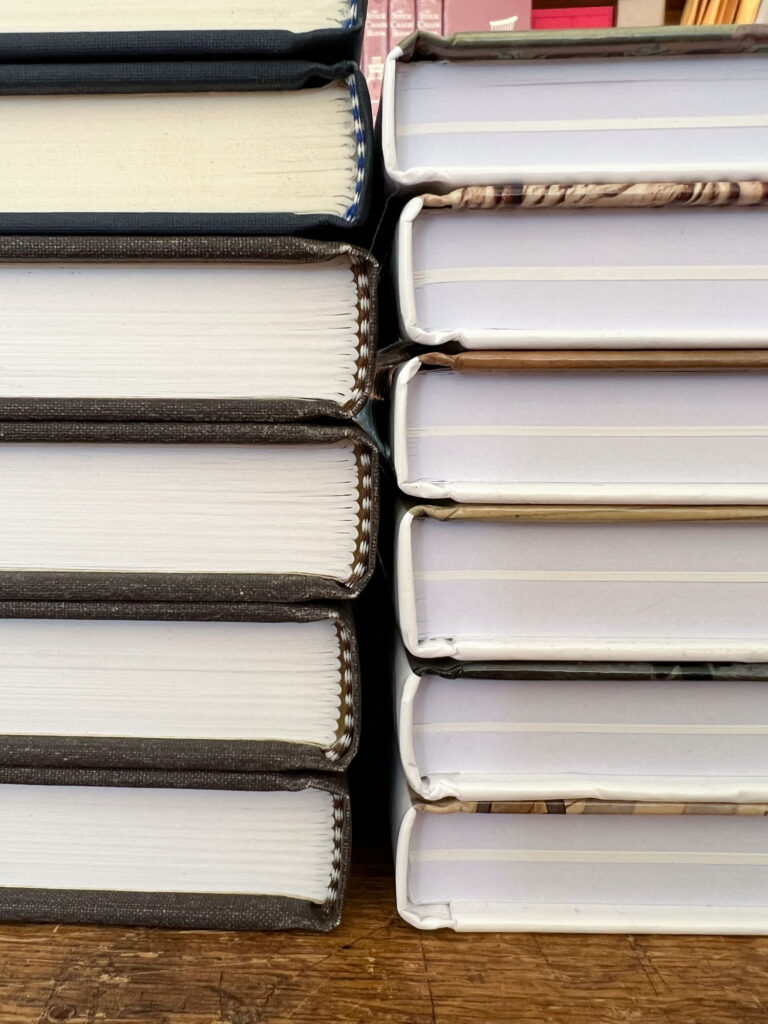
This week I’ve been reading a newly published set of six history books. And unfortunately, I should read them as quickly as possible because these books are designed from the get-go to fall apart in short order.
As a consumer this is maddening. The set cost me $550 (or $91.66 per volume). And after inspecting the books, I feel certain the publisher is likely greedy and thinks we are ignorant. Let’s take a look.
The new set of books are on the right. Some traditional books are on the left. If you look closely, you’ll see the difference. The books on the right are “perfect bound.” What does that mean? Basically, the printer took a bunch of single sheets and applied glue to one edge. It’s how cheap paperbacks and other impermanent publications, such as magazines, are made. And perfect binding – once unthinkable for expensive books – is now common.
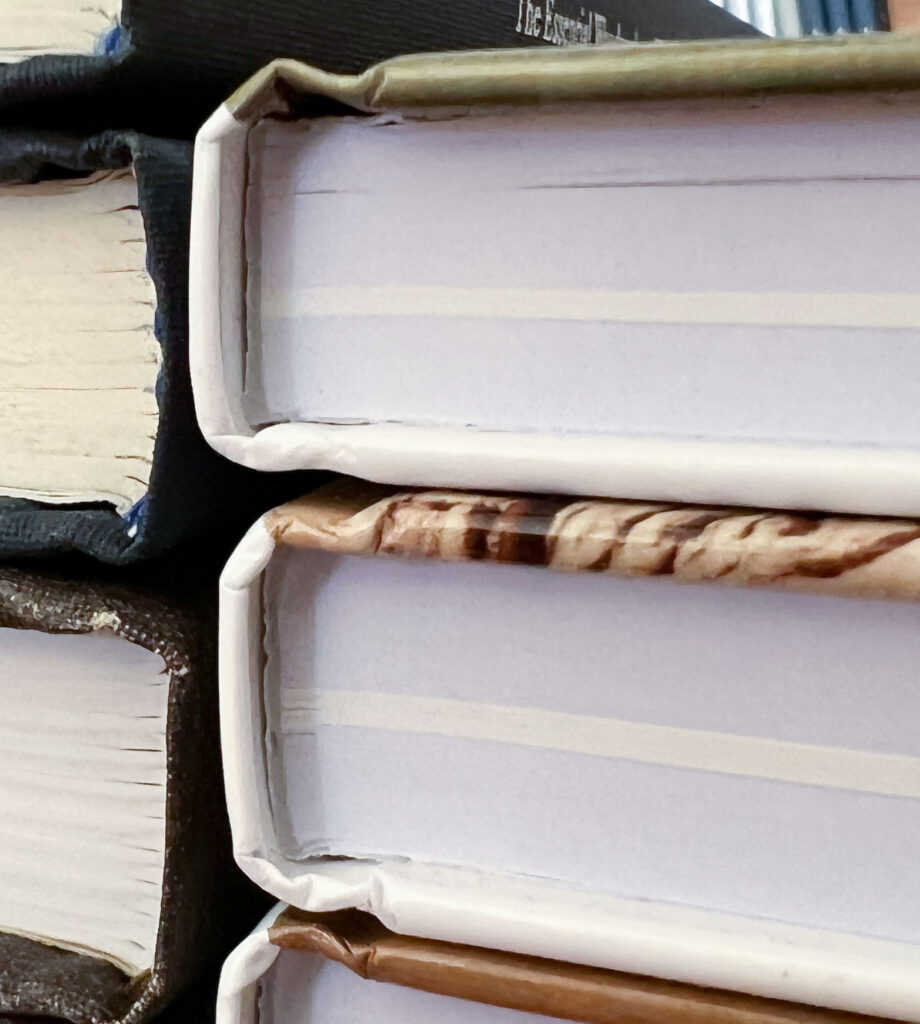
The glue will get brittle. And if you stress the binding to, say, try to make the pages lie flat, then the pages will start to fall out, one by one.
