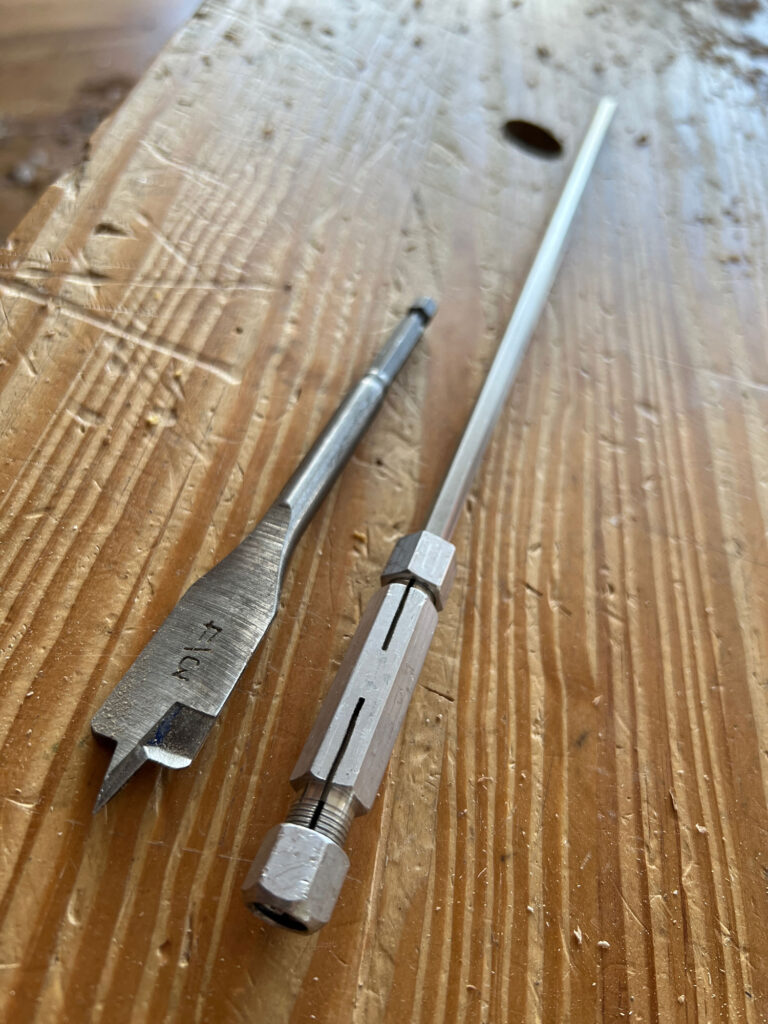
While some aspects of the U.S. economy have recovered, the printing industry is still on its heels. Because of labor and material shortages, we are still fighting lead times that are four times as long as normal. And we are the lucky ones. Many printing plants are simply turning away new business.
While we wait (patiently) for our books to make it through the long queue, we have been at work on new tools for Crucible. One of the tools I am working on with designer Josh Cook has been moving swiftly forward. Here’s a snapshot of our progress.
The GoDrilla Bit Extension
I use bit extenders almost every day, and I can tell you that every commercial one I’ve used is lacking. Many of them hold the bit with just a rare-earth magnet, which isn’t enough to keep the bit in place. Plus the fit is sloppy, so the holes you drill aren’t accurate.
Other bit extenders might hold the bit tightly, but it’s not concentric with the chuck of your drill or brace. So once again, your hole is going to be rough and larger than desired. To be fair, I think these bit extenders are designed for carpentry, so it doesn’t matter if the resulting hole is rough or a little oversized. But when it comes to making furniture, a little runout can ruin your day.
Finally, bit extenders don’t last long. They are easily bent and then become more difficult to use.
I wanted to make a bit extender that:
- Holds the bit fiercely and concentric with the chuck.
- Can be tightened by hand, but also can be cinched with a wrench when you need it to stay put.
- Is able to extend the reach of a bit from 6” to 24”.
- Is repairable if the shaft ever gets bent.
