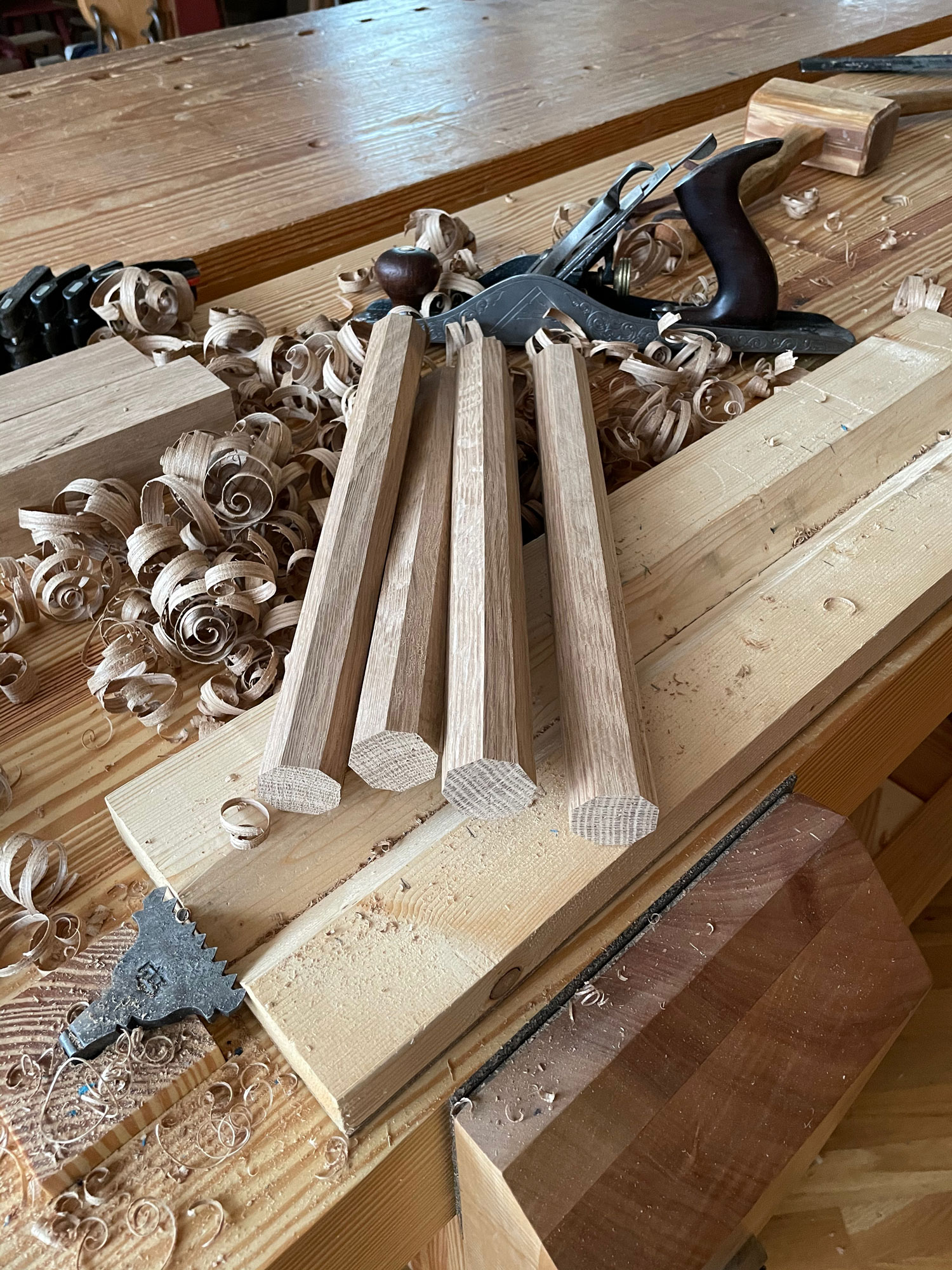
For the last seven years or so I’ve been working with kiln-dried wood that I have rived to help straighten out the grain in my components. But I haven’t really written about it because – I’ll be honest – I was uneasy about presenting the process.
