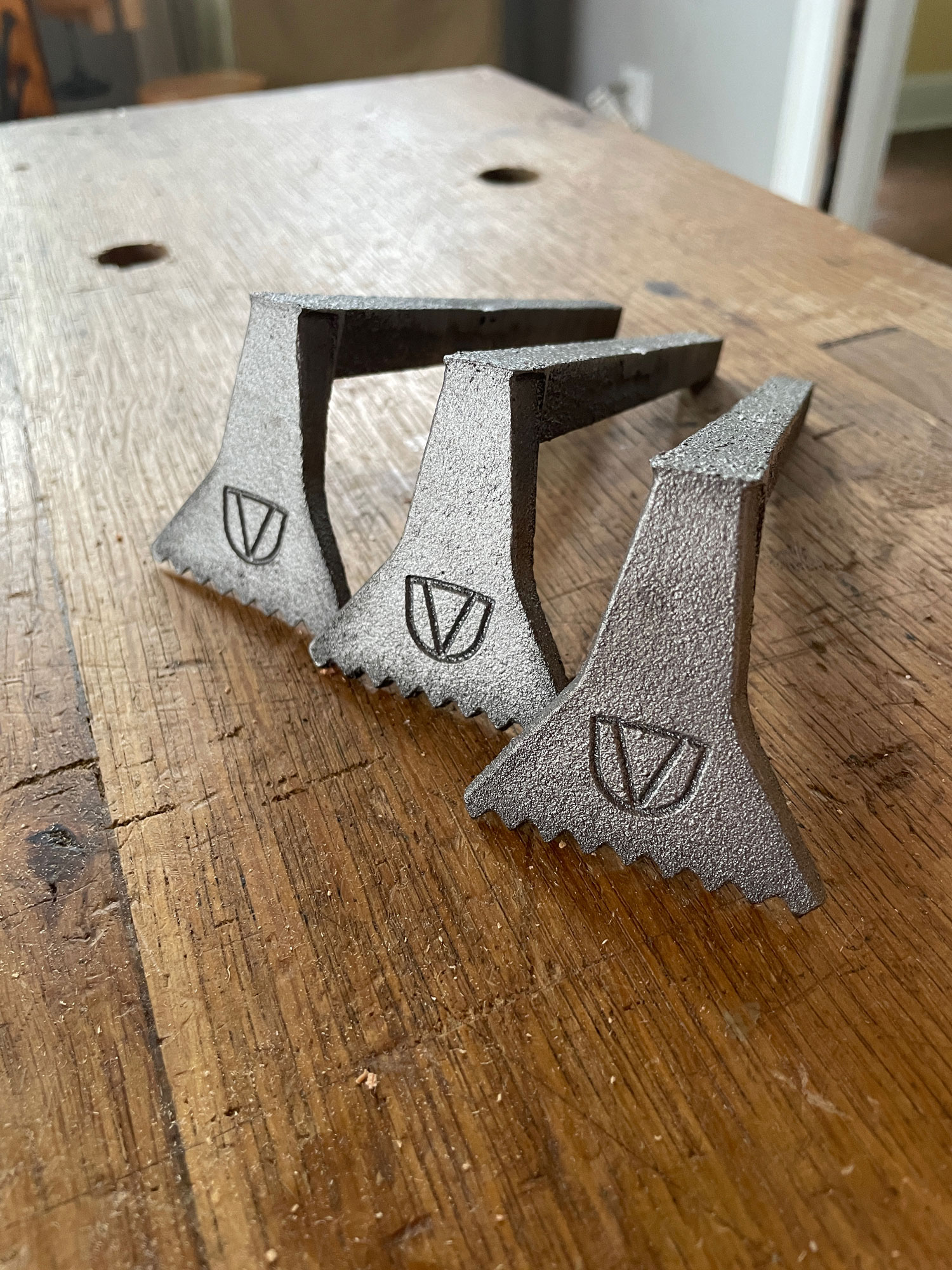
We are in the final stages of producing our latest tool, a Crucible Planing Stop that is easy to install, looks similar to a traditional hand-forged stop and is reasonably priced (about $49).
I hope this tool will be out by the end of the year, but we are at the mercy of our supply chain, which loves to whip us almost every day.
Here’s why I think the world needs another planing stop.
I love blacksmith-made planing stops, which are embedded in the end of a block of wood that is about 2-1/2” x 2-1/2” x 12”. The block is friction-fit into a mortise in the benchtop and moves up and down with mallet taps.
