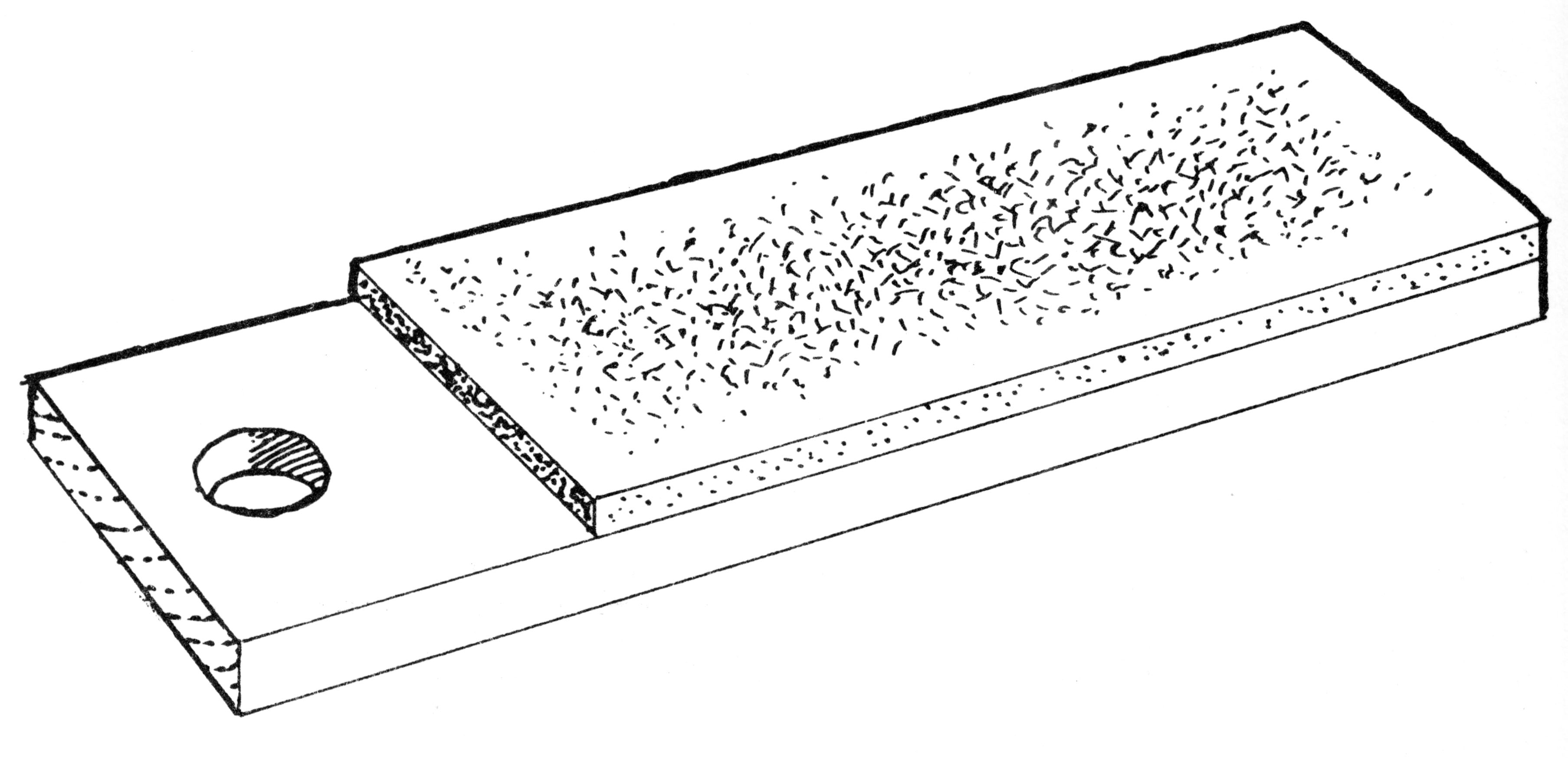
Editor’s note: Following the success of “The Essential Woodworker” – our second-bestselling time of all time – we worked with Robert Wearing to republish a book filled with some of his best jigs, fixtures and appliances for handwork. During his career, Wearing had published two books of jigs for woodworking (both out of print), that are filled with insanely practical and simple devices.
