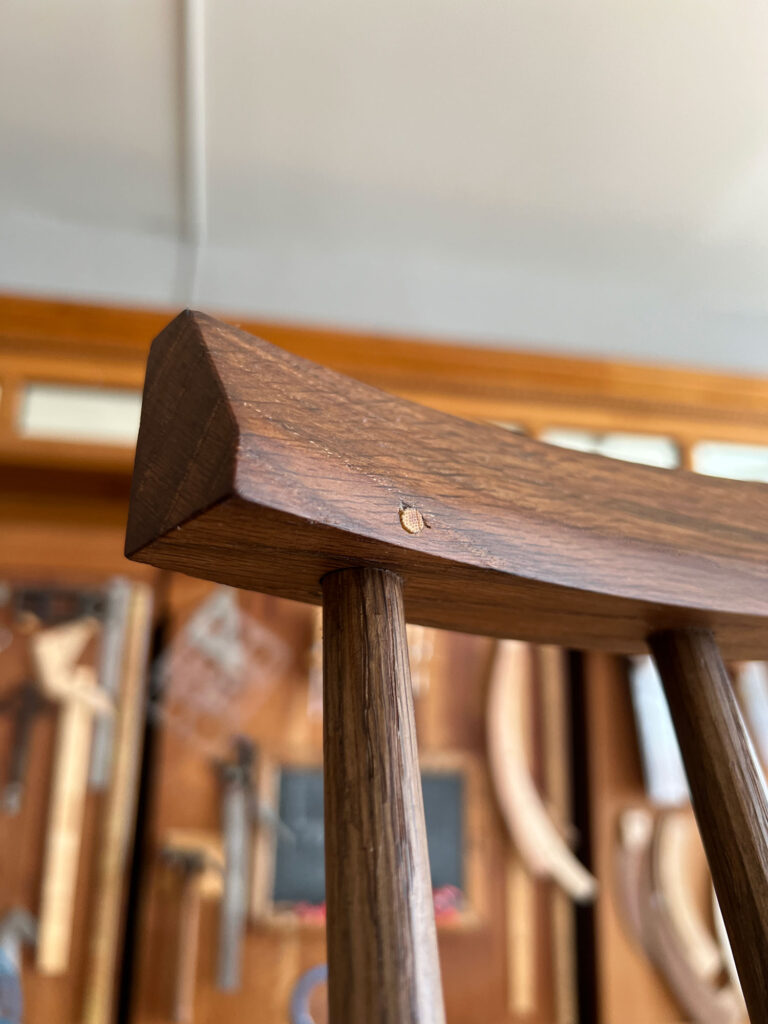
One of my favorite magazine articles by Adam Cherubini was titled: “How to Saw Faster than a Table Saw.” His solution was: Don’t saw. Instead of ripping a board to a particular width, try to work with the boards you have on hand and their existing widths.
This blog entry is somewhat in that vein.
When fitting the comb onto a chair’s back sticks, you have a few choices about how to do it.
- Shave the sticks until you have a perfect 1”-long x 1/2”-diameter tenon on each stick
- Use a tenon cutter (or plug cutter) to size each tenon
- Do nothing to the sticks or their tenons.
I’m talking about No. 3 in this entry. Once while teaching a stick chair class, I realized I had left my 1/2” tenon cutter at home. It was the last day of class, and everyone was behind schedule. There was no time for students to shave their sticks.
Then it hit me: The chair’s combs are secured on the sticks with pegs. So the fit between the mortises and the tenons doesn’t have to be airtight.
Then I knew exactly what to do.
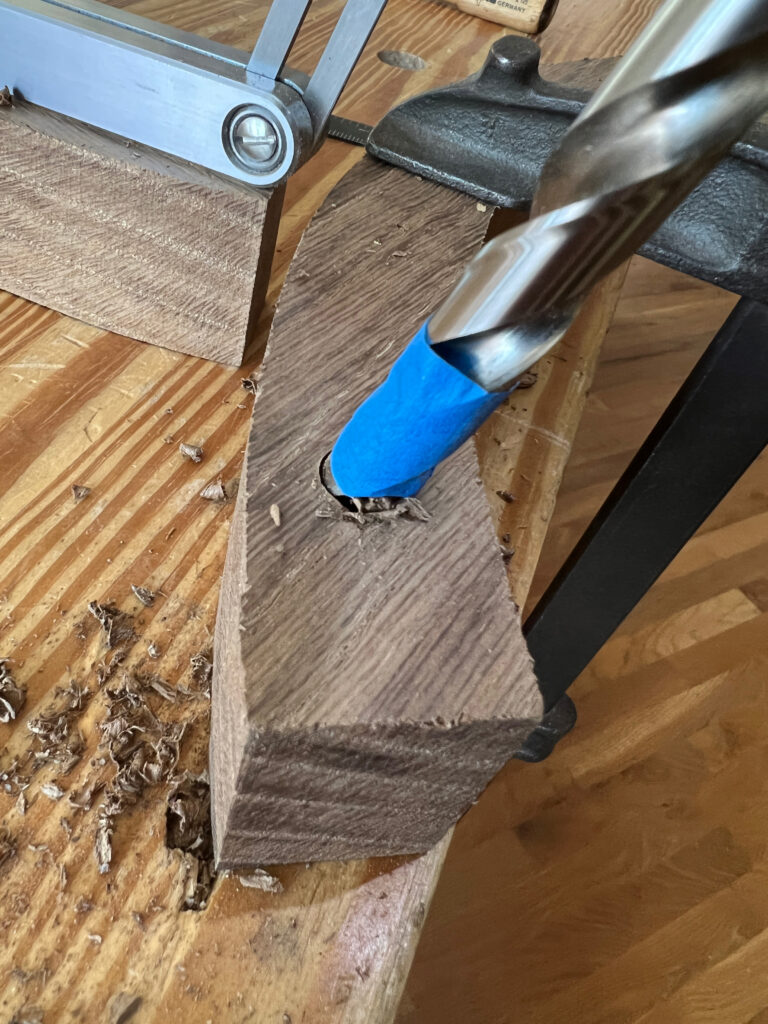
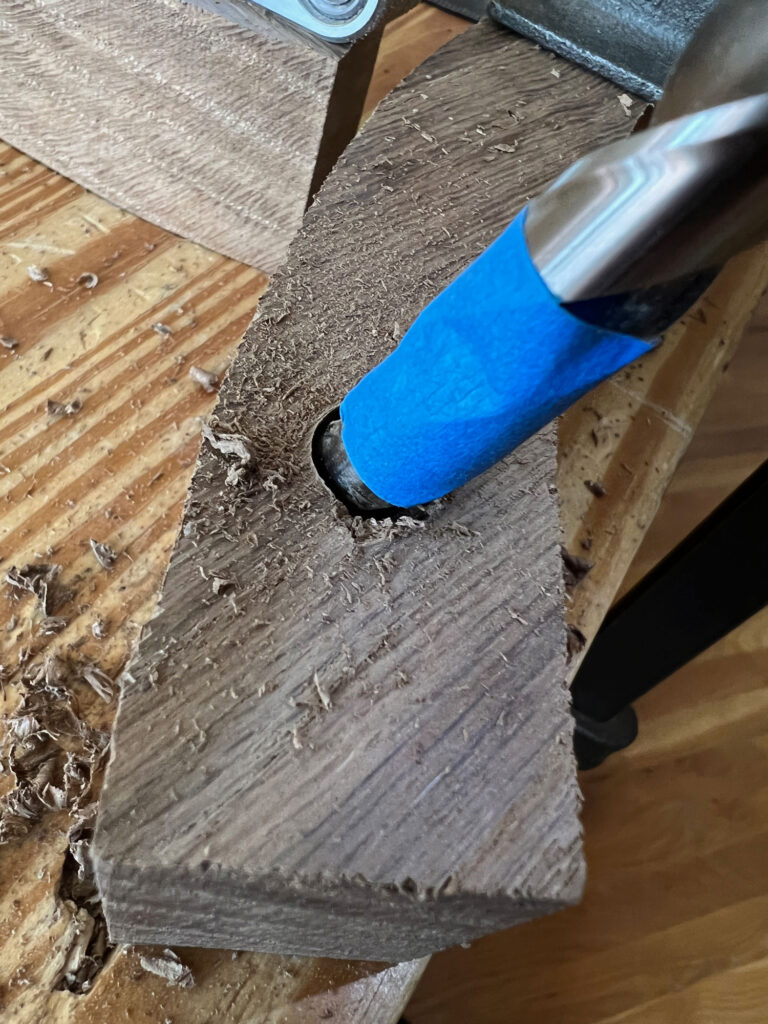
I drilled the 1/2” mortises in the comb then “wallered” them out by rotating the bit around the rim of the mortise while the bit was turning. This created a tapered mortise.
On a chair’s back sticks, the tip is almost always tapered because of the way we shave sticky things.
This little trick worked brilliantly. After a little “wallering,” the combs dropped onto the students’ back sticks with a few mallet taps. A little glue and some pegs secured the comb.
And we all got done in time to go get a beer.
This is how I now fit most of my combs. It’s faster, and it usually looks better, too.
More tips to come.
— Christopher Schwarz
P.S. If you own soft-jaw pliers, you can also compress the tenons a bit and waller the mortise a little less. Your call.
Awesome article as always. Really appreciate all the work.
