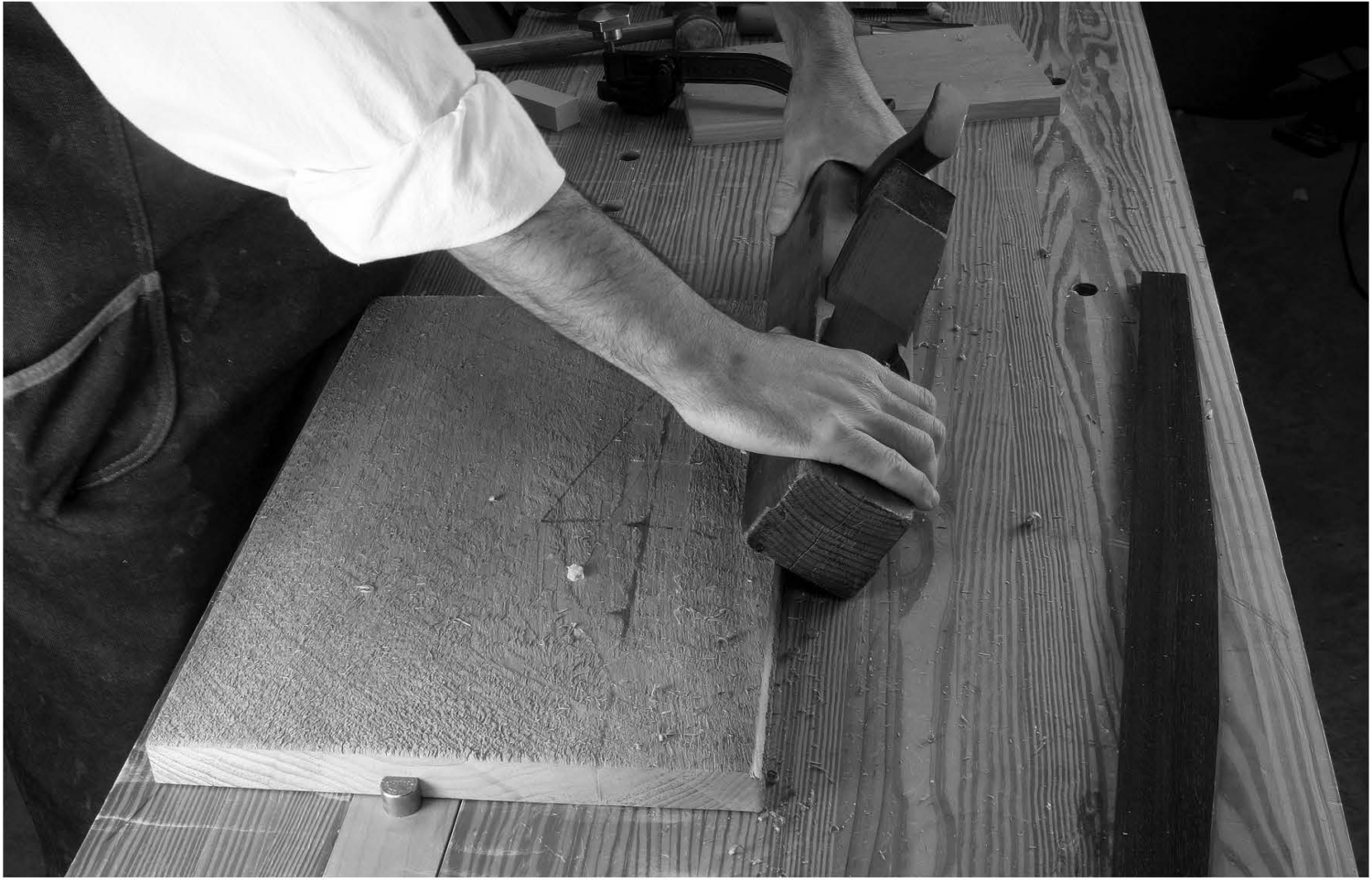
The following is excerpted from “The Joiner & Cabinet Maker,” by Anonymous, Christopher Schwarz and Joel Moskowitz. The original short, book released in 1839, tells the fictional tale of Thomas, a lad of 13 or 14 who is apprenticed to a rural shop that builds everything from built-ins to more elaborate veneered casework. The book was written to guide young people who might be considering a life in the joinery or cabinetmaking trades, and every page is filled with surprises.
