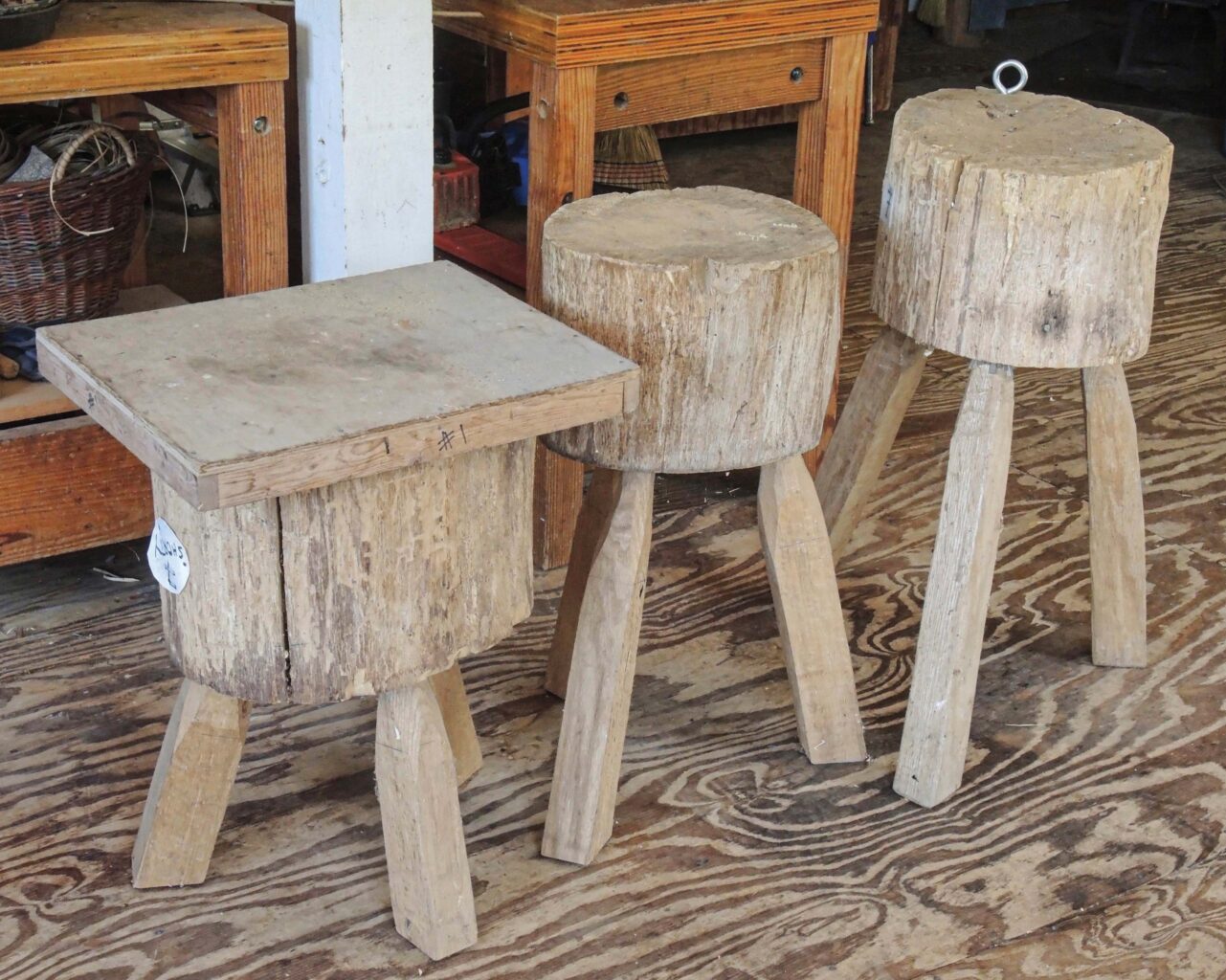
The following is excerpted from “Country Woodcraft: Then and Now,” Drew Langsner’s revised and expanded edition of his 1978 book that helped to spark a movement (still expanding today) of hand-tool woodworkers who make things with mostly green wood. Among many other additions, it includes greatly expanded sections on building shavehorses, carving spoons and making green-wood bowls. One of the key tools for working with green wood is a chopping stump. Below is how Drew makes his.
Chopping stumps may seem so ordinary that even seasoned axe users never give them much thought. They’re just a chunk of a log, cut off more or less square, at whatever height happens to happen.