With Wearing’s help, we picked out the best jigs for hand-tool woodworkers from his two books and compiled them into one volume: “The Solution at Hand: Jigs & Fixtures to Make Benchwork Easier.”
Just like with “The Essential Woodworker,” we had to recreate the book from scratch – all of the text, photos and drawings had been long lost to the publishing machine. And once again, the royalties to this book went to help Wearing, who was in an assisted-living home, after an incredibly rich and long career.
You can read more about Wearing’s life in this lovely 2017 profile. Shortly after “The Solution at Hand” was published, Wearing died at age 99 (read our obituary here).
The following tools are selections from Chapter 3: Tools, of Robert Wearing’s “The Solution at Hand: Jigs & Fixtures to Make Benchwork Easier,” a hardbound book of our favorite jigs from Wearing’s career. The book covers a wide swath of material, from building workbench appliances for planing, to making handscrews (and many other ingenious clamps), some simple tools that you cannot buy anywhere else, to marking devices that make complex tasks easier.
In all, there are 157 jigs, all of which are illustrated with Wearing’s handmade drawings. The book is designed as more of a reference book than something you read straight through. Already after editing the book, I now find myself returning to it and thinking: I know Wearing had a solution for this problem. And he did.
— Christopher Schwarz
Oil Pad
“Park your plane on its side lad.” This is a folk custom dating back to the age of wooden planes. The blades of these planes were firmly held by a tightly hammered in wooden wedge. Following this advice, however, will disturb the lateral setting of an iron plane whose blade is nothing like so firmly held. Instead park the plane on the oil pad made by gluing a strip of carpet to a plane-sized board [Fig. 1, above]. This is a tidy arrangement which both protects the blade and reduces friction. Very little oil is needed.
Beam Compasses
This excellent and virtually cost-free tool is shown assembled at Fig. 9 A. In constructing it, first machine an overlength piece of square-section material, say 5/8″ x 5/8″ (16 mm x 16 mm). Cut off five pieces to make respectively, pieces a, b, c and d. All except d are sawn in half. The inside ends of c and d are finished quite square and all other ends are angled. Glue the a pieces to the stem and c and d between the b pieces using a short waxed block cut from the stem as a spacer. Hold the pieces together flat on a piece of polythene sheet. Drill a hole in end B for a pencil or ballpoint, the latter is often better, then drill a small terminal hole of 3 mm (1/8″) and a lateral hole for the clamp screw. A brass roundhead 12 gauge x 1-1/2″ is well suited for the cramp up. Drill halfway at 1/4″ (6 mm). Drill the remaining distance at 1/8″ (3 mm). Saw the slot with a saw having a wide kerf. Screw up and test with the chosen pen or pencil. File off any protruding screw point.
A similar routine is adopted for the sliding point unit. There are several possibilities for the clamping screw. Either put a clear hole halfway through and tap the other half 1/4″ BSW, or metric equivalent. Use a thumbscrew to tighten or make one by soldering a wing nut on to a piece of screwed rod. Or solder a wing nut to a brass woodscrew. Screw in a normal woodscrew first, then replace with the one made up. Or drill clear holes right through and use a 1/4″ (5 mm) coach bolt with wing nut.
The point can be made by grinding up a piece of silver steel of about 3/32″ (3 mm) diameter. Clean up the whole job, lightly sand and finish either with a polyurethane varnish or teak oil.
