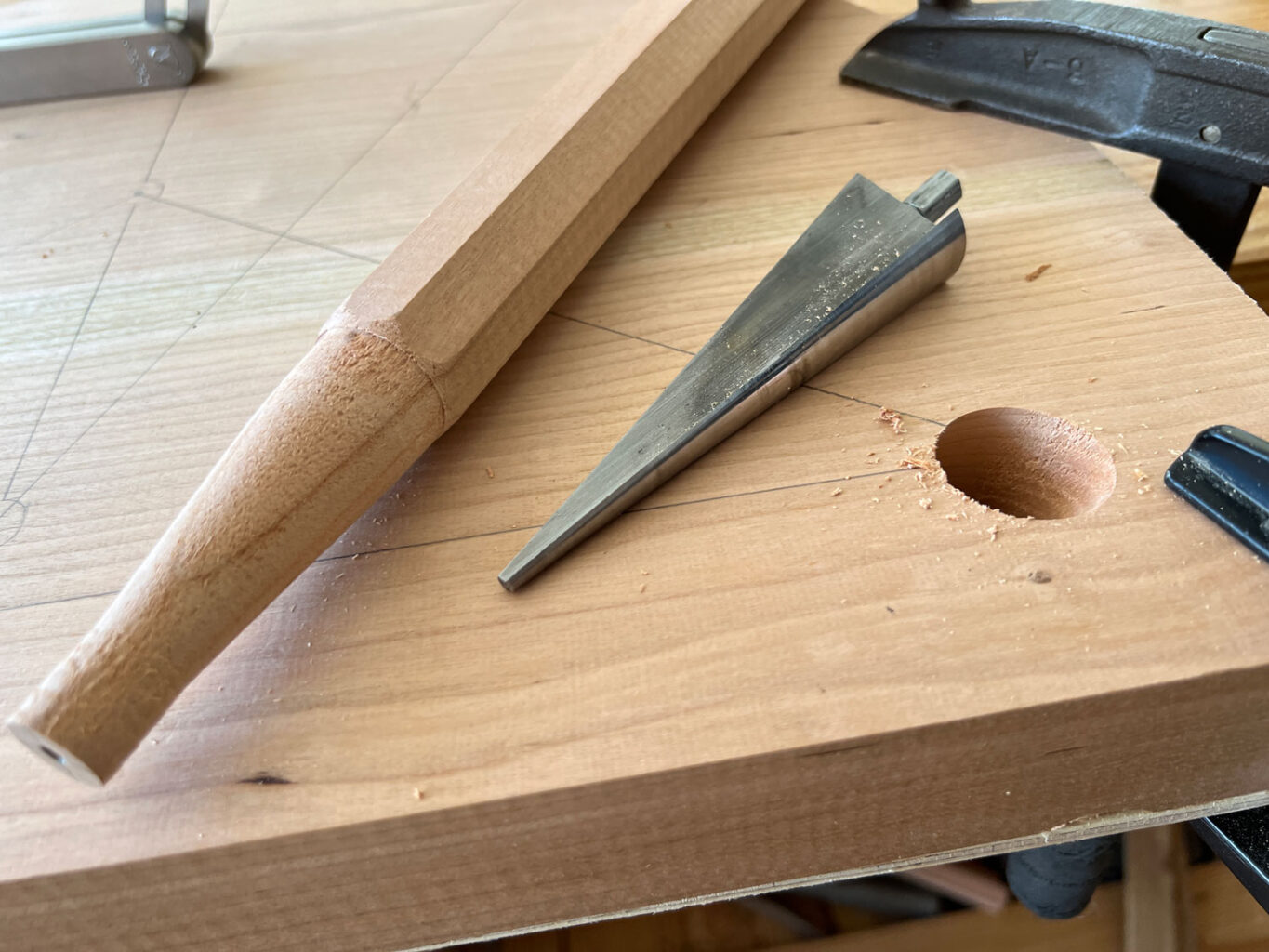
No matter how many words I write about reaming holes, my message doesn’t seem to get through. People ream for way too long, which burnishes the hole and cooks the reamer.
So I made this short video that shows how I ream holes and correct ones that are off. I hope this video helps any Baby Reamers along.
— Christopher Schwarz
Been there. Done that. Been bailed out by Chris. -_-
if a picture is worth 1000 words, your video is worth 7,279,000 (assuming 29 frames/sec). Thank you!
This is very helpful. Thank you!
