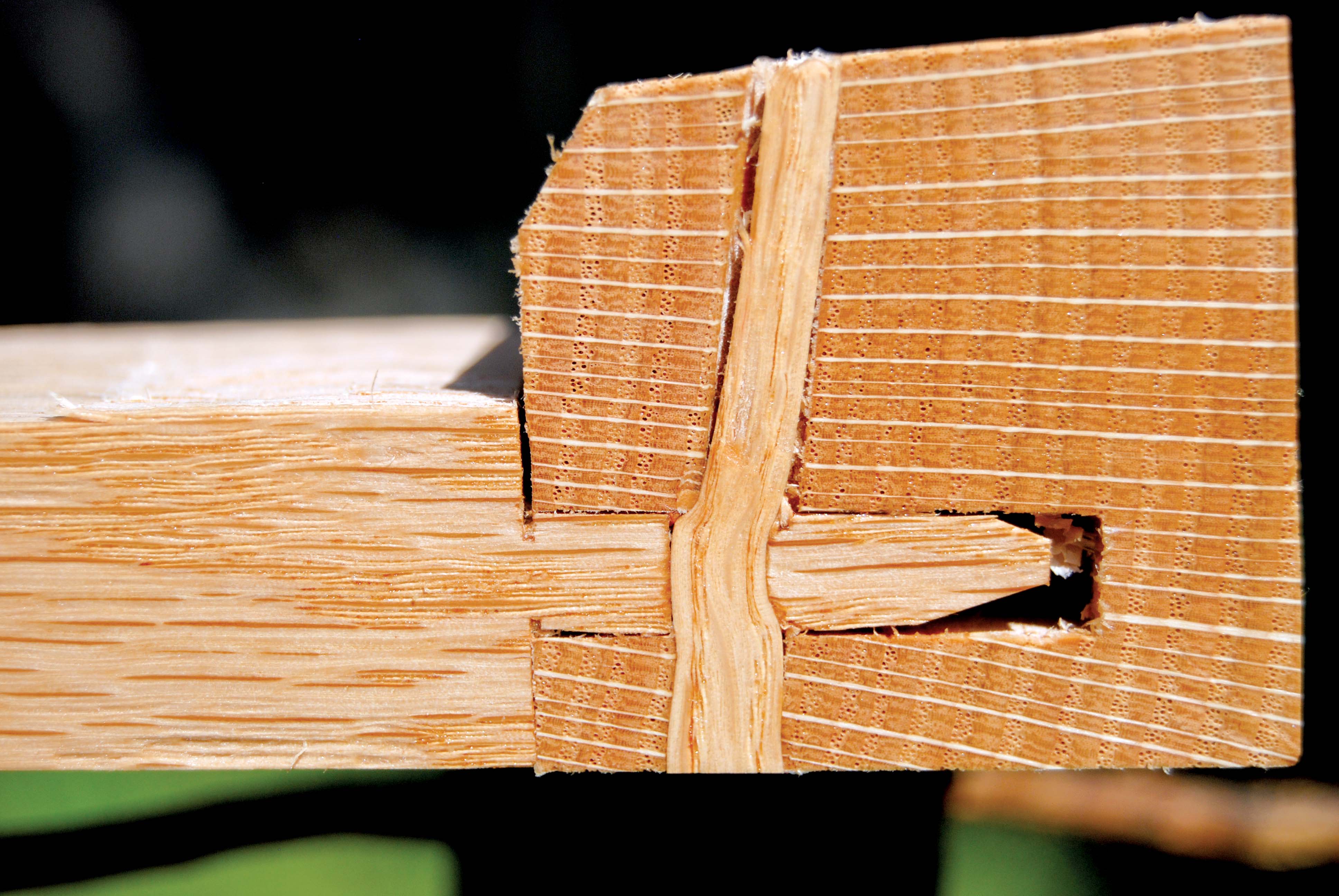
When people ask what sort of books we publish at Lost Art Press, my answer is simple: Difficult books.
Not all of our books experience troubled gestation periods, but many do. “Make a Joint Stool from a Tree,” was one of the most trying. In fact, it probably wouldn’t have been published if it weren’t for Peter Follansbee‘s unending patience/pigheadedness.
Peter and Jennie Alexander had been working on the manuscript off and on for years. When Lost Art Press offered to publish it, Peter went into high gear to get it completed. And after months of work, we had a finished book that was ready to go to the printer. But there was one big obstacle: Getting Jennie to sign off on the text.
After working with Jennie for many years, I concluded that she was more interested in continuing her research instead of publishing the results. We sent her printed proofs of the finished book, but she said she couldn’t read them easily. So Peter did something extraordinary. Over two evenings, Peter read every word of the book to Jennie over the phone. He took careful notes on what she wanted changed.
And, miracle of miracles, Jennie signed off on the work.
And thank goodness. “Make a Joint Stool from a Tree” is an eye-opening look at how early joinery was performed – and it’s not like how we do it in modern shops today. The book weaves historical research and practical work together with photos and drawings (made by Roy Underhill’s daughter, Eleanor!) to present a clear and complete picture.
The following is excerpted from “Make a Joint Stool from a Tree,” by Jennie Alexander and Peter Follansbee. This book is in its second printing, and we’ve updated the paper stock to a matte coated stock that prints more crisply, plus it’s now a casebound hardcover format and is printed at a different plant (the old one went out of business). As a result of these changes, we’ve lowered the price significantly.
