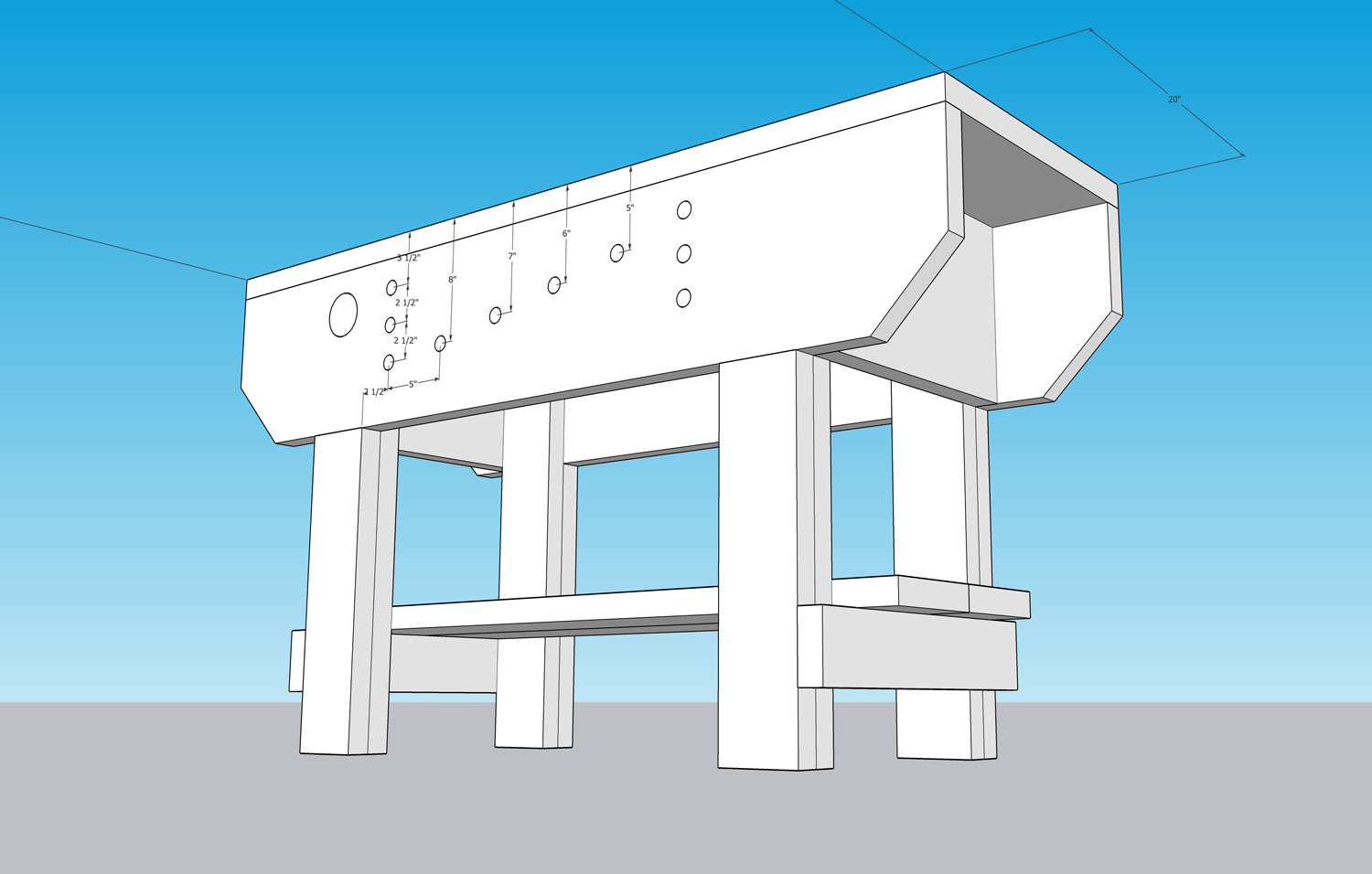
Today we started work on the workbench for the Cincinnati Museum Center’s new permanent exhibit, “Made in Cincinnati.” Our workbench is supposed to represent what woodworker Henry Boyd (1802-1886) might have used at his furniture business.
I decided to design a British-style joiner’s bench for the exhibit. It was tempting to build a German-style workbench, but Cincinnati’s German population was just beginning to blossom when Boyd was a young man. (In 1830, only 5 percent of the city’s population had German blood.)
So a British bench seemed more likely, based on the population at the time and the fact that this simple bench style was ubiquitous in 19th-century America. Also, Cincinnati was still a new city when Boyd was alive, so a bench that could be made quickly without a lot of material (or machinery, which entered Cincinnati in a big way circa 1850) made sense.
I know the bench above looks small. That’s because the floor space allotted to the workbench exhibit is only 20” x 60”. So I had to design the bench to fit the space and make it look realistic.
We’re building this bench with yellow pine, which was widely available in Cincinnati in the 19th century – it’s in all our old houses. We are building the bench using hide glue and cut nails – plus a linseed oil finish. In addition to the planing stop and holdfast holes, I’ll add a face vise powered by a wooden screw.
After we finish the bench, the museum’s staff will antique the piece so it looks shop-worn.
You can download my SketchUp drawing of the bench here. It requires five 10′-long 2x12s.
