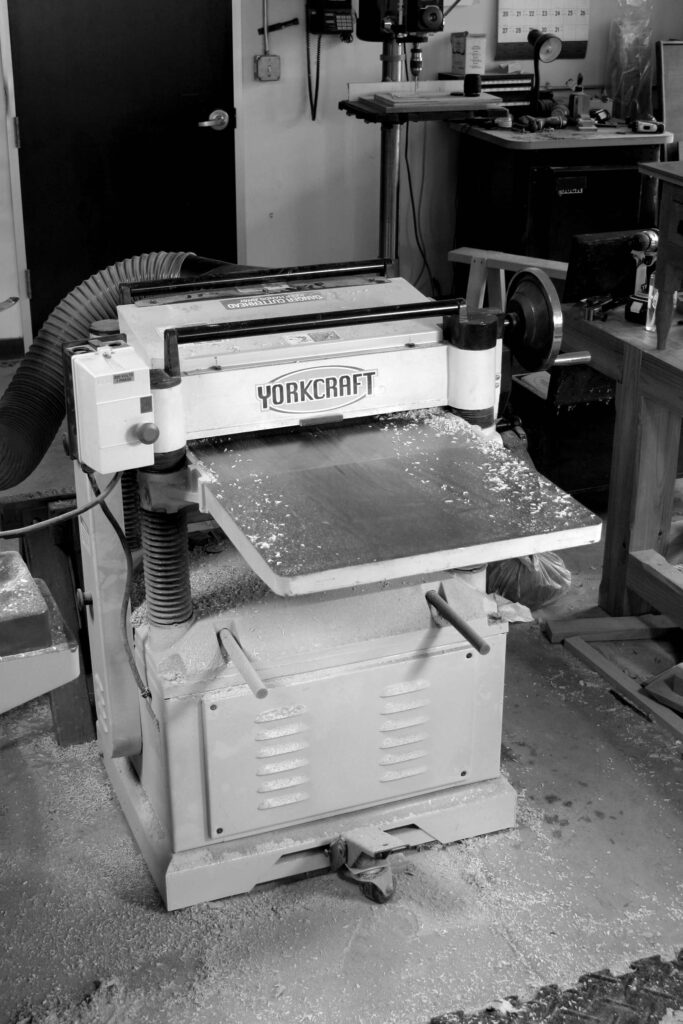
The following is excerpted from “The Anarchist’s Tool Chest,” by Christopher Schwarz.
“The Anarchist’s Tool Chest,” paints a world where woodworking tools are at the center of an ethical life filled with creating furniture that will last for generations. It makes the case that you can build almost anything with a kit of fewer than 50 high-quality tools, and it shows you how to select real working tools, regardless of their vintage or brand name.
“The Anarchist’s Tool Chest” will guide you in building a proper chest for your toolkit that follows the ancient rules that have been forgotten or ignored.
And it will make the argument that building a chest and filling it with the right tools just might be the best thing you can do to save our craft.
The first time I ever visited Frank Klausz, it was to shoot some photos for an article on dovetailing, for which he is a well-known savant. The photographer, Al Parrish, and I flew into Newark, N.J., late in the afternoon and Frank graciously insisted we come by his shop for a visit before the photo shoot the next day.
Frank’s Cabinet Shop is a large, clean and efficient commercial shop. The walls are covered in hand tools. Many are for display; many are for use. And the machinery is well cared for. After a tour and some chit-chat, the photographer asked Frank a question that took me by surprise, mostly for the fact that I don’t ask it myself more often.
“Frank,” Al asked, “what’s your favorite tool?”
Without hesitation, Frank started striding to the back of his shop. “Come,” he said. “I’ll show you.”
With Frank’s reputation as a dovetailing genius and his traditional training, I was expecting his answer to be some sort of traditional tool, perhaps something from his native Hungary, perhaps something handed down to him by his cabinetmaking father.
Nope. Not even close. Instead, we stopped at a stroke sander, a huge piece of industrial machinery. Frank launched into a speech about how much time this machine saved him. How much labor. And how he could use it to sand curved surfaces like no other machine.
I was surprised, but only for a moment. Sometimes the personae of a person gets filtered through the media in a way that’s basically right but not quite the whole story. Frank loves his hand tools and is a master at hand-dovetailing because he teaches it everywhere he goes. But when it comes to the day-in-day-out work….
