Editor’s note: The following is an excerpt from “The Anarchist’s Workbench,” which you can download for free here. This excerpt discusses one way to choose wood for your workbench: its cost per pound.
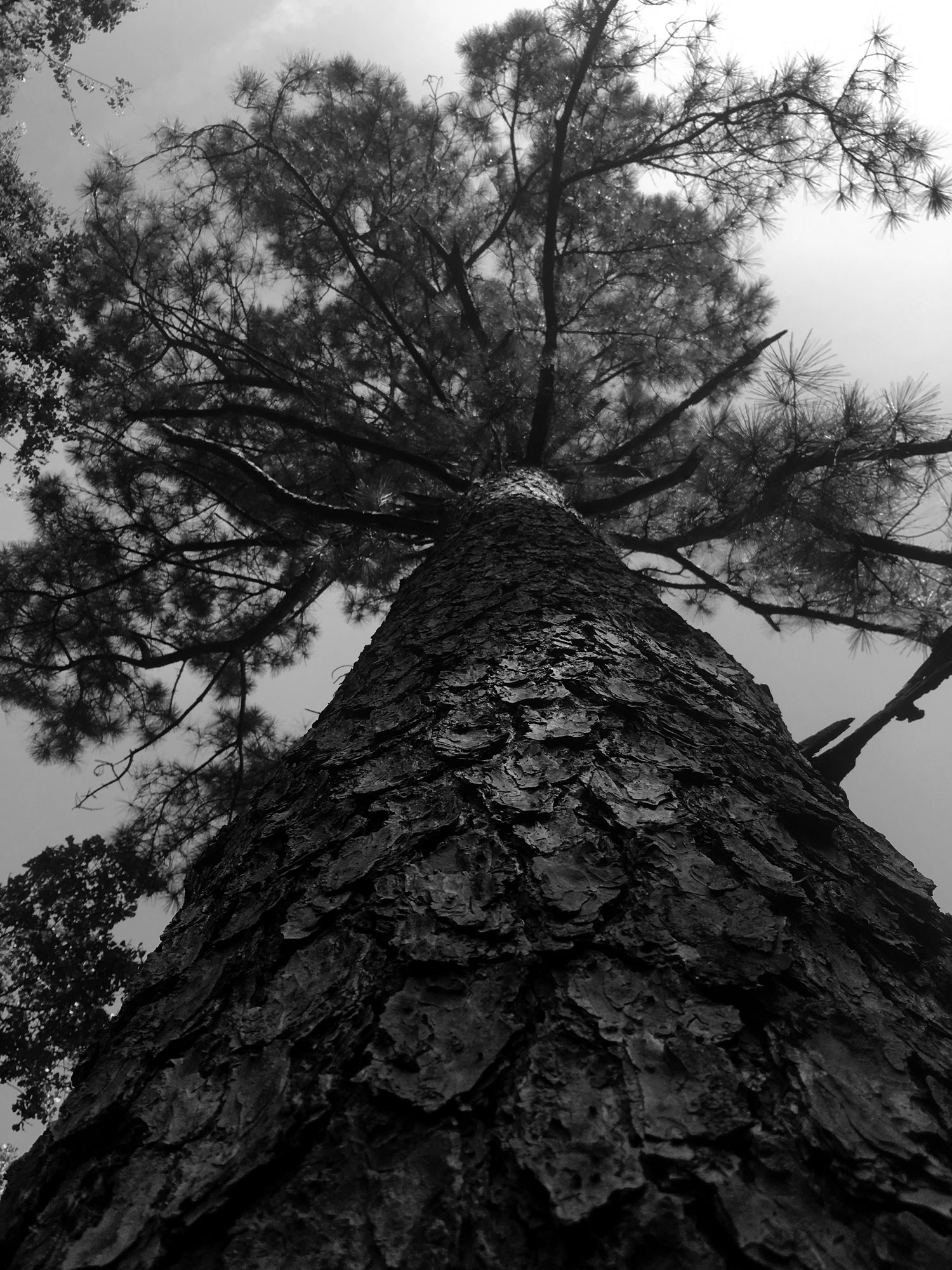
After years of working with yellow pine on our Arkansas farm, I convinced myself it was an ideal wood for a workbench.
