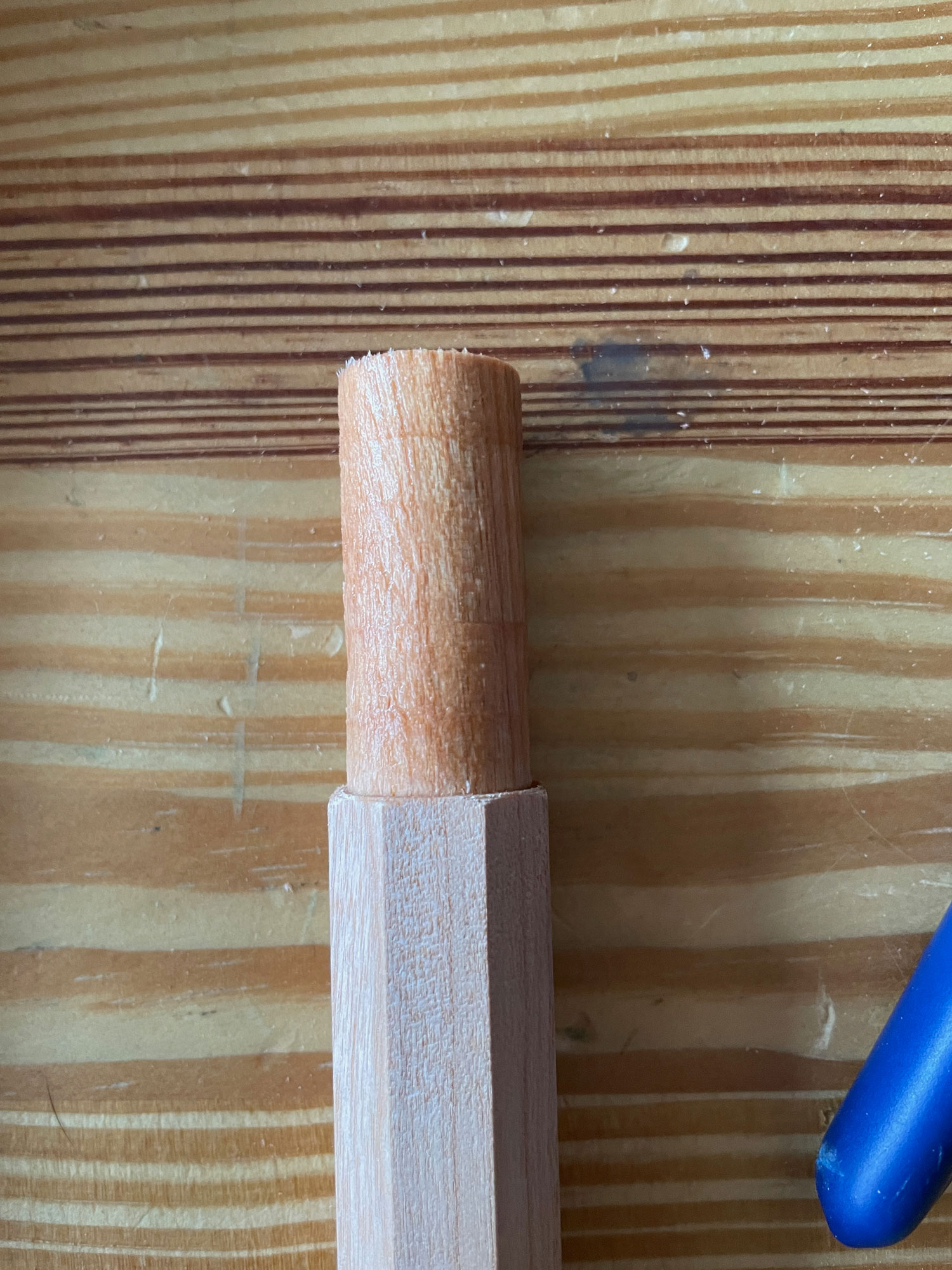
Most of my chairs are made with kiln-dried hardwood from the lumberyard. Its moisture content is usually at equilibrium with my shop – just like a good flat woodworker would want.
But I know and respect the wet/dry construction methods used by Jennie Alexander and other chairmakers who use moisture content to strengthen mortise-and-tenon joints. (An oversimplified explanation: A wettish leg mortise shrinks on a dry tenon rung to lock the joint.)
After much flailing about and experimentation, here is how I now imitate that process with wood that is kiln-dried.
