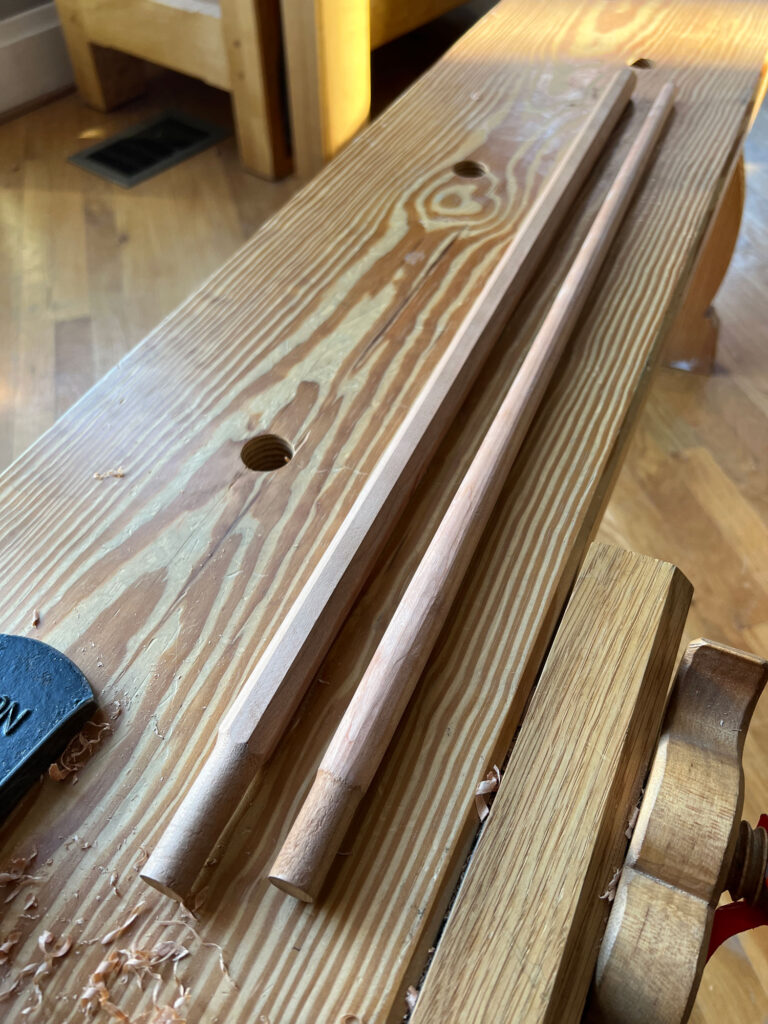
I am always looking for a faster way to make the 26”-long sticks that make up the backrests of my chairs. Making the 12-1/2”-long short sticks is easy. I can bang one out in a minute or two with a block plane.
But the long sticks have a complicated shape. They have a 5/8” tenon at the bottom. Then the stick swells to 3/4” and goes back down to 5/8” along the next 8”. I have to get the swelling exactly right because the stick wedges in a 5/8” mortise in the arm and supports the arm from below. Finally the stick tapers to 1/2” at its tip.
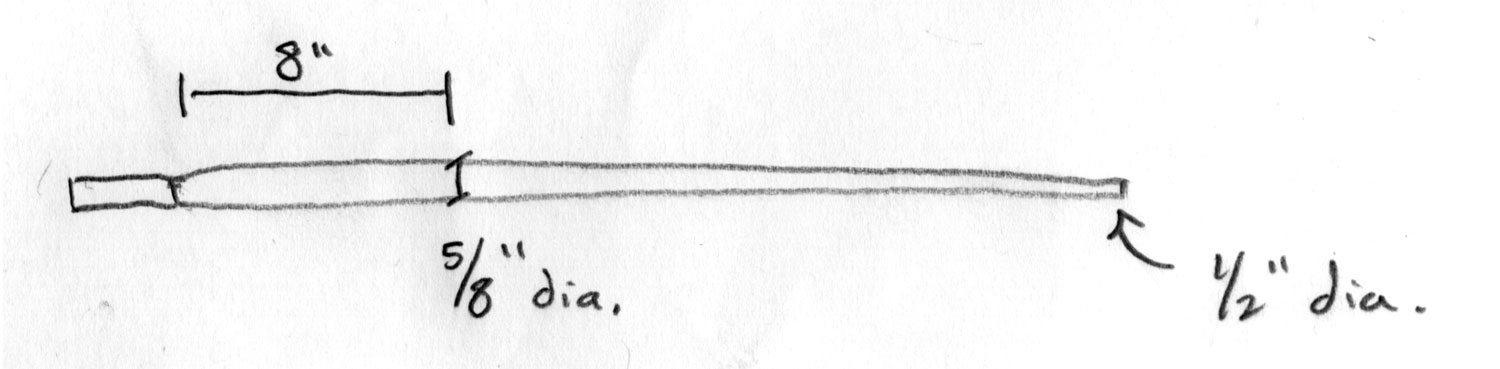
I first learned to make long sticks with a drawknife and shavehorse. Then I was taught to use “trapping planes” on a lathe. Finally, I settled on using a jack plane and block plane. These were tools I already had an intimate relationship with. And I don’t need a shavehorse.