On the left is how Lost Art Press and some other publishers make books. The book starts as large sheets of paper that are folded into “signatures” – basically self-contained booklets comprising eight, 16 or 32 pages. Then we stack these signatures in order and sew them together with thread (a process called Smyth sewing). Then we apply glue to the edges of the signatures plus a fiber-backed tape to add durability and flexibility to the book.
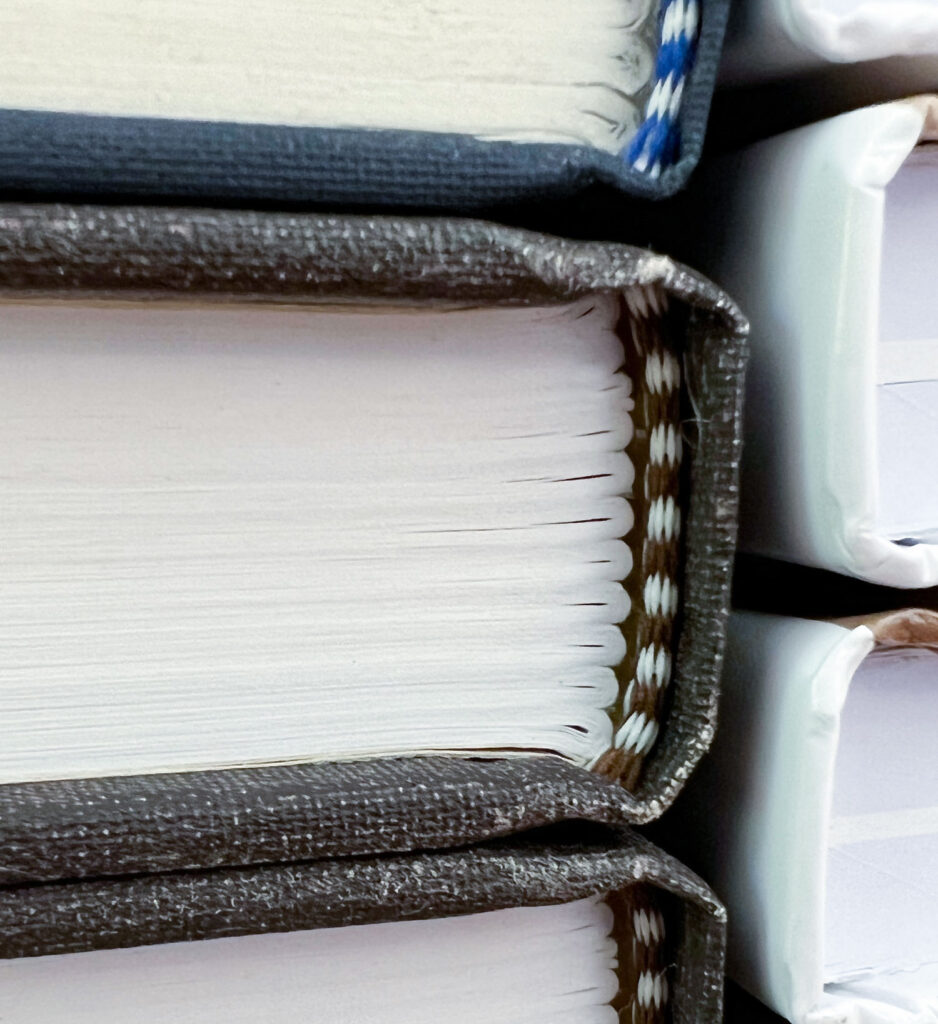
Books made this way are designed to last many decades and suffer abuse.
So I know there are some people out there who are saying: Perhaps the publisher of the perfect-bound books couldn’t afford to use an expensive binding. How can we know what the book cost to make?
Well after 32 years in this business and quoting hundreds and hundreds of jobs, I can guess.
Based on the paper weight and page count, I estimate these books cost about $7 apiece to manufacture – so $42 total for the set. If they had switched to a traditional sewn binding, my best guess is that the books would cost $10 to $14 each to make (the paper is quite thin). So $60 to $84 to manufacture the set, max (and I’m being generous).
So no matter what the publisher is paying the authors (likely 10 percent to 15 percent of gross), the publisher is basically printing money. For itself.
I know this might sound like a “holier than thou” blog entry. But – particularly when the content is worth preserving for future generations – I have no patience for cheap, fall-apart books. And I hope that perhaps this blog entry will help you spot these ornery critters in the wild.