It works really well. It’s not as perfect as riving green stock – that’s the gold medal technique. But it can greatly improve the strength and working characteristics of your parts and allow you to use plain-old lumberyard wood.
As this is one of the core techniques in “Guerrilla Chairmaking,” I thought I’d begin the discussion about it here on the blog and take my spanking.
Here’s how I do it.
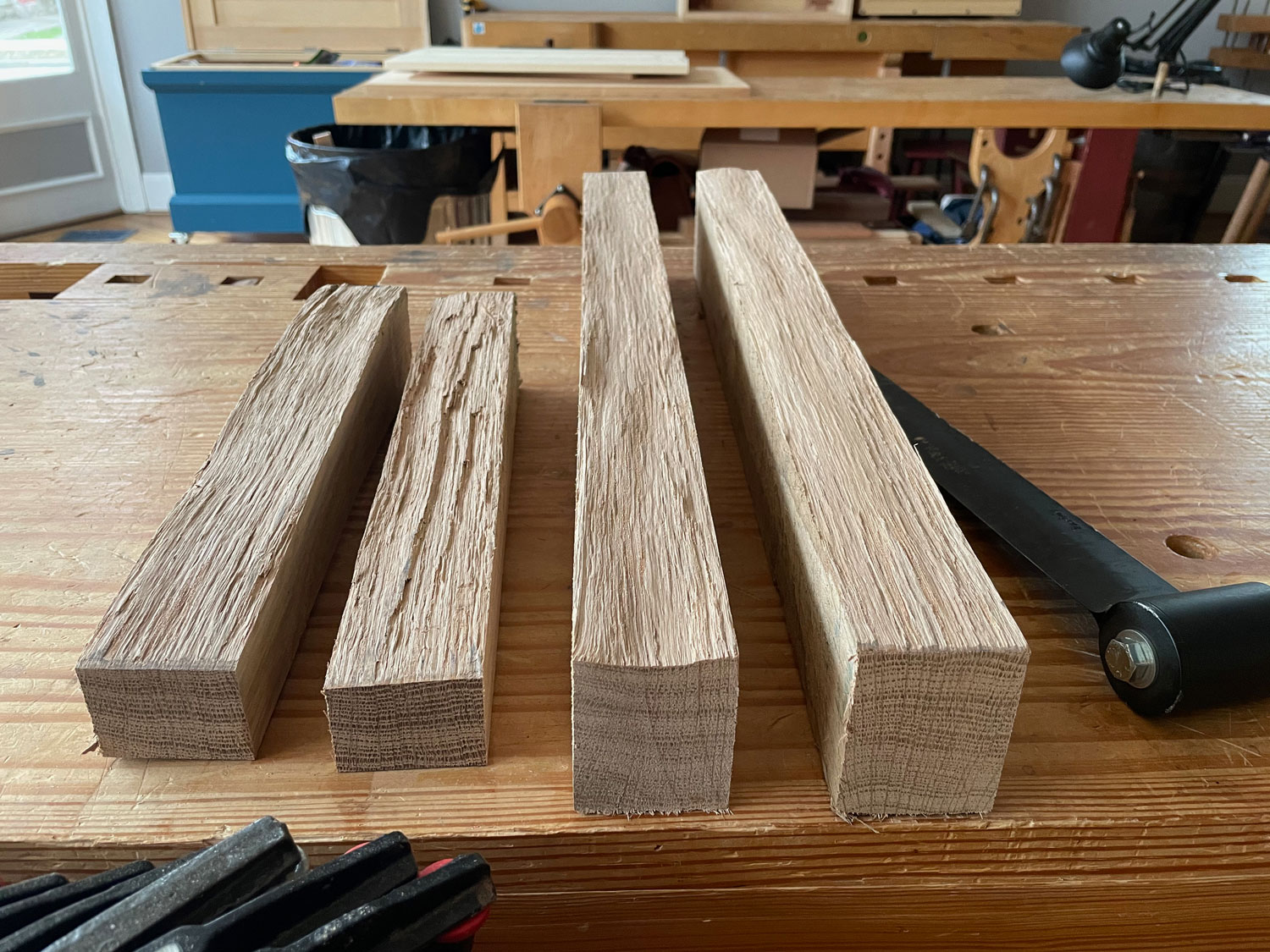
I use 8/4 quartersawn white and red oak when I go “dry riving.” I’ve done it with walnut and maple, but oak splits the best among the species I can get here. At the lumberyard I look on the edges of the boards for the straightest grain possible. Most quartersawn boards will have pretty straight grain on the edges and faces. The boards might have some curvy grain near one end – likely the beginning of the tree’s root mass. That’s OK – the curvy stuff comes in handy.