Unlike other woodworking books of the time, “The Joiner and Cabinet Maker” focuses on how apprentices can obtain the basic skills needed to work in a hand-tool shop. It begins with Thomas tending the fire to keep the hide glue warm, and it details how he learns stock preparation, many forms of joinery and casework construction. It ends with Thomas building a veneered mahogany chest of drawers that is French polished. However, this is not a book for children. It is a book for anyone exploring hand-tool woodworking.
In our expanded version you’ll find the unabridged and unaltered original text; a historical snapshot of early 19th-century England; chapters on the construction of the three projects that show the operations in the book, explain details on construction and discuss the hand-tool methods that have arisen since this book was originally published; and complete construction drawings (you can download those files here).
With the glue dry, it’s time to flatten one face of all of your panels. Thomas begins with the jack plane then moves to the trying plane, yet the details of the operation are sketchy in “The Joiner and Cabinet Maker.”
Early workshop practice was to use the jack plane (sometimes called the fore plane) across the grain of a panel. This operation, which Joesph Moxon called “traversing” in his “Mechanick Exercises” of 1678, allows you to remove a good deal of deal without tearing the grain too deeply. Working the grain diagonally in both directions allows you to get the board fairly flat – Thomas checks the board with a straightedge as he works, which is always a good idea.
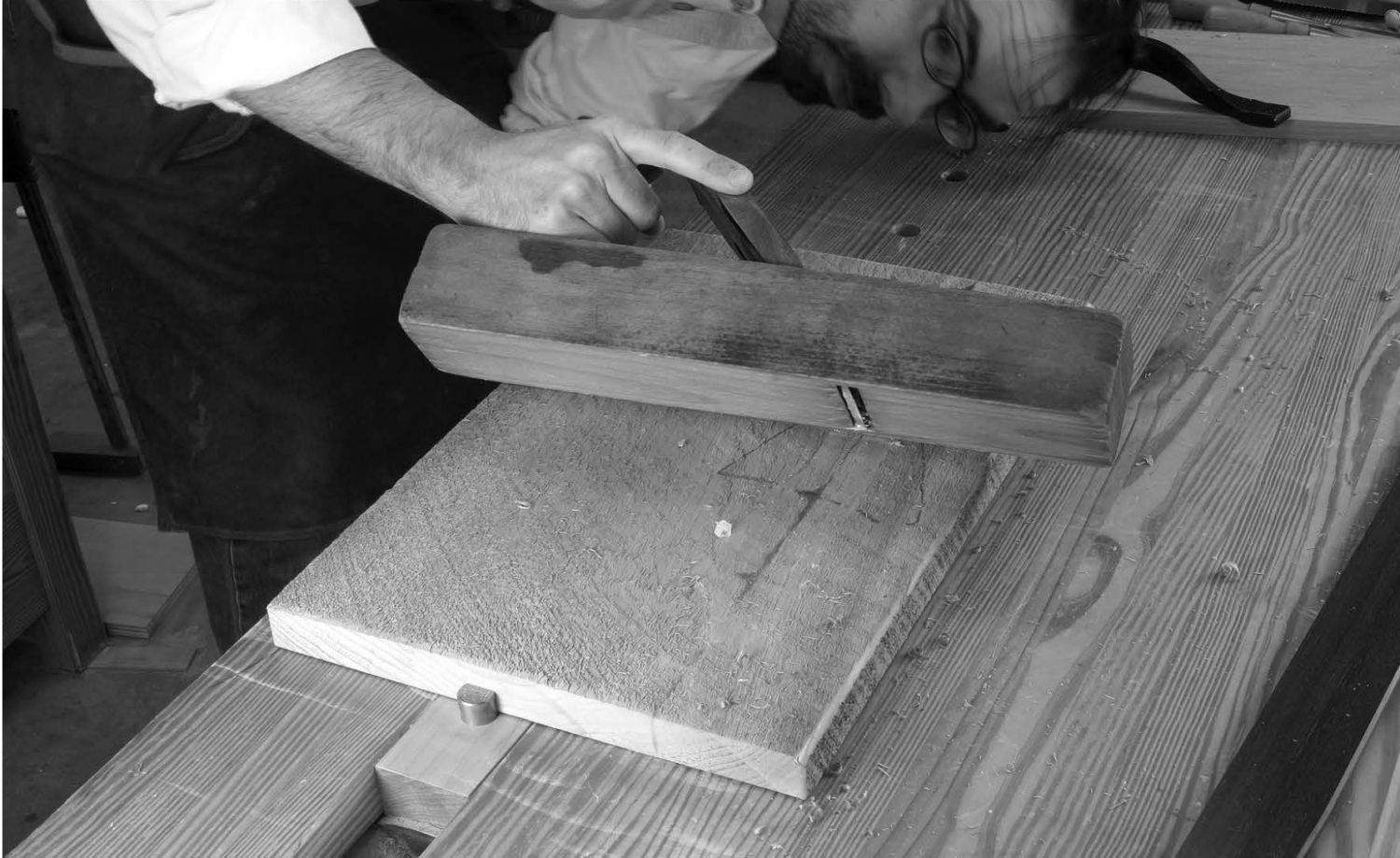
Note: When you work at 45° to the grain of a panel, you will typically see more tearing in one direction than in the other. This is normal. Just make sure you finish your diagonal strokes in the direction that produces less tearing.