Let’s Talk About Weight
When you compare the weights of species, you need to make sure the comparisons are all at the same moisture content (12 percent is the typical comparison unit). You can compare the density of a species by comparing its “specific gravity,” which is a method that compares the weight to a cubic meter of water. Or you can look at the average dried weight of a cubic foot of the wood (also at 12 percent moisture content).
These are useful, but I think you can also make some important comparisons by factoring in the local price of a species. It’s like buying meat at the butcher. Is rib eye ritzier than hamburger? The price per pound helps us answer that question (and yes, it is).
For example, a cubic foot of hard maple consists of 12 board feet of maple. If maple is $4.73 a board foot, then a cubic foot of maple costs $56.76. That cubic foot weighs 44 lbs. Or $1.29/pound.
Longleaf pine (a yellow pine) is 78 cents a board foot (for No. 1 grade), so a cubic foot costs $9.40. That cubic foot weighs 41 lbs. Or a remarkably cheap 23 cents per pound.
Because I live to poke fun at Ipe, let’s run those numbers. Ipe costs $17 a board foot, so a cubic foot costs $204. That cubic foot weighs 69 lbs. So Ipe is $2.96/pound. Not a great deal at the wood butcher’s.
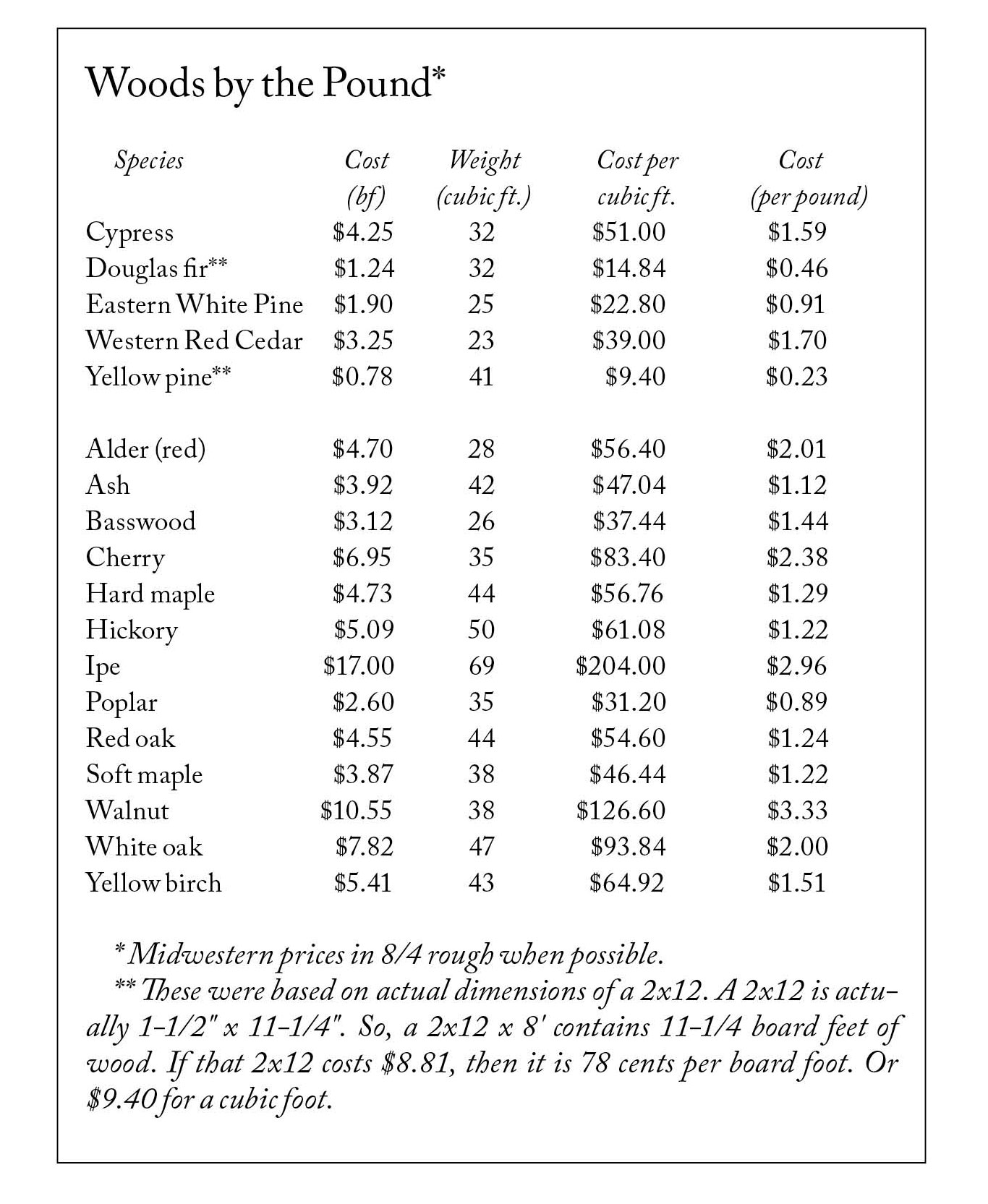
The chart compares some of the common U.S. hardwoods and softwoods using typical Midwestern retail prices circa 2020 (this is not wholesale or trade pricing). This cost-per-pound calculation is simple to do yourself using your local prices.