For me, the planing stop is as important as the workbench’s face vise and has almost-endless uses.
My main problem with a blacksmith planing stop is that it can be tricky to install. You need to drill a stepped hole in the block of wood or heat up the shaft of the planing stop in a forge and burn it into the block. And there is always the risk of splitting the block during the process.
Also, some people think that blacksmith stops are too expensive (I disagree), which can cost $100 to $300.
The Crucible Planing Stop is made from ductile iron, so it can take a beating. Hit it with a metal sledge, and it will not shatter (unlike typical gray iron). The teeth and the angle of the head of the stop are based on A.J. Roubo’s planing stop from the 18th century.
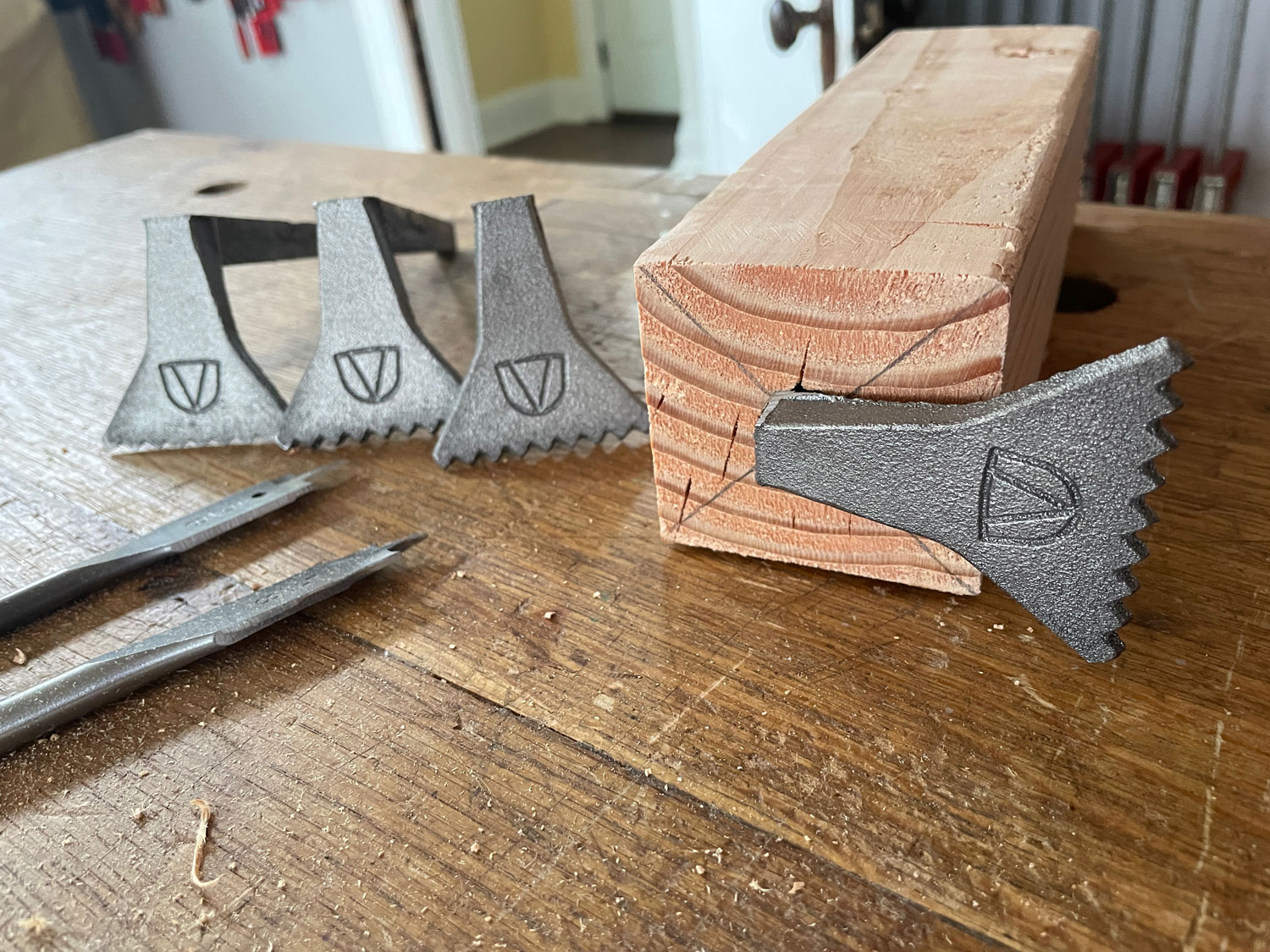
And – this is important – it is easy to install. Here’s how you do it: Buy a 5/8” (or 16mm) spade bit (less than $10). Drill a full-depth hole in the block of wood and remove the sawdust and chips. Drop the shaft of the planing stop into the hole and it will stop about 1” from the bottom of the hole. Knock it with a hammer a few times and the stop will cut its way into the hole and bed itself in place. Done.