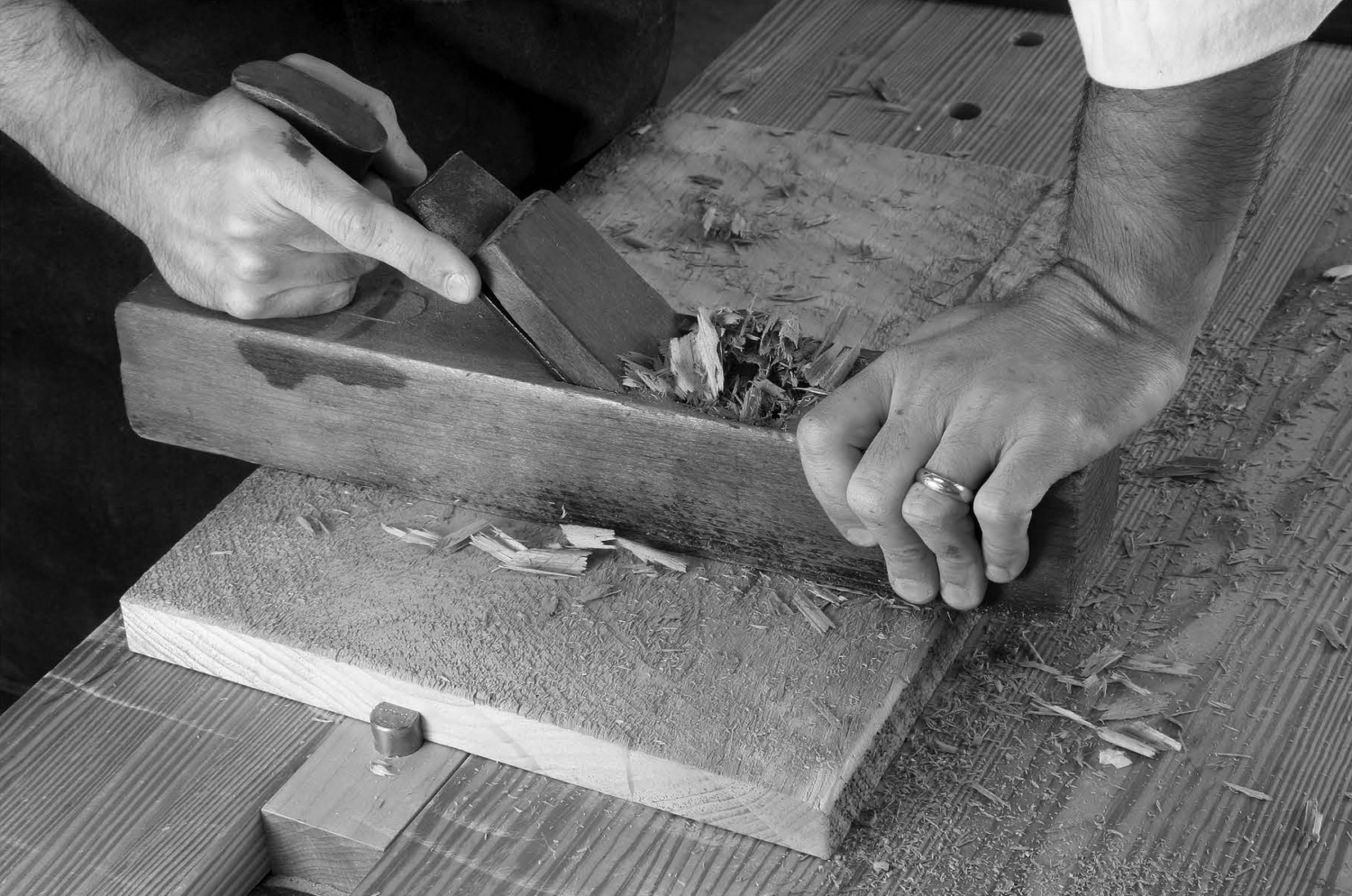
Determining when a board is flat can be a challenge. After some practice, you learn to tell by the way your planes respond when dressing the panel. The shavings become consistent in thickness, width and length all along the board. A straightedge can help. So can winding sticks, which aren’t mentioned in “The Joiner and Cabinet Maker.”
