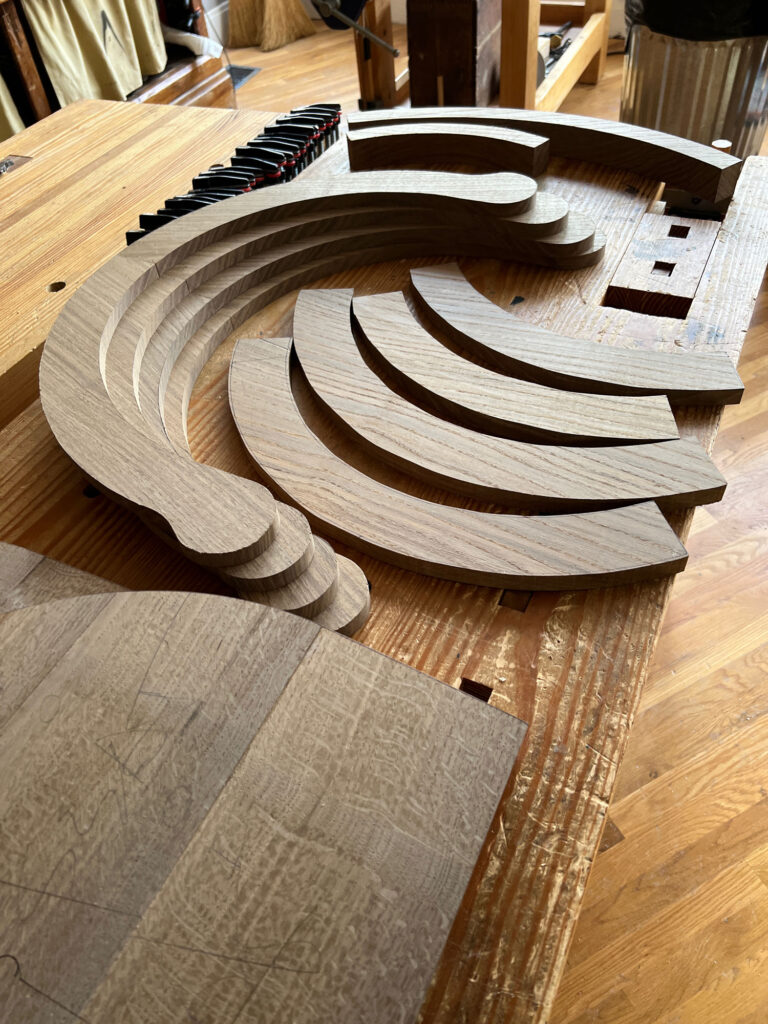
One day in the 1990s, a few of us at Popular Woodworking Magazine were talking to Troy Sexton – one of our contributors – about table saw blades. We asked Troy what blades he liked.
“Thin kerf,” he said. “Always thin kerf.”
One of the other editors scoffed a bit. “Why would you need a thin-kerf blade on your 5hp table saw?”
Troy said: “They save wood. The difference between a 1/8”-wide blade and a 3/32” blade makes all the difference at times.”
I couldn’t agree more. Today I was roughing out the parts for two new chairs from some precious material: bog oak that is between 2,000 and 4,000 years old. I would never buy this material for myself. It’s too rare and unpredictable. But local furniture maker Andy Brownell had some chair-sized scraps from a dining table commission. He generously let me pick through the scraps for pieces that had dead-straight grain and few splits.
I’ve worked with bog oak before. So I was skeptical that I could make a chair from it. But I also trust Andy’s judgment when it comes to wood. So I gathered up enough material to make a chair and headed home.
I started cutting into the oak on Friday and was absolutely amazed. The bog oak I had used years before was lightweight and brash (brittle). That oak was filled with tension, so pieces warped like crazy. And some chisel handles I turned from it broke in short order.
