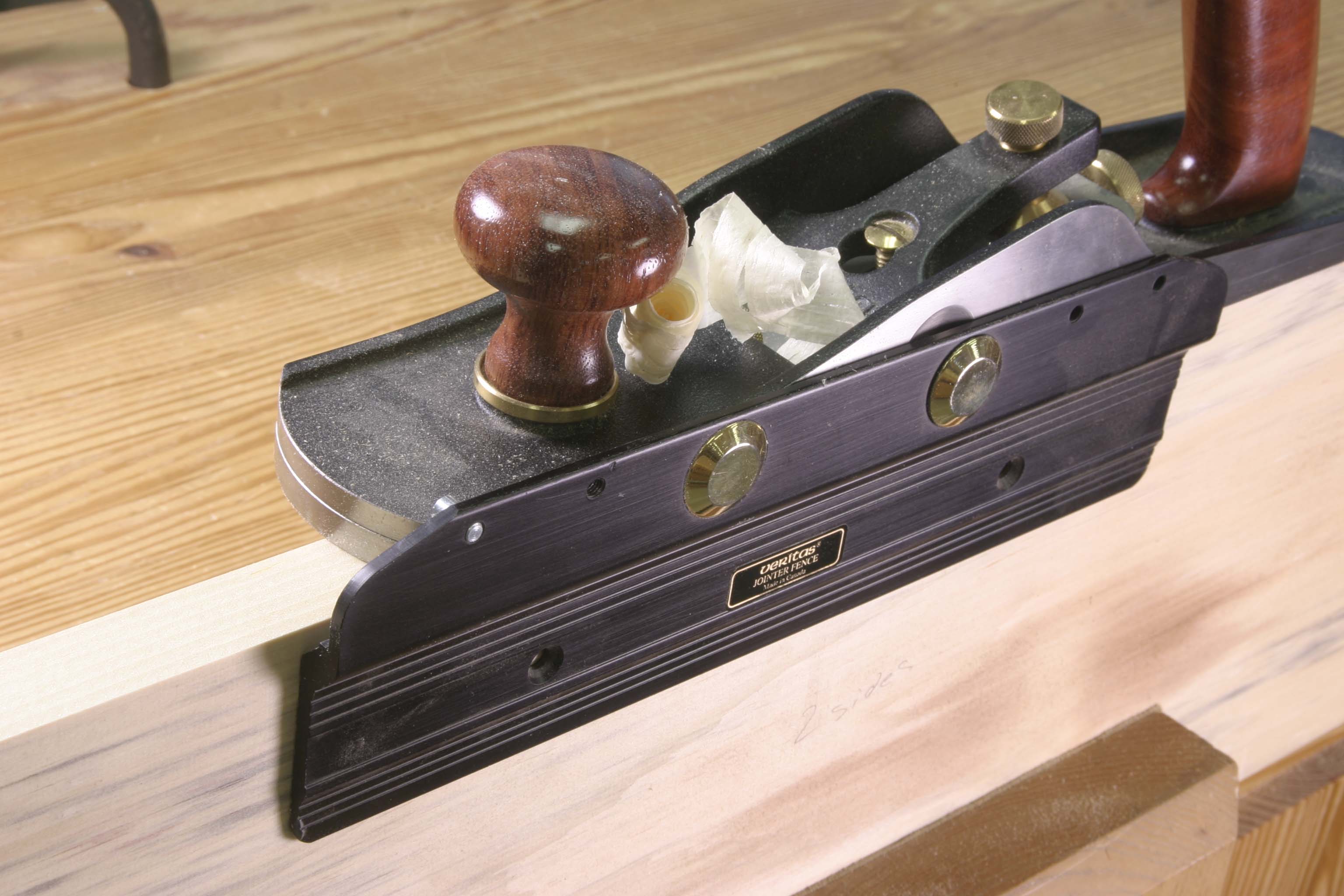
Q: I have a question about using a handplane to make a spring joint.
