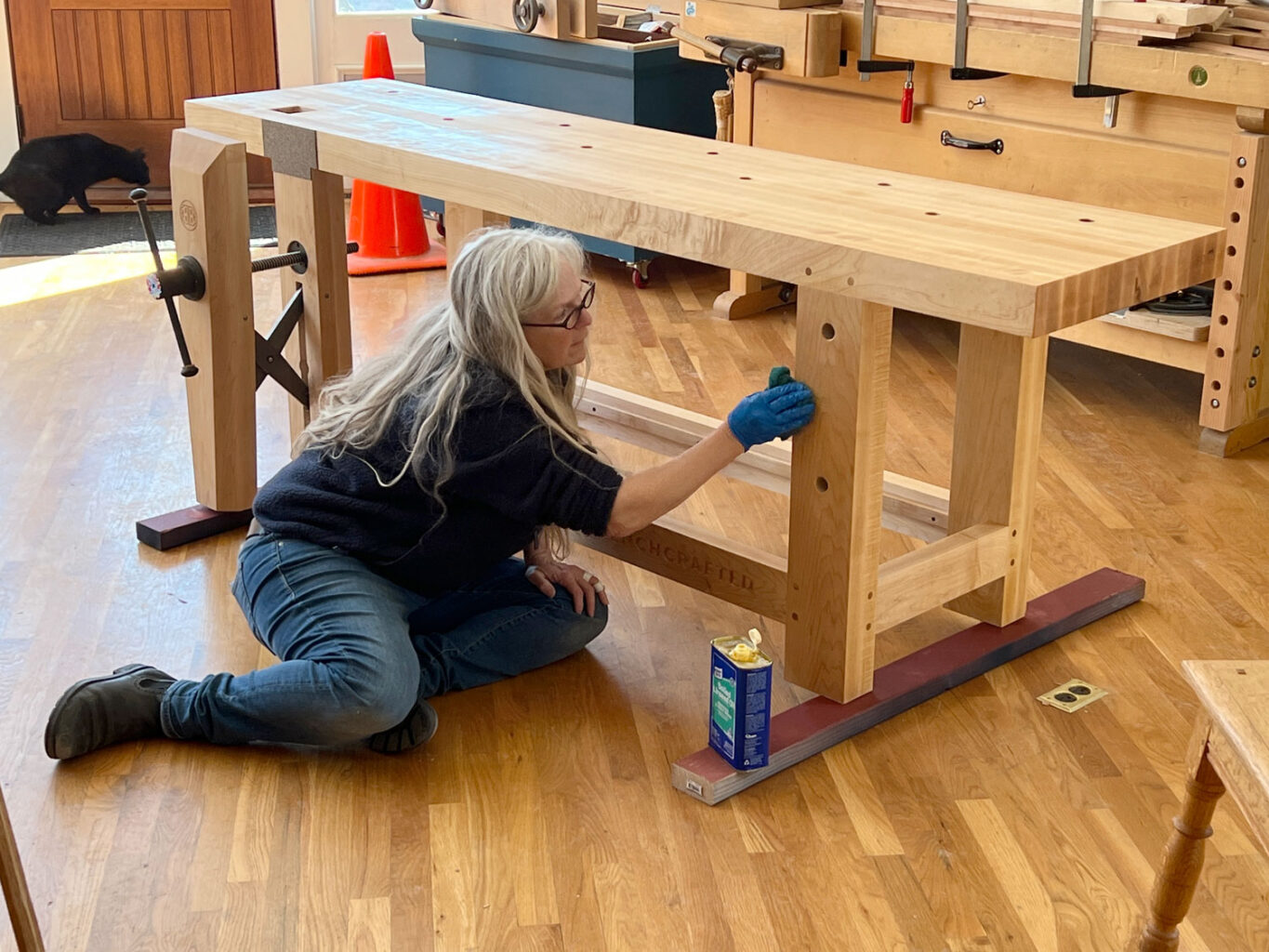
We have just received delivery of a new Benchcrafted Classic Bench in our shop, which replaces Megan Fitzpatrick’s LVL bench in the center of our bench room. Megan and I have been in long-running discussions about building her a new workbench sometime during 2022. But recently we decided to buy (actually, trade) for the Benchcrafted bench. Here’s why.