Then I crosscut the boards to the lengths I need. That’s 23” for legs and long sticks and 13” for short sticks. I mark out my parts on the end grain and plan the splits to follow the annular rings. Then I put the stock on my workbench (over one of the bench’s legs) and rive it out with a froe and a mallet – just like green stock. With dry stock, I haven’t found as much need to rive the stock in half and then rive it by half again. I just pop the parts off the board.
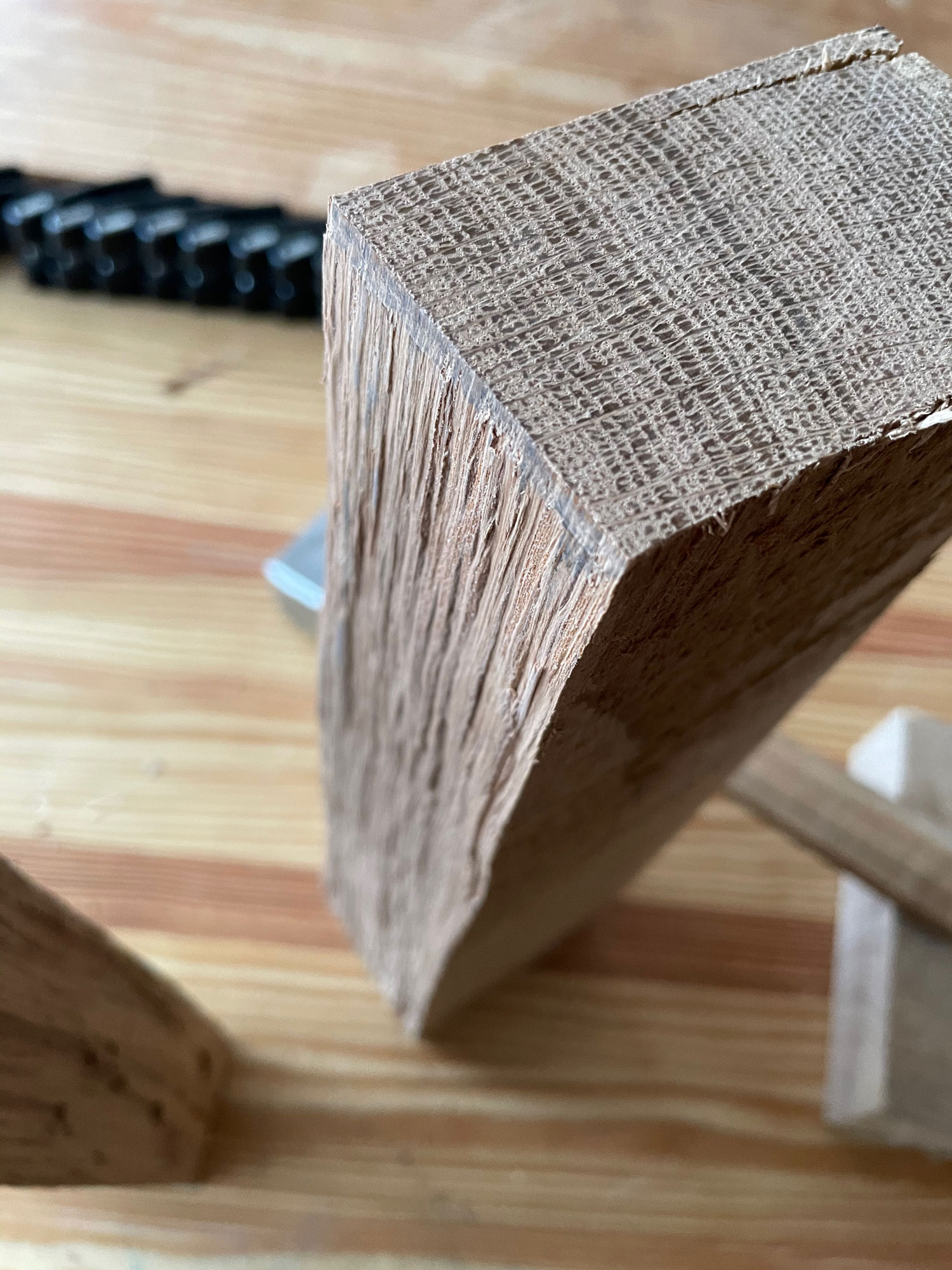
If I purchased straight-grained boards, I’ll get a flat surface along the split. I dress that with a jack plane and then work from there to true up the stick off that riven surface. I use a jack plane for most of this work, working either in a cradle (as shown) or against a stop a la Chris Williams and John Brown.
When the grain curves, I don’t throw that stock away. As you can see in the photo the top section is straight, but the bottom is radically curvy. I have a couple choices: crosscut the straight section and use that as a short stick. Or use the curved shape as an arm or crest.
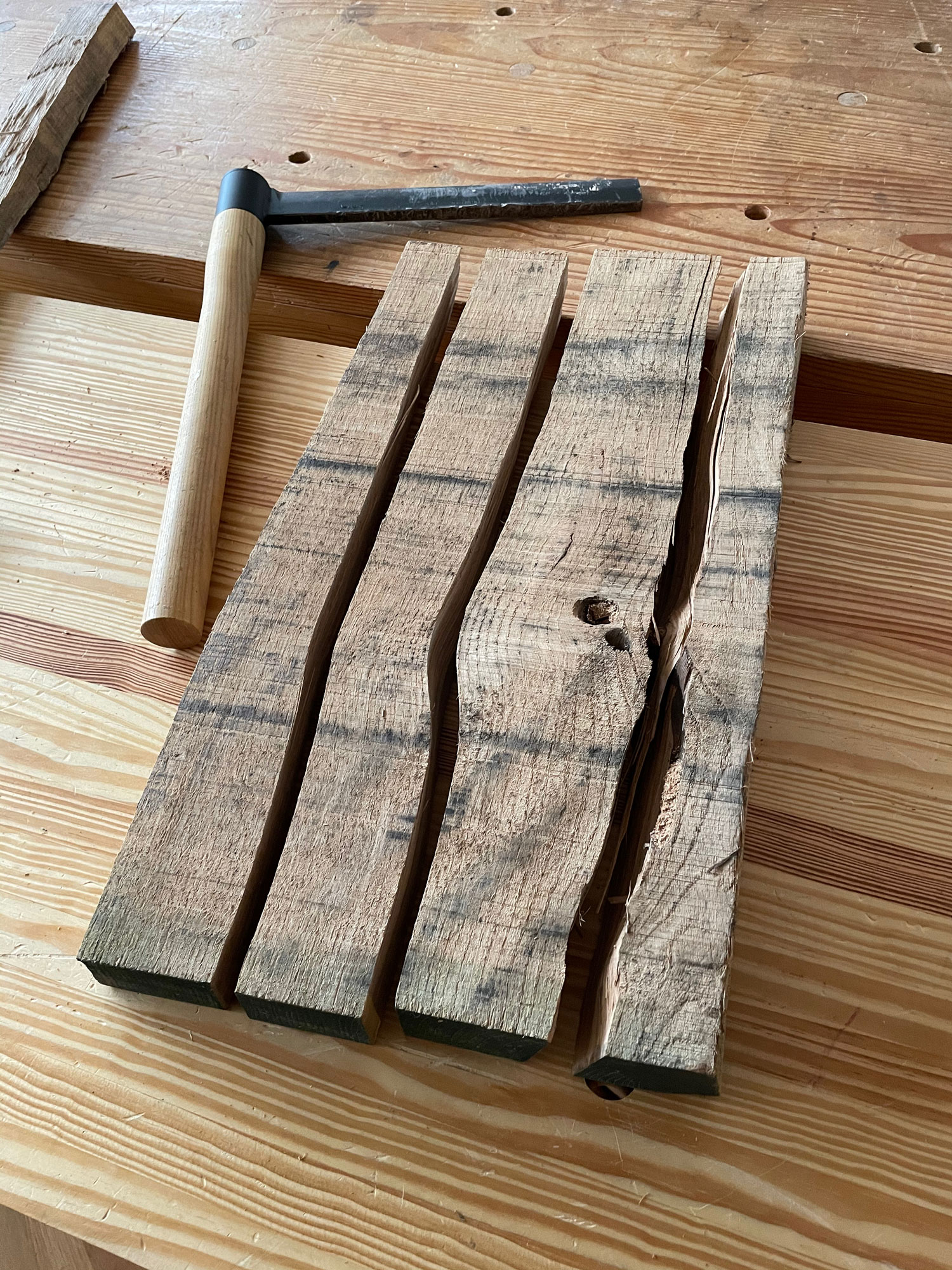
The parts I make seem strong as hell. For the book I’m going to test them against green rived stock (that has been air-dried). Chris Williams has a torture test for brash wood that also weeds out blanks with short grain.
