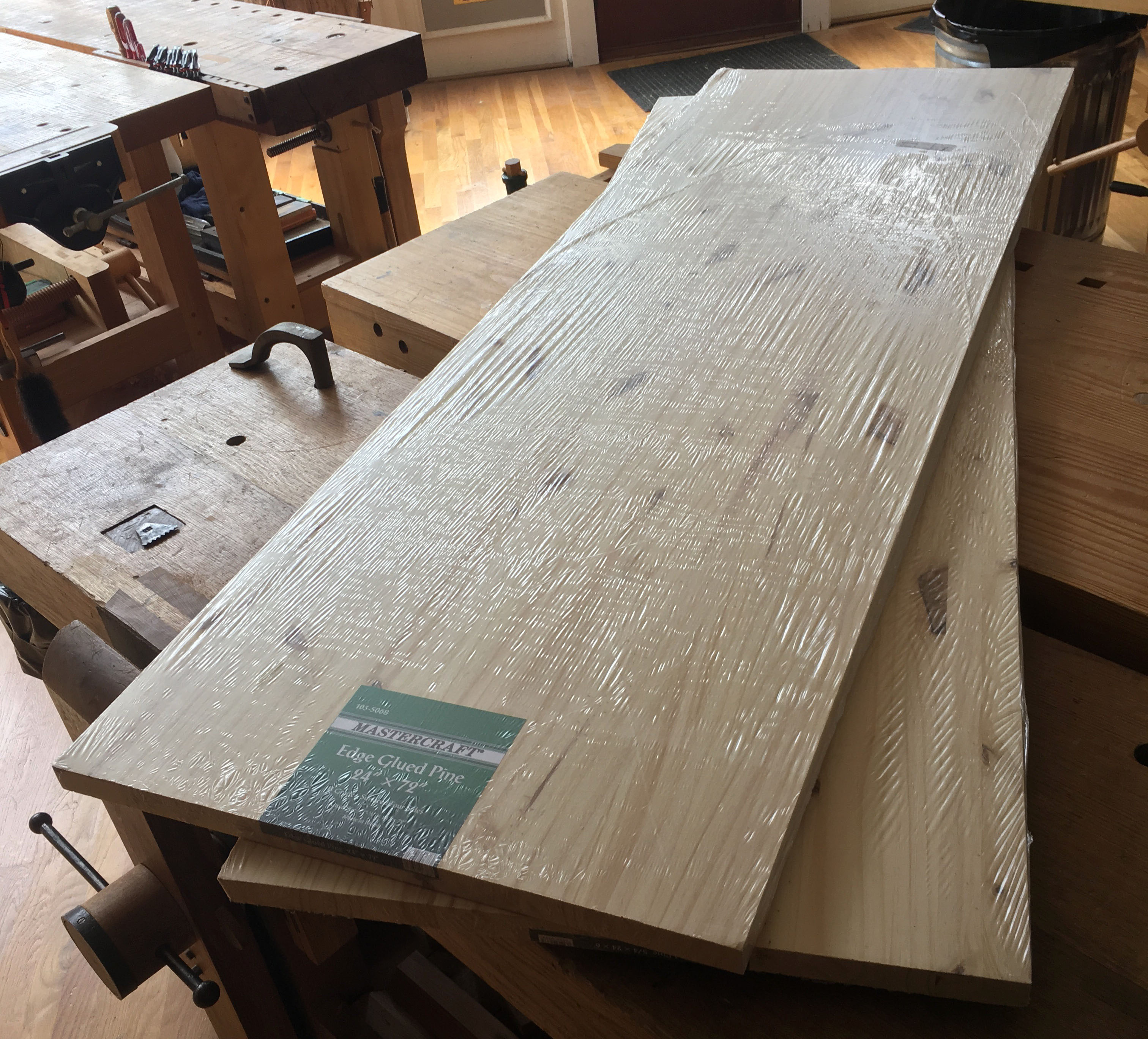
Q: Rather than glue up a bunch of my reclaimed pallet wood, I’m thinking about using some pre-formed “project boards” from the big box store to build a Dutch tool chest (further glue-ups in the house have been outlawed, so it’s either that or wait until it’s warm enough for Titebond in my unheated shop). I’m not too worried about the source material looking like a bowling alley for Smurfs, but I question whether milk paint will stick to something that appears to be 30 percent glue.
And because they also sell a 16″ project board, I thought I’d ask if either of you have seen a DTC that deep. Seems like I’d have to make it 36″ wide so it wouldn’t tumble over, and at that point, I might be better off with an English chest. What are your thoughts?
A: You can certainly use “project boards,” but there are a couple of cons: they cost about twice as much as gluing up your own panels from 1x, and they are often moisture-laden. They might look flat and inviting while sitting there all shiny in their plastic wrap, but remove the plastic and they might cup like a Pringle. But they might not. It’s a crap shoot.
