectangular notch cut into the edge or end of the benchtop. In many cases, these notches are used as face vises. You put the work in the notch then use a wedge to immobilize it. I’ve had great – actually, quite spectacular – success using these notches for cutting tenons and shaping the work with chisels, rasps and files.
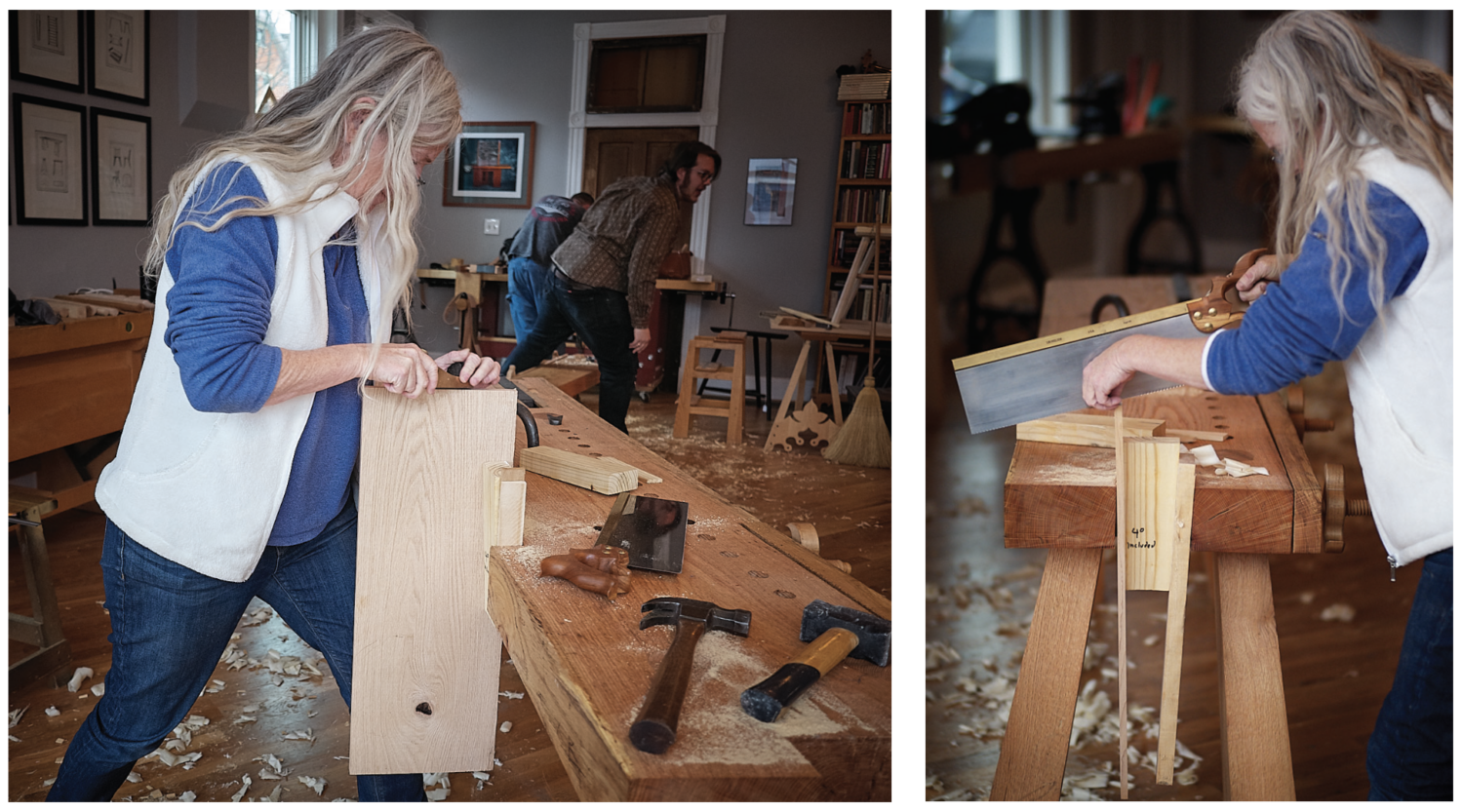
It took a little experimentation, however, to get the wedges right. As it turned out, I was making things too complicated. At first, I used oak wedges in the shape of a right triangle that I planed clean so they had an angle at the tip of about 15°. They held the work, but not reliably. So, I tried isosceles-shaped wedges with a variety of angles, looking for the magic number.
After several hours of messing with the oak wedges, I thought I was headed down the wrong path. So, I went to my scrap pile and grabbed a white pine 2×4. I sawed it to 12″ long and tapered one edge with a jack plane (I later measured the angle at 2°). Then I drove it into a notch.