Machinery, when properly used, is like having some noisy apprentices. You have to always be the one in control. You have to know how to direct them. And you never ever let them take charge of the shop.
I use my machines to deal with rough stock. Dimensioning rough lumber by hand is time-consuming.
Doing it by machine is child’s play. Then I’ll use it for roughing out some of the joinery, including mortises, tenons and rabbets. Everything else gets done by hand because it is safer, more accurate, faster or looks better in the end.
As to buying machinery, I don’t have a lot to say for this book. I can cite model numbers and brand names by heart, but that won’t help you because the powered machinery business changes so fast that the information becomes outdated before you can get it into print. Heck, I’ve seen Black & Decker replace its line of cordless drills three times in a calendar year. That is just wrong.
But I can give you some helpful principles that never change when buying electric thingys.
- 1. Buy good brands. It sounds like a no-brainer. But so many woodworkers are such cheap wieners that they end up buying tools from discounters that have no track record. No-name tools always stink. I can say this because I’ve tested them. I’ve had routers flame out on me. Nail guns squirt oil all over my work. Miter saws that couldn’t cut straight.
- Purchase tools that you have observed on job sites that look like they have some miles on them. These tools cost more than the stuff aimed at the weekend picture-hanger, but they will last you a lifetime.
2. Shoot for the middle. If you spend more than 15 minutes shopping for tools, you’ll notice that they are clustered around three different price points. There will be a low-end price point ($200 table saws, for example). These tools are designed to be used a couple times, or not at all, then thrown away. Really.
No lie. Stay away from these tools. At the other end of the spectrum are tools that cost an incredible amount of money ($6,000 table saws, for example). These are great machines, but their benefits do not befit their price for a home woodworker.
So shoot for the cluster in the middle ($1,000 table saws, for example). These mid-range tools are going to be sought out by the frugal tradesman – a good place to be.
If you want a quick education in which tools are in the middle range, check out the local or Internet classified listings. The used machines that retain their value – about 60 percent of their new price – are the machines you want.
3. Buy vintage if you dare. In the last 20 years, most machinery manufacturing has gone overseas to Taiwan and China. Some of the toolmakers have done this gracefully, and the quality control is excellent. Other makers have botched it royally and are just selling their faded nameplate on crappy goods and hoping that no one notices.
If you don’t want to research this topic to death, one way to get around the problem is to buy used machinery from the disco era or earlier. You can save some serious money and get a better machine. The only real problem is that you need to be able to evaluate the machine before you buy it. Are the bearings shot? (That’s always a deal-killer in my book.) Are the critical adjustments still adjustable? Is the motor fried? Do you need to replace the wear parts, such as belts, tires, guides etc.?
In other words, you need to educate yourself before you blindly buy. Go to the Old Wood-working Machines website (owwm.com) and just start reading. In a few days you’ll be ready to go vintage.
I will tell you that there are deals to be had. I bought my 14″ Delta band saw for about half of what it would have cost new and it is 100-percent solid. Every part but one is solid metal. And the sucker just hums.
4. Metal, not plastic. An easy way to size up a machine is to examine its parts. Are the handles and adjustment knobs plastic or metal? (Aluminum counts as a metal.) Metal is always better than plastic. No exceptions.
What Machines Should You Buy?
Few people buy all their machines at once. They acquire them over time and build their shop as they build their skills. That’s how I did it.
If you can’t buy everything at once, there are different paths you can follow when buying machinery. If you are going to be a power-tool woodworker, you should probably start by buying a table saw and purchasing lumber that has already been surfaced. You can go a long way with just that machine. After the table saw, you should buy a powered jointer and planer. Then (in no particular order) a drill press, band saw, powered sanding machinery and mortiser – plus lots of dust-collection equipment.
However, if your shop is going to be based on handwork, then I would recommend a much different route. My recommendations are unusual. In fact, I’ve never seen anyone else recommend this path in print. But I think it’s the right way to go.