Here’s how: Take your cost per board foot (use 8/4 prices) and multiply that by 12. That’s the cost for a cubic foot. Now divide that number by the weight of a cubic foot of that species (a statistic that is easily found in books and online). The result is the cost per pound.
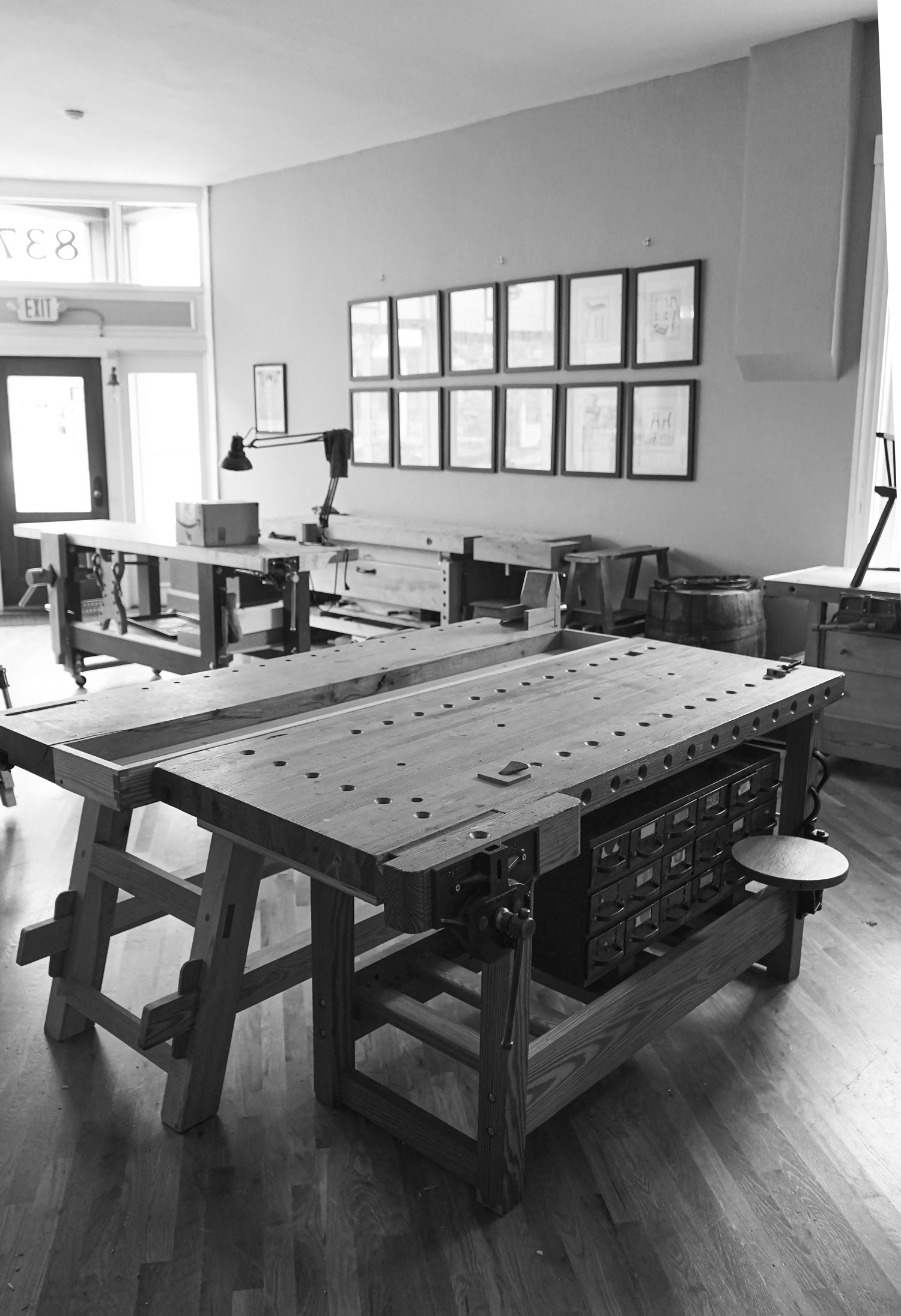
The yellow pine in this workbench is now about as hard as maple and moves little with the seasons.
Do the Math
From the chart, ash looks like a good choice among the hardwoods. The problem with that assessment is that by the time you are reading this book, white ash might be almost extinct. The emerald ash borer has devastated the ash forests in the United States. So, you might not be able to buy it at any price. And if you do find it, you want to ensure it hasn’t rotted. We have been plagued by punky ash for the last few years as the sawyers have milled up trees that have been standing dead.
Aside from ash, poplar and the maples are a great bang for the buck. Both are easy to work, readily available and fairly cheap by the pound. I’ve made workbenches using all three species and think they’re fine. Neither is considered a noble species for a workbench, like European beech. But as long as you aren’t out to impress anyone, go for it. You’ll have no problem finding those species at almost any lumberyard in America.
But if you want to go full redneck, read on.
Softwoods that are used for structural members in home construction – the yellow pines, Douglas fir, hemlock and some spruces – are an outstanding value. They are heavy, cheap and readily available at any lumberyard. After working with them most of my life in residential construction and workbench building, they remain my No. 1 choice for workbenches.