Let’s say the joint has a 5/8” (.625”) mortise, which I drilled with a spade bit. I then make the tenon about 15 thou oversized (.640”). This size tenon is too big to enter the mortise.
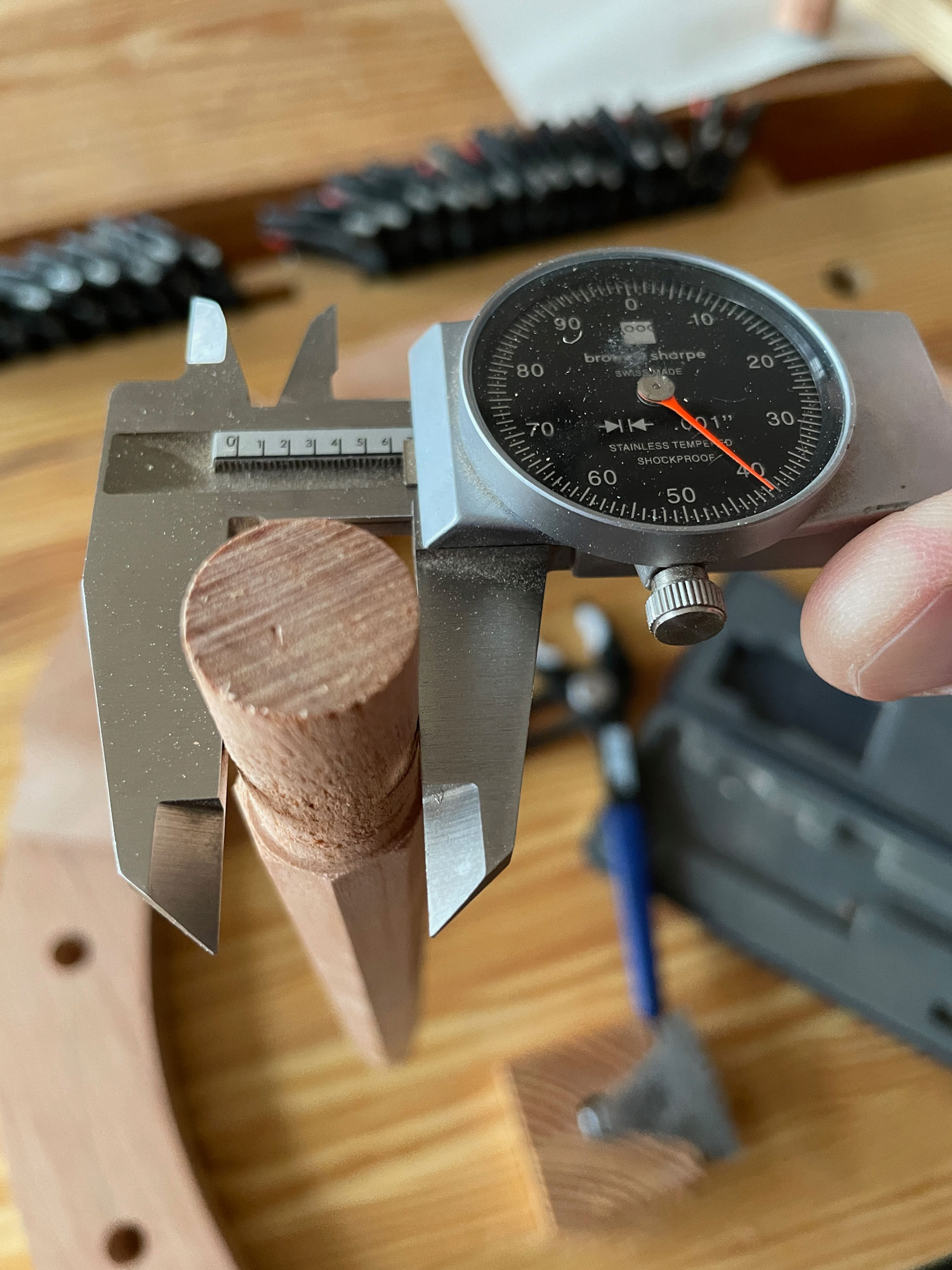
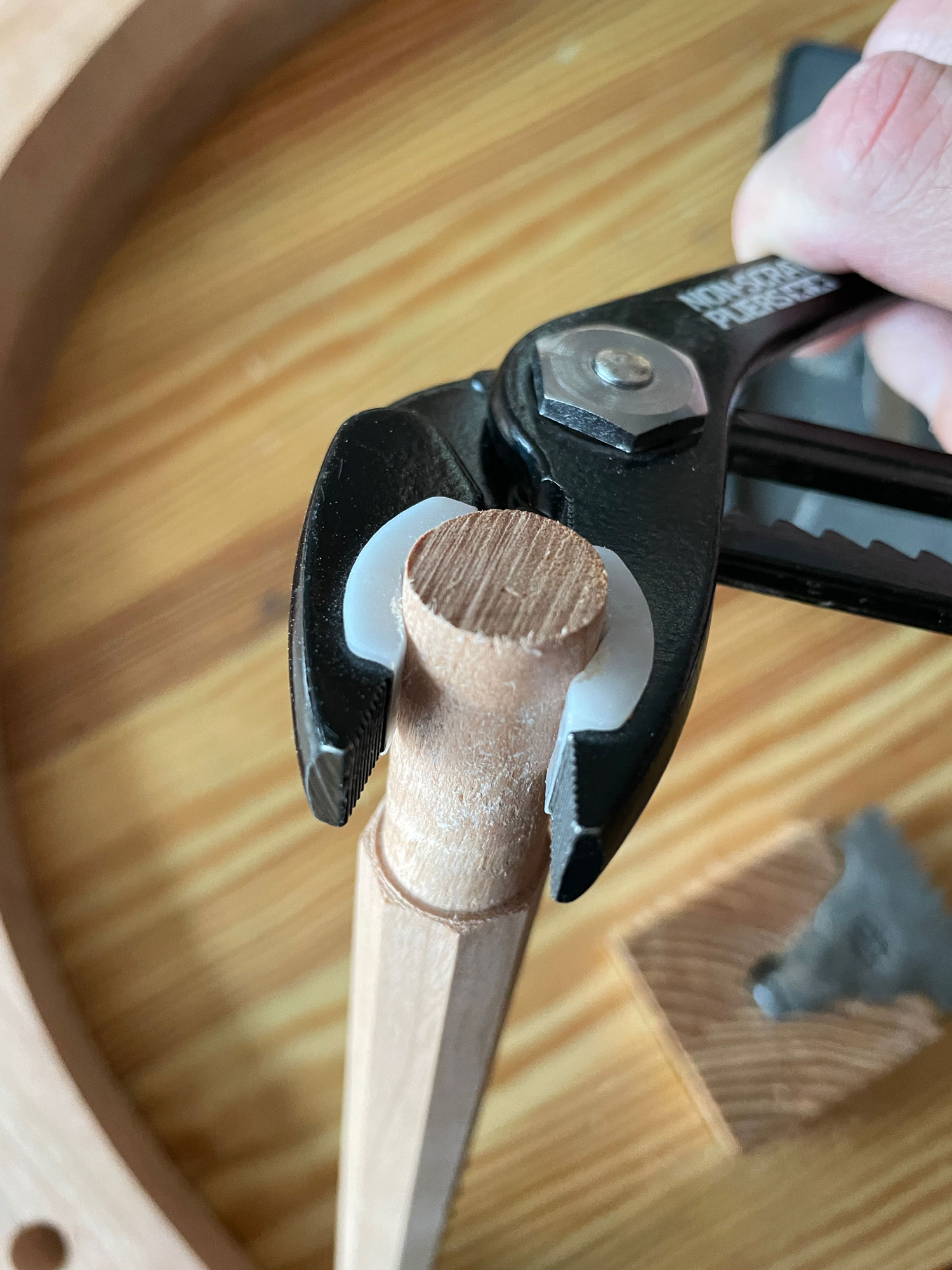
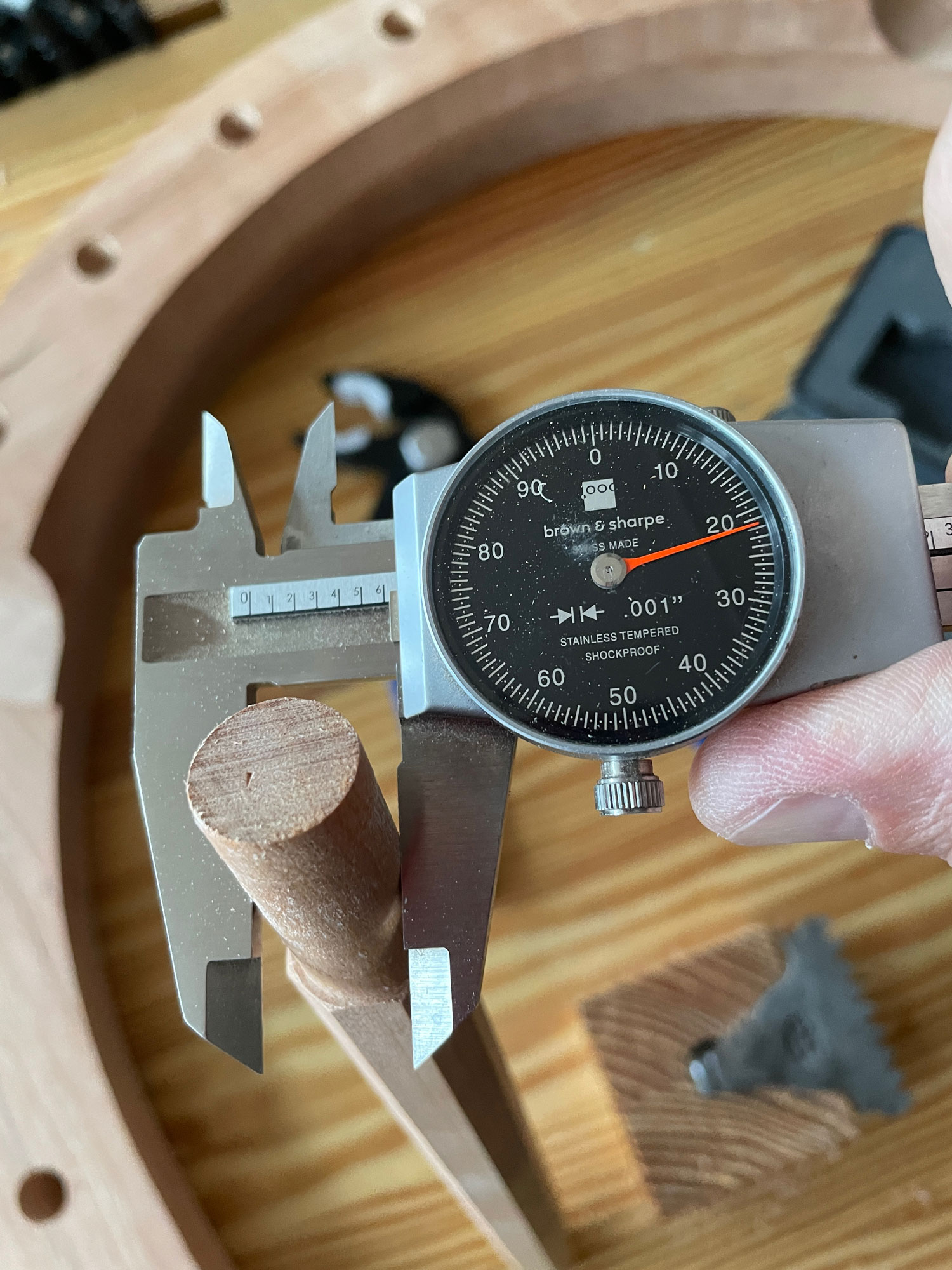
So I compress the tenon with soft-jaw pliers. By using a firm grip on the pliers and rotating the tenon, I can compress it to just under 5/8” in diameter (.620”). This tenon will easily fit into the mortise.
Then, when I add hot, wet glue and put the joint together, the tenon swells up to (nearly) its original size, locking the joint.
I know this is true because I’ve done a lot of experiments where I have cut apart sample joints. Plus, I have made a lot of chairs this way. But here is a simple experiment you can try, which is more decimal.
First, some facts. The common woodworking glues (both PVA and hide glue) are about 40 percent water. I use liquid hide glue for almost all of my joinery, plus a little PVA here and there. (Note that there are waterless glues out there, especially polyurethane glue. I haven’t experimented with these glues, so I have no opinion on whether they would work.)
So when I take the compressed (.620”) tenon and dip it in some warm water for a second or two, it swells. (This is much like steaming out dents in pieces of wood with a wet rag and steaming clothes iron.)