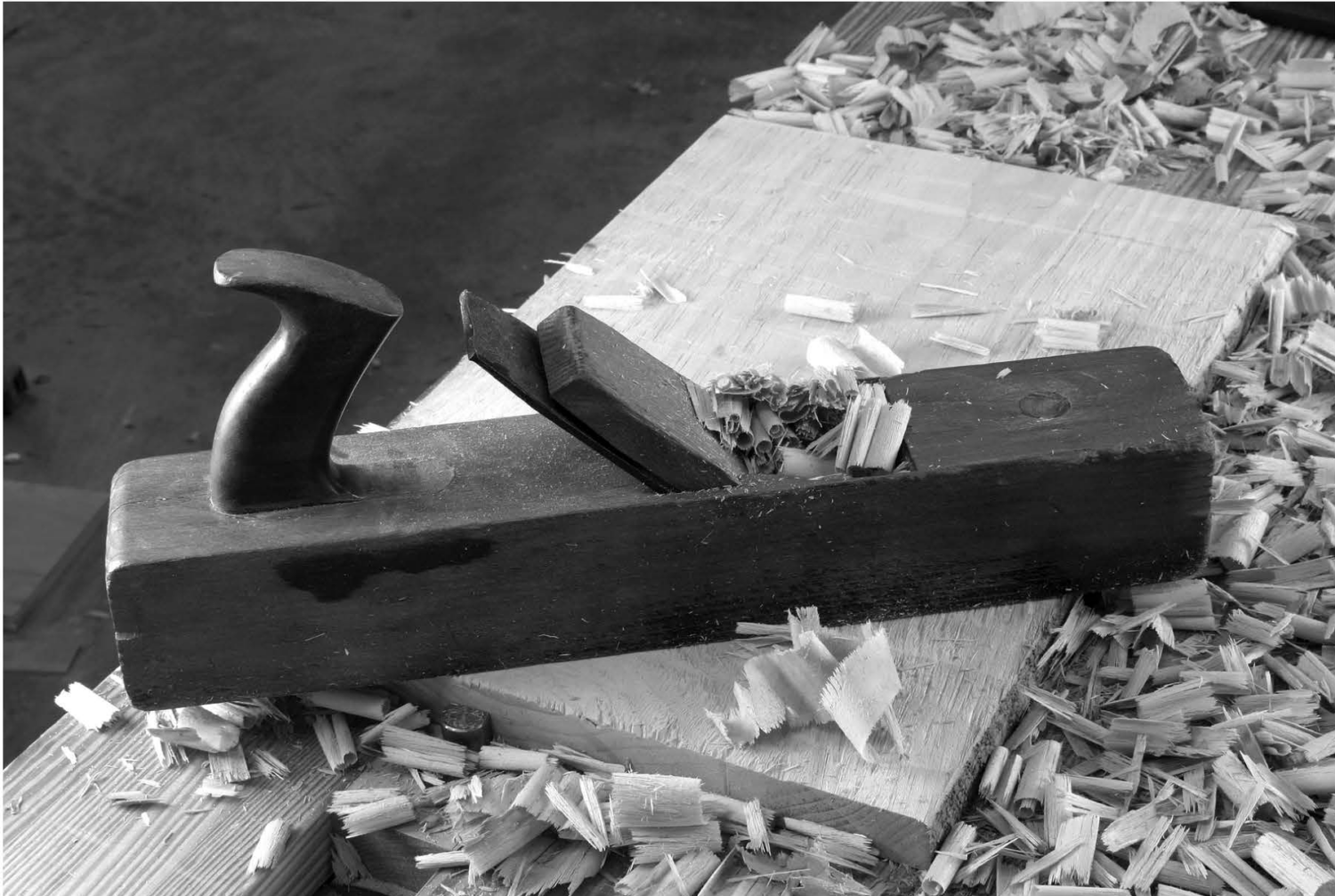
Winding sticks are two identical sticks that are longer than the board is wide. They are placed at several points across the width of the board and compared by eye. When the panel is twisted, the sticks aren’t parallel. And because they are longer than the board is wide, they exaggerate any wind. The author of “The Joiner and Cabinet Maker” has a novel solution: Compare your panel to