If you’d like to help us build Boyd’s bench, get in your car next Saturday (March 26) and join us at our Open Day in Covington, Ky. We’ll have the storefront open to the public from 10 a.m. to 5 p.m., selling Lost Art Press books, Crucible tools and apparel. We’ll also assemble Boyd’s bench in the storefront. We welcome any and all gawkers and helpers.
The storefront is located at 837 Willard St., Covington, KY 41011. There is plenty of street parking on Willard and 9th streets.
— Christopher Schwarz
P.S. Donating my time and money to this important exhibit is possible only because we hired Megan Fitzpatrick on full time. Without her help carrying our editorial load, I would have had to pass on this opportunity. And the reason we could hire Megan is because of your support. I’m not asking you to buy more stuff. I’m just saying thanks and letting you know that your support makes a difference.
How will antiquing be done? will they set kids on the bench? That seems to works pretty fast.
ROFL using kids for the antiquing processs… so true! i built my 4 and 5 year old a bench with a 3″ thick laminated mdf top. the bench is now full of nails, covered in thick fist size globs of glue, has large gashes from saw and file work…. oh and my 5 year old recently discovered that the pointy end of a claw hammer makes a pretty good substitute for a mortise chisel. nevermind all the scrap boards i give em. they want to work “on” their bench.
Sweet! I wish I could be there.
Me too! It looks a lot like (maybe a bit simpler, I use half lap dovetails throughout, yours seems nailed only) my work bench, or the one I built for the kids, and the bench I’m sitting on during meals. Or the table for the band saw…oh, or the bench from the ADB 🙂
Have fun! Wish I could be there to join in.
I had to measure, but my Wee Roubot that’s in an upstairs bedroom is 20×52. It actually a good size for the vast majority of my hand work. Sure, the extra length of my basement workbench is sometimes useful, but I could make the small bench work for everything if I needed it to.
Cool. Any photos of the actual bench? Any chance these drawings could be made available? Been wanting a second smaller bench in my garage and I like the looks of this. Happy to support LAP by the way, you publish great books which makes it easy.
Hi Joe,
Are you asking for photos of Boyd’s historical bench? There aren’t any. After we build this bench, we’ll post photos of the finished article. As to plans, I have uploaded my SketchUp model to the 3D warehouse. You can download it here:
app.sketchup.com/app?3dwid=ff4f8aa6-d512-42a2-b698-49aef55f195b
Thank you for making the model available. Look forward to seeing the photos of the bench.
I don’t suppose that you could point to the .SKP file directly. I only have Sketchup2017 and the link above does not let me do anything to it, including downloading it.
https://3dwarehouse.sketchup.com/model/ff4f8aa6-d512-42a2-b698-49aef55f195b/Henry-Boyds-British-style-Workbench
Thanks Chris. It was the dimensions of this bench and the sketch up link was helpful. Looking forward to the seeing the build.
All joking aside, it would be interesting if you could document the antiquing process in this blog. That is describe the processes used, as well as some of the finishes, and perhaps a few pictures. Sorry, I’m sure you have all of this unlimited spare time.
If Chris gets a free microsecond or two, he’ll start another business. Probably something like remastering obscure vinyl records that had press runs in the double digits–Lost Press Art.
Rimshot, then I’ll see myself out. 🙂
Hahahahahahashs….
Damn right I would.
They’ll be doing this off-site, so I won’t be able to show it.
However, we have a book in the works on this very subject that will come out later this year: “The Belligerent Finisher” by John Porritt.
OK, I had some beverage come out my nose on that one.
It’s a real book. We are designing it now.
Well, that’s the best title I’ve ever seen.
Totally. I can see me buying it just to have the title visible on the shelf….
Joking aside, it could be really cool, finishing is a dark art to me.
The Woodworker magazine had an article years ago on how UK cabinetmakers used to “age” their newly made replica furniture for the antiques market. They would put the furniture item in a pigsty with lot of piglets. The fumes and muck would quickly colour the wood while the piglets running in and out of the legs would round off the legs and stretchers so they looked age-worn.
That’s a great project. I built a similar one based on your Knockdown Nicholson, it’s a good little bench. Just finishing two “French” workbenches for future students right now, and thanks to your writings, there was no head scratching.
What a great project! How traditional are you planning to be in the construction? Will you start with logs and get the volunteers to improvise a saw pit?
Nope; we’re starting with 2x12s, for which you can blame me – I’m lazy 😉
Also, I am 100% sure that furniture makers at the time in Cincinnati would not have started from the log. There were plenty of sawmills around here
Interesting project and thank you for the Sketchup file. Curious about using holdfasts in the 1-1/2″ benchtop. For many holdfasts I’ve seen described that is either too thin or borderline. Have you had good luck with that thickness?
I’m interested because my workbench is a super-heavy bench that my dad built back in the ’30s out of Douglas Fir 2x6s with beautiful tight, straight grain. You know, just construction grade lumber of the day.
Hi Larry,
If the fit between the benchtop and shaft of the holdfast is tight, then it will work fine. I probably will glue scraps of 2×12 to the underside of the benchtop to beef it up.
Go down one size in the hole. My English bench has a top that started 40mm rough sawn. A holdfast (Gramercy?) for a nominally 19mm hole works OK in an 18mm hole. It’s good in the holes that are actually drilled true.