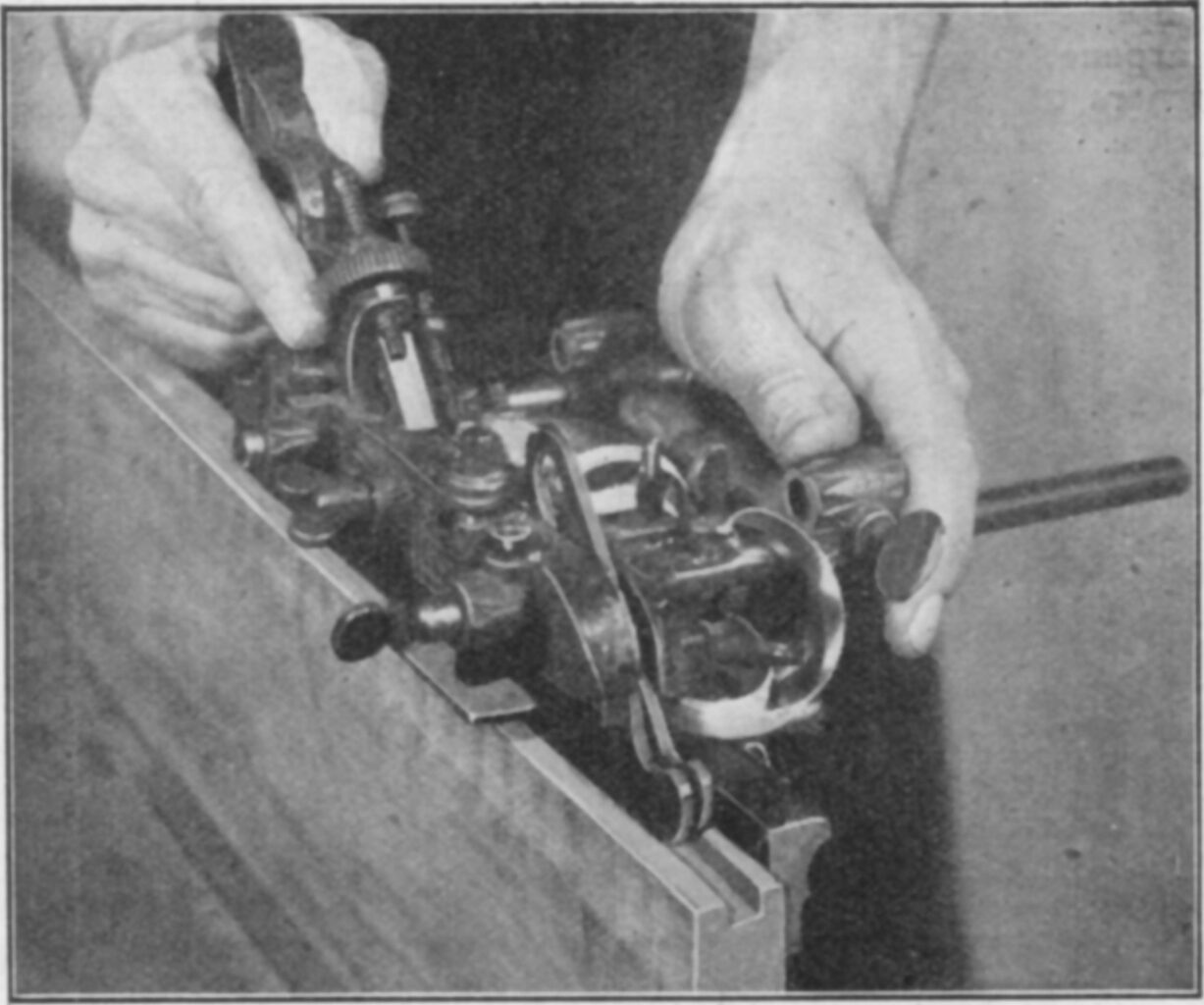
The following is excerpted from Volume III of “The Woodworker: The Charles H. Hayward Years.” First published in 1950, the book is beautifully illustrated by Hayward and contains the kind of spare prose that made him the best woodworking author of the 20th century. Like a good woodworking joint, Hayward’s text contains nothing superfluous and lacks nothing important to the task at hand.
This can be one of the simplest operations; it can also be one of the most awkward. To an extent it depends upon the tools available, but it is chiefly a matter of whether the groove has to be stopped, is straight or curved, the direction of the grain, and its position near to or away from the edge. We deal here with straightforward grooving, and shall follow next month with stopped grooves.
Perhaps the simplest examples of grooving are the parts of a door with grooved-in panels. It is merely a matter of setting the grooving plane to the required distance from the edge, adjusting the depth stop, and taking the plane right through. You can use either the wooden plough, or one of the special metal grooving planes. Let us consider first the setting of the plane, dealing first with the wooden plough.
Setting the Wood Plough. Select the cutter of the required width (there are generally eight), sharpen it square, and insert it so that the groove on its under-surface rests upon the metal edge of the sole piece (see Fig. 2). Set it so that the cutting edge has the required projection, and tap in the wedge. A fairly heavy shaving can be taken in softwood and when the grain is straight, but hardwoods and awkward grain require a fine cut.
