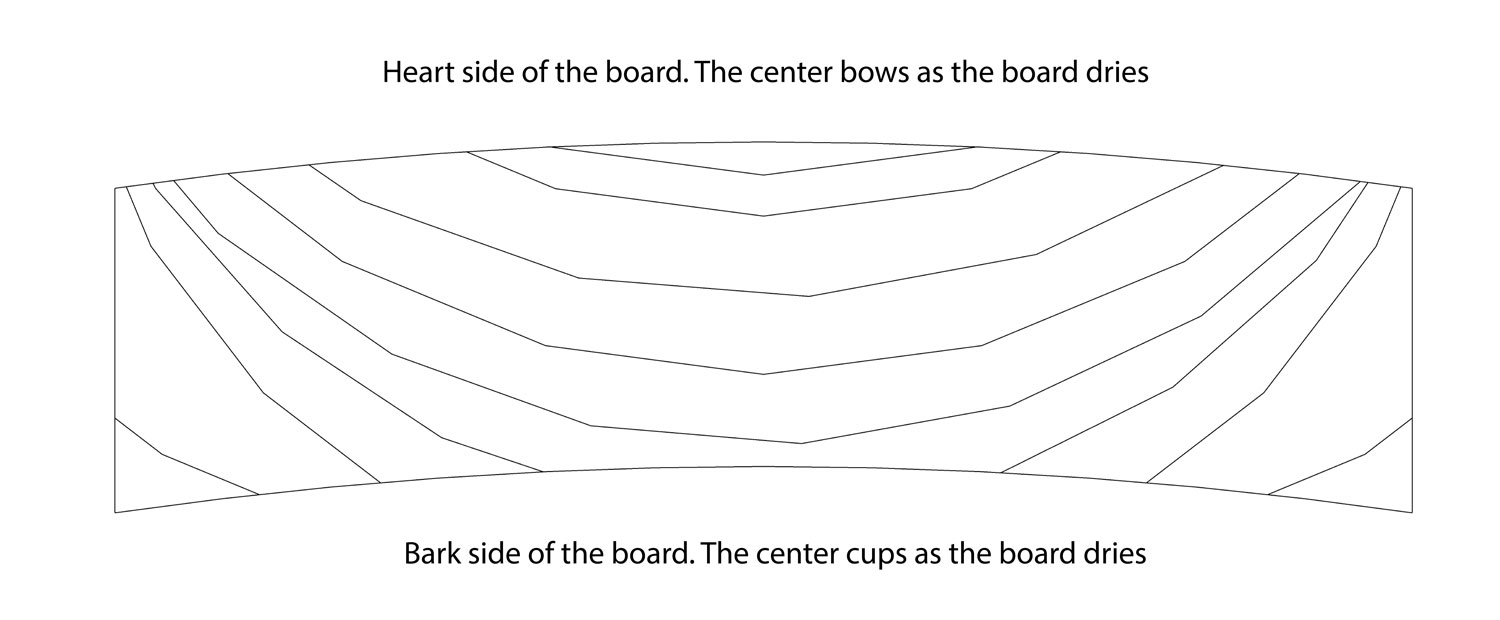
Some people were left confused by the correction to “The Anarchist’s Workbench” I posted yesterday. And I don’t blame you – the ideas of right and wrong, correct and incorrect were being juggled furiously in the entry.
So let’s start over.
Construction lumber is usually sold in a wetter state than furniture wood. I’ve bought about four metric tons of it in my time, and it seems to come in about 14 percent to 18 percent moisture content on average. That means that as the wood dries to your shop’s equilibrium moisture content, the board is going to move a bit on you.
When wood loses moisture, the bark side of the board (the outside of the tree) tends to cup. The heart side of the board (the inside of the tree) tends to bow out. See my drawing above.
If you need to laminate the construction lumber face to face – such as gluing up four layers to make a big workbench leg – you should use the above fact to your advantage.