I’ve built a lot of workbenches since 2000, written five books about workbenches and have been hailed/derided for popularizing the 18th-century French bench for woodworkers who like to use hand tools. And when Megan first approached me about replacing her bench, I said I was happy to help build her a new one based on plans in “The Anarchist’s Workbench” (the book is free to download).
But after looking ahead at our schedule for 2022, my brain began to do the math. I can build a bench in about 40 hours of work. The hardware would be about $400. The wood would be about $500. On the other hand, the Benchcrafted Classic is $2,900. After about 5 seconds of ciphering (and carrying the gazinta), the decision to order the Benchcrafted was obvious.
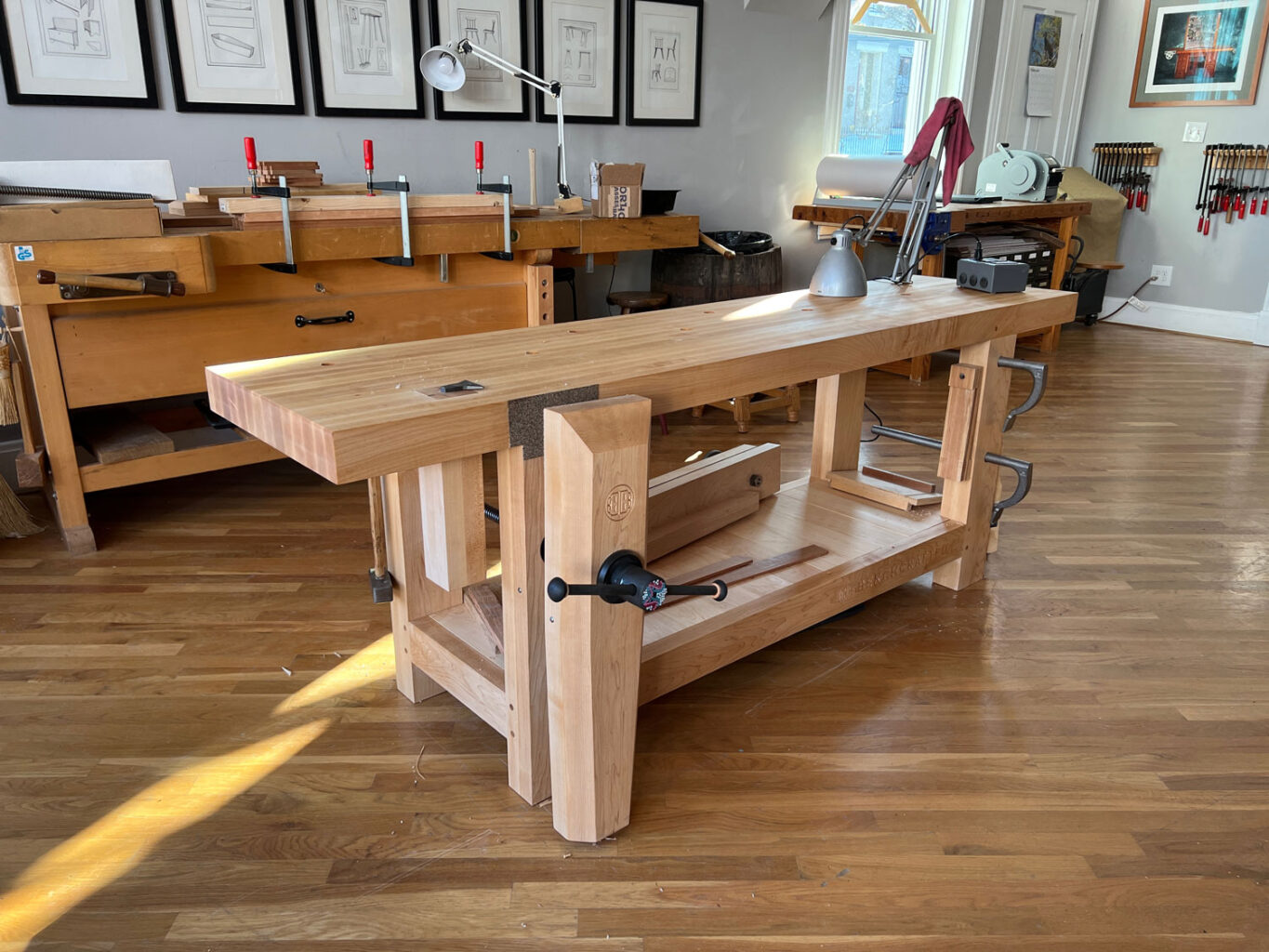
First, the bench completely fulfills my dictum for a good workbench: That you can work on the faces, edges and ends of boards with ease. The Benchcrafted Classic comes with a Crucible holdfast and a planing stop (they added our planing stop by request), and the holdfast pattern is the same pattern that’s on my workbench.