In Wood-Carving Land, chopping stumps are an honored member of the shop equipment. They are the pre-workbench workbench, especially for axe work.
There are several qualifiers that separate good stumps from the also-ran stumps. Height is the first consideration. Stumps should be tall enough that you don’t need to lean over with bad posture when hewing something small, like a spoon. And low enough that you can get a powerful swing when hewing something larger, as when shaping the exterior of a bowl. This means that you should probably have more than one shop stump.
Chopping stumps shouldn’t wobble – for safety and efficient use of energy. Freshly cut stumps are heavy – they’re about half water – and the surface can become chopped into uselessness quickly. You need to plan ahead.
The chopping surface should be free of abrasive detritus. When a sharp axe chops into a gritty surface, it quickly becomes dull, or even chipped at the cutting edge.
Most stump grit comes from the bottom of someone’s footwear. Almost everyone will rest a foot on a stump of the right height, or climb onto a stump to reach something on a high shelf. Keep your stumps covered with something like a plywood shoebox lid.
Stumps can be most any kind of log, with harder species preferred. Mine are red oak. Drying a stump takes time – years – so you’ll most likely be using your first stump while it’s wet and heavy. If drying happens too quickly the log might split – sometimes so badly that it becomes firewood. You can dry the log stored on its side, or on prop sticks to let air circulate underneath. Do this in a sheltered place, without direct wind or sun exposure.
The chopping surface can be roughened with chain saw scoring grooves, and/or a small and rough chain-sawn hollow. These provide places to hold the work steady for hewing.
I learned about stumps with legs while looking at photos of sabot (wooden shoe) makers’ long-handled block knives. Almost always, the stump is rather short, supported by three stout legs. So smart!
Stumps with legs are not only lighter weight – appreciated when you need to move one – but also more stable with the wide three-point base.
Making a stump with legs
You can go fancy, but I use rough-split legs with very little shaping. Ideally the stump and leg materials are split and left to dry before assembly. This will take more than a year. So, realistically, stumps with legs are often made using wet wood, with the hope that drying will be proportionate. If not, the legs will eventually come loose, but the fix isn’t difficult.