The process to make long sticks that’s outlined in “The Stick Chair Book” is one I have used for many years and is pretty fast. But during the last few months I have been experimenting with different combinations of strokes to see if I can speed the plow. The following process cuts my stick-making time in half. That cuts almost an hour off the time I need to make a chair.
Note that when I make sticks using planes, I skew the planes significantly (about 30°) to speed their cutting action.
Three Stages
As mentioned above, I use a jack plane and block plane to make my long sticks. I place a little stop block in a vise so it is 1/2” above the jaws of the vise. Or I use a planing block (shown in the photos) that is 1/2″ tall. I press the tip of the stick against the stop with one hand and push the plane with the other. The weight of the jack plane keeps it in the cut.
My long sticks begin as 3/4” x 3/4” x 26” octagons of straight hardwood. The work is divided into three stages.
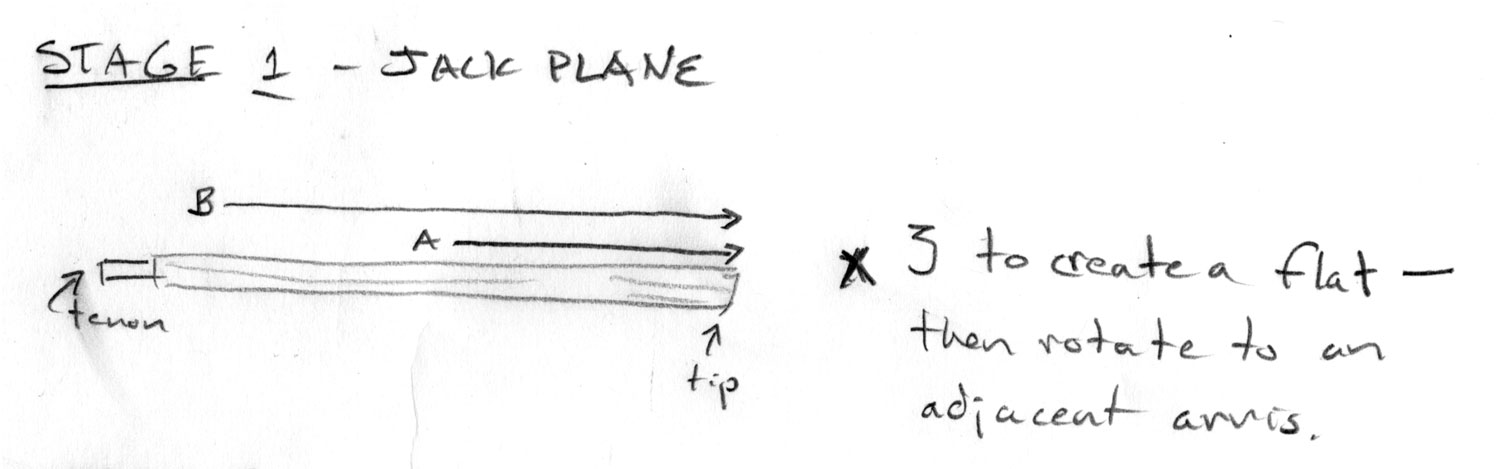
Stage 1
I hold the tenon with one hand and the jack plane with the other. I make two tapering strokes with the jack plane. The first begins about 13” from the tip of the stick. The second begins back at my left hand. I make this pair of strokes three times without rotating the stick. This creates a significant flat on the stick. And by the third set of strokes, the jack is a little difficult to push.
