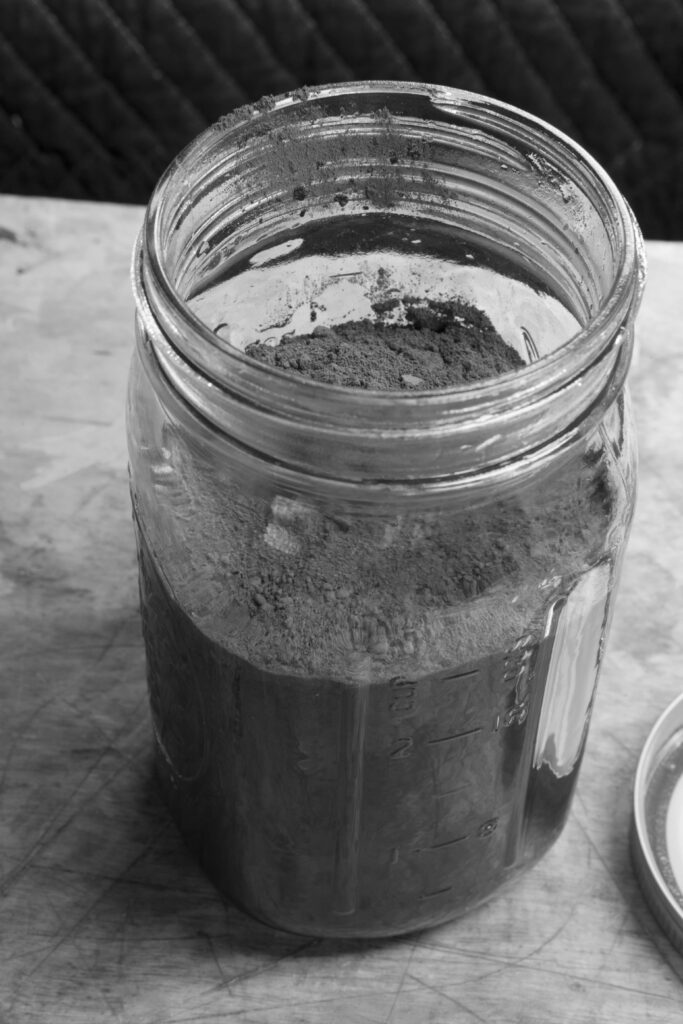
There is one topic in woodworking where I have changed my mind completely – 180° – from when I began woodworking. And that is with finishing.
My first woodworking job was finishing doors in a factory where we used industrial (read: nasty) coatings. And when I signed on at Popular Woodworking in 1996, we used a Binks 2000 system to spray lacquer and all other sorts of solvent-based finishes.
And I loved it.
These finishes produced outstanding results in minutes instead of days. I could finish an entire bedroom suite in a few hours with a spray gun and fast-drying lacquer. Yes, I wore a face mask. And we had a fantastic spray booth. But that’s not enough. Volatile organic compounds (VOCs) are prevalent in many woodworking finishes. And though the home woodworker is probably OK if he or she uses them every couple months in a well-ventilated area, I have turned my back on finishes with unhealthy solvents.
Why? Perhaps it was one too many headaches after spraying lacquer, or cleaning something with acetone or xylene. Now, I try to use finishes where the solvent is water or something nearly as harmless.
When I did this, I was afraid I was doomed to use some difficult finishing processes. It turns out, however, that safe finishes can also be fast and easy. When it comes to paint, a good place to start is milk paint. The following is excerpted from the “back matter” – this is one of the appendices – of “The Anarchist’s Design Book: Expanded Edition,” by Christopher Schwarz.
— Christopher Schwarz
About Milk Paint
First thing, milk paint is essentially a myth… I have never seen anything called ‘milk paint’ advertised in period publications (of the nineteenth century), it doesn’t show up on probate inventories or other historical records and is apparently entirely a made up 20th century idea.