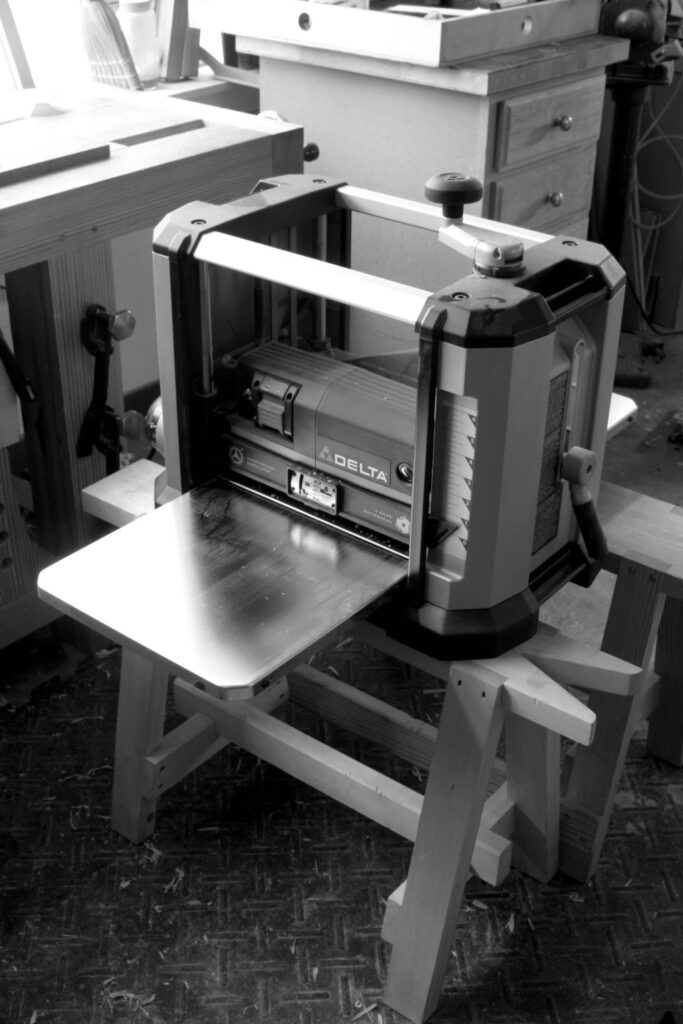
Buy a portable 12″ or 13″ planer first. Why? Because surfacing lumber to thickness is the absolute most time- and energy-consuming job in handwork. So the portable electric planer is a lifesaver. It is cheap, accurate, durable and leaves a surface finish that beats what you get from a big industrial planer. Why? Because their cutterheads are powered by high-speed universal motors.
Why not buy a powered jointer first? Good question. When you use a powered jointer and a planer, you surface one face flat with the jointer, then you thickness the board with the planer. If you have a jack plane, you can quickly surface one face of a board true, then run that board though the planer to get it to finished thickness.
What about jointing edges to make panels? A jack or jointer plane can do that job. In other words, I think you can get away without a powered jointer. But the powered planer is a must-have.
The Second Machine
Get a 14″ band saw. A band saw will remove the other biggest drudgery when working wood with hand tools: long rip cuts. In addition, a band saw can do so many other tasks that it is mind-boggling. It can cut curves, it can knock down rough stock to size, it can make thin boards or even veneer, it can cut perfect circles, it can assist with dovetailing.