The bench’s form is based on the 18th-century plan. The joints are drawbored. The raw material is hard maple. And the bench weighs plenty for handwork – 300 lbs. The craftsmanship is excellent – as good as any workbench I’ve made. The joints are tight. The vise runs smooth. And the top is flat.
The bench even comes unfinished – a real blessing. Today Megan added a boiled linseed oil finish to the bench, which suits the way we work. A straight oil finish adds a little protection and color, without adding any slipperiness that comes from a wax or varnish.
If you have been reading my books on workbenches, then you know that this Benchcrafted bench pushes all of my buttons. Benchcrafted got it exactly right with no compromises. And they made it for less than I could, at my hourly rate.
So about the payment. I was perfectly happy to pay cash for this bench. But Jameel and FJ said they were interested in trading the bench for one of my stick chairs and a Dutch tool chest made by Megan. So everyone is happy.
Megan has a new workbench with a leg vise that works perfectly. Her LVL workbench is going to live in her basement as “an expansive horizontal storage facility.”* And I’m sure it will be used as a workbench. It’s still a good bench – it has just been eaten up and beaten up by all the workholding experiments I’ve inflicted upon it.
And I have 40 more hours this year that I can use to work on other projects – chairs, refurbishing the bar in our storefront, books and new tools for Crucible.
Now I just need to figure out what to do with our Ulmia workbench, my least favorite bench in the shop. And then the workshop will be complete (cue the laugh track).
— Christopher Schwarz
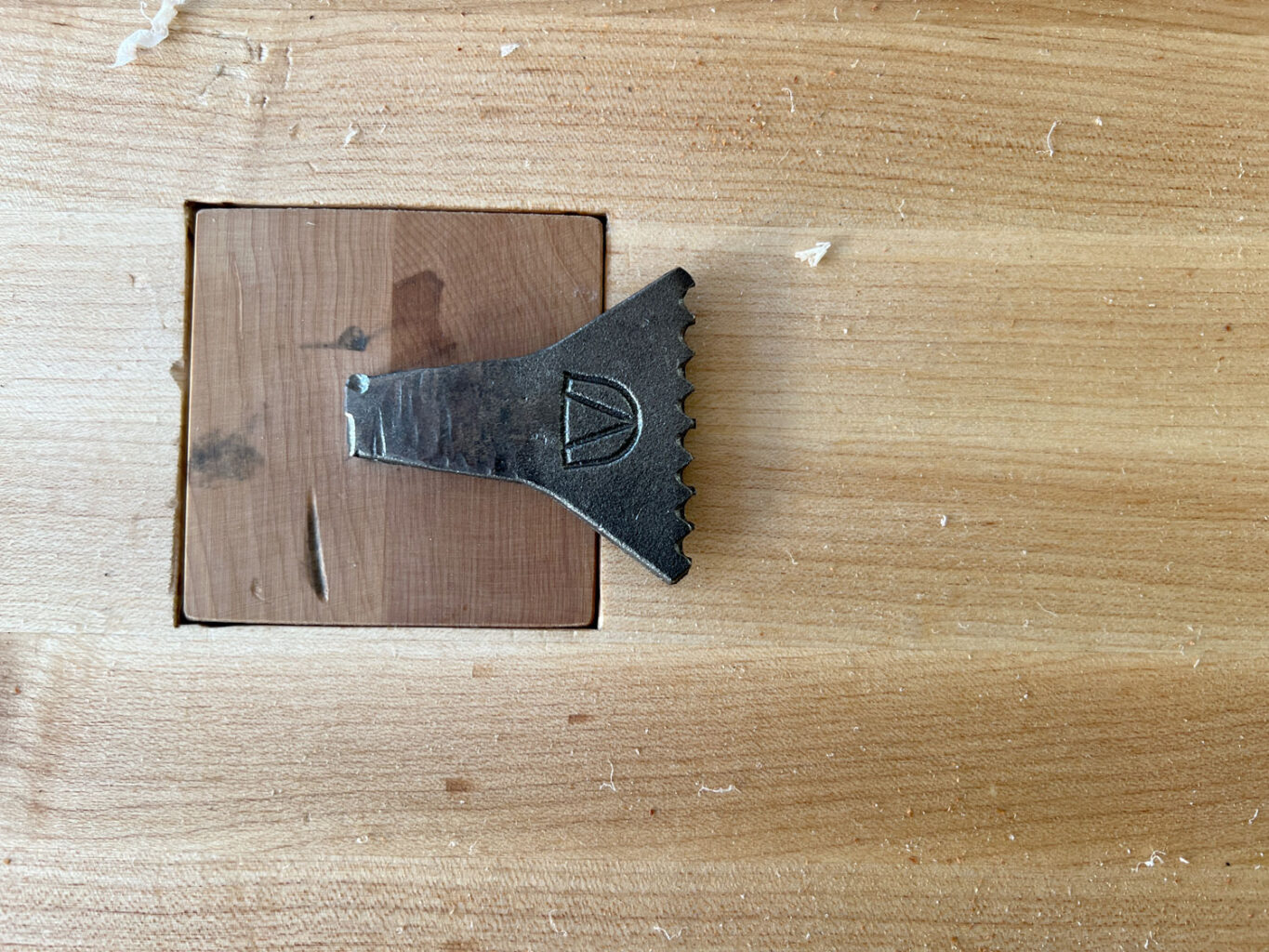
