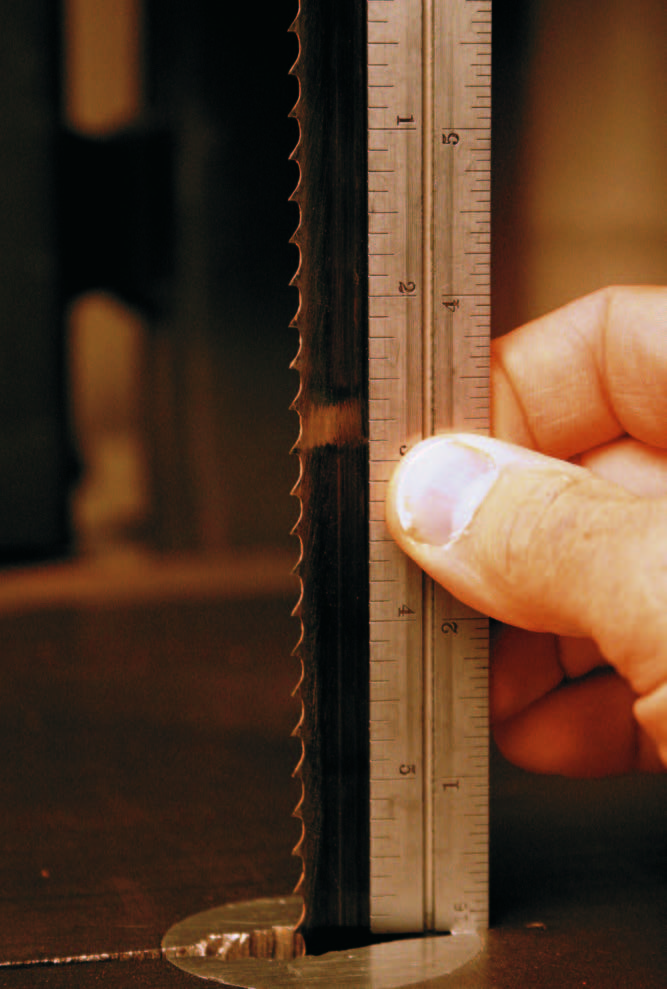
Editor’s note: When I first encountered this book in the 1990s, I read it reluctantly. I wasn’t much interested in making wooden planes, but I was still in the “I’ll read anything about woodworking” phase. About 10 pages into the book, I was hooked. This isn’t just a book about making planes, this is a book about setting up tools and machines to a very high level so you can do truly excellent work (such as making planes). I read and re-read the book several times, loaned it to friends and eventually wore it out.
When the book went out of print, we were thrilled to bring it back with David’s help. The Lost Art Press hardback edition is made in the United States with pages that are stitched, glued and taped. I seriously doubt you could wear it out. But feel free to try.
David is still an active woodworker (and nice guy) and focuses on violins now. Check out his work here.
These wooden planes are associated closely with James Krenov (who wrote the book’s foreword). We published the definitive biography of Krenov by Brendan Gaffney: “James Krenov: Leave Fingerprints.”
The following is excerpted from David Finck’s “Making & Mastering Wooden Planes.”
Use sharp 1/2-inch-wide, 4 teeth-per-inch (TPI) wood-cutting blades. Hook-tooth blades cut faster and rougher, and skip-tooth blades cut smoother and more slowly. Skip/hook-tooth blades (sometimes called “furniture bands”) are a hybrid that I prefer, combining adequate speed with a smooth cut (1–13).
Critically examine the blade weld. The sides should be smooth and free of lumps. Check that the blade was properly aligned when welded by gauging the back edge of the blade with a six-inch straightedge; it should present a straight line (1–13). Faulty welds are fairly common and seriously undermine the performance of the saw. The blade may bump and shudder each time it contacts the thrust guide. A lump in the weld may prevent the side-mounted guides from being spaced closely enough to support the blade adequately. Keep blades and tires free of gummy deposits and sawdust. Scrub them off with the metal bristles of a file card at the first sign of buildup.
Set the upper and lower saw guides precisely. Arrange them as close as possible to the blade without rubbing it. The side-mounted guides are positioned just behind the gullets (the arcing gaps separating each tooth) of the blade (1–14). The guides on the back of the band saw, the thrust guides, contact the blade as soon as sawing commences.