— Christopher Schwarz
Make Your Own ‘Signatures’
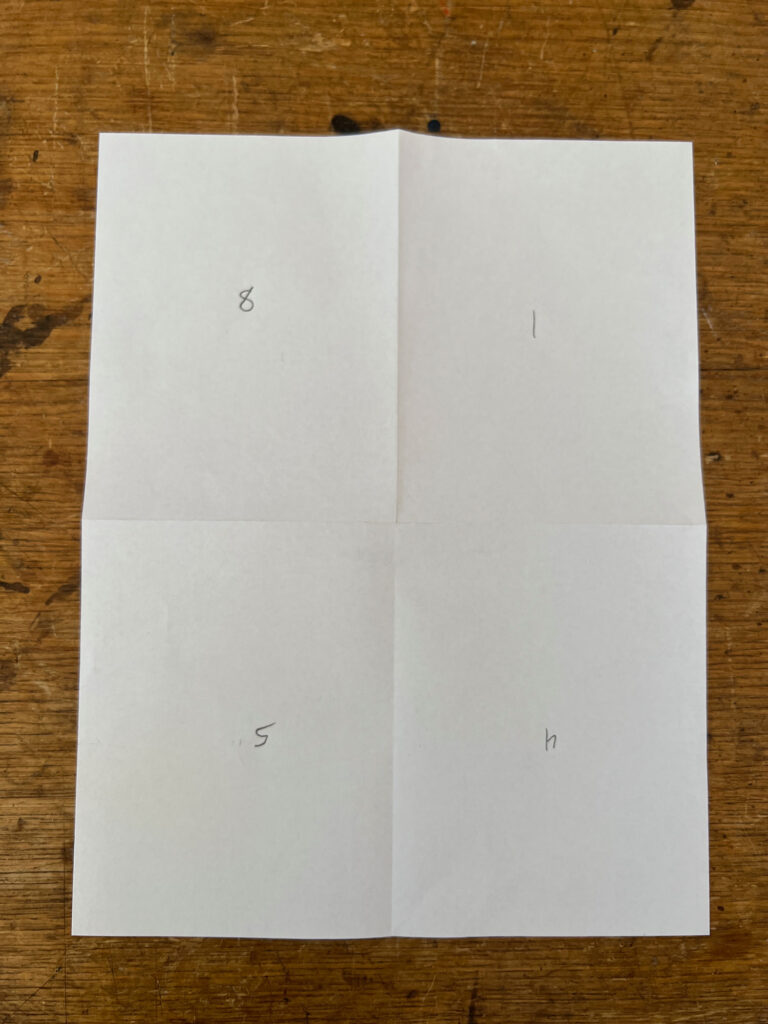
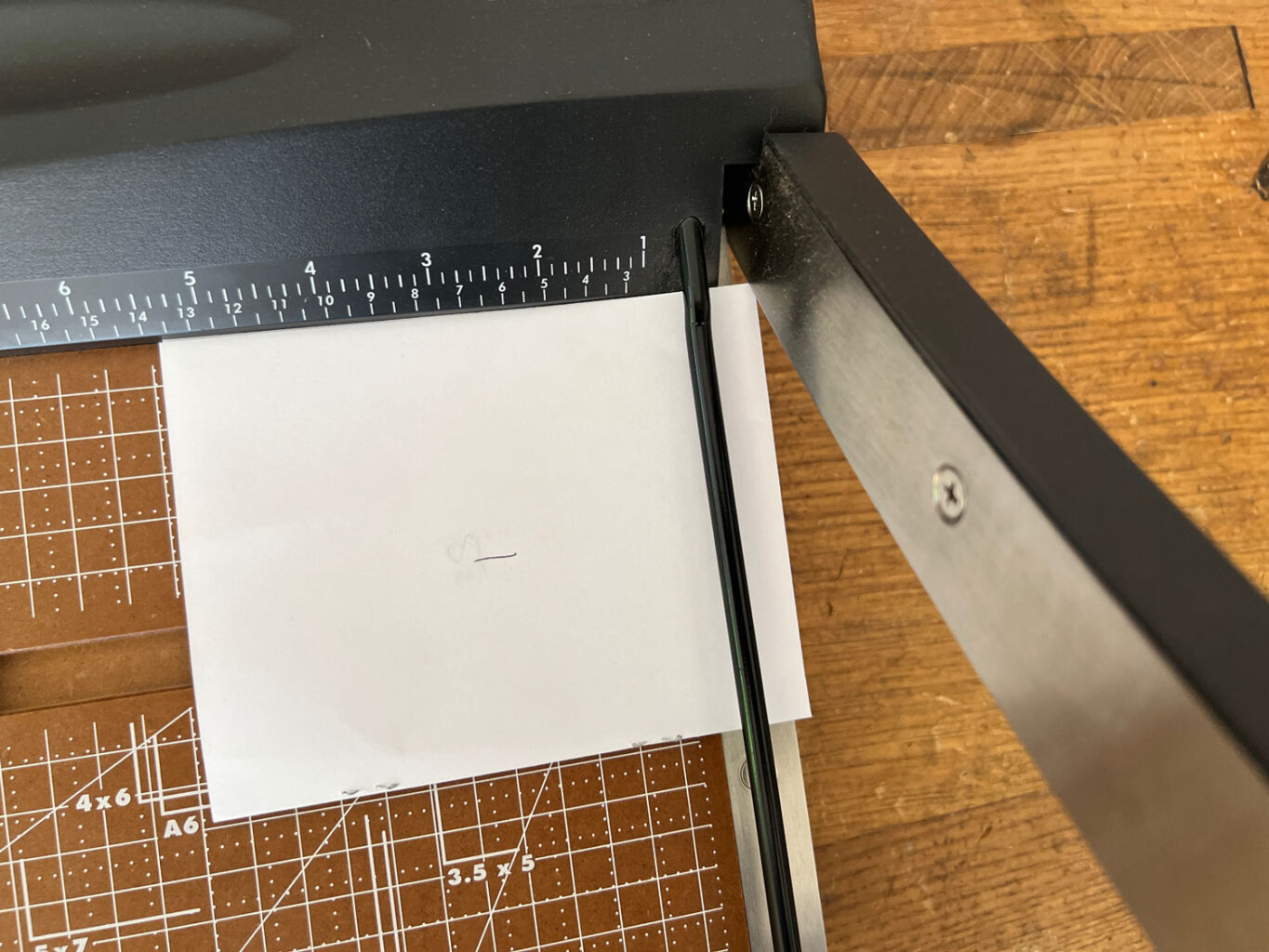
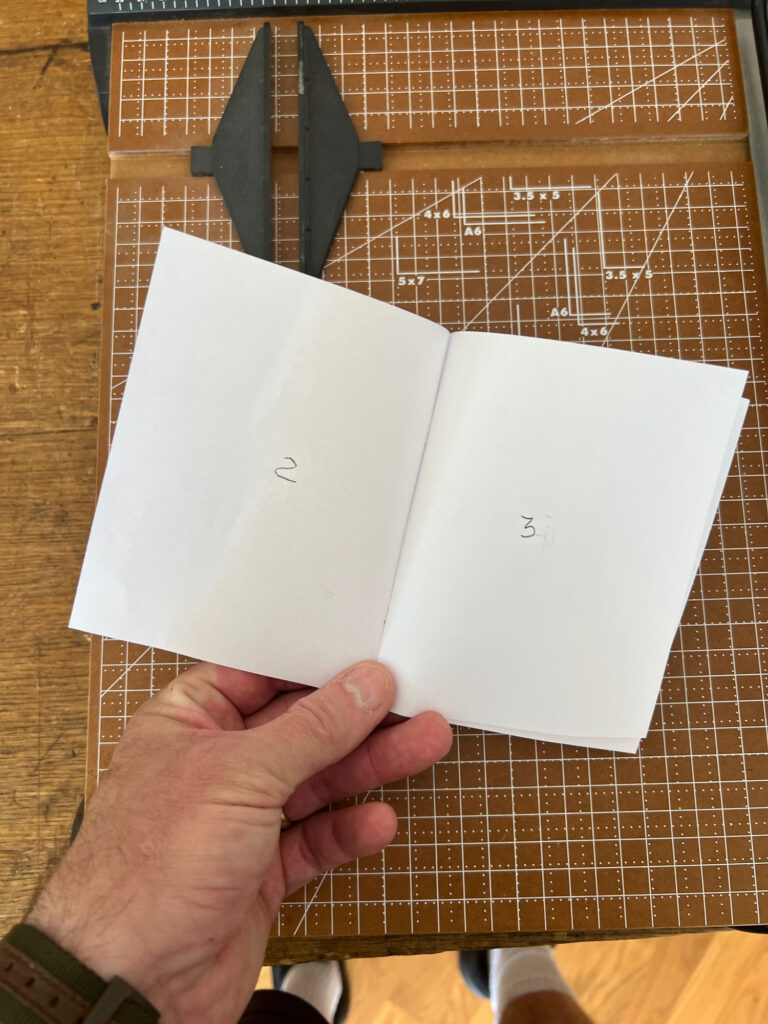
I agree completely! Well constructed books last, just like well constructed furniture or buildings.
What is the brown and white (blue and white in the top two) piece in the Smyth sewn signatures?
Those are called “headbands.” Many people think they indicate the book is sewn, but that’s not the case. They are merely applied rolls of thread that are glued to the tops and bottoms of the book block. They look nice. And they protect the spine of the book block from damage.
‘Capitals’ used to be functional – weaving the ends of the threads used to bind the signatures with coloured string to add to the overall quality of a book. Sadly this has been ‘substituted’ by glueing on a poor substitute.
Digial printing used in Printing on Demand may be part of the issue here. Sheets not signatures without all the extra work signatures entail. I also remember a local book printer showing me tests of the adhesive binding we were using for an offset printed museum catalogue. It is pretty good, much better than the “glue” used in the cheap paperbacks we grew up with. I have some blank dummys that I use as notebooks and have had no failures over the years. That said, a Smythe sewn book is a lovely and durable object.
The glue today is indeed better than the glue from the 20th century. But it’s like furniture. If your piece relies entirely on glue – instead of a mechanical interlock – then what do you have, really?
Print on Demand (POD) has absolutely accelerated this trend – I agree. But the real crime is that sewn signatures are not that much more expensive than perfect binding.
And this is absolutely the hill I choose to die on…..