In the rough, the legs can be about 30″ long, and about 3″ across. Make them long, so that you’ll have options when it comes to determining the working height of the stump.
Cylindrical leg tenons are best made on a lathe. Tenon diameter can be 1″ to 1-1/2″, depending on what size auger is available. Tenon length is 2 -1/2″ to 3″. Don’t make the tenons too tight. They should be a tap-in fit. If a lathe isn’t available, follow the steps for carving cylindrical tenons in Chapter 15: Wheelbarrows.
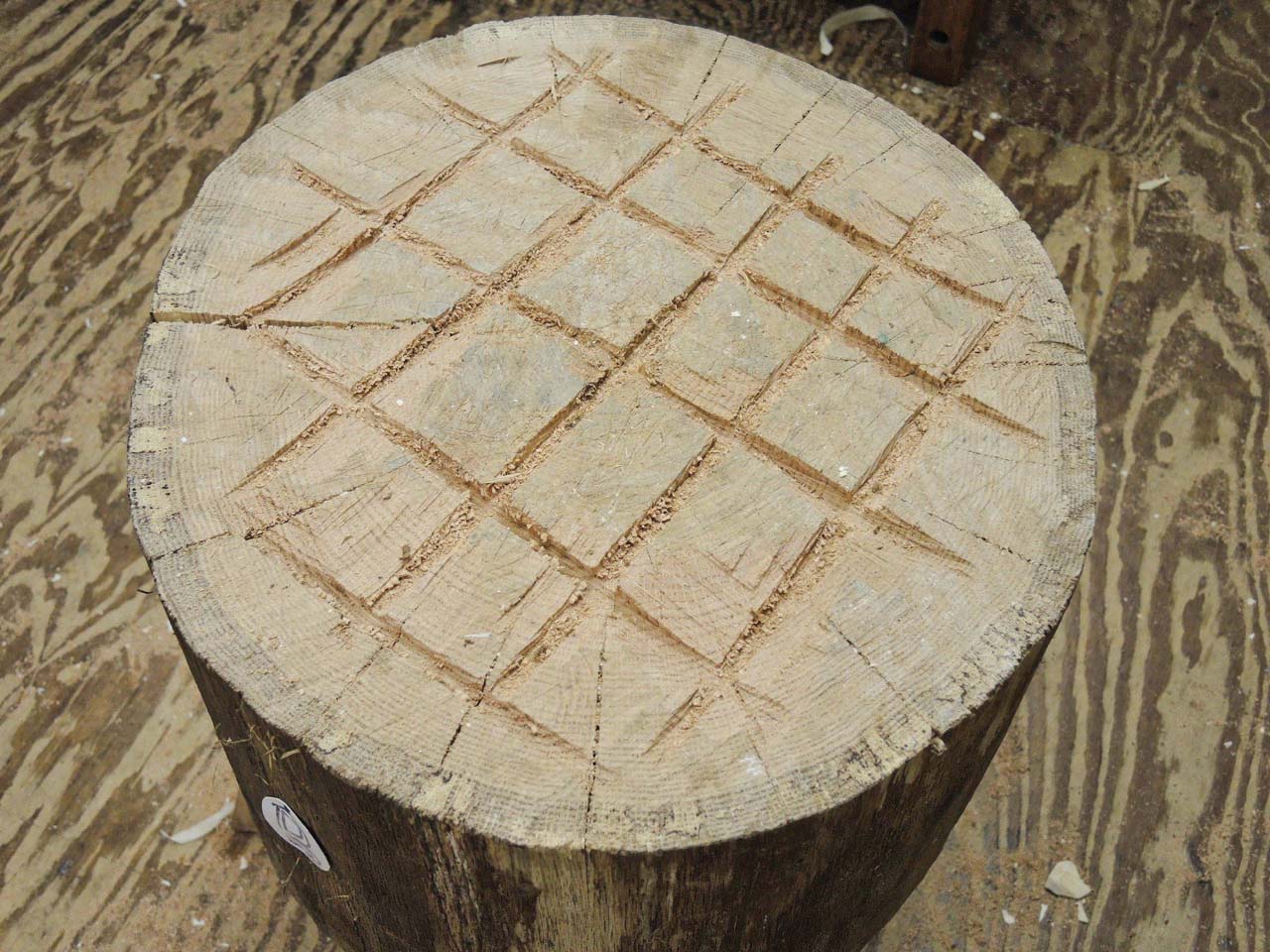
The leg mortises are bored into end-grain, so be ready to do some real work. You can use a bit and brace or an electric drill. The brace should have a 12″ sweep; the electric drill needs a 1/2″ chuck and a side handle to stop it from twisting you around.
Locate three drilling points on the bottom of the stump. They should more-or-less represent an equilateral triangle. Use a crayon or felt marker to draw sighting lines from the drilling locations to a common center point.
Angle the drill 12° to 15° from vertical, facing toward the center point. You may need to remove frass periodically as you drill. This depends on the type of auger.
After the legs are inserted, turn the stump over – so that it’s upright. Don’t worry about how it looks at this stage. Level the top surface by sliding low-angled wedges under two legs.
Decide on the height. Spoon-carving stumps are usually 30″ to 36″. Bowl-hewing stumps might be 26″ to 30″. Subtract the height of the desired stump from the height that it presently is. This is the amount of wood that will be removed from the bottom of the legs.
The next step is scribing from the floor to the cut-off, using the result from the little math exercise. You can do this scribing with a pencil placed on a block of wood of the suitable height. Or use a stout compass. Scribe around each leg.
Use a carpenter’s panel saw to saw off excess length at the scribed lines. To do this, make an effort to secure the leg well so that you can make an accurate, angled saw cut. A bench vise will sometimes work. Or use clamps, or your best friend.
Before starting the kerf, aim the saw so that it’s in alignment with the scribed lines on the other two legs. Because the stump has three legs, you don’t need to be concerned with making super-precise saw cuts.