It cinched down as hard as any screw-driven vise I’ve used. It worked so well I laughed out loud.
If you are interested in making these notches (what do you have to lose?), here are some details. In the old images, the notches have vertical walls. Some fellow woodworkers have suggested cutting them at an angle that is sympathetic to the wedge’s angle. I haven’t found that necessary.
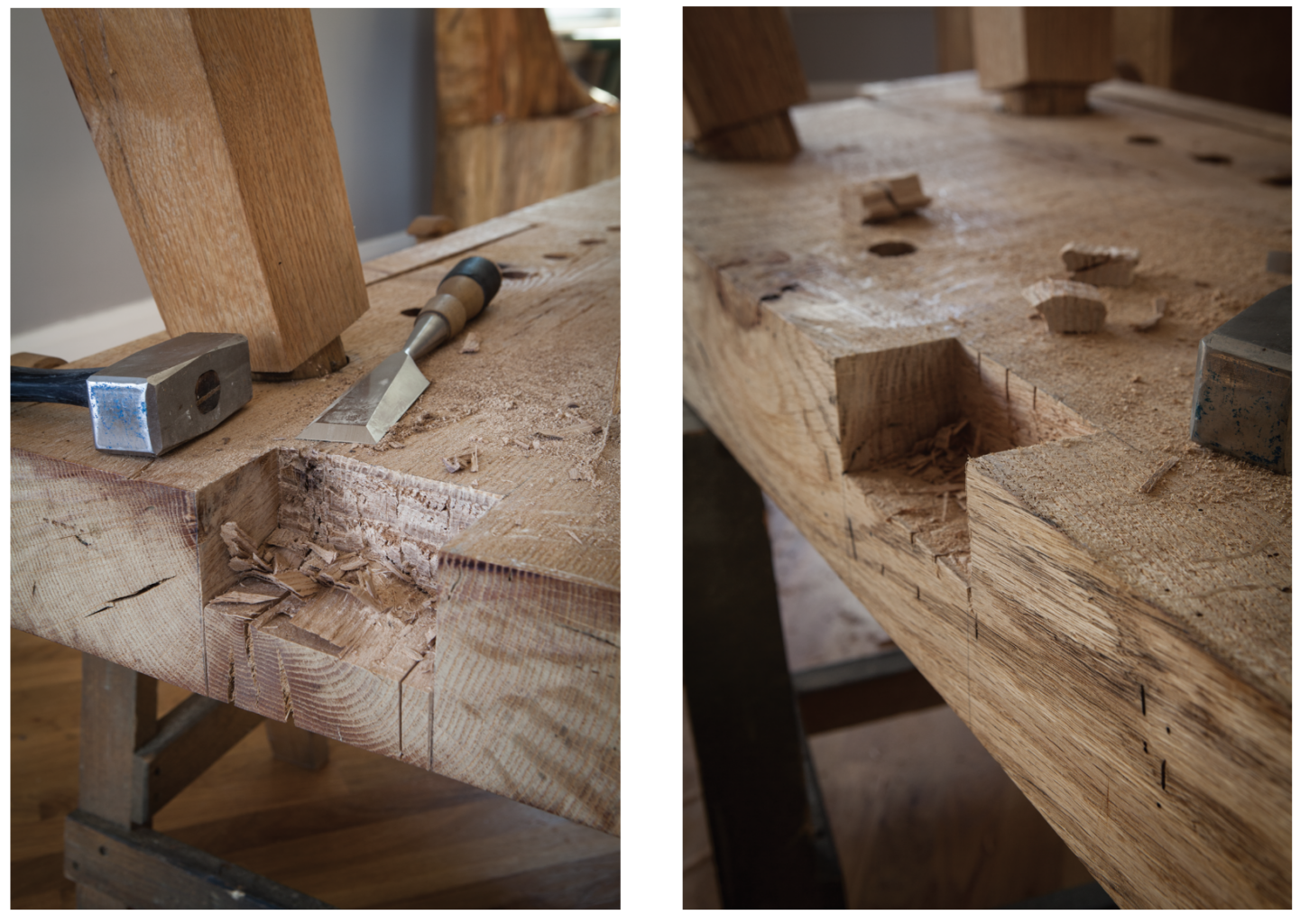
On some benches, the notches are in the end of the benchtop. In others, they are cut into the edges. I tried both. Functionally, I couldn’t tell any difference between them. They both held just fine. Making the two kinds of notches, however, is quite different. The end grain notches take about twice as long to make because the wood is fighting you the entire time. You have to rip saw the walls of the notch then chisel out the waste like cutting out a huge dovetail. There is a lot of chopping vertically then splitting out the waste. It’s not a horrible task, but it’s much more difficult than creating a notch in the edge of the benchtop.