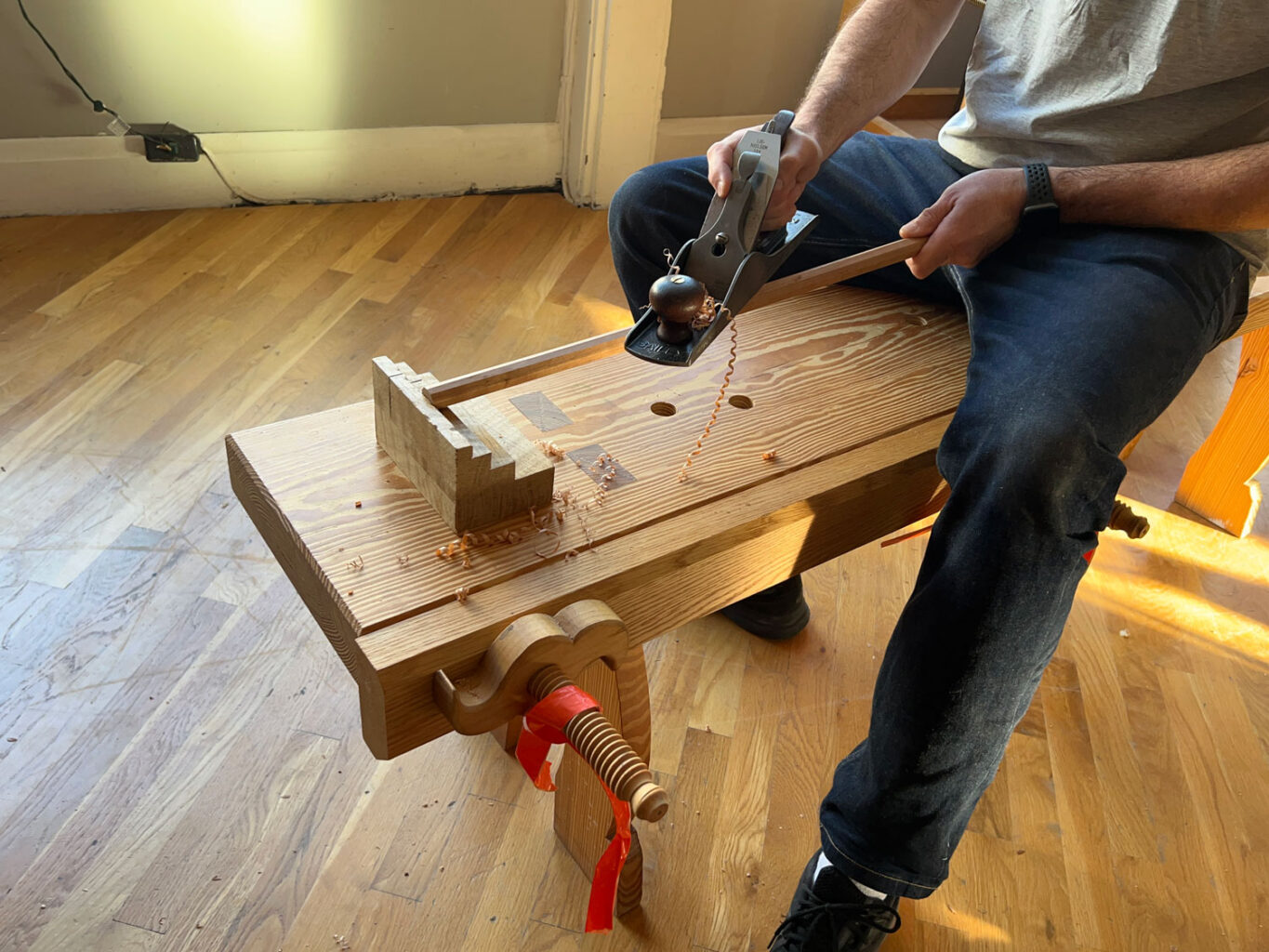
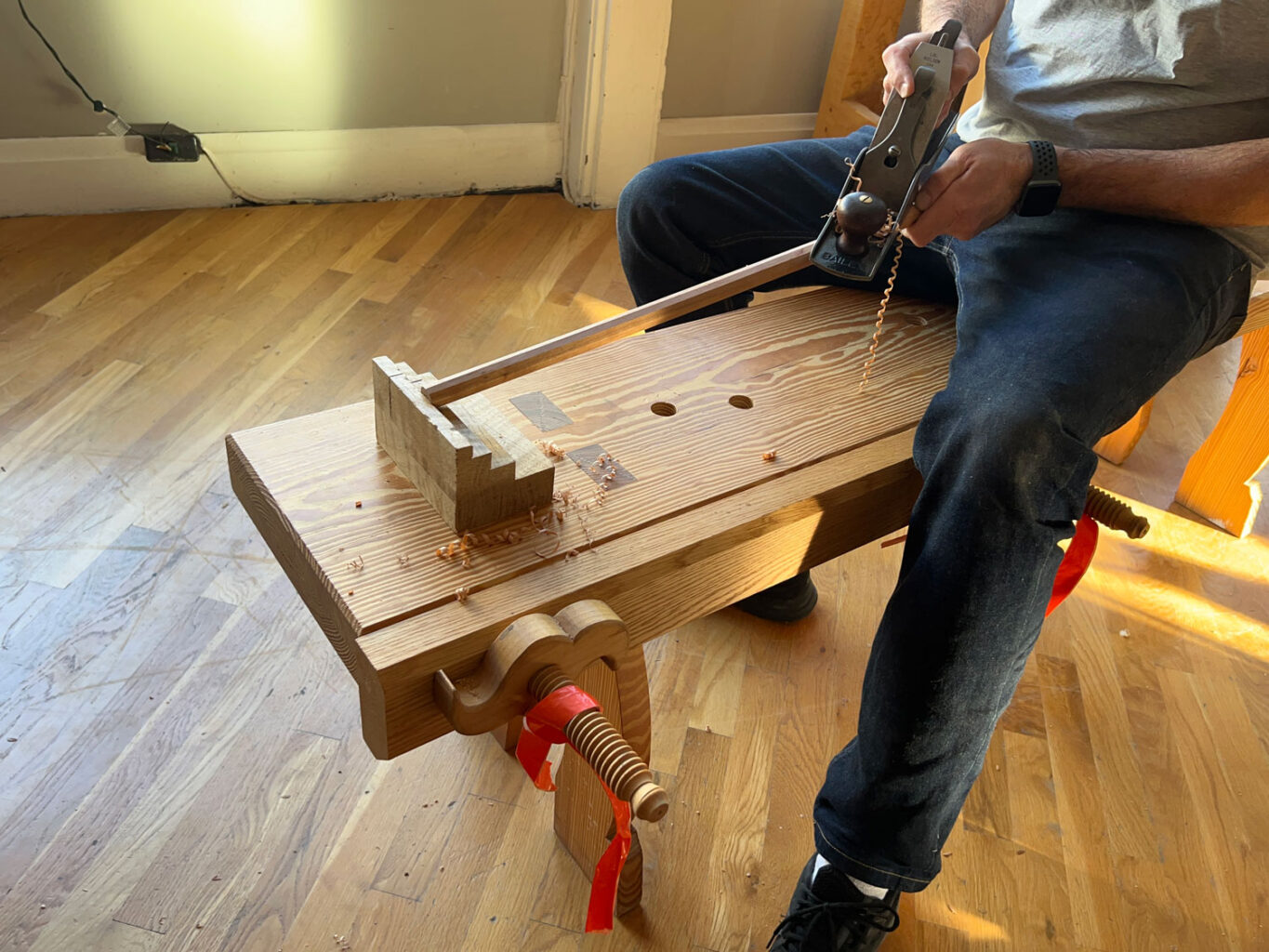
Then I rotate the stick until an arris (aka a corner) is facing up. Then I repeat the above strokes – making the arris into a wide flat. Then I rotate the stick again. I keep stroking and