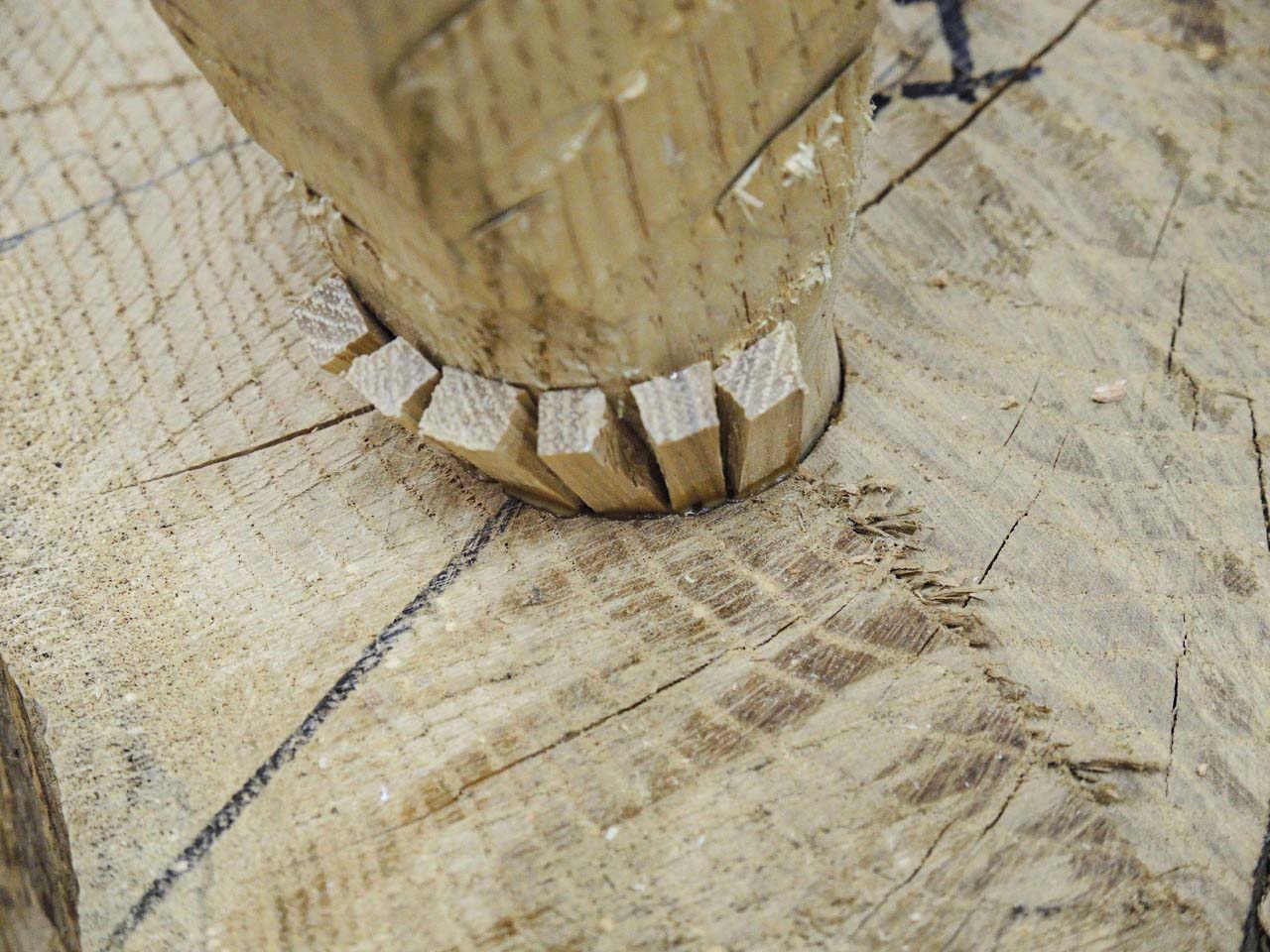
…One or two years later…The leg tenons may shrink more than the stump mortises, causing wobbling or even legs falling loose. If this happens, make up a batch of small wedges and tap them into the loose spaces where the leg tenons enter the bottom of the stump. (This is very funky coopering.) Be sure to have the legs orientated so that the foot trim angle is still flat on the floor. Use a little glue, also.
When you stop hewing, don’t leave the axe with the blade driven into the stump top. The axe could get knocked loose, and become a dangerous flying object. Also, this odious practice chops away the stump surface, destroying your pre-workbench workbench.
