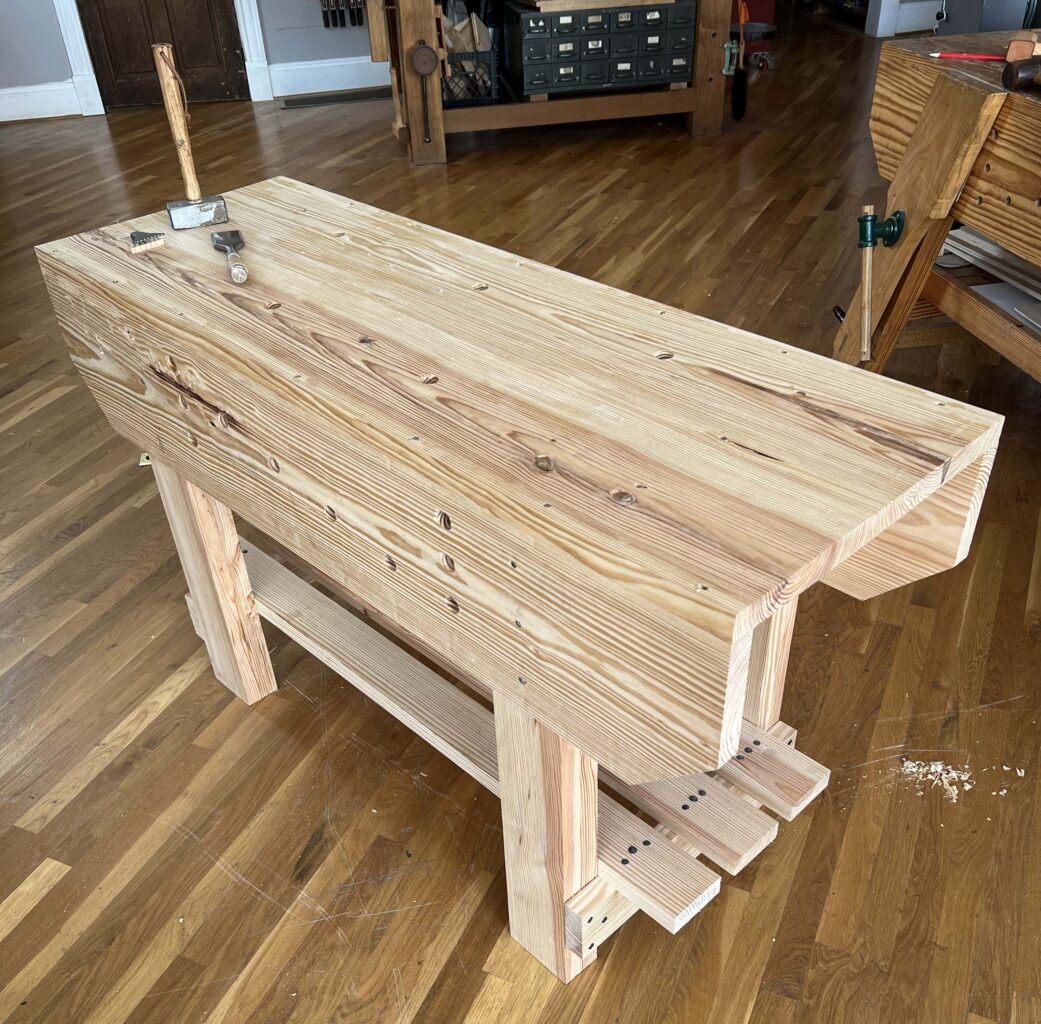
Thanks to the many people who helped cut parts for and knock together this wee Nicholson bench at our last open house, by the end of the day on March 26 there wasn’t much left for Chris and me to do to get it ready for the opening of the Cincinnati Museum Center’s “Made in Cincinnati.”
Our volunteers (again, thank you!) cut the angles on the front and back aprons, nailed the bench together and drilled all the holdfast holes. All that remained was to install a planing stop, and make and attach a crochet.
Today (yes, two months later), I did one of those things; tomorrow (or maybe Monday), I’ll make the crochet. When Chris returns from his Great Plains adventure (he’s in Omaha right now to fulfill a teaching promise made long ago), we’ll decide how we want to install that. (I’m leaning toward nails, because I don’t know where to find appropriate bolts – ones that were made in the first half of the 19th century, or at least look as if they were.)
“Made in Cincinnati,” scheduled to open July 1, includes a “made by hand section” – an educational display about important 19th-century Cincinnati craftsman, one of whom was Henry Boyd. Boyd was a formerly enslaved person who bought his freedom, and later owned a furniture making business in downtown Cincinnati. On exhibit will be one of his “swelled railed bedsteads” and a re-creation of his shop space, which is where this Nicholson-style workbench will end up. (Also, we have been working on a book on Boyd for the last couple years – we’ll be able to tell you more about that in autumn).