rotating until the stick’s tip is about 5/8” in diameter – or about 1/8” above the 1/2”-tall stop in my vise.
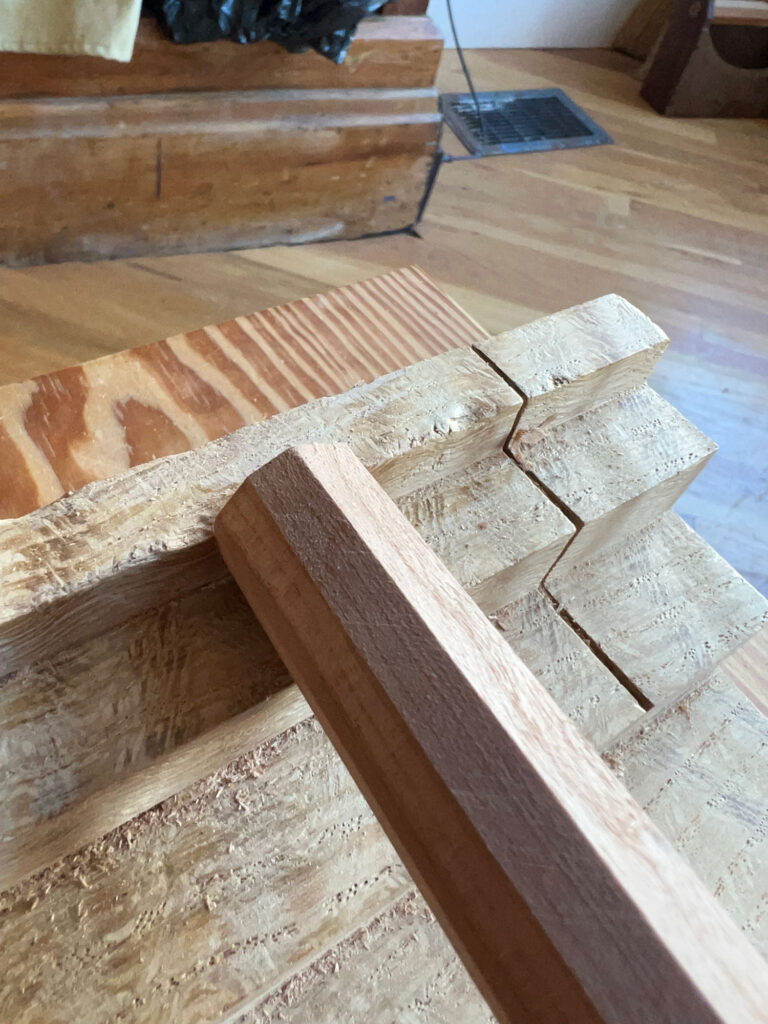
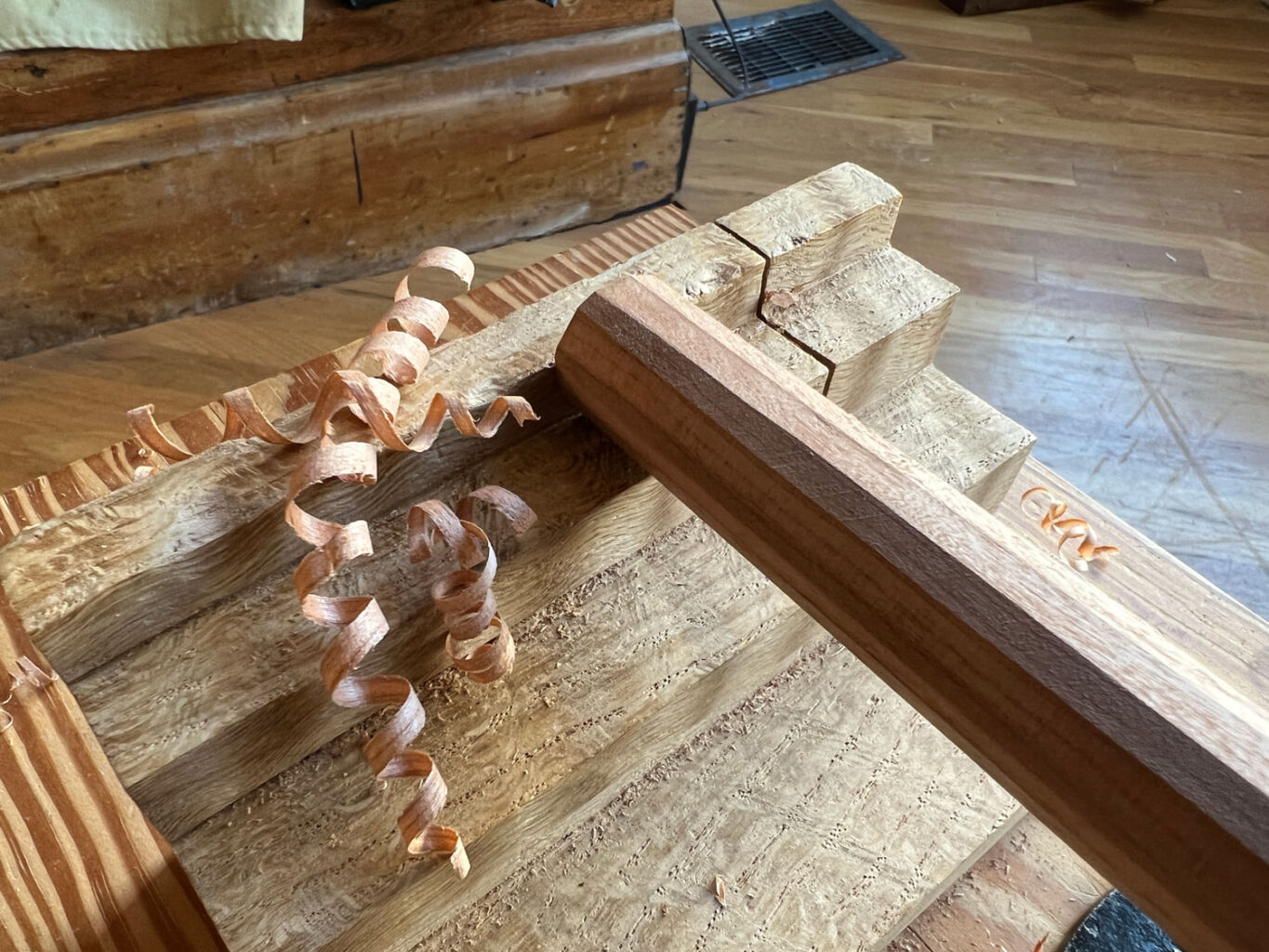
Then I enter Stage 2
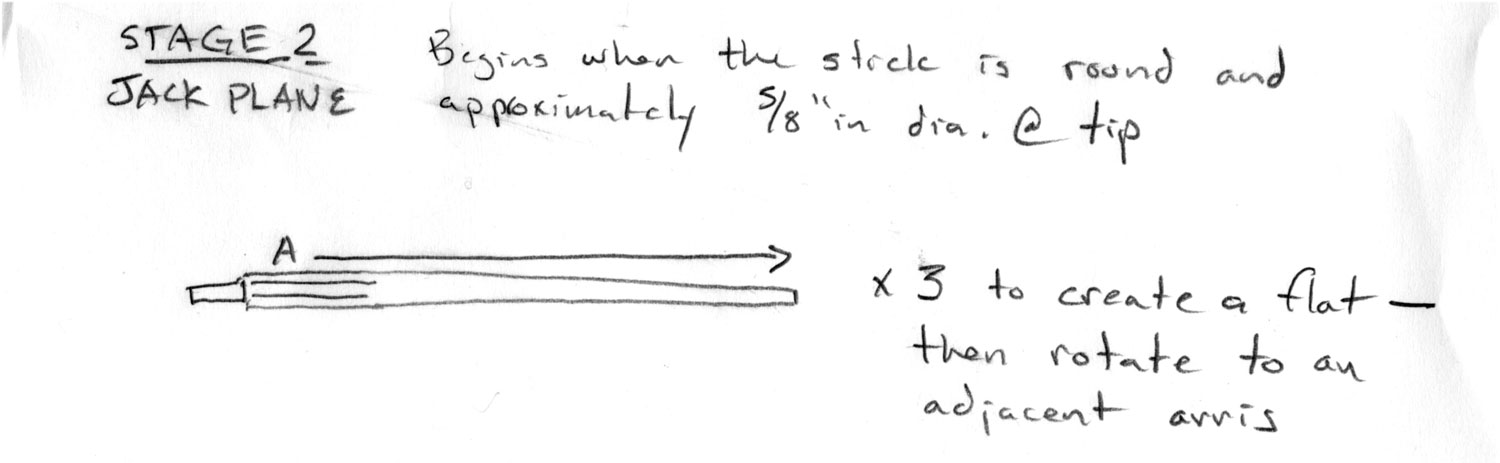
Stage 2
Stage 2 is simple. It is just full-length strokes on the stick – from my hand (still holding the tenon) to the tip. I start on an arris and take three strokes, again making a flat. Then I rotate the stick until an arris faces up. Then three more strokes to flatten it. Rotate. Repeat.
