
This six-stick comb-back chair is inspired by two Welsh chairs – one that I inspected at Tim Bowen Antiques and a second chair that I have in my collection. The chair is built using 4,000-year-old bog oak that was harvested in Poland. All the parts of this chair came from one tree.
I am selling this chair for $1,500 via a random drawing. Details on purchasing the chair can be found near the bottom of this blog entry. Here are some more details about its design and construction.
This stick chair is a new design – a definite break from my previous chairs. It features new shapes for the seat, arm, hands and comb. The rake and splay of the legs are new numbers. But in the end, it is still just a stick chair, a humble and vernacular form found in many cultures.
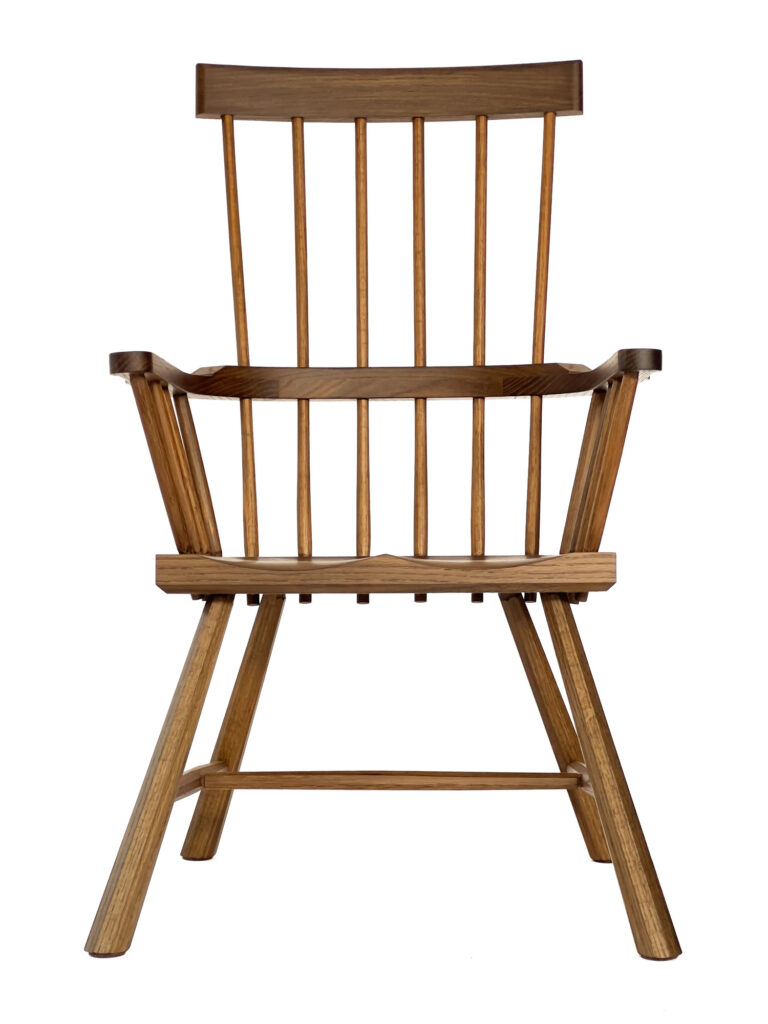
This particular chair is set up for working or dining. The back is fairly upright at 11° off the seat. And the seat tilts at 4°, giving the chair an overall tilt of 15°. The seat is 16-1/2” off the floor to accommodate both short and tall sitters, and the chair is 40-1/2” high overall. So it has a nice presence in a room.
One of the goals with this chair was to make it a bit more roomy. There is 20” between the arms, and the arm shape is square-ish to accommodate stocky sitters.
The bog oak used in this chair is a gorgeous nutty brown, with hints of green and orange in it. All of the chair’s major joints are assembled using hide glue, so repairs in the (far) future will be easy. The chair is finished with a non-toxic soft wax, a blend of beeswax and raw linseed oil that my daughter cooks up here in our shop. The wax is an ideal chair finish. It is not terribly durable, but it is easily renewed or repaired.
Among the unusual design details of this chair are the through-tenons in the seat. The chair’s sticks were left long and protrude out the bottom of the seat. This feature is more common on Irish chairs, but I like the look, and it gives a sitter something to explore down there.