The only annoying thing about installing the planing stop was that because I decided to put it in line with the holes in the top (though one doesn’t need to), I had to chop right through a large, sticky sap pocket, so the shoulder isn’t a clean as I would like…and my chisel is a lot less clean than I would like (or at least it was – paint thinner and my woobie have taken care of it). After laying out the mortise location on the top and bottom, I drilled out most of the waste, then used a 2″ chisel to pare back to my layout lines, working in from both sides. (Thank you to Katherine the Wax Princess for helping me to flip it over…and to Archimedes for teaching me how to flip it back.)
So now, it’s down to the crochet – but no hurry; this isn’t getting picked up until June. (What? That’s only 11 days away?!)
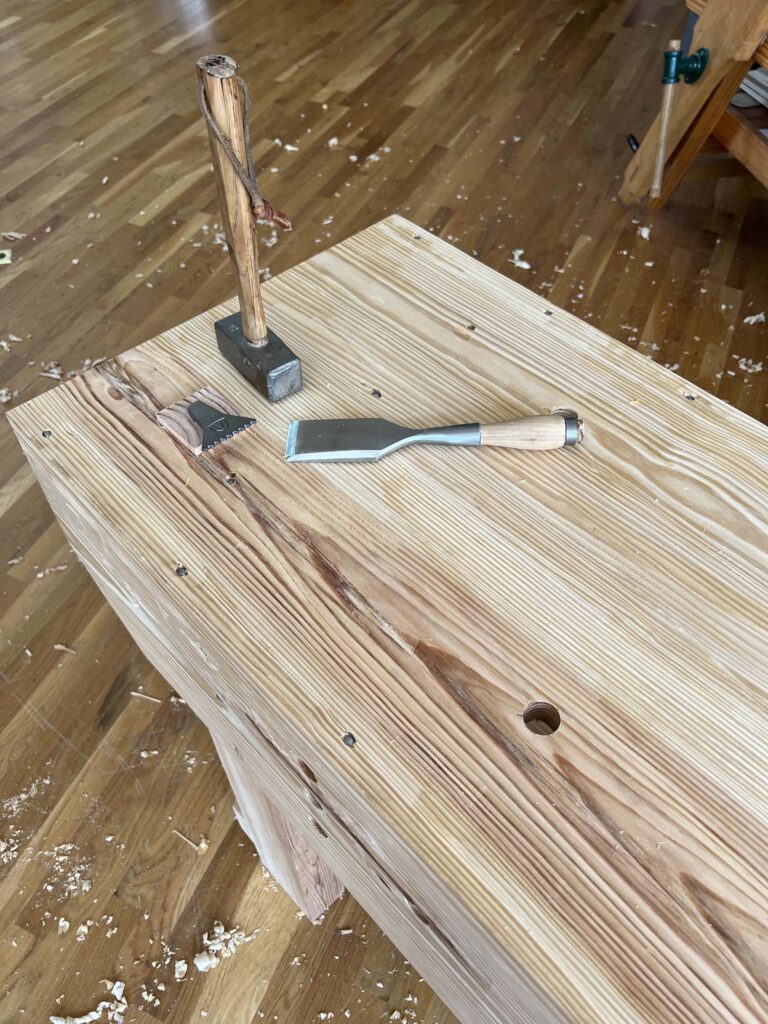
— Fitz
I’ll make the crochet.
What’s a ‘crochet?
Newbie Here!
It’s the hook-shaped thing on the end of the bench shown here: https://blog.lostartpress.com/2014/05/24/the-nicholson-bench-for-starters-also-beginners-newbies-and-novices/ (You jam a board into the gap between it and the bench, and in conjunction with a clamp, or a simply support underneath at the other end, it holds a board in place on edge)
Thanks for the lesson
I bet they would have been square headed bolts and square nuts. As a young boy working with my dad in the late 40s and early 50s that is about all I saw. If I was home I might be able to find some but I am visiting my cousin in Wyoming. A hardware store or general store still around from the old days might have some in the back room. Or someone who disassembles old buildings and structures. “F” wrenches (monkey wrenches) we’re made for those square heads.
Good luck. 🙂
Perhaps you could dovetail the crotchet in place. I guess I would do it from above. YMMV. BTW, thanks for all you two do. ELF
Any idea if the exhibit will still be there when I’m in Covington in September?
It should be! We were told it would be a permanent exhibit (a few things may change from time to time, but the Boyd shop is supposed to stay).
Re: the bolts – would the square head bolts, or maybe the traditional carriage bolts from Blacksmith Bolt do the trick? Or are they still too modern? I’m admittedly not well versed in the nuances of early 19th c. hardware.
In any case, the bench looks great!
On Season 3, episode 3 of the Woodwright Shop, Roy attaches a crochet with a mortise and tenon wherein they are both cut as a parallelogram instead of a rectangular cube so that the crochet (mortised piece) locks in. Kind of have to watch the episode to understand but it seems pretty cool.