I glue up my legs so the heart side of one board faces the bark side of its neighbor. That way as the boards dry, they will all move in unison and keep the joints closed. Like this:
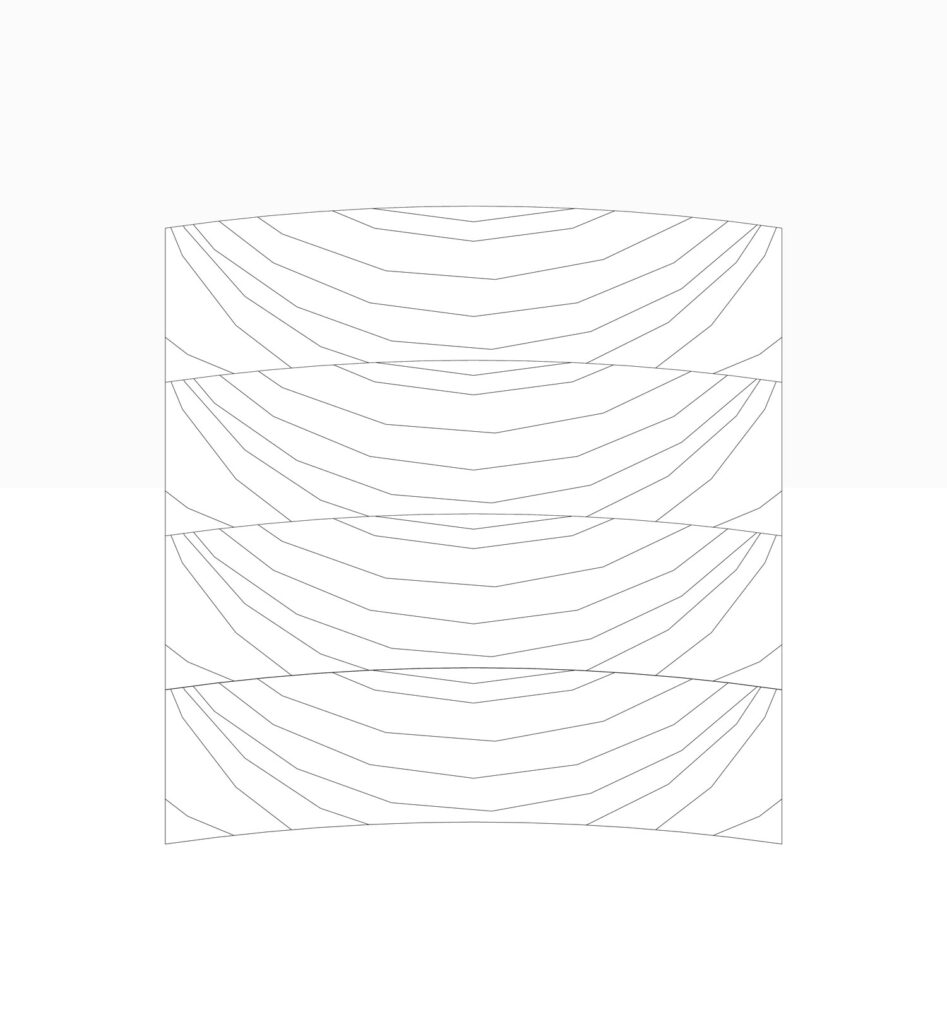
If you flip one of the boards, so the heart side faces the heart side of its neighbor, the edges of the lamination tend to open up as the boards dry. Like this:
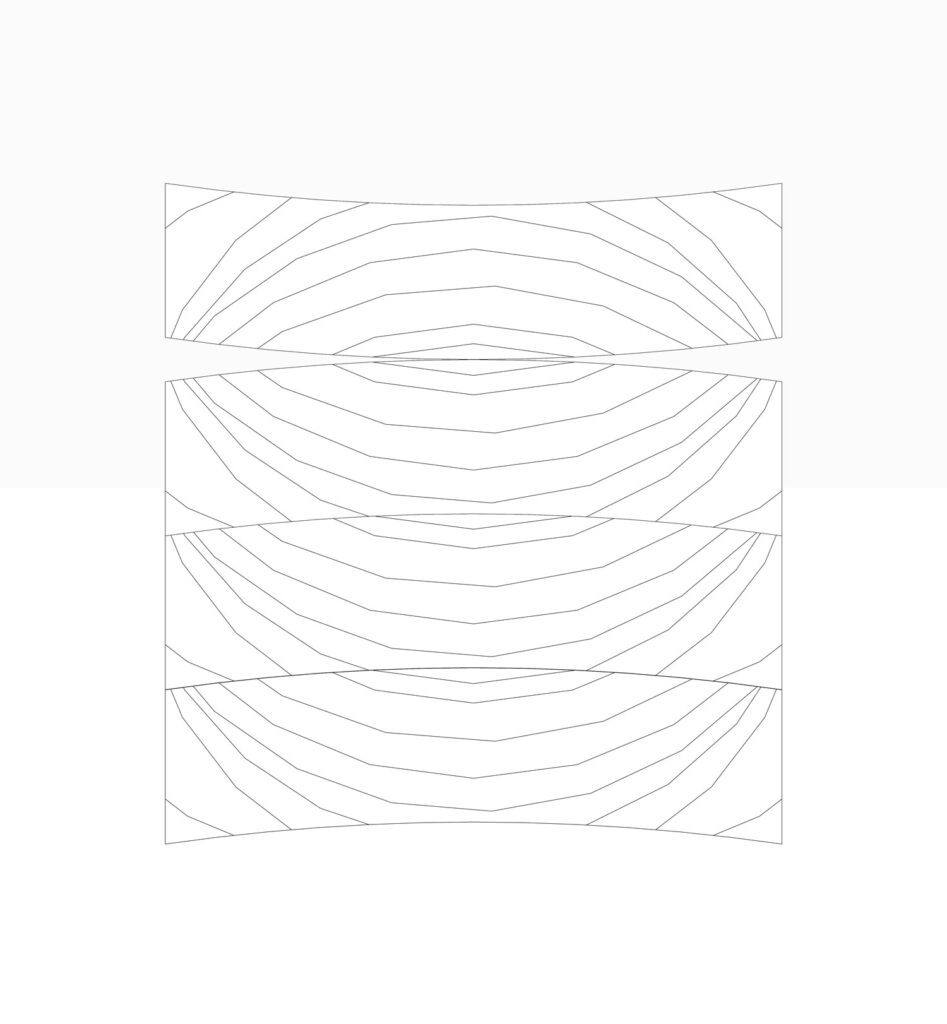
If you glue the bark side to the bark side of its neighbor, the interior of the lamination tends to open up.
I’ve seen this happen. I’ve never seen the joint fall apart because of it, but it ain’t pretty to look at.
I hope you will forgive me for yesterday’s confusion. In the coming days I’ll correct the free pdf.
— Christopher Schwarz
Thanks for clearing this up, I’ve had people try to argue with me over which way the grain should go.
I usually just walk away shaking my head. Now I can point to an expert…
An excellent explanation. My ol’ man use to tell me to keep the center of the tree facing the center of the piece (that I was constructing).
Thank you for this explanation. It’s one of the best I’ve seen. I appreciate your integrity in bringing the original problem to our attention.
Thanks so much for the long form explanation of this and drawings to match – it really helps.
Cheers
Chris, that was an exceedingly well written post. Your use of graphics was excellent as well. It’s not easy to explain difficult things simply.
So for face glueups,keep the ring pattern consistent so that they don’t delaminate. For panel glueups on edge grain, alternate the ring patterns so that the boards’ cups cancel each other out and the panel as a whole stays flatter. Is that correct?
Hi Devin,
For edge glue-ups… it depends. If you are working with dry lumber, just make it look as best you can (the alternating-growth-rings argument does not line up with the historical furniture record and I have never followed it).
If the wood is wet, I’d let it dry so that your top doesn’t look like a roller coaster. Then ignore the heart-side-bark-side rule.
I will be hung in effigy for this. So let me also add that you don’t have to finish the underside of a board to prevent cupping. And that Skyline is my favorite chili.