My wife is a librarian and many years ago while in graduate school, she took a class on the history of the book. The professor had a gathering at his house for students and their significant others to do some printing on his antique press and also do some paper marbling. For those of us that were not his students, he went through the parts of a book and what makes a well crafted book. The example he showed, was in his words a terrible piece of literature, the equivalent of a modern dime store romance novel that he would never actually read. But the book itself was exceptionally well crafted. He pointed out the marbled paper on the pastedown and endpaper, the craftsmanship of the raised bands on the leather spine, and importance of the stitching on the signatures. He lamented that for a couple bucks of savings, printers and publishers today would rather roll out books that are little better than magazines with stiff covers. His book collection harkened back to a time when the physical printing and construction of a book was perhaps even more important than the content on the pages. I expected the evening to be dull, hanging out with budding librarians, but I walked away with an deeper appreciation for books that still sticks with me some 20 years later. If this professor is still with us, he would surely join you on that hill.
True! Books from the early age of printing are still around. And books produced in the Industrial Age are most prone to need conservation because their basic compounds are deteriorating at an alarming rate, eg paper disease and their binding failing. Not to mention what has been produced the last decades – read it once and it will fall apart.
As a “life long” printer, having been at this for over 40 years, I can wholeheartedly agree and add that it’s not just in the bindings but in the quality of the print as well. While POD and digital presses may be here to stay, that is still no excuse for shoddy workmanship. As in the actual printing process, be it offset lithography or letterpress, the number of qualified or even interested people to carry on this craft is aging and dwindling. While almost anyone can perform the perficbound process, it takes real skill to actually sew signatures and bind a long lasting book.