This! I’ve got some screen-captures if that would help.
Being a crochety old man in training, I’ll have to track that down. Sounds like an interesting variation.
Would one of these work, Megan?
https://www.oldwestiron.com/collections/square-head-bolts
https://www.oldwestiron.com/collections/lag-screws-lag-bolts
Maybe not enough time for shipping though.
Instead of nails, how about a tusk tenon with a mortise on either end so that it can be use for either left or right handed workers.
This is a museum exhibit, and the bench will not be used for woodworking.
Plus, we are trying to keep in mind that this bench was built in a frontier town in the 1830s-1860s. So we are trying to get it to look right. I have never seen a bench with a crochet that could be moved. Nor have I seen an historical bench with a crochet for lefties (though I am sure they exist).
Lots of museums have weird fantasies when it comes to workbenches. The Creation Museum had Noah’s workbench that had a tail vise that operated with levers, pulleys and rope…. We are trying to keep it real.
Please note this is not a criticism of your idea. Just an explanation of why we aren’t going to do that.
The Creation Museum? You’re pulling my leg.
I kid you not.
Some aliens or civilations far in the future are going to find the creation museum and be like WTF? Really unfortunate use of a lot of materials. I also noted the modern workbenches. They should have consulted you Chris to set up the woodshop. Would you have said no thanks?
They asked me to consult on the Ark Encounter (which also owns the Creation Museum).
https://arkencounter.com/
They wanted my help on sourcing appropriate timber for that time period. They were unsure how to get “gopherwood” (Genesis 6:14). They had apparently called several lumberyards and were laughed at. Unfortunately, I am not a scholar of the woodworking during that time period. Nor do I have the linguistical skills to deal with the twisting translations. If you are interested in reading a little about the debate, go here: https://en.wikipedia.org/wiki/Gopher_wood
Holy crap. Excuse the irony.
Wow.
Ha ha. Imagine those commitee meetings trying to figure out how to find gopher wood. It sounds some higher power in the sky was treating them like the new guy on the jobsite. “Go to the lumber yard and get me some gopher wood.” I am looking forward to checking out the Boyd presentation sometime.
looking for bolts and nuts in Roubo plates;
treenail (also trenail, trennel, or trunnel)
Usually round, although square ones will do. https://www.instagram.com/p/CcKN5kmtsWh/
housed sliding dovetail
https://www.finewoodworking.com/1997/04/01/housed-sliding-dovetails
…
I see on the link above “swelled railed bedsteads” that he was using wooden screws.
Why no vise on the workbench then?
He had a separate device for making the screws that has been investigated by the Smithsonian. Boyd very well may have had vises on his benches. We don’t know. We do know this bench style was very popular here during this time period.
Back in the day, whenever we were on the job together; we just called him “Archy.”
Nice bunch of Eastern Shore Mahogany.
Square head bolts and nuts can often be found in farm equipment dealers. At least they could when I last drove combine in the 1980’s (No Not the 1880’s!). Often old farms will have a stock in the equipment shed. As usual soak them in vinegar to blacken them.
Archimedes: a man whose intellectual gifts just keep on giving 2000+ years later.
Love it.
Oh deis immortal es! Sap pockets…
Here in Germany, with our Scots Pine (pinus sylvestris) those take a long time to harden. I have two holdfast holes in my front apron, they were oozing sap for a year or so. Having that in the mortise for the planing stop would be a catastrophe, if it was not a show piece. The stuff is really sticky. Apparently you can use it as some sort of tooth cleaning chewing gum, once it had some time to harden. Otherwise your teeth will get glued together…
Archimedes, huh. Cool!
But, how’d you get the bench into the bathtub??
I have a similar shelf on my Nicholson bench but I put the cross-braces on the inside of the legs rather than the outside. This enabled me to install the front shelf board flush with the front legs and apron of the bench.
I’m building a crochet right now for my low bench. It’s my first go at it. I was planning on using a couple of 3/4″ dowels to attach mine.
Meghan – I have some old square head bolts from my grandfather’s collection of hardware that might work. 4.5″ long, 5/8″ diameter, complete with square nuts. The heads are cool because they aren’t completely flat – an artifact of the manufacturing process. Wouldn’t be surprised if these are at least 75 years old. . . .I could priority mail them to you.
Cheers
Dave
Thanks, Dave – but I think we’re going to go with nails (likely authentic to the time and circumstances, and I’m not worried about longevity here, as it won’t be used)
sounds good – best of luck!
Sounds like ya’ll have settled on nails. But, this website is a great resource for older style fasteners, bolts, screws etc. for use in historical woodworking or metalworking.
https://www.blacksmithbolt.com/
Yep – that’s where I get all of my slot screws, for both classes and for my house!