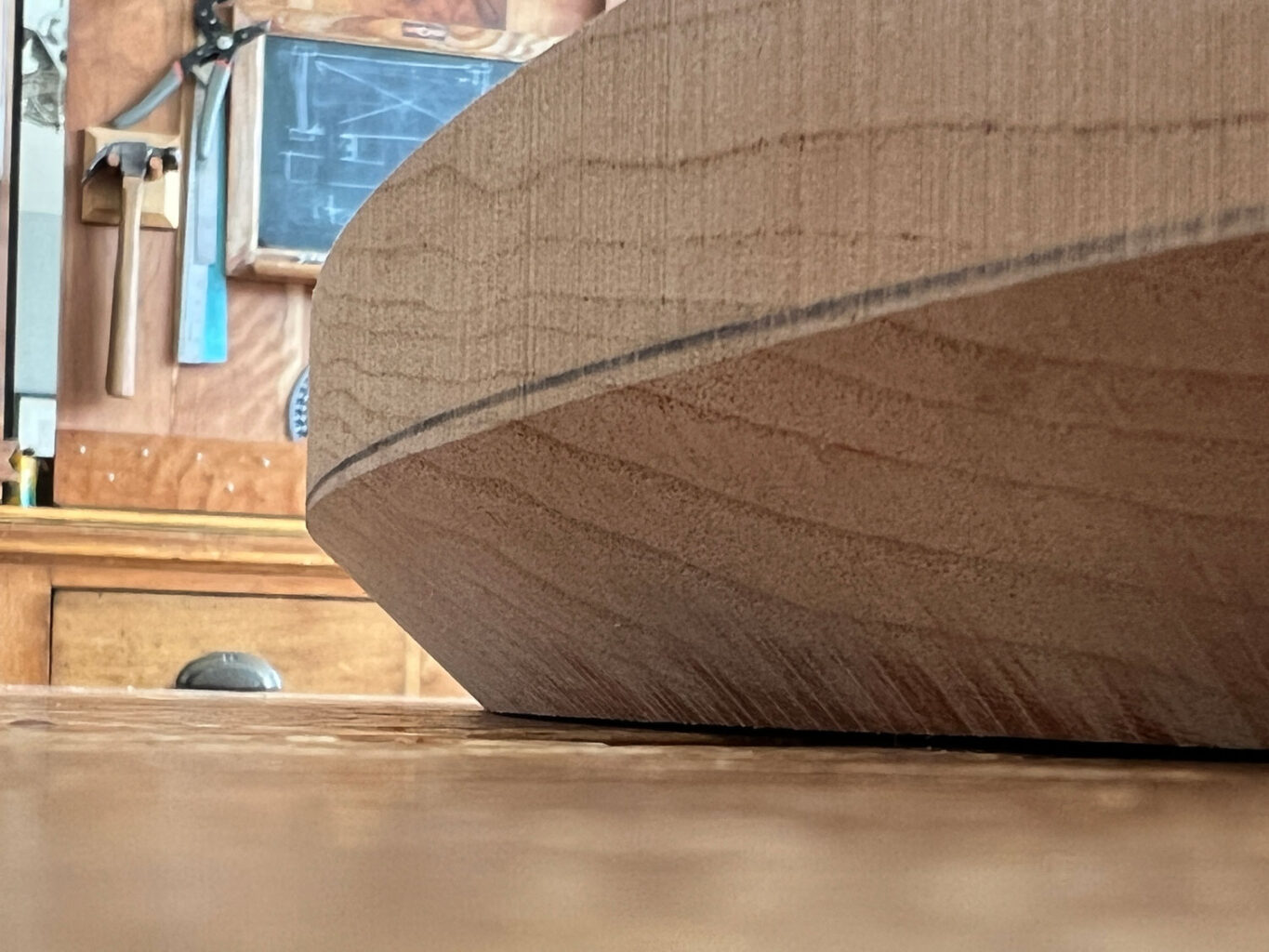
When I teach chairmaking, many students are hesitant to cut the underbevel on the band saw. It’s a straightforward and safe operation. The only trick is learning how to steer the seat. This short video shows how I go about it. Your first underbevel might look a little rough, but by the third one you’ll be an expert.
— Christopher Schwarz
I have 2 bandsaws. The earlier one was a 14″ Delta clone. Utter crap, and I only use it now for scroll cuts.
The trunnions on that saw were pot-metal. When I went to tilt it, one trunnion broke into several pieces. On removing the table the other one crumbled. I made two trunnions from hard maple, without the slots for tilting. It’s now fixed at 90 degrees.
Don’t buy crappy knockoff tools.
Agree. My saw is an early 1980s Delta/Rockwell with a 1/2hp motor. It is the machine I use the most. I’ve had to replace some parts (fractured pulley, seized thrust bearing), but parts are easy to get and cheap.
I think I’m less inclined to do cuts like this because I don’t want the hassle of returning the table to 90 degrees. Free bandsaw are great because they were free, but they aren’t totally free.
Thank you for this! I’ve been wondering about the bevel technique for some time — and to a greater extent, larger pieces. Would you use the same approach for e.g. the drinking table’s underbelly, or is there another jig / outrigger sort of system that one might recommend? https://bit.ly/3KWdUOP
The small top (beneath the big one) can be done easily on the band saw.
i have a powermatic 14″ band saw. tilting the table is really easy and takes about 30 seconds. for an “alternative” (read convoluted a la Douglas Adams) method that keeps the table locked at 90 degree, click my name and read the article “the chip carver’s guide to the workshop.”
I know this is not a bandsaw maintenance post but I have that same sound that you refer to as the thrust bearing howling in pain. Would appreciate any information on the fix for that?
Hi Derrick,
That howling sounds occurs when the bearing is in contact with the moving blade – even while you aren’t cutting. It can be the thrust bearing either above or below the table. To diagnose: Turn the saw on and look carefully to see which bearing is spinning (it could be both!). Turn off the saw (unplug it for safety).
Now loosen the allen screw that positions the thrust bearing. Move the bearing backward until you have about .006″ between the blade and bearing (I usually wrap a dollar bill around the blade and set the bearing against the bill. Lock the post. Turn the saw on and see if the bearing has stopped spinning. If not, move it back some more.
The blade should only contact the thrust bearing when you are cutting, not when the saw isn’t under load.
Hope this makes sense!
C
Thanks, Chris. I always appreciate your brief, informative videos. I learn a lot from these little guys. Please do keep them coming.
Love the Bitter Southerner shirt. I have one myself.
Where’s the 30,000 cfm dust collector come in at……:)