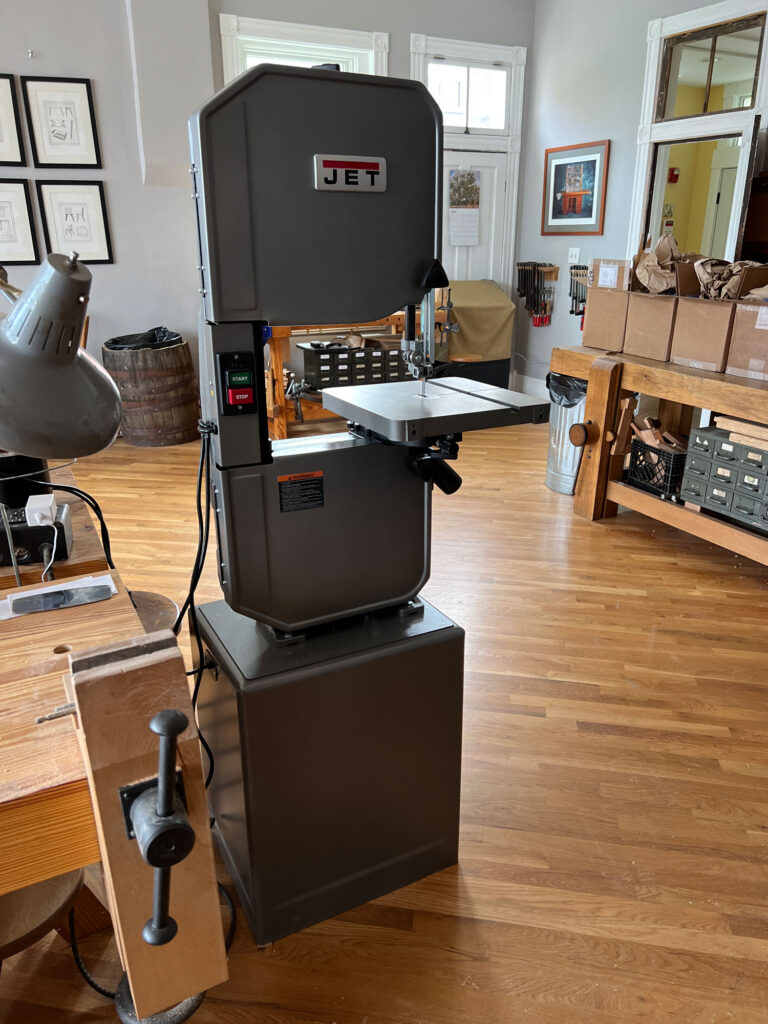
We needed an additional band saw for our bench room. We have several chair classes coming up fast, plus we use my old 1980s Rockwell band saw so much that there are times we need to have two band saws running simultaneously.
My first instinct was to buy a second old USA-made Delta band saw and restore it. But I honestly do not have time to restore a machine now.
So I bought a metalworking machine instead.
One of the odd little facts about machinery is that metalworking machines are built far better than their woodworking counterparts (and have a price tag to match). A 14” band saw for woodworking might cost $1,300, while its metalworking cousin will cost $2,300.