a known flat panel. If your panel rocks on the flat one, it’s in wind. Of course, the trick is getting that first panel flat. It’s possible to create two panels that are in wind but don’t rock on one another – the high spots of one panel nest into the low spots of the other and result in a false reading.
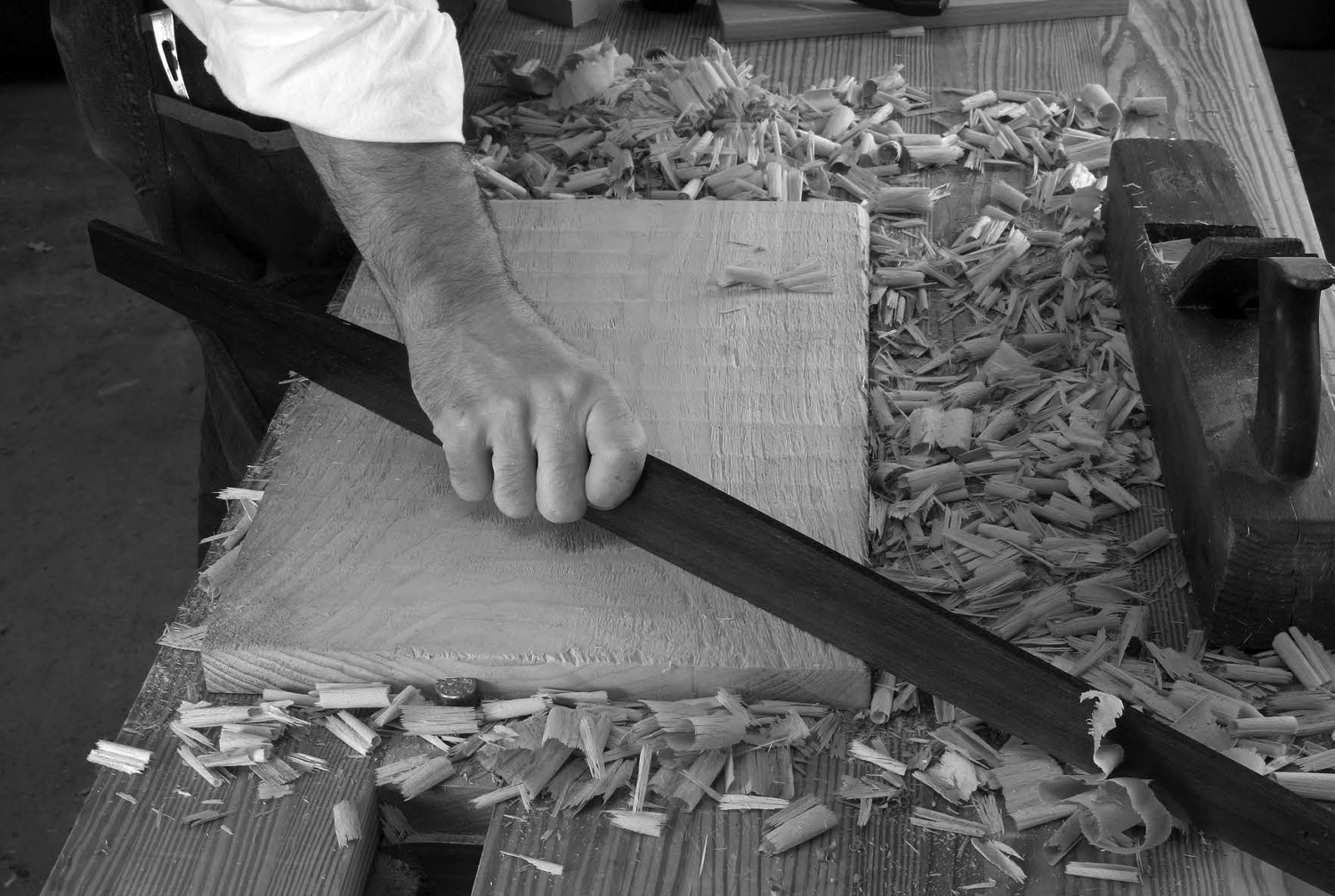
However, once you get one panel flat, the method explained in the book works well.