— Christopher Schwarz
About Drawboring
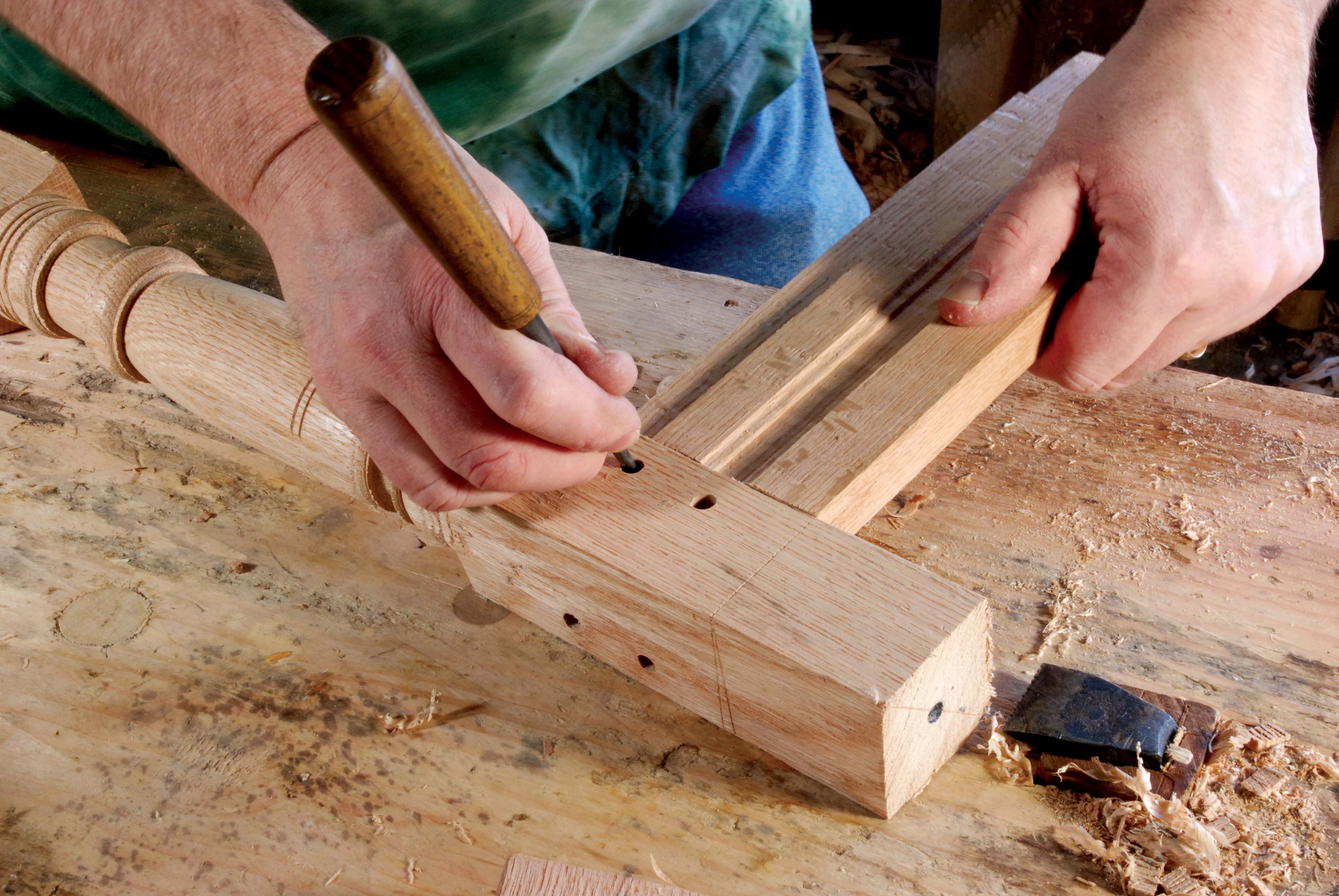
Now we come to the most exciting part of the work. Drawboring is the heart of the matter – get it right and your stool should last hundreds of years. Simply put, drawboring is an intentional misalignment of the holes bored in the mortises and tenons. These holes are bored through each component separately, and they are offset so that a tapered pin driven into them will pull the tenoned rail up tight against the mortised stile. We know this technique is a period practice because we have seen it in surviving works, sometimes in disassembled pieces, or in those worn down by misuse. Fig. 6.10 is a pin removed during restoration from a New England joined chest made about 1670-1690, clearly showing the kink in the pin resulting from snaking its way through the offset holes. In addition to this sort of evidence, we have a documentary record for drawboring as well. Joseph Moxon describes it in his section on joinery:
Then with the Piercer pierce two holes through the Sides, or Cheeks of the Mortess, about half an Inch off either end one. Then knock the Tennant stiff into the Mortess, and set it upright, by applying the Angle of the outer Square, to the Angle the two Quarters make, and with your Pricker, prick round about the insides of the Pierced holes upon the Tennant. Then take the Tennant out again, and Pierce two holes with the same Bit, about the thickness of a Shilling above the Pricked holes on the Tennant, that is, nearer the shoulder of the Tennant, that the Pins you are to drive in, may draw the Shoulder of the Tennant the closer to the flat side of the Quarter the Mortess is made in. Then with the Paring-chissel make two Pins somewhat Tapering, full big enough, and setting the two Quarters again square, as before, drive the Pins stiff into the Pierced holes.