I was wondering if this question would come up. For what it’s worth, my experience is exactly the same as yours.
I’ve never eaten chili of any kind. Not once.
On the “flipside“ of this discussion… It’s been 43 years since my high school wood shop class but I think when gluing up a wide table top you should take your same principle – but alternate the boards so that you have one board Bark-side up the next board heart side up and repeat…
By doing this the wide table top will offset itself as the wood moves. Instead of ending up with one big curved piece of wood you will have a big piece of wood that has a little bit of waffling all the way across.
Is my thinking correct or my recollection correct?
Definitely helps. Describing it with the simple case of all the boards having the same structure makes it much easier to internalize. Then it may be worth also showing the real-world example so folks can see it applied where the radii and centers of the rings differ.
Does getting the rings to more-or-less line up, as you did in the “good” example by picking the order in which the boards were layered, further help ensure everything moves together? Or is it just for looks? (Which would be a good enough reason, I’m just interested.)
Thanks! If I wanted to learn more would With the Grain be a good book to read?
Yup. Or if you want to go Full Wood Nerd, “Cut and Dried.”
This makes so much more sense. Showing the incorrect example actually failing makes things instantly click.
This post made a lot more sense! This explaination fits with everything I’ve always learned / experience in the past.
Splendide and thank you! Clear like a gin!
I’ve always thought of it as “The growth rings want to be flat” and orient boards accordingly.
Ditto. I just use that to my advantage when it matters
Is there a way to glue up some of the boards bark side to bark side such that they will cancel out the cup, yet keep the glue lines tight?
Ahhhhh. Ok, then.
Is there a way to glue up two of the boards bark side to bark side such that they will cancel out the cupping, yet keep the glue lines tight?
As I understand it, your options are: Carefully manage the moisture/humidity during and after(!) build so the wood isn’t tempted to move, use a wood that doesn’t move much (supposedly aged pine settles down pretty well), back the glue up with screws or something else to keep them even more firmly clamped to each other than the glue does, take your chances and hope, or some combination of the above. Not sure whether using quartersawn boards would make a significant difference or not.
Again as I understand it, hope will often work in the short term with modern glues. Unless you have a good reason to want that arrangement, though, I wouldn’t bet on it.
I’m a beginner. I may be completely wrong.
Or: slice a veneer layer off the heart side, glue it to the bark side so both sides look like they’re heart side, then glue up as per Chris’s suggestion? As Iong as the veneer doesn’t split…
Thanks Chris, that’s super helpful. It’s also the first time I have ever understood this. John
Scaffolding boards are always an option that seem to be a much better quality compared with any construction lumber. Envious of your choices in US.
I wasn’t familiar with “scaffold boards” being sold as such … but it seems they are, even in the US. However, in my quick websearch they seem to be commanding a price of 50% more than “#2 and better” of the same size and species.
It works best when the grain is spooning!
Chris,
Your mention above in reply to another comment of Cut & Dried, and the context of sympathetic lamination in a workbench build, made me remember something I’ve been meaning to ask you.
In Cut & Dried (which, by the way, is a fantastic book that I heartily recommend!), Richard Jones writes about these very issues in sections 7.6 and 7.7 (pp. 105 ff.), and among other things has this to say:
” […] there are many woodworkers who build a workbench for themselves and want a 3″ or 4″ […] thick top of beech or maple. The only way this is normally achievable is to glue together the 3″ to 4″ […] wide faces of several 1″ to 2″ […] thick boards. In this circumstance, one area to pay special attention to is the orientation of the growth rings at the end of each board. Where the end grain shows every plank tangentially cut as in figure 7.30, there are arrangements that work with the natural shrinkage of the wood, and arrangements that work against this movement.” (p. 107)
In figure 7.30 (p. 108) he then proceeds to illustrate face glue-up heart-to-bark (7.30 A), heart-to-heart (7.30 B), bark-to-bark (7.30 C) and with quarter-sawn laminates (7.30 D), and the potential consequences of cupping/bowing on these joints, along the same lines as what you have described in this (and the previous) post.