— Stephen A. Shepherd, “Shellac, Linseed Oil, & Paint” (Full Chisel Press, 2011)
The milk paint used for in-door work dries in about an hour, and the oil which is employed in preparing it entirely loses its smell in the state to which it is reduced by its union with the lime. One coating will be sufficient for places that are already covered with any colour….
— Henry Carey Baird, “The painter, gilder, and varnisher’s manual …” (M. Taylor – London, 1836)
Milk-based paint has been around a long time – I’ve found dozens of sources that describe how to make it from the 1800s and earlier.
It was inexpensive, didn’t smell, dried fast and could be made with commonly available materials – milk and lime. Some recipes added linseed oil, pigment, egg yolks (to give the paint more sheen) or white pitch (to make it weather-resistant).
I’ve used it for almost 20 years now on furniture and can attest that milk paint looks good, wears well and is not going to expose you to nasty solvents. You can make your own – there are lots of recipes online – or you can buy a commercial powder that you mix with water. If you live in the United Kingdom, casein-based paints are available from stores that cater to the restoration trade.
Most beginners will opt to buy the commercial powder because it’s foolproof and comes in lots of nice colors.
If you go this route, here are my instructions for mixing the stuff:
- Throw away the manufacturer’s instructions.
- Mix the paint 2:1 – warm water to powder.
- Mix your proto-paint for 10 minutes to ensure all the lumps get dissolved.
- Let the paint sit for 30 minutes. It might thicken a bit.
- Strain the paint through cheesecloth and into your paint tray or bucket.
After that, it’s just like using a very thin paint. It’s not like latex or oil paints that have a lot of body or oiliness. It’s like applying colored water.
It dries quickly, so I apply the paint with a small foam roller then use a natural-bristle brush to push the color into the details and corners. Then I “tip off” any flat surfaces.
After one coat, you will have a translucent colored surface. If you applied the paint with any skill, you can stop painting here if you like the look (I do).
If you want things more opaque, then sand the first coat with a #320-grit sanding sponge, dust off the project and apply the second coat.
