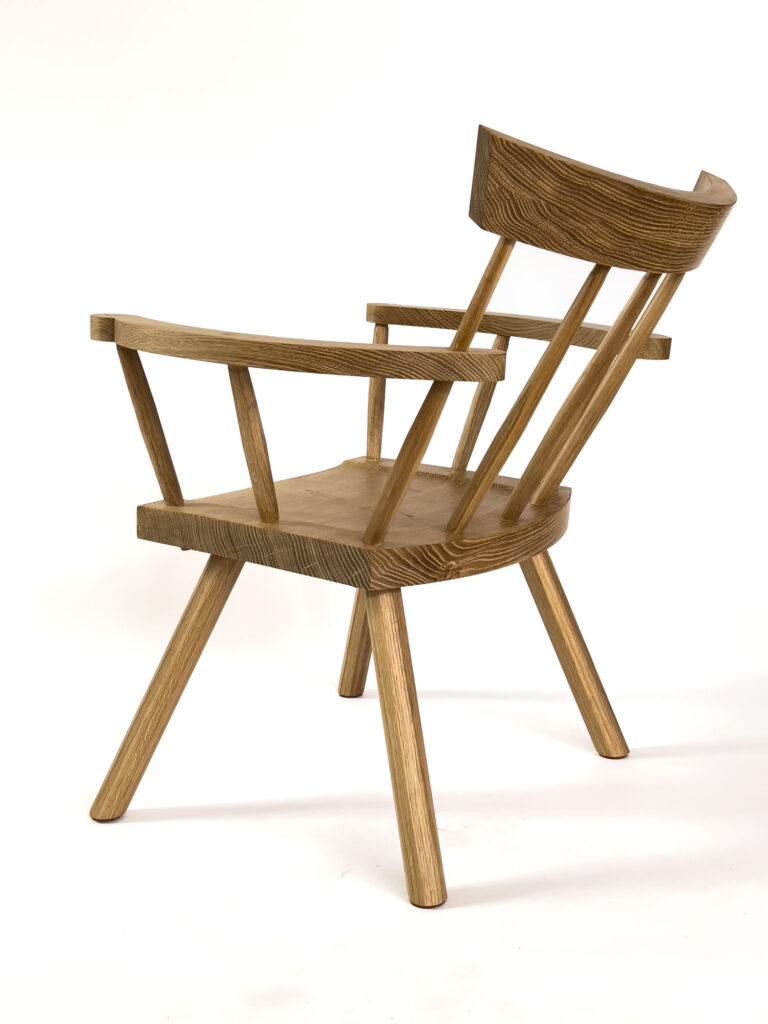
This Irish-inspired stick chair is built specifically for reading and relaxing. With a back that is pitched at 28°, a seat that tilts back at 4° and the sweeping curved backrest, this is one of the most comfortable wooden chairs I make.
The seat is 16” off the floor, which is 2” lower than a chair for keyboarding, though I don’t find the chair difficult to get out of. The overall height of the chair is 31”.
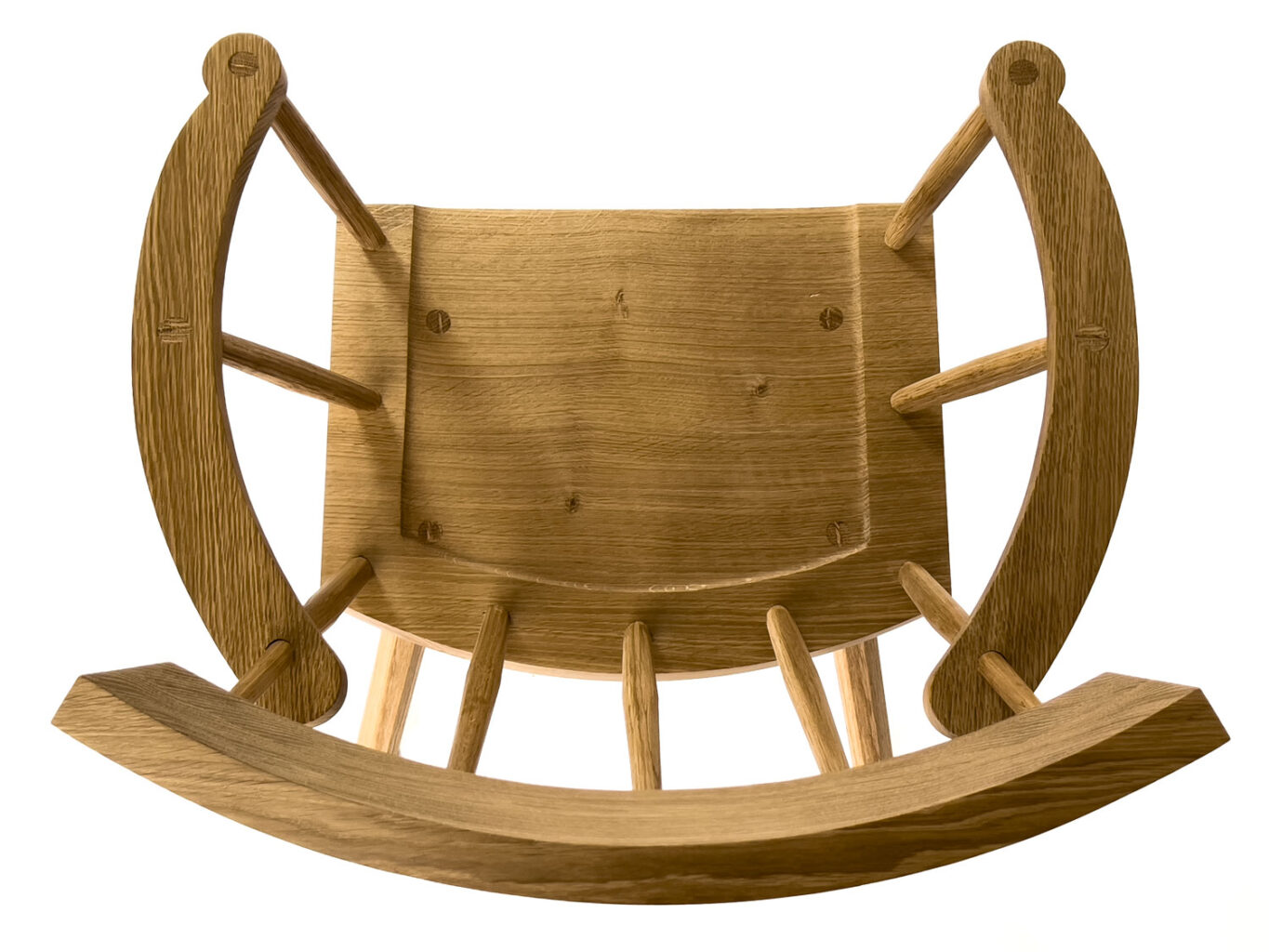
The chair is made from European oak (grown in Germany), which has an oranger tone than American oaks. The seat is a single board of oak, which was the most challenging saddling job I’ve had since I saddled a seat in dry elm. This chair is finished with three coats of super blonde shellac. The chair is assembled with hide glue, which means it will be easy to repair by future generations.
The design is inspired by the Irish chairs I inspected during a trip to the island a few years ago. Lucy and I visited numerous museums and private collections, and measured many examples. Like stick chairs in England, Wales and Scotland, Irish vernacular chairs were made using readily available materials with many ingenious touches of “made do.”