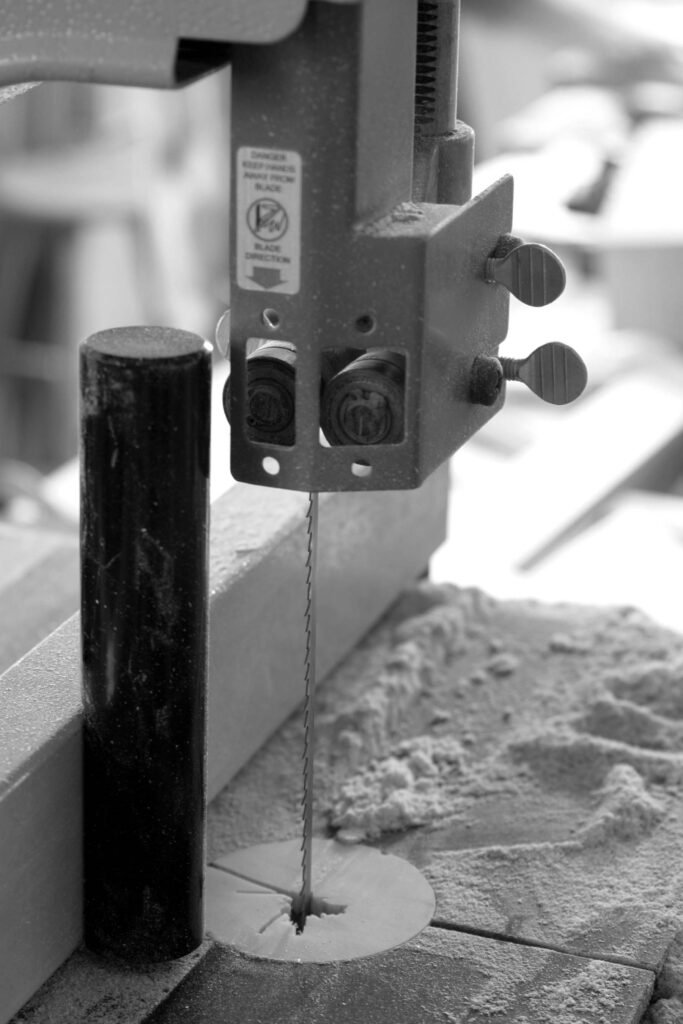
Plus, band saws are one of the safest saws ever invented. They don’t kick back on you. Their guards are safe and well-integrated into the machine so there is no need to ever remove them.
There are downsides, of course. Compared to a table saw, a band saw is fussy. You will tune it and tweak it more often than a table saw. The blade guides need occasional attention. The tires on the wheels will wear out. The blades will occasionally snap. The dust collection is terrible (but it’s terrible on most table saws as well).
Still, I would get rid of my cabinet saw before I got rid of my 14″ band saw with a cast iron frame.
The Third Machine
Again, my advice is odd. Get a hollow-chisel mortiser. Cutting accurate mortises by hand is drudgery, especially if you have more than four to do. A mortiser is a miracle machine, and it was one of the first machines developed in the 19th century.
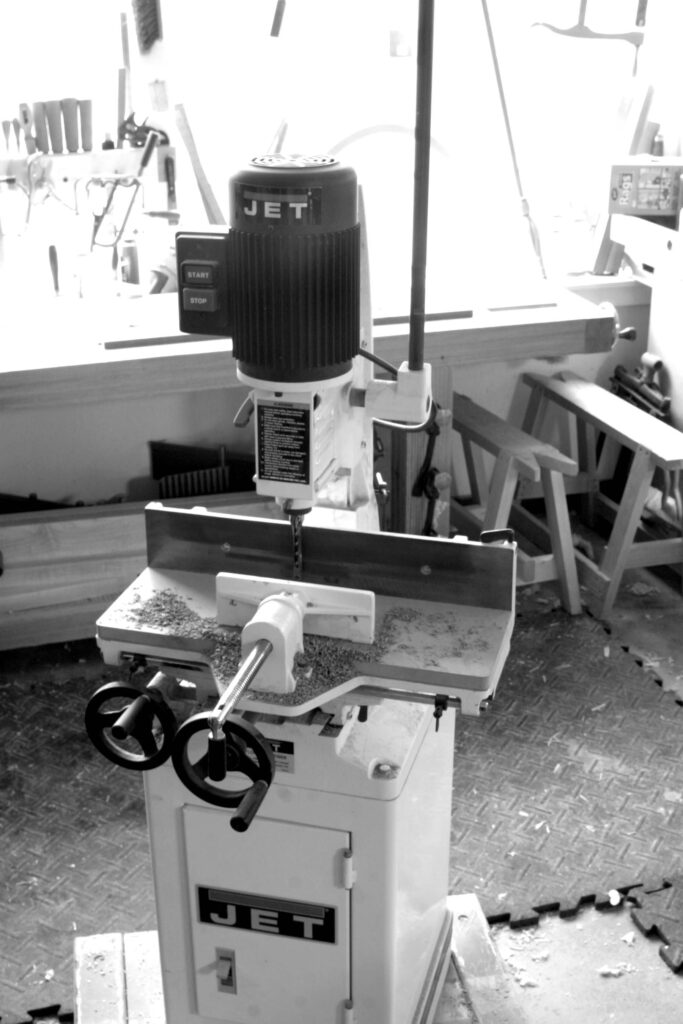
Cutting the matching tenons by hand or with a band saw is much easier than chiseling out a mortise. I have thought many times about getting rid of my mortiser. But I dismiss those thoughts every time I build a piece of traditional furniture.