As a woodworker—and, more importantly in this case—a lover of books, I found this valuably enlightening. So fortunate to be an owner of many Lost Art Press volumes.
A Cultural History of Furniture?
Very interesting. Thanks.
Thank you for sticking with quality construction for your books. I have also spent way too much for books with junk binding and it infuriates me every time. I expect that when I am buying a book in the range of $20. But there is no excuse when I am spending upwards of $60 – $100. Those are not supposed to be disposable. Especially when they are niche topics and quickly become hard to find. I know a couple of publishers who are notorious for this.
I used to be an outreach librarian and regularly took books to several corrections facilities. I had no budget for materials, so I used library discards. Having so many books with perfect bindings made my life easier because newer books would start falling apart and be discarded when the pages were still quite readable. The covers were often just held on with the endpapers, so a little tape and/or flexible adhesive and I had a fairly nice book for the inmates that was probably stronger than when it was new.
So there is one situation where the non-durable “perfect” binding is advantageous.
Seems like a perfect solution to the problem, thank you for your service!
Your attention to detail and quality is what makes you and your company a “cut above”. I look forward to all the new books and other good stuff from Lost Art Press.
One of my favorite books is the Encyclopedia of Shaker Furniture. I couldn’t guess how many times I’ve gone through it. Huge book, fantastic pictures, great insight. I can’t recommend it enough. The author did a fantastic job. The publisher did not.
But it has a complete crap glued binding, as noted above. It also cost over a hundred bucks. I would very happily, eagerly, paid another 20 for a lifetime binding.
I have that book as well and have the same feelings. If they had spent another $5 on manufacturing, the book would be sewn signatures. It’s really not that expensive.
But greed is strong.
So, you estimate an extra 3-7 dollars for better binding on each of the above books. Any estimate on better paper? Just curious.
Paper is the biggest expense. And “better” isn’t always thicker. It can be whiter. It can be the coating.
Paper is like wood selection. Finding the right material for the design. Some publishers use ridiculous paper for books that is awkward. Like making a workbench out of solid ebony.
Personally I prefer to read books on, what I assume, is very cheap paper. I like it absolutely flat and with no glare from overhead lights – more like newspaper than anything in a “nice” book.
Newsprint is what we call “groundwood” (it’s not an insult). Used mostly in airport paperbacks.
Readability is a big issue for us. We use uncoated paper when possible because there is zero glare and text doesn’t fatigue your eyes. But printing photos with adequate clarity and contrast is challenging or impossible.
So for photo-based books, we use a coated paper that is matte. Expensive. But it’s fairly readable and the photos reproduce very well.
My goal is to go to uncoated paper for everything. But that’s a technical battle that I am still working on. You can see where we are in the process with “The Stick Chair Book,” which is printed on uncoated stock. It’s not perfect. But it’s not bad…..
There are some established workarounds for having excellent picture quality on uncoated papers — but, as always, there is added cost. And AFAIK cost times six is what one pays in the bookstore.
I own this same book and encountered the same issue. Like wrapping a diamond in a greasy newspaper the valuable content might be missed because the wrapper is garbage.
Sadly, the quality of a book’s construction is not generally described in reviews.
Actually I have seen several reviews of several books like this on Amazon with pictures of it falling apart. Especially classics that are public domain.
You can’t fake quality and craftsmanship!
My mom was a librarian for a local grammar school, I would go with her to buy books during the summer.
It was a binding house in Massachusetts I believe and they did an excellent job binding books.
I have a set of the Lord of the Rings given to me in 1976, I have read the book 4 times and my kids have read the books as well. They are still in great shape. I have read books that fell apart and now I know a lot more about book construction and what to look for when buying used or new books. Perhaps you can judge a book by its cover!
Thank you. This gives me a much better perspective on the importance of quality.
The original copy of Country Woodcraft my father purchased in the early 80’s is now a collection of hundreds of loose sheets that fortunately are still in numerical order, as if the glue completely evaporated.
Extreme care must be used to take it out of the bookshelf for consultation…
I never heard the term “perfect binding” but it is not an accurate name for this at all. I am glad the LAP copies can be safely taken to markets, demonstrations, lent to friends, brought in the workshop and only show minimal wear..
I’ve read that those flat, letter opener-like paddles called “page turners” by antiques sellers/collectors were actually for cutting open any parts of signatures that weren’t reached in the trimming process.
Many newspapers and periodicals until the 20th century were sold “uncut”, printed and sold as folded signatures. For that reason there’s a premium to be paid for vintage “uncut” periodicals. Reading these was sometimes described as “cutting” them, because that’s what you had to do to turn the pages!
Victorian books were sold uncut too. You had to go through each page with a paper cutter.
Sorry, I see someone said that. Anyway, Victorian books were often sold unbound, with a wrapper that had the title on it. In novels and plays, sometimes referred to as “books in yellow paper covers/wrappers.” You could have the book bound to match the others in your personal library. Or, if it was something ephemeral like a novel (instead of a nice, morally improving collection of sermons, or the like), pass the unbound book around among your friends to read, till it fell apart.
Joe Martin, Republican Speaker of the House in the early 1950s, had a copy of Aristotles Politics on his desk for all to see. The pages were all uncut. Maybe he read half the pages?
Thank you for the education! I knew some paperbacks fell apart quickly but had not idea that a “Hardback” could suffer the same fate. I equated the fact of being hardback with higher quality but know better now. As a woodworker, I appreciate better made products and will look for Smyth sewing in the future, like I look for quality joinery in furniture.
Sadly now we have become a throw away society ,manufactures have become so intent on the bottom dollar that if it looks good and we can cut the manufacturing costs send it out. using the cheapest materials and the cheapest cost to manufacture ,companies don’t care about the customers .ever try to talk to their customer service .