For a Dutch tool chest, however, a 1×12 is wide enough for all but the lid. In fact, that’s the recommended material for those who don’t have access to a jointer and planer (and who don’t want to process material by hand). So were it me, I’d look for the flattest, straightest 1×12 you can find, then go to town. And for the lid, when I’m gluing up panels for a class with our limited number of clamps, I use Titebond and leave the clamps on for only an hour. Now I’m not saying you should…but surely there’s an hour in the day when you could get away with it? (Then hide the panel behind the garbage can overnight while the glue fully cures.)
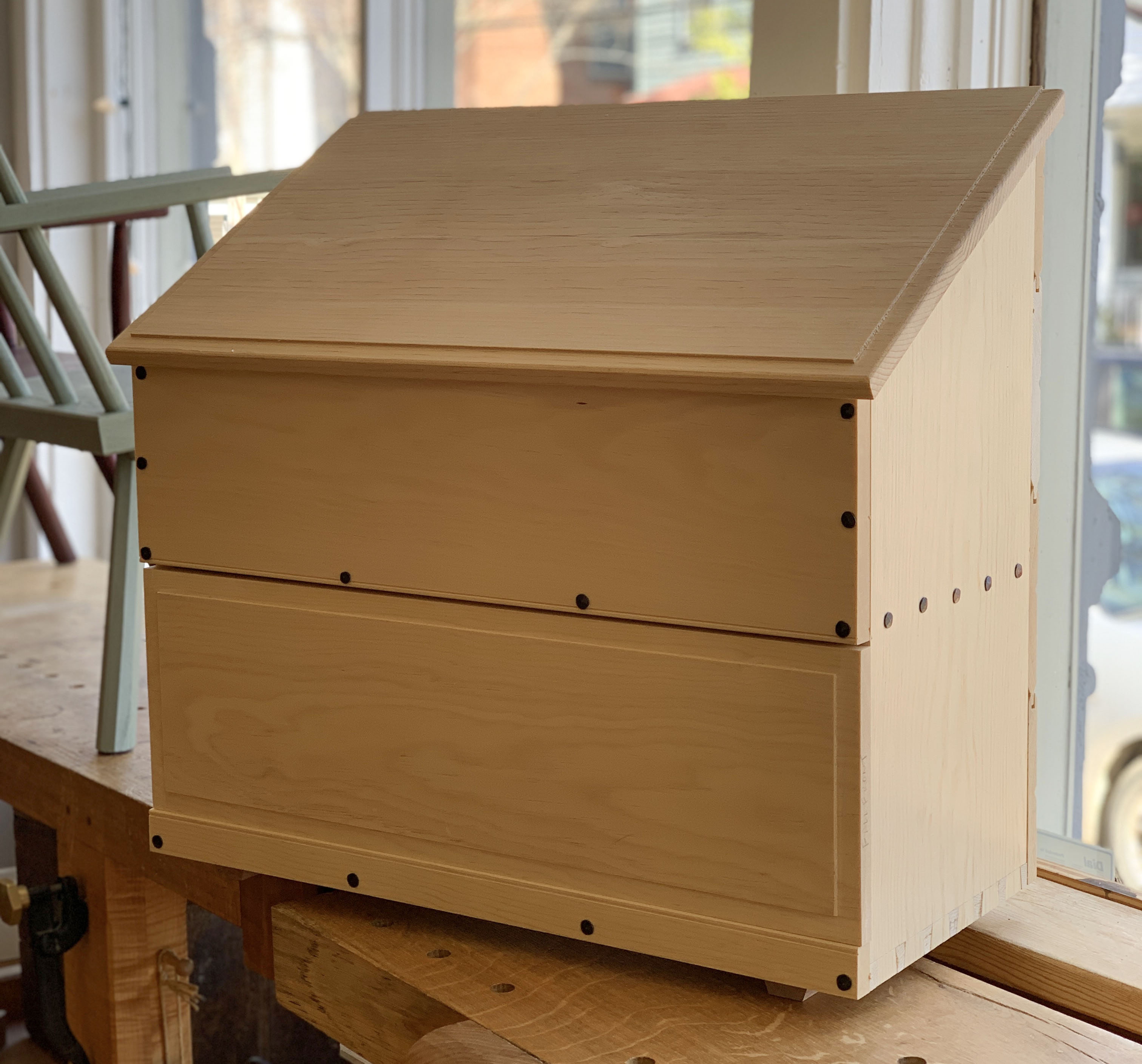
But yes, milk paint will stick to the project boards – but if you’re at all concerned about it, you can apply a barrier coat of dewaxed shellac between the raw wood and the paint.
And sure – you can make a Dutch tool chest 16″ deep (which will end up at 17-1/2″ after you attach the front and back). In fact, it’ll be more stable than the usual 12-3/4″ deep DTC). I’ve seen them in all sizes. The only drawback with making it deeper (or larger in any dimension) is that it’s no longer as portable.
— Fitz
I’ve used these boards for my ATC and several other projects that would be painted. I would highly recommend them if gluing up your own panels are too time or cost prohibitive.
I used 12″ “project boards” from the same green bbs for the sides, bottom, and shelf of my dtc. They were plenty stable and worked great. Though they had been sitting in my shop for several years before I used them. Personally I like the extra inch of depth. Left more room for a double rack and sliding till in the top compartment. I used leftover latex house paint for mine. Fully loaded (overflowing really) mine weighed in at 120#. because of the size I could lift it fine but definitely wanted it on the caster dolly whenever possible.
