
Editor’s note: “The Stick Chair Book” – $49 plus domestic postage – is now shipping from our Indiana warehouse. If you order it from Lost Art Press before Dec. 12, you will receive a free pdf of the book at checkout.
Though I have written a lot about the delays with printing “The Stick Chair Book,” the truth is that the book is about 10 years early.
My plan was to begin writing the book in about 2030, which is when I’d have about 27 years of experience making these chairs. During the last three years, however, I’ve been through four cancer scares (my father died of an aggressive form of prostate cancer). So after a few rounds of biopsies, MRIs and (so much) blood work, I threw out my long-term calendar and grabbed my sketchbook.
“The Stick Chair Book” is a love letter to my favorite form of furniture: a simple wooden chair that is comfortable, durable and built with simple tools plus whatever wood is on hand. Anyone – and I mean anyone – can make these chairs, which were first built by farmers and part-time woodworkers for their own households.
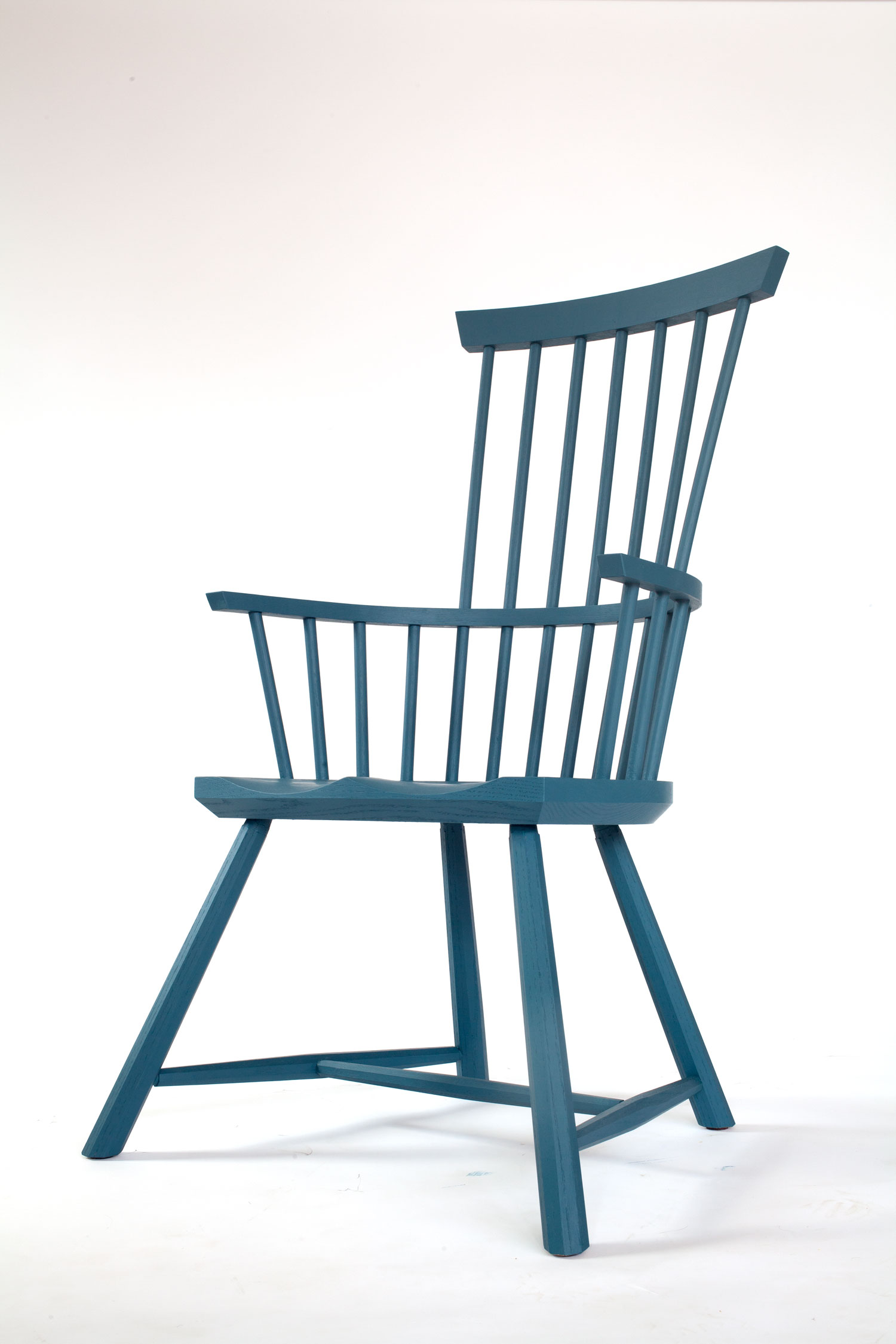
Unlike high-style Windsor chairs or frame chairs, stick chairs weren’t built to impress neighbors or show off wealth. They are only supposed to hold your bones in front of the fire after a long day of work.
