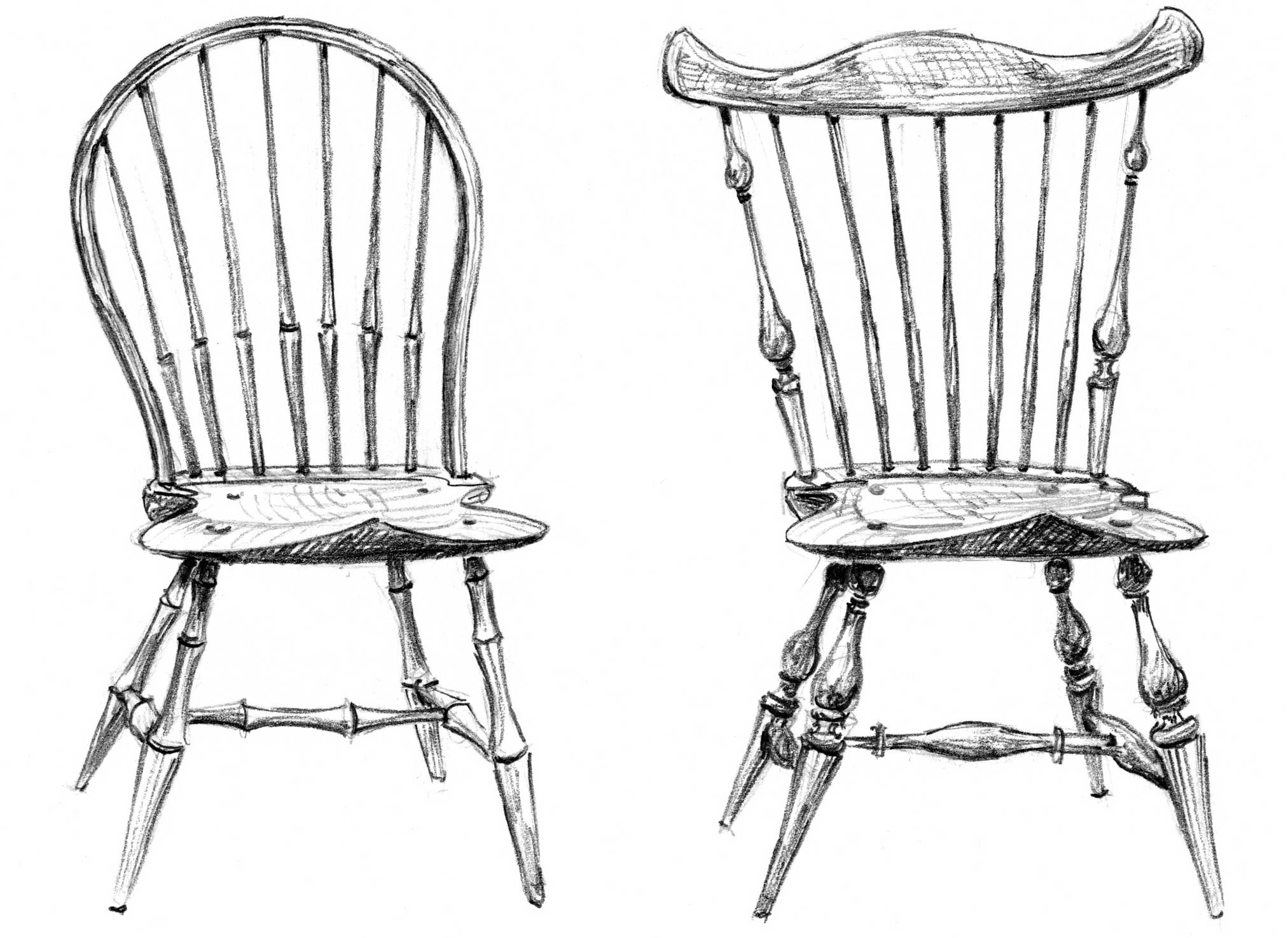
I love going to the Lie-Nielsen Toolworks Open House (almost) every summer for a number of reasons, but one of the best is getting to hang out with chairmaker extraordinaire Pete Galbert for a few days. He’s been there at every event I’ve had the pleasure of attending.
Pete is one of those people who always puts a smile on my face, because there’s always one on his. He’s just so darn nice and fun to be around. And he’s an extraordinary teacher – I was blown away by his presentations at Woodworking in America (back in my former life).