Here’s why: Anyone can buy it. You don’t have to search out a specialty lumberyard or set up a commercial account. Just go to the home center if you want (though I always prefer family lumberyards). They have plenty.
Also important: They have plenty. A typical home center or family lumberyard will have hundreds of planks of 2x material in the racks on any given day – everything from 2x6s to 2x12s – with lengths from 8′ to 16′. At a home center, you can spend hours sifting through the racks to find the best boards – the employees don’t care. At a family lumberyard it pays to ask permission (they will sometimes be happy to help you). Either way, just be sure to restack the lumber nicer than you found it.
Here’s another buying tip: Some lumberyard chains carry No. 2 yellow pine, others carry No. 1. The price difference is minimal, but the quality isn’t. No. 1 is worth the extra nickels. If you find a yard that deals in No. 1, you might be able to buy all the wood for your bench in one swoop. If you buy No. 2, you might have to hit all the yards in your town, county or region.
Yellow pine is easy to work. I’ve built yellow pine workbenches using only hand tools, and using a full-on machine shop. It’s friendly stuff. Yes, there can be some knots, but if you pick your boards with care, you’ll have almost none of those to deal with.
So there must be disadvantages. Yes, but they are slight. Construction lumber is sold in a wetter state than hardwood lumber.
While hardwoods are typically sold at about 12 percent moisture content (or at equilibrium with some environment) that is not the case with construction lumber. It is wetter.