*Megan here. I do still love my LVL bench, and the top remains dead flat after 11-plus years of hard use – an excellent result from our material experiment. But we also built the base out of LVL, and that was less successful. The stuff is made to compress a bit (to handle earthquakes and the like), and compress it did from the force of the leg vise against the top; the top got pushed back from the front of the leg over time – and despite many efforts to fix it, nothing worked for long.
Now, I have a scabbed-on piece of plywood at the top of the leg to bring that front edge flush…but I know it will move again.
It’s not that big a deal to me; I’m used to it and have myriad workarounds – but I don’t like it when students have a less-than-perfect experience with our equipment, hence my desire to build a new bench. But I am delighted to not build one. I have plenty to be going on with, too, and the Benchcrafted Classic is darn close to what I would have built anyway – basically a larger, heavier version of the petite white pine Roubo in my basement shop (which features an OG Benchcrafted Glide vise).
So now I’ll have two good benches in my basement shop – one little, one big. Oh – and one crappy built-in “bench” – I use the term loosely – that was left by a previous owner. It is indeed a horizontal storage facility. The two actual benches, however, will get used for woodworking. In my free time.
— Fitz
I was exposed to the studio version during a class with Chris. A few months later I bought the Classic version and what a joy it is to work on.
The BC hardware is sooooo nice, I spent 30 years without a proper bench mostly because I was too cheap to spend the money but also because I wasn’t building as much furniture as I was cabinets and millwork so the ol’ 4×8 assembly table was all I needed. The leg vice is to die for, I made my split top 96” long. Also a very fair price, i think the maple for mine was $400-$500 but so cool that they would do a trade!