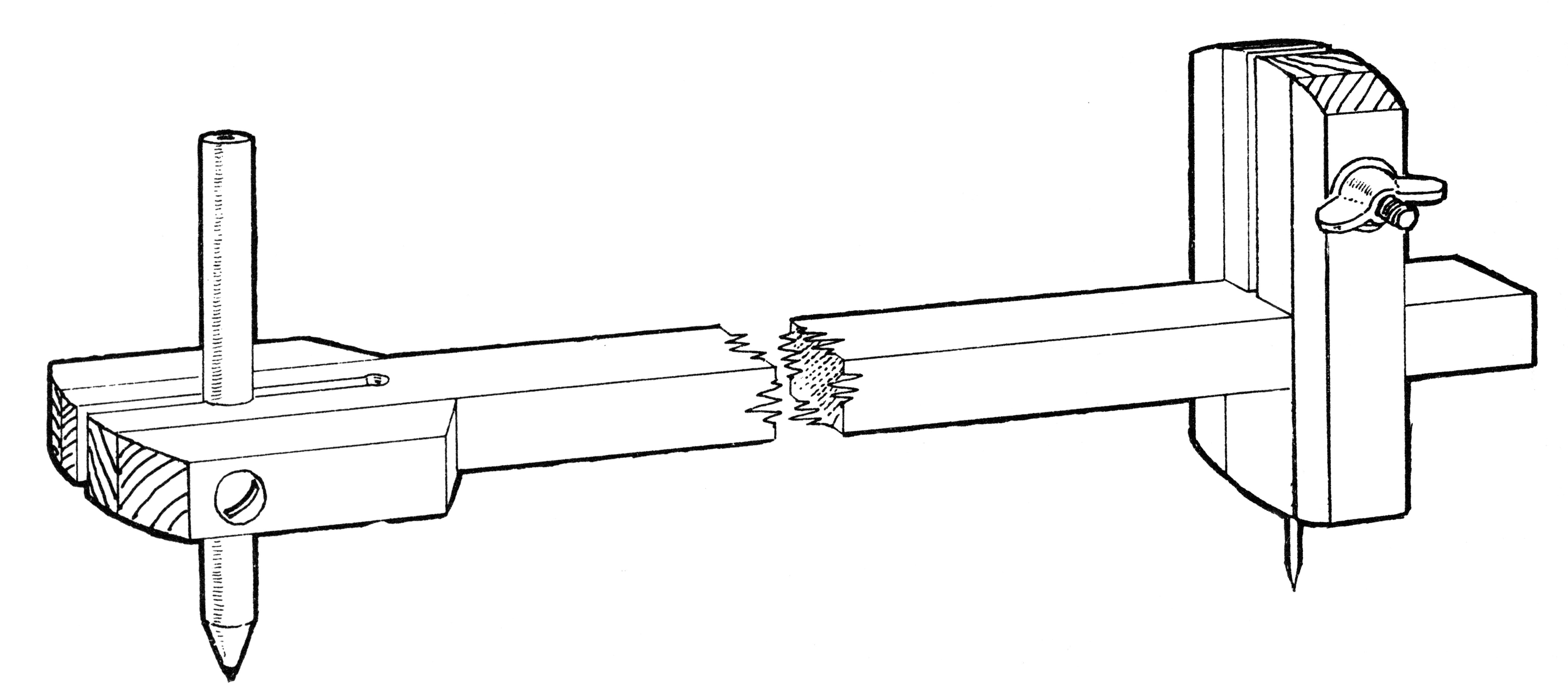
Awls
Of this large family of tools from the days of handwork, only the bradawl remains in the catalogues. The convenient materials for making awls are tool steel, silver steel (commonly stocked in good tool shops) or old or unwanted screwdrivers.
The bradawl, A, is most used for screw holes and is either filed or ground on both sides and after hardening and tempering is honed to chisel sharpness on the oilstone.
Marking awls, B, are made out of thinner material ground or filed to a long, fine and round point. Small electrical screwdrivers with plastic handles convert easily. This awl is not really suitable for work other than marking as it cannot remove wood.