Fairly new here. Great info…is there a part 1 and part 2 somewhere?
https://blog.lostartpress.com/2022/03/07/chairmaking-on-the-cheaper-part-2-leg-tenons/
https://blog.lostartpress.com/2022/02/24/chairmaking-on-the-cheaper-part-1/
Hey Christopher, I love your use of “wallering”. I am from the Appalachia South in western NC. It is very common to “waller” out all manner of things. Thanks for making me feel at home!
Been following Lost Art from the beginning. LOVE what ya’ll do. Keep it up!
I’ve always been amused that “waller” and “cattywampus” and a few others that show up here were also part of the everyday vocabulary in SW Kansas in the 1970’s and 1980’s too. I need to set up a search to find out of “peawadden” shows up in any blog posts.
Necessity is the mother of invention. The father of invention has left the scene in the dead of night and isn’t likely to return any time soon ; ) God bless our mother! It seems right to me that vernacular furniture forms take advantage of all sorts of “field engineered” workarounds. Folks making their own furniture likely had a basic set of tools and made up for that with a lot of ingenuity. The better creative thinkers came up with solutions like the one you posted here. The not so good ones generally didn’t make stuff that lasted long enough for us to examine and it wound up in the fireplace or the trash heap.
Are your bamboo pegs sustainably sourced from Fitz’s back yard?
Ha ha. (I succeeded in removing it all two summers ago. Finally.)
Ha. You think it’s gone? That’s just what it wants you to think.
The Stick Chair book n the cheap addendum. Can we get a PDF??
Gorgeous wood pictures. The first one is stellar. Also the tearout adds more than most will decipher.
Miss Cherubini… what’s he up to these days?
Any news on The Period Finishers
Manual ?
We haven’t had an update from Don recently; I’ll see what I can find out.
Thanks ! Anxiously waiting…