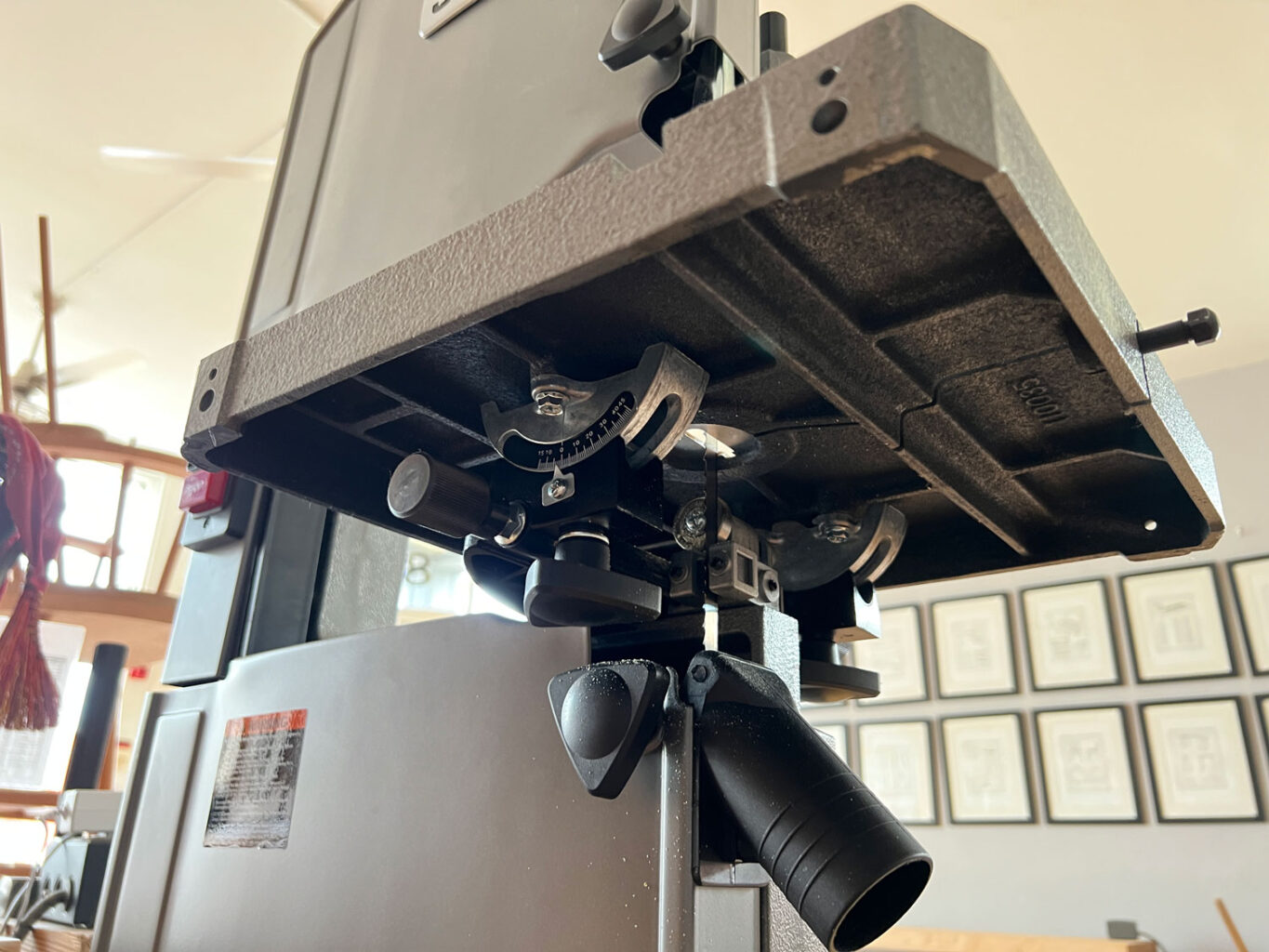
I first learned thiskl in the 1990s when working in the Popular Woodworking shop. We had a Wilton belt/disc sander that was built like a tank. All the controls were metal – no plastic. It ran smoothly and was insanely powerful. The machine’s trunnions were heavy cast iron. One day I looked up the machine in a catalog and discovered it was designed for metalworking.
When I looked at the equivalent belt/disc sanders for woodworking, they looked like toys. Plastic controls, sheet-metal trunnions and aluminum where I would have preferred cast iron.
From that day on, I got a taste for metalworking machines. (Manufacturing tools for Crucible also pushed me along this path.) When I bought a belt grinder for our shop, I made sure it was designed for metalworking. Sure it cost about three times as much, but it is more than three times better than its woodworking cousin.
And when I started shopping for a 14” band saw, I went right to the metalworking section. I settled on a Jet 14” band saw that is designed for both metalworking and woodworking. It has massive castings, heavy trunnions, metal controls and carbide blade guides. It weighs 110 pounds more than its woodworking cousin.