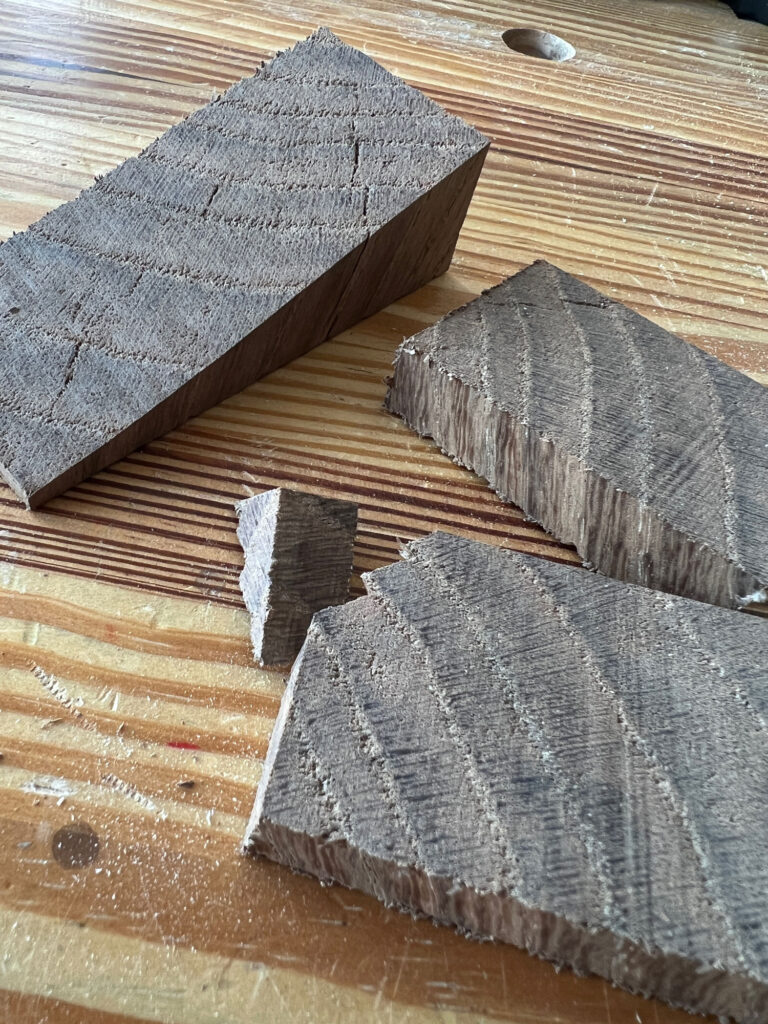
This stuff from Andy is different. It is heavy, stable and incredibly strong. I made some 3/4” x 3/4” sticks and hit them with a sledgehammer (the “sledgehammer test” in “The Stick Chair Book”). The sticks just bounced, as I would expect from straight oak that was cut last year.
Why the difference between this bog oak and the brittle stuff from a decade ago? I can’t say exactly. I am sure that one difference is in how quickly the two oaks grew. The bog oak from 10 years ago was very slow-growth stuff. So there were tons of pores. This new bog oak grew incredibly fast. Some of the growth rings were 1/4” to 3/8” apart. Fast-growing oak is much stronger than slow-growing oak.
The difference might also have been how the material was dried, handled and processed. I have no idea how the bog oak from a decade ago had been dried. But the new stuff came from M. Bohlke Lumber north of Cincinnati. Bohlke specializes in cutting and drying incredible and difficult woods. The Bohlke facility is nothing short of astonishing.