I am using a No. 8 Stanley that I reconditioned, meaning that I flattened the bottom as best I could on float glass and sandpaper and installed a new Hock blade sharpened straight. I am using it to make a joint 7′ long for a dining room tabletop. I am using my No. 8 because it is the widest plane I have and the top is 1-1/8″ making the edge 2-1/4″ wide when folded over.
My question is why does it feel like I am hitting and missing along the length of the cut? I apply all the pressure I can on the knob at the beginning and on the tote at the end of the pass. To make the gap in the middle, I take a short cut in the middle, then a slightly longer cut in the middle, then another etc. But every pass, the plane cuts in some places along the length and not in others. Some hits and misses are approximately in the same places, but not always. Also, even though I apply pressure in the beginning, I usually get a couple of inches of a gap, maybe 0.003″, along the start of the joint instead of being tight there when the boards are stacked before clamping. Clamping does not close the gap.
I have made two passable joints out of the five I need to make, and they took several tries, so I am a little frustrated. I think I have read every article in Fine Woodworking, Popular Woodworking and Woodwork on spring joints, but there they are making short joints.
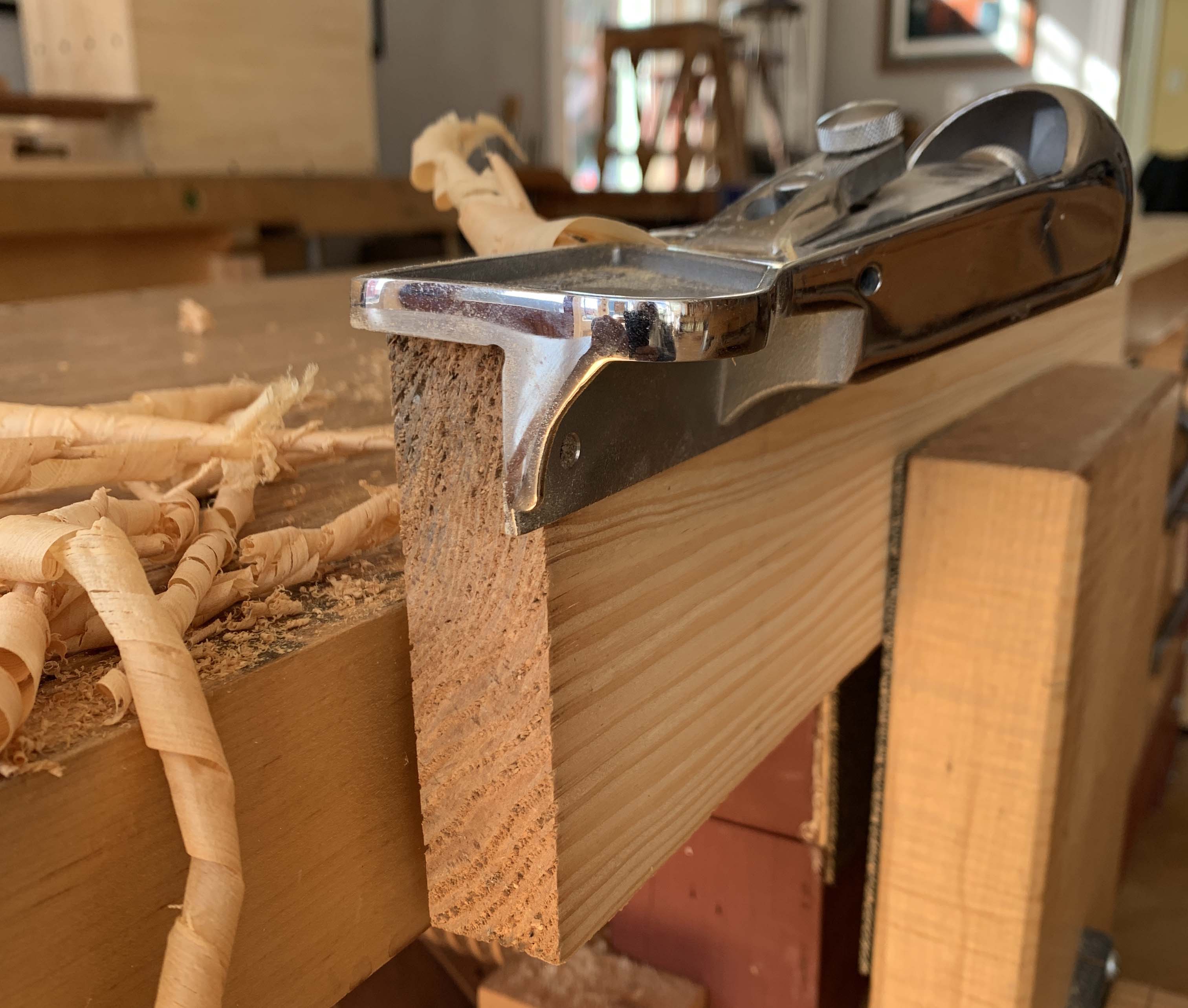
A: Without watching you work and seeing the edges in person, it’s difficult to diagnose the problem…but know that a perfect 7′-long glue joint by hand would be difficult for me, too. That’s a big one.
My best guesses, however, are:
• You are applying a LOT of pressure at the beginning of the cut but not as much pressure as you move farther onto the edge, then a LOT of pressure again at the end. That’s a pretty common problem, because one thinks about transferring pressure at the beginning and end when part of the plane sole is off the board, but in the middle, not as much. So concentrate on keeping constant pressure through the whole cut.
• You might be tipping left and right slightly as you move down the board – this would explain why the hits and misses aren’t always in the same place – you’re tipping differently with every pass. To address this, attach a fence of some kind to help you keep the plane at 90° (like this one https://www.leevalley.com/en-us/shop/tools/hand-tools/planes/maintenance-and-accessories/41716-veritas-jointer-fence?item=05P3001)