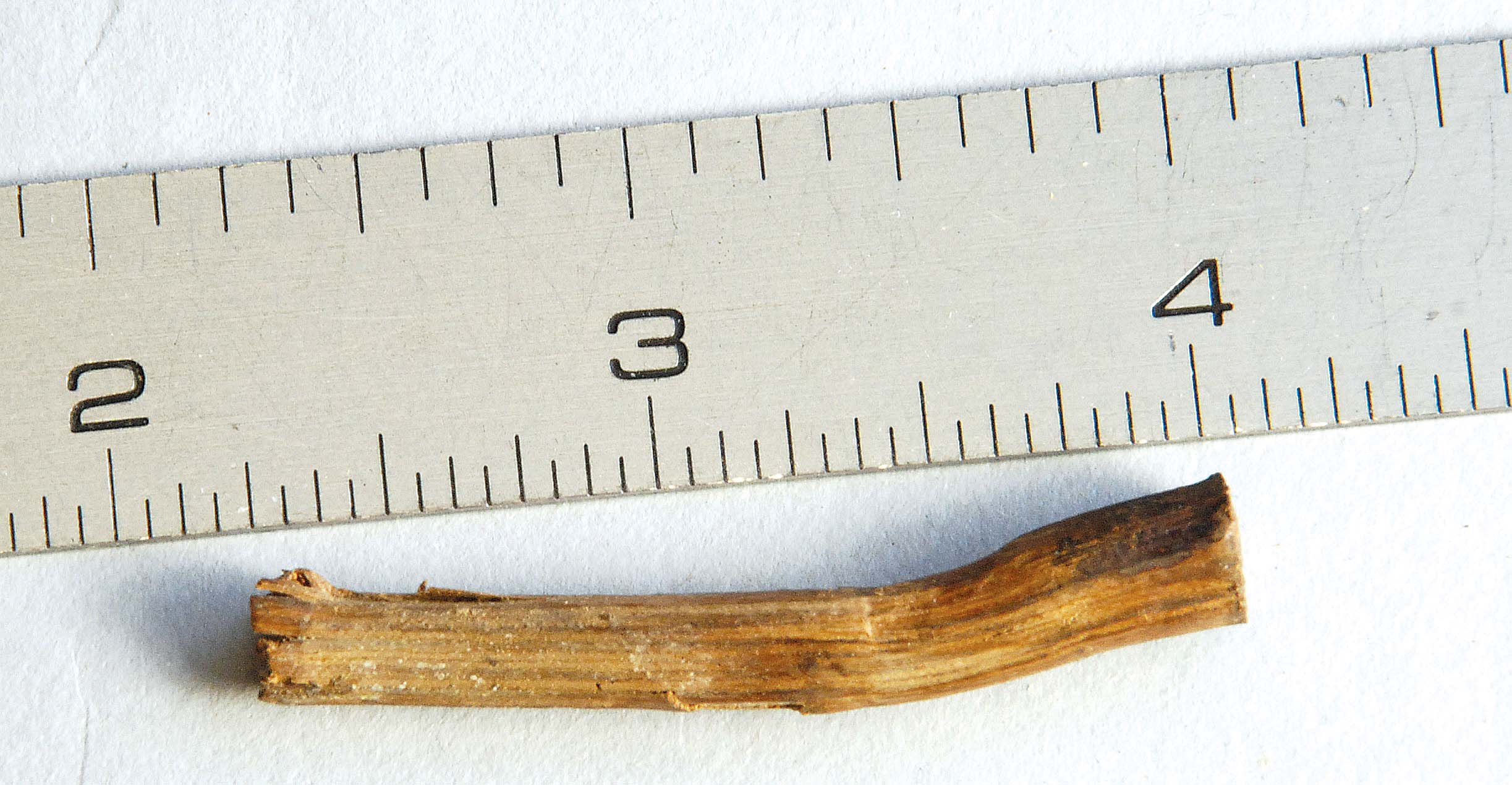
With the test-fitted frames on the bench, mark the tenons for the pins that will secure these joints for the next few centuries. The faces of rails and stiles must be in the same plane. The rails’ outer shoulders should be a tight fit against the stiles’ arrises. The inside shoulders should not touch the stiles.
Check that the apron’s upper edge lines up properly with the marks on the stiles that define the top of the stool. At the stretcher level, be sure there’s no gap in the mortise above the stretcher, where it will be visible in the finished stool. If there is a gap, bump the stretcher upward, shifting the space beneath the stretcher. You might need to check the end grain of the mortise; sometimes it intrudes