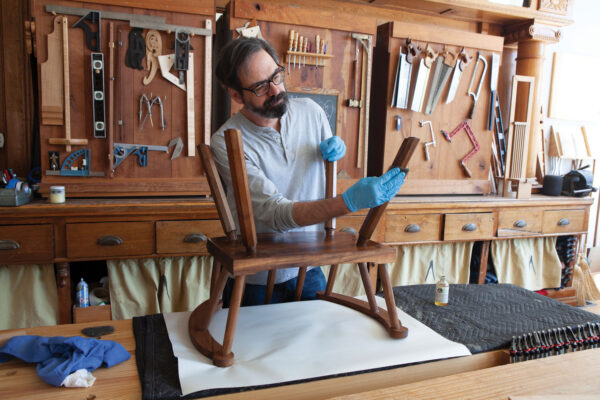
Applying a linseed oil and wax finish is one of the easiest things to do…
If. You. Follow. Instructions.
Every single problem I have encountered with applying this simple finish can be traced to not following the application instructions. Why is it always user error? Because almost nothing else can go wrong. The finish isn’t particularly sensitive to humidity, temperature or the way you apply it. You can put it on with a rag, steel wool, synthetic woven pad or cheesecloth. There are no brush strokes to overlap or tip off. There are no spray patterns to learn. Heck, the workshop can even be a little dusty.
So what can go wrong with this finish? Well, I’m sorry to say it, but it’s you.
Here are the instructions.
- Prepare the raw wood just like you would for any clear finish. Remove excess glue. Make sure all the show surfaces are prepared to the same level of refinement. Break the sharp edges.
- Apply a good coat of the linseed oil/wax finish. Saturate the wood, especially the end grain. Get the whole chair, box or shelving unit covered with the stuff. Look for dry spots (especially on end grain and in corners).
- Now get a clean rag or towel (we use Huck towels). Rub the entire project until you have absolutely and positively removed all excess from the surface. If there is a greasy film that you can leave a fingerprint in, then you have not removed enough. You should keep rubbing the project until the wood is basically dry on its surface. It will feel a little cool to the touch but there should be no discernible greasy film.
- Wait 30 minutes. Get a coffee or a glass of water.
- Go back to the project with a clean rag or towel and rub it dry again. Some woods will leach out some of the oil after the first application, and you don’t want that stuff pooling on the wood. Get in the corners. It’s easy to miss a few spots on the first rub-down, so this is your chance to find the excess.
- Go away for two hours. When you return, the project can be handled. Sit in your chair. Move the shelves to their final resting place.
- Now wait for two or three weeks. Look at the project. Are you happy with the sheen? If so, walk away. Does it look a little dry? Then return to step two and apply another thin coat of the stuff.
- Now wait a year. Look at the project. Are you happy with the sheen? You know what to do.
If you haven’t figured it out, the biggest error people make with this finish is they don’t remove the excess finish. They leave a little extra on top, thinking: “That will add extra protection.” Wax/oil finishes don’t work that way. When you leave a little extra, the excess bunches up like a rubbery scab. Or it refuses to fully dry.
This problem is especially acute with casework. The woodworker finishes the interior of the secretary or cabinet then closes up the case – robbing the finish of the air it needs to cure. So the finish never dries. And it smells awful. If you use this finish on the interior of something, you have to leave its doors and drawers open until it cures (which is two to three weeks).
Most projects don’t need the interior to be finished (historically, finishing the inside of a piece was seen as a waste of time and material).
Finally, take the rags or pads and lay them out to dry. Don’t bunch them up – it’s a fire hazard. In Europe, many woodworkers burn the rags. In some parts of the country, they put the rags in plastic bags filled with water. I lay the rags out, and I have never had a problem.
Troubleshooting tip: What if you left too much of the finish on the surface, and it is a sticky mess the next day? Get a solvent such as low odor mineral spirits or a citrus solvent (limonene) and flood the surface. It will dissolve the excess wax and oil, and everything can then be wiped away. Wipe the project until it is dry and you are back to wood. Let the piece dry overnight. Then begin again with step two above.
