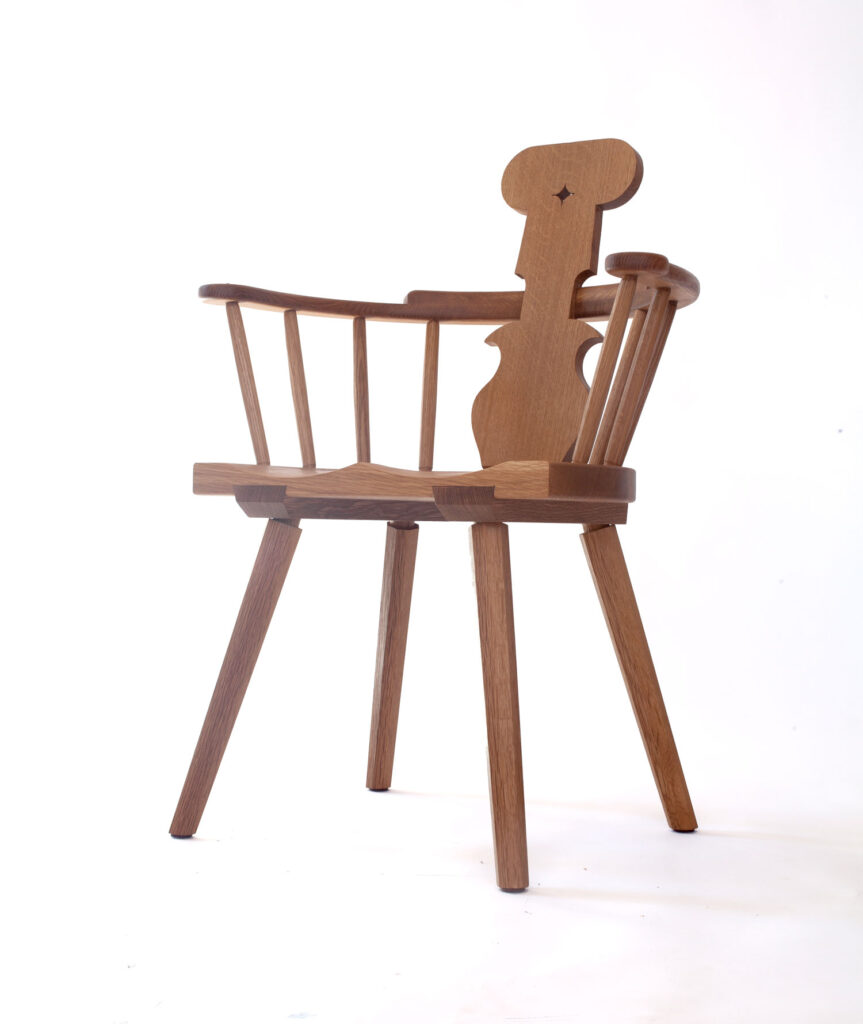
My latest chair is a white oak backstool/armchair that is inspired by the chair that Bilbo Baggins sits in during the opening of “The Fellowship of the Ring.” This full-size chair is by no means a copy of that chair, however. Read on for details.
With a seat that is 17-1/2” off the floor and a back splat that is tilted at 12°, this chair is set up for keyboarding, dining, drawing or writing epic tales. It is about as comfortable as you can make a backstool, which has a solid backsplat.
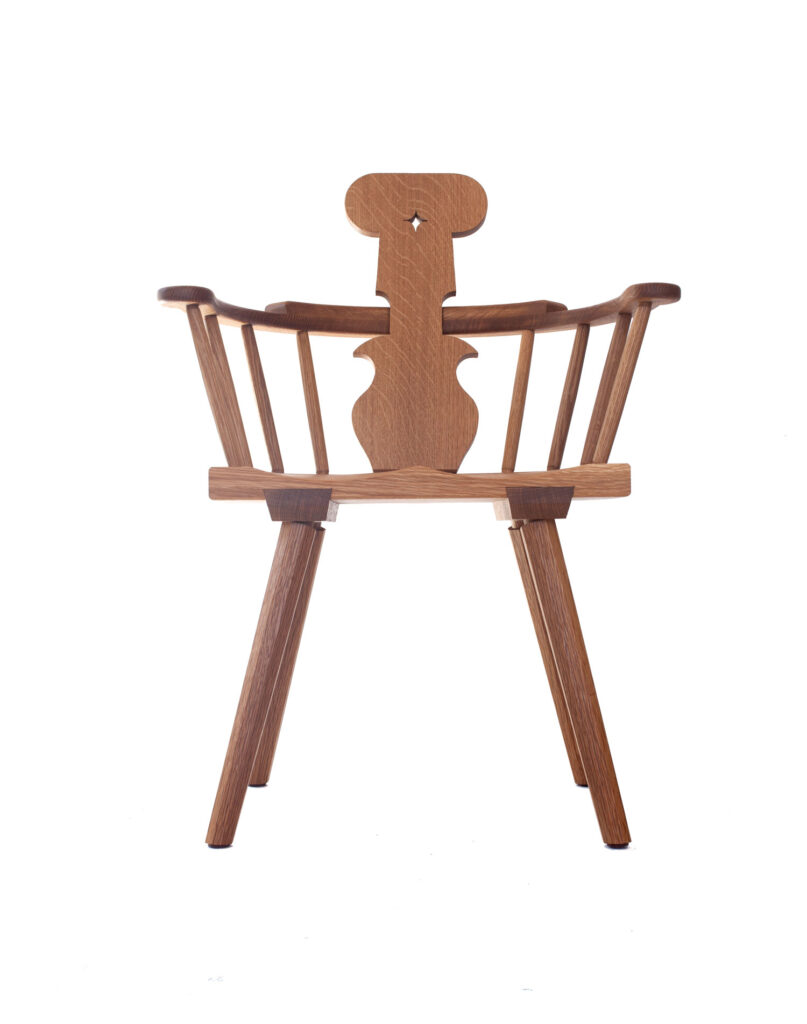
The chair is 35” high, 26” wide and 22” deep, making it fairly compact. The undercarriage is Swiss/Germanic with reverse-tapered legs that are tenoned and wedged into solid oak battens. These battens are then joined to the seat with sliding dovetails.
The seat is lightly saddled, as per most vernacular chairs. The short sticks are shaved octagons. The chair’s hands are based on many Irish chairs I’ve inspected. The tenons through the hands are left proud and knifed to shape.

The chair’s backsplat is tenoned into the seat and then let into a large notch in the armbow.
All the joints are assembled using hide glue, so if anything ever becomes loose, it can be easily repaired. The finish is a blend of organic linseed oil and beeswax. This is not a durable finish. But it takes on patina quickly and is easily repaired.