Josh and I fired a bunch of ideas back and forth, and we decided to build the GoDrilla around 1/4” steel hex bar. We will make the collet for the bit, but the user can use any length of steel hex bar to make the bit extender long or short. (The GoDrilla will come with a 12” length of hex bar, which is a common length required for chairmaking. You can order many sizes from McMaster-Carr.)
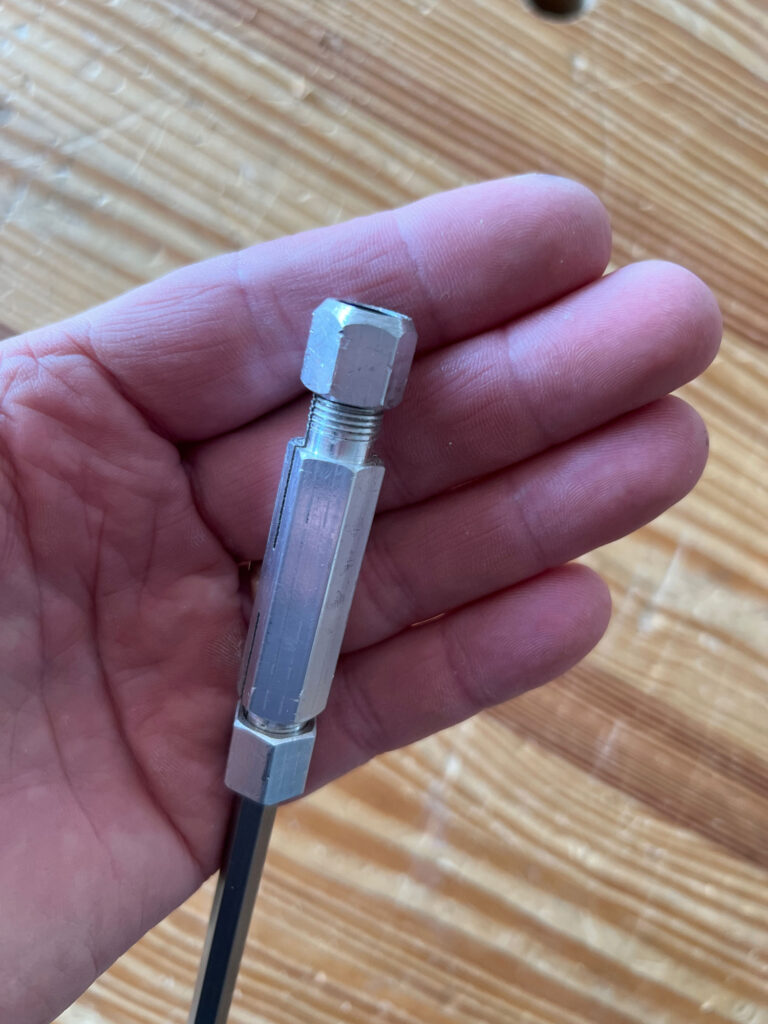
The collet works like a router collet (why did no one ever think of this before? It was Josh’s brainstorm). The collet has two ends: One grabs your hex bar (which gets chucked into a drill). The other end of the collet grabs 1/4”-shank drill bits. You can put anything you like in the collet, from a spade bit to a screwdriver bit to a countersink bit to anything with a 1/4″ hex shank.
It basically extends the reach of any of the thousands of tools that have a 1/4” hex shank.
The collet locks great with hand pressure. But you can make the bond unbreakable with a wrench.
The photos here show a rough working prototype in aluminum that has seen a ton of abuse. The real GoDrilla (gorilla not included) will have nice knurled nuts (with flats for a wrench), and the body will look a lot nicer.
We plan to make the tool in Tennessee – all our tools are made in the U.S. And we hope the GoDrilla will be about $43. While that is more expensive than other bit extenders on the market, this one works really well, and does things that no other extender does. Plus, it should last you a lifetime (instead of for about 10 chairs before it gets bent).
We hope for a summer release.