I just wrapped up building a workbench based off the Benchcrafted Classic and Anarchist workbench design (hard maple, half lap joinery, Crucible holdfast / planing stop, etc..). My bench came out great and I’ve been loving every second of it so far. However, even though I appreciate having built it myself, I can confidently say that I never want to go through that again. The Benchcrafted classic benches are a bargain. 8/4 hard maple is no joke, especially if you don’t have a full power-tool workshop at your disposal. I really had no clue what I was getting myself into equipped with a couple bevel-edge Narex chisels and a lump hammer. Congrats on your new bench, you definitely made the right call!
Right? I’ve built 1-1/2…and helped with many more. No need anymore to prove that I can!
Enjoy the new bench Megan. I know what it feels like.
We made a long distance move recently. When ciphering the cost of moving a heavy bench versus the price of SYP in the new location, I decided to leave the old bench behind and build a new one. The ONE thing I did not leave behind was the Benchcrafted criss-cross vise, a perfect bit of machinery. My new Anarchist’s Workbench is almost ready for that great vise.
Nice bench. Too bad your cat photobombed you!
That was no photobomb. I prefer to have a cat in every picture of me.
If you tried to keep them away, they’d still get in there.
Feel free to send me the Ulmia 🙂
We will sell it to you if you pick it up.
Although I live in upstate NY, that would give me a fantastic reason to finally make it to your shop!
$800 and it’s yours. If you want it, let Megan know at fitz@lostartpress.com.
Good Afternoon Chris,
If Dan decides to pass on the workbench. I would be happy to purchase it, and pick it up. I sent an e-mail to Megan at the address indicated.
Thanks,
Jacob
Congratulations on your new bench!
Free time? Hahahahahahahaha…
Another sneaky lesson from the great LAP teachers, lest anyone get too dogmatic about absolutely having to build your own bench, when the authorities on how to build a bench buy one, you think, hey, you can do that? Yep. Love it. John
Megan, the Benchcrafted video shows their plane stop’s profile fitting within the footprint of the wooden block and can get flush with the benchtop. The installed LAP stop projects proud of the wooden block and so can’t get flush. I’m interested because my LAP stop is in the mail and I will be installing it soon. Can I use a bigger block and make my LAP flushable(?). I presume the Covington gang does not think it matters.
Right…we don’t think it matters. BUT, if I did want to recess ours, I wouldn’t use a larger block (the teeth need to extend over the edge of the block for the stop to work); I’d excavate a shallow mortise in the benchtop into which the sticky-outy-bit could recess.
If you take a close look at the Benchcrafted video, Bill (I take you mean the one on the Classic bench page?!), you’ll see that what Megan says is in fact exactly what they have done: mortised a shallow recess into the top in front of the through-mortise for the block, into which recess the protruding part of the metal stop can be, well, recessed. I did the same on my bench, and it works a treat.
And congratulations, Megan, on the new bench! Same as you and several others here have already said, I’m really glad to have built a bench, for the result, for the experience and for all the things that it taught me, but I don’t particularly want to ever do it again.
Just put together a six foot STR base with white oak. I have never tackled a project this involved before. a few small mistakes but I’m happy with the results. What a learning experience. It is the knockdown version because I’m 76 and someday it will need to be moved. I’m ready to start the top. Your book and recommendations have been a great help.
Ray
Would it have killed you to add some blue dye in the BLO?
I love the Classic workbench design and have thought about purchasing one, but I pause at the thought of having to flatten a hard maple top by hand. How would you tackle that? or is it unlikely to be an issue on this bench?
All benchtops move a bit. But unless the top is exposed to extremes of humidity, the movement rarely affects the work. This benctop came in at 8 percent MC, so I seriously doubt we will have to do much of anything with this top for many years.
Benchtops are not granite surface plates. And some high and low spots have zero affect on planing operations. So I wouldn’t worry.