I keep this pattern up until the tip of the stick is 1/2” in diameter and does not stick up above the stop in the vise.
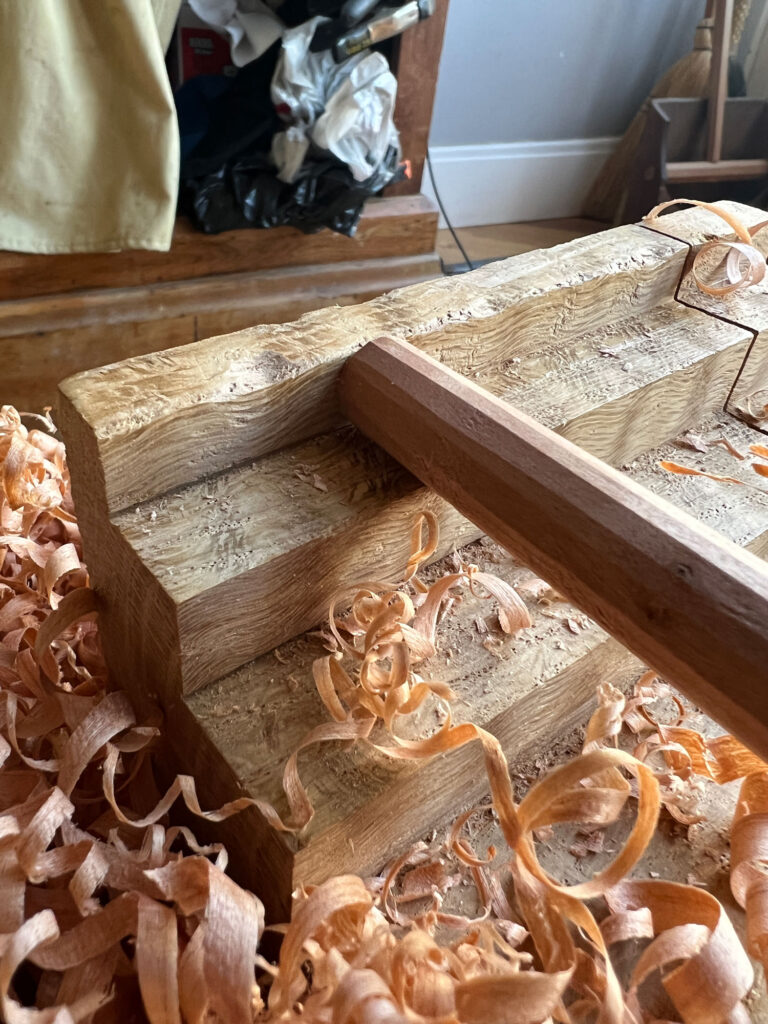
That’s when I enter Stage 3.
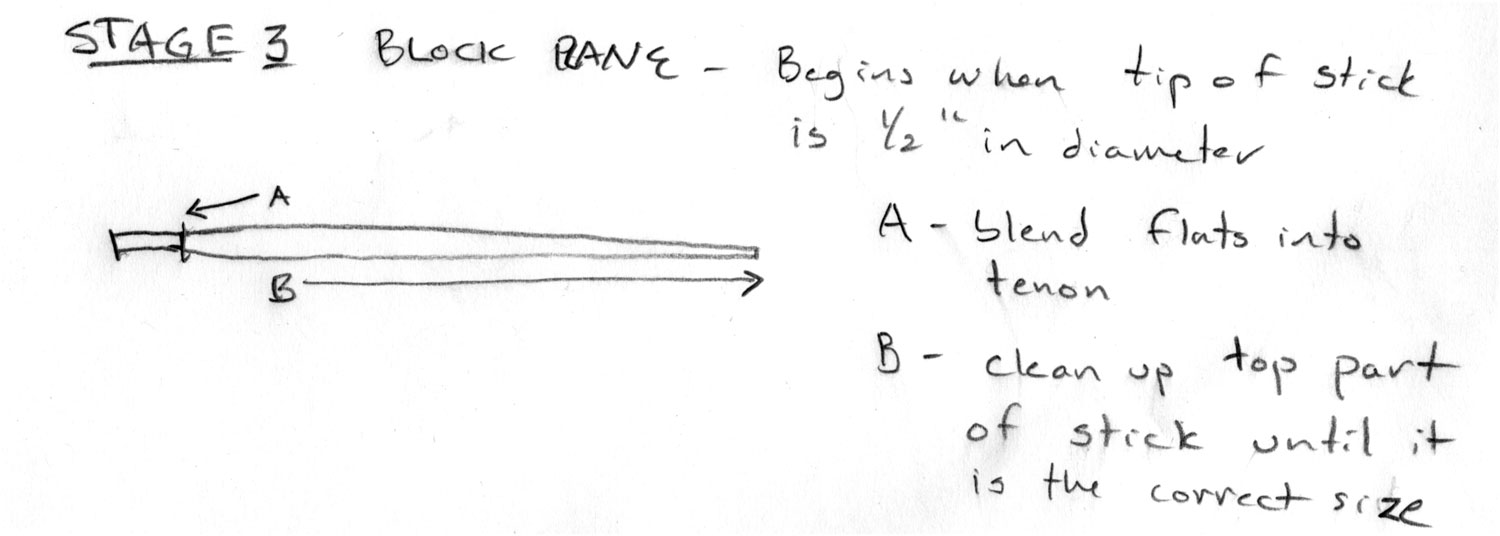
Stage 3
I turn the stick around and press the tenon against the stop in the vise. Then I use a block plane to taper the bottom of the long stick down to the tenon. I do this by making quick, short cuts and rotating the stick. This work is quick.