Hopefully I’ll get to see him in person next summer (if not sooner). But for now, I’ll have to make do with seeing him on his spindle turning and milk paint videos. And, of course, reading from his book (for which he also did all the gorgeous drawings).
Excerpted from Peter Galbert’s “Chairmaker’s Notebook.”
Obviously there is a long history to the Windsor chair. And along the way, I’m sure that just about every imaginable technology has been used to build them and all sorts of design innovations have been tried. I am neither a historian nor a wood technologist; luckily, there are a number of good books on both subjects. In setting out to write this book, I wanted to make chairmaking accessible and open a door into a gratifying kind of woodworking.
Looking back, I recognize that my own transition into working with green wood took place in stages. I remember simply wanting to see what a drawknife could do, and I didn’t care if it was on a split piece of oak destined for a chair or a 2×4. I encourage you to act on your impulse to explore and play. These are vital steps in the learning process.
Even though I could simply lay out a single path to success for making a chair, I recognize that each of us comes from a different background, workshop and skill set, so I’ve tried to stress the principles that you’ll encounter, knowing that you will apply the information that best suits your ability and interests.
I’ve structured the information so that the basic concepts are illustrated, and if you want to go deeper into the topic, you can delve further into the text. Illustrating the book myself was an obvious choice for me because not only do I enjoy drawing, but I also hope to impart as much visual information as possible. Plus, the chairs, with their thin lines and crisp silhouettes, translate beautifully when drawn.
The project portion of this book details the process of building the two chairs shown below. While the process for building a chair is simple, there are many opportunities to learn more about the materials, tools and techniques.
The project chairs were chosen both for their similarities and differences. Besides some aesthetic elements, the chairs are structurally identical from the seat down. That way, making one chair will give you experience that will serve you in the other. From the seat up, the difference is both aesthetic and technological. If you have access to green wood, you will find the balloon-back attainable. If you are limited to sawn (hopefully air-dried) lumber, you can make your way through the fan-back, which lacks the extreme bend, yet it has slightly more complex joinery in the crest.
Another reason that I chose these chairs is that they point the way toward two different families of design within the Windsor tradition. The balloon-back is a great introduction to the classic forms, such as the continuous-arm, sack-back and comb-back.