Also unlike high-style chairs, stick chairs are made with dirt-common woodworking tools – most of which are already in your shop. And you can build them with wood from the lumberyard, the home center or your backyard.
So how do you get started? “The Stick Chair Book” is divided into three sections. The first section, “Thinking About Chairs,” introduces you to the world of common stick chairs, plus the tools and wood to build them.
The second section – “Chairmaking Techniques” – covers every process in making a chair, from cutting stout legs, to making curved arms with straight wood, to carving the seat. Plus, you’ll get a taste for the wide variety of shapes you can use. The chapter on seats shows you how to lay out 14 different seat shapes. The chapter on legs has 16 common forms that can be made with only a couple handplanes. Add those to the 11 different arm shapes, six arm-joinery options, 14 shapes for hands, seven stretcher shapes and 11 combs, and you could make stick chairs your entire life without ever making the same one twice.
The final section offers detailed plans for five stick chairs, from a basic Irish armchair to a dramatic Scottish comb-back. These five chair designs are a great jumping-off point for making stick chairs of your own design.
Additional chapters in the book cover chair comfort, finishing, sharpening the tools and answering the most common questions asked by new chairmakers.
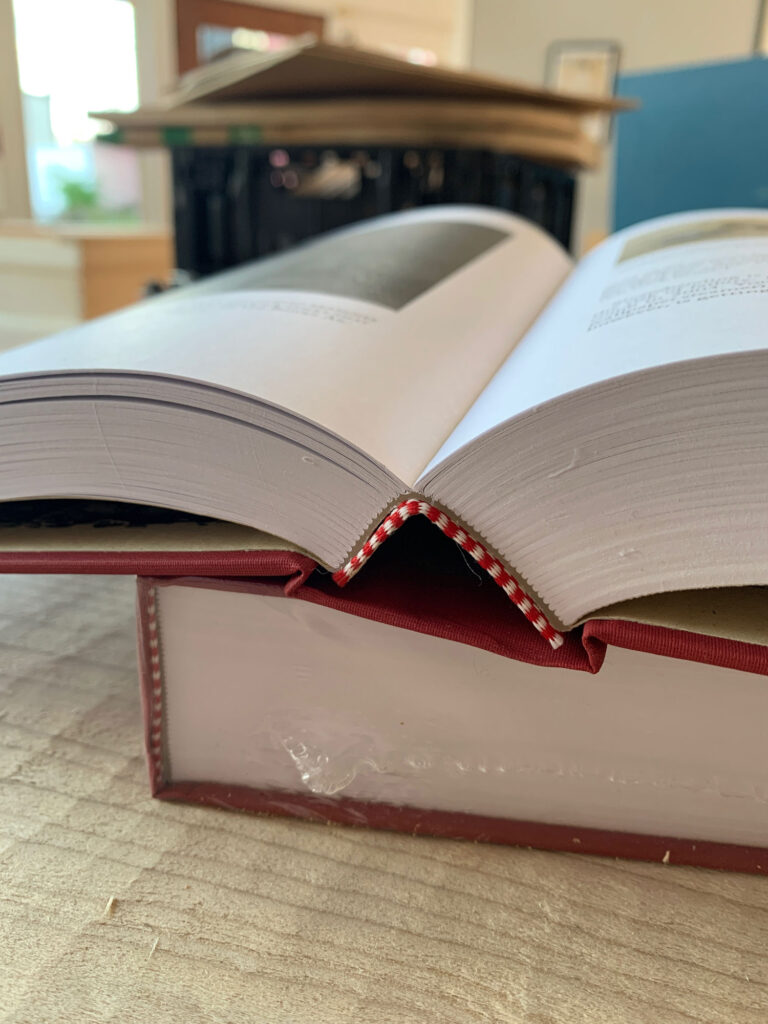
“The Stick Chair Book” is 632 pages and printed on a brilliant white 70# uncoated paper. The pages are sewn, glued and taped for durability. And the whole thing is wrapped with 98-point boards that are covered in cotton cloth. Like all Lost Art Press books, it was produced and printed in the United States.