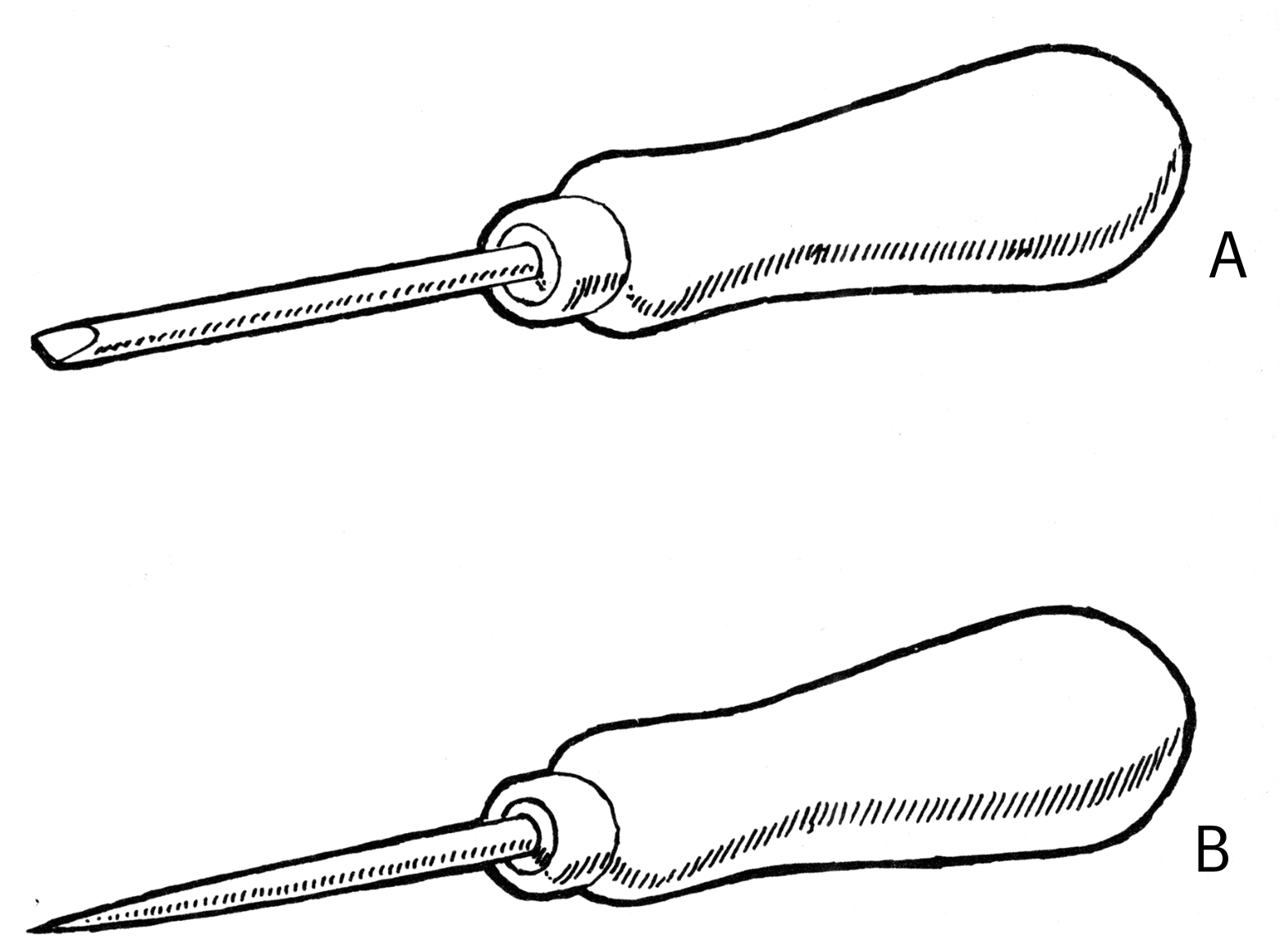
The four square awl or small hand reamer, C, is useful in the bigger sizes for enlarging holes and in the smaller sizes for making pilot holes for small screws. It is filed really square in section and after hardening and tempering is carefully honed to give four keen cutting edges. It can be made from either round or square material.
The hooked awl, D, is particularly useful for marking out the second stage in dovetails. A good material for making these is old-fashioned steel knitting needles.
Turned hardwood handles with ferrules are well worth the trouble taken. Fit the blades into the handles by drilling slightly under size, filing the end of the awl to a chisel shape and then driving on in a vice. If the section is big enough the handle and blade can be drilled through and pinned.
