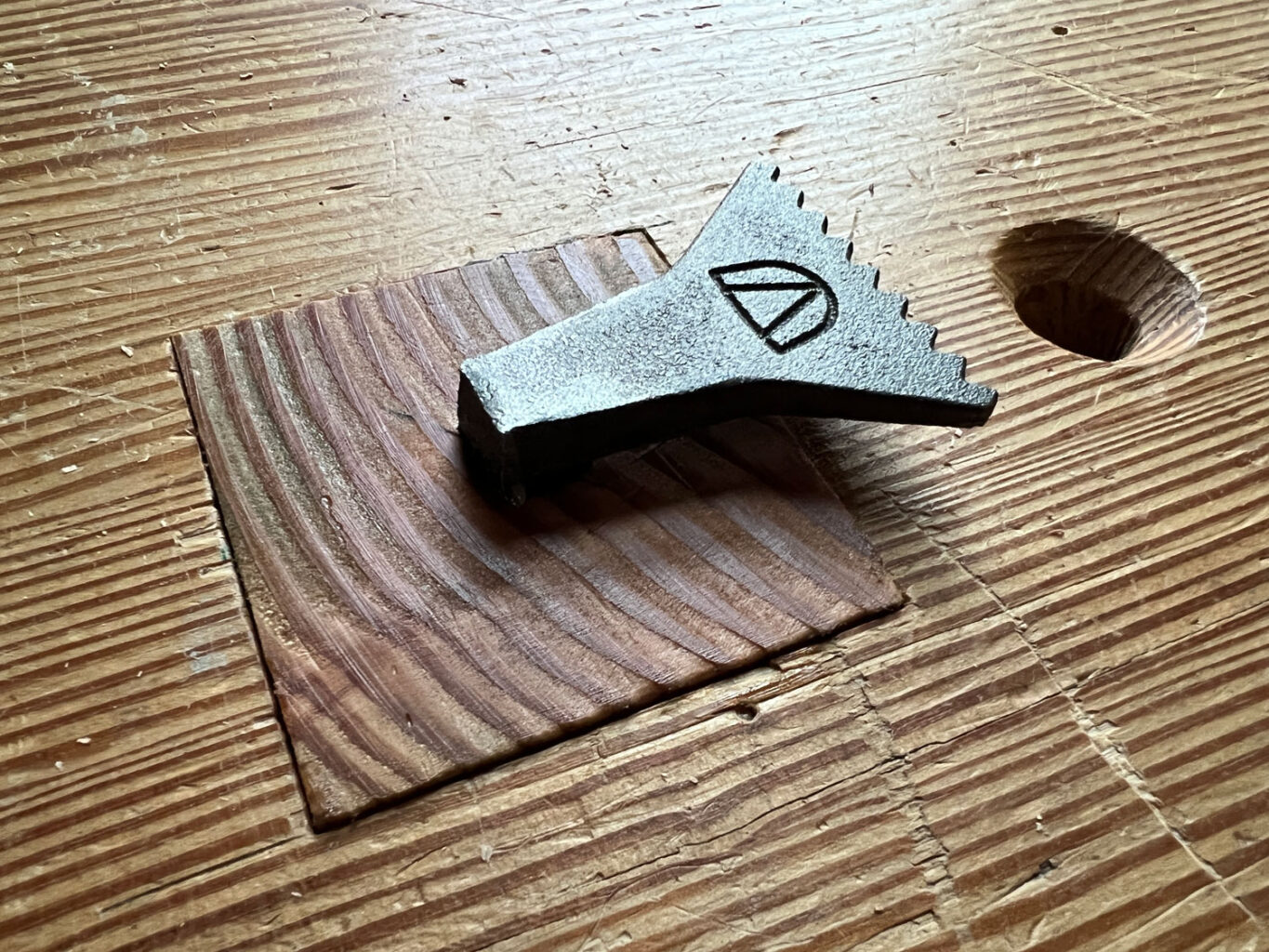
The Crucible Planing Stops will go up for sale on Monday in our store. The stops will be $49 plus shipping (I’m afraid they are unlikely to arrive at your address before Christmas).
These planing stops represent two years of work and almost a $50,000 investment in patterns, matchplates and ductile iron. This is our biggest-ever tool run, and we are holding our breath a little bit about how they will fare in the marketplace.
The idea for these cast-iron stops came to me while writing “The Anarchist’s Workbench.” We have had great success with our ductile iron holdfasts, and it occurred to me: why not make planing stops out of ductile?
These stops are less expensive than a blacksmith-made stop, and they are quite easy to install. I’ve made a short video that shows the process here:
The stop is based on the planing stops shown in A.J. Roubo’s masterwork, with some minor tweaks. The stop’s teeth sweep slightly upward, instead of being parallel to the benchtop. This makes it much less likely that a handplane will collide with the stop.
Also, the teeth come sharp – but not too sharp. Beginners can get used to using the stop. Then, when they are comfortable, they can grind or file the teeth so they are needle-sharp, which is how I like mine.