And though this book is coming out 10 years earlier than planned, there are two reasons that I’m glad I didn’t wait until 2030. First, when I started writing, I discovered that I had accumulated so much information on making these chairs that there was no way I could get it all into one book. (That’s why I’m writing a series of smaller follow-up books on other forms of stick chairs.)
Second, during my career I’ve known five woodworkers who had a really good book in the works that – unfortunately – died with them. So even if “The Stick Chair Book” isn’t my best work, I sure as heck didn’t want it to end up as worm food.
— Christopher Schwarz
P.S. Health-wise I am doing fine, with no cancer detected at the moment. I have excellent and engaged caregivers, so you’ll probably get that book on campaign birdhouses that I’ve been promising – likely after 2030.
Excellent! I will patiently wait for it to become available at LV.
Take care of yourself. As time goes on I’m beginning to realize it’s going to be a longer wait than I’d hoped for that baroque furniture book.
No wonder the campaign birdhouses book will have to wait until 2030, the Shaker birdhouse workbench book that the woodworking world is just gasping for will need a lot of time and attention first.
And don’t forget the Arts & Crafts Birdhouse book…..
In all seriousness, there does exist an actual Gustav Stickley birdhouse design.
And some of the designs in “Boy Bird House Architecture” (1920) seem Arts and Crafts adjacent.
While we were after hours socializing during the last pre-Covid Chris Williams Welsh stick chair class, I told you that you were there most influential woodworker in America.
This is more validation of my assessment.
Just an opinion, but I think many agree.
Keep well, Rob
Thanks Rob. That’s a very kind assessment that I hope to live up to in time!
Glad you’re ok and I’m looking forward to many more books from you.
When you started posting about the book and stick chairs, I didn’t really get them. I couldn’t imagine wanting to build one. My tastes run more towards the post and rung styles. They’ve grown on me though and I’m planning to build some over the winter.
am i missing something here???? what cancer???? what medical condition?????
I have to agree with Rob, you Chris are a very influential person in our community. The best part about it is you do not blow smoke and do selfish promotional B.S. Everything you put out that is not satire is tried and true. I look forward to receiving my copy, I just placed my order. Any word on when the plane stop will be released?
Thank you.
John
They poured them this week. And should be finishing them next week. We hope to receive them in two to three weeks.
Thanks for the book. When my dad passed from his third heart attack in 2005 I had to go see the doc for shortage of breath and I thought I was having one too. I was an older college student at the time. Then I started having panic attacks over it and though it has been a while since I had one of those I find myself on the verge sometimes. I guess it is a fear cause I just wanna be around to build more stuff. I wish you many more years to build a lot more stuff and write the books you really wanna write. Like the staked birdhouse furniture one I am waiting for. Peace to you and yours.
CHRISTOPHER,
THANKS FOR YOUR TEAM’S HARD WORK. I WANT TO THANK YOU FOR YOUR PERSONAL CONTRIBUTION AND WISH YOU VERY WELL WITH YOUR HEALTH. WE NEED YOU TO BE AROUND FOR A LONG TIME.