into the mortise and needs to be cut back so the rail will bump up into its proper position. When all that is checked, scribe inside the hole onto the tenon face with a thin, sharp awl.
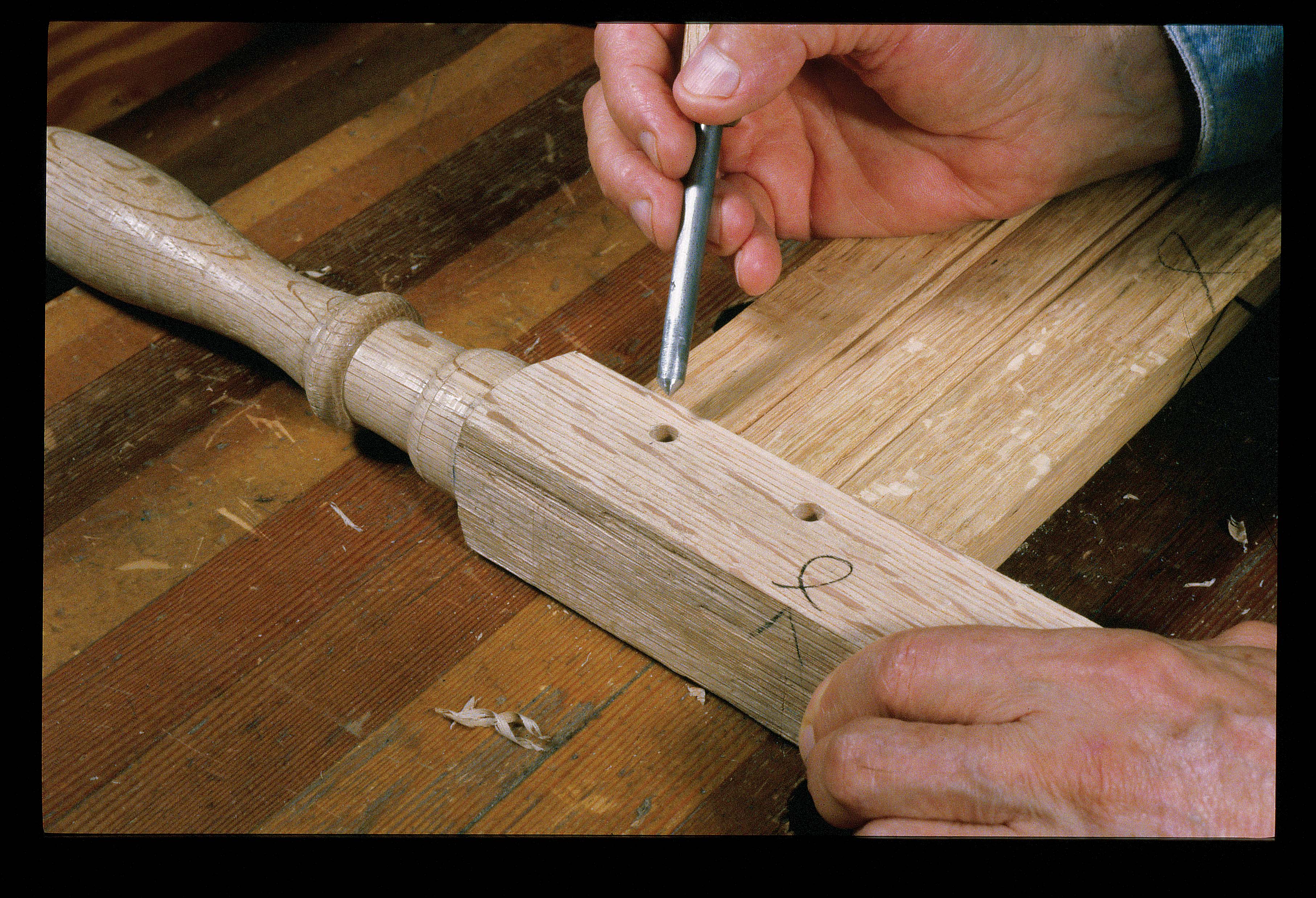
Alexander prefers lightly tapping a centerpunch into the pin hole. Make a punch by pointing the shank of an old drill bit or steel rod that fits snugly into the pin hole.
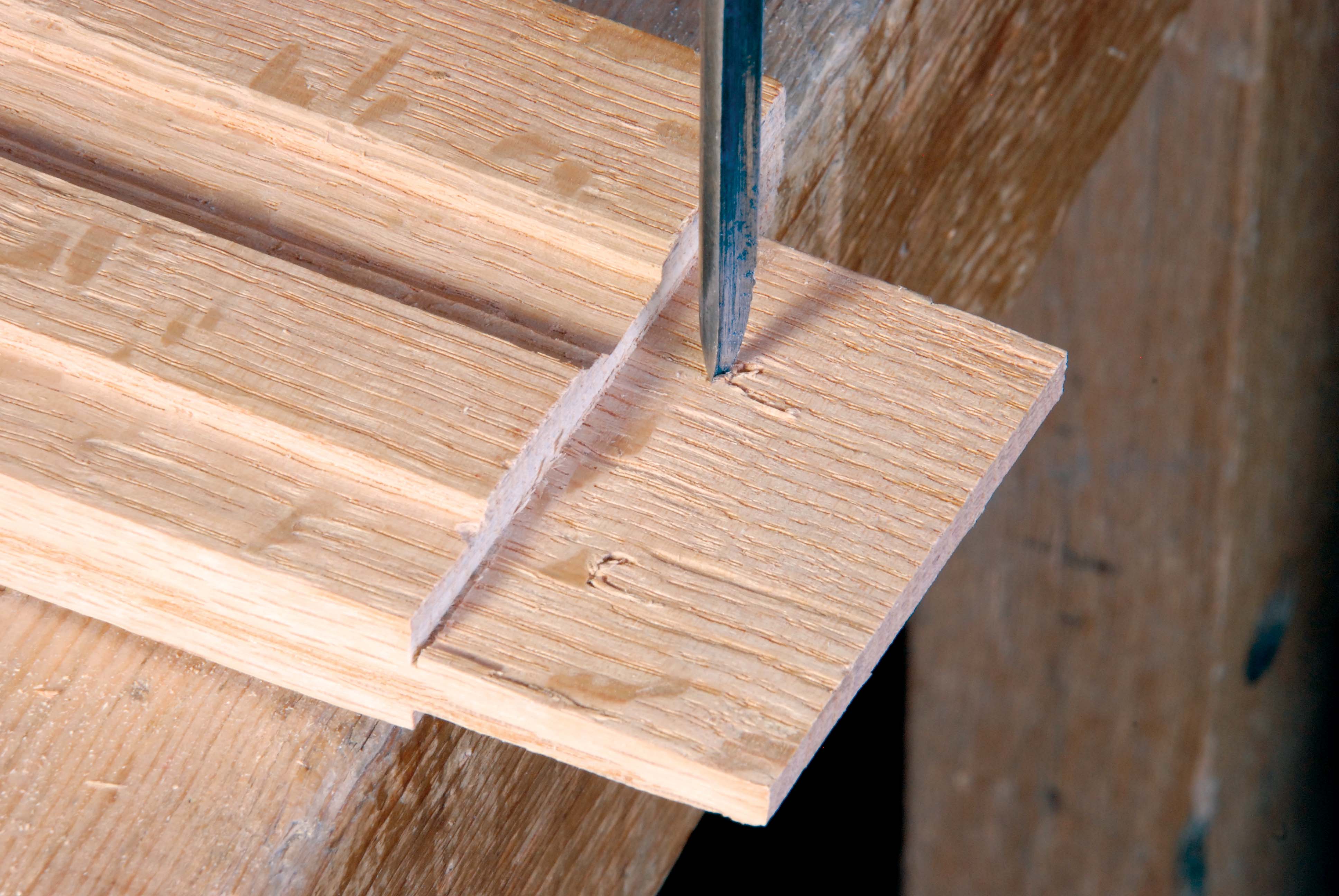
Disassemble the frame and bore the holes in the tenons. It is critical to remember to move in the proper direction – toward the tenon shoulder! You can eyeball this placement, or you might find it helpful to mark the center of the tenon’s pin hole. With the awl, prick the new centerpoint about 1/16″ closer to the tenon shoulder.