This coat should obscure most of the wood grain, but not all. Repeat the sanding and painting if you want a third coat.
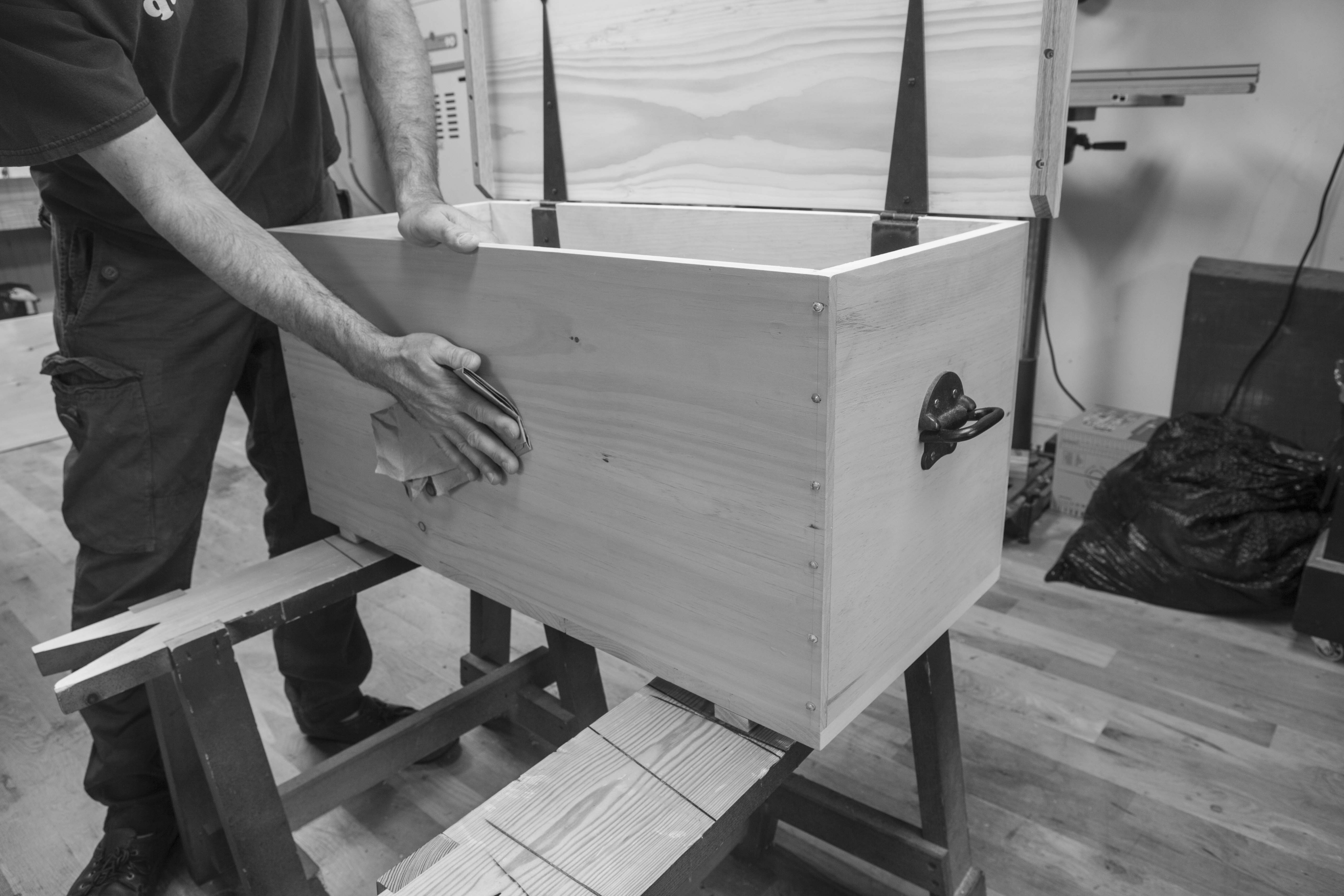
Once the color is laid on, you have a choice: Do you add a topcoat of some other finish to it or not? The raw painted surface will be dead flat. If you like this (I do), you can smooth the painted surface with a folded brown paper bag and call it done.
If you want some sheen or a deeper color, smooth the paint with the paper bag and add a coat of boiled linseed oil, wax or varnish. This will make the finish look less chalky.
As always, make a sample board if you are unsure of the look you want or if you are unfamiliar with a finishing product. I know you won’t do this, but I am obligated to beat my head against this particular wall.
Milk paint is definitely on my to-try-out list, to the extent that I recently bought a couple of bags of milk paint powder. My current finish experimentation, however, is with linseed oil paint from Ottosson and also with their linseed glaze oil for a more translucent result.
As it happens, I was looking at one of their paint tins just yesterday, and noticed that amongst the fine print on the label it said “VOC: 0%”. 🙂
Anyway, so far I am very happy with the results, although pure linseed oil paint does of course have the drawback of a rather long drying time (from one up to two or three days between coats for interior work). So yes: I am looking forward to giving milk paint a go, too!
Cheers,
Mattias
I miss Steven Shepherd and his blog.
Milk or casein based paint goes back to Ancient Egypt, or maybe even longer.
The basic recipe for Milk/casein paint is basically to make cheese curds like in cheesemaking, rinse, add borax, then use as paint binder for pigments.
Basically, any culture that knew how to make cheese, could make milk paint.
I forget whether Charles Lock Eastlake mentions this in his book on Oil Painting, but I do recall mention of hide glue and gum and resin being used as binders for early finishes, watercolors, and paints.
Eastlake theorized that Oil Paints were a later development from oil surface finishes and varnish, used to protect early painting mediums, such as hide and egg tempera based paints (and maybe casein based paints).