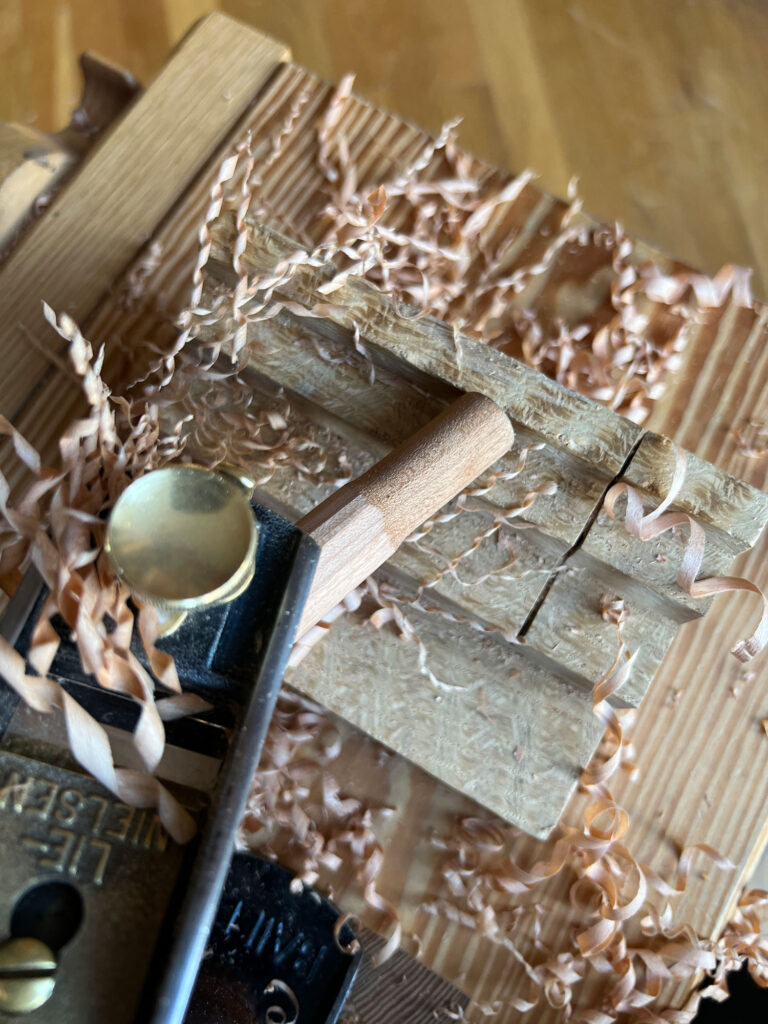
Then I turn the stick around again, pushing its tip against the stop in the vise, and I clean up the top part of the stick, making sure it is round and the facets are nice and even.
I check my work by dropping the long stick into a mortise in my armbow. The stick should get wedged with about 8” of the stick (plus the 1-1/4” tenon) showing. If I need to remove more material, I remove the stick from the arm and shave it more with the block plane. Look for arrises and smooth them out.
This might not be the fastest way to make sticks, but it’s the fastest way I know of today.
— Christopher Schwarz
P.S. Why don’t I turn my sticks on a lathe? I don’t have a steady-rest or any other equipment that could make this work. I prefer to work with bench tools when making chairs in order to keep my tool kit as small as possible. Plus, I’m a fairly lame turner.
“Note that when I make sticks using planes, I skew the planes significantly (about 30°) to speed their cutting action.”
Can you clarify this? I’m assuming you’re not referring to the skew causing the plane to remove more material. Is the skew to make the plane easier to push down the length of the stick?