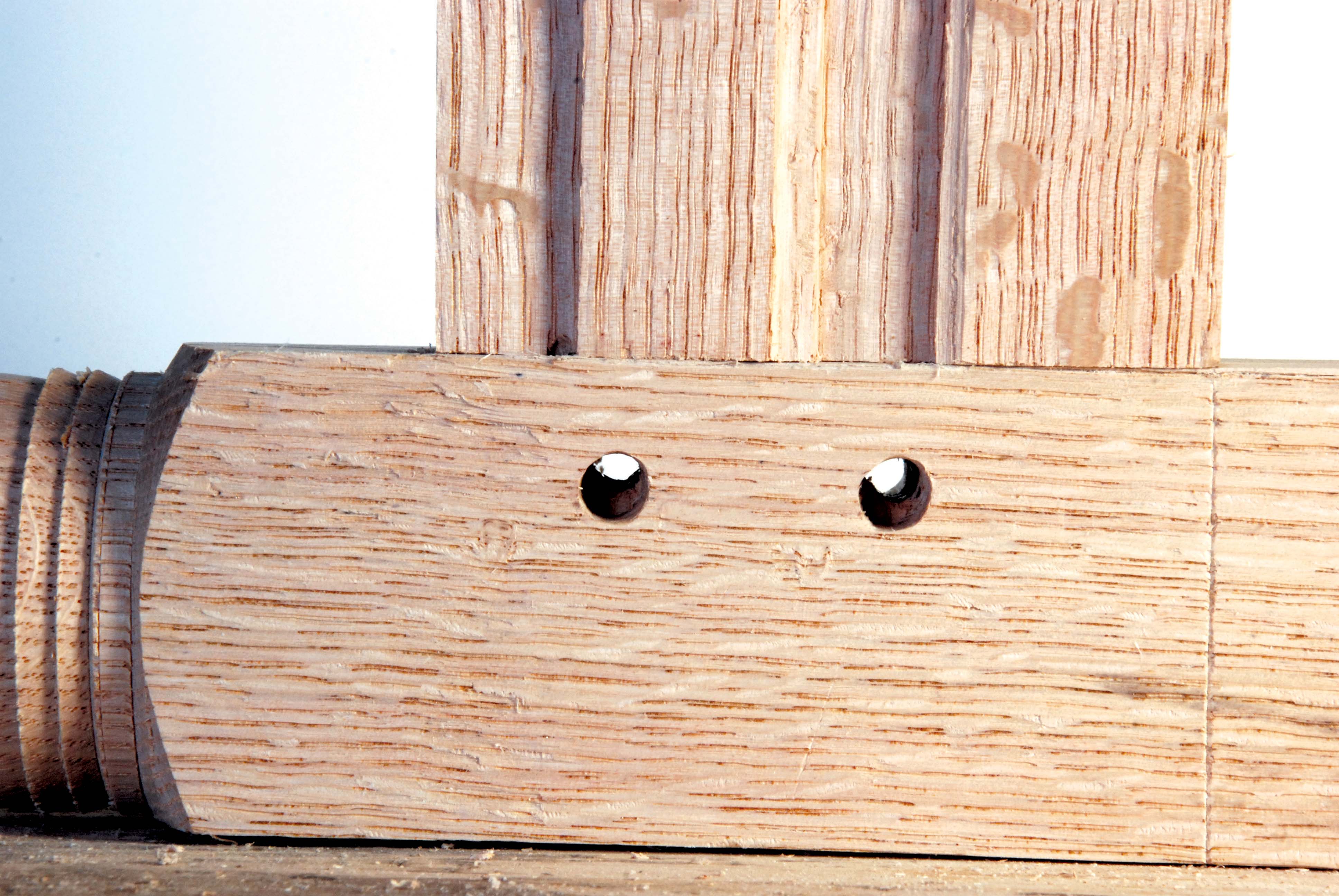
Reassemble the joint and sight through the offset holes. Refer to fig. 6.13 for a general idea of what we’re after; the offset should take up about one-quarter to one-third of the hole. When you have bored all four tenons for one frame, you can test-assemble this frame yet again, and lightly pull the joints tight by driving in tapered metal “drawbore pins.” These pins can be easily made by adapting a machinist’s alignment pin. Any rod or awl that tapers from 5/32″ to 5/16″ along 4″ can be used. Installed in octagonal cross-sectioned wooden handles, they can be tapped in with a hammer and easily removed by hand.
If there is a question about a particular joint, remove the pin and sight through the hole against the light. If the interference is too great, use a handheld square-tapered reamer to enlarge the tenon hole. This tool is nothing but a drawbore pin that has been filed to a sharp-edged square cross-section. You are approaching final assembly. Don’t hurry. Drawboring is the heart of the matter. …
Make the Pins
For the pins to pull the joints together, they must be incredibly strong. Make them from the straightest-grained off-cuts you can find. Alexander and Follansbee have different approaches to pins; we will show you both methods.