Other Machines & Tools
I think most hand-tool woodworkers would be happy with the three machines listed above plus some good dust collection. A drill press, a jointer and a table saw are all nice things to have on occasion, but they won’t save you as much labor as the three machines above. In fact, before I bought any more machines beyond the three basics, I’d buy a nice battery-powered drill. I find it almost impossible to live without one of those in the shop.
Editor’s Note: More than 15 years after writing “The Anarchist’s Tool Chest,” Chris builds few pieces that require square mortises; the hollow-chisel mortiser would not be his third machine, especially because the Domino has since been invented. The Domino can cut mortises at a multitude of angles, and takes up less space. So these days, it would possibly be his third machine choice – but it’s a toss-up between that and the restored 12” jointer in our machine room – it’s such a time saver. Your needs may vary. (I, miss the hollow-chisel mortiser; it was sold to a neighbor. I don’t cut a lot of mortises – it feels like all I do is cut dovetails – but it was a fun machine to use.) – Fitz
All my woodworking machines were bought over a period of years starting with my table saw in the 80s. Some were new but most are used.
They are all heavy duty cast iron or steel. one of my most prized possessions is a 20” Powermatic Bandsaw with a table that weighs as much as some of the smaller saws I see in the stores. They are easily reparable when they are that size, bearings are no big deal. I enjoyed refurbishing all of them and using them even more. They are really quite simple machines to fix. When schools got rid of their woodworking equipment a lot of the machines were put in warehouses so one might find some bargains there. Having a walk out basement helped, my bandsaw weighs about a ton. I would never been able to manhandle such a beast down a hatchway or flight of stairs even if I had completely disassembled it. The only mistake I made was when I bought a couple of scroll saws, the newer ones are so much better so those I gave away. It surprises me how much I use my new one. My point is to think about what your going to make, if you keep at it your skills evolve over time and your needs will change.
I would not be without my bandsaw. But then I am not into production. I like hand sharpening my planes and getting exercise.
I loved this article Megan, great advice!
It’s like you knew my new planer was arriving today!
Nice article. All of my machines are old (vintage) from the 1970’s or before. They get to be like old friends. Maintaining them is almost as satisfying as building fine furniture. I disagree with your selection though. A good Delta 10″ Unisaw with two fine Forrest blades: One for solid wood and one for laminates would come first for me. That’s what I built my shop around. Next a good 8″ jointer. Good suppliers will surface your lumber acceptably to whatever thickness you need. My 13 x 6 four post planer was added much later. Glad to have it, but after a lot of other things. A good shaper is another priority. If you are making a lot of doors or millwork, it will pay for itself in short order. Look at auctions for your machinery. I bought my Delta Model 10 radial arm for $55. My first Unisaw for $600. Look for Delta and Powermatic. Their quality has stayed good for generations. You might have to get your hands dirty tuning them up but it is so worth it. I’ve been doing this for forty years. That’s my two cents worth.
This may be a question of what your marketing plans are, if any. I’m less interested in speed and repeatability than in playing with wood; for me a shaper would be massive overkill.
I did overspend on the table saw, but I wanted a Sawstop … and then got one with a larger top than I’ll ever really need (though I can drop router into the wing, which makes it a touch less impractical)
FYI: Stumpy Nubs has a plan (that you may buy) to make your own domino style mortiser.
Fitz, Wonderful thoughts and advice and it pretty much mirrors my usage of powered tools. I bought a Domino joiner DF 500 when first released by Festool, and it is a great tool, easy to use and very accurate. So my Benchtop mortiser is never used. There is now a second larger Domino version now, DF700, for big tenon joinery, but it is pricey and as yet I have no need for one. Keep up those great blogs. Thanks.
I still haven’t gotten that book. Really should.
Suggestion to on that topic: how about a suggested priority list for books, yours and others’? I admit that I buy woodworking books like I buy tools — faster than I actually get around to using them — but that isn’t going to change and if I’m building a library it ought to be a good one.