How wet? In the Midwest it might be 15-20 percent moisture content. On the West Coast, it might be even wetter (as in wet enough to ooze and squirt water). So, you need to gather up what you need to build your bench, cut it to rough length, stack it and wait a bit.
It might also be “case hardened” because it was kiln dried too quickly. When lumber is rushed through a kiln it can develop tension that is released when you cut it. It’s particularly obvious when you rip a board. Sometimes the wood will pinch so hard on a blade it will stop a 3-horsepower table saw like pinching out a candle.
How do you deal with this? It’s not difficult.
- Plan to cut things a bit over-wide. And have some wooden wedges handy to keep the kerf open when you rip the wood. After that first rip, a case-hardened board will usually lose all of its fight.
- Make your rip cut to a shallow depth at first – less than half the thickness of the board. Then raise the blade, flip the board end-over-end and finish the rip.
The final disadvantage: Softwoods are uber-redneck. No one is going to “ooh and ahh” over your choice of yellow pine. It’s the mullet of the forest.
The True Cost of Yellow Pine per Pound
I’m not a trusting soul. After I calculated the cost of yellow pine per pound (23 cents) based on published statistics, I decided to see if that worked in the real world. So, I weighed several 2x12x8s and came up with an average weight of 30.4 pounds each.
These were boards I’d had in my shop for months, so they had likely lost some of their water weight (as all softwoods do). Plus, the boards in this particular pile were fairly average – not full of sap or with lots of heavy summerwood. In other words, they were a bit on the lightweight side.
Each of these boards cost $8.81 each, so that’s 29 cents per pound – about 6 cents per pound more expensive than the published weight tables indicate. But still a great deal.
I wondered, how did that work out after surfacing the boards and gluing them up? What was the cost per pound of “finished” yellow pine?
Here’s how I calculated that. The benchtop for the workbench at the end of this book is made from nine 2x12s, ripped in half, glued up and planed so the top is 5″ thick. Nine 2×12 x 8s cost $79.29. After gluing up the top, I managed to weigh it on a heavy-duty scale we use for shipping crates. The top weighed 240 pounds. That’s 33 cents per pound. Still a bargain (if you ask me).
— Christopher Schwarz
I got lucky on my last trip to the big box store. I found a couple great boards, but they had a split on one side, which didn’t affect my purpose. The person actually helped me put the other boards back and said the ones I chose were cull boards and are half price. 3 sections of bench top for $8.
Lumber prices have gone wacky over the past year. A $2.00 2×4 is now $7.00 so expect to spend more.
It’s been about four years since I last purchased rough sawn cherry at MacBeth hardwood in San Francisco (an awesome huge hardwood lumber yard). I paid $3.75 a board foot. I’m starting to run low. With how much material prices have gone up in the last year, I’m starting to worry what the new price is. I think I have enough wood to keep me busy for a year. Hopefully wood prices will be lower by then.
Woodworkers of the future will have to own their own Wood-Mizer if they want affordable lumber. 😛
Those $8.81 SYP 2x12x8s are currently running $30.99 at Menards. (!!)
I’m going to try to wait for prices to go back down before I build my bench, but I have a feeling that might not happen.
A new way to measure wood for projects. As in ‘I have decided on the size of my new cabinet, it needs to weigh 53lb’.
Making a buying by mass comparison is always interesting. Do it for cars and you will see one pays for the volume of air inside. (comparing a sedan with the station wagon of the same brand and model – obviously there a little bit more glass and metal but not that much and no added technology).
My wife hate when I look at the price per kilo of cosmetics.
Current big box prices in omaha nebraska have #2 Doug fir at $0.73/lb and mdf at $0.50/lb. When combined with all the time saved laminating the top, mdf was a no brainer for me. I added a 3/4″ maple edge band and looks ok. Pine would look better, but so much more time building furniture.
Americans considering Euro beech as a fancy wood never ceases to make me chuckle. Over here it’s generally the cheapest and definitely least prestigious of the hardwoods. Though I guess anything that comes from far away automatically gets fancier the further it travels.
Local woods are great. We have so much Black walnut here that people used to build houses from it.