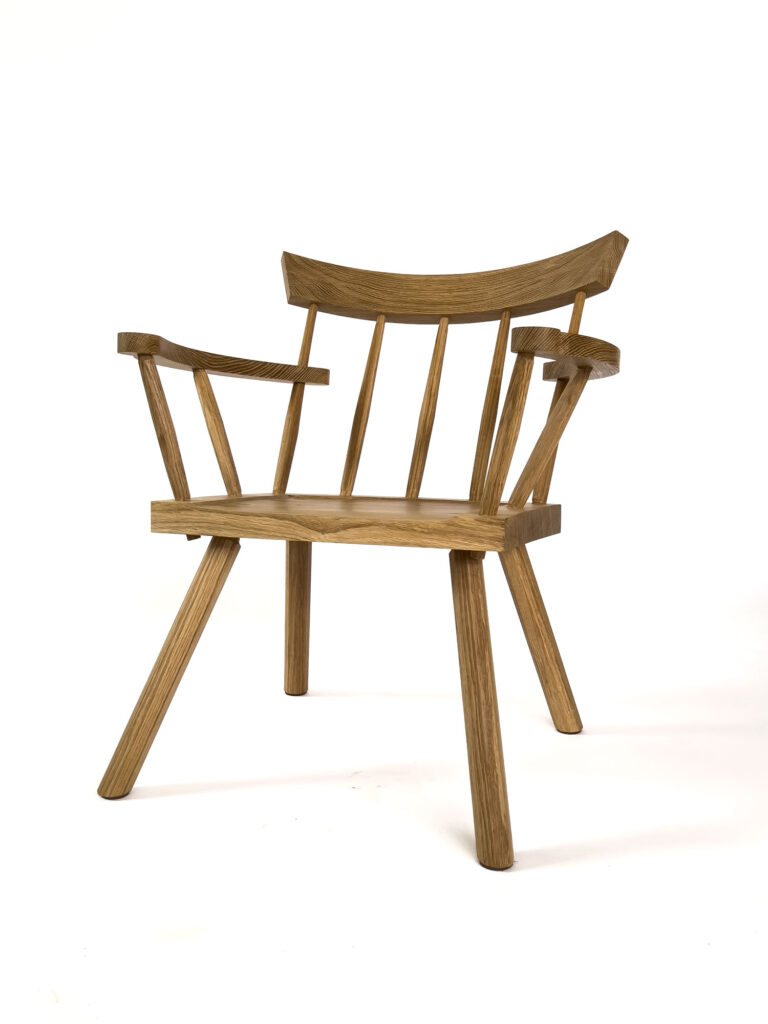
This chair had its challenges. I had only a small amount of European oak, and I struggled to get all the parts out of the boards on hand – and get the color and grain looking good. Surprisingly, it turned out OK.
Purchasing the Chair
This chair is being sold via random drawing. The price is $1,500. (I’m sorry but the chair cannot be shipped outside the U.S.) If you wish to buy the chair, please send an email to lapdrawing@lostartpress.com before 3 p.m. (Eastern) on Friday, April 15. In the email please use the subject line “Irish Chair” and include your:
- First name and last name
- U.S. shipping address
- Daytime phone number (this is for the trucking quote only)
Shipping options: You are welcome to pick up the chair here in Covington, Ky., and also get a free yardstick. I am happy to deliver the chair personally for free within 100 miles of Cincinnati, Ohio. Or we can ship it to you via LTL. The cost varies (especially these days), but it is usually between $200 and $300.
— Christopher Schwarz
P.S. Complete plans for this chair are in “The Stick Chair Book.”
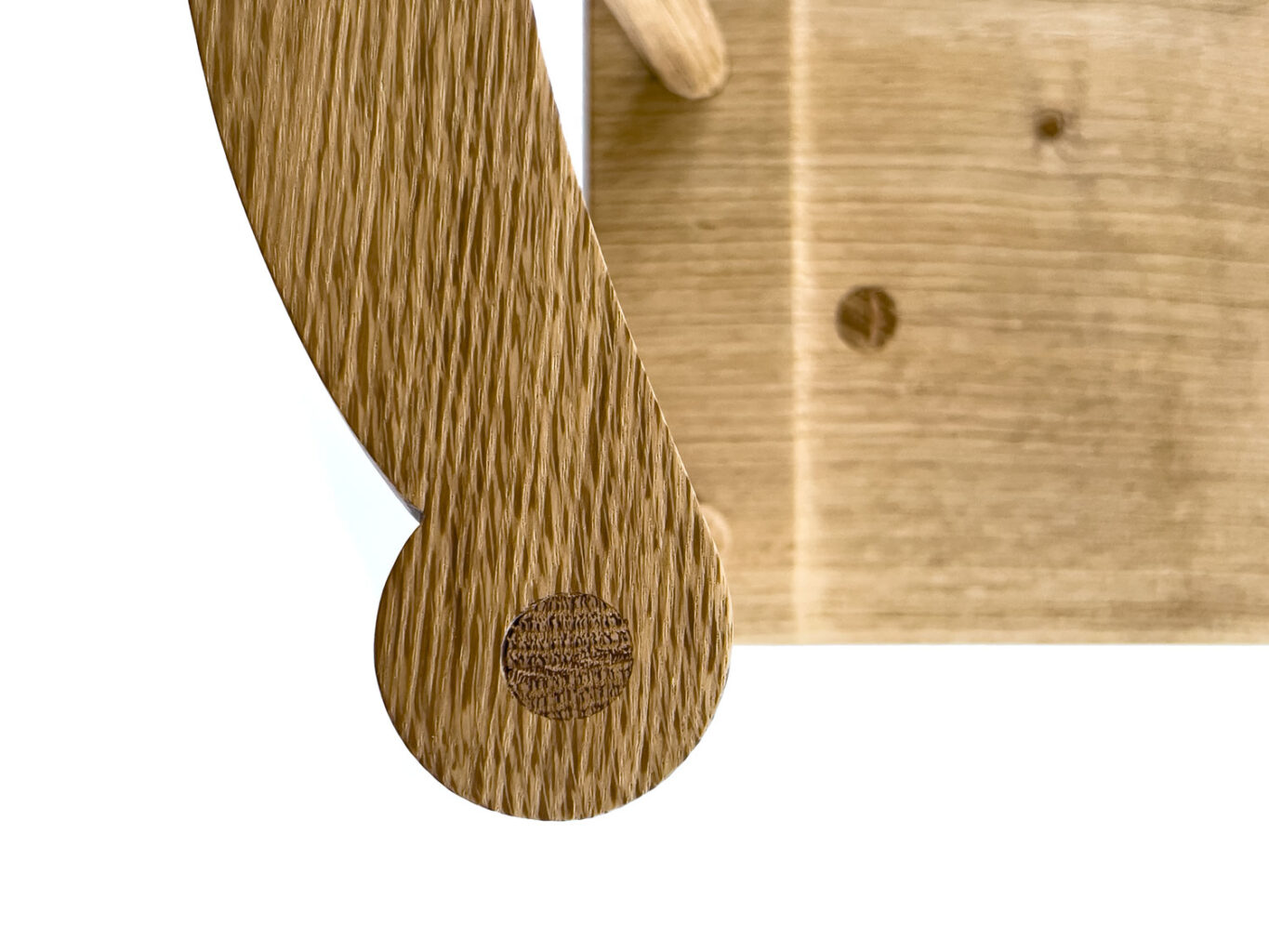
Would this work well for a fire side chair on a covered patio? Leaning towards paint or a more durable spar finish for the weather of so. No direct rain exposure, but changes in humidity would be certain in my central Texas area.
For outdoor use, I would probably use epoxy for the joints and paint for the finish. Hide glue and shellac are not designed for outdoor use.
I feel your pain, I tried saddling a seat of dry elm once, it almost required neuclear weapons. I was getting nowhere with edge tools and finally resorted to an angle grinder.
Oranger!!!