— Christopher Schwarz
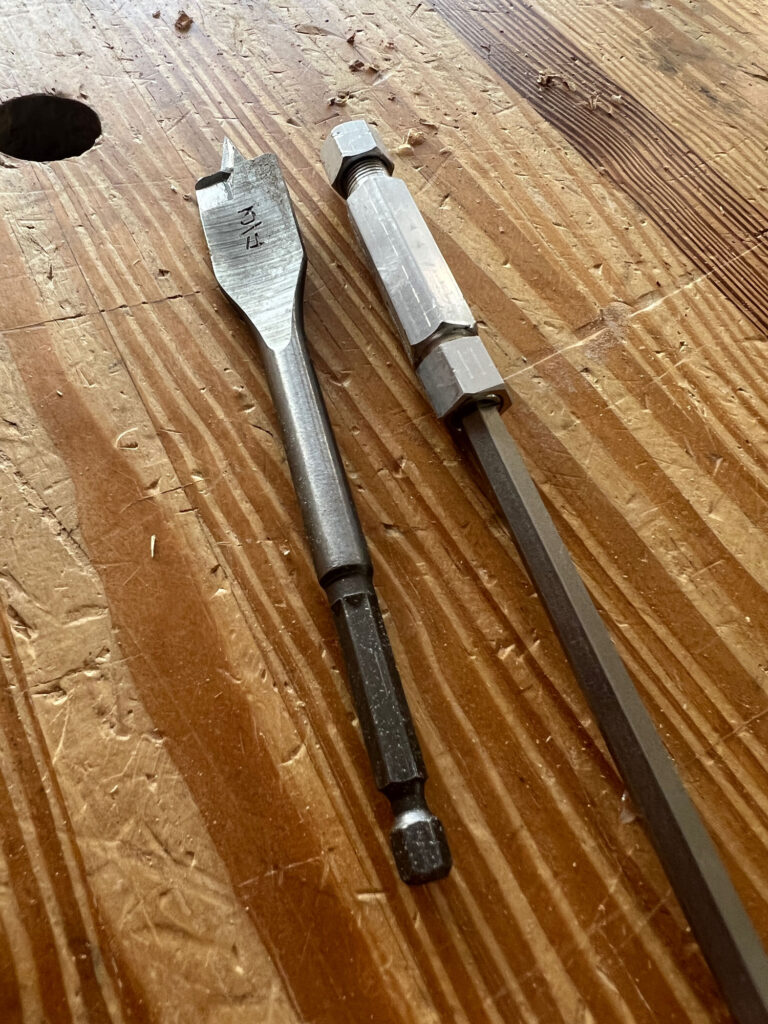
Great idea, I’ll take three!
Pretty cool
😀
What will the smallest hole the hex part will fit through without taking it apart?
We are trying to make the body as slender as possible. Right now: 0.570″
Can we have one with a No. 2 Morse Taper? With a couple of different collet sizes up to about half an inch?
That’s an ingenious solution! Looks like standard flange fitting nuts for gas and water lines with tapered internal threads. Good choice if the user loses a nut they can replace it at most hardware stores. Please tell me that the inside of your collet is also a 1/4″ hex and not just a circle gripping the corners? This is a perfect application for a rotary wobble broach.
Also please please PLEASE tell me that you at least did a basic patent search to see if you can patent this design? Yeah collets are well documented technology but “Use of” patents define most of my work in medical devices. Orthopedic surgeons are functionally bone carpenters. A lot of traditional tools see new “Use of” life in the medical device industry.
Hi Sean,
Patents are only worth something if you can afford to defend them. I covered this issue several times as a journalist and I can tell you that there is no way we have enough money to defend a patent infringement.
This is the way. There is probably a team of Chinese engineers cranking these out right now based in this article. That being said; it will be made of cheaper material and will use your pictures to sell.
But, your customers will still support you. Keep up the great work!!
Very nice design – I trust you will be shipping them to Blighty eventually?
As with all our products, we offer them to our distributors. It is up to them as to whether they’ll carry it.
And if they don’t decide to carry certain items will you ship directly to customers in the UK.
Only ask as I’m really keen to get my hands on the new dovetail template.
We cannot, but Leavalley tools can
A bunch of smart fellers you are.
(A middle schooler would change that around and have a giggle but, I’m definitely above that)
But seriously- Brilliant. Bravo.
Perfect! One less curse word in the shop!
Nice! I’d buy a few. You know that spade bit would work better if it had the little spurs at the corners…to score the fibers at the edge of the hole. 🙂
Yes: https://blog.lostartpress.com/2022/02/07/apologies-for-this-spade-bit-rant/
What is the final choice of material for the extender?