Interesting comment on the $175 workbench. Does wood harden over time, and that much, too? I am wondering because I just made legs for my workbench using old wooden beams. They are some softwood, presumably quite old (50+ years) and it was rather challenging to chop out the mortises. Could it be that they are also hardened due to age?
Some woods harden over time, particularly resinous woods. The caissons under the Brooklyn Bridge towers were made from southern yellow pine. The wood needed to be dense, and water and air tight. After the resins hardened, it was the perfect wood.
Hi Chris,
When I bought and read the book, I found this section to be really good. Glad you put it out as a blog post.
I think folks get analysis paralysis when it comes to what wood. Personally, I’d rather save some money on the wood in the bench and spend the money on slightly nicer wood I use on my furniture. While I don’t purposely abuse my bench, it does scars from use.
Sincerely,
Joe
My house in PGH is framed in black walnut.
I understand that a good workbench needs mass to give it stability but I believe this is the exceptional example. Most woodworking projects – cupboards, boxes, shelves, desks and so on – are based on the quantity of material rather than the weight and so the column of your table citing cost per unit volume will generally be the most useful one.
I don’t remember ever seeing Yellow Pine being sold in Michigan. How would I know? I built my bench some 20 years ago, using hard maple and a plan from Lee Valley. I probably spent $700. My only regret is making it so long, about 9 feet including the tail vise. It took four guys to carry the top upstairs.
There are pine floor joists in my 92 year old house that are too hard to pound a nail into.
atleast, Don’t know about Michigan but in Cincinnati the lumber will be stamped SYP (Southern Yellow Pine).
I am buying SYP here in Grand Rapids. The wider 2×12 lumber was DF but has recently been replaced by SYP.
One of the things I take from the table is that Douglas fir has the next-lowest price per pound, after (Southern) yellow pine. Finding cheap yellow pine seems to be hit and miss in some parts of the US. (My local Lowe’s sells SYP 2×4 lumber — but only in 2ft lengths!) Douglas fir seems readily available nearly everywhere. If you can’t find cheap yellow pine, then Douglas fir can be an excellent substitute.
I built a bench from (cheap) Douglas fir 4×4 posts. Like Chris’ $175 bench from yellow pine, my bench has held up well for 20 years and shows no signs of giving up. The 4×4 starting dimensions can reduce the number of glue-ups compared to 2x lumber.
I have been using SYP for shop projects (mostly the 4 benches that I’ve made ) for the last few years. I think I actually got this recommendation from Chris. Menards sells #1 SYP in joist widths, Lowe’s and Home Depot only sell #2 or worse. I look for some with pith, then rip off the edges to make rift-sawn lumber and let it dry for a few weeks. I’ve lived in several houses with SYP joists above the basement and after a few years of aging, it’s tough to even get a nail to go into them.
The Lowe’s in Highland Heights carries No. 1. Don’t tell.
The mullet of the forest.
Find a local Roof Truss manufacturer. Most are using southern pine in higher grades like Dense Select Structural or Machine Stress Rated for parts of the truss that require high strength lumber. The higher grades are more dense, tend to be straight and have fewer defects. I only ended up rejecting a couple of boards that had fork lift damage. Everything else was great.
Great discussion. I thought I would build a cheap bench in pine, any old pine actually. When I got to the store, however, I saw a prettier dress, I mean, hard maple (and a challenge). I grabbed that instead, but I was scared witness to do anything with it for 2 years! By that time, I considered it a sunk cost that I did not have think about anymore. Finally made a bench that fits me and got over the pain of thinking, calculating, constructing, and second guessing. Thank goodness.
Here in the northeast, finding yellow pine at a lumber yard is like finding black walnut. Even speciality yards do not stock yellow pine. The only yellow pine available comes in the form of stair treads – 5/4 x 12″ x 3′ or 4′ or 16′. I purchased the 16′, ripped them into thirds and laminated them together for the bench top. I was pleased with the outcome even though it as quite expensive.
In the Twin Cities, SYP is unobtanium. I’m building a bench with Douglas Fir that I paid through the nose for at a smallish local lumberyard because it’s almost knot free.