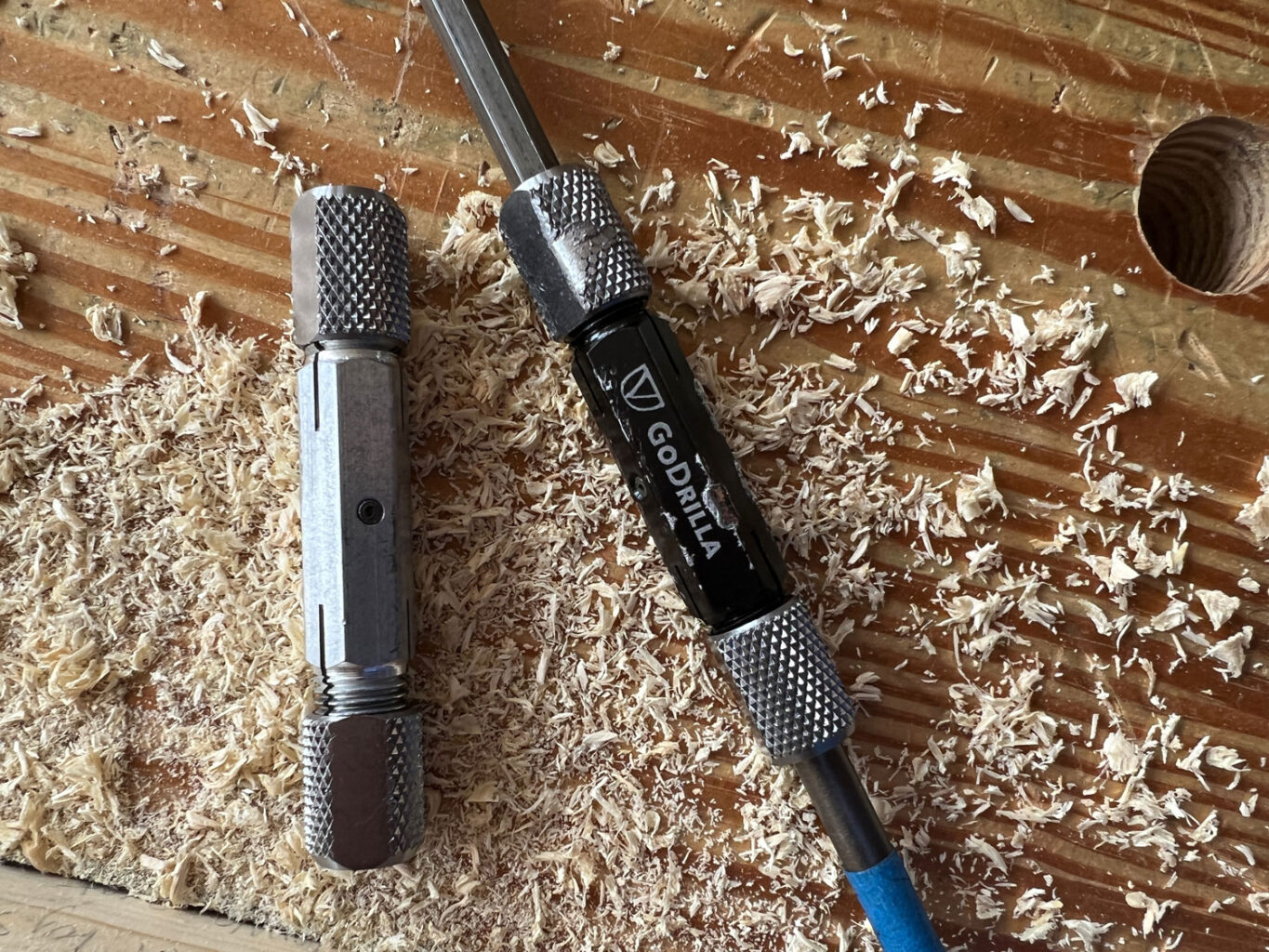
Tool designer Josh Cook and I are making good progress on snaking GoDrilla through the CNC birth canal. (What is GoDrilla? Read this.)
We got the aluminum tool bodies and steel nuts manufactured, and now we are working out the kinks. There are always kinks. I spent Friday morning trying out five different hex shafts to see which one we should choose to ship with the GoDrilla (different materials, hardness, manufacturers).
During the testing I managed to lock one of the steel nuts on the aluminum body of the tool. Nothing would break it loose. Josh ultimately suggested a soak in WD40, which did the trick. A close examination of the tool’s parts revealed that some of the black anodizing on the aluminum body had stripped off and jammed the threads.
So we will add a manganese phosphate coating to the nuts (which will both fight corrosion and add lubrication). And we will also apply lubricant to the threads during assembly so they don’t seize.
After I added a drop of machine oil to the threads, the tool stopped locking up, even when horrifically abused (see photo above). That was reassuring.