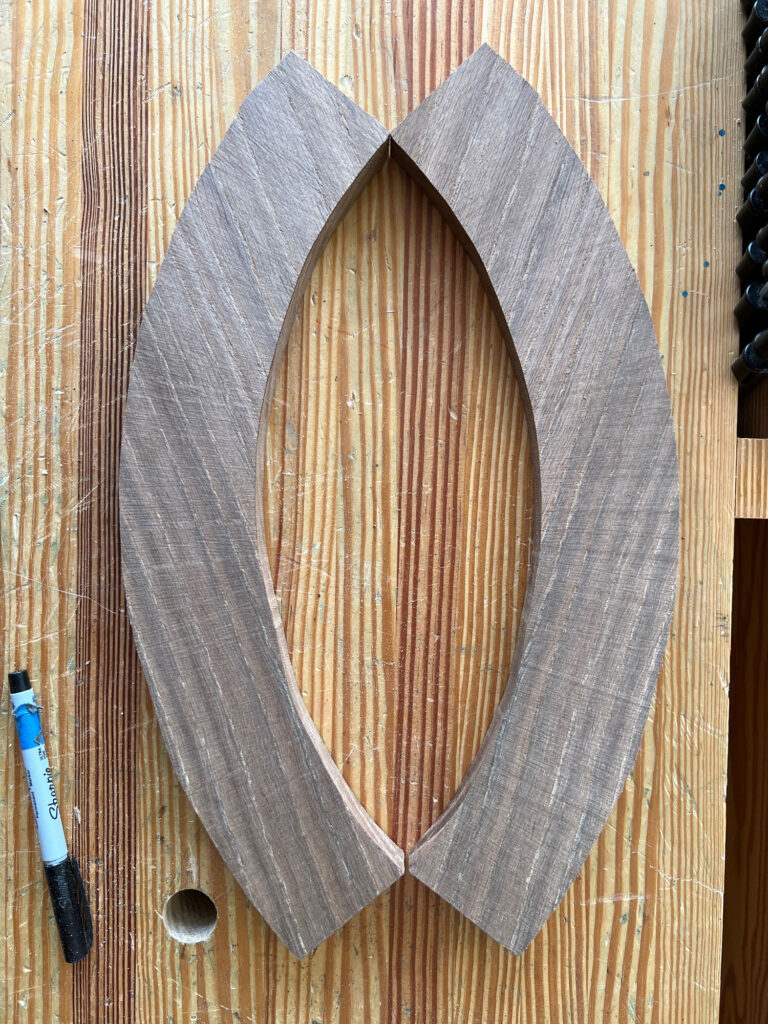
In any case, because of a thin-kerf table saw blade and lots of planning, I was able to squeeze parts for two chairs from the lumber I’d hoped to get one from. I did this by carefully resawing the curved parts from lumber that was 2-1/8” thick in the rough. Even with modern oak from a reputable kiln, resawing can be tricky. Tension in the wood can make the boards warp immediately when sawn through their thickness. And if the wood isn’t completely dry, the boards can curl later on.
This stuff was as stable as resawing MDF.
Even though everything has been going well so far, I know that trouble lies ahead. All this bog oak is from one tree, which is great. But there is an amazing amount of color variance along the widths of the boards. The wood goes from a charcoal-amber to an almost pitch black. Juggling all those colors means I have to finish the parts before assembly to ensure my chairs don’t look like calico quilts.
Luckily, I have about three times as many sticks as I need for two chairs. Also, when building chairs you don’t need all the wood to match exactly. The wood in the horizontal plane (seat and arms) can be a little different than the stuff in the vertical plane (sticks). And the undercarriage (legs and stretchers) can be another shade without looking wrong. Light hits a chair differently than it hits a cabinet.
With all these variables with the material, I decided that the chairs’ designs shouldn’t be an additional one. The two chairs I am building are designs I have built many times, so there won’t be any surprises when it comes to angles or how the chairs’ forms will look.
But I am sure there will be other difficulties ahead I can’t foresee.