• And if you haven’t attempted it already, clamp the two board together tightly, but in opposite directions, i.e. match planing. If you can plane them together well, minor errors can cancel each other out. (I find a long match-planing job pretty difficult, though, FWIW.)
Honestly, on a joint this long, I’d probably reach for a No. 95 plane were one handy (e.g. https://www.leevalley.com/en-us/shop/tools/hand-tools/planes/54862-veritas-iron-edge-trimming-planes?item=05P0301 or https://www.lie-nielsen.com/products/1-95-rt-bronze-edge-plane), then use the jointer just for the spring joint only.
— Fitz
On a joint that long, I find the #8 is so long it creates problems. I like a “4 for a spring joint. Assuming the edge is already straight and square. There’s very little wood that needs to come off to spring the joint.
Anyhow, that’s my process. I own a jointer plane,not a jointer. Don’t like them. I take the #4 to the edge right off the table saw.
I agree. if your bench is long enough – lay the board flat on the bench and ‘shoot’ the edge with your #8 on the side. Once the edge is flat, go with a shorter plane – #5 ½ is my preference for this length.
I, too, have come to prefer a shorter plane when finessing and chasing errors like the person asking the question describes, and would use my #5 with a cambered iron (so that a varied depth of cut across the width can be achieved by moving the plane sideways), followed by a final light pass (or possibly two) with my #7.
I find I get much better feedback through the hands from the #5,I suspect because of the lesser width, length and weight compared to the #7, but also that with the #7 I too often introduce a new error at the same time as I remove a previous one.
Mattias
I can understand the idea of better tactile feedback from the #5, obviously, because of it’s mass/dimensions, but I can’t help but wonder whether your comfort level using the #5 over the #7 comes from greater use of (and a naturally arising greater facility with) your #5 v. the #7. Do you think that could be part of it?