For all those history and book nerds here is an interesting story of Jefferson and the signatures in his books.
https://www.monticello.org/site/research-and-collections/jeffersons-bookmarks
Apart from the fact that sewn signatures are much stronger and longer-lasting to start with, they are also eminently repairable, should a book really have suffered along the way! As long as the signature folds are still strong, you can easily take the book apart and re-sew them together; should the folds be very worn, they can be reinforced with Japan paper or similar before re-sewing.
Back in the day, one of my brothers was a journeyman bookbinder, and taught me a fair bit about how books are bound, including how to sew the signatures myself – it is not very difficult!
Oh, and even further back in the day (almost, but not quite, before my time) books were often sold in two versions: one more expensive, fully sewn, properly taped and glued, with hard covers, maybe a dust jacket, and cut signature edges (in Swedish sometimes called förlagsband ≈ publisher’s binding, as it was bound to the publishers specifications and all copies were the same); and one rather less expensive, just stitched together, with the signature edges left uncut and only a thick paper cover, lightly glued to the back of the stitched signatures. The idea of the latter version was that the customer would then take it to their bookbinder to have it bound to their tastes (thereby creating a privatband ≈ private binding), including cutting off the signature edges. Of course that often never happened, and instead the owner would use a letter opener or a knife (or even their finger!) to more or less carefully slit open the signatures and read the book, which would quickly deteriorate (but still remained reparable, at least as long as the signatures had been slit open with sufficient care that no text was missing.
Not that I’m expecting LAP to start doing that, though; that would, I think, be taking things a smidgen or three too far …
By the way, Chris, would I be right in thinking that, to add further insult to injury, many perfect bound books actually start out as signatures anyway, i.e. that they are printed on larger sheets which are then folded, same as with sewn books, and that only then are all four edges cut off the bundle of signatures to prepare it for its glue bath?! At least it wouldn’t surprise me if ’twere so, as I suppose that would be a more efficient and economical way to actually print the stuff than printing each single pair of pages separately …
Cheers,
Mattias
On perfect binding: It depends on the press being used.
If it’s a sheet-fed offset press, then yes, they fold them, assemble them and cut off the good parts.
If it’s a digital press (which is becoming very common these days), then no. It’s basically a photocopier with a hot-melt glue gun at the end….
Ah, yes. Digital presses. Hadn’t thought of those. Thanks for making that clear! Well, much as I (usually; I dare say there are cases where it makes sense) dislike the result of perfect binding, at least with a digital press they don’t actually produce the good parts only to immediately remove them. Cold comfort, but still.
Cheers,
Mattias
Sadly, buying online is the only option in a lot of cases so it’s next to impossible to spot these cheap books before we buy. Thanks LAP for making high quality books.
So would you say these are BOUND to fail?
ouch
binding us to your PUNishment i see.
The pun police should really throw the book at us.
thanks for sharing Chris. after buying my first LAP books i immediately noticed the difference in quality. it was night and day. though, i couldn’t begin to tell you why. if it were me buying a$500 set like that, I’d write a nasty letter to the publisher and reviews and demand a refund. I’m amazed you did not mention the title or publisher in your post.
I recently found this guy who is an amateur bookbinder (amateur in the true meaning of it)
here is a way to convert a paperback to something better ( or to save a book falling apart):
many interesting videos:
https://www.youtube.com/c/DASBookbinding/videos
including pdf printing to make signature:
I’m not sure what you mean by amateur. I make my living binding books. Maybe you mean I do hand bookbinding as per most bookbinding prior to the 20th century. But that would make Chris an amateur woodworker. Anyway, very surprised to see someone mention me in the comments.
I was trained as an historian in the 1960’s and 1970’s, with a hiatus to do the Southeast Asia Grand Tour. In other words, I’ve been immersed in books and what some of us call book-like objects for the last 60 years and more. I haunt the bouqinistes along the seine, dusty and dim shops in London, Edinburgh, Dublin, and Vienna, and occasionally (when my pocketbook allows) places like Maggs Bros. A lot of my books suffer from a bit of foxing, and fabric covers worn thin by a hundred years of hands. One reason I like books from this site is that I can imagine my great-grandchildren holding them and enjoying the feel and smell as much as I do, and noting that ‘This Stain’ is from Great Granpa’s coffee. Thanks for this essay, and for your work.
Did you say history books? Then, no big loss. By the time you read them someone else will have rewritten the history and you can use the books for fire starters.
OTOH your Charles Hayward series is worth much more than the price you charge for them. Thanks for the quality!
Chris,
Being a man of accuracy and precision, I have a question for you about…paper cutters! I’m a professional graphic designer and on more than one occasion I’ve used a paper cuter. I find the best ones are repurposed guillotines from the French Revolution, but those are becoming harder and harder to find. My question is, how do you avoid/remedy what I call paper creep when using the cutter. For example, if I make two marks on either side of a piece of paper and use them as guides to cut, without fail my cutting will not line up. Perhaps, I’m assuming the paper is square? Must I true the blade, like a table saw? What does one do? Tell me, oh Yoda of the Pines!
Paper creep will be adjusted by any printer that has a basic knowledge of his craft. One can check the basic quality of printing by holding a sheet against a light source. Lines of text should line up (except where avoiding a typographic snafu might occur). Margins should not be visually different between different sections of a book, etc.
I have a friend with an industrial paper guillotine. So I’m no help here. Sorry!
The paper cutter shown in the photo stinks.
Most of us know and greatly appreciate the attention and importance the principals at LAP place on the quality of the books produced and sold, not least of which is the choice of binding techniques. It’s one the main reasons we continue to so highly appreciate and buy these great books. Of course the best of all possible “bindings” are the digital books (such as the .PDF format), since those will NEVER physically break apart, and that is another greatly appreciated LAP publishing choice often made available to us in spite of the possible losses of profit in that very useful product alternative.