— Christopher Schwarz
Thank you, Chris — that was very clear and instructive!
Just two follow-up questions:
After your rags have dried, do you then wash and re-use them? Or do you throw them away?
I am a woodworker in Europe and do indeed burn my linseed oil-soaked rags; don’t Americans do that? If not, why not?
Cheers,
Mattias
That’s the first time I’ve heard of burning the rags. I just rinse mine out with water then hang them over my bin to dry over night.
After the linseed oil dries, I will try to reuse the rag if possible. If it’s too crusty, I will wash it. Huck towels are durable and can last many years before they fray.
As to burning rags…. you would think that Americans would LOVE to burn rags. I have no idea why it is not common here. Maybe if the rags exploded we’d be more interested in the practice.
C
Many communities have restrictions on burning, leaf burning – no, rags / trash burning – no, politicians – no, steaks / smores – OK.
I usually hang them to dry, reuse if i can or throw them in a 5gal bucket with water. I usually have a burn pile 3-4 times a year so when the bucket is full I just drain the water and throw them in the burn when it’s super hot…
Unless you burn the rags inside , it’s against the law in most states to burn stuff outside. it used to be okay many years ago, but no longer.
For me, it’s one and done. I just drape the rag over the edge of the garbage can for a few days. Then just tip the stiffened “shell” over.
Nice article, even after all these years woodworking I am still guilty of not wiping enough on occasion when in a hurry. All of my furniture finishes have been a hand rubbed oil mixture of some sort, In the past couple of years I have been using Osmos and now Saicos, have you tried them? They are expensive at least it seems that way until you realize how little you need, my last quart did 3 coats on a king sized bed, 2 hall tables, 2 bedside tables and some of my tool cabinet. It’s also fairly safe as far as finishes go – Saicos is my go now to as time between coats i think is three hours. So far seems to be pretty durable, it is not a high sheen product very slight and has a nice natural look to it. Also I have been using wypall x70 as a replacement for cloth rags, work great for about everything about 90-95% replacement for a cloth rag, i did find that the last coat of Osmos or Sacios is better wipe with a cloth rag and the trick is you REALLY need to wipe hard and long…
oh, I see where I went wrong. Step #4. I had a beer not water or coffee. 🙂
Haha. It may not have been the Beer you had after that caused your problem, it might be the half dozen before you started wiping. 🙂
Oh — OK. I see where I went wrong. It was step #4. I had a beer not coffee or water. 🙂
Just one?
The way I read his comment(s) I think he had two… maybe more…
I found one of my favorite shop tools while roaming around an antique store. It’s the American Wringer Company No.1 Empire Clothes Dryer. It holds all my finishing rags while they dry and then folds up nicely to the wall when finished. I used to hang rags on the edge of my trashcan but this allows me to continue using the can for trash and it gives me piece of mind not having to worry about some random rag falling into the trash and starting a fire.
Would you coat the wooden parts of a cherry Roorkee chair in BLO? I ask because I’m currently making one and have used garnet shellac and black wax on all previous chairs (white oak, walnut and mahogany). I love the look of cherry once it’s aged a few years.
I apply the oil with a sanding pad. In effect, I wet sand the wood. Chris may be holding a pad in the photo.
For this, I have not noticed big differences between gray, maroon, or green pads.
I find it easier to achieve even coverage by applying a slightly generous coat and then wiping off the excess.
I use paper towels for the initial wiping and then switch to rags for vigorous rubbing. That makes the rags last much longer.
Rub, rub some more, keep rubbing, rub it again. Got it.
Your article reminds me of a piece of advice an ex-girlfriend once gave me. “There is one constant in all of your failed relationships… I’ll let you guess who that is.” Harsh yes, but it needed to be said.
I was taught this exact method in wood shop in the late 1960s. Great refresher!
“If. You. Follow. Instructions.”
Every time we had a new aircraft mechanic starting to work for us in Seattle or Toulouse the first training document I gave him had only one line on it: RTFM. It was also known as Rule #1.