Thank you for this video. It emphases the need for patience along with technique. One of the things we were taught as kids is to always clear your bit after small advances. I guess this has been forgotten.
I acquired some really wild looking, really old, big reamers years ago. I’m gonna try that 2 second rule. One of those big reamers is a finial adornment on a cabinet that I made for all my hand drills.
It’s astonishing that such a simple, straight-forward (even though tapered), rudimentary, tool can require so much finesse and technique. It’s also such a necessary skill for any staked furniture project. I’ve been doing this wrong for several years, getting your predicted burnished-wood results, along with a very hot burned tool, This, combined with your prior advice regarding how to sharpen the reamer edges, including the tool recommendation (Lee Valley Universal Sharpener, $23.90, back in stock), was also VERY MUCH appreciated by this almost eight-score-year-old Baby Reamer. The companion tapered “pencil-sharpener-style” tenon cutter tools are also similarly tricky to use effectively, and the combination of tutorials for these and the reamers are essential skills for anybody making staked furniture. Somebody should write a book.
Ok, totally new to chairs, so please pardon my ignorance.
How come you don’t taper the hole on the top (sitting side) very slightly? Seems that the wedge would splay the leg and lock it into the hole.
I am thking like how I taper the mortise in a wedged M & T joint. I don’t have it front of me but recall seeing a drawing in the ADB(?) that sure looked like the wedge is splaying the leg in a tapered hole on the sitting side. Thanks in advance.
When you drive the wedge in, the tenon compresses the wood of the seat and creates a reverse taper. This works best when your leg is of a much harder wood than your seat.
Also, the reverse taper needs to be an oval, not a circle, since the wedge only spreads the tenon along one axis. If you want to cut away a reverse taper, it is better done with a rasp or file than with a reamer so you avoid some unsightly gaps. This can be a good idea if the leg and seat (or whatever – I’ve done it on a spindle to arm bow joint before) are the same hardness wood.
Some chairmakers do exactly this and open the outfeed side of the mortise with a chainsaw file or round rasp. We do this with our hammers because of the forces involved in using the tool.
With chairs, however, I rarely do it. A single-tapered joint is naturally self-tightening. The more you sit on it, the tighter it gets. (Very different from a hammer head.) Also, I want the joint to be easily repaired. A second taper can complicate disassembly.
I might be totally wrong, but that’s how I see it. And lots of chairmakers before me have done it that way as well, for better or worse.
If you used the old time brace with a tapered reamer you would not have the burnishing issue. Its also much quieter and leaves shavings, not dust. Granted it’s more work and takes longer, buts it’s closer to being “hand made”.
Yes in pine and poplar. Good luck in oak or maple.
I agree that I prefer doing this by hand, with a JA style reamer not a brave reamer, but I also make my seats out of pine and so did many of our forebears. Chris is right though, tapering large holes in a heavy hardwood is tough work by hand. I did it a couple times to make tapered tenon cutters, and it’s perfectly doable, but a chore. If you build as many chairs as Chris does and can learn the skill to nail it that well with a drill, it’s the obvious choice. If you are like me and build only a few chairs a year, the slower approach of the manual reamer is a safer and helps avoid going too deep to nail the angle.
This video also demonstrates a trade off of electric vs hand, and the style of the chair. Each trigger pull advanced the reamer something like 1/4-1/2”, whereas by hand you can easily pause and check your work every 1/2 turn, which only advances the work maybe 1/16”. Thus it is harder by hand to overshoot the depth while finessing the angle. I couldn’t believe when he went again at the end and went so deep to correct the angle, because that would be so noticeable on the Windsors that I make. If your legs are fairly simple, like stick chair legs, or they lack stretchers, overshooting by 1/4” isn’t likely to be noticeable and getting it done fast may be worth it. If you have complex legs, and particular complex legs with stretchers, that 1/4” overshoot could be the difference between a stretcher looking level and looking askew. In my case, where overshooting could mean needing to custom turn a new leg with a bigger tenon that would still be noticeable in the form of a chunkier upper baluster, a spending the extra 10 minutes to ream 4 legs by hand may be worth it, since a new turning is at least 20 minutes plus a day to superdry in the kiln. But if I were regularly using oak seats instead of pine and the difference between power and hand were 20 minutes or more, I might think differently.
Hi Stephen,
At the end of the video – the last ream – I advanced the reamer less than 1/16″. You can take off one shaving (a half-rotation) if you like with a cordless drill set to low. I’ve never had to make a new set of legs, but I don’t use baluster legs as you said.