I have a toothing blade in my Lie Nielsen low angle jack. It does a fantastic job of flattening hard or gnarly stock. And it gives a nice little grab for the surface of a workbench. It’s the perfect tool for a job, and I could teach a chimp to use a plane with a toothing blade.
I just built a bench similar to this and that’s exactly how I flattened mine. The toothed blade doesn’t have to be sharpened as much and there is little to no tear-out. Getting the tooth marks out is very quick with a jack plane / smoother if you don’t want them.
I flattened both underside and top side on my hard maple bench top with a #7 jointer, using (almost) only diagonal and traversing (across) strokes, and found it to be rather easier going than I had feared. Because the jointer has only a minimal camber, scalloping on the top was not an issue, while finishing with a couple of sets of traversing strokes with a freshly honed iron and a very light cut left the surface nice and grippy with a lovely sort of satin feel to it rather than the polished feel one would get by planing with the grain.
The only other thing I’d say about it is what goes for basically any flattening operation by hand: don’t work blind! Use winding sticks and sufficiently long true-edges to know where and how the piece is out of whack, work methodically (tell-tale pencil lines are a great help) to unwhack the situation, and check progress frequently.
Now we know Jameel will trade for a bench. I just need to figure out something special I can make. I have it! Tennessee Hot Slaw! About 1000 gallons should be fair.
Did you have this built to a specific height? I know that 34″ would be too high for me.
Don’t you know? All LAP benches are 39″ tall!
Close — 38”. The 39” benches are for punters.
I did. 30″ – it’s so cute 🙂
Love it. It’s great. You’re all great. That cat is great.
Question regarding the BLO – I avoid klean strip and recommend T&T Danish Oil (then meander into complaining about the name overlap with Watco) when it comes up, being under the impression that klean strip has icky additives and T&T is just heat-treated linseed oil.
Am I mistaken and/or over-worried?
I am a recovering Waterlox devotee, doing my best to stick with apply-in-the-nude finishes.
Thanks for everything.
We prefer linseed oil without the heavy metal driers. But this can has been sitting around for years and we are trying to use it up. Using it is better than throwing it away.
Hope this makes sense.
Chris
Having more time than money, I’m going to start building another bench. I’ve already made a smaller Ruobo (6 1/2’x24”x5”) that fit in the previous shop space out of 2×12 SYP. The plans came from your red workbench book. I built a knockdown Nicholson, also from your plans, which I’m not as big a fan of. Nothing against you, it’s just I got spoiled with the ruobo which I prefer. That one will go to the good home of a friend. But I have all the lumber cut to rough length and ripped for a second Ruobo, and it’s stickered and drying in the basement. This one will be much bigger than the first as I’ve moved and the shop space is bigger. So I’ll have 2 Ruobo benches, both with benchcrafted hardware. Pretty excited. Though I also did have to schedule recurring regular chiropractor appointments in preparation. So there’s that. Those are the hidden costs associated with bench building, particularly solo.
Any advice on most cost effective way to ship it home?
Ironically, Popwood just released their top articles of the year list, and the LVL bench is on it. Sure is amusing seeing all the machine use, yellow glue, lag bolts and lack of grey in all parties involved.
That is rather amusing. It really is a good bench! It’s just had too hard of a life, I think, to make it an easy bench for students to use. I still love it!
That bench looks awesome, which prompted the following question: I’m beginning the Anarchist bench and I’ve always planned on the Benchcrafted leg vise. Then I discovered the Hovarter vise. Do you have any experience or input on the hovarter? Thank you in advance.
I have used the Hovarter vises in a couple classes. But I have never installed one. Nor do I have any long-term experience with one. Others might – don’t take my ignorance as a negative.
I built my own with Ash, a great project that ended up with the best tool in my shop. Yes it was not a simple build, especially with the wagon vice, but skills were acquired . I did mine in a split top and that just lets everything fall through to the shelf. Made a strip that is solid to stop that. I leveled mine with a router sled, string and a few boards. Hardly removed any material and use the number 7 to clean it up. Only problem… my dang floor is not level. Enjoy your bench Megan!