But it should also be said, the differences and distinctions between the various book-binding techniques in the final quality and durability of a book goes FAR beyond the binary choice between the Symth-sewn and perfect-bound distinction. The choices of all the materials involved, including paper, inks, covers, binding tapes, end-papers, glues and pastes, threads, not even to mention other book-design choices such as size and format, type fonts, decorations, page-count, and archive-quality, are also incredibly important in the final result. Even after printing of the signatures, no large-scale, commercial, printing and publishing operation can hope to achieve the final end-quality achievable by a true artisan master book-binder. Most “artisan” woodworkers will (or should) also have a great appreciation of the art, craft, skill, training, and experience of the serious bookbinder. There are SO many unique artistic enhancements possible! Bookbinding, like woodworking, has a very long and ancient tradition and practice. In fact, book-binders have long been dependent on great wood-workers for the provision of the various arcane tools and fixtures needed in their craft.
For an excellent video overview of this craft, I recommend “Men in Sheds”-The Bookbinder, which can be seen at:
I learned so much from it, and came away with a much greater appreciation of the historical craft and book possibilities.
Perhaps there might also be some miniscule market for the raw, unbound, press signatures of LAP books, so that we may bind them ourselves into legacy-museum-quality, molded, corded, engraved and decorated, leather covers with hand-made paper end-sheets? Or maybe not.
googling “perfect binding”
http://printwiki.org/Perfect_Binding
So Mattias Hallin hereabove is right:
“to add further insult to injury, many perfect bound books actually start out as signatures anyway, i.e. that they are printed on larger sheets which are then folded, same as with sewn books, and that only then are all four edges cut off the bundle of signatures to prepare it for its glue bath”
So in the print/book jargon, “perfect binding” means what Chris got.
This is clearly deceiting the unaware consumer.
Like many things in US this is done with the point of view of the manufacturer ( it is the cheapest and so it is perfect!) and not the consumer’s one (worst binding method).
Numerous example:
Like selling as a 2 X 4 something much smaller under the pretext that it was 2 X 4 before passing it though the planer.
And so on.
A 1TB drive is only 920GB. I figure the best way to go through life is to expect that nothing is quite what we want or expect it to be. Within limits of course. Expectations are a roadblock to satisfaction.
In the words of the great philosopher Westley, “Get used to disappoinment.”
I often feel cursed, caring and obsessing over details. My dad used to say “anything worth doing, is worth overdoing”.
May we hear about the paper? I’ve been colorizing the drawings in Honest Labour and The Stick Chair Book. The paper has a nice surface for colored pencils. Growing up, defacing books was taboo. Hey – my money, my beautiful books. I try to stay inside the lines.
A woodworking Book and Paper conservator here.
Yup. It’s embarrassing what the publishing industry is doing anymore. I repair most books of this type with a modified binding which will last much much longer.
I have to take the book apart. Using mild heat (if I’m lucky, less than 300F) I have to peel off the blasphemous mess they call glue to start re-making the spine. if not, I have to use a paper guillotine to chop off the deity-forsaken mass of glue.
Once done, re-jogged and stacked I place the whole book block in a press, and clamp until the ink bleeds. Either in something in a Moxon-like vise (we call them bench or laying press), or a 500lb Iron backing press.
Then a saw is used to cut a kerf of at least 1/16-1/8in, depending on the thickness of the volume. This is done in 3 kerfs perpendicular to spine, head, center, tail, and then 2 more at a 45deg angle one each between center and head, and center and tail.
Full strength PVA glue is laid down in the kerf, allowed a minute or two to start settling in, lightly worked into the ends of the paper, and then a long-fiber cording, hemp, flax, mulberry is laid into the glue filled kerf, and more glue worked in and round.
This has to set for a full 24 hours before starting a “normal” conservation spine re-build.
This repair/conservation of a perfect bound set of pages, a book block, takes 3 full hours of bench time to complete, not to mention tying up a resource for a full 24 hours.
The publisher needs to be sent the bill for my time, fixing their sh*t they put out which is disturbingly called “perfect binding”.
Thanks for describing the process! Though I once thought that the kerfing would be sort of standard procedure, apparently it is not.
I once bought a terrible physics textbook (from alpha to Z0), which is similar to the BSO (book shaped objects) described by Chris. The content is as bad as the binding, at first glance quite good (hard back) but then it falls apart. Unfortunately this BSO was needed for the class.
You are preaching to the choir! There’s a ‘quality’ printer of art books who uses perfect binding. About 1/3 of the books I buy from them start coming apart within a month of me removing the shrink-wrap.
Thanks for sharing this knowledge. I am better prepared now to spot these things. Plus, it looks like fun to do at parties.
Rare bit of transparency here from a publisher. He is calling out his competition but also revealing his own margins. Commendable.
Ouch. I publish books on historical costuming. They are perfect bound and they seem to last. My printer is McNaughton & Gunn and they are very good. I gave up selling directly to readers after Amazon began to dominate the retail book business. Everyone wants to buy from Amazon. To get into Amazon and other bookstores I have to use Ingram, a wholesaler who requires a 55% discount, plus extra fees. I could sell directly to Amazon. But they want the same discount for no wider distribution, and small publishers say Amazon is awful to work with. I could sell directly to other bookstores, except most of them want to buy from Ingram.
The common rule of thumb is to price the book for at least five times the unit manufacturing cost. That does not include anything that happens before manufacturing, such as writing, editing, indexing, illustration, book cover design, etc.. All of which cost money. Or anything that happens after manufacturing, such as warehousing and shipping. OK, so $5 extra in manufacturing cost means the reader pays $25 extra for the book. I sell to theatrical and historical costumers, who are thrifty. If they can possibly make the dress from used curtains they bought at a thrift store, instead of paying for new material from a fabric store, they do it.