For my first 50 Roorkee chairs, I reamed all the joints by hand. And it was a commercial endeavor. You can absolutely do it and make money at it. To be honest, I now use a cordless drill because of tendonitis in my elbows (from handwork). So the choice isn’t about speed as much as it is about doing it or not doing it. I prefer to keep doing it.
Usually I don’t feel the need to comment, but by using vimeo you apparently couldn’t care less just how fast our bank accounts are drained.
What do you mean? You don’t need a Vimeo account to watch our public videos. We pay $900 so you can watch our videos ad-free.
I always apprecite that you host them on Vimeo. It is so nice to not have YouTube cruft. Didn’t realize it costs so much, so… thanks!
Chris already pointed out that you don’t need an account to watch the videos, but the “Basic” account is free.
I’m confused also. I have a Vimeo acct but I’m never logged in and I watch all these videos without a hiccup. Pretty sure you don’t need an account to view hosted videos.
Thanks for the helpful video. Now for the rest of the video series on making a chair(s)…..
Thanks for the video! Do you usually use a backer/scrap clamped to the seat for reaming or was that just still in place from drilling the holes?
nice Bitter Southerner shirt!
Very helpful, thank you. Do you have advice on what to look for in a 1/2″ chuck drill for chair boring operations? I’ve tried (and returned) a few higher end DeWalt and Milwaukee corded drills but each had disappointingly wobbly chucks. I’ve seen you using cordless and I’m willing to give that a shot (and make that investment) but given my track record so far I don’t quite trust my instincts on where to start. Much appreciated, as always
The two drills I use are the Milwaukee corded Hole-shooter, and the U.S.-made DeWalt cordless 20v drill. The world of cordless changes every month, so look for the U.S.-made drill with an all-metal chuck.
The Milwaukee drill doesn’t seem to change much. It’s about $100 and is pretty indestructible. (But it lacks a clutch and all the other bells and whistles.)
Thank you!
Awesome thanks for this. Haven’t gotten to this point yet but I am sure i would have botched it the first time i tried. I tend to be like Tim the toolman taylor.
“set a small fire in your hole” ha. I’m a child.
I’d like to make a drinking game out of this video; must take a drink at every unintentional innuendo.
Hold onto your liver….
How do you fix a hole that has been reamed too large? Do you plug it and try again, glue shavings to the tapered tenon or give up and drink a pint? Just asking for a friend…..
Lots of historical chairs have plugged mortises. So you would be in good company.
I don’t think I could sell a chair with a big plug so I would likely scrap the seat (which is the easiest wood to find for me) and start again.
Chris, a somewhat-related question: In TSCB you advise, when making tapered legs, to cut the tenon first because it’s hard to level the leg in a vise once it’s been tapered. But then, in the section on tapering the leg, you lay out lines on the end of a leg that hasn’t been tenoned, implying that you taper first, then cut the tenon. I ran into this problem when I cut my legs into straight octagons, then made the tenons, and when I went to taper them, had a lot of trouble laying out the lines for tapering (I ended up setting a pair of dividers to the final diameter and scribing a line on the shoulder the tenon cutter left, but the resulting facets of the tapered octagons were uneven). Am I missing something obvious?
Ha! I know this sounds like I am a loon. Here’s an explanation that I hope will help.
When I make a leg entirely by hand, I plane the taper and then make the tenon with the tapered tenon cutter. So the leg never has to be leveled in a vise.
When I use a powered taper tenon cutter in a drill, it needs to be level in the vise for that operation. So I cut the tenon on the untapered leg, then taper the leg’s facets down to the tenon shoulder with a jack plane.
Sorry I confused you.
C
Thanks for the reply! And no worries, it appears any confusion was self-inflicted, as your explanation makes perfect sense. I basically did your latter explanation, so any resulting wonkiness is only attributable to me. Guess I’ll just have to make another chair (like I wasn’t going to anyways)!
Chris , If you ever do a full length companion video for the Stick Chair Book I would be delighted to purchase a copy . Your short videos on spindle shaping and reaming have been very instructional . I confess to being a bit of a visual learner and your video work complements the Sick Chair book very well ., all the best , Peter
That is the goal this summer – once I complete Vol. 1 of The Stick Chair Journal
That is great news and will support my goal of getting a first chair built by the end of 2022 ! I look forwards to both the video and Vol1 of the Stick Chair Journal