In the book, I’ll go into a lot more detail than is possible with a blog entry, but this entry has enough for anyone to give it a try.
— Christopher Schwarz
A very timely blog post for me, so thanks!
Just before they closed for the holidays, I picked up a 10 foot plank of 4/4 (European) kiln-dried oak at the lumberyard two villages away, from which I plan to rive the blanks for the drawboring pegs for my bench build (quick update: I am now halfway through planing the top laminates to size and S4S; progress is slow but steady).
I couldn’t find anything perfectly quartersawn, but the one I picked up in the end seems to have quite straight grain all the way through for at least 2″ of the 4-1/2″ total width, so I should be able to get at least 32 best possible (and another 30 to 40 less good, if needed) 7-1/2″ long blanks, which of course will be more than enough (if I double-peg each joint, I’ll need 24 pegs).
I’ve more or less successfully riven kiln-dried lumber before for pegs, but only from flatsawn stock, and for smaller dimension pegs (1/4″ to 1/2″), so am very interested to see how it works out this time round?!
Cheers,
Mattias
great post, the number one target for good chair joints is straight grain. Whether is comes from green, air-dried or kiln dried stock does not matter as much other than ease of working. most of the chair repairs i have done are due to grain run out in the parts.
I’ve done this too, though usually only once per board – after I have a riven edge, I flatten that and then rip remaining parts using this new edge as reference.
This works most of the time for me. The problem arises (for me) when I want to get more than three pieces from a board.
The first rive creates two rived surfaces, plus one “leg” (or whatever).
Then you can rip parts from the two rived surfaces. But you can’t get a third part from the existing board because the remaining edge is sawn, not rived.
Hope I’m making sense.
Yes, that makes perfect sense… but if the grain is straight I just keep going, using first parallel-to-rive sawn surfaces as reference. That gets 4 parts from 1 rive.
This is probably sufficiently poor practice that I shouldn’t be sharing it. It’s not like clubbing a board with a froe is hard work.
If the grain is straight on the board, your technique works great. If it wanders a little bit that’s when I run into trouble
I suppose next you will be telling us how you put the legs into a steam box before drilling the holes so that when it dries it will lock onto the rungs?
Its interesting that you don’t need to rive by halves, as with green wood. I wonder why that is.