The rear left view side and end grain makes me think zebra striping(can’t tell if I picked correct word). The top down looks like sandstone. Fantastic. It has a great outline that you’ve spoken of in the past. If it’s an easy answer, can you explain what looks like very square edges on the chair. Did the Irish put the chairs together and get them right to work? Or did they ever ease the edges some?
Hi Sligo,
I don’t make reproductions – I am trying to push the designs I saw forward. All of the old chairs I’ve inspected have gently eased edges, whether by rasp or time. I like a crisper look. All the corners are eased so nothing will pinch the sitter. But I’ll leave the future easing to time and long evenings by the fire.
Really beautiful chair and beautifully figured wood. As I just read the Stick Chair Book and am about to start building my first stick chair, I couldn’t help but notice the grain direction in the arms/hands. In the book you put a great emphasis on avoiding short grain in the hands, so I just have to ask: is this here a case where your experience and judgement tells you it will be fine, or is it the seemingly thicker stock of the arms or the material that rules out any concerns?
My hope is that you don’t take this as a form of critisism, but as an honest question from someone being interested and curious.
Greetings from Germany.
Leo
Hi Leo,
With that arm shape, there is no way to avoid short grain (unless you find a naturally bent stick or bend the arm). So the way I deal with this inherent weakness is by increasing the thickness of the arm. This is covered in the chapter on wood.
So the arms for this chair are 1″ thick according to the plans. I made these 1-1/8″ thick because I had the material and it gave me a little more strength.
I hope this makes sense.
C
Well yes, it does make sense.
Thank you for explaining and thank you for your time!
Leo