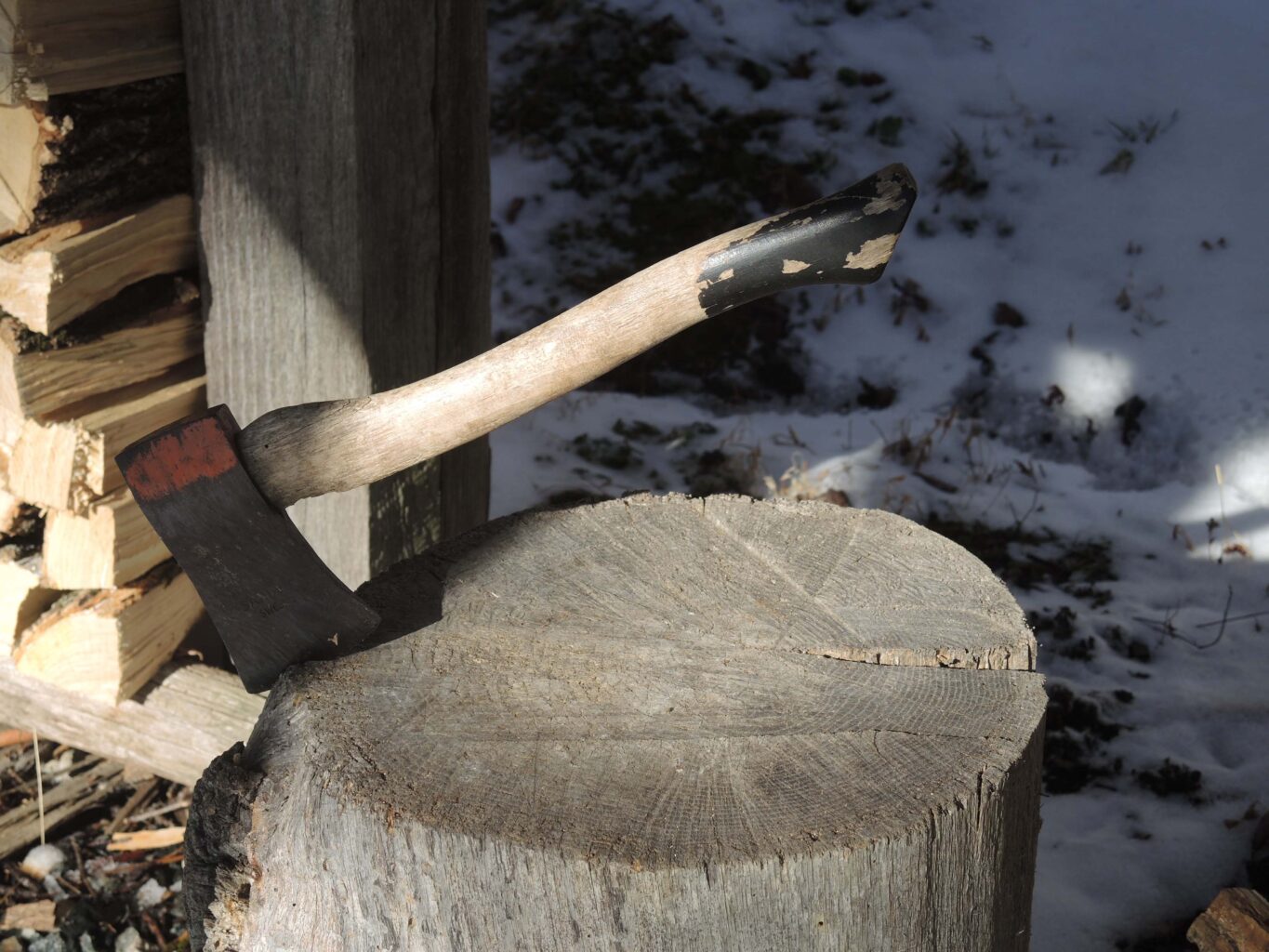
Thank you ! My next book…
Still there is a point I don’t get : he says in the text :”Before starting the kerf….”? I don’t understand. The last time I made a stump, i have issues with the legs getting out cause naturally everything was green… having no experience, I made a kerf on the top of the tenons and inserted a wedge, then drove the legs in. Never had any other issues. Thank you for your explanations !
When sawing the bottom of the legs to length, aim the same toward a neighboring leg.
I like that idea for a a conical tenon going into a thick stump. I am going to try that.
Drew’s Chairmaking book is still one of my favorites.
I reserve my right to drive my carving hatchet into my stump to turn a spoon around in my hands for a second. Not for storing mind you. A wise man once said don’t give much weight to sentences that start with “never…” Maybe that does not apply in this situation though.
When will the Crucible Stump™ be available? And will you do overseas shipping?
A thought… If you have an oven available, you could always try drying the legs before insertion. Then they would expand over time, as the bore shrinks, making everything nice and tight. I recall hearing about someone doing this with Windsor chair legs.
How much of a difference does having end grain vs turning the stump sideways make? Would one last longer?