The other surprising kink we are working out is some weird runout we get when we first put the 12” hex shaft in the body of the tool. After a short break-in period, the runout disappears and the tool runs insanely smooth. We think we know what is causing this and have a potential fix so customers don’t have to “break in” the GoDrilla.
We hope to have this tool out by the end of the summer and have it cost less than $50.
Or we will run into a brick wall. Bringing new things into the world – tools, books, aprons, furniture – is like a trip through the Fire Swamp.
— Christopher Schwarz
https://www.air.tv/watch?v=y5h2R_HjQIOgmCviRm2DQQ
That dog deserves an Oscar (Meyer Wiener).
It looks like a good tool that doesn’t currently exist. And it’s interesting to see your process to test things out before releasing it into the world. I can only wish the very large manufacturers did the same.
Thanks. If we’re going to put our Tighty Whitey Underwear logo on it, we want to make sure it’s not filled with…. oh I am extending this metaphor too far.
Great work! Will the inside of the bit collet be hex or round?
Hex.
Exactly, what is “runout” that you referred to?
Where are the tool does not spin perfectly concentric
Surprisingly, it’s not the Fire nor the Swamp that you have to watch out for the most. It’s those pesky R.O.U.S.’s
Those don’t exist.
Looks much more useful than the steel shank/coupling that takes some time to find the sweet spot where it runs mostly true and not too far out of round. Combine your version with a Jacobs chuck and not be limited to hex shank bits. Sounds like a winner.
People don’t always think about the tool section and the actual craft work that goes into things and just focus on a final product. Glad to see something giving more detail on this.
Hi. Does the end that takes the spade bit and other things only have a hex shaped receptacle? Can that end accept round shanked drill bits? I can’t tell? Because I’ve been looking for a drill bit extender that takes regular round shanked drill bits.
It is for hex-shaped tooling, so the interior is hex-shaped.
A jawed chuck would be too bulky for what we want this too to be able to do.
Rather than wd40, you might want to try mixing equal parts automatic transmission fluid and mineral spirits, it’s an excellent penetrant and light lubricant, I have made a good deal of money off of wd40, it has a tendency to dry to a gummy brown varnish. An oil can, brush or spray bottle are suitable applicators.
Great! I would love to pre-order one (maybe two), whenever that becomes possible.
Looking good. Also a wide potential market for it outside the furniture/chair makers world. I think many carpenters, plumbers and electricians would get one for their tool kit.
Love the Fire Swamp. Patiently awaiting the Godzilla.
Yikes, steel and aluminum threads together. The harder material always wins.
Yeah, but they’re kinda stuck on that one. Broaching hex holes through a long tube, it’s either soft material or lots of tool wear/ $$$
Not necessarily true.
The whole reason Watch movements are jeweled (ie. Use Sapphire/Ruby bearing surfaces) is because the brass watch gears were made from would get dust particles embedded in them, which would then wear away the steel watch pins over time, despite the steel pins being harder than the brass.
In the case of aluminum and steel, the aluminum is the softer alloy, but hard anodizing creates a very hard surface layer, similar in hardness to Sapphire.
Thanks for pointing this out….
I don’t know for sure if I need this but I KNOW I want one
I plan to be all over this when the time comes. Good work and good luck working out the final details.
Speaking of drilling, it would be fantastic if someone would reproduce a Millers Falls egg-beater drill with modern day materials and tolerances. I have a couple of solid old ones, but I wouldn’t mind a new one that’s been produced with love.
Or you could look up Wiktor Kuc…
Wktools.com
Sometimes a solid restoration business is easier than setting up a whole new assembly line.
Indeed. There are several people who restore these hand drills and resell them.
Making one from scratch at low numbers (like we would have to) would make these cost at least $500 retail. The better bet is to buy a restored one as there are thousands of examples out there.
Even unrestored hand drills (about $50 to $80) can run as good as new.
the combination of steel and aluminum in any “bolting-together” joint always tend to get stuck after a while of usage. The aluminum tends to cold weld to itself under pressure. So when you have some aluminum particles in the threads (just from wear of the threads) they might get stuck at a different position in the thread, causing more wear and more particles, so that the issue gets worse and worse. Also like it was pointed out before, the anodizing is very hard and if particles brake loos, they will scratch either the aluminum of the shaft or the steel from the bolts.
So maybe its worthwhile to investigate other materials, like brass for either the shaft or the nuts? Also different coatings (maybe PVD) seems to be a good idea!
What about galvanic corrosion?
Patent pending? I hope so. Inventors rarely make money off inventions but it’s worth a try.
File a provisional patent application ($75 cost at the USPTO) then you can legally put the words “patent pending” then you have a year to find a licensee for it. However you’ve already publicly disclosed this so, on second thought, that’s not an option at this point.
If you are going to go to the trouble to file a patent, you better have the money to defend it. We do not.
Yes I would investigate the galvanic corrosion issue
I hear a BOC song in my head. Oh no, there goes a hole. Go Godrilla. Sorry.