WAYNE WRIGHT
ANCHORBEND1@GMAIL.COM
My partner calls the curvy Irish one the “sexy chair”, so that’s getting made first. 4 stick high-comb for me after that. I sit on your staked high-stool as a desk chair everyday. Thanks for including the plans, been looking forward to this.
YAY!
Hoping the answer is “yes,” but if I place an order this week, I’m assuming it will arrive by Christmas? Thanks!
Yes
In 2030 you’ll have ~ 10 more years of insights into technique. That will be great for the updated edition along the lines of your workbench book and the books you’ve “rehomed” (MACFAT, Country Woodcraft, Hayward’s, Landis’, Roubo).
I’m sure you will rediscover another topic along the lines of Roubo or Roman workbenches that the rest of us didn’t realize we should be interested in that no other publisher will touch.
Chris, the book is another winner. You make the techniques understandable. One thing you don’t expand upon is cutting off the wedged tenons above the seat. You briefly mention that you go between a flush cut saw and a scoop. In previous books, you’ve discussed using blue tape and a coarse flush-cutting saw to remove most of the waste, and then a fine tooth saw for the final work. You also talked at one point about using a heavy duty Japanese saw with the set removed. You note, though, that all of these methods can seriously mar the surface of the piece without care. Might you consider a short video with the method you have settled upon after all years of experimentation? This is one of those operations one does late in the process, and ripping up the chair surface during assembly is soul crushing. Again, the book is wonderful. I’ve ordered a couple as gifts for my children.
I have been chewing through the PDF version of the book and enjoying it a great deal.
Once some of my current build backlog is completed, I know what I’m building next!
While I am serious in being concerned to hear that Chris had some health concerns, I’m happy to hear that things are ok right now: That being said, knowing that health is always a delicate matter, I cannot help but suspect that the following scene will play out eventually.
< heart monitor starts to beep an alarm>
Doctor: I’m sorry, I guess he’s finally passed.
< suddenly, heart monitor starts beeping frantically reporting elevated heart rate>
Chris: “Hey, i have an idea for a blog post on riving chair legs”
Doctor: pauses…. “I think….”
< Heart monitor starts up again>
Chris: “OOOOH: another chapter on Roman workbenches!!!!!”
Some sort of post failure: some lines of the text disappeared. perhaps simply delete as a failed attempt at humour 🙁
Reserved a copy this morning, with ‘your man in Sweden’ – Rubank Verktygs AB.
Very much looking forward to it. I have a persistent hope (plan!) that this book might (will!) help to open up a new avenue for me, woodworking-wise. I’ve bought & installed a small lathe this past year, and practised my turning so I can make shapely, round spindles fairly competently. And I have the chairpanzee computer — love the simplicity of it 🙂 Work’s been good this month, which means I might be able to afford a coupla ‘ big pencil sharpeners’ / tennon cutters & corresponding reamers & drill bits in december (I have resigned sigh to the fact that my chairmaking will have to be done in Imperial measurements – or unlikely fractions of arbitrary silliness, as I like to think of it – but, hey! Why not be numerically bilingual while you’re at it ?).
When I am an old man, and my body too weak to shift & work large amounts of materials, I will make chairs. Just stacks of pretty, small, just so! sticks and a pile of fat seat-blanks 🙂 Give me 10 years to teach myself how to, and hopefully to find a suitable apprentice or two, and the Burghers of Oslo will again be able to buy high quality chairs, locally made. And the torch will have been passed on, as it usually is — there is in each generation a small number of slightly odd boys & girls who find great satisfaction by making stuff outta … stuff. Show them quality wood, how to sharpen steel to a vicious edge and how to work it and they will be enthralled by it’s beauty and utility.
We all get older and brush up against death. Sooner or later we will be gone. So ist es. But not yet. Not today. There is still work to be done. There is still beauty and joy to be found. There are still cats to charm us (Hey, Bean!). I am so grateful for this and for the good work that others do to help me along.
So, thanks!