I’ve only recently begun to do what I shall call “something approximating enough” woodworking, and so my mastery of planes remains a bit off in the distance as of yet. (I’ll admit to a growing love affair with the lot of ‘em however.) That said, because the ol’ #4 has been in the stable for a couple decades, I’m more facile and comfortable with it than, well, take your pick of my half-dozen or so others. (My L-N block plane is moving up fast, however!)
Perry,
I’m sure you are right and that greater familiarity is a part of the equation; in fact, I should have said as much in my previous post, and also added a caveat about my not being a great authority (or even a very minor one) on any of what is being discussed, but just wanted to share my for-what-it’s-worth experience.
But yes: I have used the #5 considerably more than the #7, and that should be factored in. However, as I’ve mentioned a few times before in comments on the blog, I’m currently building a workbench with a laminated top, and have now planed and jointed all 13 laminates to (pretty dang near) S4S, using handplanes only (I don’t have a planer or a jointer [yet], nor access to one, so there was no choice in the matter), and in that process have used the #7 extensively, to the point were I feel I’m getting to know it’s foibles rather better than what used to be the case. So even from that vantage point of much increased affinity, I will still say that I experience a noticable better tactile feedback from the #5.
But there you go: this is just one person’s two cents worth, on top of which the coinage in which I offer said two cents is likely to have been clipped and to be of inferior value.
Cheers,
Mattias
Thanks for the kind reply, Mattias, and let me say that I hope I didn’t seem to impugn you or your efforts in any way; I certainly did not intend to. Sounds like you’re having an adventure building up a new workbench. I, by the way, am about to embark upon same. (My current workbench sometimes seems to have more in common with rickety picnic tables than anything a woodworker would rightly claim as a workbench!) I would guess that our experience levels aren’t too terribly different, but please note—that’s just a guess! Anyway….
I’m new to following the blog, and so am not familiar with (at least most of) your previous posts, if any. It they’re of equal quality to these, however, I’ll be on the lookout for ‘em—I’m always interested in thoughtful opinions, experiences, etc.
Hope you’re enjoying a wonderful weekend.
Cheers back at ya!
Perry
You’re welcome, Perry, and fear ye not: no impugning whatsoever was perceived at this end. On the contrary, I was glad of the opportunity to add clarity about the relative worth of my thoughts on the matter at hand. And thank you so much for your kind words!
And yes, I suspect you are likely indeed to be spot-on in thinking that our experience levels aren’t miles apart.
As for my workbench, Chris was kind enough to include a link to my blog on the build in one of his recent posts here. Were you to follow the links, you’d soon enough find out that the blog is, alas, in my wild and wooly native tongue of Swedish, but in the comments section of Chris’s post are some suggestions for how to get at least a rough machine translation (please note, should sufficient interest be engendered to dig that deep, that if translated via Google Translate, only the first photo in each post can be viewed in the translated version, even when there are multiple ones in the original).
Cheers, and may your weekend, too, be a good’un,
Mattias
You’re soon to have another follower of your blog, Mattias! Just so I can see the photos, if nothing else. [I’m sorry to say, my familiarity with the no-doubt glorious lingua franca of Sweden is even less than extremely limited. I think perhaps in Swedish, “no” is the “no” I’m familiar with, and I think there might be a “ja” or something like that meaning yes, and “okay” seems to have joined every language, at least informally, and I think I recall that our “good day” turns into “gud dag”. Beyond that…well, I’d be totally at sea, I’m afraid.
I’ll look forward to seeing and hearing more from you around here.
Cheers, always,
Perry
I hear of folks who joint-plane every edge square, straight, and true, and I bounce between reactions of envy and disbelief.
I’ve still got a lot of learning and practice to be done to get even close to such a work style. A seven-foot spring joint for a table top would be a challenge for me, too, and a whole package of ‘em would be enough to cause a wee bit of heartburn, I fear.