One of the sources Eastlake cited was Cennino Cennini‘s ‘Il libro dell’arte’, an important Late Medieval/Renaissance guide on painting technique, which later was shown having recipes that went all the way back to Ptolemaic Egypt( as found from papyrus manuscripts that have been found listing identical recipes)
If you haven’t read the Eastlake it has the type of minutiae you seem to like, although it’s 1000+ Pages
Anything which says 0 VOC annoys me as a practicing scientist in a field which measures VOCs (and similar) in the real world. If you can smell it, then there are VOCs present. Even if you can’t smell it, if it’s made of organic compounds with a low boiling point, then there VOCs. Spices would be worthless without VOCs, mint wouldn’t smell, etc etc etc.
But I do get it; I’m just being a nerd. From a professional perspective, the majority of hobby woodworkers will not receive doses high enough and chronic enough to cause health effects. That doesn’t mean that they’re healthy. My finishes are limited to actual BLO, milk paint and shellac. (Let’s be fair, the solvent in shellac does produce VOCs, there is a health based limit to alcohol fumes and it is a poison even if some people enjoy ingesting the poison.) My preference is to not wear gloves and a respirator for fun since I regularly have to wear them for work.
If anyone does use strong solvent finishes and has a concern about their potential exposure, there is a very good way to measure it. Search “helium diffusion sampling ALS”. The ALS Salt Lake City lab is probably the leader in the sampling/analysis technique and they can do a full VOC scan or targeted analysis. The collection unit is a little pressure cylinder not much bigger than a film canister which diffuses helium, creating a vacuum in the canister which pulls the air in. It’s easy, easy to work while wearing and effective.
I have been using calk paint made by watering down Latex Paint and adding Plaster of Paris. It applies like milk paint need two or more coats leaves a dead flat finish, Then to finish it off I use a couple coats of wax . always looks good
In hindsight, I’d do as you say and save a week of screwing around. “After one coat, you will have a translucent colored surface. If you applied the paint with any skill, you can stop painting here if you like the look (I do).”
I’m in the middle of kitchen cabinets with Real Milk Paint peacock color. I keep it really wet and blend in some of their black. Sand, recoat, cry, sand again. Eventually I call it good, sealing with 5 or 6 coats of water-based polyurethane. Sanding. Then waxing the whole thing for a semi-satin look (using nasty solvent based wax). They look great and clean up well.
Countertops are hard maple and screaming for bee’s wax – except it’s always sold out. I’ve bookmarked the Soft Wax 2.0 and will keep checking.
For countertops I personally like the Osmo top oil(or polyx). I feel it holds up well to the abuse a counter gets and much less toxic than most other finishes out there.
Make your own. The soft wax is easy to make and 1 batch would be plenty for a kitchen. Chris posted the recipe on the blog.
I actually like the look and feel of the soft wax over milk paint. Like literally wipe on and then wipe it off as best as you can. I buy the paint from Real Milk Paint and have had good results.
I’ve mixed up my own a bunch of times and used the General Finishes powder but keep running into random issues with adhesion. I’ve been working on bigger (pine) pieces for the last few years and no matter how meticulous I am about the uniformity of my surface prep, I find that that a tiny spot or two won’t take and subsequent coats and tend to peel the edges up more and more. I’d love to be pointed towards any resources on this – most of the milk paint info out there seems directed towards people seeking a fake, pre-distressed look that I can’t stand. For now, I’ve been mixing in Liquitex matte gesso and have found that Krylon matte glaze does a great job of fixing down problem areas but that stuff smells like death in a can. I’d love to reliably get a clean, even finish without synthetic additives.
Thank you so much for the tip on 2 parts water to 1 part powder. I had followed the manufacturer’s directions which were a 1:1 ratio and it was a nightmare to work with. Didn’t strain well, etc. I’m starting to plan out the next year’s projects and I want to have at least one item that has part of it painted with milk paint. I like natural wood but want to mix it up a bit.