He never quite comes out and says you must do this, or you should do that, although the implication seems to be an order of preference of D, A, C and B.
What is you take on this?
Unless I’m much mistaken (and I spent quite some time poring over photographs in all your books on workbenches, and watching your workbench tour videos over and over), you do not seem to be too bothered about this; on the AWB for example, it looks to me as though there’s no discernible pattern to the grain orientation of the top laminates?!
In the end, I decided not to be bothered either, and prioritised getting coherent planing directions on top and bottom, while spending a lot of time finessing the joints to be as tight as I could make them, independent of end grain orientation.
The hard maple I used had originally been air dried, then shipped across the Atlantic, then stored under cover but in open air, so when I bought it it was at 13–15% MC; at glue-up, after about a year in my workshop (which during that time had an average EMC of 10,3%), the laminates were around 12–13% MC; today (some six months later and in the middle of winter) they are at 11-12% MC.
So far, my workbench has neither im- nor exploded (although, as we all know, if a workbench can explode, it will, so I guess I’d better start wearing a bomb squad suit around the workshop), and the joints are still nice and tight.
I paid my money and I took my chances, so I’m not asking you to neither condone nor condemn my choice (‘twould be rather pointless, anyway, after the fact), but am just curious to know a bit more about your thinking on this, as in the AWB you talk about end grain orientation for the legs, but not for the top?
Cheers,
Mattias
“He never quite comes out and says you must do this, or you should do that, although the implication seems to be an order of preference of D, A, C and B.”
True. I don’t say you must do one or the other glue-up arrangements. Leaving aside aesthetic considerations and concentrating entirely from the point of view of stability and reduced chances for that type of glue-up to tear itself apart as discussed and illustrated in the book you’ve interpreted the preferred order correctly.
I think the guidance possibly matters significantly for a glue-up to make a square column out of three or four pieces, such as a refectory table leg that needs to be 6 inches (~150 mm) square prior to further shaping, e.g., turning. In the case of a workbench top, let’s say 600 mm (~24″) wide by ~75 – 100 mm (~3 – 4″) thick, somewhat less attention to grain orientation is acceptable, but completely ignoring such a factor wouldn’t generally be optimal.
Thank you so much, Richard, for confirming that at least I’d understood the advice correctly, even if — alas! — I didn’t follow it all that well when it came top the top, although I did carefully heed it for the legs and stretchers (each of which was a two-board lamination), and also for confirming that the guidance matters more in the latter case.
My workbench top is of course what it is now, so time will have to tell how it comes to fare.
My workshop (which is in Belgium, i.e. in a climate very similar to that of at least the southern part of the UK) is in a heated and well-ventilated basement where, over the last 18 months I’ve kept daily track of the EMC. Seen as a monthly average, it varies with the seasons by about 4% from driest (8.7%) to wettest (12.7%) when measured on a test piece (always the same piece, and always the same moisture meter, so while probably not exact in an absolute sense, the numbers should at least make up a comparable series of data). So far, movement in the top is noticeable — it has shrunk in width since summer by maybe 1/32″ (0.8 mm) over a total width of 22-9/16″ (573 mm) — but the joints still look fine. Early days, though — I’ll be interested to see what it’ll be like in 15 years or so … ?!
If you don’t mind me asking a further question on the subject, what it is it, would you say, that makes the difference between a smaller glue-up of fewer laminates, like a leg, and a very large one, like a workbench top? The amount of glue surface involved? The speed at which EMC changes spread throughout the piece? Countering forces from neighbouring joints moving in the other direction? All of the above? None of the above?
Again many kind thanks for taking the time to reply!
Cheers,
Mattias
If two parts shrink or grow by the same percentage, the larger part will have more total change.
Indeed — the total dimensional change should be proportionate to the size of the object being changed.
However, I’m not sure that that would explain why a smaller laminated component (say, a leg) is more liable to joint failure from non-sympathetic glue-up than a larger one (say, a bench top), which is what I was wondering about.