Given my own current skills with a plane, whether it be a jointer, a jack, or a smoother, this would be…difficult. Enough so that I’d give serious thought to purchase of a No. 95. And now that we’re talking about the 95, I’ll say that I’m somewhat surprised it isn’t a bit more commonly mentioned by hand woodworkers who do lots of tabletop joinery. I’d be interested in hearing from others with more knowledge, experience, skills, and chutzpah why that is. Perhaps it’s everyone’s “secret weapon”, never talked about for fear of annoying the woodworking gods?
FWIW, I find Fitz’ comments illuminating and convincing. I especially like the idea that pressure (which can have an effect even on a #8, I believe, though I have only a #7 in my army) varying along the edge as the plane travels very nearly the length of Shaquille O’Neal can produce relative high and low spots. I think that such a problem might be magnified with a shorter plane; it’d be interesting to see some testing done there. (We need to remember to respect the many variables that are in play on the field of hand woodworking.)
Let me finish by saying I wish the very best to the woodworker laboring so well and so lovingly on what I’m certain is to be a beautiful table. God be with ye, my friend.
Ok, who makes that sleek looking 95 plane that’s gleaming chrome? The tool addict in me wants one!
I use my powermatic jointer and get really good results but I suppose that’s cheating.
It’s not cheating. That is made by Veritas. In stainless or nickel-resist. I forget. Great plane
I have the L-N right hand #95. It’s a work of art, and a darned fine plane too.
Do you still have your collection of all the different #95 planes?
Yup!
I dont think I’ve seen them all laid out together before. Please consider a group photo and maybe a blog post some day.
I checked out the Veritas website, and they now offer what they call an Iron Edge-Trimming Plane (http://www.veritastools.com/Products/Page.aspx?p=391) in RH and LH versions, of course. It’s now not stainless or nickel-resist or anything shiny much at all—in fact, a wee bit homely, in my opinion, but it’s no doubt a great plane, though it looks like it came from the Lodge cast iron kitchenware collection. One advantage, I think, over the gorgeous L-N 95 is the blade size: 1 1/4 inches v. 7/8 inch. Obviously, for the craftsperson posing the original question, with a 1 1/8”-thick table top, the beautiful brass version from L-N would not be suited to the task simply because of size, but the Veritas tool would probably be a great choice.
Another option would be to build an extra long krenov style laminated plane. I’d aim for around 40″. They are easy to make and you can use the same iron from your #8. I built mine from leftover big box store oak. Stacked 3, 3/4″ thick boards face to face. Cut a 45° for the bed of the iron, ~60° for the relief. Then used 1/4″ vertical side pieces to tie it together. Add a 3/8-1/2″ oak dowel for the pin, make a wedge. And you’re done. I went ahead and made a tote too, but that isn’t necessary.
I have found that by marking a line on both sides of the board, Then plane a bevel on each side to the line then use the #7 or #8 to take out the point you just made gives you a nice edge that is 90 deg and straight.
Great tip. Thanks!
I’ve been working on a dining room table as well. 10’ long with 6/4 material. I’ve had many of the same problems. Finally ended up buying a LN N8 and clamping a block of wood cut to a perfect 90 as an edge guide. If you search, there’s a short PW piece about this written by CS. I can now reliably get a 90 but there are still a few gaps (a few thousandths) here and there. I’m going to pin loose tenons to reinforce the joint.
I was so glad to read your blog post, as I am struggling myself.
Last thought, don’t leave straight and trued pieces out in the shop for too long. They may end up warping. Don’t ask me how I know….
Could it be that the match of the Stanley Bailey no. 8 with the Hock blade is an issue? I have Hock blades and breakers in nearly all of my Baileys and Bedrocks. They perform wonderfully. After I restored a Bailey no. 8 from rust bucket status, I installed a Hock set (as a matter of principle even though the restored originals cut like butter with no chatter). I could never get the Hock blade edge set properly in the throat, even after endless adjusting of the frog. Skips and dust instead of curls. I set the no. 8 on the bench next to a disassembled Bedrock no. 606 with a Hock set and tried to duplicate the frog setting. Apples and oranges of course. The no. 606 cuts beautifully with the Hock metal, but no luck with the no. 8. So, I reinstalled the restored original Stanley iron and breaker in the no. 8 and they still cut beautifully. I put my experience down to over engineering. This is not a knock on Ron Hock because his stuff is top shelf. But it did make me wish for a Bedrock no. 608.