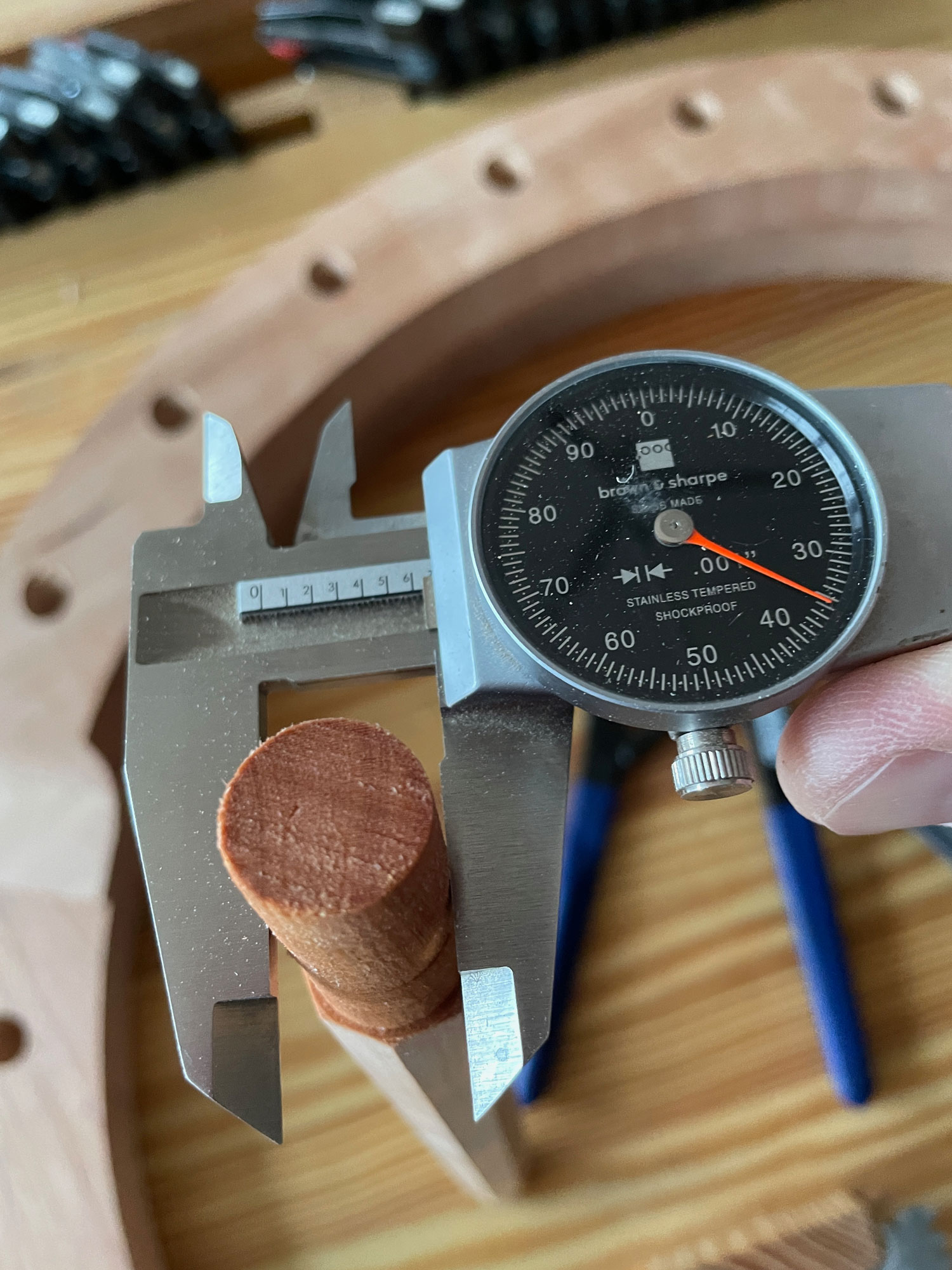
After a couple minutes, the tenon swells to .635”. After an hour or two, it swells to almost its full size (.640”).
When I assemble a chair, I can feel this process at work. The tenons enter the mortises with a little effort. The hot, wet glue hits the mortise and within 10 seconds or so, the joint becomes difficult to rotate. After a few minutes the joint is impossible to move.
If this seems like a lot of work, it’s not. It might add 10 minutes to the entire construction time involved in a chair. But I suspect those 10 minutes of extra work might add years to the lifespan of a chair.
Try it before you decry it.
— Christopher Schwarz
A great method. I use it all the time now and I’ve taught it to students in my college classes. It works. For the teachers out there it’s a great way of illustrating some critical properties of wood, much like the classic parlor trick of steaming a dent out with an iron. Thanks Chris.
I’m convinced. And the 10 minutes of extra work is far less time than felling a tree and splitting the lumber.