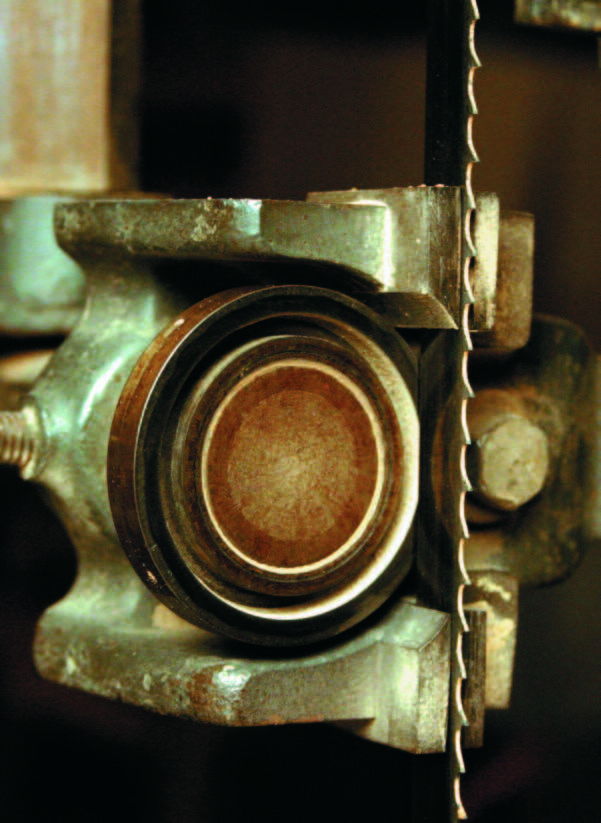
Tensioning the blade correctly dramatically improves the quality of cut. Unplug the saw and remove the upper wheel cover. Tension the blade while slowly rotating the wheel by hand to stretch the blade evenly. Occasionally twang the free section of the blade (the portion unencumbered by guides) and note the increase in pitch. It goes from a rattle to a very low but discernible tone and proceeds to climb in pitch with increases in tension. Best results usually come with the blade tensioned to a clear, musical tone. Spin the wheel a turn or two to see if the blade is tracking in the center of the tire, adjust the blade if necessary, and reinstall the wheel cover.
If the wheels have been trued and crowned and the saw is running smoothly, the tension can be fine-tuned with the saw running. Bring the upper guide post down low to the table to provide maximum protection from the blade. Loosen the upper and lower guides so that they are well away from the blade. Turn on the saw and observe the blade, assisted by bright lighting and a white background. If the tension is correct, the blade will appear sharply in focus with no trace of flutter. The blade looks blurry if it’s vibrating.
Try altering the blade tension in very small increments while the saw is running. Be careful! Keep well away from the blade while making the adjustments and pay attention to where the blade is tracking. As the tension is increased, the blade creeps forward on the tire, and as it is decreased, the blade creeps back. Carefully alter the tracking adjustment while tensioning the blade to keep it in the center of the tire. Scrutinize the blade after each adjustment.
When the flutter is gone, stop the saw, note the position of the pointer on the tension scale (if the saw has one) for future reference, and twang the blade once again to get an idea of the amount of tension on the blade. If the saw is less than an industrial-quality machine, consider relieving the blade tension when it is not in use to save wear on the bearings and castings. As a pertinent aside, remember, when a blade breaks or hops off the wheel, a loud bang ensues from the release of spring tension on the upper wheel (provided by the blade and the spring on the upper wheel assembly). When this happens, cut the power immediately. Then step back and wait for both wheels to coast to a stop.
BAND-SAW CHECKUP
Properly trued and crowned tires and a saw free from excessive vibration critically impact the saw’s performance. These points are easy to check, as described below. Corrective measures are not difficult, but go beyond the scope of this book. For more information on tuning band saws, refer to Mark Duginske’s Band Saw Handbook.
Trueness and Crown
Every point where the blade contacts the perimeter of the tires must be the same distance from the axis of the wheels. If not, the tire is “out of true” and the blade will undergo changes in tension, resulting in potentially excessive vibration.
“Crown” is the convex arc across the width of the tire. Lacking sufficient crown, the blade will not track properly, wandering on the face of the tire, even hopping off completely.
Checking Tire Trueness
Unplug the saw and remove the wheel covers and the blade. Use the guide post, the table, or some other convenient part of the saw to steady a stick, and hold its end about 1/32 inch from the surface of the tire, where the blade would normally ride. Spin the wheel slowly by hand and observe the gap between the tire and stick (1–15). If the width of the gap holds steady, the wheel is true; if it fluctuates, the tire is out of true. Check both tires.