FYI, I am not oblivious. For years I owned the Jet 14” woodworking band saw and was completely happy with it. It was the best 14” cast iron band saw I could buy at the time. But its metalworking cousin is another animal entirely.
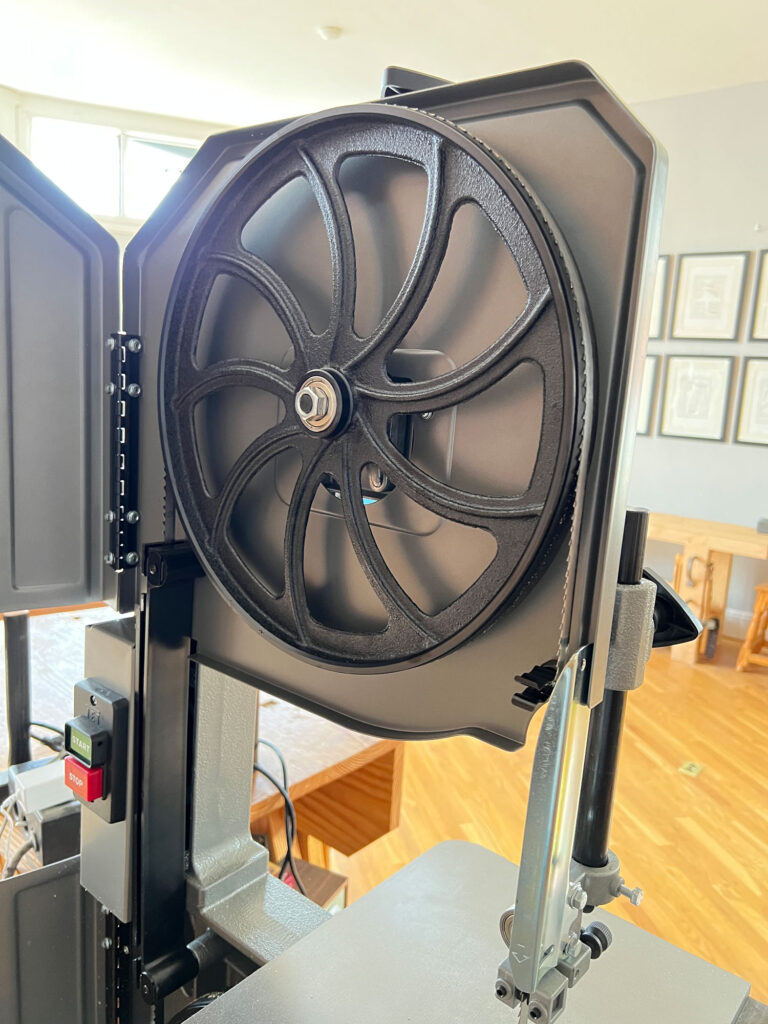
Why am I telling you this? I love old iron. Most of our machinery was made back when I wore diapers (or my parents were in middle school). But sometimes buying and restoring an old machine is just not possible because of where you live, your skills or the time required to do the restoration right.
When that’s the case, here’s another option to consider: look at the metalworking machines. There isn’t always one available, but in some cases (especially with band saws, sanding machines, lathes and drill presses) there’s another line of machines out there that you might not be considering.
— Christopher Schwarz
It’s true though, isn’t it? Working in a machine shop that serviced surface pumps when I was out of high school bent my mind towards metal applications to woodworking in ensuing years.
Which leads me to a chicken/egg conundrum: what came first? Woodworking or metalwork? Surely woodworking but at some point as man developed metalwork and woodworking were not mutually exclusive to ancient craftsmen.
Never thought of the metal working bandsaw being heavier but makes sense, that Jet looks like it will fit your needs well. The small low cost bandsaw to be on the lookout for is a used minimax 16 (mm16) built by Centuro, thing is a beast and can tension a 1” lennox CT to 20k which is what a CT blade requires to perform well (i use the 3/4” timberwolf as well which is a lot easier to tension, works well and about 1/5 the cost) i can resaw 12” 1/16” veneer on that saw. I paid 2k for a 2003 which is a little high but the guy delivered it. The new 16” bandsaw from SCM is now made by ACM another premier bandsaw maker.