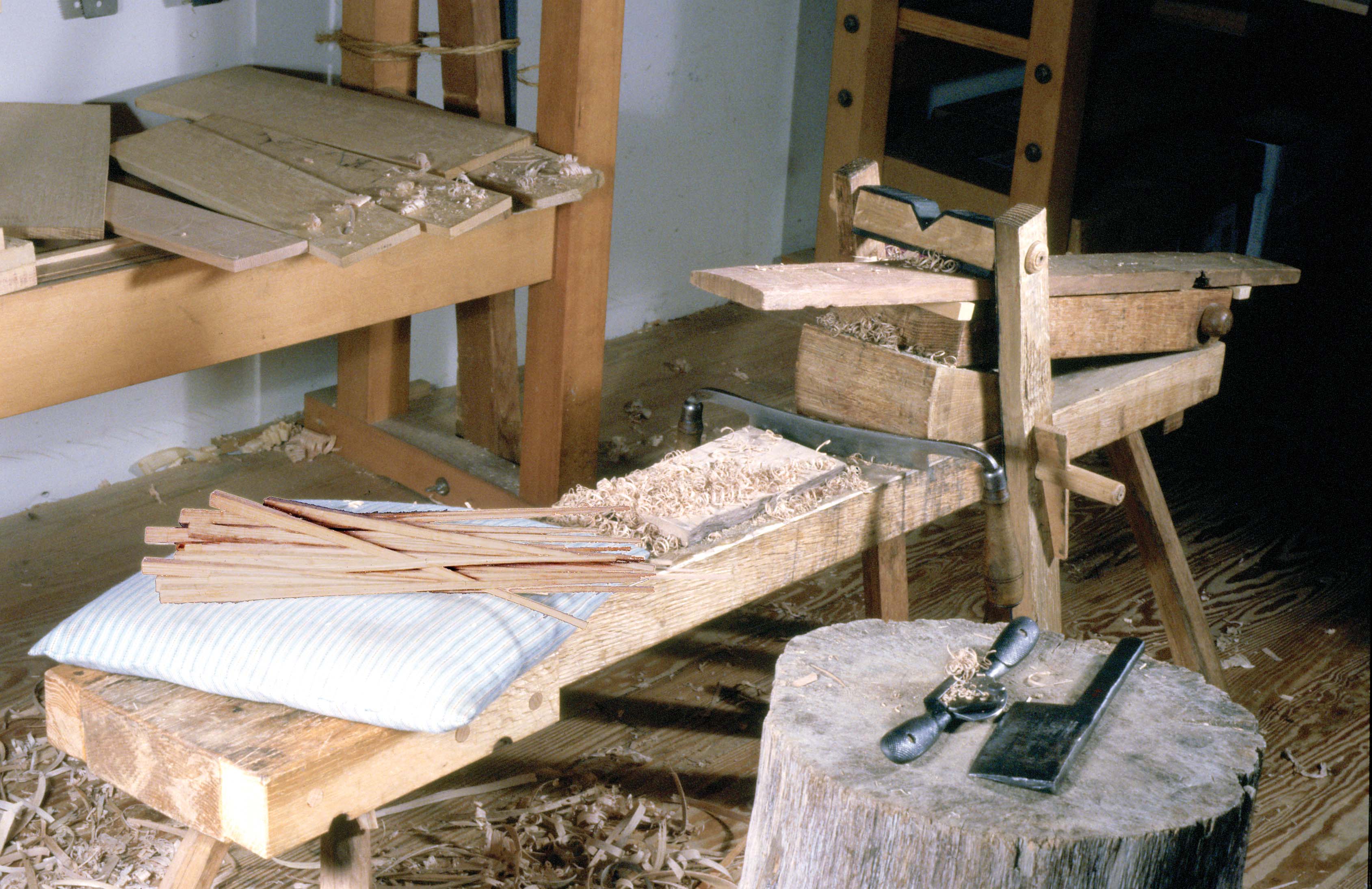
Alexander uses a shaving horse and drawknife to make very carefully tapered long pins from riven straight stock. Select the best straight-grained 15″-long rail stock. Rive this into ½”-square sticks. Hold the stick in a shaving horse and drawknife a 5″-long square on the butt so that the shaving horse can secure the stick and register it when it is rotated 90° at a time. Support the thin stock with a narrow board held under the workpiece. Place the square butt under the shaving horse jaw and make a 10″-long taper. Bore a test hole in a thin board with your piercer bit and taper the pin until it goes halfway through. Try your drawknife with the bevel down and up to see what works best for you. After the tapered square stick is finished, slightly relieve the corners.