Hi Wilbur,
Skewing the planes removes most of their soles from the cutting equation. So the jack plane acts like a plane with a 3″-long sole, but has enough weight to stay in the cut while being used one-handed.
If you don’t skew the planes, the soles will ride the high spots on the stick, requiring more strokes.
Hope this makes sense.
I had the same question. That’s a crystal clear explanation. I’d only ever thought of skewing as a way of reducing effective iron angle or narrowing the planing path. Thanks!
It sure does. It’s like by skewing your jack plane, you’re transforming it into a spokeshave, of sorts. Could be the basis for the next Michael Bay movie.
A one-handed spokeshave that will easily stay in the cut as you push it forward.
Thanks, Chris. These technique blog posts are super helpful. I spent a little time admiring the planing stop. It looks like it has pulled its weight in your chairmaking.
Any chance of a Vimeo on this? The explanation is crystal clear, but I think a ~3 minute video would make major “aha” moments. Here, let me ask you to do more work, do ya like that? Do ya?
I was going to do a video, but Megan decided to go home early and work on her bathroom renovation. So I didn’t have anyone available to run the camera. I’ll try to do a video when we both have a slack moment.
Yes please and thank you!
Is that the Roman workbench that you’re sitting on in the pics?
Yup. The planing block (removable) is from Hulot.
I love rabbit holes. Your mention of Hulot led me to a search, which led me to a couple of Follansbee’s old posts on 17th century shavehorses, which led me back to a couple of your old blog posts, which led to a side trip to Larmessin. Tonnes of fun.
Is this the same cambered blade you use to thickness planks? And, what radius do you use these days?
Yup. I use a 10″ radius now because it suits my honing guide. But you don’t need a cambered blade to do this operation. A straight blade works just fine.
Thanks. It’s nice, I suppose, to be able to switch blades for different operations. In practice it’s a bother. I’d prefer to not swap things if I can avoid it.
Can I ask how you octagonalize (octagonalate?) your spindle blanks?
Either a band saw or with a jack plane in a planing cradle – it depends on what’s available.
How is the stair step thingie (planing stop?) mounted to the bench? Why does it have a saw cut in one end?
It has a 3′ x 3″ post on it that drops into a mortise in the benchtop. That way I can swap it out for a traditional planing stop or “palm” accessory.
The sawcut (also from Hulot) is a 90° cutoff box. I put a backsaw in the slot and cut my sticks to length there.
I find this interesting because I’m weirdly indifferent about buying a lathe. I appreciate the benefits, but love the simplicity of a hand plane and workbench.
Is there a historical precedent for this, or were human-powered lathes typical in pre-industrial shops?
There is LOTS of historical precedence. Shaving on a low bench shows up in M. Hulot (18th c) and “Woodworking in Estonia” for starters.
There’s is nothing new!
I have been using a horse with the drawknife and spokeshave to make the sticks. I have found I can rough in the stick pretty fast on the horse, then move to the bench and find tune the sticks with the block plane. Have you tried that system?
Oh sure. And it might be faster – no clue.
We don’t have a shaving horse in the bench room. And I’m more comfortable with a jack plane than a drawknife.
So… you’re basically turning the plane into a spokeshave?
I like the method, but the body English in the picture seems like it would feel awkward to me. In part I think it’s because I learned somewhere that lower body work is for rough and tumble operations, and more detailed work should be more elevated.
I think I saw a picture somewhere in Ingenious Mechanicks that had a pad fixed to the front of an apron to hold the end of a spindle. Maybe it was somewhere else. I’m wondering if having a pad up closer to the shoulder, just south of the clavicle, would let you ‘hold’ the closer end of the stick just by leaning into it, without actually impaling yourself… along with an elevated stick-stop. Could be as simple as a 2×4 in a vise with a shallow hole drilled into it, with the hole just south of nipple height.
With the stick sloping down and away from you, trapped between your chest pad and the stick-stop, you’d have both hands free to move the tool back and forth more easily.
So, both hands free, using body English for clamping. Similar in concept to a shave horse… Call it a shave monkey?
I’ve done this with a bib and very much prefer the method shown here. One hand on the stock and one on the tool is a fast way to work.
This isn’t a new and wacky method. John Brown shows a variant on it “Welsh Stick Chairs.” And James Mursell (Windsor Workshop) also does a lot of one-hand-on-the-tool stuff like this.
For the first planing in stage 1, do you start on a flat or an arris?
Arris. Everything starts on an arris.
Hey Chris,
How rank is your jack plane set for this?
Fairly rank. You’ll know when it’s too light — you won’t get anywhere fast. The third stroke of an arris should be a little difficult to push.
Great technique! Can’t wait to give it go. BTW – I assume the red tape on the vise screws is to reduce your Workman’s Comp claims 😉
Yup. It will bark your legs.
Chris, do you ever stand at the vice for this process like JB as a change or you really prefer sitting at the low bench?
Oh sure! Standing works just as well. But if I can sit, I will….
Smooth plaining. Beautiful piece of art. Thank you for sharing Chris.