Don’t metal band saws run at a slower speed? Does that impact cutting wood?
If the saw is designed only for cutting metal, then yes. However, you can convert it to woodworking with an inexpensive pulley. Many metalworking saws have a stepped pulley so you can increase the speed for woodworking.
Thank you!
Is the dust collection adequate? My 80’s vintage Delta has a similar but smaller dust port next to the blade. A lot of dust gets past it. I am debating adding a 4” port in lower door.
The little port helps. But it’s not enough. Most of these band saws need a 4″ port somewhere in the lower cabinet. So your instincts are good.
We don’t have a dust collector in the bench room, so I just clean up after each job….
Good advice, I think.
Good insight.
looks like a great saw! is the motor inside the cabinet? one of the things that pushed me to the powermatic 14 over the jet woodworking model was that the jet had the motor mounted in the outside of the cabinet and used a pair of L brackets mounted upside down on the back side to keep the saw from tipping. the whole thing screamed sloppy band aid.
Can machine lathes run at the high rpm needed for woodworking?
I was wondering more about tool rests. Machine lathes don’t use them the way woodturners do.
Likewise; I feel like most lathes for metalworking, while certainly functional in the sense that they’ll likely readily shape wood, are less what most woodworkers would actually look for in a lathe. Unless there are metal working lathes that follow similar lines to woodworking ones, but I am not familiar with such…
I used to work at a small optics shop. The way you break something that looks like a three foot cube of ice down to slabs to hole drill into lense blanks was machinist tools with a retrofitted lubricant drip. Major difference between the glasscutting and machinist shop was what you had to clean up and the glass cutters diamond toothed cutters.
And for the old ways, think about this: for every operation you do, you can NOT clamp, but you may wedge or set up a barrier (wide planning stop anyone?) That the glass would push against. The glass cutters had traditional setups and imagination.
Great idea, if your woodworking puts food on the table and keeps a roof over your head.
For those of us who are lucky enough to make a gift box for a friend that maybe does or doesn’t get put into a closet for the next 20 years, this advice doesn’t make a lot of sense.
But, I understand that you, Chris, fall into the category in the first sentence, and so the advice works.
Hi, thanks for the great tip. I am having trouble figuring out what type of Jet machine this is. Could you please help out?
https://www.grainger.com/product/JET-Band-Saw-13-1-2-in-Throat-3WRN9
What is the Resaw capacity?
6″
is the motor located in the cabinet or on the outside? i can’t tell from the pictures or the manual.
Inside.
In Michigan there are many small shops along a line south of I-94. Over the last 20 years of manufacturing moving offshore larger companies are shutting down.
This is an opportunity to buy used equipment at bargain prices. A Doall 30 inch bandsaw was in every machine shop I worked in over the last 52 years. Most were old when I met them. From the WWII era. Completely rebuild able with commonly available motors, belts, switches and all the other things that wear. Manufacturing meant hard use and regular maintenance.
The machines often come with a blade welder. Great for making new blades and the opportunity to cut a hole in the center without a left through from the outside.
Check with a local realtor. They know who has a building sitting.
It is painful to see those still usable machines peeking out of a collapsed building.
Buy one and your great grandchildren will be using it in their old age.
I think there’s a lot that could be added to this post explaining the nuance of using a metal machine for wood. Reduced resaw capacity, inadequate dust collection, and wheel RPM among them. I get what you’re saying and I agree with the general concept, but I think there are a lot of things a beginner (i.e. the people seeking advice on this kind of thing) would really need to know/understand before they took this kind of leap.
Also, I think this is probably generally good advice for a bandsaw when applied correctly, but which other woodworking tools would do you believe this applies to? Not a lathe, surely? I don’t really see a milling machine replacing a drill press with any level of practicality.
I don’t mean to be a deliberate naysayer, just a couple of things that jumped out to me.
Actually something like a Rong Fu milling/drilling is a much better alternative to a drill press for a ww and I am not a fan of asian machines.
Thanks for the tip. I knew they were heavier , stronger and solid but I never equated them with woodworking. Makes perfect sense.