Mattias, In a smaller glue-up for let’s say a leg that’s going to finish square in section, e.g., 100 mm square only two to four pieces laminated together are required, so following the suggestions given in the book are best, especially if you carefully select boards with a very similar end grain pattern, e.g., similarly arced end grain in tangentially sawn board. Orientating the cupping of tangentially sawn boards means they should ‘work together’ for want of a better description.
In the case of bench top such as yours which is wider than it’s thick you’re likely to get or use boards with dissimilar cuts, some tangentially sawn, some rift sawn, and perhaps even some with a figured cut, see figure 5.18 in the book. You might even find some pieces that are quarter (radially) sawn. In other words you’re likely to produce pieces for your glue-up with some variance in the end grain patterns and it’s almost impossible to arrange this thick panel as in figure 7.30, example A. Arranging the end grain growth patterns to work relatively sympathetically together I’d say is the best strategy. When arranged in this way there will be some discrepancy in shrinkage patterns in each piece of the thick glued up panel but with a larger number of parts than a100 mm (~4″) square column I think the stresses induced through shrinkage and expansion tend to cancel each other out.
Having said that I’ve come across thick laminated bench tops that do have splits at glue lines so the strategy isn’t perfect. In most of those cases the end grain was covered by a clamped (breadboard) end, so it wasn’t always possible to clearly see how the end grain of the laminated boards were arranged, see figures 7.3 and 7.4 in the book for example.
Hi Mattias,
Sorry for the delay in responding. We were at the lumberyard.
You are correct that I didn’t make any accommodation for heart vs. bark when gluing up the top. Two reasons:
My primary concern with the top was getting the grain direction consistent in all the boards (running from right to left) to make it easier to flatten without tear-out (not that tear-out is a big deal on a bench).
Oh, and Richard is correct that having narrower board reduces the cupping.
Thank you so much, Richard and Chris, for your kind and enlightening replies!
(And please, Chris, no worries and no need to say sorry – for starters, you getting on with your work is rather more important, and also you are not exactly running Woodworkers’ Question Time here.)
Richard, I quite see what you mean – most of my laminates have tangential grain at the top of the butt end, and rift sawn at the bottom (or vice versa); a few are through-and-through tangential; none are figured or quarter sawn. In any case what you say about opposing stresses cancelling each other out makes me reasonably hopeful that it’ll stay together.
Chris, I, too, prioritized grain direction on the top side, for easier subsequent flattening, to the point where I got the front seven laminates to all plane right to left, and the rear six to plane from left to right (in other words from right to left when standing behind the bench), so that the top could be worked along the grain from both sides with equal ease. In the end, that turned out to be largely for naught, though, because I much preferred the surface I got from traversing with my jointer: more velvety than polished and rather more grippy.
In any case, the lumber had been in my shop for a full year before glue-up, so was hopefully sufficiently acclimated that cupping and bowing won’t be too much of an issue down the road. It was fairly flat when I bought it, but did cup during storage before I began working it. That cupping was then removed in planing and jointing, and did not reappear during the several months between doing that and final glue-up.
I’m sure I could have arrived at a more optimal arrangement of the laminates, but I’m not overly worried about their current state; my questions here today were in any case not about angling for assurance for the future (’cause that cannot be had anyway), but about improving my knowledge and understanding of these matters. And that both could be and was had, so many thanks, once more, to both of you for so kindly taking time to help with that!
Cheers,
Mattias
Same tip I use when laying down pressure treated deck boards. “Turn that frown upside down.”
gack. I have so much respect and appreciation for your work.
But I have found in construction that failure to finish all sides leads to uneven drying, and therefore bad wood movement. This is common wisdom from experience, I’m surprised it wouldn’t apply to tables.
I have no opinion on chili, or rather, as a Virginian currently, I realize none of the sides want to hear my opinion
That may depend on how dry the wood is before finishing. AIUI, it shouldn’t dry much further unless you’re deliberately working with green wood or have an unusually humid working space… Choice of finish might also matter; some are more elastic than others, and some seal more than others.