Once we get our first volley of planing stops out the door, we will offer these to our retailers around the world. It is my dearest hope that somehow, someday, one of these stops makes it onto a Roubo-style workbench in Paris – completing a 240-year cycle.
— Christopher Schwarz
As a full ignorant about planning stops (almong thousands of things) would it be possible for you to show how you use it in videos ? i (mistakenly) am afraid of using iron made planning stop , because i ‘m so scared of the wrong move that would make my beloved plane blade meet and kiss the planning stop ….. It might sound stupid for rexperienced users but for a self taught like me the way to use it is not that obvious….
(And since i’m here, if you do not know about them, here is a retailer in France that might be interested by all your fantastic tools and book (https://www.auriou.fr/) they are the rasp masters….
Have a nice day (and christmas and end of the year…. )
I understand your concern. The use is fully explained in The Anarchist’s Workbench, which the PDF version has been made available for free. I do believe that if used properly, the teeth of the stop will always be below the surface to be planed.
Use a mallet to adjust the planing stop to ½ the thickness of your board. Push the end grain of the board that you’re planing into the teeth. Start planing. Reposition the board as necessary so that you’re always planing inline with the stop
To see one in action, go to the Benchcrafted YouTube channel and find a video called “Benchcrafted Planing Stop.”
There is a brief but clear video in one of Chris’s earlier posts here on the blog that shows him working against a planing stop, both planing and traversing.
My personal experience of working with a planing stop is also very positive, and I must say I have never felt worried about running my plane into it. I’m not saying it could never happen, but as hs laredy been said in reply to your comment, the set-up is such that the stop will always be well below the lip of your workpiece.
Great news! I have been waiting for these(and the sliding bevel). You’ve got at least one sold on Monday.
What time on Monday? From the left coast, need to set an alarm!
I’m not sure these will work on the Pacific coast. You might have to turn the teeth around the other way.
Our tests indicate we only need to turn the teeth for the Southern Hemisphere.
No-no, you put them in upside down for the Southern Hemisphere. On the West Coast we push the board into the non toothed side. You can spin it around to do that, or you can just put it in the right way and put the board on the otherside, which is preferable for lefties.
Ahhh. That makes more sense.
Oh dear, I have been using my homemade one based on yours incorrectly. Must have not paid proper attention. As everything is upside down and back to front it can be a confusing part of the globe.
Hi Kevin,
My guess is that we will launch about 11 a.m. Eastern. But we have an insane number of these stops. If we run out immediately I will streak through the streets of Covington – igniting more Sasquatch calls to the local PD.
So, What your saying is there is a chance to catch a Sasquatch calling streaker on video?
That would definitely have to be posted to Youtube!!!
Chris, be careful what you wish for, haha.
If you streak, the rule is, as always, ‘video or it did not happen’.
I’m not exactly in the market for another planing stop right now – the one Tom Latané made for me is doing a great job, and still tickling my fancy a delightful shade of happy pink everytime I look at it, use it, or both – but I think it highely likely that a Crucible one shall nevertheless have to come my way at some point or other in time.
I must say I was very impressed by the ease of installation shown in the video – you obviously have given proper and thorough consideration to the degree of taper on that shaft!
On dealing with shrinkage of the block in the dry season, I have had very good results with the simple expedient of adding pieces of 2″ wide masking tape to the back of the block. I first thought it would get chewed up real quick with tyhe up and down movements, but it turns out not at all, so far. Less permanent than shimming with veneer, albeit less fancy.
And talking of fancy, and lads of that ilk, I’d say that to my mind the better reason than protection against the teeth for chopping a recess for one’s planing stop is that that is much the quicker way to get it out of the way when one wants to use that part of the top for other purposes than planing against the stop.
I quite agree that really there is not much cause to be afraid of the planing stop teeth – I leave mine sticking up above the top almost all the time, and have never felt threatened or feared for my hands or fingers or tools for that matter. (After all, we fill our workshops with very sharp and potentially dangerous tools; my worst hurt so far came when I managed to run a Tite-Mark cutting gage across a knuckle – that led to the ER and needed three stitches.)
But I’ve already had several occasions when it was very convenient to get the stop out of the way for a moment to do something else there. Sure, one can just take the whole thing out, but that is a slower affair (and leaves a big hole for things to fall through). And if one has a tail vise with dogs behind the planing stop, it is even more convenient when long stuff needs to reach those dogs. Yes, there is a downside in that the recess is a potential miniature hamster’s nest – it will collect dust and shavings – but I think not so bad that it outweighs the advantage.
As we all know, though, mileages do vary, and to each their own.
Cheers,
Mattias
I’ve been planning and building my Roubo bench for many months now and have been eagerly awaiting this stop since the beginning of the project. I think you’ve nailed the design. The proportions, angles, and size are just right. Looking forward to installing this damn thing so I can call my bench complete. Congrats on the recent tool releases.