I had to file the front of the throat on my Bedrock #8 to use a Hock iron. The back of the iron rode on the bed otherwise, and wouldn’t seat properly.
John, that’s a good suggestion and probably will allow necessary blade clearance on my no. 8. I do resist making irreversible modifications, particularly in this case because I have the original iron and breaker that function quite well. Maybe I should look for a no. 8 that already was modified. Thanks for your suggestion.
Is the No 8 too wide to work an edge that is only 40% the width of the iron? Does that introduce the rocking that requires a fence?
With the caveat that the longest spring joint I have ever done was about 5’2″, I have had success by augmenting the magnetic fence with a wooden block so that the plane is centered over the board’s edge, balancing the plane. I use a #8 but wish I had a #7 for jointing. I set up the iron like a smoother with a very slight camber, so I can dial in 90 degrees with very slight lateral adjustments.
I don’t know if you have already seen it or not, but Bob Van Dyke has a video on making a spring joint using a #4 plane on the Fine Woodworking website. The link to it is here: https://www.finewoodworking.com/2020/02/07/video-creating-a-spring-joint-with-a-handplane
I built a 9ft. Table top a couple of summers ago and I chased my tail trying to get a descent joint ,finally got some sidewalk chock I stole from my grandson painted one board clamped them up ,an every high spot showed up.also found out that 80 grit sandpaper worked good when you only have to remove a little sliver of wood
The wider the plane the harder it is to keep it in propel orientation horizontally. The tendency is to get the plane out of horizontal. Easier with a mass that is less wide.
The other problem is that with a short plane, the plane follows the actual wood rather than keeping the edge “perfectly” straight. These are reasons I think there is a better solution than a #8 or a #95.
I believe the “perfect plane” for truing the edge is a 5 1/4. Fairly long, not so wide, and pretty easy to use on its side.
Find a flt surface ( kitchen countertop, or similar) and shoot it on its side.
Next time I get the urge to make a Krenov style plane, I will make a really long shooting board style plane. 1 1/2 – 2 inch wide blade is good enough. 24 inches long sounds about right.
Two things that I have notice in my successful and unsuccessful attempts :
1. You want to take very thin cuts and check the gap with a feeler gage or thin paper.
2. Spring joints in harder woods are much harder than in e.g. pine.
When it just won’t work right, I use my shop built edge sander: looks almost like the edge plane but is longer and made of plywood to which a 90 slat is attached. The sandpaper is clamped between the side and the 90 degree slat. The pieces are screwed together. Works with a good amount of elbow grease and best with coarse grits.
I don’t recall, exactly, but when I sprung the joints on my dining table top i used a feeler gauge to help me find the high spots and ensure the gap was even and gradually closed. That might help diagnose if it’s a varying pressure or a rocking issue.
I think I used my 607, not my 605.
Aloha,
Since we are talking about ‘joining’ wood together and not stone or metal, we dealing with a ‘living material’, that breaths and expands and shrinks with the moisture present in it’s location. Expansion is something the builder must take into consideration with the structure’s size and it’s giving and taking across a hopefully long life of usefulness to it’s owner. built correctly, it will stand the ‘test of time’, or not and the piece will fail in to ruin. Grain direction, kiln dried wood or air dried, finish applied, joints used, environment it is housed in, all these factors the careful builder takes into the type of design used.
Would this be a place for the old trick of clamping 2 eventually adjacent pieces together and sawing down the crack between them?
I always take a couple of swipes out of the middle of the edge before attempting to joint the whole thing. That way the middle is lower than the ends, so the first time I get a full length cut I stop. I’m not saying it’s failsafe, but it works 100% of the time for me.