As the song goes (something like):
“If you can’t be with the one you love, love the one you’re with”
That makes complete sense, so here’s a follow-up question: how did you make the tenon in these photos? Veritas hollow auger/straight tenon cutter? If “yes”, how easy/difficult do you find it to dial in the .640 diameter?
Cheers,
Mattias
I make my tenons with a Veritas tenon cutter or on the lathe. With either option it is very easy to dial in to the desired tenon diameter. Hitting .625″ (or 16mm) is just as easy/difficult as hitting .640″ (16.2mm).
I think I will experiment making a “wooden swedger”. What I mean to try is drill let’s say a .625 hole in a suitable piece of hardwood scrap, cut the hole I just drilled in half and then compress the tenon in my vice until I get the desired diameter. The gap I would create with the saw kerf should give enough room for compression. I might be able to get away with one saw kerf so I get a spring joint and I could just rotate the piece for the desired effect.
I just don’t need another tool in the shop that I can’t remember where I put it.
One might even try super drying the tenon in a small kiln still leaving it large, then compress it.
With the mass of a seat around the joint I wouldn’t think you would be in danger of cracking anything.
Nothing wrong with trying a homemade solution, though it too can be misplaced, of course… and requires that you make a different one for each size you’re trying to compress to. (Though on the other hand, it may give you clearer indication of when you have compressed enough.)
I’ve seen soft-jawed pliers recommended for this task before, though I don’t recall where.
Hi Tom,
Also, I should have mentioned that you don’t have to use soft-jaw pliers. Just wrap some blue tape around the jaws of your Vise-Grips and that will work just as well.
One has to take into account the compressibility of the wooden jaws. It is minimum in the grain direction.
Thanks Chris. Do you have a preference on which liquid hide glue to use? I’ve been using the Titebond stuff. It flows well if I let the bottle sit in some warm water for 10ish min before I use it. I haven’t branched out to other types and just wondering if they behave the same or different.
Hi Joe,
I prefer the Old Brown Glue. It is 100 percent reliable.
I have had some glue failures with the Titebond, particularly with panel joints. Perhaps a bad batch or two left the factory – I don’t know. But Old Brown has never let me down.
That’s simple enough. It’s just a kiln-dried wood version of the “super drying” that Curtis Buchanan does with his tenons. He will fit the tenon with air dried stock. Then he’ll stick just the tenon through a hole into his kiln and dry it well below the level it would reach if air dried. Then the chairs gets assembled and the tenon will swell with hide glue. Between that swelling, the glue, and the wedge for the tapered tenons I don’t think his chairs will need repair in his lifetime.
If you don’t have a kiln you can heat up a can of sand on a hot plate and stick rough turned tenons in. When dry final-turn, return to the sand and do your glue-up when everything’s ready.
… It occurs to me to wonder whether this effect, or wedges, came first. Basically the same principle…
I’m with Maittias on this one. there is also the old tenon cutter I use a Stearns hollow auger. how can I make that work.
So just to confirm the process in my head, you are not rotating as you compress because that would remove wood…you compress, ease up, and then rotate…correct? Thanks, will give it a try.
Nope. Squeeze and rotate. The nylon jaws will not remove any material – only compress it.
I would love to know how to apply this technique to rectangular tenons.
If you have a metal-jawed vise (no wooden jaws), you can compress square tenons. I’ve done it several times. There’s typically a lot more surface area so I don’t get as much compression. But it definitely works.
The Japanese use this technique all the time. They use a hammer with a rounded striking face to compress the wood.
Very clever, I was wondering what those pliers were for when I was rooting around in your ATC at the open house! 😁
On top of making a stronger joint, I see your technique as making the assembly much easier than fighting with sticks that get stuck and refuse to seat completely in the mortise because of the swelling effect of the glue.
You are correct. (But I didn’t want to over-sell the technique. It was beginning to sound like a Ronco commercial.)
Ha ha! yes, not a Ronco, but one of my favourite ones is the Slap Chop commercial with Vince Offer. Joking aside, I started reading your Stick Chair Book, and it is really well done. I think it will become a reference for the type of chairs.
Are you becoming slightly Japanese? A bit like their hammering, “killing”, the wood before assembly… Makes a lot of sense.
I don’t use this method on chair tenons, yet. But I turn all my own knobs for furniture, and I use this method to compress the tenons to fit into the holes on drawer fronts. I learned the method from you, quite a while back. And those are really well made pliers, as well.
I know I’ve covered this ground before, but with the new book out I thought it bore repeating