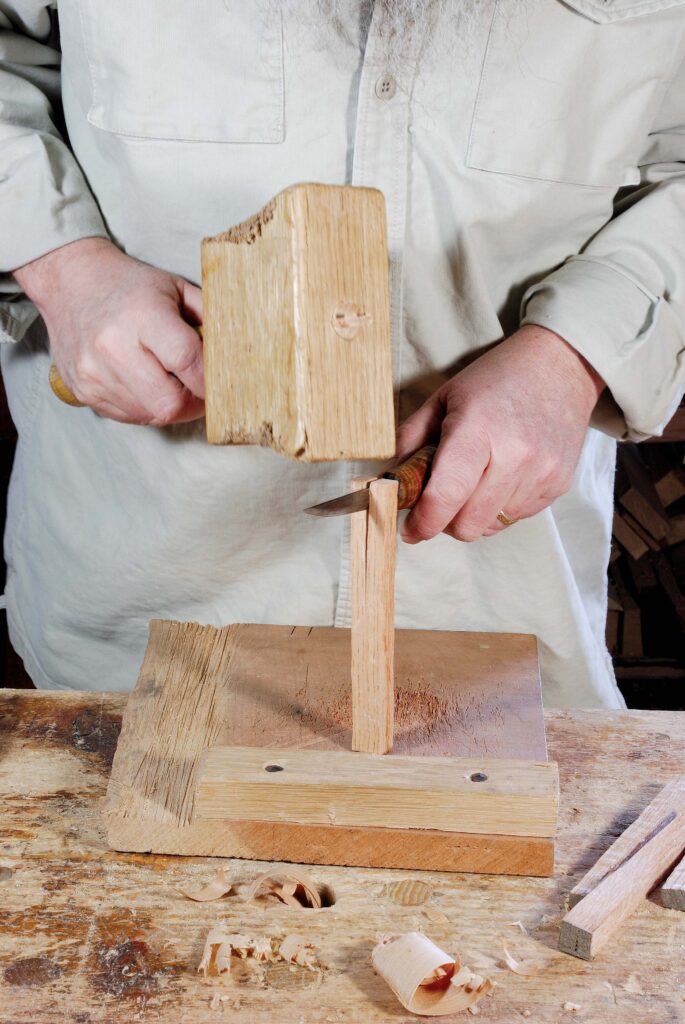
Follansbee shaves pins at the bench from short (5″- to 8″-long) stuff using a large broad chisel. These blanks are riven into sections about ⅜” square using a stout knife or small cleaver as a sort of mini-froe. Hold the blank from its top end and shave downward with the broad chisel. Position the tip of the pin on a piece of scrap wood so you don’t mark up your bench. Working each face in turn, shave them into even squares. Then taper them by paring down with the chisel, taking shavings from each face for an even taper. Sometimes you need to flip the pin end-for-end to get the right amount of taper. Once it’s tapered, shave off the corners so the resulting piece is generally octagonal. Then point the thin tip with your chisel or a knife.
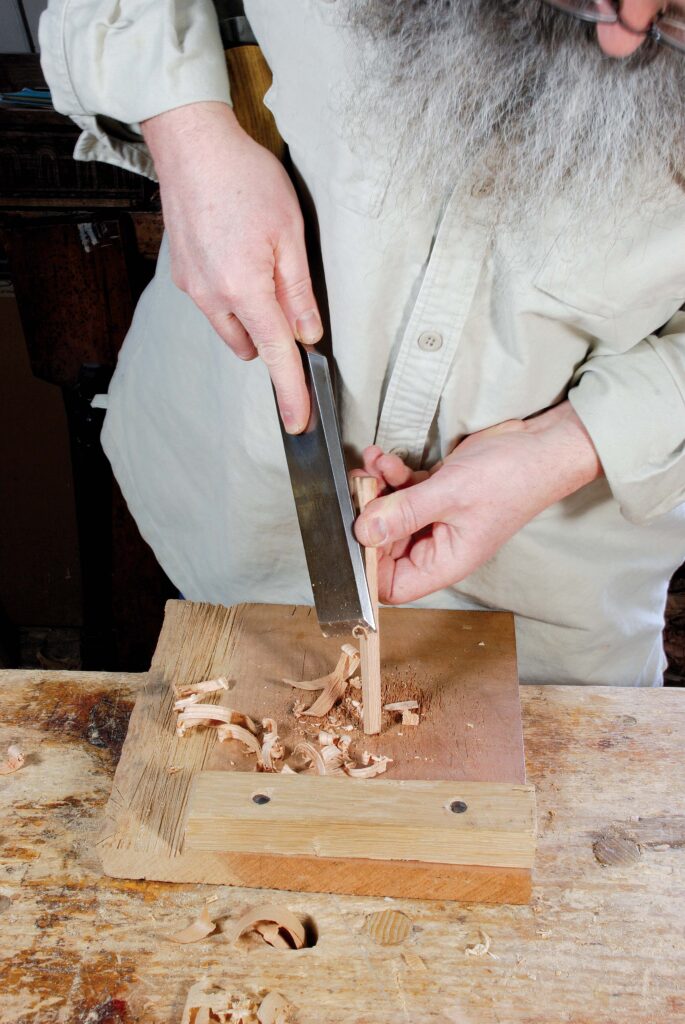
People are leery of shaving small stuff like these pins with a large chisel, but like many of these procedures, body position and movement make this task simple and efficient. For a right-handed joiner, hold the chisel in your right hand with the forefinger extended along the back of the chisel. The chisel is braced in your grip, and your arm is tucked against your torso. The movement comes from your legs. Rise up on your right foot and come down with the chisel in place. With your arm braced against your torso, you limit the travel of the chisel. It is quite a short stroke. This posture provides considerable power and accuracy. With some practice you will become quite accurate and able to shape pins quickly and easily.
I might be over-analysing this but it seems to me that the really clever thing about the fitting of the peg shown in section in the first picture (6.8) is that the woodworker has taken the time to drill the hole at an angle so that it is at right angles to the grain, thus maximising the strength of the joint. Now that is attention to detail!
I bet you anything that apprentices got clouted in the ear for centuries, for not doing that. 😉
Why shouldn’t the inside rail shoulder touch the stile? I’ve always taken great care to make them square especially when making breadboard ends. In fact I have an old breadboard that must be 80 years old and there is no gap on either side. Have I been doing this incorrectly?
I also back up the pin hole when I’m driving a pin through a stile it helps to prevent the pin exiting from blowing out the hole.
I believe that this is a period joinery technique intended to save time in a hand-tool only production environment (e.g. a 17th century joinery business) by putting the full effort only into those bits that will show, same as with only smooth-planing show surfaces. The inside rail will not be visible in normal use of a stool, and therefore does not need to be as precisely fitted as the outside.
This is discussed in some detail in other parts of this book, so I think that the comment in this particular extract stems from the reader having been instructed elsewhere in the book to cut the inside shoulder of the tenon to be not-touching, which means that if both inside and outside of the rail were then made to touch the stile when laying out the drawbore, the mortise and tenon would line up incorrectly.