As for organic solvents. I’m a Ph.D. organic chemist. I’ve worked with all kinds of really nasty stuff. Some stuff we used to joke and call either cancer in a bottle or death in a bottle. I don’t want to work with harsh chemicals if I can avoid it. There are plenty of good finishes that don’t require harsh chemicals. As a hobby woodworker, I don’t need to concern myself with high flow of parts that need to be finished and I don’t need to concern myself with the finish being inexpensive to keep down the cost of goods. I use what works well and looks good.
Sorry, I am picking up steam as I type. There are lots of nasty chemicals that I think are under appreciated by woodworkers. For example, dichromate can be used in woodworking. Holy crap. As a chemist, I avoided that at all costs. A few years ago, Fine Woodworking wrote about it and I was dumbfounded. The next issue, there were quite a few strongly worded letters to the editor by chemist/woodworkers expressing concern. I guess what I am saying, is be careful at what you work with and read up on anyting new. Safety data sheets are a good staring point.
The only problem I’ve had with milk paint (without a topcoat) is water spotting. A coat of wax or oil will help with that.
Whats the deal with using a different base color than what is on top? Is that just to kind of mix the two? I’ve seen a bunch of people do it over the last few years and have a project that is going to get some milk paint here in the next couple weeks and have been thinking about it.
I don’t know the exact provenance of the practice, but I’ve seen it done with various colors… the so-called traditional one being black, on green, on top of red.
My guess is that repainting furniture to renew it was standard practice, and over time, there was a certain look that old furniture had, where there were multiple colors that would show through where a chair or table had been rubbed frequently, or in some way ‘distressed.’ Over time, the grunge-lovers… sorry ‘people who believe patina adds value’… would look for such effects as a sign that the chair or table was a well-made piece with a lot of history, as evidenced by the various layers of paint applied over years, still work through by decades or hands, butts, and the general
indignities of day to day life.
Now ‘distressed’ furniture seems to mean setting a monkey loose on brand new termite barf garbage, letting him use a random orbit sander to knock the paint off of the corners and high spots, even if no one would actually touch those areas.
The tip we got in school was to have a (decent sized) piece of scrap on hand, prepared similarly to the piece being finished.
Apply one coat to the scrap wood, and let it dry. Every time you add a coat to the piece, add a coat to the scrap.
The logic is this: if you’re not sure how the piece will look with another coat, look at the scrap, because it will always be one lap out in front. If you like the effect that the piece has, and the scrap looks like you’ve gone too far, then stop where you are.
Sinopia milk paint is the bomb. They have developed an extroardinary premixed recipe, their paint goes on even, has a shelf life, excellent consistency, and is durable outdoors. (at least here in LA). I have used Real Milk Paint and its a great product but I was looking for an exterior recipe and hit upon Sinopia. Real Milk Paint has a better color selection but Sinopias paint is a dream.
Thanks Mike! I ordered some to try.
Way to really stir some coals with this post.
https://m.youtube.com/watch?v=eFTLKWw542g
When making your own, is it OK to mix the paint in a blender (on slow speed)?
The blender doesn’t provide much in the way of extending the life or degree of emulsion you get. A handheld mixer or immersion blender is way easier to clean afterward
Thanx. As I was reading his post, the word “milkshake” popped in my head and wouldn’t leave. Then the Lazy-SoB in me read “Mix your proto-paint for 10 minutes” and thought using a blender would be a good idea. Not so much. Thanx again.
I’ve painted the top of my pine Dutch Tool Chest with Real Milk Paint twice and each time several crystalline streaks appear in the breadboard top. It looks great for a week or two with hemp oil applied, but then begins to look like crap. I tried using the milk paint adhesive additive. Before I sand it down and try a third time, is there anything I should be doing differently?
I haven’t encountered that problem. Could it be sap leaching through the paint perhaps? I’ve had that happen over time in pine pieces. What did the paint company say?