I consider this chair a prototype, and it is not perfect. On one of the arms there is a small bit of tear-out (3/16” square) that I filled with tinted epoxy. There are also tell-tale signs of handwork everywhere on this chair. You will find faint rasp marks on the arms. Scallops from the jack plane on the underside of the seat. Facets from a spokeshave on the comb.
I prefer these subtle marks to a homogenous sanded surface. Though some people would call them flaws.
How to Purchase This Chair
This chair is being sold via a random drawing. The chair is $1,500 plus domestic shipping. (I’m sorry but the chair cannot be shipped outside the U.S.) If you wish to buy the chair, send an email to lapdrawing@lostartpress.com before 3 p.m. (Eastern) on Wednesday, July 13. In the email please use the subject line “Chair Sale” and include your:
- First name and last name
- U.S. shipping address
- Daytime phone number (this is for the trucking quote only)
After all the emails have arrived on July 13, we will pick a winner that evening via a random drawing.
If you are the “winner,” the chair can be picked up at our storefront for free. Or we can ship it to you via common carrier. The crate is included in the price of the chair. Shipping a chair usually costs about $250 to $300, depending on your location.
— Christopher Schwarz
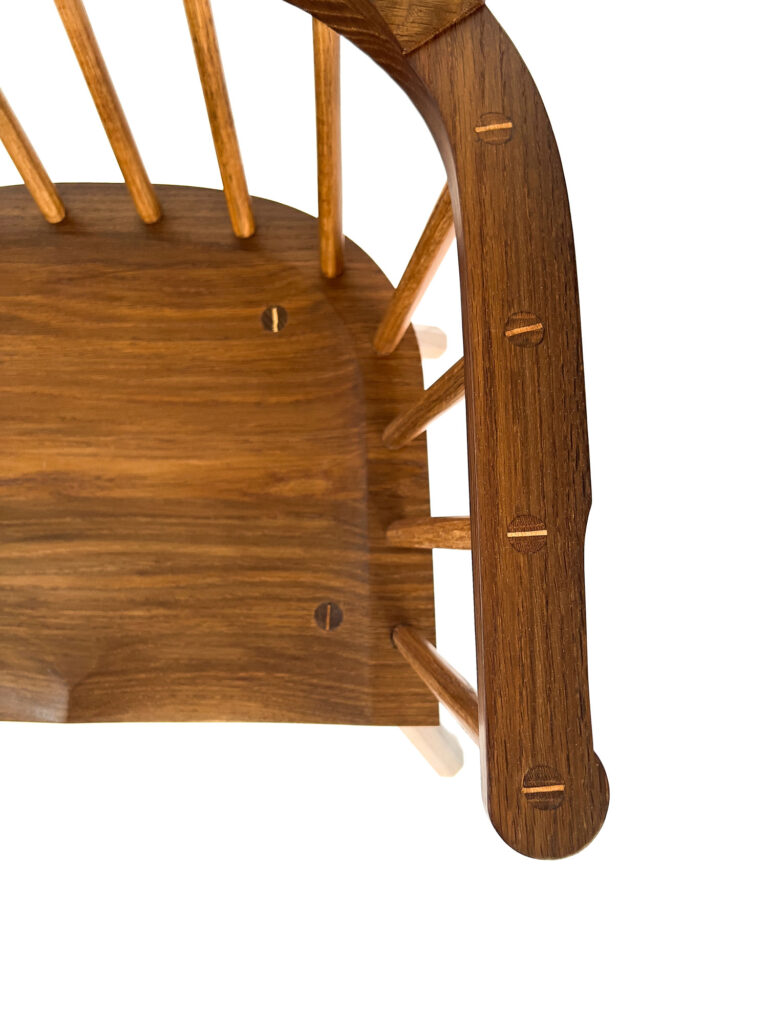
Very , very nice , and at that price…..too bad shipping fees to France would be twice the price of the chair otherwise i would have tried to buy it… I would like to ask you what is the tenon/stick diameter for that chair please (i’m in a hugh 5/8 vs 3/4 dilema). Thank you and have a nice day.