There you crosscut the walls (crosscutting is always easier than ripping). Then you split the waste out with a few chisel chops. Splitting wood along the grain is always easier than chopping across it.
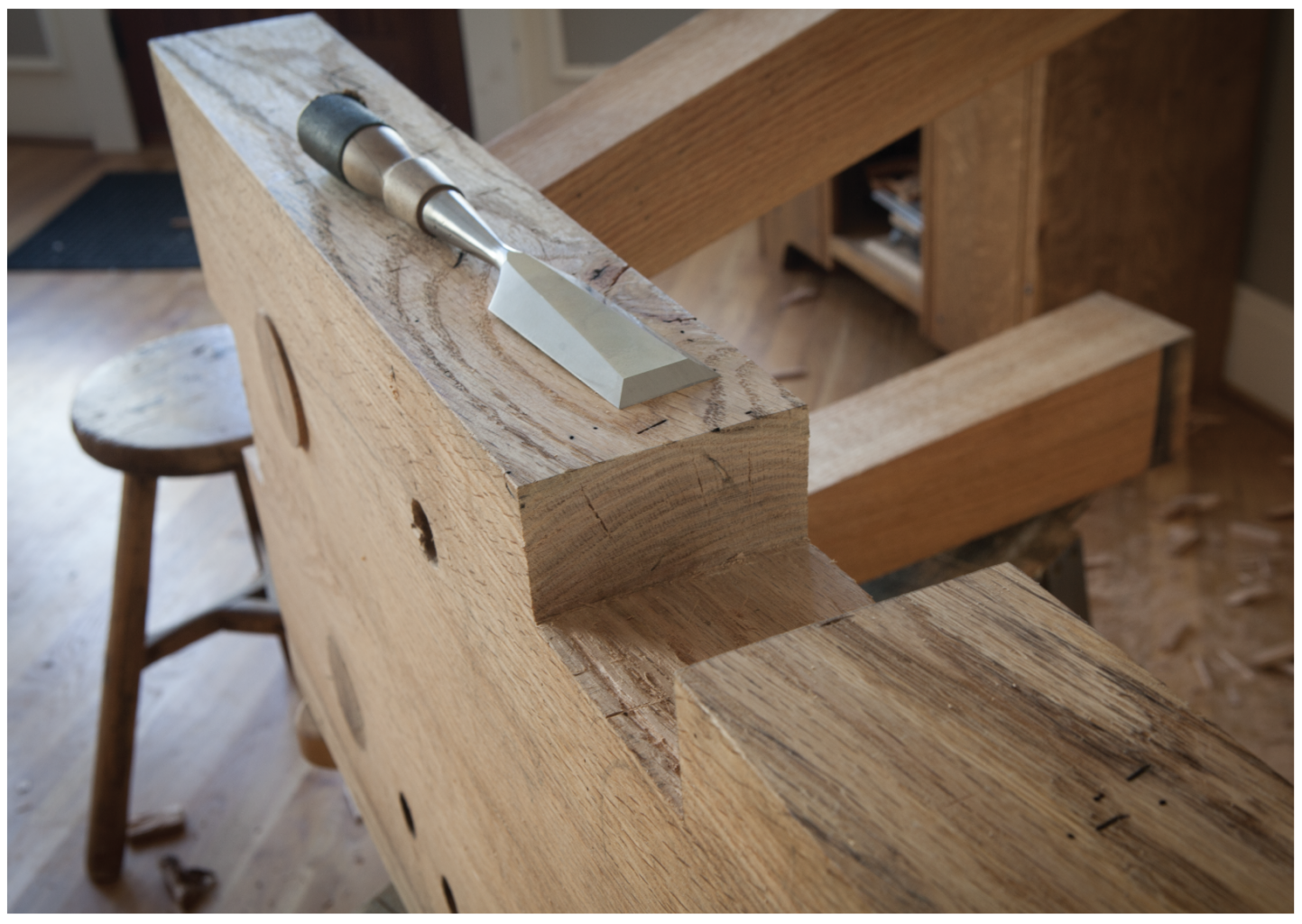
Here are the measurements for my notches. Don’t feel compelled to copy me, however. The end-grain notch is 4-1/2″ wide and 2-1/2″ long. The edge notch is 4-1/4″ long and 2″ wide. I have a variety of softwood wedges scattered about that can handle work from 1″ wide to 3″ wide.