Speaking of which, I still need to build the formal shelving for my library to replace the 4′-square1x12s-and-plywood-and-shelf-brackets units I threw together for my second apartment. They’ve been rock-solid all these years, but stylish they ain’t. And since they were assembled dry with screws, they can be recycled right into other projects. Current thought for the replacements remains some flavor of modular, possibly with at least some campaign-ish stylistic touches. Plus one unit that only looks modular, since I promised myself a secret door.
This list needs to be updated, but: https://blog.lostartpress.com/2018/07/18/why-these-books-in-what-order/
Do you have a good way to read Hayward’s books? I know this might sound crazy. I have them and tried reading it in straight order but, for example, 10 saw sharpening articles in a row is too much. It’s great info to have all co-located (and I am grateful for this) for when I want to do a specific thing. It just makes reading it feel like a bit of slog and I desperately want to read them cover to cover.
On reading Hayward: how about checking off the articles with pencil in the table of contents as you read them? Jumping around seems the right approach. You just need a way to track your progress.
They are bathroom books (doesn’t everyone read while enthroned?). Start at the beginning of one with a bookmark and a small notepad or slips of paper to mark particularly interesting articles. An article or two per visit and you would be surprised how far you get how fast. I admit to unfair advantage since as a female I sit every time but even so…..
Thanks for the tips. I will try pencil check marks and skipping forward to new topics and then as I make a loop through the books the topic should feel fresh again. Little by little I will make my way through it. I’ve read all of the other LAP books. I do want to read these.
I found it odd that I bought machines in the order of ATC, the thickness planer first (a little before ATC came out(?)) and then the bandsaw much later.
What’s also odd is how I feel about the machines. The bandsaw gives an amount of versatility, subtlety, and manual control that I never imagined from a machine.
The planer, on the other hand, is an obnoxious screaming lunkheaded beast that I tolerate because it saves so much work. In the past, I also disliked that it was such a one-trick pony, but after designing a new kind of planer sled that eliminated any desire I would have ever had for a jointer, I’ve softened my stance somewhat. A two-trick pony is twice as nice?
Another aspect of acquiring power tools if you’re aiming – for whatever reason – for those that are used is opportunity. Several years ago, I mentioned to a friend of mine who was a recently retired carpenter that I was looking for a used bandsaw, and he said that he had one he could part with. (He had just finished building his last house, off-the-grid and just for him and his wife so he didn’t have enough power any longer to run his industrial-strength power tools.) I went over to his place to look at it and discovered a whole garage full of power tools. I ended up with a 14” bandsaw, cabinet table saw with extension, 8” jointer, and 15” planer, all in incredible condition, all for $1300 even though I was happy doing a lot of my shaping and surface prep by hand. When opportunity knocks, consider answering even if it doesn’t fit a preconceived pattern.
Points taken. I guess the difference probably lies in my doing this for a living. I actually have three table saws that are almost constantly running: one Unisaw set up for hardwood, another for laminates (both with granite table extensions and Bissmeyer fences, and a Foley set up for dados, with a custom 64” fence ( allows stops on both ends for stopped dadoes in 24” cabinet panels). I love my hand tools too, and use them whenever I can. But if I had to rely on them to pay the bills, it would get to be a while between paychecks. No, the planer is nice and when I need it necessary, but if I can have a couple hundred board feet surfaced to whatever thickness I need for $30.00, it doesn’t make much sense to spend shop time at $125 / hour doing much of that. Funny too, just got an 80” long-belt sander in here. Should have bought that along time ago!
Nice article. Use power, finish by hand.Unless people collect your work. Then they will pay you to fool around.
I liked your selection. I work on boats where we the square is thrown away. So Bandsaw is king…
Thanks. The ATC is a fantastic book. I’ve read it a few times and am due to give it another reading.
I started woodworking in 2015 with hand tools. Though I could debate the order (and likely loose), I do agree on the top three tools.
I have a table top mortiser and like it; it got purchased first as I had a lot of mortises to cut on a project and I lacked the confidence to do them by hand. Over the last six months, I’ve gotten better and more confident at chopping my own mortises by hand but much past four I start to loose interest in doing them.