I find it hard to believe you spent $50,000 and two years ” developing” a planning stop that looks like a reproduction.
I’ll say it so Chris doesn’t have to…
You’ve obviously never been involved in manufacturing at any sort of scale. It’s insanely difficult, and expensive, especially when you’re doing the testing and development in house but outsourcing the manufacturing. Each iteration has to be tested, improved, improvements tested etc. And each production run has to be fit into the casting schedule at the foundry, assuming they have been able to get the iron, and the sand, and the labor etc. etc. etc. ad nauseum.
Making things is HARD.
I invite anyone to make one for less. Please.
Maybe, just maybe, figuring out how to cast a stop in nodular grey iron in a way that is reproducible and always produces the correct details within a specified margin of tolerance is not as simple as you make it to be. Maybe, just maybe, making trial runs involving molten metals, in a way that one can scale things up for production is not as trivial as you think. These are my two guesses on why it costs 50K to develop a production run.
I wonder how many prototypes were produced bringing it to market?
One less than the production version. Sorry, couldn’t resist.
$50 is a bargain. My wife spent that on shipping (UK to USA) for the $100ish blacksmith stop she bought this summer for my birthday. It’s very nice. However, the shaft is about 95 degrees and unevenly tapered, like Roubo’s. Common for this type of stop. It was very difficult to install. I drilled three different diameter holes to keep it tight; it was hard to get the angles correct into the 2.5” square walnut block. I didn’t want the long shaft to protrude out the back side of the block. My first try, without the angled hole was a fail: when fully bedded into the block, the teeth were just a hair less than 3/4” above the bench. A no go for planing anything less than 1.5”! I spent several hours and two walnut blocks getting mine right, it works like a charm now. I watched Chris’ video with envy at the ease and design of the Crucible stop. At $50 for cast ductile iron and one straight hole, damn, that’s a deal. You’ve got a winner.
These look fabulous and I hope they make it to the Old World soon. Meanwhile, I have a doubt as to how exactly the teeth of the stop are filed. I imagine they are filed to a point – is my thinking correct that this point has to be at the top of the stop so that when the teeth engage, the workpiece gets wedged downward onto the workbench surface? Or am I overthinking this?
Hope my question is clear…cheers in adavance!
The teeth are indeed filed on the underside. Here’s a photo:
https://www.dropbox.com/s/l1cbf3ykzt5k21p/underside-of-teeth-IMG_0072.jpg?dl=0
Very helpful pic – thanks a lot!
Glad to hear you produced a bunch on this first production lot of planing stops. Missed out on the sliding bevel release. Any idea when the next batch of those will be ready?
We hope to have another batch in the coming week. Everyone is working flat out to make that happen!
The new Crucible planing stop made it onto page 20 “tools & materials” in the Feb 2022 issue #292 of FWW magazine. The straight forward installation of this planing stop ranks somewhere near the Colossus of Rhodes on that Wonders List!
Thank you, Kent. We spent a lot of time getting that detail right!
OOOOOPS! Make that FWW issue # 294 – Still on page 20 – “tools & materials”
The Anarchist Workbench is based on 1 1/4 inch boards. Would it make sense to make this 2 1/2 or 3 3/4 since the 3 inch you show in the video won’t work?
Rob,
If you look up the cutting list for the AWB (p. 211) you’ll find that the planing stop block is indeed specified as 2.5″ x 2.5″ (by 12″ long) to fit a mortise created by leaving out material from two of the 1-1/4″ top laminates (see pp. 219 f.).
In other words, I think one might fairly say that while 3″ x 3″ is a pretty good set of basic or standard dimensions for a planing stop, they are not set in stone (or wood, for that matter) or something that must be adhered to at any cost. I have not experimented to find the outer, practical limits, up or down, for variation, so cannot say for sure, but suspect that you would probably not want to go much below 2.5″ nor much beyond 3.5″. With a very narrow block, you might overly and unnecessarily increase the risk of it splitting on seating the shaft; with a very wide block, its center would end up further in from the edge of the bench than yoiu might want.
When I built my bench, I created the mortise before glue-up, although not in the same way as suggested in the AWB, as my laminates were +/- 1-3/4″ thick, but by cutting away (with saw, chisel and router plane) the waste to a depth of 1-1/4″ on both sides of what was to become the glue joint. I also did my best before glue-up to get the end grain walls of the mortise square, but ended up having to finesse these after the top was together. The finished mortise was therefore not quite square – it measures 2-1/2″ wide by 2-5/8″ long – but that is of course not an issue, as the block is simply planed to fit the mortise.
Cheers,
Mattias
The thickness/width size of the movable wooden block is limited on the upper end by the length of the teeth. If the block is too big the teeth won’t extend past the block, making the device mostly worthless.
The block is limited on the lower end by the strength of the material of the movable wooden block. A small block will more easily split. I like to aim between 2.5″ x 2.5″ on the low end and 3″ x 3″ on the upper end.
Thanks for the responses Chris and Mattias.
Merry Christmas to you and your families.