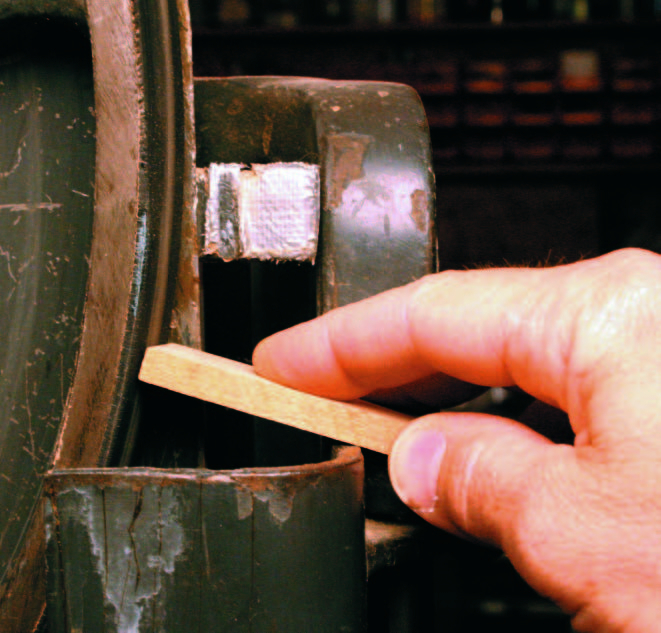
Checking Tire Crown
Place a six-inch ruler on edge, across the width of the tire. Rocking the ruler end to end should reveal a nicely rounded arc. With the ruler centered on the high point of this arc, there should be about 1/16 inch of space between the edges of the tire and the edge of the ruler (1–16).
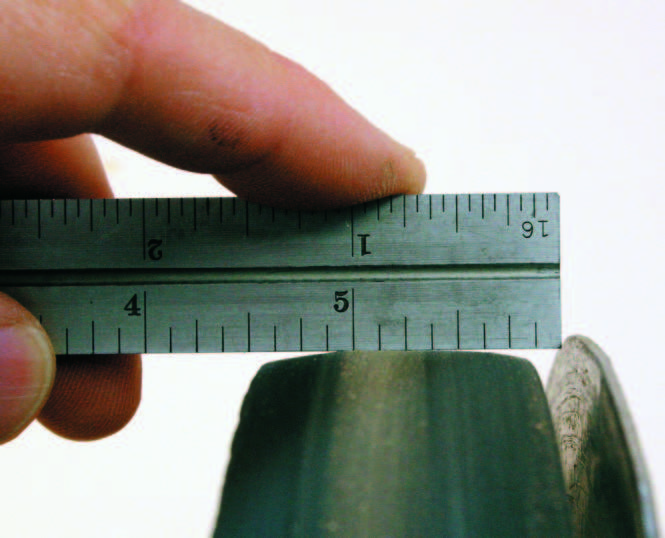
VIBRATION
Excessive vibration results in rough and wandering cuts. To check for vibration, with the saw running, lay a small wrench near the edge of the table. It should remain there quietly without moving. Any rattling or motion betrays excessive vibration. By systematically isolating portions of the drive system, vibration sources can be isolated and rectified.
Excellent, excellent book.
David’s book is excellent, I have a copy mod his revised edition. On setting up a bandsaw, he is spot on, until he gets to the fence, which he wants adjustable for drift. If a good band saw is setup correctly, you can set the table so the miter slot is parallel to the blade, and eliminate the “drift” issue, then just set your fence parallel to the miter slot, and a true cut is yours — no drift.
cheers
Uncanny! How ever did you know I just picked up a 1959 Delta – Rockwell 14″ band saw! It needs correcting (i.e.: rehab,) but I have the time. Great tips.
A good blade does wonders. I have a powermatic 14″ saw and went through several timberwolf, starrett, and Olson blades before finally trying a wood slicer. The difference was night and day. I’ll be interested to check the weld from now on as I remember struggling to keep it from rubbing. Does David offer a suggestion on how to fix a fat weld? Grind it down maybe? Or just return the blade?
This is terrifically timed, as I just acquired a used Rigid 14″ bandsaw, previously owned by a guitar maker. It’s my first band saw, bought partially on your recommendation in the ATC book (and partially because I got a heck of a deal on it 😀 ). I’ve yet to explore its capabilities and potential, but these setup tips will really help me get there, I am sure.
One question: It came with a variety of blades, most look quite dull. I’m experienced in sharpening handsaw blades, so is it reasonable/common practice to sharpen band saw blades, even big re-saw blades, or more effort and time than it’s worth?
Cheers, Aaron
I tried following all those fiddly adjustment techniques that are in books with absolutely no success for resawing. It turns out that the critical factors are that the deepest part of the gullets should align with the centerline of the tire, that none of the bearings or blocks should touch the blade, that the tension should just be enough that if you softly tap the blade sideways with a finger that the blade is displaced about 1/8 inch, and that your feed rate is slow enough to give the gullets time to clear the sawdust. I learned all that from Alex Snodgrass’ (from Carter Tools) brief video here: https://www.youtube.com/watch?v=wGbZqWac0jU