— Christopher Schwarz
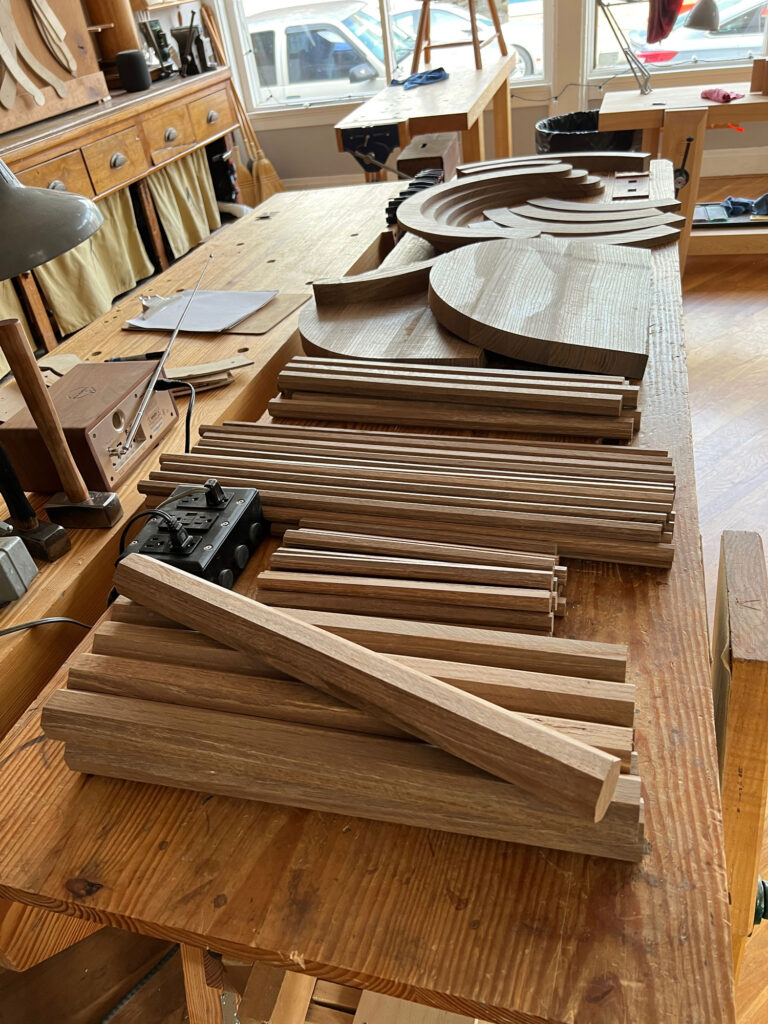
I know nothing about bog oak, so I find this really interesting.
I’d love to hear about how it planes, bores, and saddles.
I sawed som big pieces of iroko. Some of that warped and twisted as it was cut. The bits that distorted were also very tricky to plane with grain running all way. The wood was not kind to the plane blade either.
How cool.
Can friends like Andy be ordered online?
😂
Easy, in the chair that really fits you.
Wow. Will this chair be sold on the blog, or do the rare materials warrant a different destiny?
I’m not sure. First I have to make two chairs that pass muster.
can you tell me what kind of radio that is? Bog oak sure looks a lot like Walnut.
It’s a Sangean WR-11SE.
https://www.sangean.com/products/product.asp?mid=164&cid=4
It’s a good shop radio. Not nearly as nice as the refurbished Tivoli Model One we use upstairs.
https://tivoliaudio.com/products/model-one-refurbished
I believe they’ll be sold on the bog
Sorry. I’ll see myself out.
Nice find. The hues and grain look really good.
Interested to see how you finish these…will you do a little John Porritt alchemy or straight soft wax? Will have some delightful character for sure. Now to find some bog elm!
I probably won’t be experimenting with new finishing techniques either. I’ll save those for the red oak….
Not sure what is wrong with red oak. Am I that far out of the loop
Nothing! I use red oak all the time. It is plentiful and inexpensive. So ideal for experiments.
Awsome Chris, can”t wait to see the chair finished. What ever finish you use will be fantabulis. Hope to see them soon.
“Fast-growing oak is much stronger than slow-growing oak.” I’ve always experienced the opposite. Why is this different?
My experience mimics Peter Follansbee’s:
https://pfollansbee.wordpress.com/2021/01/12/slow-growing-oak-vs-fast-growing-oak/
You’ll also find a lot of scientific papers out there about it.
Can’t wait to see the finished. Chairs.
Chairs are looking great Chris, can’t wait to see them together.
For the readers, my experience working with this bog oak has varied from piece to piece, even though it was all from the same boule. I learned the areas of the wood on the outside of the log (darker charcoal colors), a bit more unstable and prone to movement over long dimensions. So imagine this x 5 table top joints in the dining table I just finished. I had to use three steel stabilizing bars underneath to keep it flat. The locations of those stabilizing bars—which in turn determined the position of the table leaf hardware—also drove the design of the base. As far as color, grain and overall uniqueness, this is one of a kind. The table leaves have the most medullary rays and even appear olive green in the right light. You really have to see it in person to truly appreciate it. For the finish, I used 5 coats of General Finishes Arm-R Seal, satin finish, applied with a poly brush and sanded between coats.