Release the wedges holding the arms, and slide the fence until it is the required distance from the cutter. Press in one wedge thumb-tight, test with a rule to see that the fence is parallel with the metal sole, and push in the remaining wedge. Test once again to make sure, and tap home both wedges, tapping each lightly in turn. The depth gauge is generally controlled by a thumbscrew at the top, and this can be turned to give the groove depth.
Using the Plough. Start at the far end of the wood, and remove a shaving a few inches long. Then at each subsequent stroke bring the plough a little farther back as in Fig. 3. The advantage of this is that the tool is less likely to drift from the edge, since it runs into the groove it has already worked. Be careful always to press well against the side of the wood for the same reason, and work with the fence against the face side in every case. Otherwise, if the groove is not set to the exact centre, the parts will not go together flush.
It is essential that the plane is held upright, because, not only is the groove untrue otherwise, but there will be some curious results. At A, Fig. 4, the plough leans towards the user, and it is clear that the cutter will begin to operate at a different position from that intended. It will be nearer the face side. Then, as it sinks into the wood, it will either begin to bind and cease to cut, or the plough will be forced upright, when it will continue its groove in the wrong position. At B the groove will simply lean across at an angle.
Metal Plough. The setting of this depends upon the type. In the case of the small Record No. 040 and 043 planes the cutter is set in the stock about flush with the sole, and the lever cap screw lightly tightened. The cutter is then lightly tapped forward to give the required cut, and the screw finally tightened. Never strike the body of the plane to bring the cutter in; loosen the screw and withdraw it. The fence is slid on to the arm, tightened in the required position, and the depth gauge set.
In the case of the 050 A plane, a sliding section is provided to support the cutter at the near side, and it is the screwing up of this that clamps the cutter. When setting, therefore, the screw should be lightly turned only. This enables the final setting of the cutter to be made with the adjustment screw, after which the fixing screw is finally tightened. A small screw to the rear of the cutter is provided to help in keeping the sliding section parallel with the main stock. Fence and depth gauge are set as before.
The larger Record Multi-plane (405) and the Stanley 45 have their cutters tightened by means of a tapered bolt. The cutter is thus secured to the main stock only, independently of the sliding section. The latter is slid on afterwards so that it is level with the near edge of the cutter, or stands in a trifle. On no account let the cutter stand in from the sliding section, because this will cause binding. The fence has two sets of holes so that it can be fixed in a high or low position, whichever is the more convenient. A fine screw adjustment is provided on the depth gauge, and, after setting, the lock nut is tightened.
Setting for the Stanley Universal plane, No. 55, is similar, but, since the sliding section is adjustable in height, it is necessary to set this so that the cutter has the same projection on both sides. Slacken the lock nuts before turning the adjusting screw. Another point about this plane is that, since the fence can be set at an angle, it is important to see that it is upright before setting the plane for normal square grooving. Fig. 1 shows the Universal plane in use.
Some metal ploughs are provided with spurs which fit in recesses in the sides of both the main stock and sliding section. Their purpose is to cut the sides of the groove when working across the grain. They are unnecessary when grooving with the grain, and should be set in the neutral position. When they are in use, the plane should be drawn backwards for a couple of strokes to make sure that the groove sides are cut. Otherwise the grain is liable to tear out.