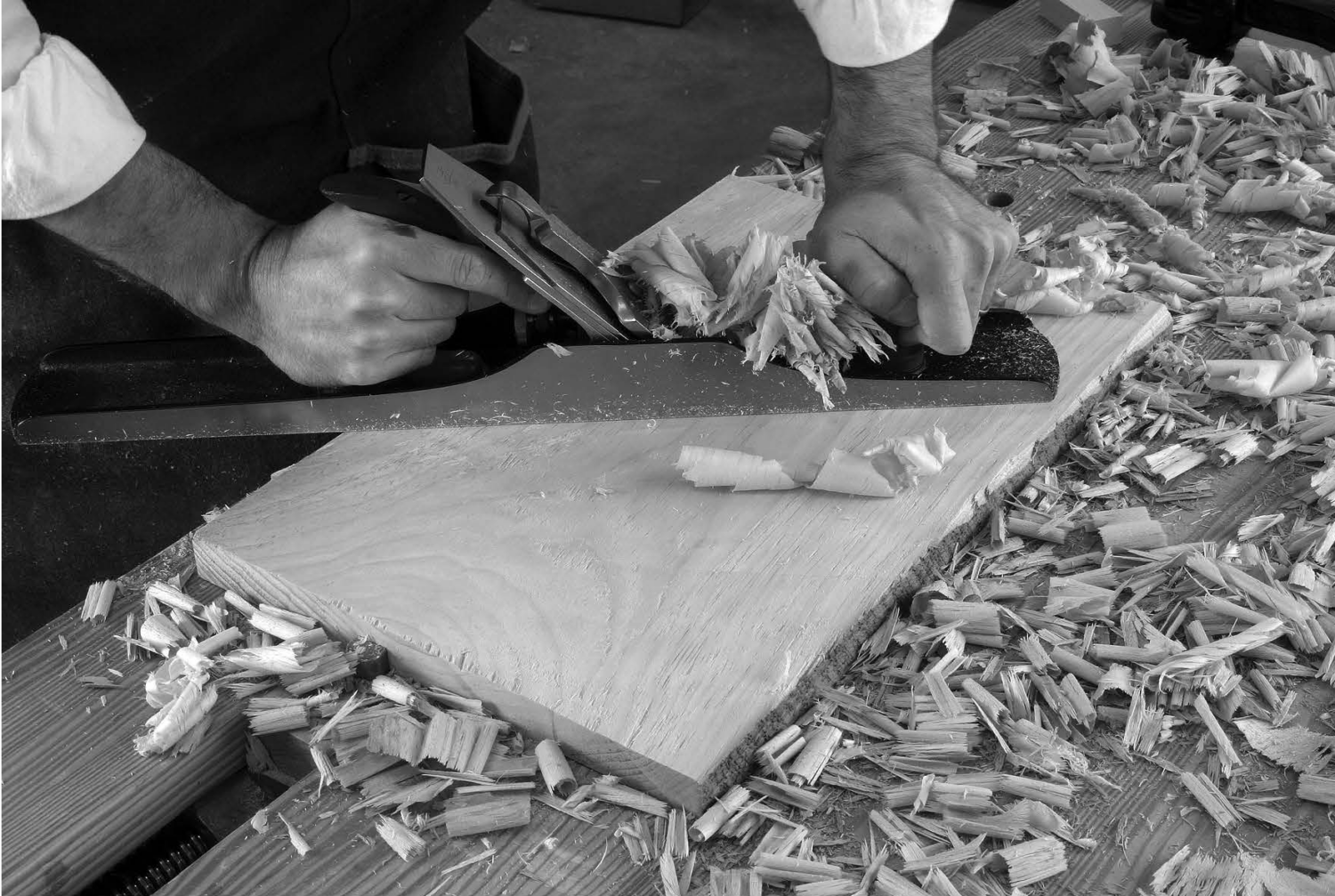
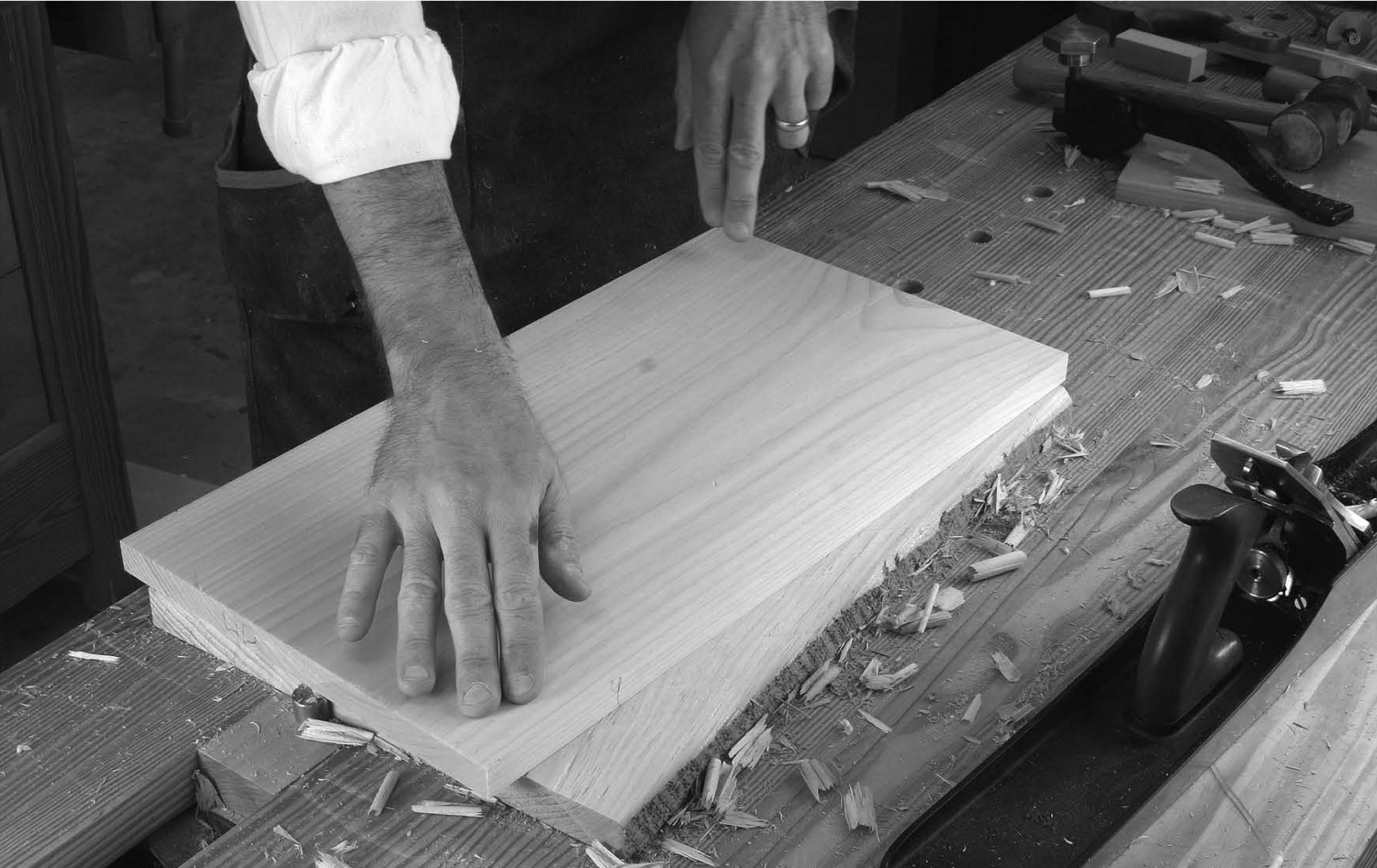
I don’t understand why so many woodworkers insist that traversing with a plane is wrong. They act as if you’ve assaulted their fundamental religious beliefs. Two minutes with a jack plane and a rough board should be enough proof for anyone.