We are still working on that.
You’re right, why didn’t someone think of this before? Atta boy Josh for doing so now! I’m down for at least one.
As noted this is a great solution. I’m in for a couple.
You are the Niche King!! Great ideas that are so useful for woodworkers and specifically chairmakers. I appreciate all the time, thought and work that goes into the Crucible Tools- usually the prices are a little out of my range but I will definitely buy a lifetime tool like this. Thanks from all of us!!
I have a feeling you have awakened a sleeping giant with this. I have one that works “so so” on round bits, but requires you to tighten 2 allen bolts just right. And it takes me 2 minutes to find the right allen key. Have not had any luck with hex bits except for electric/construction work.
This is simply a brilliant idea.
One question, which I’m sure you considered: How deep is the collet? As the bit you show next to it demonstrates, some bits have an indentation for a ball catch, and that limits the surface area available for keeping the connection straight unless the socket/collet is deep enough to reach a bit past that. May not be an issue given that the collet clamps down on the bit shaft, but might be worth considering when fine-tuning the design.
Also.. pls remember Japanese bits like the Wood Owls have a different dimension here that doesn’t work in US quick release chucks.. it would be nice if these extensions worked w those too. 😉
This is what came to my mind as well. I think they’re 7/16″
Say “nice knurled nuts” ten times fast.
I’ll take one, or two.
Have you given any thought to making something like this that accepts ER20 collet? It would allow use of brad point or other bits, rather than just hex shank bits.
Using a connection on either end and hex rod is ingenious. I have a screw driver handle from Lee Valley (05K0201) that uses a collet to grip the hex bit. I really like how well it holds the bit when tightened.
👏
Fantastic Idea! What it the outside diameter of the hex body and/or bottom nut? I know a lot of chairmakers use the 1/2″ round shaft coupler with a 1/2 shaft, and that a 7/16″ hex shank does work nicely in a 1/2″ round coupler.
When I was in high rise construction we used two typical 12inch bit extensions to fasten hardware and drill tie holes on the far side of concrete formwork. Often the work is done at height and when your last bit pops out because the magnet is weak or or covered in filth it is a long climb down and back up.
In short, yes please, and not just for furniture.
When I was in high rise construction we used two typical 12 inch nit extenders to fasten hardware and drill tie holes on the far side of concrete formwork. Often this os done at height and when your last bit pops out because the magnet is too weak it is a long climb down and back up.
In other words yes please and not just for furniture.
Chris, Josh, that’s brilliant! I wonder, have you experimented with putting three slices into each end of the extender, rather than just one? Three cuts would give the collet six “fingers” instead of just two, and would therefore come closer to actually grasping the flats of the bit’s hex, rather than just grasping the points of the hex.
Excellent idea, and I would buy one for sure. Anything to relieve me from looking for an Allen key or worse, loosing the small set screws…
Ah ok it’s a play on Gorilla… I thought it was Godzilla.
Will it work in a Jacobs chuck on a lathe? My primary experience with bit extenders is some kind of stupid boring (no pun) task on a lathe and as you mention, all the options are trash.
History shows again and again how nature points up the folly of man
GoDrilla!
Great idea, and deceptively simple! Though making it a sturdy and reliable tool is less simple though you seem to have figured it out.
Now I just need a brace that is less wobbly and an excuse to buy the extension…
Slowly but surely you are eliminating the “My tools aren’t good enough” excuse. Either with inexpensive workaround (chair tenons!) or by creating tools that don’t have the flaws of the others.
A tool that works better. Is repairable. Designed and made in the USA by a mom and pop company. Hell yes!
I’m in!!!
I love the idea behind this, if successful I’d love to see a version of this that can accept 1/2″ hex shanks for stuff like bigger forstner bits. All those troubles you mention with cheaper bit extenders sound like a headache when trying to use it with a lathe and I’ve love to use a bigger version of this with mine for a few projects.
I hate to say this, but are you going to patent it? Defensively so someone else can’t claim they came up with it put your product at risk.
We don’t have the money to defend a patent. A sad but true aspect of modern manufacturing