It’s a dirt-simple tool, but getting to this point took more than a year of experimenting with hand-forged stops, developing the casting patterns and (where we are now) developing the risering so the liquid metal goes where it needs to go.
RIght now we are trying to get on the foundry’s schedule as soon as possible. We will let you know when the wheels have started moving.
Making stuff is hard.
— Christopher Schwarz
You might contact Ruger Investment Casting in Newport, NH. It would be a tiny job for them, but they’re certainly capable and they make gozillions of small parts. Or you might be able to make the parts with metal injection molding and RIC has a division that does that in St. Louis.
“Making stuff is hard.” I guess that’s why it’s called hardware.
I am glad you persist, though.
Making hard stuff is fun…
Maybe give Unicast in Boyertown, PA a call?
Making stuff is hard but ain’t it FUN !
Re drilling stepped holes.
Have you tried using “stepped” drill bits, These are designed for drilling and expanding holes in sheet metal, they basically act as reamers with multiple sizes per bit. My set is lost in the shop at the moment, but I think they may have potential.
Just as an example this is an in-expensive set from Harbor Freight, but any place that sells tools should have them.
https://www.harborfreight.com/3-piece-titanium-nitride-coated-high-speed-steel-step-drills-91616.html
And I see they have a “stepless” set that is even cheaper.
https://www.harborfreight.com/3-piece-stepless-drill-bits-66463.html
Found my step bits while searching for something else. 🙂
They cut a nice hole in a scrap of unknown hardwood I rescued from a pallet.
Definitely interested in this stop, at least once I have a slightly better bench setup to work on. I have to admit that price and sourcing has been a stumbling block for me — though gods only know why — so having an inexpensive option from folks I trust is a Good Thing.
I can’t wait to order one of these!
I’m glad I procrastinated on buying from the competition. Now I can have a stop to match my holdfast!
Are the teeth on the stop going to be “as cast”? Or will they be milled sharp?
We are working on the grinding now. The goal is to get them sharp or within a couple file strokes of sharp.
I finally took the plunge and made a “toothy critter” from a piece of reciprocating saw blade meant for pruning. Figured I’d try out the concept before buying something nicer. I love it and use it all the time now. Guess I’ll have to point my better half your way for Christmas ideas 🙂
I’m the very (very!) happy owner and user of one of Tome Latané’s gorgeous wrought iron stops, with another one on order, should winter shrinkage oblige me to have two stops, so I’m not really in the market, at least not for the time being.
However, I am curious about how you see these cast stops in relation to the also available steel ones, such as those from Benchcrafted and TFWW, rather than blacksmith-made wrought iron stops? Before you told us about Tom Latané last year, I was planning to go for the Benchcrafted planing stop; I’d even bought one already …
Cheers,
Mattias
Tom Latané, not “Tome”; apologies for this slip of the keyboard.
Mattias,
I am not one to disparage competitors. Good ones, like Benchcrafted and Gramercy, I consider compatriots.
I will say that our stop is the width of traditional stops, it is installed like a traditional stop (though more easily than many) and looks very much like a traditional stop.
Chris,
Thank you so much for your reply! Just to be sure there’s no misunderstanding, I did not at all think you would be disparaging of either of those compatriots, to use your term, nor were I fishing for a bashing of them or anyone else — ’twas just genuine curiosity.
That said, the point you make about the width of a traditional stop makes a lot of sense, in particular now that I’ve begun working with one. I’ve just been down to my workshop to measure them, and indeed: the Benchcrafted stop is about 5/16″ narrower between the outermost points than the Tom Latané one!
I don’t mean to say that I think the former would not work a treat — au contraire! — but even with only a couple of weeks under the belt with the latter, I also think that that extra bit of width takes the matter as near to optimal as makes no difference.
Or, to put it differently, “traditional” tends to be the way ’tis for a reason, and often enough that reason is a good’un …
Cheers,
Mattias
I’d rather be without a vice than a planing stop.
I’ve tried just a block morticed in the bench
with an old saw blade screwed on
with an old piece of hinge with sharpened points & a cross bolt holding it on
If I change again, I know where to go!