I’ve been saving for a bandsaw and dust collector. In a perfect world I would have gotten these first as one can also thickness (resaw) with a bandsaw. I agree 100% that thicknessing by hand quickly looses its luster. I have some pieces I’ve built that have some components thick than ideal (e.g. 5/8″ would have looked better than 7/8″) because I was too lazy to thickness by hand.
I will likely also get the Dewalt 735 planer with a Shelix head in it. Not sure if I will need the planer but I am almost certain I will end up owning it. It’s more noisy and disruptive that I’d care. Ever since I was a kid, I hated loud jarring sounds.
Only other tool I’d like to have is a table top drill press and a Tormex (don’t mind sharpening by hand BUT try to create an 8″ camber by hand; it can be done but it’s not fun). As for a jointer, not all that excited about one as I could rig up the planer with a sled to joint if I had a board I didn’t want to do by hand. A compromise might be to get an electric hand held planer should I ever “need” one.
If the goal is to cut the time and tedium on re-profiling steel with the Tormek, I think a slow/variable speed grinder with CBN wheels is worth considering. They’re loads faster and even with all the jigs you could want, you’re probably in for less than the Tormek, and more versatile to boot.
Hi Keith, I might go that direction.
I borrowed a tormek from a friend to regrind bevels. Boy that was a mistake. it was ok on the 1/4” o1 chisel. But everything else took forever. I think I averaged over an hour (maybe 2) per blade on a wide variety of chisels and plane irons. In the end it was no faster than using my 300grit diamond plate by hand. A couple months later I found a 1980s vintage jet 6” grinder at an estate sale. Can’t remember if I paid $15 or $25 for it. I would gladly shell out the full $200-$300 for a brand new one if I could get my time back on the Tormek. It’s a fantastic machine, but a grinder it ain’t. It’s for honing only.
Thanks Jesse. I didn’t realize it would be that slow. What I’ve been doing is using a 4 foot long board that has 60 or 80 grit adhesive sandpaper on it if I need to hog off material. The more comments I see on a Tormek being slow makes me lean more towards a traditional grinder with a CBN wheel.
Sometime around the mid point of the last century, when I was in grades 6, 7 and 8, we had to attend classes in “Manual Arts”. I’m pretty sure that this was done in order to give our regular teachers some respite from trying to control 11, 12 and 13-year-old miniature criminals. These were carpentry classes. The teacher, Mr Byles, taught us how to use hand tools. There were no power tools, which meant that we all finished grade 8 with all our original fingers, ears, noses and eyes. Mr Byles’ expressed belief was tha, if we learned how to make a proper dovetail, mortise or tennon, we could always make one in later life, even using power tools. He was, of course, correct. I have a number of power tools, which I use. I’ve also got a large number of hand tools. I’ve never severed an artery with a hand tool, although I have done that with a circular saw. This endeth the lesson.
I have been known to pay $500 for a much used machine, such as a table saw, and have driven 8 hours one way to pick one up – because I knew how it was built (like a tank) and that it cost someone three times that much years before when it was new. And I am still using them years later after purchasing them.
Wonderful article and great advice.
in regards to picking the machinery I felt like you were preaching to the choir – a planer is the only major tool I own
that being said I think the top 3 should machines for hand tool woodworkers should include a bench grinder. I sharpen and shape the tools by hand and am counting the days until I can get a decent slow speed grinder setup
Ranking the bandsaw so high is interesting. I had assumed the table saw was the one traditionally held in high regard.
I’m currently unemployed so I can spend a lot more time thinking about buying things than actually buying things. I had finally convinced myself to get a table saw when I have income, but maybe a bandsaw is in my future.
I have a hand-me-down table saw which I now use almost exclusively for crosscutting and case mitering. I use my bandsaw for everything else and do without a planer in favor of a LN #62. I don’t make a lot of large furniture so hand planing doesn’t create an issue with scale of work. I do have a nice 14″ bandsaw and that helps but I rip with it, break down lumber with it, resaw and cut curves. Some days I think I’ll build a nice sled for it for cross cutting and get rid of the table saw, but case miters on the table saw make more sense.
I guess i’m a bandsaw partisan, but for the work I do, a bandsaw is the primary power tool and it’s better than a table saw in a small shop.