I have been working with one of these older wooden jack planes to flatten a 2m long board of beech in the absence of a planer/ thicknesser. It’s thirsty work but this post has been a godsend in giving me confidence that some tear out is not down to me being useless. Setting these planes also takes twice as long as a modern plane – but when you get it right its very satisfying.
are you trying to sight the blade when you set it like with a metal plane? try instead putting your 2 fingers on the bottom of the mouth where the edges of the blade come out. carefully put the blade in until it touches your fingers. you can then easily feel if the blade is parallel with the sole and how far it is protruding. setting a smoother going for a whispy shaving can be fiddly, but this is a jack. all it needs is to be on the same continent as parallel with the sole and set with a heavy cut. imo way faster than a metal plane. for more info, check out the Shannon Rogers at Renaissance woodworker and the guys over at mortise and tenon magazine.
Flattening a board needs planing in (at least) 3 different directions.
Planing in only two directions might result in a non flat “ruled surface”
Google “wiki ruled surface” and look at the drawing of the “hyperbolic paraboloid” which is obtained by two series of straight lines. (sixth drawing).
So 2 times 45° and along the grain (after traversing if cup/crown) makes the 3 directions needed.
One obvious thing I didn’t thought about:
“Just make sure you finish your diagonal strokes in the direction that produces less tearing.”
love this book.
I don’t own a jointer, so I “flatten” all of my lumber by hand. Since I own a planer, I only need to remove bow, cup, and twist from one side. A flat bench and winding sticks are very helpful in checking progress and identifying the remaining work.
The surface is quickly flat enough for the planer, even If it remains scalloped from my scrub plane or rough from a toothed blade in my jack plane. I then use the planer to flatten the opposite surface. Finally, I flip the board and use the planer to make the hand-flattened surface smooth and parallel to the opposite face.
Since I don’t process large volumes of lumber, I don’t really need a jointer. But I work enough lumber that I am glad I have a planer. Respect to the folks who (used to) do this entirely by hand.
This is an area where I would love to see someone like a Richard Maguire or anyone who works predominantly by hand REALLY working at speed to prepare boards for a project. I have the luxury of not needing to use machines for stock prep but am always astonished at how much of the effort of making something is invested in getting material ready for joinery. I’m a hobbyist, and it feels like the stock prep is literally half the effort. While I work I always suspect that back in the day, there were probably umpteen allowances made in the name of efficiency, but I have no idea what they were. And then there are the occasional posts about such shortcuts, but never a place to see them really applied as a practice.
There’s a new book in the works from Joshua Klein at Mortise & Tenon Magazine called Worked: A Bench Guide to Hand-Tool Efficiency that looks like it will address that and many similar questions.
As it isn’t yet out, I’ve obviously not seen it, but it certainly looks interesting enough to me that I’ve pre-ordered a copy to which I’m rather looking forward! I, too, prep and dimension my stock mainly by hand, and just like you say: as a hobbyist, I can afford to spend the time it takes, and if nothing else it is very useful practice.
Cheers,
Mattias
Have a look at the site of Peter Follansbee:
“Peter Follansbee: joiner’s note”
I don’t remember having seen him measuring (unless by reference) although it certainly happens sometimes.
Of course, he doesn’t make kitchen built-in.
Jim Miller has published The Foundations of Better Woodworking which is aimed at the body mechanics of hand work, i.e. shortcuts to save effort. The best advice I can give is parroting St. Roy (Roy Underhill), buy the wood already S2S, or S4S (surfaced/sanded 2, or 4 sides).
Traditionally wood was cheap enough to not waste time on a crap board. 🙂
Oh, not exactly on point, David Charlesworth videos from some years back go into great detail dressing boards completely by hand. I do not remember the titles, my apologies.
Looks like something has changed with your mobile template, on Android anyway (v9). The page width has gotten much narrower. Your computer template looks the same. I would vote for rolling back any recent mobile template changes. Thank you.