Ahhhh thanks for posting this today! I am just getting ready to put legs on my AmWelsh and was trying to decide if I wanted to wait to find a greenredoak log or saw from kiln dried. Now I have another option!
green red oak
This is awesome.
New to all of this but became particularly interested after seeing several huge oaks taken down in our neighborhood. It broke my heart after learning they would just be hauled to the dump. I befriended the arborist and found an acceptable alternative in the form of a local mobile sawyer with 30 years of experience and a woodmizer. After a few days, a dozen helping hands, and a LOT of saw dust, +2500 bdft is waiting patiently for me to learn to work wood. I’ve got a few years before any of it is dry enough to build proper joinery so I’ve started practicing riving the off cuts and spindle making by hand. I took several woodworking classes in the past and while I enjoyed it, I always came away discouraged at the machinery investment and real estate that it would take to do things “right”. The Anarchist Trilogy changed all of that for me and I am looking forward to add “Guerrilla Chairmaking” to the quarter sawn oak bookshelf I’ll build once enough has dried. Until then they will remain readily available and stacked on my staked bench.
I’ve read Williams and Brown regarding steaming and drying. Any new insights in “Guerrilla Chairmaking” or is that a spoiler alert for future blog posts?
Thanks, good to know you can do this successfully.
I’m watching Peter Galbert’s chair making videos and he shows this exact process for the first chair in the series.
This is so cool! As an amatuer luthier I’ve learned to rive dry spruce for bracing soundboards and backs. The process is pretty much identitical to what you describe, with the obvious differences between soft and hardwood taken into account. Braces are small enough that I’ll rive the same billet multiple times to get many braces, though if the grain looks straight enough I might just rip a second brace off of one riven piece as I believe you were discussing above.
Sorry for being dense. Why rive KD, QS, straight grain hardwood? Why not rip it? Works for legs. Have nothing against riving and enjoy riving the endless supply of green white ash (otherwise firewood) here in the Midwest.
Some people have trouble following the grain when marking out rips. Some people end up following the cathedrals or other structures. A quick rive shows you exactly where the grain falls. It also can be faster than a band saw….
Both work!
I am a fan of avoiding rip cuts by hand and dust from the table saw so will split out stuff all the time if there is enough material for the extra waste. I rive lots of green stuff when taking down trees if its strait enough. Cut it if there is wind. I am not sure this is riving since you don’t really control/steer the split through braking against the thick side. On kiln dried wood or even finished air dried this might just be splitting.
If you already have quarter sawn strait stuff not sure this makes it stronger 90% of riving is stock selection its got to be strait and clear otherwise its to much axe work after the riving . if you have a quarter sawn piece that was done with care and cut parallel to the grain you are already there as far as strength and quarter sawn orients the grain to minimize movement . If this helps identify what is parallel that’s great . makes less dust, great . For me riving is really about how to get a board out of a tree with out thousands of dollars of tech(sawmill). In the end developing the skill costs just as much in material and time, and you cant use a tree grown on a hill unless you like spiral board LOL.
As usual Chris, this is very interesting. Thanks, I will have to try it.
Thank you! This is extremely helpful — I have been playing with the idea of riving dry stock for a while, but wasn’t sure if I was barking up the wrong (dry) tree.
Thanks for posting this. So is the goal of riving to maximize the number of single, uncut fibers in a finished piece? And to achieve that you split the stock down to be as close to the final dimensions as possible before you have to cut it?
Exactly correct.
Excellent. Thank you.
Did a course with Jögge Sundqvist and he rived dry birch for parts. Straight birch rives beautifully, dried or green.
I have a small pile of air dried mixed species with some questionable milling (by yours truly) and have been experimenting with probably dry riving following the grain where possible for handles for tools. They have so far been all successful and any further information on this I would look forward to reading. Other than avoiding obvious defects and removing the short grain from the blanks what other factors are to be considered?
Hi Chris,
Not related to this blog, I was on YouTube and came across a video on a sculptors version of the low Roman workbench. Thought you might like it.
Sincerely,
Joe
https://youtu.be/_Vc9D0WAX7o