I collect antique books and have taken courses in book design and manufacturing. I’d love to print on 100% rag paper. I have books 200 years old in my personal library and because the paper has not burned itself up, I can still read them! And I’d love to have sewn signatures, hardcover bindings, and gorgeous endpapers. But readers would not pay me for any of that. I get flack all the time for not selling them electronic files at $2 per book because they think publishing a book somehow doesn’t cost the writer or publisher or anyone involved, any actual money. And apparently, my time is worth nothing to them either. I’m not going that low. A good-quality perfect bound paperback seems like an acceptable compromise.
Honestly, most people don’t care about quality any more. They are used to seeing their clothes, furniture, and everything else fall apart. They think everything is disposable and you just buy new stuff all the time to show off on social media. And these are the same people who complain everyone else is destroying the environment!
Having said that, as a reader I too have bought a few of those large, perfect-bound hardcovers that fell apart the minute I opened them. And many that have not. Quality really depends on your printer.
That 5x multiple for determining retail is true for a good part of the business. But not the people who print overseas using perfect binding. A 128-page 8.5″ x 11″ full-color paperback on #65 matte coated with perfect binding and a 12pt. cover stock would cost $2 or $3 to make. And then they would sell it for $19.95 to $24.95. Last time I checked overseas prices was in 2016. So it might have gone up to $2.20 to $3.30. But retail has gone up.
Woodworkers are the most parsimonious customer base I have ever served in my career. But even though they will use expired Exxon credit cards from 1986 as glue spreaders, they will pay for quality. Not all of them. But enough.
I get spams from Chinese printers every day. Just. not. going. there. I’d rather have a guaranteed printer in the US I can communicate with well.
The title of this post reminded me instantly of an article I read years ago about the cheap, sugar- and salt-laden, denatured, processed mush that nowadays makes up most of what most people eat. The author refused to dignify these items by calling them “food”, rather he called them “Edible Food-like Substances”.
I think the economic, industrial and cultural drivers of this issue, and the end results, absolutely parallel the trend you’re describing in publishing. And in pretty much every other industry for that matter. Cheap, bland, soulless rubbish; pump it out of a factory, drown it in marketing and just keep shovelling it into the unwitting populace.
Keep right on defending that hill, it’s the good fight.
When I went to college in the 70s my wife talked me into taking a craft class as an elective. One of the projects was hand making a bound book that was Smyth sewn. It gave me an appreciation for well made books which, in addition to the content, is a big motivator for purchasing several Lost Art books. Probably my biggest book disappointment was buying a fairly expensive Bible years ago that started losing pages due to cheap binding within a year of purchase. I mean really, you’re going to skimp to make extra profit on a Bible?
I know your books will out live and I appreciate that, I just hope that they will go to someone who will appreciate them like I do
Great information. Can no longer see a “critter in the wild” without examining it.
I’m going to generalize something. I think trying to squeeze every ounce of profit out of something is sinful. It leads to bad decisions that shouldn’t be made but frequently are. I get not wanting to waste and being thrifty. However, for a bit more money you can have something made that will be of high quality. Automakers are notorious for doing this. God forbid they spend another $100 to put a better set of brakes in the vehicle. I had a friend who drove his pickup truck for 450,000 miles before he passed away (mobile business that made two loops across the USA each year). Was fascinating talking to him about what did and didn’t hold up and his learned preventative maintenance. He was religious about oil changes every 5,000 miles and got over 300,000 out of the original motor before the water was mixing with the oil. Given how much he drove, he didn’t want a temporary fix that might leave him stranded so he just put a new motor in it and that cost significantly less than buying a new truck.
Most consumers want to get everything they can cheap and don’t care much about quality. So you can make gorgeous, top-quality products but not enough people will buy them to keep you in business. As long as most people enthusiastically embrace junk furniture, junk clothes, junk food, etc., you can’t put all the blame on manufacturers.
Another example: shoes. Branded, high end, really hip. You know, around 400 euros a pair. With laces that snap the first time you put some effort in putting the shoes on. So, you head out to your shoe guy and get a pair of laces that will last. Costs you 6 euros, might cost the shoemaker about one or two – so what gives? Capitalism!
I’m with you – for that price Is’d be furious to get a psudo-book made like that. This is basically how tear out pads are made. Worst part is there is no way to fix the book eithier. I’d return them instantly.
This was spellbinding. Seriously, it was informative. Glad you strive for quality.
It would be sad as an author to see your hard work so shoddily produced. Perfect binding isn’t perfect, but it has a place and price point. Wrapping perfect bound pages in “Hardbound Covers” is a bit disingenuous-Caveat Emptor.
As for your books – Thank you for the quality your books will be around for a while. Printer here, that 8 page signature: we called it a folding dummy. It looks simple and it is, but easy to get a page upside down too, ask me how I know – ha
When I encounter books made as you describe above, if the inside margins are wide enough I will take the book apart, divide the pages into 1/8” stacks, needle punch and sew them by hand with archival thread, then stitch the collation back together and sew each into the binding tape and back this with glue. I will while I am at it bind the book with quality leather. If a book is worth keeping it is worth the trouble, but of course I am not paying someone else for the labor involved. I got into bookbinding as a collector of antique books from 1500 – 1800s that suffer cover deteriorations due to the organic glues and leather curing of the past; though the rag papers in them are nearly as supple as the day they were made.
I love books that you publish for content as well as the physical durability and beauty. I have a nephew who will receive all of your publications as the time comes to pass them on. Whenever he is in town he passes the bookcase and finds a book, a seat, and great education.