These sticks start out at 3/4″. The tenons are 5/8″ and all the sticks taper down to the 5/8″.
Either works! Chris Williams uses 3/4″. I like them a little smaller.
Too many things made out of wood these days are 3/4. That makes 3/4 jump out at me, any place I see it. To my eye, it’s either too thick or too thin. Case pieces, shelves, etc should be thicker. Spindles ought to be thinner.
As the years go on, I make more things slimmer than I used to. Drawer sides are a lot thinner, as one example.
That’s just how my eye sees things.
Looks fantastic! The transition between the arm and the hand is a nice design element, and the protruding sticks, love it.
Thanks Pascal! Much appreciated.
Those protruding sticks under the seat make the chair look like it was urgently needed to be put into permanent use before it was quite entirely completed. I LOVE that!
Absolutely incredible– I can’t stop staring at these photos.
Material cost of that much bog oak must be more than the cost of the chair, no? It’s super rare stuff!
i like the proud through tenons too. does leaving them proud save work or is it more like proud pins/tails that doubles the work and makes cleanup after the fact impossible.
More work. Looks cool.
I like the changes and the lesser angle of the back (which is more comfortable for me). I am not a large person but I also like the dimensions. It increases my interest in building a stick chair.
Thanks Chris. You give some dimensions and label it as a good dining chair or work chair with a slightly wider seat. I’ve also seen other chairs with specific angles and you’ve mentioned them as good relaxing chairs. Is there some consolidated location for all this info such as The Stick Chair Book by you so that when I get around to making chairs, I have a good idea what to use for the intended use of the chair? Also, are those various angles, etc good guidelines for other chairs such as Curtis B’s democratic chair?
Hi Joe,
I use backrest angles from 10° to 25°. But the angle of the back isn’t the only thing. You also have to take into account where the back hits the sitter. I make lowback chairs with a 25° lean. But because of the low position of the backrest, it’s a chair for dining or working.
While I am sure there are guidelines published out there, the best way to learn is to go to a furniture store and sit in a bunch of chairs. When you find one that is comfortable (or terrible) try to figure out why. Take photos of the chair so you can determine the angles of the back.
I hope this is some help. Wish I had some iron-clad guidance to give.
In your lecture a couple months back, you mentioned John Brown’s 1-3 finger approach. That was helpful. especially the bit about avoiding 3 fingers unless the chair is meant for the rapid growth of one’s liquid grain storage bin.
Thanks Chris. Easy enough to do.
Prototype shmototype, that is one nice chair.
This nice chair makes me wonder: are there any other lumber species that are preserved in bogs? I only ever hear of bog oak.
I have heard of bog yew from the Isles. I have heard of bog cypress here in the States as well. I assume bog tamarack is a thing as well. It is a northern relative of the cypress. I have never seen these in bog harvested form. I pulled some floorboards out of a barn that I believe are tamarack and they form the outer wall of my Dutch tool chest. Not from a bog but I took them form under a pile of debris and they were sopping wet but when dried out the became once again solid and straight boards to be put to various uses.
In Louisiana we always called it “sinker cypress,” but the idea is the same…
I purchased a large 2.5” thick slab of redwood from California 8 years ago that had been the base (including the roots) of a tree that had been in a forest fire sometime in the past 200 years and had been underground in a boggy location since. Whether that qualifies as ‘bog wood’ I don’t know; certainly not having been underwater for millennia, but the tree itself would be many centuries old. I got it because of its coloration: deep purple, grey and lavender tones with contorted grain.
I had completed a ribbon-grained maple electric guitar body with solid rosewood neck and details I had had on hand for nearly 30 years. I designed and made it for my professional musician brother and it turned out to have the best feel and sound that he and his friends had experienced, and they are all of them guitar collectors. Having never made an instrument, we had any no reason to expect that level of success, but I put it down to their expert advice.
So I laid out another guitar body using the redwood, going as far as cutting it out on my bandsaw (a somewhat steampunk design with the idea of using polished bronze for all the metal), but other projects have taken precedence and it has gone no further at present.
That is amazing. I should like to see a picture of that piece of redwood and the guitars that came from it too.
Very nice chair here, Chris. Good work. I love the subtle curves of the sticks as they go into the head rest. The color is great.