One more nice use for the notch comes when cutting curves with a bowsaw or coping saw. Place your work over the notch while sawing and it will vibrate less.
Would someone mind explaining the 8/4 size notation to non US based people? “I recommend you make the hook big enough so that it can handle 8/4 stock.” I’ve come across it a bit recently and can’t quite fathom it. I can reasonably happily work in imperial as a second language but I don’t think we’re talking 8×4″ here are we?
2”. (It’s in 1/4” increments)
Wood is sold in the U.S. in different thicknesses called “quarters.” So 4/4 stock (four-quarter) is 1″ thick in the rough. And 8/4 stock (eight-quarter) is 2″ thick in the rough. Six-quarter (6/4) is 1-1/2″. And so on.
I still can’t wrap my head around buying a cubic meter of wood, so we’re all struggling.
Thanks, that makes a modicum of sense.
Working in cube is easiest thing ever once you are used to it and enables price to be quoted separate to size.
At least in those parts of Europe where I’ve bought wood in the rough, it is sold in the same thicknesses, only they’re expressed in the (rounded off) equivalent in millimetres; for example 4/4 is sold as 26 mm and 8/4 as 52 mm. I think I may have read somewhere (‘though I don’t remember where, and wouldn’t swear to it) that the US system has become if not a formal, then at least a de facto world standard for rough lumber measurements. In fact, the chap at my local lumberyard here in Belgium as happily speaks “quarters” as millimetres.
But yeah: I vividly recall first coming across the 8/4 notion in the Benchcrafted Classic bench construction notes, where they talk about the top being “[…] made from 8/4 lumber, flipped onto its edge and laminated […], how utterly confused I was, trying to envisage a piece of lumber eight something by four something making a good bench top laminate … and what a complete light bulb moment it was when the penny dropped!
But don’t talk to me about board feet. Those I don’t think I’ll ever suss.
Cheers,
Mattias
Board feet are similar in concept to selling lumber by the cubic meter (a concept that I have difficulty mentally translating into boards of the sort and size that one would actually use for building furniture, etc.; I always seem to think of it as this solid cube of about 40 inches X 40 inches X 40 inches…):
One board foot is 144 cubic inches.
The easiest way to envision it is to think of a board 1 foot (12 inches) long X 1 foot wide X 1 inch thick; do the arithmetic, and you have 144 cubic inches.
Another example: 2 board feet (288 cubic inches) = 24 inches long X 12 inches wide X 1 inch thick, OR 12 inches long X 12 inches wide X 2 inches thick.
I suspect that it is easiest to use the system that you are used to, and other systems are more difficult to use until you have that “light bulb” moment.
Some thoughts on the process of cutting out the end grain notches:
Why work so hard? Chop out the waste?
Here’s how I’ve done it….Do rip cuts for the sides of the notch. Then use a cross-cut saw, with cuts on the diagonal to remove the majority of the waste. Follow up with a bow saw with a thin blade. Takes much less time and effort.
Then clean up as desired with chisels.
If your saws are well tuned, little clean up should be necessary.
Interesting with the wedges. I made a small supply to carry with me for work and the sizes range 90 x 45 x 250-300 mm equating to about 9-10degrees. The ability for them to wedge does shift markedly the lower the angle but I also needed to ensure there was a small amount of durability built in too. Too thin or shallow an angle and they didn’t hold up for repeated use, or have a face big enough to belt with whatever was at hand. Never thought I would use them as much as I do .
One crochet-related question I haven’t seen addressed: I would expect the board’s arris against the crochet to be blunted. Does that not happen or is it just something you deal with?
Hi Chuck,
I can never recall it being a problem, even with my more wedge-shaped crochet. It’s definitely not a problem with Roubo’s version.
The photos of the notches as face vices are particularly inspiring. It is easy for me to imagine how the crochet works, but without those photos I’d never have grasped how well the notch could hold boards of that size. Impressive!
In the last photo, is that a 1-1/2″ Lie Nielsen chisel?
Not sure of the exact width. But yes, LN made these for a short time.
Whoa. I’ve never seen one over 1″
The most valuable thing one of my dearly departed friends left me is a box of wedges he’d made. He didn’t want to have to make them again so I’m set. Probably pass some of them down too. I always keep several in each of my toolboxes. Never can tell when you might need one. Or an opposing pair.
I suspect you mean lag screws, not carriage bolts, for attachment of the crochet. You would not use a ratchet (first photo) on the head of a carriage bolt, and you would need to install a nut on the other end.
While this has only marginal connection to the crochet, I would like to know why crucible hasn’t made or manufactured bench knives?
Because you can find them in every drawer?