So what’s different about this chair from the one in the movie? Lots. The battens are a different shape and are joined to the seat with sliding dovetails for durability. The turned sticks on the movie chair are shaved on my version (and I added two more sticks). The one-piece arm in the movie chair is replaced with a three-piece armbow. And my hands are a different shape.
I can’t tell if the chair seat from the movie is saddled because it is covered in a cushion. I saddled mine.
The chair is $1,300 plus actual shipping via common carrier. Shipping typically runs between $100 and $225 depending on where you live. Delivery within 100 miles of Cincinnati is free – or you can pick it up at our shop in Covington, Ky. If you are interested in the chair, send an email to fitz@lostartpress.com. Ask all the questions you like, but the first person to say “I’ll take it” gets it.
I’m working on another one of these chairs right now, and it should be up for sale in a week or so.
— Christopher Schwarz
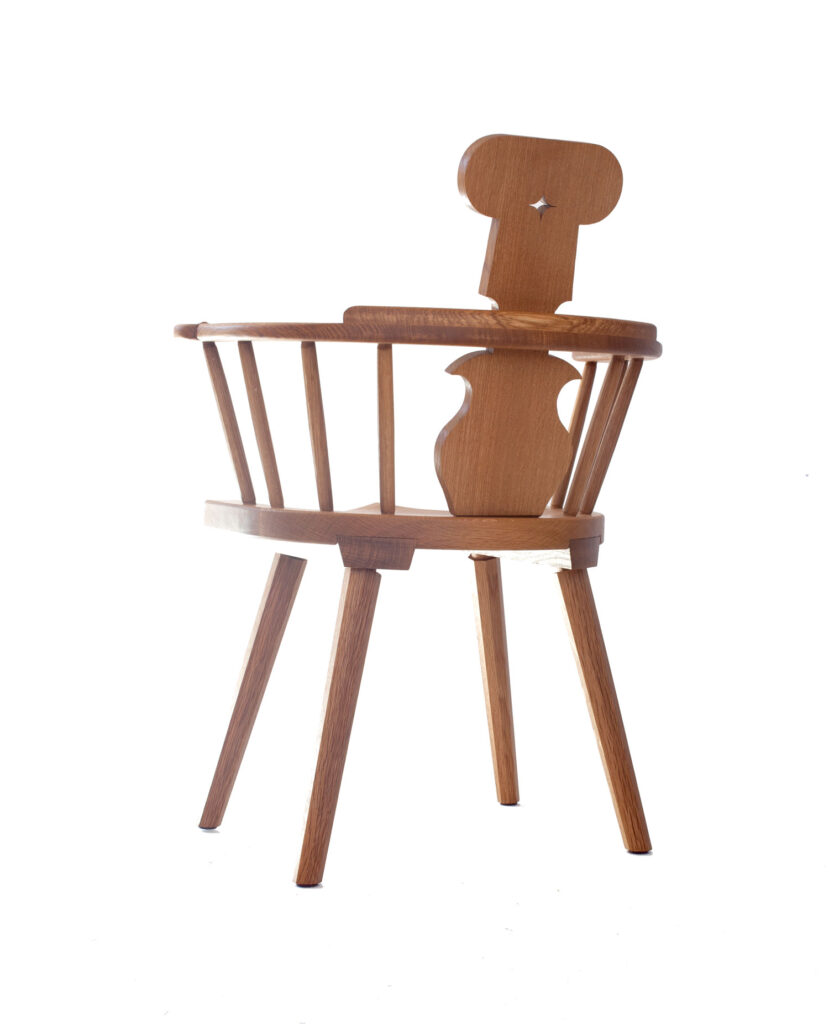
Hello, is there a place where i could learn how to do the dovetail seat part ? i’m not a cabinet maker and i have troubles finding some good explainations… (and if there is some in French it would be fantastic….) In France these kind of chairs is called “chaise alsacienne” , you can find many sample on antic dealers websites…To be honest for someone who is quite new in wood working those dovetail are quite freaky-spooky, i don’t even know if i would need a special plane to do it ore if there is a super trick…Thank you and have a nice day (P.S: Very much loved the video of your heaven-ish work shop).