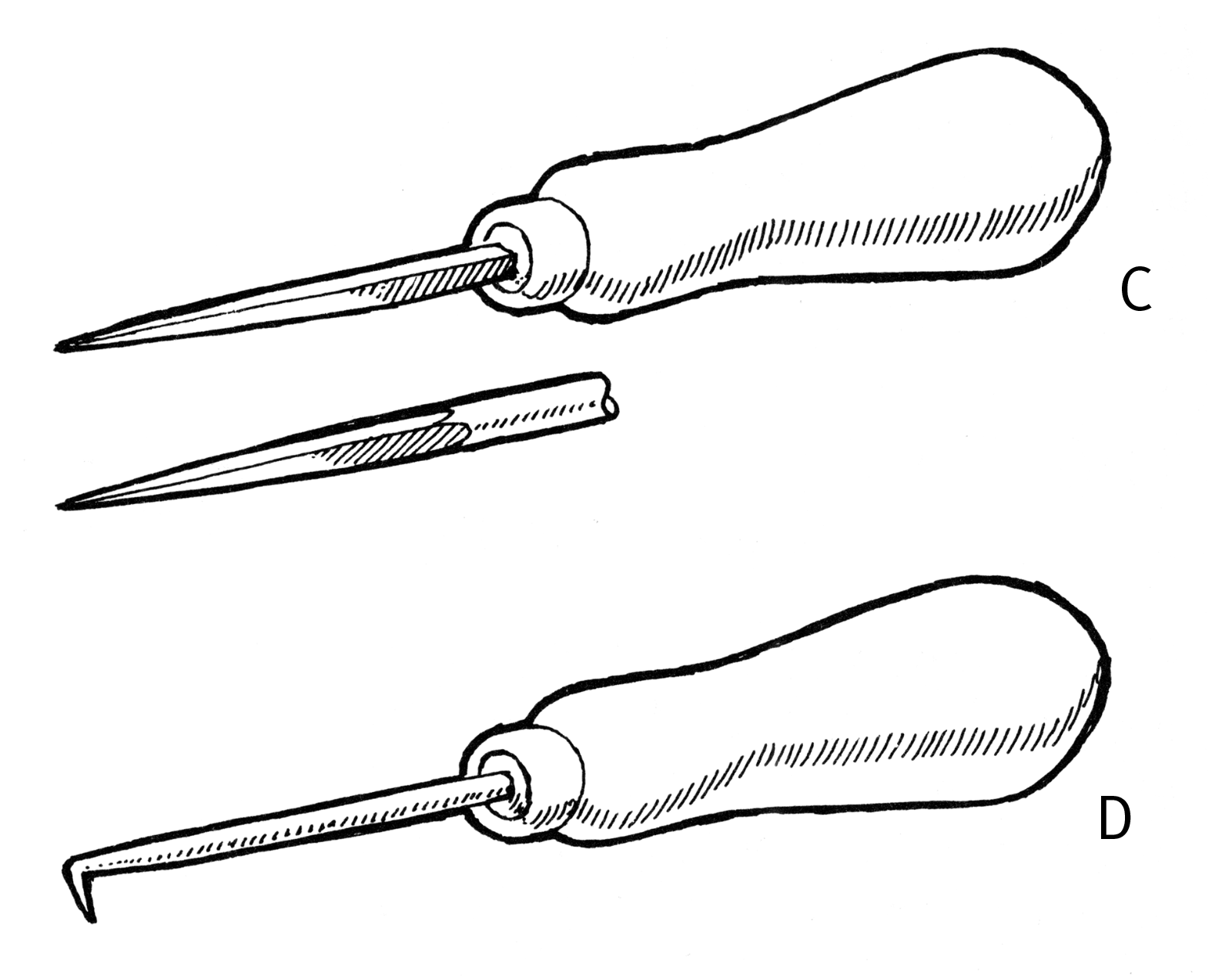
The hooked awl for marking dovetails is intriguing. Has anyone ever tried it?
I have! It was a common form in the late 19th and early 20th centuries. It is ideal for marking out full-blind dovetails. At the transfer point from tails to pins, it’s almost impossible to get a marking knife in there to park the pins. The hooked awl has no problem whatsoever.
Mine has a chisel-like blade at the tip. So it cuts like a marking knife instead of scratching like an awl.
Thanks! On the rare occasion I’ve done full blind dovetails I’ve used an oddly shaped xacto blade.
Can you share from what you made the hooked awl?
Tom Lie-Nielsen made it for me 100-odd years ago. It’s designed to fit into a tool handle. Here’s a photo:
https://www.dropbox.com/s/pmlazmm0ze9ua9i/IMG_4325.JPG?dl=0
Most excellent, thanks. Very different from what I was thinking.
I found a copy of Wearing’s “Making Woodwork Aids and Devices” and it, along with “The Essential Woodworker” are invaluable resources. I will happily purchase this new volume to add to my knowledge base. Wearing is a treasure – thank you Mr. Wearing for sharing your vast and valuable knowledge and thank you Lost Art Press crew for doing what you do to keep this info alive and available!