If your interest runs more toward more modern options, the fan-back leads to other designs with clean Asian-influenced lines, such as the birdcage and the step-down-crest styles. My unpainted contemporary designs are mostly rooted in the technology that begins with the fan-back form.
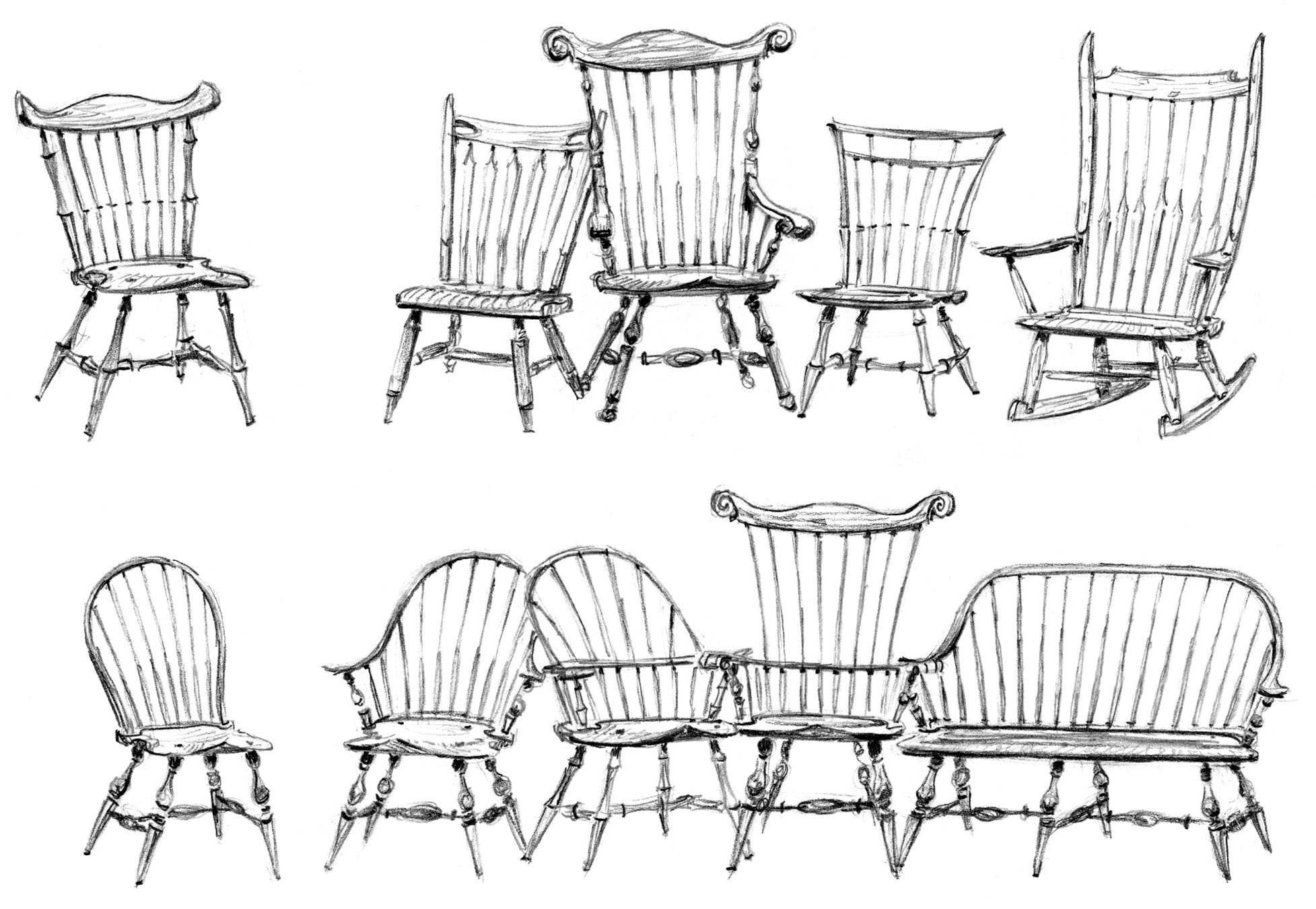
I also cover options for building these chairs using the lathe in a limited way, or without using a lathe at all. While turning is the most efficient way to make the legs and joinery, not having experience with or access to a lathe should not stop you from making a fine chair.
In this book, I’ve tried to address the questions that riddled me as I ventured into chairmaking and share some of the lessons and discoveries I’ve found helpful along the way. I spent most of my earlier years as a woodworker poring over books to squeeze out the information that I needed. One thing that struck me was that I got something new each time I returned to my favorite texts. My goal here is to not only demonstrate ways to achieve the tasks, but to show some of the common problems you might encounter and how to address them. Because of this, some of the descriptions might make more sense to you once you’ve worked with the process and found a problem for yourself. If the depth of the information here ever seems daunting, take a deep breath and rest assured you can make a chair that will exceed your expectations with only the basic concepts in hand. Once you’ve grown comfortable with them, the rest of the information might be more inviting.
Even for experienced furniture makers, each process will likely introduce new challenges. From splitting wood to turning, steam bending to carving, it’s a different way of looking at making a piece of furniture. While there are many steps involved in making a successful chair, and mastering the process can be a lifetime pursuit, a little effort and resilience will pay off at each turn.
My hope is that the information here encourages you to build your first chair, or perhaps just your latest.
Check out Santore’s The Windsor Style in America, Vol. I and II, a large book with great background and photographs, most complete on the subject.
Draw knives are just plain fun. Savage yet delicate, depending on the user.
The best chair building book bar none, thanks for helping put it together.
I had the great pleasure of taking one of Pete’s classes at NBSS a few years ago. He’s a fantastic teacher. I highly recommend his book, LAP and Vimeo videos as well.
I always thought drawknives were very simple to sharpen. But Pete’s Drawsharp that Benchcrafted makes makes sharpening fast and simple, and brings the edge to a new level.
I have a sneaking suspicion I’m going to unwrap that book in the next few days. Looking forward to it! Have only heard good things about it.
I’ve never seen the back and arm spindles wedged from the bottom of the seat. Why is that? You would think those joints experience a great amount of stress when someone leans back.
Several makers do this. Including Thomas Moser.