It is of course perfectly possible to make both inside and outside fit just so, but by hand it is more work, which takes more time, which in a production setting is a cost. This does not matter so much to the modern amateur/hobbyist hand-tool woodworker, for whom time is not a business cost, while I think the absolute majority of modern production is made with the help of machines that in general terms make it just as quick and easy to make both sides fit to a T.
This explanation makes sense. I have also seen Richard Maguire mention and show this in his various videos that I have purchased. It is definitely a time saver in a hobbyist hand tool shop.
I found one of Richard’s posts I was discussing. Good read, and Richard’s proof is in the pudding as they say:
https://www.theenglishwoodworker.com/gappy-joints-speed-strength/
I’ve seen Richard’s instruction as well. I was taught the same back-gappy fitting years ago. It really is a time-saver. The first application for me was stretcher-to-leg fitting. Looks perfect where it counts, save labor costs where THAT counts.
With the greatest of respect, that’s not what they say – or at any rate it shouldn’t be 🙂
The saying goes “The proof of the pudding is in the eating.”
Tom,
I am not speaking for anyone but myself when I say this, others including Peter and Jennie might have or had a different reason or opinion. Here is my reasoning as to why I do just that.
The inside of the panel, underside of a table, or the no show face of a breadboarded cutting board should not touch the stile. I do this so there is not any interference from the inside shoulder. This allows the “show” joint to be tight and true. I leave a gap of about 1/64 to 1/32. Just enough to hang a finger nail in. If you leave a gap larger then this you risk splitting the stile.
I hope this is clearer then mud!
John
If one side is longer than the other, you can be sure that side is going to make contact, and with that much of a gap the long side will compress a bit, shutting off any imperfections in the edge and making it the tightest possible joint.
This only works, of course, if only one side of your joint is going to be showing, like on the rails of a table (which is where I normally see people talking about them).
Also, I think there’d be an issue with breadboard ends “racking” because the tenons are generally relatively thin, meaning you might make the ends off-square.
Perfect timing. I am just preparing for drawboring some wedged, but overly sloppily fitted through tenons on a commercial workbench that have come loose. Looking forward to using this for guidance.
Thanks for all the reply’s, now I understand what the principal is.
I cut my tenons ( collective gasp) on a table saw! It’s most practical to make your shoulders square, to make one shorter is much more work using machines. In my case I’m making a 10’ breadboard for a kitchen cabinet base. There is no reason to have it out of square in fact that would create issues for me. Then again I’m more machinist than woodworker, (oh woe is me). Anyway I’m a little bit smarter now but I’m certainly not a purist.
Tom,
Using machines to shape wood has been a thing since the 11th century. And it takes just as much skill to do well.
I am so weary of the electron-shaming. You’re a woodworker, Tom. Don’t let anyone convince you otherwise.
Lately I kind of choose power or hand tools based on size and or how many of something I am making. Last breadboard I made was a dining table out of solid walnut. I used a dado stack on the TS and router table for all the joinery. And like you mentioned, its machined perfectly. I could swap breadboards end to end and they would fit. The current stool I am making i am using all hand tools and each leg needs to go in the right spot. Its like with other hobbies. I like to kayak and mountain bike. But I drive an SUV somewhere to take them out. I rarely ever ride my bike for actual transportation. All tools have their place, its kind of fun learning how to use them all. Currently getting into japanese hand tools which is another animal.
Just to be sure there’s no misunderstanding, I just wanted to add that my previous comment to this post was of course not in any way whatsoever intended to express or imply any disdain for machine-based or -aided woodworking, or to take whatever sort of purist position; I only wished to try to help clarify the context of the excerpt from the book (which, as it happens, I am at the moment halfway through, concurrently with my annual re-read of The Lord of the Rings).
As for my tenons, I cut the cheeks either by hand or on the bandsaw, but the shoulders always by hand, because I don’t have a (full-size; I do have a micro one for scale model work) table saw, nor a router, nor owt else electron-fired that’d do the job, and as a happy hobbyist, I can permit myself to take the additional time to (try to) make all the shoulders fit just right (though not interchangeably so) even by hand.
I think, though, that at some point shall have to give the undercut inside technique a try-out — who knows, I might like it?!
Cheers,
Mattias
This is a magnificent book and record of a decades long friendship that might never have seen the light of day if not for Lost Art Press. Peter Follansbee is a wonderful writer—pithy, clear as straight-grained oak, and you can kind of hear him talking as you read. Much respect to all involved. And now it comes in a dang slipcase! Well done LAP. If I didn’t have this already I’d buy it again.
Hi David,
The new edition isn’t in a slipcase (I wish we could do that). Instead, it has a hardbound cover that has paper glued to it (like “Grandpa’s Workshop”). The interior paper has been upgraded to coated matte stock. And the binding is the same: Smyth-sewn. Hope this makes sense.
Ah! Of course. Apologies for sloppy reading. You all are more or less notorious for the design and print quality of your books and I’m sure this one’s no exception. Congrats on the new printing… and on finding paper for it!
The first picture in this post is gorgeous. The grain of the wood, the rays, the open pores, and the perfect fit of the pin at the bottom are as satisfying as anything I’ve ever seen.
I really like the photos in the book. I’m assuming Peter did the photography, too. I’ve been lucky enough to manhandle the stool on the cover multiple times. The experience really didn’t add much that the photos and text didn’t already convey. Hmm, except, I guess, for unintentional bragging.
Fantastic book to get over any fears of green woodworking. I used it as the guide to making a coffee table and it’s nearly all hand tools. I’ve used the bandsaw to rip my riven oak to closer dimension. Especially the top. I’ve hand planed the top and have purchased a 10″ jointer so I don’t have to again!