Hi Jonathan,
I show how do do it in “The Anarchist’s Design Book,” but I am sure there are lots of places to learn to make the joint.
The chair that uses this joint is common called a brettstuhl. So you might search for techniques using that keyword. Peter Follansbee showed how he did it in these posts:
https://pfollansbee.wordpress.com/?s=brettstuhl
My method is simple. I make the battens and plane the long edges to 12°. Then I use the batten as a guide for my handsaw. I clamp the batten to the seat, press the saw’s plate against the angled edge and saw the angled sides of the sliding dovetail.
Then I use a chisel to pry out most of the waste. Then I clean the bottom floor of the sliding dovetail with a router plane.
There are special handplanes that cut this joint, but they are not widely available in this country.
Hope this helps.
This helps a lot, thank you very much.
Hey Jonathan, don’t feel bad. I have been woodworking for over 30 years and those dovetails still scare me too. In fact, I am too scared to build a chair in general. I am used to building things more box shaped, squares and rectangles.
The legs of this chair are attached to the seat with battens, vs. directly to the seat itself. How do you determine which method to use? In viewing the photo, I would imagine that the seat is likely too thin, and thus not enough anchoring space for legs.
It is mostly a cultural and material issue. The battens are found mostly in Germanic and Scandinavian countries. Tenoning the legs directly into the seat is more common in the UK.
However, battens are used in any culture when the seat is too thin. The battens thicken up the seat without creating a problem with wood movement.
Hope this helps.
I made a version of Chris’ desk from ADB. Since I only have the LN small router plane and no big one, I kerfed the joint. Then, used a narrow chisel and the small router to clear out the outside edges of the dovetail. Then used a wider chisel and my jack plane to clear the middle of the dovetail. The process was cake. What was tricky was making the dovetail the correct width. I messed that up making it too wide 🙁 and am still not quite sure how to get it right.
Oh my word… that is a beauty. Even if not covered in red paint. 😉 While it probably wouldn’t LOOK as nice (and maybe it would weaken the armbow too much?), do you think recessing the backsplat into the armbow might make such a chair more comfortable for leaning back a bit and pondering in? I apologize if that’s a dumb question. I have gathered from your posts that different back angles lend themselves to different seated activities, so maybe a chair of this type is just meant for sitting up fairly straight in, or leaning forward to write/draw, and pondering is best done in a different chair type.
The back splat is mortised into the arm, but it is not flush with the arm. I have made it flush with the arm before and it does lend some support, but it can weaken the arm. So it’s a balancing act to be certain.
This would look nice paired with a hobbit drink stand or taboret (what ever that would look like?).
how is the back splat attached to the arm bow? Bamboo skewers? Screwed from the back? I am guessing the order of operations, is build the seat and arm bow, drill for the spindles, dry fit the arm bow, then lay out the backsplat?
The arm is notched around the backsplat. The arm, backsplat and sticks were all finished before assembly. And it was glued up in one go.
Hi Chris,
I’m curious about the leg tenons. Do the mortises extend into or through the seat?
-John
PS, just wrapped up The Stick Chair Book. It’s a great read and worth the wait!
The tenons stop in the battens and are wedged in place.
I assumed “reverse-tapered legs” would mean the opposite of the norm – ie. thicker at the floor and thinner near the seat. These look like the typical sort of leg taper. I gather I’m missing something.
Never mind. I gather you mean the reverse of the typical stick-chair/welsh chair sort of leg.