In the UK, it can be tricky to get good pine 1×12’s, especially from a big-box store. So for me, project board (often called furniture board over here) was a fair compromise, and was actually less expensive than a good pine 1×12 would have cost. But, as you mentioned was possible, cupping was an issue I had to work around. However, it all came together fine and is working well 18 months later.
Same here, Germany and Norway. 1×12 from a big box store? Pull the other one…
My DTC is made using the cheap project board and tongue and groove boards for the back. Paint covers a lot of crap wood. The stuff can be a pain to chisel the dovetails, especially if your chisels are not super sharp.
My favorite solution for glue ups in an unheated shop is a cheap electric blanket. It works great and is far cheaper to use than heating the shop for just a glue up.
I built a much deeper and taller tool chest with a deep lid that when opened is supported by pneumatic hinge stays and has magnetic holders for an array of hand tools, a second level for tools too large for the tool board lid, a pull out countertop for sorting, and a drawer for hardware (screws, bolts, nails, hinges, etc.) The remaining open shelves beneath are for much larger power tools, and containers for clamps, rags, bungee cords, paint, etc. Of course it sits on heavy rotating 5” castors.
Recently, I have made a few projects from #1 SYP joist material (#1 available at Menards, #2 only at Lowe’s and HD). It is somewhat knot free, more so I think than common 1x material. I rip it when needed and can re-saw into 1x material, too. When ripping, I look for the pieces that have pith, so I end up with 2 rift-sawn narrower pieces and a narrow piece of scrap. If I was re-sawing the whole 2×12, I’d avoid the pith. SYP dries very hard over time.
If you’re worried about adhesion on anything except bare wood use Milk Paint EXTRA-BOND sold by The Old Fashioned Milk Paint Co. Warning — I ordered some in the winter once, and it apparently froze and separated out into two components during shipment. Couldn’t get it to re-mix. The company sent me a replacement.
I use their milk paint for the insides of my band sawn boxes. Very easy to use — it goes on like cream.
At least here in GA, at both HD and Lowe’s for a painted counter height bookcase the paint grade glued up panels were much less expensive than any combination of various widths of the #2 pine boards at either big box for this 70” x 30” x 13” carcass with two vertical dividers and a shelf per section. Only pains were a few knot areas requiring some additional filler, and a thickness of 21/32”.
They were flat and not plastic wrapped like the more expensive “Project Panels”. Looks like pine but the Lowe’s panels were manufactured in Brazil. I told my daughter that the bookshelf was special because it was made with exotic imported wood from South America.
I tried counting the pieces that make up those Project Panel Puzzles. Some of the finger jointed pieces were as short as 3″ x 2″. I got to 73 pieces on a single board before I got too dizzy and had to stop. Seriously.
Whoever invented the machine that can put all that scrap together in an affordable panel is some sort of genius. Sort of like the guy that composed the Kars for Kids song.
They make up pieces much larger than the normal plywood sheets and then rip and crosscut into the “sales” dimensions. I assume they also cut metric sized. The original glue ups are thicker than the “sales” thicknesses also and they are run through a planer. I hope that this is a use for lots of unsalable shorts instead of them going into a boiler. Must be really automated to make them cheaper than dimension lumber
I gotta say, they are more aesthetically pleasing in the boiler.
Suggest you only use in painted projects
I just finished making two shelving units with project boards. My issue wasn’t flatness but how brittle they were. All the little finger-joint points wanted to jump out, and even a rabbet was too complex for the wood to handle. Of course the grain went in all directions at once. I tried to do good joint work with the first unit, but the second one I just screwed together. The second one looks better.
I love them they are great I made my ATC out of that stuff. made my dads coffin using them also.
Thanks, Megan (and everyone else) for your ideas. Jesse’s comment sold me on the merits of a slightly deeper chest, and I heard enough about project boards—can be “just fine” or “peanut brittle with end grain”—to decide that they are beyond my dovetailing and dadoing risk tolerance. Pine sticks it is!
On my last couple of trips to the Big Box Store, I checked out the 1″ by 12″ eastern white pine boards, and all of them were either cupped, bowed, or too twisted for even Joaquin Phoenix to play. But there were plenty of 1″ by 6″ and 1″ by 8″ boards that seemed fine. So, rather than risk another you-ruined-my-sweater confrontation (she put a nanny-cam in the laundry room), I’ll wait a few more weeks and glue up single-seam 12-3/4” panels out in the garage, far from her cherished woolens. Sixes to the front for verticals and eights for the horizontal pieces, to avoid joining seam-to-seam. And pallet wood for the fall-front, tongue-and-groove back boards, and the lid.
Fair enough — but glue up an 11-1/4” board (the additional 1-1/2 in the width is the front and back)
I calculated 12-3/4″ panels as the sum of 7-1/4″ for the nominally 8″ boards and 5-1/2″ for the 6″ boards. Add in the front and back for 14-1/4″ exterior. I’ve got a couple of things that will just fit nose-in to a 12-3/4″ interior that would have to go sideways in 11-1/4″.