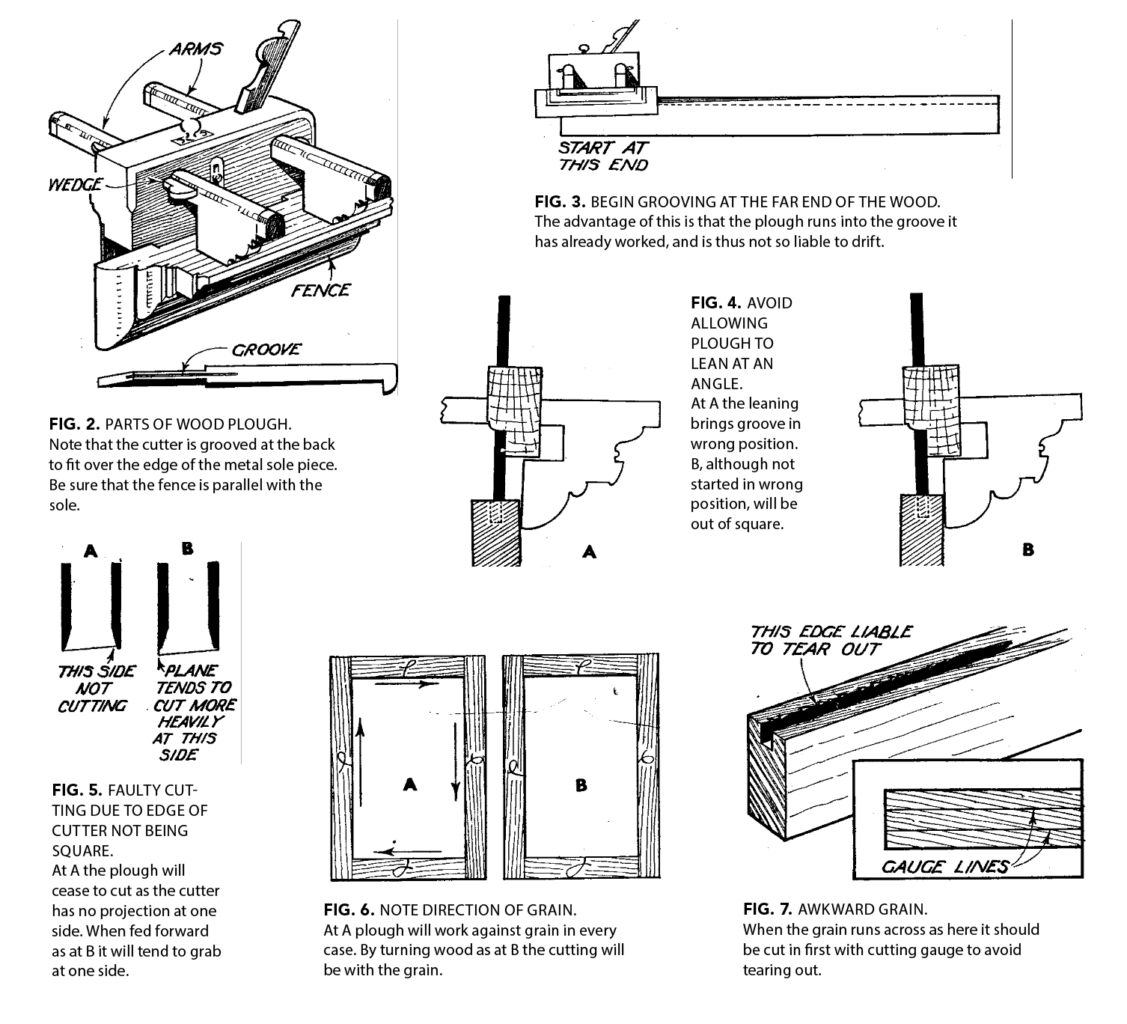
Using the Metal Plough. The use of the metal plough is similar to that of the wood type, but lubrication is more essential. A pad of cotton wool soaked in linseed oil is handy, or a wax candle can be drawn along the bearing parts.
As a guide to holding the plane square it is a help to press the fence against the side of the wood with the left hand as a preliminary step. You can soon tell when it is bearing on the wood, and this is the best guide as to when the plane is upright. You will soon get the feel of it. For a start, try the plane on a spare piece of wood, and examine the end of the latter as you progress to see whether your work is at all out.
Clearly, the cutter must be sharpened perfectly square. This is partly because the bottom of the groove will otherwise be out of truth, but chiefly because a cutting edge which is not square may cause bad cutting or may make the plane fail to cut altogether. Take A, Fig. 5. At the main stock (left) the cutter has the required projection, but at the sliding section it has none at all. This will prevent the plane from cutting, and, to make it cut, the cutter will have to be set forward as at B. The result of this is to make the plane tend to grab at the side having the greater projection, and this will probably throw the groove out of truth.
When the grain is straight and parallel with the wood the shavings curl away sweetly and the work is clean. A difficulty occurs when the grain either runs at an angle or is curly. Consider Fig. 6, which shows a door frame. Since the plough has always to be worked from the face side to ensure the grooves being level throughout, it will work in the direction of the arrows shown at A, and will be working against the grain owing to the slope of the latter. By reversing the parts as at B before marking out, the plough can be made to work with the grain in every case.
In Fig. 7 the grain runs across the edge at a decided angle, and the probable result would be that the groove would tear out at one edge as shown. To overcome this the groove position should be cut in first with the cutting gauge as shown inset. This will ensure the surface being clean. If it tears out down below it will not matter.
Many metal grooving planes are fitted with small spurs or cutters, the purpose of which is to cut the fibres when working across the grain. If not used the grain would be liable to tear out. They are not needed when working with the grain and they should be reversed into the neutral position. Small set screws hold them in position. One will be found on the main stock at the off side, and the other on the sliding section at the near side. Both are just in front of the cutter.
The fences of my 70’s vintage 405 would too often slip so plane was little used. A machinist suggested I replace the difficult to tighten knurled bolts with set screws. Genius!
“We deal here with straightforward grooving, and shall follow next month with stopped grooves.” Will you be providing the follow-up?
Probably not – it’s excerpted from one of our books, and we excerpt from a diff book every week.
Can someone explain what is the meaning of ‘stand in’ in the context of the following sentence? “The cutter is thus secured to the main stock only, independently of the sliding section. The latter is slid on afterwards so that it is level with the near edge of the cutter, or stands in a trifle. On no account let the cutter stand in from the sliding section, because this will cause binding.” I re-read it many times and am now more confused than ever.
The cutter on the 45 is supported by the main part and the sliding section. I think he’s just saying don’t set the two parts apart wider than the cutter itself. I can attest that even if you think you’ve set them at the same width as the cutter, it can still get pretty sticky in a deep groove.